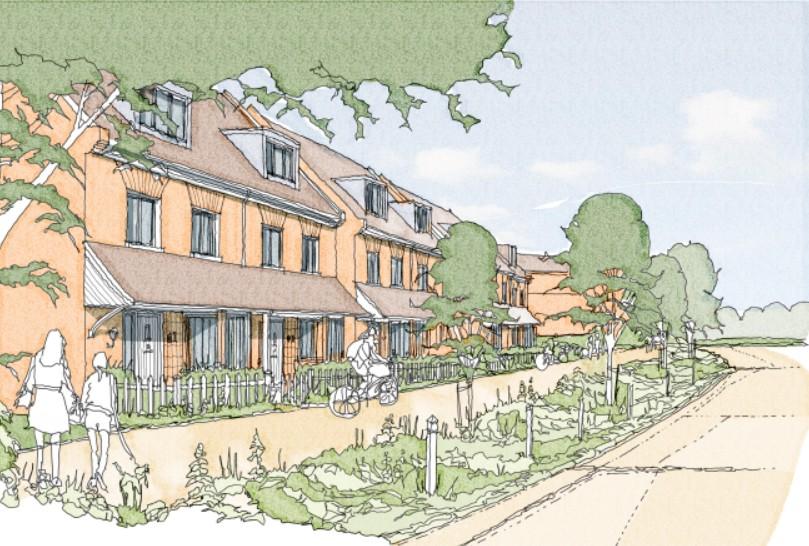
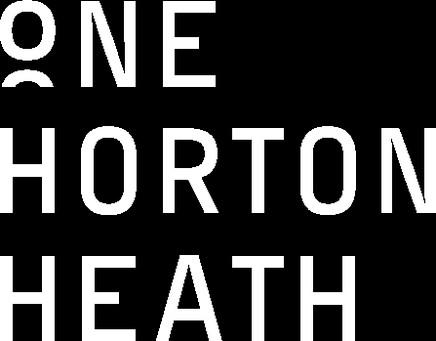
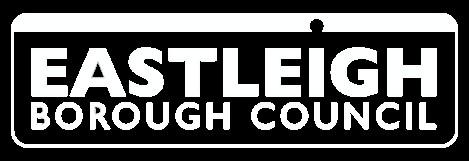
The One Horton Heath (OHH) Development Project is committed to operating in a manner that strives towards achieving and maintaining a Vision Zero workplace, and will pro-actively explore every opportunity to have a Positive Impact on the Health Safety and Environment, of its developments in general and specifically the employees, contractors, suppliers and customers.
This booklet is intended to set out the minimum standards applicable to all One Horton Heath operations – which include construction projects, land management, commercial developments, and any assets that we may develop, control, maintain, own, or operate. It does not offset or change any requirements of the H&S or HR department policies of Eastleigh Borough Council on direct or contract employees general conditions or responsibilities. This booklet is intended to set out the standards for the types of operations and processes not normally executed by EBC itself.
To this end, all employees, consultants and contractors engaged in the OHH development are to ensure that the controls and management systems for the sections applicable to their activities/projects/works are clearly stated and detailed in either the project Construction Phase Plan (CPP/RAMS) their Risk Assessment & Method Statements (RAMS) or their Design Risk Assessment (DRA) these are required before the work commences, and are to be regularly updated for the duration of the works.
To facilitate use, this booklet is divided into two parts.
Part One – Sets out the General Outline Requirements for common activities associated with common works.
Part Two – Provides detailed information and guidance on the OHH policy requirements and aligns the standards to the OHH Safety Management System.
All individuals and organisations engaged in the OHH development scheme will have been appointed or employed based on their competency, experience and knowledge as being required and applicable to the works to be executed by the processes in the Safety Management System and EBC procurement policies.
The key requirement on all persons and organisations is to comply, so far as reasonably practicable, with the OHH Safety Management Policies and all current HSE regulations, codes and guidance, industry practices and standards. Where these requirements can be improved upon then the expectation is that such improvements will be enacted wherever practicable and that such best or improved practice is to be shared with all parties involved on OHH.
OHH as the client organisation, has a duty under the Health and Safety at Work Act 1974 and the Management of Health & Safety of Work Regulations 1999, to ensure that all organisations (contractors, consultants etc) are effectively executing and managing their works correctly and safely.
This requires the employer to provide, so far as reasonably practicable, a safe place, methods, plant equipment, materials and, colleagues, to execute their works in a manner that will not cause harm to their health safety and welfare, or that of others affected by the works.
Key to this responsibility is for the employer to set out, how they expect the works to be actioned, what hazards and risks are associated with the works, and how the employer anticipates controlling these aspects to the lowest practicable level.
This is achieved by reviewing the works following the Hierarchy of Controls (Management of Health & Safety at Work Regulations 1999 regulation 4 and Schedule 1.) Providing a written record of the hazard review process and the associated risk assessment for operatives and others to safely execute the works.
This booklet is provided to indicate and assist the actions and requirements needed to ensure due consideration is given to the Risk Reduction Process.
Section 1. Fall Prevention –
True and proper application of the hierarchy of control is to be maintained to ensure that the risk of falls of people or materials is; a) preferably eliminated or at least, b) mitigated through the application of suitable fall prevention techniques starting from the initial design and the need to work at height, to the needs of maintenance and eventual demolition or removal purposes.
This will include the use of site access equipment including items such as edge protection barriers, fall restraint, fall arrest, ladders, podiums step ladders and hop-ups.
The use of these items will need to be justified within the issued Risk & Method Statements (RAMS) for the works.
Permits to work will be required for the use of step Ladders to ensure adequate application of
the hierarchy controls.
Suitable measures are to be established for the loading and offloading of materials and equipment from vehicle beds, these should be detailed in the relevant CPP/RAMS when issued.
To ensure that hazards related to the movement and interfacing of people and vehicles, material distributions, temporary conditions, and poor housekeeping are effectively identified and managed. Minimum standards shall be compliant with HSG 150 Health and safety in construction & HSG 144 The safe use of vehicles on construction sites
The CPP/RAMS/ RAMS for each section of work and each development package shall detail, on suitable site drawings, the primary vehicle routes, pedestrian routes, junctions, interfaces and cross overs. The drawing should indicate traffic flow directions, significant signage at crossings and junctions, and clearly state the maximum speed as 5MPH on the site roads.
Most construction transport accidents result from the inadequate separation of pedestrians and vehicles. The following actions will help keep pedestrians and vehicles apart:
Entrances and exits - supply separate entry and exit gateways for pedestrians and vehicles; Walkways - provide firm, level, well-drained pedestrian walkways that take a direct route where possible;
Crossings - where walkways cross roadways, supply a clearly signed and lit crossing point where drivers and pedestrians can see each other clearly; Visibility - make sure drivers driving out onto public roads can see both ways along the footway before they move on to it;
Obstructions – do not block walkways so that pedestrians have to step onto the vehicle route; and
Barriers - installing a barrier between the roadway and walkway.
To ensure that competent persons are appointed to plan work and implement controls; in accord with the hierarchy of controls, for the execution of any excavation of materials for foundations, services, drainage or similar, roads and paving’s or general terra-forming, and that any plant and equipment used is fit for purpose, and properly used by competent persons at all times.
The CPP/RAMS will need to identify areas of the site that are to be used for stockpiling of materials and show the planned routes to and from for the haulage equipment and identify what if any type or specification of haul roads to be installed, taking into consideration the generation of both noise and dust impacts on local occupants and the workforce.
Groundworks and earthworks are to be carefully controlled at all times and particularly where there is the potential for there to be underground services local to the works. Before any work commences there should be a full desktop and physical survey undertaken to identify the routes and depths of any known services, this should include hand excavation or VacEx sampling along suspected routes to confirm locations. (As per guidance in HSG 47.)
In conjunction with the CPP/RAMs associated with the Logistics and Groundwork operations, the employer should identify how they intend to manage the impacts on the local environment by the issue of a Construction Environmental Management Plan (CEMP). This requires the employer to risk assess the impact of their operations on the general local environment and set out the necessary elimination, reduction and control measures to be followed.
To ensure that competent persons are appointed to plan work and implement controls; in accord with the hierarchy of controls and specific legislation requirements, for the execution of all lifting operations, recording of regulatory inspections, and that any plant and equipment used is fit for purpose and operated only by competent persons.
The planning of individual routine simple (lift-off and lower) lifting operations may be the responsibility of those who carry them out (e.g. a slinger or crane operator). For more complex lifting operations that require specific changes in location or placement to locations other than on the ground, a written plan shall be developed by a person with significant and specific competencies - adequate training, knowledge, skills and expertise - suitable for the level of the task. Generally, this person will be trained as an Appointed Person (L) under the CITB CPCS scheme.
For straightforward, common lifting operations, a single initial generic plan is required (e.g. fork-lift trucks or telehandlers, or excavators), which could be part of the normal risk assessment for the activity. However, from time to time it may be necessary to review the plan to make sure that nothing has changed and the plan remains valid. Routine lifting operations which are a little more complex may, depending on the circumstances, need to be planned each time the lifting operation is carried out.
To ensure that all electrical installations and equipment are designed and built to be fit for purpose, correctly installed, protected to prevent electrical shock or fires, appropriately maintained and only worked on by competent persons. All electrical works, in general, shall be designed, installed and tested following BS 7671 18th Edition
All electrical distribution services for the site works should be compliant who BS7375:2010 Distribution of electricity on construction and demolition sites. Code of practice.
All electrical installations and equipment, including portable tools and equipment, are to be regularly inspected and maintained in good working order. Portable Appliance Testing where applicable should be scheduled for all site located equipment at not more than three monthly intervals. Temporary Accommodation Units (TAUs) and compound store services etc are to be tested and certified upon installation and annually thereafter or following re-locations.
All foreseeable risks arising from the occupation of the site, as well as any such risks to occupational health arising from the actual works, are assessed, and effective control measures implemented to prevent injury and ill health, which, along with appropriate welfare facilities work to create a better and healthier working environment.
To ensure that effective arrangements are in place to assess and minimise the risk of, and manage the consequences of, all potential fire and emergencies arising from the occupation of the site, the working on the site and the items under construction to protect life, property and business continuity.
To ensure that effective arrangements are in place to minimise by assessment, the foreseeable risk of, all potential environmental damage and or emergencies to protect the environment locally and regionally, and manage the consequences of any foreseeable incident on the property and business continuity.
To ensure that in addition to the content of any work specific Risk Assessment the MINIMUM level of PPE to be worn on site always is set out.
OHH shall require a site-wide minimum for normal site works of:
Saturn Yellow Hi-Vis Waistcoats to ISO EN 20471 (Class 2:2)
Head Protection to EN 397. [BLACK for Supervisors]
Safety Footwear to EN ISO 20346 S1
Hand Protection to EN 388 grade 4:4:4:4
Light Eye Protection to EN166 Class 1
For Highway working the following will be needed as the MINIMUM;
Saturn Yellow Hi-Vis Sleeved jackets with Trousers to ISO EN 20471 (Class 3)
Head Protection to EN 397. [BLACK for Supervisors]
Safety Footwear to EN ISO 20345 P
Hand Protection to EN 388 grade 4:4:4:4
Light Eye Protection to EN166 Class 1
To ensure that all parties have a clear understanding of what OHH will accept as the basic H&S training requirements for primary functions on the development.
Managers & Surveyors Etc.- CSCS PQP Card + Professional Body / Technical Qualification + IOSH Managing Safely or similar.
Construction Managers - CITB SMSTS Certificate with CSCS Black (NVQ4+) or Gold (NVQ4) Card
Supervisors- CITB SSSTS Certificate with CSCS Gold (NVQ3)
Advanced Crafts Skilled workers – CSCS Gold (NVQ3)
Skilled Worker CSCS Blue Card (NVQ2)
Labourer’s CSCS Green Card (NVQ1)
Plant & Machine Operators – CPCS Blue Card (NVQ2) unless undergoing training up from Red Card.
Scaffolders
CITB CISRS Card right for task level and type of Scaffold.
Mobile Tower Scaffolds PASMA Certificate.
MEWPS IPAF Certificate for the type of plant to be used. Rope Access (Arboreal etc.) IRATA or AFAG trained Street Works NRSWA Supervisor or Operatives Cards
Alternative accredited cards are acceptable as listed on the CITB web site https://www.cscs.uk.com/about/partnercard-schemes/
To ensure the suitable provision of welfare facilities across the range of development locations the OHH development will require all Welfare provisions to fully comply with Schedule 2 of the Construction (Design Management) Regulations 2015.
