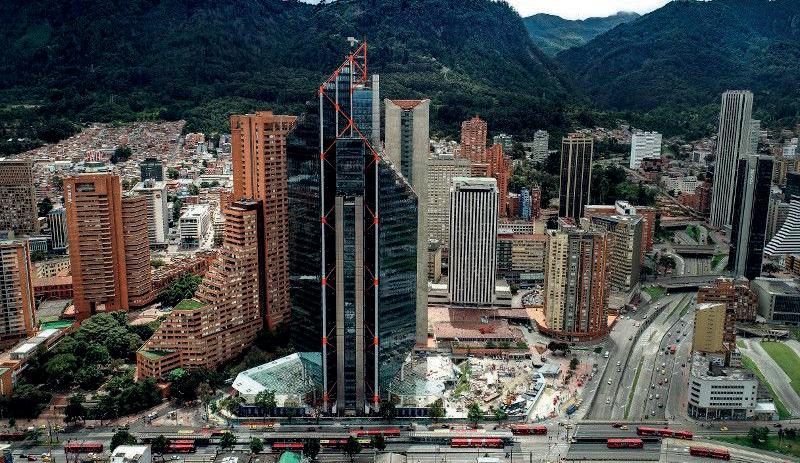
10 minute read
Más cerca de las estrellas Atrio, Torre Norte
from Noticreto 17
Arquitecto Rodrigo Rubio Vollert. Gerente del Consorcio Arpro-Ellisdon. Ingeniero Agustín Bolívar Ramírez. Gerente de Construcción, Arpro. Ingeniero Oscar Leonardo Guerrero Ramírez. Director de Calidad, Atrio Torre Norte.
Fotos: Cortesía Arpro
Advertisement
El proyecto Atrio es un complejo arquitectónico de 250.000 m2 de construcción y de uso mixto –oficinas y comercio– ubicado en el centro de Bogotá, en la intersección de la avenida Caracas con la calle 26. Comprende dos torres de 44 y 63 pisos de altura (respectivamente Torre Norte y Torre Sur), un centro de convenciones y cerca de 10.000 m2 de espacio abierto al público. La Torre Norte, construida entre 2014 y 2019, dispone de cinco sótanos, 200 m de altura y 120.667 m2 de área total. El diseño estuvo a cargo de la oficina de arquitectura RSHP, Londres, bajo la dirección del reconocido arquitecto inglés sir Richard Rogers, premio Pritzker, y de gran reconocimiento por proyectos como El Centro Georges Pompidou en París y la terminal T4 del Aeropuerto Barajas de Madrid. La construcción fue ejecutada por el consorcio colombo-canadiense Arpro-Ellisdon.
La estructura
El sistema estructural de la Torre Atrio se compone de un núcleo central en concreto al que se adosa un sistema de vigas metálicas que luego conforman un perímetro de columnas de sección mixta en acero estructural y concreto reforzado. Las columnas se conectan por medio de riostras metálicas diagonales que cumplen un papel fundamental en la respuesta sísmica de la estructura. Las placas perimetrales con lámina metálica colaborante y concreto se montaron consecutivamente conectándolas a las vigas metálicas y al núcleo central. La cimentación está compuesta por pilotes de hasta 64 m de profundidad y una losa de fondo de 3 metros de altura.
En la construcción del edificio se utilizaron 8.350 t. de acero estructural, 95.000 m3 de concreto y 10.000 t. de acero de refuerzo.
Vista general del proyecto Atrio Torre Norte, actualmente el edificio más alto de Colombia.
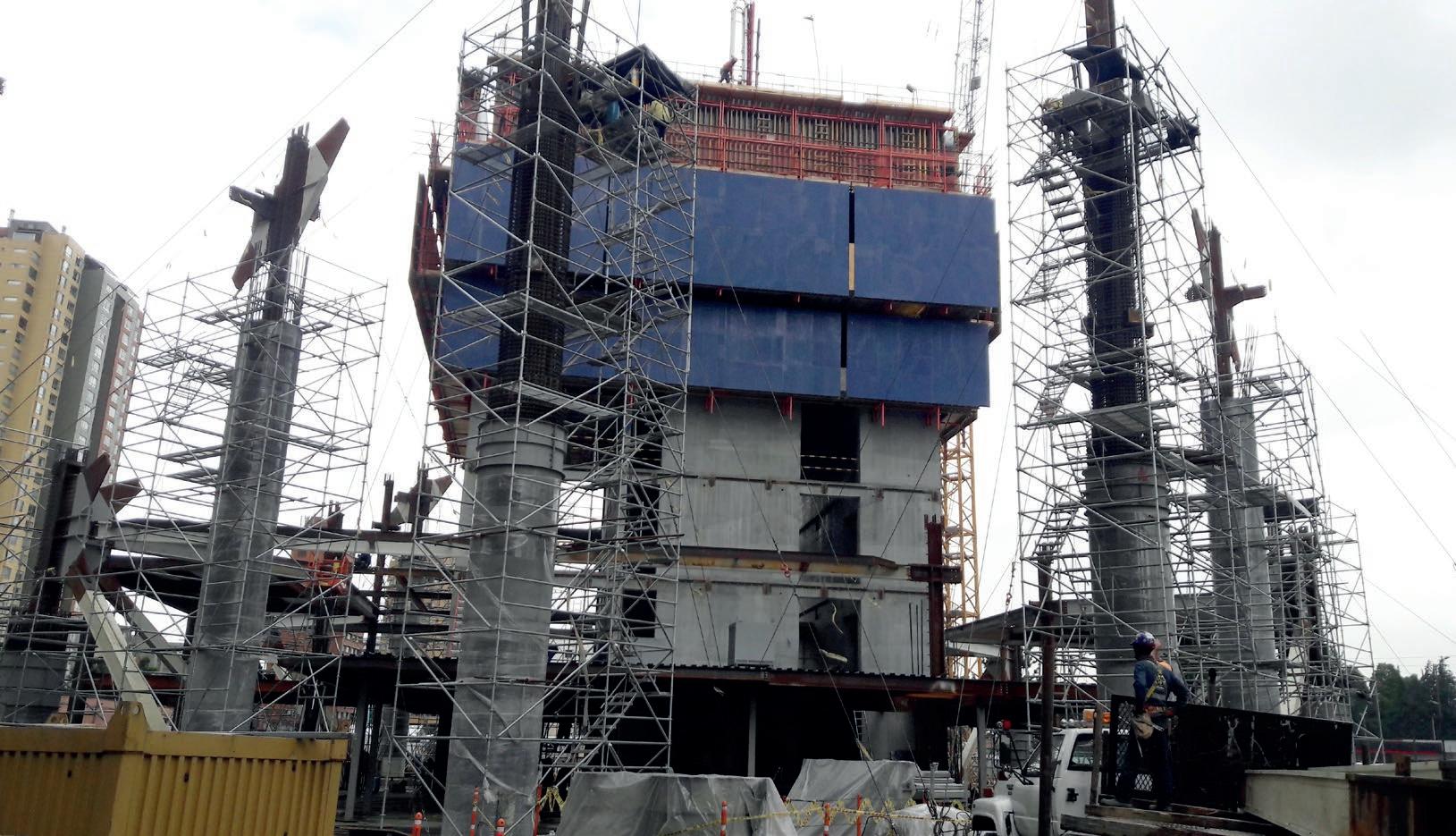
Conformación del núcleo central y columnas perimetrales.
