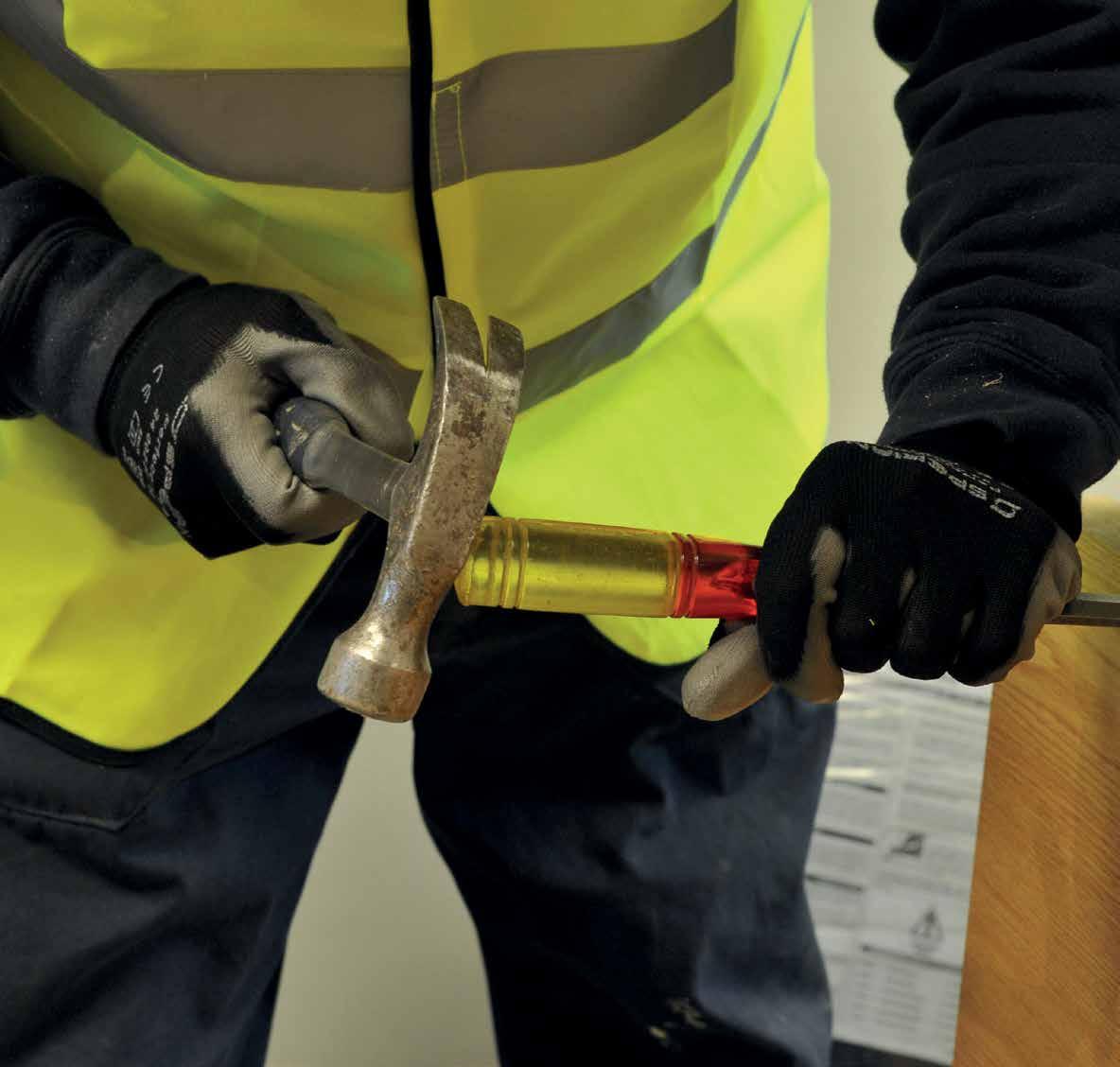
6 minute read
The role of the passive fire protection installer and maintainer
Ross Newman discusses the importance of installation and maintenance in the protection of buildings.