This is an applicable standard for all work locations and can be provided by the use of TAUs such as Garrick or Oasis units for periods up to 6 weeks for small and short-term site locations.
Daily mobile gangs on isolated multiple locations should have use of a centrally located provision of welfare facilities (not public facilities). These gangs should be supplied with their own 1st aid provisions, hand washing, drinking water and sanitising provisions and have agreed on access to toileting facilities if none are specifically provided.
One Horton Heath can influence the design of the development and specific works from the position of a client. It is, therefore, OHH’s responsibility to ensure that, a specific Design Review is carried out to highlight and eliminate environment, health and safety risks in design, construction, fit-out, operation and maintenance.
The design evaluation process should follow the hierarchy of controls and provide passive collective protection measures over individual or engineered solutions.
To this end, there are various guides and assistance available but the simplest is the use of RED AMBER & GREEN lists of processes, materials and operations to be considered provided by recognised bodies such as CIRIA and the HSE.RAG lists are practical aids to designers on what to eliminate, avoid and encourage.
During construction, operation and maintenance further reviews must be undertaken to reassess the HS&E management approach and to identify revised methodologies for delivering improved environment, health & safety-related outcomes.
Hazardous procedures, products and processes should be eliminated from the project where possible.
Lack of adequate pre-construction information (e.g. asbestos surveys, details of geology, obstructions, services, ground contamination and so on).
Hand-scabbling or drilling of concrete (e.g. ‘stop ends’ or multiple fixing points).
Demolition by hand-held breakers of the top sections of concrete piles (pile cropping techniques are available).
Specification of fragile roof lights and roofing assemblies.
Processes giving rise to large quantities of dust (e.g. dry cutting, blasting and so on).
On-site spraying of harmful substances.
Specification of structural steelwork which is not purposely designed to accommodate safety nets.
Designing roof-mounted services that require access (for maintenance and so on), without provision for safe access (e.g. barriers).
Glazing that cannot be accessed safely. All glazing should be anticipated as requiring cleaning replacement, so a safe system of access is essential.
Entrances, floors, ramps, stairs and escalators not specifically designed to avoid slips and trips during use and maintenance, including taking into account the effect of rainwater and spillages.
Design of environments involving adverse lighting, noise, vibration, temperature, wetness, humidity and draughts or chemical and/or biological conditions during use and maintenance operations.
Designs of structures that do not allow for fire containment during construction.
Amber lists
Products, processes, and procedures to be eliminated or reduced as far as possible and only specified or allowed if unavoidable. Including amber items would always lead to the provision of information to the principal contractor.
Internal manholes and inspection chambers in circulation areas.
External manholes in heavily used vehicle access zones.
Specification of ‘lip’ details (i.e. trip hazards) at the tops of pre-cast concrete staircases.
Specification of small steps (e.g. risers) in external paved areas.
Specification of heavy building blocks (e.g. those weighing more than 20kgs).
Large and heavy glass panels.
Chasing out concrete, brick or blockwork walls or floors for the installation of services.
Specification of heavy lintels (slim metal of hollow concrete lintels are better alternatives).
Specification of solvent-based paints and thinners, or isocyanates, particularly for use in confined areas.
Specification of curtain wall or panel system without provision for tying or raking scaffolds.
Specification of blockwork wall more than 3.5 metres high using retarded mortar mixes.
Site traffic routes that do not allow for one-way systems and/or vehicular traffic segregated from site personnel
Site layout that does not allow adequate room for delivery and/or storage of materials, including site-specific components.
Heavy construction components which cannot be handled using mechanical lifting devices (because of access restrictions/floor loading and so on).
On-site welding, in particular for new structures.
Use of large piling rigs and cranes near-live railways and overhead electric power lines or where proximity to obstructions prevents guarding of rigs.
Green lists
Products, processes and procedures to be positively encouraged.
Adequate access for construction vehicles to minimise reversing requirements (one-way systems and turning radii).
Provision of adequate access and headroom for maintenance in plant room, and adequate provision for replacing heavy components.
Thoughtful location of mechanical and electrical equipment, light fittings, security devices and so on to facilitate access, and placed away from crowded areas.
Specification of concrete products with pre-cast fixings to avoid drilling.
Specification of half board sizes for plasterboard sheets to make handling easier.
Early installation of permanent means of access, and prefabricated staircases with handrails.
Provision of edge protection at permanent works where there is a foreseeable risk of falls after handover.
Practical and safe methods of window cleaning (e.g., from the inside).
Appointment of a temporary works co-ordinator (BS 5975)
Off-site timber treatment if PPA- and CCA-based preservatives are used (boron or copper salts can be used for cut ends on-site).
Off-site fabrication and prefabricated elements to minimise on-site hazards.
Encourage the use of engineering controls to minimise the use of personal protective equipment.
All contractors/service providers employed by One Horton Heath must actively support the One Horton Heath vision of operating Incident & Injury Free with the aim of Vision Zero .
All contractors/service providers formally engaged to provide development, construction, management or maintenance services must go through the relevant pre-qualification process which will include an assessment of the organisation’s ability to meet any relevant safety management requirements such as a Safety Standards in Procurement (SSIP) registered assessment via Construction Line or similar.
Competence for the required type and nature of work by following up of references, and all other provisions including adequate insurance cover for Public and Employees Liability and where necessary the provision of Design and Professional Liability Insurances. The environment, health and safety responsibilities of key contractors/service providers, and the significant risks associated with their works must be clearly defined for each engagement.
The relevant OHH standards and any other EH&S requirements must be provided to these organisations to adequately plan and price the work. The quality and accuracy of the contractor/service provider documentation in response to the management and controls of HS&E issues should be a key factor in selection.
Contractors/service providers must employ adequate numbers of competent supervisors, provide proof of competence for key workers, particularly those supervising and or carrying out high-risk activities or, undertaking work where proof of competence is required by law, and collaborate with One Horton Heath in pursuing compliance with the HS&E Standards.
All new contractors/service providers’ contractual documentation shall contain confirmation of agreement to follow the OHH Code of Construction Standards, as well as acknowledge OHH’s powers to enforce compliance, or reflect the obligation for One Horton Heath, to stop dangerous non-compliant activities.
For contractors/service providers who are conducting major or high works, a pre start kick-off meeting must take place before any work takes place to review and document clearly in the specific CPP/RAMS & RAMS:-
How compliance with the relevant Standards will be achieved, e.g. fall prevention, site logistics and emergencies.
Review the documentation outlining their safe methods of work.
Establishing performance monitoring, supervision and incident reporting protocols and procedure
All contractors/service providers require a briefing before work commences to ensure that all HS&E precautions are in place.
Where a third party contractor is appointed by a land purchaser or tenant to undertake work within a One Horton Heath operational areas, specific requirements should be included in the covenant to ensure all relevant environment, health and safety legislative requirements are adhered to, particularly those addressing risks to the overall operation such as logistics and movement of vehicles, plant and equipment, environmental controls, waste management, fire protection and public protection.
Contractors/service providers on operations where high-risk activities are being undertaken must hold daily coordination meetings to communicate the key activities for the day and any measures required for managing interface issues.
Weekly contractor coordination meetings to plan and coordinate future works (unless the activity is minimal and low risk) must be held with all relevant contractors and OHH to review environment, health and safety performance, Safe Systems of Work (SSOW) and Permit to Work (PtW) compliance. The action points for these meetings must be recorded and implementation verified.
Monthly contractor/service provider Site CDM co-ordination and management meetings shall be held with all relevant contractors/service providers to review environment, health and safety performance (including any contractors/service providers engaged to conduct low risk and low-value works that need to be aware of the high-risk activities potentially impacting their work). The meetings will review compliance, set improvement goals, and plan and coordinate future works. The action items from these meetings must be recorded and implementation verified.
The following items/tasks are considered High-Risk Works, for which the contractor MUST supply their specific Risk Assessment and Method Statement or Safe System of Works (SSOW) and where necessary, apply an additional control via a suitable Permit to Work :
Use of suspended access equipment (e.g., bosun’s chairs, cradles, gondolas, swing stages)
Use of Mobile Elevated Working Platform (MEWP) (e.g., scissor lift, cherry picker)
Installation use and dismantling of Powered Vertical Access Equipment (e.g., Mast Climbers, hoists and building maintenance units – BMU’s)
Temporary Works as defined by BS 5975-2011 Temporary Works / Falseworks Design /Loadings
Demolitions – as per BS 6187-2011Full & Partial
Metal Frame Erection
Concrete Formwork Erection
Cladding and façade work next topavings
Access and work on roofs (other than from fixed scaffolding)
Work within penetrations, risers, shafts and voids (including lift/elevator installation and maintenance)
Structural alterations that require temporary support to prevent collapse
Working on a telecommunications tower, power pole or other installation
Erection use and dismantling of scaffolds (other than to TG20:13 standards)
Any activity (not described above) requiring the use of a fall arrest or fall restraint harness as the primary means of fall protection
Working in, over or next to a road or railway
Creation, access and maintenance of excavations.
Piling, directional boring or drilling
Working on, or near, a pressurised gas or oil distribution mains and consumer piping
Creation, access and maintenance of bridges and related structures including the placement of spans and pre/post-tensioning
Working in, over or next to water where there is a risk of drowning
Use of heavy plant for civil and groundworks (e.g. bobcats, excavators, backhoes, graders, dump trucks, rollers and compactors
Tower crane erection, climbing and dismantling
Use of mobile cranes
Any lifting operations requiring; load slinging, crane management or, lifting over work areas, thoroughfares or public areas
Entry into and work within confined spaces `
Work in an area where there are artificial extremes of temperature .`
Hot works, including welding and grinding
Working on or near a chemical, fuel or refrigerant line
Clearance of UXO
Work requiring strict environmental controls to prevent air, noise, soil or water pollution
Work involving the use, removal, transport or handling of hazardous materials and any dangerous or highly toxic substances
Any other activities not listed above shown as high risk due to the potential to harm workers, the public, property or the environment
Permit to Work (PTW) procedures must be implemented to ensure that regularly encountered high-risk works are effectively controlled. The applicable duration of any permits issued will be dependent on the identified risk but by default should be only for a shift or a day.
Where contractors have their own permit procedure, they may use their own system if the controls detailed in One Horton Heath permits are included and One Horton Heath operatives will monitor compliance.
Where a change in circumstance requires a deviation from an agreed approach to any activity (e.g. resulting from changes to personnel, equipment type or availability, climatic conditions, adjacent activities etc) work crews must not make ad-hoc adjustments and deviate from the agreed method of work without agreement from a competent supervisor and/or person(s) authorised to approve such changes any such changes must be recorded in writing (hand written is acceptable) before commencement.
Adequate numbers of competent supervisors must be in place to monitor the activity and to ensure it is conducted as planned. Supervisors and operatives should provide proof of competence as required by law, and the activity must be managed to ensure both the Standards and legislative requirements are met.
Before commencing work all staff, contractors and service providers must receive an induction.
The induction must include references to OHH’s Vision Zero and include content specific to the current operations including details of any site rules, any environment or safety specific standards, and any emergency procedures. The length of induction should vary according to the role of the organisation or individual, the work to be undertaken, and any previous training and experience relevant to the operation.
Records must be kept of all persons receiving an induction as well as copies of all relevant training and skills cards. These are to be retained on-site for records and follow up inspections.
Operatives or visitors that are either not subject to full induction or do not hold a suitable skills card shall not be allowed to access site areas without a suitable escort, and they should be kept in line of sight at all times
All visitors entering a secure area (e.g. within a delineated construction area, and/or within an area where high-risk activities are occurring) must be given adequate safety instructions when entering the premises (e.g. visitor identification and information cards identifying risks and emergency procedures). If any high-risk activities are taking place visitors must be escorted at all times.
Proof of competence (certificates, licences, training records, or knowledge testing) must be provided for any employees of contractors/service providers conducting on-site .activities.
All supervisors must be fully assessed by their employer as competent for the role in which they are appointed. They must be able to assign work in a manner that ensures it will be performed without incident or injury, be able to recognise and reinforce safe work practices, and constructively correct unsafe work practices.
Regular HS&E briefings and toolbox talks (TBTs) must be conducted at proper intervals, monthly, or on topics relevant to the activities occurring at or around the operation and the attendance to and content of each TBT should be recorded and retained on site for reference and inspection.
