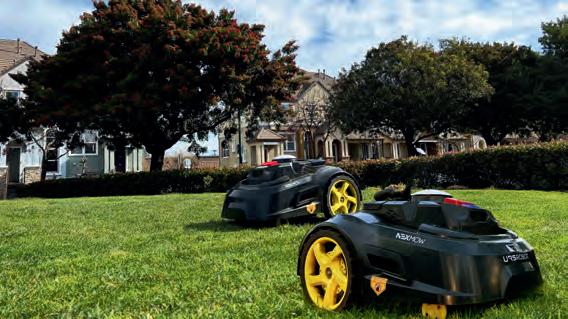
4 minute read
PREVENTIVE EQUIPMENT MAINTENANCE IMPROVES THE BOTTOM LINE
Aclear, creative vision is essential to a successful landscaping project and so is the equipment used to bring that vision to life. When equipment breaks down or malfunctions, the project schedule suffers, the budget suffers and so does the customer experience—and possibly your company’s reputation.
Regular maintenance and inspections of equipment such as backhoes, skid steers and mini-excavators are key to protecting the bottom line by preventing unexpected equipment-related downtime. Yet, many landscaping companies under-maintain this equipment, often because they lack the time or qualified technicians to do the work or the expertise to develop and implement an effective maintenance program.
Given the payoffs of maintaining equipment per the manufacturer’s maintenance guidelines (based on engine hours, mileage or days in use), it’s worth finding a practical, cost-effective solution.

Benefits of Performing Regular Maintenance and Inspections
Developing and following recommended maintenance and inspection schedules benefits workers, project timelines and profits. Consider these rewards:
Safety: Faulty equipment is potentially dangerous equipment. Long hours of use in hot weather put heavy wear and tear on machines, and worn chains, cables and other parts put workers at risk. Broken pedals or levers and malfunctioning safety lights or audio signals can also result in preventable accidents. Properly maintaining and inspecting equipment can help reduce the number of safety incidents and worker injuries.
Productivity: Following manufacturers’ recommendations for equipment inspection, maintenance and parts replacement can improve productivity by reducing unplanned downtime. If equipment fails or malfunctions, work may stop while you arrange for repairs, search for hard-to-find parts or shop for replacement equipment. Even equipment that is underperforming due to lack of maintenance may slow down operations. One delay causes a domino effect, affecting other projects and customers.
Financial: Reactive maintenance—fixing machines only when they break—can drive up the total cost of equipment ownership. When equipment must be taken out of service at critical moments, the impact on the schedule takes a financial toll. Wages are wasted when workers can’t perform the intended tasks, and you may need to pay workers overtime to make up for lost hours or days. Preventive maintenance, on the other hand, helps keep projects on schedule and within budget. Often, it trims repair costs by addressing small problems before they lead to big ones. It also extends a machine’s useful life, delaying the need to purchase new equipment and preserving the value of the equipment when it’s time to sell.
The Value of Outsourcing Maintenance
For small, busy landscaping companies, staying on top of maintenance and inspection schedules isn’t easy, especially in the middle of landscaping season when equipment is constantly in use and moving from one site to another. Retaining skilled mechanics and trained service technicians capable of maintaining and repairing today’s sophisticated equipment is also challenging.
Outsourcing maintenance and inspection to a company specializing in customer-owned equipment repair and services can be a smart strategy for owners who want to protect their profits, their equipment investments and the safety of their workers.
Top-tier equipment repair and services companies have deep experience developing maintenance and inspection programs—and the trained, experienced technicians and certified mechanics required to execute them. In addition, they have access to supply chain networks for equipment parts, which eliminates long waits for parts and speeds up repairs. Because these companies purchase parts in bulk, you may receive favorable pricing.
Using a work order management system, customer-owned equipment service providers will keep records of what services are performed and when. If emergency repairs are needed, the mechanic can easily call up the service records to see what maintenance has recently been performed. Good service records can also reduce your liability if your equipment is involved in a safety incident.
Relying on equipment service professionals to track maintenance needs and provide regular maintenance and inspections can cut costs, save time and provide the peace of mind that comes with knowing equipment remains in optimal operating condition. Above all, it lets you focus on what you do best: designing, creating and maintaining beautiful landscapes.