The workmanship of installers and maintenance teams plays an important role in fire protection.
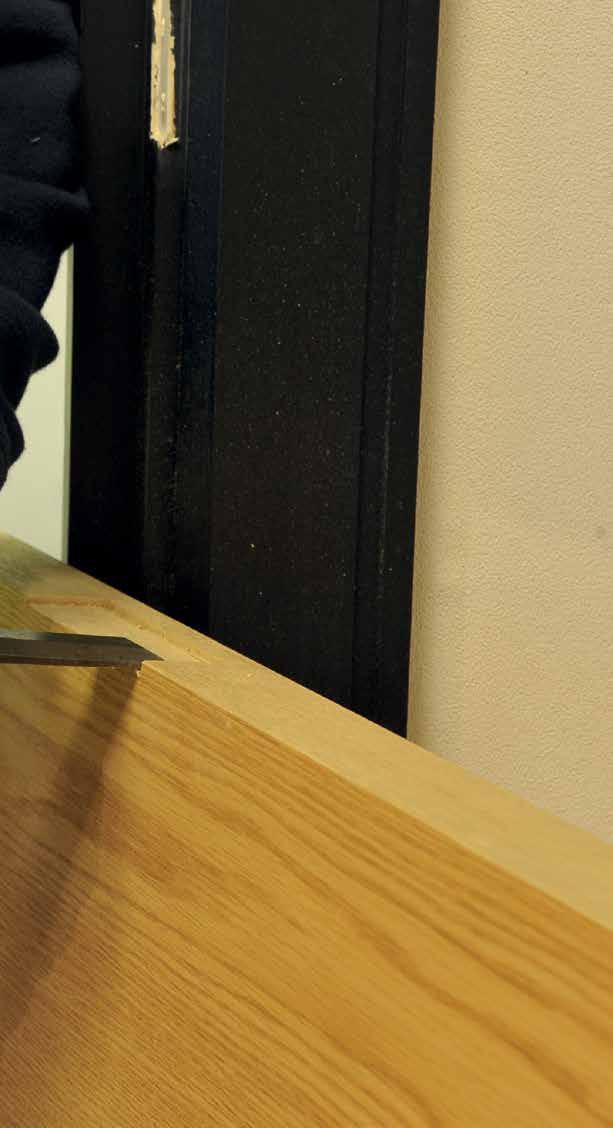
Awell-designed passive fire protection (PFP) strategy and specification are not the only considerations in adequately protecting buildings from fire. Of equal importance is the workmanship of installers and, thereafter, the maintenance team.
PFP is built into the fabric of a building in the form of walls, floors, ceilings, beams, columns, screens, seals, firestopping, doors and shutters. It performs two essential functions in the event of a fire:
1.It allows the building to remain stable for a specified period to allow people time to escape and firefighters to attend.
2.It resists the spread of fire and smoke between buildings/ dwellings, or between subdivisions within a single building/ dwelling, helping to protect people or valuable contents within.
Installation
PFP strategies comprise disparate elements that together make a critical system. Installing a single one of these elements without an understanding of the overall critical system can lead to integration errors, even when that element is correctly installed.
The impact of fire and smoke has the potential to be extremely grave. It can kill and severely injure. It will also destroy or write off fixtures, furnishings and equipment, and fatally weaken the structural integrity of assets.
In an industrial setting, this sets up a domino effect of negative impacts, interrupting business and leading to financial losses, lawsuits, redundancies and even insolvency or bankruptcy. Although the risk cannot be eliminated altogether, the impact is so detrimental to operations as to demand efforts to minimise it.
Fires and smoke are dangerous but they usually become catastrophic when they spread from the room of origin. The point of PFP is to prevent this spread or, at the very least, delay it. All too often, however, fires do spread, often because of faults with the installation and building management/maintenance. >>
Maintenance
Certain elements of PFP construction such as masonry walls or timber or steel structures are likely to remain untouched throughout the life of the structure. They are generally low maintenance and require relatively little vigilance from the point of view of fire safety. Therefore, the main risks arise if they are not installed correctly in the first instance.