Where any work activity or hazard is observed which has the potential to result in an injury, damage to plant or equipment, property or environmental damage; action should be taken by the observer (including a conversation with those conducting the activity and/or those responsible for the area or hazard) to stop the activity or control the situation. Such incidents must be reported immediately to the relevant supervisor or manager.
Details of the observation, as well as any action items, should be recorded and copies forwarded to the OHH HSE team.
Regular performance monitoring must occur to ensure risks are effectively controlled. The following monitoring must be conducted, during which any relevant environment, health & safety observations should be recorded:
Daily checks must be made of all high risk/permitted works by the responsible manager,
A senior member of the operations management team should conduct weekly reviews.
Senior manager not normally on the site should carry out a quarterly review
All incident types must be recorded including Injury Incidents; Property Damage; Environmental Incidents and Near Misses. Initial reports should be made as soon as possible to the OHH Delivery Team – Construction Manager, H&S Lead or Head of Delivery.
After relevant milestones (e.g. design, procurement, key packages, end of the overall construction, fitout, contractual periods, investment cycles etc) relevant lessons learnt related to any successes or challenges should be identified and set forward for future development as part of the ongoing continual improvement process outlined under Section 4.0 of the OHH SMS.
The following information is intended to provide all persons and contractors engaged with the OHH development, what OHH management expect in response to the Duties of Contractors outlined in Regulation 15 and Part 4 of the CDM Regulation 2015
All applicable environment, health & safety legislation and recognised codes, standards and other external requirements shall be complied with at all times. Where there is a difference between these Standards and those required by legislation, recognised codes, standards and other external requirements the higher standard must be applied.
Purpose: To ensure that the risk of falls of people or materials is eliminated or mitigated through the application of the hierarchy of risk control and suitable fall prevention techniques. (Working at Height Regulations, regulation 6 et al + Part 4 of the CDM 2015 Regulations)
The hierarchy of risk control must be applied when designing, planning and conducting all work at height to ensure that the safest practical work methods are employed which, (a), eliminate the need to conduct work at height or (b), effectively prevent the fall of people and materials if the need cannot be reasonably avoided. (BS8560-2012 Code of Practice for Design of Buildings incorporating safe work at height.)
Where work at height cannot be eliminated, the most practical form of collective and passive protection must be installed to provide restraint to prevent persons or materials from falling.
Where collective fall prevention is not reasonably practicable, the use of individual fall arrest systems may be necessary, but these will need to be confirmed as being the only practicable solution via a Design Risk Assessment. All users of these systems must be correctly trained in their safe use. Suitably designed anchorage points, traversing lines and a clearly set out rescue plan for the rescue of suspended persons are to be in place before works commence.
If work at height is required and it is not practical to install physical barriers, or work needs to occur outside the physical barrier, full-body harnesses must be used to provide either fall restraint (preferred) or fall arrest protection. The work must be planned and conducted following the requirements for High-Risk Activities.
Any safety harness in use must be attached to an appropriate anchor/tie-off point(s) utilizing a compatible connector that provides sufficient fall restraint or incorporates a decelerator to provide appropriate fall arrest. All of these components must be fit for purpose, properly inspected, tagged and maintained in line with the manufacturer’s guidelines and be properly used by a competent person. Effective emergency rescue procedures must be in place before works start. (Ref BS 8437-2005 CoP for Selection, Use And Maintenance Of Personal Fall Protection Systems And Equipment For Use In The Workplace)
All structures under construction or demolition (including the construction/demolition floor) from which persons or materials can fall must be effectively protected by physical barriers of sufficient height and strength to prevent people and materials from falling or being blown off the edge of the structure, e.g. screens, scaffolds, guard rails, or cable and netting systems. The means of protection employed must of a suitable form that can be used on the structure, and must be fully designed under the Temporary Works regime to take into account all relevant parameters, such as nature of construction works, structural stability, and weather conditions. (Ref BS EN 13374-2013 Temporary Edge Protection Systems- Product Specification – Test Methods; Part K Building Regulations; EPF Code of Practice 2014.)
Where any works are conducted outside of the perimeter protection, the requirements for working at height High-Risk Activities must be achieved and suitable fall prevention arrangements made.
Access to general work areas or floors should be provided by the permanent solution wherever possible.
Where this is not possible, temporary staircases of adequate width and complete with handrails should be provided. The permanent solution should be no more than two floors behind the progress of the construction. Any temporary structure should be structurally sound and designed for a specific purpose, including the use for temporary loading arising from construction.
Effective measures must be in place for managing the use of all mechanical access systems (for example MEWPs, scissor lifts) used for work at heights to ensure that the work is planned and conducted in accordance with the requirements for High-Risk Activities. Guarding must be fit for purpose. Restraining harnesses must be worn and secured by persons working in boom type 1b and 3b MEWPs.
Suspended access equipment (e.g. bosun’s chairs, cradles, gondolas, swing stages) must only be used where safer means of access are not practical. All persons working on suspended access equipment must wear and use appropriate fall prevention equipment to protect them from any failure of any part of the equipment. Effective rescue procedures must be prepared, practised, and be ready for implementation.
The erection of all-metal frame structures must be designed for, planned and conducted following the requirements for High-Risk Activities.
All metal frame members must be safely lifted following the issued design and the published Lifting
Once in position, framing members should be connected using a Mobile Elevated Work Platform (MEWPs), a boom/scissor lift or another specifically designed safe work platform. Workers must deploy an appropriate harness (adhering to any regulatory or manufacturer's requirements for MEWP’s) to provide secondary fall restraint.
For metal decking works, appropriate collective and passive fall protection netting and perimeter guardrail systems should have been designed and should be in place to provide fall protection before any work commences. To avoid work at height, perimeter guardrails should be fitted to beams at ground level before the beams are lifted into place.
Fall protection netting should always be a minimum of one bay ahead of the area of work except for the last bay when edge protection has already been fitted. Rescue plans, equipment and trained personnel must be available and in place for working with netting. Netting must only be erected by competent riggers (FASET) and should be inspected daily before use.
The erection of all concrete formwork/falsework must be designed for planned and conducted following the requirements for High-Risk Activities and following the Temporary Works procedures (Ref BS 5975-2011 Temporary Works / Falseworks Design /Loadings).
Work at height should be eliminated by design where reasonably practical and all wall and column formwork/falsework, reinforcement cage and shutters should be fabricated at ground level and lifted into position.
If prefabrication is not practical then an appropriate work platform must be used to construct the formwork/falsework. These platforms must have edge protection to both the work face and outer edge or where proprietary shutter systems with in-built concreting platforms are used, stop ends must be provided and adequate protection must be provided to the work face.
Concrete floor slab formwork/falsework systems such as GASS or Sky Dek should be erected from below using scaffolding or temporary platform systems which enable the placement of deck formwork from the floor below and erected only in compliance with the manufacturer’s instructions and training.
Concrete core/bridge pier/formwork/falsework should be designed to ensure it is fully clad to prevent falls of materials. All working platforms must be fully sealed horizontally to prevent falls of items, except for an opening for re-bar placement at the top level.
Work must not be carried out on the decking with exposed edges or unprotected floor openings. Edge protection systems must be installed as part of the frame erection process and should protect the following works, e.g. cladding, bridge beam spans.
Effective measures must be put in place to prevent falls of persons or materials down penetrations, risers and shafts. During design risk reviews, the number and size of penetrations, risers, and shafts must be reviewed and reduced as far as practical. Riskreducing methods such as prefabrication or installation of GRP gratings or similar protective measures must be considered.
All lift/elevator shafts must be constructed in such a way to protect both those carrying out the construction and those below carrying out the lift installation. Safe working platforms must be provided for all those working in lift shafts.
Openings to lift shafts must be fully protected with a secure, full-height system, which prevents unauthorised entry and prevents the risk of falls of people or materials. Lift shaft opening protection must not be removed unless a safe working platform is provided or the lift doors are in place.
Penetrations and risers must either have Fibreglass gratings or structural reinforcement cast in during construction or be fitted with other protection such as metal guard rails or covers, which prevent falls through them. The integrity of such covers or grating must be checked every week as part of the Temporary Works inspection regime.
All floor openings must be protected with securely fixed (screwed or bolted) and marked (e.g.‘Hole below – do not remove’) covers to prevent the fall of materials or persons through them. Covers must be constructed so that they do not present a tripping hazard and must have their designed SWL clearly marked. The design and construction, inspection and maintenance of Service Protection covers and openings are required to be controlled via the Temporary Works procedure.
Protective measures must only be removed when work is actually taking place in or around the opening and effective safety measures must be employed to prevent falls of those working on them. Protective measures must be replaced as soon as practical and be regularly inspected.
All proprietary scaffold towers and platform systems shall be erected and used following the published manufacturer’s recommendations and usage. The mixing of components from different proprietary systems shall not be permitted.
Any variations to standard system use will require designs and permission from the manufacturer, and any calculations and drawings should clearly communicate the working limits and loads allowed and clearly state the requirements to those checking and constructing the scaffold or working platform.
Guard rails, mid-rails, and toe boards must be installed on all open sides of platforms from which people or materials may fall. Where there is a risk of materials falling over toe boards, means of preventing materials falling must be provided, e.g. netting or fencing. Where there is a risk of dusts, liquids, or small objects arising from works on scaffolds creating risks to workers or the public, additional precautions, such as plastic nets/sheeting, must be installed; such measures may require the manufacturer to calculate and approve the application of such screening if it is subject to wind loading etc.
Mobile Tower scaffolds must be fitted with top guardrails, mid rails and toe boards as well as a safe means of internal access to the work platform. Mobile tower scaffolds must also have a covered hatch in the platform to allow safe access and lockable wheels which must be locked to prevent movement at all times when persons are on the scaffold. No person is allowed to remain on a scaffold tower platform while it is being moved.
Working platforms must be closely boarded or planked, which must be free from defects. Any damaged boards or planks, debris, materials and waste must be removed from scaffolds as soon as is practical.
All tower scaffolds / platforms must be stable and secure to prevent movement and collapse. Scaffolds must be plumb, have adequate cross-bracing, sound footings, and be tied into structure where height /height /minimum base ratio is greater than 3:1.when used internally or 2.5:1 externally and in all cases over 9m height.
The erection/ alteration and dismantling of such scaffold towers or platforms must only be carried out by competent persons trained to the Prefabricated Access Suppliers and Manufacturers Association (PASMA) or similar approved standards.
Effective measures must be put in place to ensure the safe erection and use of all scaffolds, temporary works and working platforms (including mobile and tower scaffolds) which ensure that the work is planned and conducted following the requirements for High-Risk Activities, to ensure that work is:-
a) Planned by a competent person to ensure the design and equipment is appropriate for the specific use. ( Use of the NASC TG 20:13 etc is accepted for Standard Scaffolds)
b) Erected, altered or dismantled by competent workers following safe methods of work.
c) Inspected and signed-off by a competent person when first constructed, after any alteration and regularly for the duration, then clearly tagged as safe or unsafe to use.
d) All scaffolds must be fit for intended use, with all structural members free from visible defects;
e) Haki style staircases should be erected for safe access in any position to be maintained for over two weeks - or where tools and materials are to be conveyed by hand.
f) Any stairs / ladders must be progressively installed as the scaffold is erected to provide safe access and egress to the installers/scaffolders.. Rest stations should be provided if required.
All-access/landing points at different levels of the scaffold must be designed to minimise the potential for falls (ladders should extend 1m above level, holes in boards should be as small as practical and/or be protected with hinged covers or guardrails and/or spring-loaded gates).
Where ladders are used for access, safe means of transporting tools and materials up the scaffold must be provided in addition to the ladder access (HAKI or similar staircases)
Climbing up the outside of scaffolds must be prohibited. This would include the screening of the bottom lift by Hears fencing or similar if there is a risk of unauthorised access at any time.
All loading platforms must be assessed before installation and regularly inspected by a competent person. They must be fitted with guard rails on all sides, including on the front/exposed edge, that prevent falls of people or materials. Loading platforms should be arranged so loads can be deposited without removing the guarding or creating a risk of falls, for example by employing gate systems that provide full fall protection. (Tube & Fitting Scaffold standard designs should be in accord with TG20-13 and compliance drawings issued with SSOW)
Ladders
The use of all types of ladder must be minimised as far as reasonably practical by effective work planning and employing safer means of working at height, e.g. by using equipment such as scissor lifts, scaffold towers and podium steps.
Step ladders must only be used for conducting short-duration work (i.e. work lasting less than 15 minutes) or work in confined locations and only if three points of contact can be supported.
Inclined lightweight ladders used on steep roofs to prevent workers from sliding (i.e. ‘cat ladders’) should not be used for roof access.