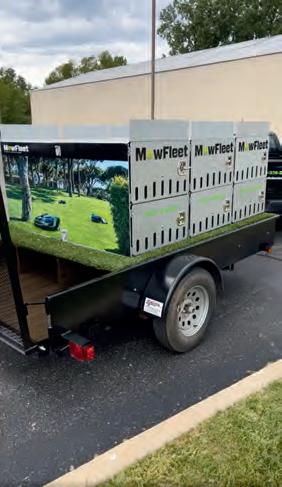
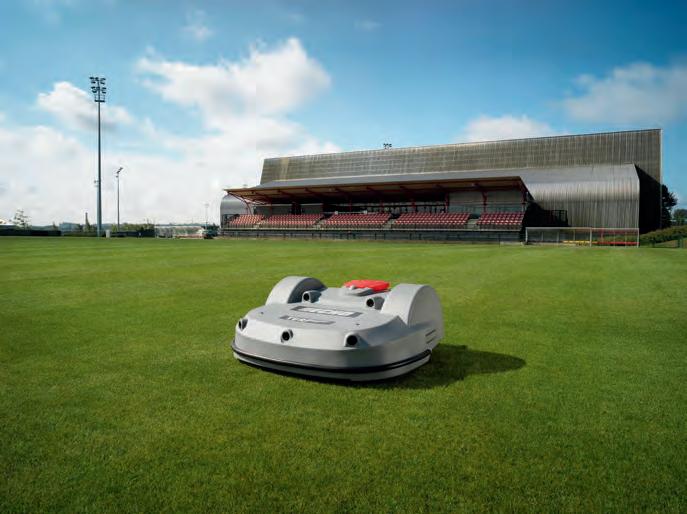
Getting Started
As the end of the season approaches and work slows, it’s the perfect time to inspect and service your equipment. One call to a customer-owned equipment repair and services company will get the ball rolling.
Landscape business owners have multiple challenges to contend with, including labor shortages, low-priced competitors and economic uncertainty. Equipment maintenance doesn’t have to be one of them. A reputable equipment service provider with expertise in maintaining the type of equipment you own and experience creating and implementing maintenance and inspection schedules can take the burden of maintenance off your plate and potentially save you money in the process.
About Bret Kasubke
Bret Kasubke is director of Customer Equipment Solutions at United Rentals. He has 20-plus years of demonstrated excellence in driving performance improvement. From on-demand service for unexpected construction equipment repair to a turnkey fleet management solution, United Rentals’ Customer Equipment Solutions team has an option that can be catered to a company’s unique needs. www.unitedrentals.com
SIGN UP NOW for a weekly dose of exclusive industry news & insights!
Scan the QR code to get on the list.
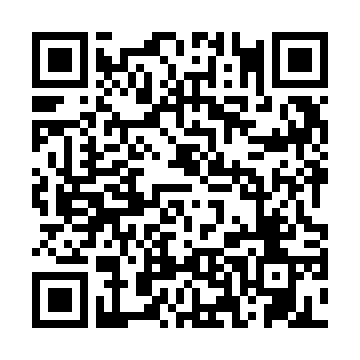
For Leaders In The Landscaping Industry

Landscape Architecture, Design, Construction, Horticulture & Maintainenance
Hi there,
As 2024 approaches, the SYNKD team is working hard to make this year counts. Since the beginning, we have taken our vision of connecting the landscaping sectors, nurturing growth and engendering a communal culture predicated on doing things right to heart. For us to hold to our standards and ramp up our production of quality content, magazine subscriptions in the new year can no longer be cost-free.
By subscribing, you are helping SYNKD fund research, journalism and creative efforts needed to grow and maintain a commitment to excellence. This will allow us to sustain our publication’s integrity and expand our coverage.
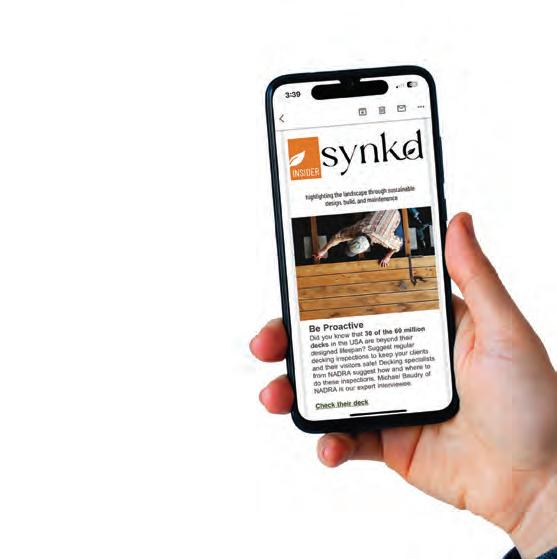
If you want to see more than one copy of our magazine sent to your door, we offer a special deal for shared subscriptions. Please email admin@synkd.io for details.
Thank you for being a valuable member of our community and we look forward to immediately delivering more insights and solutions to elevate your business.
With gratitude, The Team at SYNKD