However, other elements of construction, such as doors and partition walls, suffer from wear and tear or are more likely to be altered and are, accordingly, a higher risk factor. Those that are subjected to daily use, such as doors, shutters and so on, will need to have their fire safety role preserved through a routine programme of maintenance. Equally, elements such as partitions are likely to be altered or penetrated (to allow building services to pass through, for example) and will therefore suffer damage and require repair. The new penetrating element will need effective firestopping. All PFP systems both need to be properly installed at the start of their life and subject to a programme of continuous maintenance by competent persons with the necessary expertise.
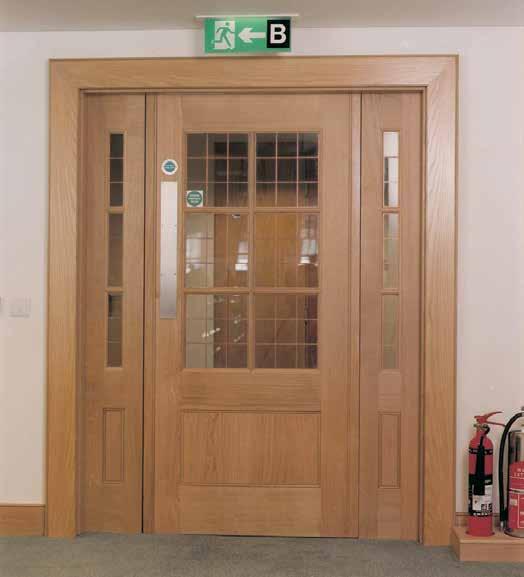
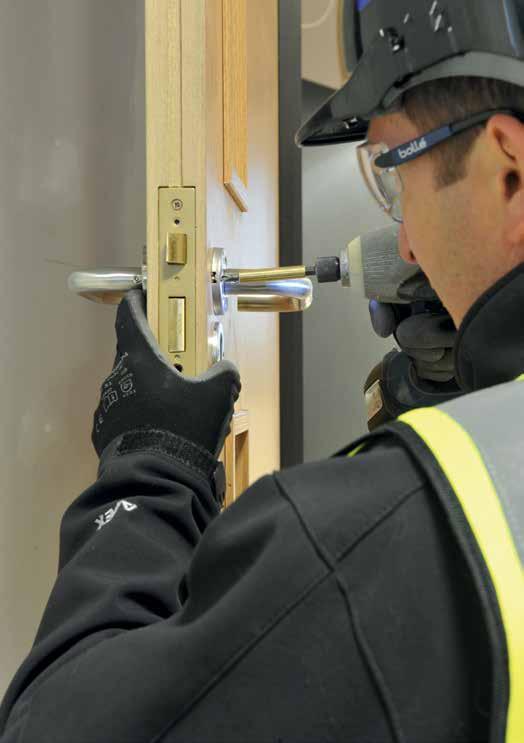
Fire doors must be properly installed
Passive fire protection
Since many PFP solutions are effectively hidden in the building, they are difficult to put right. More importantly, they are very difficult to verify or detect by cursory inspection, even if the structure is visible. It takes skill, experience and competence to accurately identify the fire rating of an element, especially in the absence of any historic documentation. In some instances it may not be possible to assess the fire rating of a particular element of construction or item of PFP without some form of destructive inspection or investigative testing.
Retrospective fixing is, of course, unavoidable in some circumstances, especially where a building undergoes a change of use or working practices are introduced that alter the existing fire risks. In instances like this, such remedial works are likely to be carried out years after original completion and often by non-specialist facilities management staff. The resulting risk is that the occupants could end up relying on systems that may not function as expected in the event of a fire.