Effective measures must be in place to manage the use of all ladders to ensure that the work is planned and conducted to address any risks shown and to ensure that ladders are fit for purpose and used correctly, including:
a) Ladders must be structurally sound and safely installed
b) Ladders must be inspected, used and maintained following the manufacturer’s guidelines
c) Ladders must be used only as a means of access (unless three points of contact can be kept during works of less than 15-minute duration)
d) Ladders must be secured top and bottom or footed to prevent movement and extend at least 36 inches (1 metre) above landing or work platform
e) Step ladders must be fully open when in use with the operative standing in a safe position, i.e. three or more rungs below the top
f) Non-conducting ladders must be used near to or on any electrical hazards
g) All ladders must be regularly inspected, and any defective ladders must be immediately removed from the site.
h) Simple inspections should be done and recorded before each use.
Where any works could result in a fall of equipment, materials or tools which could cause injury, measures must be taken to prevent the fall, reduce the distance of the fall and/or ensure nobody could be struck if they do fall including:
Tethers must be used to tie-off any tools or equipment being used outside of or liable to fall outside of any edge protection.
Horizontal catch nets or scaffolded protection fans should also be installed below the immediate work area if over public or site walking routes.
Physical barriers must be installed to prevent materials or equipment falling (for example posts fitted onto trucks during unloading of steel beams, wheel stops installed at slab edges where MEWPs are working)
Exclusion zones must be proved below or around all areas where there is a risk of persons being struck by falling materials (for example below works on the cladding of a building, around mobile crane works and loading/unloading activities, atriums, MEWPs)
Exclusion zones must be of adequate size taking into account the risks including the potential arc of fall, deflections, and bounce distances), be delineated by physical barriers and have clear signage prohibiting unauthorised entry. Hazard warning tape should only be used as a last resort to provide this barrier. The integrity of any exclusion zones must be regularly checked.
For areas where there is a risk of materials falling into them, but access is still regularly needed, protected walkways must be put in place. This includes appropriate protection to access any areas off-site such as toilets or welfare areas.
Rubbish chutes and skips/dumpsters used for rubbish disposal (from upper floors) must be located and/or fenced off to prevent danger to the public and workers.
All materials that could be blown or swept off of roofs, exposed floors or scaffolds must be removed or effectively secured when they are not being used, when work has ceased and/or when high winds are predicted.
The wind speed should be monitored while work activity is underway, along with the forecast wind condition and any weather alerts issued to provide advance warning of high winds.
Purpose: To ensure that hazards related to the movement of people and vehicles/plant and poor housekeeping are effectively identified and managed. (Ref All Part 4 of the CDM 2015 Regulations + HSG 144 Safe use of Vehicles on Construction Sites & HSG 150 Health & Safety In Construction)
All applicable environment, health & safety legislation and recognised codes, standards and other external requirements must be complied with at all times. Where there is a difference between these Standards and those required by legislation recognised codes, standards and other external requirements the higher standard must be applied.
Access to the site must be effectively controlled (including during shutdown periods) to prevent unauthorised persons entering and all persons (workers and visitors) must be recorded entering and leaving the location for accounting purposes in emergency situations. Total number of persons attending per month should be noted and forwarded to OHH for record purposes.
Where a site is extensive in length (e.g. road projects) or where works are discrete short-term activities as part of a multi-site operation where fixed site access control points as required above are not reasonably practical, a suitable method of registering persons working on the operation must be developed and maintained and attendance figures recorded and issued as before.
All operations where construction and particularly high risk activities take place must prevent any unauthorised access or danger to the public by providing suitable physical barriers to prevent members of the public gaining access to the works. For sites that are active for more than one day this barrier should be a solid section perimeter fence. Entrances/exits must be managed to prevent unauthorised access, be clearly signed and display appropriate site rules. All hoardings, fencing and signage must be of solid construction and regularly maintained to prevent risk to the public and workers.
Where a site is extensive in length (e.g. road construction or upgrade projects) and fencing the entire site perimeter is not reasonably practical, the extent and location of any signage, fencing and physical barriers must be the result of an assessment of the level of risk present, ensuring the public is kept from readily accessing or interfacing with high risk activities.
For locations active for less than one day, or when short-term activity (less than one day) needs to take place outside the fenced site boundary, a suitable physical barrier must still be erected to prevent danger to the public and unauthorised access, which should be installed with bracing and fixings following the manufacturer’s instructions.
All practical means must be employed to protect the public from any hazards arising from our undertakings, including falling materials and the movement of vehicles into/out of sites.
Protection must be provided to all public areas, that could be negatively affected by site activities.
Effective measures must be taken to protect the public, especially during lifting and vehicle movements.
Public walkways and roadways must be kept clean and free of construction-related hazards or materials at all times.
Safe alternative pathways must be proved whenever public access ways are to be blocked off due to construction activities.
Effective lighting, dust, noise and vibration control measures must be employed. Checks must be made to ensure loads are adequately secured and covered before leaving the site.
Site lighting must be arranged so it does not negatively affect the public and in particular, does not adversely impact drivers.
Any changes to vehicle traffic flow on public roads must be managed so they do not pose a risk to the public.
Controls must be in place to eliminate the risk of falls of materials onto active roads or train lines.
All locations must assess the risks presented by the movement of pedestrians, materials and vehicles around or next to the site and implement appropriate safety measures to eliminate or minimise these risks. These assessments should be laid out and control set out clearly in the Traffic / Site Logistics section of the CPP/RAMS or the SSOW for short term works.
Separate site entrance/exit points for pedestrians and vehicles must be provided to keep them physically apart where there is a likely risk of harm.
Barriers, cones, guard rails, etc. must be in place to form pedestrian routes around the site, and where vehicles operate near these should be of suitably robust construction (Titan kerbs or similar). For any circumstances where works interface with high volume traffic, crash barriers must be in place to protect pedestrians.
Pedestrian crossing points across vehicle routes must be in place and signed, lit if necessary for access to main work areas, where required fences and barricades must be in place to inform drivers and pedestrians of hazards and precautions. (Ref CDM 2015 Pt 4 Reg 27, 28,)
Parking areas must be provided that allows separation of different vehicle types. Where parking for private vehicles is provided it must be separated from trucks and heavy plant and equipment.
Detailed delivery procedures and storage arrangements must be in place, including clearly defined loading and unloading areas (which must be separated from vehicle access and pedestrian routes), crane pick areas, distribution routes and methods, and designated storage areas. Any deviation from these procedures, including changing the designated loading and unloading areas, must be planned and conducted following the requirements for High Risk Activities with any changes to loading\unloading areas or protocols adequately communicated and signposted.
Controls must be in place to ensure vehicles are appropriately braked and/or chocked and/or stabilised if appropriate (dependent upon the risk), before any unloading or loading occurs.
Controls to manage reversing must be in place. Reversing should be eliminated as far as possible by the use of one-way systems. Where reversing needs to occur suitable controls include the use of pedestrian exclusion zones, traffic signallers to direct drivers and visibility aids fitted on vehicles, e.g. reversing sensors, mirror systems and Closed Circuit Television (CCTV);
Trained traffic signallers must be used to control vehicle movements in confined or congested areas.
High visibility reflective clothing must be supplied for all persons working adjacent to vehicles and traffic routes.
Where work is undertaken next to active site roads, or similar, measures must be in place to protect workers from impacts with moving vehicles, or associated debris. Where a site is of extensive length (e.g. road construction or upgrade projects) physical barriers should be in place to segregate workers from road traffic. Where this is not reasonably practical, traffic calming measures, hazard signage, and demarcation lines and barriers must be in place to assist in managing the risks to both workers and the public.
All vehicle operators must be competent (certified/licensed) to work the vehicles they are assigned to, and be briefed on their use and particular hazards associated with the site. Checks must be made to ensure the competence of drivers concerning the specific vehicle, the site conditions and the work to be completed, particularly vehicles such as HIABs or Moffit equipped vehicles..
All operators must follow any local road rules, manufacturer instructions and site rules. Also, during any use of vehicles on-site, seatbelts where fitted, must be worn, and operator mobile phones (or other personal electronic equipment such as music players) must be turned off.
Vehicle operators are Safety-Critical operatives, as such, they must be regularly checked for any potential health issues, drink or drug issues that may adversely affect their ability to operate the equipment correctly.
Maintenance of Tools and Equipment
(Ref Provision & Use of Work Equipment Regulations, Lifting Operations and Lifting Equipment Regulations)
An effective inspection, testing and preventative maintenance regime must be implemented covering all tools, equipment and vehicles used. It must include a process to record and remedy any identified deficiencies, identify uniquely the specific tools and equipment and should align with any manufacturers’ guidelines. All inspection, testing and maintenance must be planned and conducted following the requirements for High Risk Activities. The following areas must be covered:
a) Fire protection systems, including fire detection and alarm systems and fire fighting and suppression equipment
b) Electrical system and lighting
c) Scaffolds (Including mobile and tower scaffolds), temporary works and working platforms
d) Ladders
e) Work tools and equipment (For example, power tools, grinders etc)
f) Mechanical access systems (For example MEWPs, scissor lifts)
g) Excavators & Dumpers, Tele Handlers, Fork Lifts etc.
Operators must carry out and record their daily pre-use inspection of all Non Road Mobile Machinery (NRMM), in addition, there are regular inspections to be carried out in line with manufacturers and legislative requirements that must be recorded and retained on site.
All light vehicles designed for public road use, such as cars, vans, minibuses and utility vehicles, used for work activities must comply with local legislation and must only be used for the purpose for which they were designed. They should also be serviced regularly in-line with manufacturer guidelines.
Housekeeping
Housekeeping must be effectively managed to keep a clean and tidy work site. (Ref CDM 2015 Reg 18 – HSG 150 Health & Safety In Construction)
All main access ways, emergency routes and passageways must be lit where necessary, marked and kept free from obstructions changes in level and debris likely to reduce the risk of trips and slips. Walkways should be formed of a firm even surfaced compacted material, free from rubble over 50mm diameter or other items liable to cause twisting of ankles or trip hazards
Temporary electrical supply cables must be located so as not to present tripping hazards (off the floor, overhead or away from access routes).
All materials must be safely stacked (i.e. stack is on solid ground, is stable and not overstacked), away from fences and hoardings, and located to minimize re-handling and transport distances. Materials must be stacked in a manner that does not require work at height to manage the stack (for example to attach lifting equipment). Generally, items should such as bricks must not be stacked more than 2 packs high
COSHH materials, Combustibles, flammables and other dangerous materials must be stored safely in appropriately fire-rated and ventilated storage cabinets and be identified clearly e.g. flammables.
Only the smallest amount of such materials (enough for one shift) should be taken on to the site.
Gas bottles should be stored in a shaded and secured ventilated cage 10m from any accommodation units, stocks should be kept to the minimum at all times. Empty bottles should be kept separately in a shaded secure area.
For quantities of flammable and COSHH materials over 50 litres there should be a notice displaying relevant contents and locations made available as part of the Emergency Procedures for the Emergency services.
Risks of cuts and punctures from sharp objects must be assessed and controlled, e.g. needle handing, safety knives, gloves, removal of protruding nails, protection or curving of reinforcement bars, use of safety glass, etc.
Suitable Signs in accordance with Safety signs and signals. The Health and Safety Regulations 1996 must be posted where necessary to supply clear instructions – No Smoking, No Entry, Personal Protective Equipment (PPE) etc.
A sufficient number of suitable waste receptacles must be provided, including receptacles for hazardous and recyclable materials. Processes for the regular collection of waste must be implemented.
Purpose: To ensure that competent persons are appointed to plan work and implement controls for any excavation of material and that any plant and equipment used is fit for purpose, and properly used .(Ref HSG 150 Health & Safety In Construction –
All applicable environment, health & safety legislation and recognised codes, standards and other external requirements must be complied with at all times. Where there is a difference between these OHH CoCP Standards and those required by legislation, recognised codes, standards and other external requirements the higher standard must be applied.
All ground and civil works must be designed to eliminate risk so far as reasonably practicable, assessed and the safest practical methods employed to carry them out with all work being planned and conducted following the requirements for High-Risk Activities.
Before any work commences an appropriate Permit to Work must be in place approved by persons with the appropriate limits of authority. (Ref Part 4 CDM 2015 Regulation 22,24)
Existing drawings and/or a CAT scanner and any other suitable tool must be used to find and mark underground services (electricity, gas, etc.) before works commence. Where any uncertainty exists regarding the location of underground services hand or vacuum digging must be used to identify the services.