Minimum life-safety aspects of PFP are enshrined in legislation and regulated to ensure that buildings are constructed that provide reasonable levels of protection to life safety and continue to be managed and maintained once the building is occupied. However, owners, insurers and other interested parties will often go further than the minimum legislative requirements, if the risks warrant it. >>
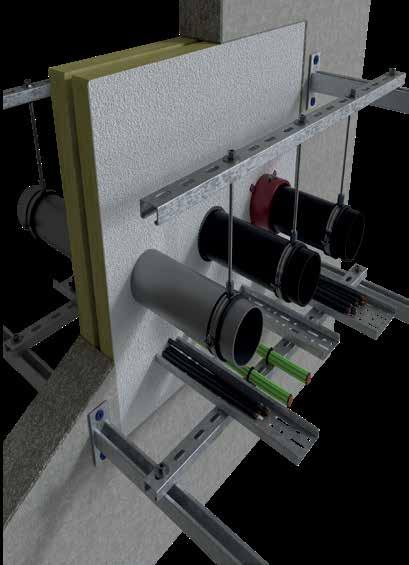
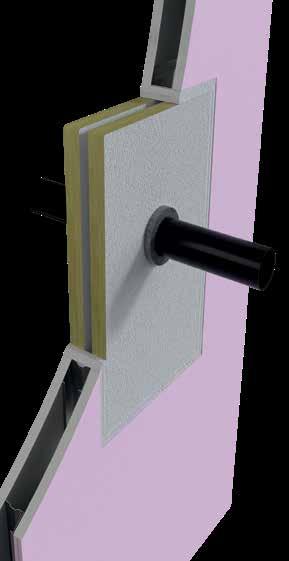
The correct installation of all PFP systems is critically important but of equal importance in the ongoing maintenance so they can continue to provide the same level of fire performance. This has been recognised under article 17 of the Regulatory Reform Fire Safety Order. Similar to installation, maintenance of PFP requires specialist knowledge and skills.
Fortunately, there are a number of highly reputable third-party certification schemes for installation and maintenance providers. Successful candidates will typically only be awarded their certificate if they have attended a training course, passed an examination and had their practical site work scrutinised by an independent UKAS-accredited third party. Further assurance is provided with regular audits to ensure compliance with the scheme is maintained on an ongoing basis.
Left: Framing out and board lining of services openings in dry-lined partitions Right: Multiple services within a single opening
Specification
Part of the solution to good installation is to get the specification right in the first instance. A comprehensive specification, clearly defined and accompanied by accurate, comparable drawings, goes a long way to mitigating the risk of misunderstanding between the different parties involved in the design and construction of the building. Wherever possible, only third-party certified, and tested products should be specified to provide added assurance. The specification needs to be effectively communicated as part of the overall strategy, with the integration issues clearly expressed. In this respect, working in a contractual Building Information Modelling (BIM) environment helps. This gives the highest possible level of confidence that the work will be carried out correctly. Specifying specialist third-party certified contractors will help demonstrate due diligence in the unfortunate event of a fire. Dealing with the damaging effects of fire is bad enough without the additional burden of being the subject of a legal claim.
Summary
There is no question that employing third-party certified installers and maintenance contractors are worth the extra cost for the fire risks they mitigate. Furthermore, installing and maintaining PFP elements correctly extends their service life. Retrospective fixes for poorly installed designs are disproportionately difficult and expensive, adding extra motivation to get it right first time round. n
Installation and maintenance
Even after handing over comprehensive specification information and clearly communicating the strategy, success still lies in the hands of the installer.
It is not enough to rely solely on the installer’s self-declaration of competency. Instead, you should check that that they have relevant recent experience, and that they can back up their claims with evidence of suitable training and skills. Additional confidence can be provided by using installers that are certified under a recognised UKAS-accredited specialist third-party installer scheme. Indeed, for added assurance insurers and fire consultants are increasingly insisting on third-party certificated services.
About the author
Ross Newman Regulatory Analyst Warringtonfire
Further reading
• WIS 1-13 Performance of fire-resisting timber-based doorsets, BM TRADA, 2018 • WIS 1-32 Upgrading timber joinery doors for fire resistance,
BM TRADA, 2020
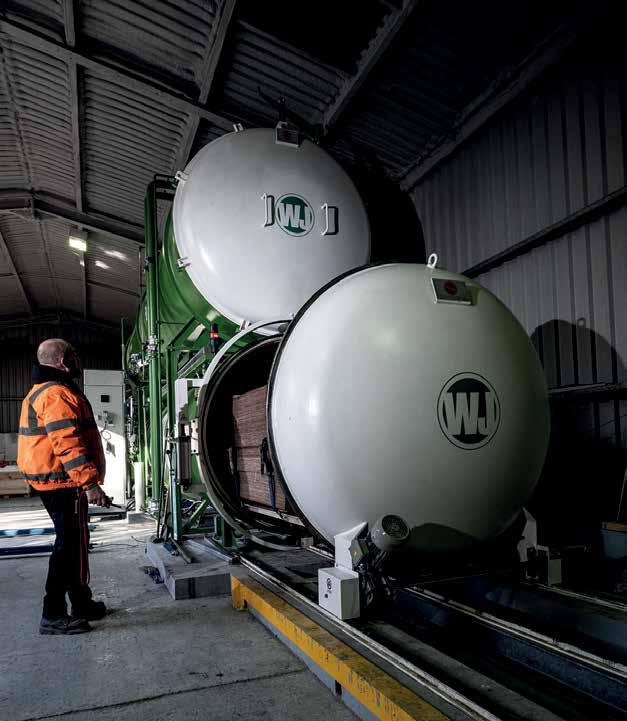
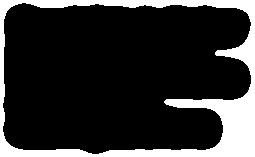
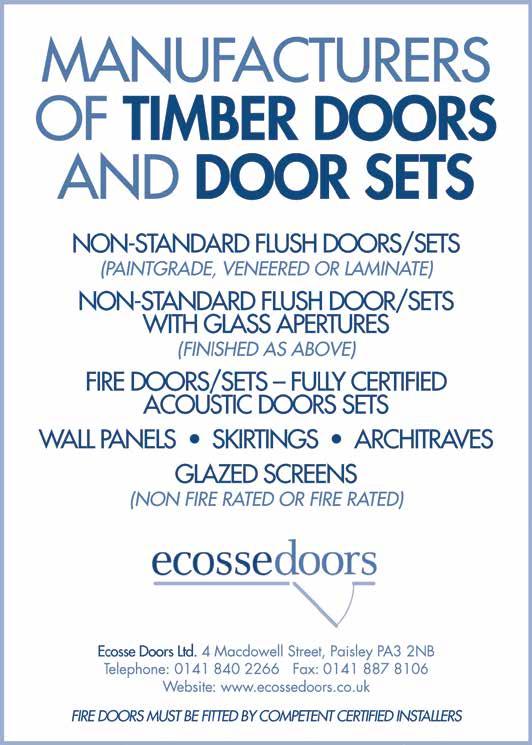
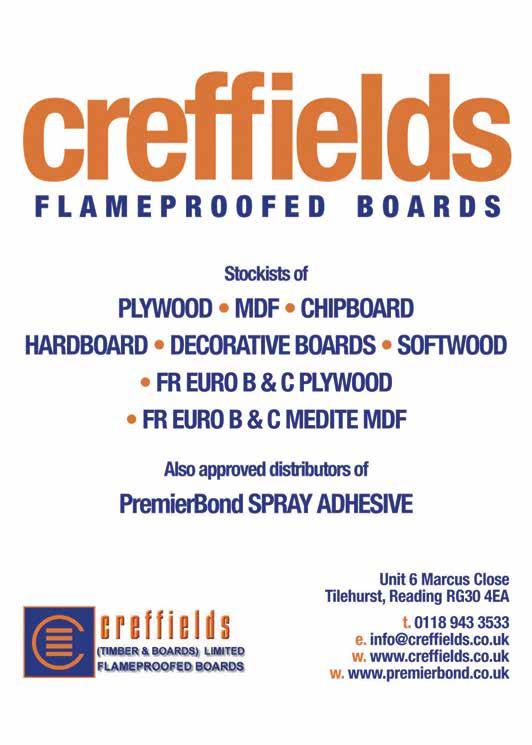