Extracts of the relevant UXO surveys of the site should be included when assessing risk.
All works must be regularly inspected by a competent person, with the frequency determined by risk assessment but must be weekly at least unless otherwise assessed. Added inspections must be made after every rainstorm or other event which could impact on the stability or any other hazard associated with the groundworks.
Excavations must be shored, step benched, or battered back/sloped to a safe angle as determined by the relevant engineer in the excavation design process. Adjacent structures, roads and sidewalks must be supported or protected where necessary to prevent collapse. (Ref CDM 2015 Reg 19)
Materials and equipment must be placed at a safe distance from the edge of excavations and normally not less than 1.5 x the depth away from the excavation.
Adequate signage, wheel scotches, barriers and lighting must be supplied to prevent falls into excavations, especially of the plant working on those excavations and of vehicles or plant from adjacent thoroughfares.
Temporary stairs (Haki or Titan steps etc.) should be installed to provide safe access into excavations where appropriate and should be at 9-metre intervals or less.
Water ingress into excavations must be controlled to ensure stability and where water is present in deep excavations and tunnels a suitable dewatering programme must be in place.
Appropriate ventilation, fresh air systems and extraction must be supplied for all tunnelling or other ground and civil works where air quality may be subject to contamination by fumes, gases, vehicle exhausts, depletion or replacement of Oxygen. Equipment used for these works should be chosen to minimise the exhaust produced.
The requirements of Confined Spaces Regulations will also need to be met where applicable.
Works around Water
Where water is present suitable measures must be taken to prevent drowning. When working next to the water, personnel should wear life preservers/jackets. Rescue equipment, such as a safety boat and lifebuoys with lifelines attached, must be kept ready for immediate use. (Ref CDM2015 Part 4 Reg 26)
Spoil Management
Any material removed during excavation or tunnelling, including any waste material, topsoil for stockpiling or mined ore, must be safely placed and stored away from the areas of the excavation and located to avoid potential overloading excavation sides and to prevent potential wash or runoff from the heaps.. Ref CDM2015 Part 4 Reg
Safe Use of Plant
Effective measures must be in place for managing the use of all mobile plant used for ground and civil works, including bobcats, excavators, backhoes, graders, scrapers, bulldozers, dump trucks, rollers and compactors, to ensure that the work is planned and conducted in accordance with the requirements for High-Risk Activities.
All plant must only be used for the purpose for which it was designed and in-line with manufacturer instructions. Ref Part 4 CDM 2015 Reg 28 + PUWER Regulation 1998 + LOLER Regulations 1998)
All plant operators must be competent (certified/licensed) to operate the plant they are assigned to and checks must be made to ensure the competence of drivers concerning the specific vehicle, the site conditions and the work to be completed. Plant operators are SafetyCritical personnel so should be subject to routine health and drug/alcohol testing.
All mobile plant must be fitted with protection where there is a risk of rollover, tip over or falling objects (e.g.loading/unloading, work on stockpiles or steep inclines, work below other material or activities) or where the manufacturer’s specifications require it.
Seat belts must also be fitted and worn at all times to protect the driver/operator in the event the vehicle/plant rolls over. In the event of a rollover, tip over or falling objects damage, the protection must be recertified or replaced before further use.
A safe means of access should be in place as per the manufacturer's design for plant cab (like built-in ladders, steps, stairs etc.) to eliminate the risk of falls from height.
All mobile plant must be equipped with appropriate visual and audible warning equipment, such as flashing lights and horns to ensure local persons are aware of the vehicles moving.. The plant should be fitted with visible warning lights for safe movement (amber) and to indicate the use of a seat belt (green) as well as audible alarms for reversing activities.
All operator mobile phones (or other personal electronic equipment such as music players) must be turned off when plant is in use.
Minimum clearance distances for overhead cables must be clearly identified with controls in place to prevent plant from coming into contact with these cables.
Drivers of the mobile plant should be provided with competent signallers as necessary.
All plant must be appropriately braked and/or chocked and/or stabilised when parked and or receiving loads from other plant. In the case of dumpers being loaded, the operator must park the machine with the hand brake fully on, engine off, and stand aside safely while the machine is loaded.
Any access ramps used by the plant must be of appropriate construction and strength for the plant using it and must be of sufficient width and appropriate slope to allow the plant to use the ramp safely.
Pedestrian exclusion zones must be established and maintained around operating plant where there is a risk of workers being struck. The specific exclusion zones for stationary but operating plant (for example an excavator with its bucket in use or a crusher etc) must be identified for each type of plant and an appropriate exclusion zone, preferably a physical barrier, put in place.
On large open or long-haul sites the use of personal electronic proximity alarm systems should be considered.
All items of plant must be fitted with appropriate guarding or physical barriers to prevent unintended access and contact with any moving parts.
An effective inspection, testing and preventative maintenance regime must be implemented covering all plant and equipment used for groundworks. It must include a process to record and remedy any identified deficiencies,
All tools and equipment should be uniquely identified (tagged) and should align with the manufacturers’ guidelines for test and inspection criteria. All inspection, testing and maintenance must be planned and conducted following the requirements for High-Risk Activities. (Ref Part 4 of CDM 2015 Regs PUWER & LOLER Regulations 1998)
Purpose: To ensure that competent persons are appointed to plan and manage risks associated with any lifting or slinging and that all equipment is verified as safe for use.
All applicable environment, health & safety legislation and recognised codes, standards and other external requirements must be complied with at all times. Where there is a difference between these Standards and those required by legislation recognised codes, standards and other external requirements the higher standard must be applied. (Ref Lifting Operations and Lifting Equipment Regulations 1998 (LOLER Regulations) and BS 7121))
Cranes and other lifting equipment (including excavators and telehandlers used for lifting) must be structurally sound, fit for purpose, fitted with appropriate safety devices (such as safe load indicators, overload alarms, earthing, anemometers, and warning lights) and marked with a means of identification and safe working load.
All lifting equipment tackle, including rubbish removal, skips or bins, hessian bags, mortar tubs etc , must be structurally sound, fit for purpose and designed for lifting (with lifting points and safe working load identified).
Effective measures must be taken to prevent cranes from coming into contact with power lines, other cranes or structures. Automated anti-collision systems should be used, especially when multiple tower cranes are in use.
A designated Crane / Lifting Coordinator shall be appointed where more than one lifting operation is to take place at the same time in the same location. This applies to lifting by crane or by excavators working adjacent. There must be one single coordinating mind behind any lifting operations in these scenarios to prevent potential conflicts from occurring
All tower or mobile crane erection, climbing and dismantling must be planned and conducted following the requirements for High-Risk Activities. A working area exclusion zone must be established for all operations.
Erection, climbing and dismantling of tower cranes should where possible be performed outside of working hours. Before any work commences an appropriate Permit to Work must be in place approved by persons with the appropriate limits of authority.
The need to exclude people working under a crane lift path must be considered in the lifting plan. Where reasonably practical, an exclusion zone must be established. Where full exclusion is not practicable the use of alarm systems, such as whistles used by the slingers or electronic proximity alarms to alert others of moving loads should be considered.
A sufficient number of competent persons must be provided and appointed to develop an overall lifting plan and oversee all lifting activities. (CPCS Appointed Person (Lifting))
All crane or other lifting equipment operators and slingers must be competent and certified to perform their role.(CPCS certified)
Work involving cranes and lifting equipment such as Excavators, Tele-handlers or HIABs must be planned and conducted following the requirements for High Risk Activities and the LOLER regulations
Clear communications must be provided and maintained between operators and signallers.
Cranes and other lifting equipment must only be used within their safe operating limits, e.g. loadings and weather conditions, and must be appropriately stabilised before any lifting commences.
Ensure that ground conditions are suitable and capable of accepting the loads that will be applied by the crane while working.
A competent person, trained as a banks man/slinger (CPCS) will use lifting equipment as specified in the lift plan, to safely sling all loads a detailed slinging diagram is required as part of the overall Lift Plan to be produced by the AP(L)
All lifting gear, including rubbish removal skips, mortar skips etc, must not be filled above their top edge and must be covered to prevent loose material from falling out.
Daily lifting coordination meetings must be held where more than one crane is in use. This should be lead by the designated Lifting Coordinator.
All Lift Plans must be submitted for review and information by EBC Appointed Person (H&S Lead) before work commences.
An effective inspection, testing and preventative maintenance regime must be implemented covering all cranes and lifting equipment (including, hoists, chains, hooks, slings, etc). It must include a process to record and remedy any identified deficiencies, as well as to uniquely identify (tag) tools and equipment.
Inspection periods should be readily identifiable (colour coded) and should align with any manufacturers’ guidelines. All inspection, testing and maintenance must be planned and conducted following the requirements for High-Risk Activities.
All cranes and lifting equipment must be examined and certified before first use, inspected at least monthly, and recertified when used for lifting personnel at 6monthly intervals as safe to use by a competent person with records available on site.
Purpose: To ensure that all electrical installations and equipment are fit for purpose, correctly installed, protected to prevent electrical shock or fires, appropriately maintained and only worked on by competent persons. (Ref 7375-2010 Distribution of Electricity on Construction & Demolition Sites – Code of Practice. ~ BS761 Wiring Regulations 18th Edition )
All applicable environment, health & safety legislation and recognised codes, standards and other external requirements must be complied with at all times. Where there is a difference between these Standards and those required by legislation recognised codes, standards and other external requirements the higher standard must be applied.
Temporary Supply (BS 761 18th Ed + BS7909 Temporary Electrical Installations))
Electrical supply panels and distribution equipment must be adequate and sufficient in number, located in suitable work areas to minimise trailing cables, secured to prevent unauthorised access.
All electrical circuits, including mobile generator sources, must be protected by an Earth Leakage Circuit Breaker (ELCB), Residual Current Device (RCD) or a Ground Fault Circuit Interrupter (GFCI), fitted at the source.
All electrical supply boards, cables, cords plugs and sockets must be safe by design for construction use, appropriate for the location where it is to be used and located or protected to avoid physical damage by vehicles, water, etc., e.g. by elevation or coverings.
A comprehensive inspection, testing and preventive maintenance regime must be implemented covering all temporary electrical supplies, including supply panels, circuits, cables, cords, plugs and sockets. It must include a process to record and remedy any identified deficiencies and should align with any manufacturers’ guidelines. All inspection, testing and maintenance work must be planned and conducted to address any risks identified
Work on Electrical Systems(BS761 Wiring Regulations 18th Edition)
Works on live electrical systems must not be undertaken, except where deemed absolutely necessary by a competent person for fault-finding, testing/commissioning work or where the electrical supply cannot be interrupted, such as those for hospital life support systems or critical utilities.
Any live work on critical utilities such as distribution and/or transmission networks must only be undertaken as directed by the utility provider with any directive to undertake such activities supported by documented safe systems of work in line with the requirements of legislated practices
Where work on electrical systems is carried out, effective precautions must be taken to eliminate electric shock and work must be planned and conducted to address any risks identified.
Prior to any work commencing, all work on electrical systems must have a Permit to Work in place approved by competent persons with the appropriate limits of authority.
A Lock-Out Tag-Out (LOTO) procedure must be followed, including meeting all requirements of an electrical isolation/access permit issued by a utility provider where work on distribution or transmission networks is required before any work is conducted. This is required to ensure:-
a) All energy sources supplying the electrical systems/equipment/tools are identified
b) All these energy sources are de-energised or isolated
c) The energy source is correctly locked out and tagged
d) The system/equipment/tool is properly tested to ensure the isolation is effective
The risk of electrical fires must be assessed and appropriate precautions put in place, e.g. adequate numbers of appropriate extinguishers provided.
People and Tools
Any work on electrical circuits, equipment and tools must only be carried out by a competent person.
All electrical tools and equipment operating from the site supply must be regularly inspected, tested and tagged i.e. marked as safe to use with the date of inspection and the initials of the inspector..
Lighting
Lighting installations must avoid the risks of electric shock, burns and glare. The use of Festoons and Halogen lighting should be avoided to prevent potential from electrical shocks and burns.
Task Lighting -- Adequate lighting which matches the demands of the job and the location must be provided to supplement natural light to ensure works can be conducted safely at all times and locations.
Safety Lighting – Where light levels are likely to fall below 25 lux (dull night time lit corridor) in the event of a power failure.
Areas such as enclosed rooms, long corridors, staircases, basements, roof spaces, should have lighting systems with an emergency back-up system to facilitate safe evacuation, this should provide emergency lighting for a minimum of 30 minutes along access/egress routes.
Portable equipment, hand power tools, battery charging units which are to be used on the site areas are to be visually inspected before use and have a recorded visual inspection carried out weekly and a full Portable Appliance Test (PAT) (where appropriate), carried out and recorded every three months and /or as indicated in HSG 107 Maintaining portable electrical equipment
Records of all routine inspections and certification are to be retained on-site for inspection by the client.
Purpose: To ensure that any health risks are assessed, and effective control measures implemented, along with appropriate welfare facilities, to prevent injury and ill health, and to create a better working environment. (Ref Health & Safety at Work Act 1974 ~ Management of Health & Safety at Work Regulation 1999 as amended ~ Workplace (Health Safety & Welfare)Regulations 1992 as amended ~ Construction (Design& Management)Regulations 2015 ~ et al)
All applicable environment, health & safety legislation and recognised codes, standards and other external requirements must be complied with at all times. Where there is a difference between these CoCPStandards and those required by legislation recognised codes, standards and other external requirements the higher standard must be applied.
Substances Hazardous to Health (COSHH)
Hazardous substances must not be incorporated into any designs and must not be used in any activities undertaken. Also, any procured equipment, fittings, fixtures and furnishings must not incorporate these substances.
If any pre-existing hazardous substances are found to be present in any structures or on the site, the substance must be tested and identified to allow a risk assessment to be undertaken to assess the best strategies to manage the risks posed. This may include removal, encapsulation or ongoing monitoring and control. Any areas where hazardous substances are present must be clearly signed with the required precautions clearly displayed.
Any work in the vicinity of hazardous substances must be planned and conducted following the requirements for High-Risk Activities.
All workers must be competent and provided with the appropriate personal protective equipment (PPE) assessed as appropriate for the substances in use. Before commencing any work, a Permit to Work must be in place approved by persons with the appropriate limits of authority. (Ref Control of Substances Hazardous to Health Regs 2002 (as amended))
The risks associated with the use of other substances must be assessed by reference to Materials Safety Data Sheets (MSDS). A materials’, use and location-specific assessment must then be made to ensure the safest practical methods are selected and the recommended protective equipment provided as necessary, e.g. respirators and chemicalresistant clothing. (Ref Control of Substances Hazardous to Health Regs 2002 (as amended))
If hazardous waste is to be handled, e.g. healthcare facilities, water treatment works etc, safe and secure collection, storage and disposal facilities must be available. Also, effective processes must be implemented for the regular collection and removal of hazardous waste.
Processes Hazardous to Health (Occupational Health)
COSHH - Areas and activities involving use and contact with hazardous substances, including all dusts, fumes, vapours, solids, liquids or gels1 must be identified, fully assessed and appropriate measures put in place to reduce the risk by elimination, substitution, attenuation or isolation and personal protection. Fully detailed RAMS for the substance will include copies of the MSDS for the materials in question AND a full COSHH assessment on the materials to be used. The assessment must be related to the location, volumes, method of use, logistics, required
1 Refer HSE HE40 for appropriate Workplace Exposure Limits (WEL’s)
controls, and any relevant Workplace Exposure Limits (WEL) limits that are to be observed (Ref Control of Substances Hazardous to Health Regs 2002 (as amended) EH 40/2005 Workplace Exposure Limits https://www.hse.gov.uk/pubns/books/eh40.htm )
Noise. Where noisy operations are reasonably foreseeable, a review shall be undertaken to see if a less noisy method of work is available before work commences. Where the noisy works cannot be fully mitigated by design or change of methodology, then the following exposure levels need to be observed and adequate controls and monitoring put in place.
This may include the provision of Noise Control Zones and exclusion zones, Acoustic Barriers or cabinets and the provision of Noise meters and routine sampling. Provision of personal dosimeters, recording of individual exposures. Where the exposure of an employee to noise varies markedly from day to day, an employer may use weekly personal noise exposure in place of daily personal noise exposure for compliance with these Regulations
Note that the requirements in the Regulations relating to the assessment of risk and exposure, and actions to reduce risk and exposure, as well as the levels at which they are required to be taken, does not allow you to take account of the reduction of noise provided by wearing hearing protection. (Ref The Control of Noise at Work Regulations 2005)
The lower Noise Exposure Action level
Areas of works producing up to 80dB(A) for over 6 hours on a daily, weekly basis, or a peak sound pressure of 135dB (C) should be signed and hearing protection made available for use. Exposures to 80dB(A) should be recorded for each individual.
The Exposure LIMIT values
Areas where activities are unavoidably producing noise levels above a daily or weekly personal noise exposure of 85 dB (A-weighted); and (b) a peak sound pressure of 140 dB (Cweighted) must have noise warning signs posted, stating that hearing protection must be worn and appropriate hearing protection must be provided to and worn by, all those entering those areas.
Typical Examples where RAMS will be required.
Use of equipment and plant generating high levels of vibration can lead to the chronic condition of Vibration White Finger. This results from damage to the capillary blood vessels in the fingertips. Hand Arm Vibration Syndrome (HAVS) causes changes in the sensation of the fingers which can lead to permanent numbness of fingers, muscle weakness, and Carpal Tunnel Syndrome (CTS) causes pain, numbness, and tingling in the hand and arm. The condition occurs when one of the major nerves to the hand — the median nerve — is
squeezed or compressed as it travels through the wrist. All three can be incapacitating lifechanging syndromes in severe cases.
Similarly, to noise, the greatest opportunity to reduce the risk from vibration exposure will occur at the design stage by elimination, reduction, the substitution of need.
Where such changes have not, or cannot be reasonably practicably made, then a Risk Assessment is required to control and manage any exposure. There are several options available for controlling the levels of exposure but all of them will require the total exposure of the individual to be recorded over the exposure duration – even if that is only intermittently each day.
A common method of measuring and managing exposure is to use the HSE points exposure tables available at the following link
https://www.hse.gov.uk/vibration/hav/advicetoemployers/assessrisks.htm
RAMS reviews should be undertaken to select methods of working or items of equipment that avoid or reduce such levels as low as possible.
The regulations introduce: -
Exposure action value of 2.5 m/s2 A(8) at which level employers should introduce technical and organisational measures to control and reduce exposure.
Exposure limit value of 5.0 m/s2 A(8) represents a high risk above which employees should not be exposed.(Ref The Control of Vibration at Work Regulations 2005).
Manual handling injuries can have serious implications for the employer and the person who has been injured. They can occur almost anywhere in the workplace and heavy manual labour, awkward postures, repetitive movements of arms, legs and back or previous/existing injury can increase the risk.
For any lifting activity: - Always take into account T.I.L.E (Task, Individual, Load, Environment.) as well as:-
a) individual capability
b) the nature of the load
c) environmental conditions
d) training
e) work organisation
a) Reduce the amount of twisting, stooping and reaching
b) Avoid lifting from floor level or above shoulder height, especially heavy loads
c) Adjust storage areas to minimise the need to carry out such movements
d) Consider how you can minimise carrying distances
e) Assess the weight to be carried and whether the worker can move the load safely or needs any help – maybe the load can be broken down to smaller, lighter components.
f) If you must use manual lifting and need to utilise multiple personnel, make sure that one person is designated as the lift leader who is tasked with coordination all efforts.
Consider whether you can use a lifting aid, such as a forklift truck, electric or handpowered hoist, or a conveyor
Think about storage as part of the delivery process – maybe heavy items could be delivered directly, or closer, to the storage area
Reduce carrying distances where possible
There are some simple things to do before and during the lift/carry:
a) Remove obstructions from the route.
b) For a long lift, plan to rest the load midway on a table or bench to change grip.
c) Keep the load close to the waist. The load should be kept close to the body for as long as possible while lifting.
d) Keep the heaviest side of the load next to the body.
e) Adopt a stable position and make sure your feet are apart, with one leg slightly forward to maintain balance
f) Think before lifting/handling. Plan the lift. Can handling aids be used? Where is the load going to be placed? Will help be needed with the load? Remove obstructions such as discarded wrapping materials. For a long lift, consider resting the load midway on a table or bench to change grip.
g) Adopt a stable position. The feet should be apart with one leg slightly forward to maintain balance (alongside the load, if it is on the ground). Be prepared to move your feet during the lift to maintain your stability. Avoid tight clothing or unsuitable footwear, which may make this difficult.
h) Get a good hold. Where possible, the load should be hugged as close as possible to the body. This may be better than gripping it tightly with hands only.
i) Start in a good posture. At the start of the lift, slight bending of the back, hips and knees is preferable to fully flexing the back (stooping) or fully flexing the hips and knees (squatting).
j) Don’t flex the back any further while lifting. This can happen if the legs begin to straighten before starting to raise the load.
k) Keep the load close to the waist. Keep the load close to the body for as long as possible while lifting. Keep the heaviest side of the load next to the body. If a close approach to the load is not possible, try to slide it towards the body before attempting to lift it.
l) Avoid twisting the back or leaning sideways, especially while the back is bent. Shoulders should be kept level and facing in the same direction as the hips. Turning by moving the feet is better than twisting and lifting at the same time.
m) Keep the head up when handling. Look ahead, not down at the load, once it has been held securely.
n) Move smoothly. The load should not be jerked or snatched as this can make it harder to keep control and can increase the risk of injury.
o) Don’t lift or handle more than can be easily managed. There is a difference between what people can lift and what they can safely lift. If in doubt, seek advice or get help.
p) Put down, then adjust. If precise positioning of the load is necessary, put it down first, then slide it into the desired position
(Ref,The Manual Handling Operations Regulations 1992 (as amended))
Any ‘safe areas’ (Green Zones or Routes) where PPE is not required must be identified and clearly signed.
Outside of these ‘safe areas,’ all persons (including workers and visitors) must wear a hard hat, safety boots, eye protection, gloves and high visibility clothing.
Also, any other items of task-specific PPE must be provided and worn if the need is identified by risk assessment, e.g. hearing protection in areas where noise levels exceed 85 db(A).
PPE requirements must be identified and clearly signed at all site entrances, at any exits from ‘safe areas’, and at the entrance to any area where other items of task specific PPE are required.
All PPE must fit the individual (particularly for respiratory protection, which must be face fit tested), be worn properly, maintained in good condition and the individual must be appropriately instructed or trained in its correct use.
Adequate supplies of PPE must be available to protect both workers and visitors, along with appropriate storage for that PPE.
Key personnel should be easily distinguished by visual markings, e.g. specific colours of helmets (black hats for supervisors) or clothing for supervisors, slingers, first aiders, etc. and must meet any regulatory requirements.
Any workers required to work outside must be provided with adequate equipment to provide protection from the elements, especially the sun and extremes of temperature.
Examples include sunscreen, hats and long-sleeved shirts with a collar for sun protection, and warm clothing for winter work in cold climates.
OHH require that the following will be required as the minimum level of PPE across the development
OHH shall require a site-wide minimum for normal site works of: Saturn Yellow Hi Vis Waistcoats to ISO EN 20471 (Class 2:2)
Head Protection to EN 397. [BLACK for Supervisors & Manager]
Safety Footwear to EN ISO 20346 S1 (Rigger Boots will not be permitted)
Hand Protection to EN 388 grade 4:4:4:4
Light Eye Protection to EN166 Class 1
For Highway working the following will be required as the MINIMUM; Saturn Yellow Hi Vis Sleeved jackets with Trousers to ISO EN 20471 (Class 3)
Head Protection to EN 397. [BLACK for Supervisors & Manager]
Safety Footwear to EN ISO 20345 P (Rigger Boots will not be permitted)
Hand Protection to EN 388 grade 4:4:4:4
Light Eye Protection to EN166 Class 1
In all working areas, at all times, a minimum of short sleeved shirts and long trousers are to be worn. SHORTS, VESTS, and BARE top working is not permitted on the development.
There are legal definitions of what constitutes a Confine Space under Regulation 1(2) of the Confined Spaces Regulations 1997. However, this must be tempered by the use of the term “Confined Space” in general.
In addition to the places referred to in regulation 1(2), the expression ‘confined space’ may also refer to the following locations and other similar places, but only where there is also the presence of or a reasonably foreseeable risk of one of the specified risks to the health and safety of those working in the space:
(a) ducts, culverts, tunnels, boreholes, bored piles, manholes, shafts, excavations and trenches, sumps, inspection and under-machine pits, cofferdams.
(b) freight containers, ballast tanks, ships’ engine rooms and cargo holds.
(c) buildings, building voids.
(d) some enclosed rooms (particularly plant rooms) and compartments within them;
(e) enclosures for asbestos removal.
(f) areas used for storage of materials that are likely to oxidise (such as storerooms for steel chains or wood pellet hopper tanks);
(g) unventilated or inadequately ventilated rooms and silos.
(h) structures that become confined spaces during fabrication or manufacture; and
(i) interiors of machines, plant, or vehicles.
This is not an exhaustive list and there may be other types of confined space.
The regulations only apply in full where spaces such as those above also contain or can create a “specified risk”. “Specified Risk” means a risk of —
(a) serious injury to any person at work arising from a fire or explosion;
(b) without prejudice to paragraph (a) —
(i) the loss of consciousness of any person at work arising from an increase in body temperature;
(ii) the loss of consciousness or asphyxiation of any person at work arising from gas, fume, vapour or the lack of oxygen;
(c) the drowning of any person at work arising from an increase in the level of liquid; or
(d) the asphyxiation of any person at work arising from a free flowing solid or the inability to reach a respirable environment due to entrapment by a free flowing solid.
Within the bounds of the OHH development with essentially normal construction operations being undertaken, it is anticipated that only the items highlighted above may become an issue to be managed. Where these circumstances do occur the RAMS for the work must take into consideration the potential for specific access arrangements, equipment and working methods.
Any new equipment and appliances requiring access for maintenance should not be installed in a confined space. The requirement to access confined spaces should be eliminated so far as is reasonably practical.
Where any confined space is present it must be clearly signed and protected to prevent unauthorised access.
Persons must only enter a confined space when no safer alternatives are available. All work in confined spaces must be planned and conducted following the requirements for High-Risk Activities and only be conducted by personnel specially trained in the correct procedures, including atmospheric monitoring, use of safety equipment and rescue procedures.
A Permit to Work procedure must be employed to effectively control any work in confined spaces. The Permit to Work must only be issued by a competent person, be valid for a maximum of a shift and require the following precautions to be checked and found to be in place before works can commence:
Appropriate measures to control entry and exit and account for each person entering/leaving the space,
Atmospheric monitoring and rescue equipment is appropriate for the situation and in good working order,
A competent person always remains on the watch when any person remains in the confined space to raise the alarm and provide assistance (only if safe to do so) if needed, and,
On completion of the works, a process is in place to ensure the confined space is closed, secured and the permit is signed-off and closed-out by the issuer.
Lone working is to be avoided whenever possible.
If it cannot be avoided, effective measures must be implemented to eliminate or control the hazards associated with lone working. Where a person is required to carry out work alone, systems should require that a designated contact is notified of their planned work location and duration.
Systems may also include periodic observations, use of warning devices (automatic and manual) activated by the absence of activity. Systems may also include periodic observations, use of warning devices (automatic and manual) activated by the absence of activity and/or indicating an emergency to alert of the need for assistance, such as back to base panic alarms.
Persons entering or working alone in partially or fully occupied premises must be made aware of any conditions or circumstances that may affect their safety, i.e landlord disputes, female lone workers or occupants etc.
Welfare
Welfare requirements must be assessed, and appropriate facilities must be provided before works starting. The facilities provided must reflect the hazards present, numbers of users and their different needs and as a minimum, comply with the requirements of schedule 2 of the CDM regulation 2015
Sufficient toilet facilities for all genders must be provided in easy access to working areas. All toilets should be plumbed into the mains where practical (rather than chemical).
Washing facilities must be provided which are appropriate for the numbers of workers and the work being undertaken. These facilities should include water for washing, the provision of soap, towels and barrier creams, and showers if the type of work requires.
Portaloo style units are to be avoided where possible and only used as either backups for remote working or short-term use for less than 2 weeks.
Appropriate break facilities must be provided for the numbers on-site, be equipped with an adequate number of tables and adequate seating with backs. It may be necessary to rotate shift breaks to avoid overcrowding. Facilities should be provided where PPE does not need to be worn.
Appropriate changing facilities should also be provided. Changing rooms must— be provided with seating; and include, where necessary, facilities to enable a person to dry any special clothing and any personal clothing or effects.
Suitable and sufficient facilities must, where necessary, be provided or made available at readily accessible places to enable persons to lock away— any special clothing which is not taken home; their own clothing which is not worn during working hours; and their personal effects.
Sufficient and easily accessible supplies of clean drinking water must be provided at all locations
Enhanced levels of welfare facilities should be provided for high-risk works or adverse environmental conditions (for example showers and PPE cleaning facilities to remove contamination from asbestos or lead removal or after work in extreme temperatures).
All welfare facilities must be cleaned, serviced/maintained and restocked regularly, especially in light of the current and ongoing issues concerning Covid 19 precautions. The Covid 19 cautions will require to be detailed in a Specific Risk Assessment specific to the particular site and numbers involved.
(Ref. Schedule 2 CDM regulation 2015, CIS 59Provision of welfare facilities during construction work)
Appropriate and sufficient first aid equipment and supplies must be available and maintained to meet the needs of persons working at or using the facilities/site and this should be decided by a written assessment by the controlling person for the facility or site.
Enough personnel must be trained to provide the assessed level of first aid required for each location and allow for maintaining cover during holidays or shift working..
If an employer, after carrying out a needs assessment, decides a first-aider is not required in the workplace, a person should be appointed to take charge of the first-aid arrangements. The role of this appointed person includes looking after the first-aid equipment and facilities and calling the emergency services when required
There must be appointed a suitable number of trained and competent person(s) for rendering first-aid to his employees if they are injured or become ill at work; and for this purpose, a person shall not be suitable unless he has undergone such training and has such qualifications as may be appropriate in the circumstances of that case.
Where an appointed first aider is absent in temporary and exceptional circumstances; it shall be sufficient compliance with that paragraph if the employer appoints a person, or ensures that a person is appointed, to take charge of – (a) the situation relating to an injured or ill employee who will need help from a medical practitioner or nurse, and (b) the equipment and facilities provided throughout the period of any such absence having regard to – (a) the nature of the undertaking, and (b) the number of employees at work, and (c) the location of the establishment.
Purpose – To ensure that effective arrangements are in place to minimise the risk of, and manage the consequences of, all potential fire and emergencies to protect life, property and business continuity (Ref The Regulatory Reform (Fire Safety) Order 2005 ~ HSG 168 Fire Safety in Construction,)
All applicable environment, health & safety legislation and recognised codes, standards and other external requirements must be complied with at all times. Where there is a difference between these Standards and those required by legislation recognised codes, standards and other external requirements the higher standard must be applied.
Every employer shall—
(a) establish and where necessary give effect to appropriate procedures to be followed in the event of serious and imminent danger to persons at work in his undertaking.
(b) nominate enough competent persons to implement those procedures in so far as they relate to the evacuation from premises of persons at work in his undertaking; and
(c) ensure that none of his employees has access to any area occupied by him to which it is necessary to restrict access on grounds of health and safety unless the employee concerned has received adequate health and safety instruction.
(d) so far as is practicable, require any persons at work who are exposed to serious and imminent danger to be informed of the nature of the hazard and of the steps taken or to be taken to protect them from it;
(e) enable the persons concerned (if necessary, by taking appropriate steps in the absence of guidance or instruction and in the light of their knowledge and the technical means at their disposal) to stop work and immediately proceed to a place of safety in the event of their being exposed to serious, imminent and unavoidable danger.
Every employer shall ensure that any provision for the necessary contacts with external services are arranged, particularly as regards first-aid, emergency medical care and rescue work.
(Ref. The Management of Health and Safety at Work Regulations 1999) Fire Prevention.
During the construction phase the responsibility of the site for health & safety passes to the Principal Contractor (PC), who therefor for the purposes of the Regulatory Reform Fire Safety Order, is the effective “Responsible Person”. The person nominated by the Principal Contractor for this role must be adequately trained, competent and nominated in writing.
The PC is therefore responsible for , and required to undertake a Fire Risk Assessment (FRA) and provide a fire safety plan to be included the Construction Phase Plan. The plan should include the all aspects of the construction areas and work phases along with the site offices, welfare and stores.
The requirements, equipment and arrangements set out in the FRA shall be regularly reviewed for maintenance purposes, suitability for current activities and ongoing effectiveness, particularly during the progressive closing in and completion of facilities.
These routine inspections must be recorded, and any defects or missing requirements addressed by the appropriate means.
Particular attention must be paid to the elimination and control of high risk equipment, materials and processes, including combustible materials (such as paper, card, timber, textiles, plastic, foam padding, polystyrene), highly flammable liquids and gases (such as solvents, liquefied petroleum gas (LPG), oxygen, acetylene, adhesives, petrol) and equipment (such as welding torches, petrol generators, halogen lighting).
All operations must minimise the amounts used and stored on site, remove waste and empty containers as soon as practicable, and ensure flammable liquids and compressed gases are used and stored safely in well ventilated stores.
Materials Safety Data Sheets must be available and used to assess risks and identify control measures for the safe storage and use of flammable materials. Information on the locations and quantities of such materials should be readily available for the Emergency services if required.
Flash back arrestors must be in place on supply hoses for any gas-powered welding and cutting sets. Acetylene gas must not be used.
Lighting (particularly halogen lights) must not be located near combustible materials, and this must be continually evaluated as construction progresses. Intrinsically safe lighting and switches must be provided in areas where explosive/highly flammable liquids/gases are used or stored.
Timber framed construction must comply with HSE guidance HSG 168 or follow the guidance provided in the Joint Code of Practice published by the Construction Industry Publications and the Fire Protection Association, throughout the construction phase, particularly the need to compartmentalise and protect outer walls during construction.
Damaged or faulty electrical appliances or installations must be taken out of service or repaired immediately.
Smoking must be prohibited in all areas of the site, except in specifically designated smoking areas. These areas must not be enclosed or in the vicinity of combustible materials, explosives or highly flammable liquids/gases, provided with butt bins and local fire extinguishers and must be well enough separated from any other welfare areas to prevent blow back of smoke into common areas.
Combustible waste must be managed to prevent the risk of fire, by regular removal and safe disposal.
All hot works processes likely to produce sources of ignition such as burning, grinding, heating, welding, flame cutting, etc. must be controlled and the work must be planned and conducted in accordance with the requirements for High-Risk Activities and must be under a Hot Works Permitted Control. A competent person must inspect work areas before issuing permits to ensure the area is safe, that appropriate fire extinguishers are in place and a post activity fire watch is in place.
Effective means for the early detection and warning of the presence of fire must be in place which must be appropriate for the level of risk identified in the FRA for the site. The FRA will also need to clearly establish the need for local or site wide alarms and /or local or site wide evacuation responses.
Fire detection systems can range from fully automated wireless or wired systems to the use of electrical bells, horns, or sirens with people assigned to fire watch duties. All offices and welfare areas should have a working smoke or heat detectors and alarm system installed. Alarms must deliver effective warning (audible and/or visual) in all areas where people may be affected.
All detector and alarm systems must be regularly checked and tested in line with manufacturer guidelines and applicable codes or regulations to ensure they are functional, and the results recorded. This should be done monthly as a minimum.
Effective means of escape must be provided and maintained which are suitable for the number and specific needs of all people likely to need to use them and identified by the FRA. At least two alternative means of escape should be provided from each work location.
Emergency escape routes must be easily identifiable, of adequate width, kept free from obstruction and not used for storage, and have emergency lighting; directional signs and exit points marked using pictograms and/or lights.
On buildings over 18 high (5-storey), temporary compartmentation to 1-hour fire resistance should be provided until the permanent solution is installed. Risers, shafts and opening should be closed off at all levels with self-closing doors and walls of at least 30 minutes fire resistance and horizontally at floor level every 10 floors at most.
Emergency routes should offer no less than one-hour fire resistance and have fire doors fitted to them where appropriate.
Enough firefighting equipment, such as fire extinguishers, hose reels, fire blankets and risers, must be provided that is appropriate for the site and the works underway and which complies with any applicable codes or regulations. All firefighting equipment must be correctly located, readily accessible, unobstructed, clearly signed and have clear instructions on its correct use.
All this information should be set out in the FRA and Fire Safety Plans that should form part of the CPP/RAMS at commencement.
Wet or Dry Risers should progress with the construction or demolition of multi-storey buildings, be no more than two floors below the construction floor and be regularly tested to ensure adequate water flow rate/pressure for the length and diameter of the riser and hose attached.
Connections for the Fire Authority must satisfy the local requirements. In exceptional circumstances where it is impracticable to provide coverage from risers and hose reels, effective means for extinguishing fires must be provided that address the risk and satisfy regulatory requirements, e.g., drench drums, fire pails and additional fire extinguishers. All of these options should be covered in the FRA which will need to be revised at key change stages of construction.
All firefighting equipment must be checked and serviced regularly, including testing of pump sets of wet risers and firefighting lift controls by a competent person following manufacturer guidelines or any applicable codes or regulations and the results recorded.
A weekly visual check must be carried out on all firefighting equipment to ensure they have not been damaged, discharged or gone missing.
Adequate access must always be maintained for emergency services vehicles.
The site emergency management plan (included in the site CPP/RAMS plan) must be implemented and communicated to all relevant people to put in place measures to prevent, prepare for, respond to and communicate about emergencies, including fires, Tower crane rescues, suspension rescues, excavation or temporary works collapse and other major accidents or major security and environmental incidents.
The emergency management plan must detail the likely emergencies, potential impacts and corresponding control measures and include details of persons with key responsibilities, incident response procedures and details for liaison with relevant people, external authorities and third parties.
Sufficient fire wardens must be appointed and trained in emergency procedures, including the need to check areas are clear of people in an evacuation and basic firefighting techniques if appropriate.
Clear instructions must be provided to all people, including workers and visitors, detailing:
a) Emergency warning systems
b) Evacuation procedures
c) Identity contact details and role of fire wardens, and
d) Assembly areas in the event of an emergency.
e) Evacuation routes and assembly points must be well signed.
Emergency escape drills must be conducted at least once every six months and more frequently for higher-risk situations, for example in areas where hot works are ongoing. Where necessary, drills should be conducted in conjunction with local emergency services or a suitably qualified fire assessment consultant.
A review of the emergency and evacuation procedures as well as the fire prevention measures, fire detection and alarm systems, means of escape and firefighting equipment, must be carried out at least annually and updates to the FRA made to the plan, equipment, procedures or construction processes as needed. This should be carried out in conjunction with local fire authorities or a suitably qualified fire assessment consultant on appropriate projects.
Purpose: To ensure that any risks or impacts to the environment are correctly assessed and that appropriate elimination, reduction, or preventative measures and effective control measures implemented in the form of a Construction Environmental Management Plan (CEMP) that will be issued as part of the CPP/RAMS requirement. (Ref: Environmental Protection Act 1990 ~ Pollution Prevention and Control Act 1999~ Environment Permitting Regulation 2010)
All applicable environment, health & safety legislation and recognised codes, standards and other external requirements must always be complied with. Where there is a difference between these Standards and those required by legislation recognised codes, standards and other external requirements the higher standard must be applied.
An assessment of the environmental aspects and the impacts upon them by the construction works should be made by a competent person prior to site set up and issued along with the CCP as the Construction Environmental Management Plan (CEMP).
The scope and range of the aspects and impacts review will be dependent primarily on the size, nature, and location of the project, but should also be extended to include aspects such as:
a) Transportation of Materials
b) Waste Reduction / Reclamation
c) Opportunities to Recycle.
d) Energy, Fuel and Water Consumption
e) Co2 Reduction or Offsetting
f) Pollution Reduction / Controls
g) Discharges to Land Water & Air
h) Sustainability.
The scope of the assessment must be realistic and in keeping with the overall complexity of the project. There would be little point in assessing the saving opportunity on copy paper for the average construction site, this should be done by the overall company assessment if it is an issue to them.
Environmental aspects so far as these assessments are concerned should primarily be those items classed as receptors of those items that can cause an impact. For instance, when assessing the impact of coal tar in road planning’s, the aspects to review would be the potential contamination of the soil, and water tables at the receiving site.
Are those items that can influence the environment, either directly or indirectly, and which will need to be controlled accordingly. The degree of the impact and its effect on the environment needs to be assessed to establish the most efficient, practicable and the Best
Available Technique (BAT) to eliminate reduce or manage the effect of the impact, without creating issues elsewhere.
Example:
Aspect Impact Effect Controls or Limitations.
Air / Water / Land
Dust
Detrimental to Local Human health by respiration and skin contact.
Surface contamination of vegetation – die back.
Contamination of water courses –silting / turbidity.
WEL limits apply to dust levels. LEL 6mg-m3 Source HSE EH40.
Control at origin by extraction.
Change of method to bursting from cutting or breaking.
Dust Suppression by use of Dust Buster water misters*.
Silt traps and settlement traps to prevent water runoff.
Water Silt /debris*
Contamination of watercourses –silting / increasing turbidity.
Displacement / changes to Oxygen loading effecting aquatic life forms
The effects of the work should not alter local watercourse quality.
Local river grading and EA quality controls apply.
Water run off from use of Dust Buster* misters to be directed into settlement areas, and allowed to dry to a damp state before being physically cleared to waste stream.
Any drainage in the areas to be covered and sealed with silt screening.
Once the aspects and impacts assessment have been carried out the resulting general controls need to be incorporated into the CPP/RAMS any specific operational controls included in the applicable SSOW’s.
Suitable and sufficient training, equipment and materials must be assessed and made available for use on site for control of spills in liquid or solid forms. All fuelled plant should be parked up over drip trays or on suitable hard none permeable surfaces. All fuel stores must be kept to the minimum necessary and stored in suitable bunded equipment or areas.
All stores areas must have suitable sized spill kits and materials available, these should be regularly inspected and maintained.
Planning of the overall site to reduce items such as noise, vibration, drainage contamination, water run off (including that from emergency or firefighting), dust and materials movement, all need to be assessed against their relevant aspects, and controls of such set out clearly in the CEMP / CPP/RAMS.
Measurement.
Key measures will need to be established against each impact to ensure the required limits are not exceeded.
Measures to confirm improvements for items such as waste reduction, waste transfer/ recovery, fuel reduction and energy usage etc will be set out, and figures recorded monthly for inclusion within the CEMP for issue to OHH.
To ensure that existing and developing assets within the demesne of the OHH development area are maintained and used safely and properly, to ensure assets do not suffer unnecessary degradation while not in use, or in use by permitted occupants.
This document does NOT relate to the function of, or liabilities related to, any LANDLORDS or LICENCEE’S function, those duties remain outside of this document as they are subject to separate legal obligations and arrangements.
The OHH development consists of various assets in the form of buildings, existing roads, grounds, services and infrastructure. This document sets out the primary requirements for those working on the development, to be aware of, and to follow whilst working on the demesne.
The same process of selection and managerial arrangements will apply to Estate Management suppliers as to those in place for Construction suppliers.
The general development site, Health & Safety rules apply in all cases. RAMS are required for works where there is a foreseeable hazard.
Reference should be made to CDM Regulations 2(1) as to what will constitute construction works and the necessary production of CPP/RAMS’s (required for single contractors on construction works).
As some of the primary existing assets are from the later 1800’s to the pre year 2000 period there is a very high likelihood that the assets will contain Asbestos Containing Materials (ACM’S) in various forms.
The policy is to keep all ACM’s where known and recorded, in an isolated and undisturbed condition. This will include securing the asset against all forms of access without the necessary protective measures being in place.
Assets that are occupied and known to contain ACM’s will be managed following its own specific Asbestos Management Plan. This will be regularly monitored, updated and controlled through the Estate Management Teams.
Those assets that are to be passed over to the development teams will have an Asbestos Removal & Demolition Survey carried out before any other works being executed. The results from these surveys are to be published as required and included in any Pre-Construction information issued with tender enquiries. The policy is for all ACM’s to be removed before any works being carried out by appropriately trained and competent suppliers.
The removal suppliers will provide full documentation of what was removed, where it was removed from, and where it was disposed of along with full clearance certification before others are to be permitted to work on the asset.
In the event of ACM’s or suspect materials, being discovered or disturbed whilst the asset is in occupied use or under construction, the incident is to be reported immediately to the Development Manager. The affected area is to be isolated and any materials left undisturbed, access doors and any windows to be kept closed.
No one is to enter the area until suitable measures have been taken to clean up and remove the ACM materials by suitably competent persons, either under the direction of the Development team for construction works or the Estate Management teams for Occupied assets.
Owing to the size and spread of the development estate and it’s ongoing change of use, several assets have been, for some time now, unoccupied or unused. This lack of use has led in some cases to the asset suffering varying degrees of degradation and decay.
Whether the asset is in a derelict condition or simply vacant, the general policy is that all asset are to be kept in secured conditions to prevent unauthorised access and use. The level of security to be used will depend on the nature and stature of the asset and the perceived trespass threat. The security arrangements will be made either by the development or estate management teams, depending on status concerning construction works.
Concerning vacant assets in general, unless they have been placed within a construction area, they will be regularly inspected for security and condition by the Estates Management team, who will provide reports on the conditions to the Development Manager.
Tenanted assets which form part of the existing infrastructure or have been handed over as the end product of the construction process will be under care and control of the Estate Management team and will be managed under the agreed levels of service applicable at the time for the specific asset.
Existing above-ground assets; footpaths, walls, roads, street lights, signage, playing fields and verges etc are all maintained and managed by the Estates Management team and EBC where appropriate.
There are some areas of shared responsibilities with external 3rd parties such as the local highways authorities, etc, but these will be managed with the Estates Team and the Development Management Team as per set out agreements.
Some assets lend themselves for alternative uses other than their original, this can include use of assets for training, local community use, filming and production, car sales etc. These types of assets and their permitted use with be managed by the Estates Management team.
Unexploded Ordnance.
Due to the location of the development area (proximity to airport and rail infrastructures), there is an assessed risk of munitions being found underground. Should such an item be suspected it is to be left untouched and isolated. The procedure shown in the OHH Safety Management System is to be followed.
Utility Management
Refer to Construction – Detailed Requirements
Utility supplies to Estate Management team assets will be managed on a per location basis. .
Lone Works
Refer to Construction – Detailed Requirements.
Assets managed by Estates Management team will have their Lone Working arrangements managed by their local line manager depending on the location and facility involved.
Bio – Hazards [Guano etc]
Refer to Construction – Detailed Requirements.
In addition to mechanical and chemical substances that may be of harm there are in some of the older assets and in the general development area, several types of biological hazards that suppliers need to be aware of.
With a number of assets, the roof and general envelope are not fully intact, this has allowed the ingress of rodents, pigeons and similar avian pests.
These birds roost within the assets and if left alone will over time deposit large amounts of guano. When wet these deposits can transmit infection by contact with areas of broken skin etc. When these deposits dry, they can become airborne and becomes respirable, this can lead to severe irritation and occasionally infections of the respiratory and ocular areas.
Examples of transmissible bird diseases associated with pigeons, geese, starling and house sparrows: Histoplasmosis is a respiratory disease that may be fatal. Candidiasis is a yeast or fungus infection spread by pigeons. Cryptococcosis is caused by yeast found in the intestinal tract of pigeons and starlings.
Rodents and other animals such as Rats & Mice, cattle etc are also a potential issue, and again it is the deposit of waste products that is the primary concern. Leptospirosis is a bacterial infection often contained in the urine of Rodents and Cattle and can cause damage to the liver and kidneys in severe cases.
Care needs to be executed when working in areas that may have been contaminated with infected urine or guano. Good general hygiene practices and use of the appropriate Person Preventative Equipment to carry out investigations of the degree of contamination followed by specialist removal and disposal, if necessary, will be the general course of action to minimise exposure levels.
Actions to prevent further egress into the asset will be taken on a specific location basis and directed by the Development or Estates Management Teams.
The OHH development is essentially a mixed green and part brownfield site and as such has a level of historic and unchartered services in addition to those utilities known to be live. All contractors must follow industry best practice health and safety guidance to satisfy themselves their area of works is free from live utilities. Where unchartered services are encountered, these should be cross-referenced against known records and verified on site as redundant before proceeding.
All contractors shall comply with recognised standards of best practice, including but not limited to;
CDM Regulations 2015;
Managing Health & Safety in Construction 2015 Guidance;
BS 6187:2011 Code of Practice for Full and Partial Demolition;
HSG 47 Avoiding Danger from Underground Services;
www.HSE.gov.uk Website.
Should uncharted services be encountered and onsite verification has been inconclusive this should be reported to the OHH Project Manager for further direction.
Reporting Utility Strike and/or Incident
The OHH development has existing water and power networks across the site. For any damage to be correctly logged the contractor Must advise the OHH Development Management Team.
This call should confirm the site location including the nearest road and postcode and the nature of the call.
Reporting of strikes involving other utilities should be recorded through their respective communication channels. Note: The contractor should follow best practice and their own procedures in the event of an incident.
Unexploded Ordnance Management Chart.