Losa de subpresión
La construcción de la losa de subpresión se constituyó en uno de los vaciados masivos más grandes del país, pues se colocaron más de 7.300 m3 de concreto durante 38 horas consecutivas. Para cumplir esta labor se diseñó –durante los diez meses previos a su ejecución– un complejo proceso de planeación utilizando simulación por modelos digitales, que incluyó prototipos de fundida masiva para determinar el tipo de mezcla y los sistemas de monitoreo a utilizar. El vaciado requirió, de manera exclusiva y continua, seis plantas de producción, 24 camiones mezcladores por hora, nueve autobombas, un centro de control de calidad y logística permanente en obra y más de 200 trabajadores. Se empleó concreto bombeable de 27 MPa de resistencia, 9” de asentamiento y 22 °C de temperatura máxima de colocación, lo cual implicó –entre otras novedades– la utilización de hielo en el proceso de premezclado. Fue necesario establecer un tiempo de tránsito de los camiones mezcladores no mayor a 90 minutos para conservar las propiedades del concreto, instalando una estación remota de control de calidad del concreto con capacidad para atender simultáneamente cuatro camiones. Para monitorear la evolución térmica del concreto se instaló una serie de termocuplas de transmisión de datos remotos y para el curado se protegió la superficie del concreto con tela térmica.
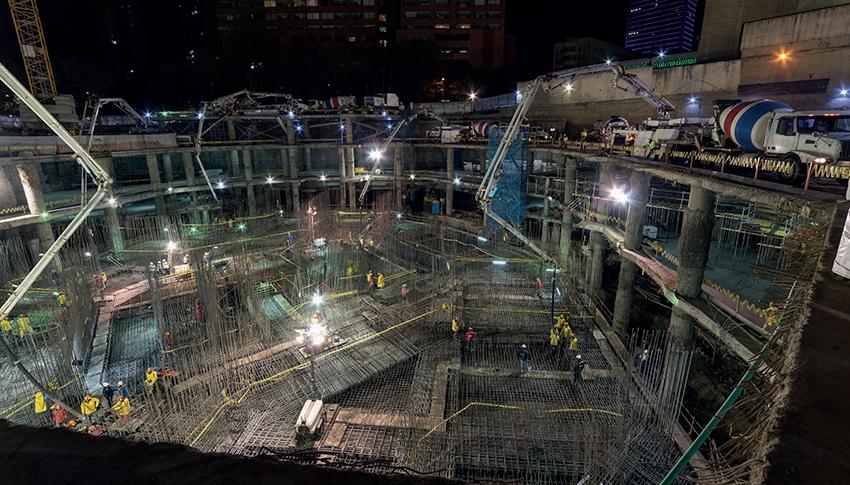
Vaciado de la losa de cimentación. Características del concreto
Para construir los muros de los sótanos, el núcleo central y las columnas perimetrales de la torre –todos elementos con altísimas cuantías de acero– se empleó concreto autocompactante de resistencia a la compresión de 55 MPa hasta el nivel 17, y de 41 MPa hasta el nivel 42. Todos los concretos para elementos verticales de la torre debieron diseñarse para satisfacer requisitos no solo de resistencia a la compresión, sino también de módulo de elasticidad, retracción, viscosidad, contenido de aire y temperatura. En la torre Sur se emplearán concretos de 69 MPa. Por primera vez en Colombia se dispuso de equipos de alta precisión para medir el módulo de elasticidad sin distorsiones por defectos de planicidad en los testigos.
Los requisitos de módulo de elasticidad y retracción son parámetros que, en edificios de gran altura, buscan asegurar que las deformaciones en los diferentes elementos verticales sean homogéneas y garantizar así que los pisos permanezcan nivelados. En Atrio Torre Norte se necesitaron mezclas que alcanzaran módulos de elasticidad de 35,2 GPa y 30,6 GPa, así como retracciones inferiores a 0,04% a 28 días de madurez. Adicionalmente se monitoreó el creep (fluencia del concreto o deformación acumulada) usando dispositivos electrónicos embebidos en las columnas y muros de los primeros niveles del edificio.
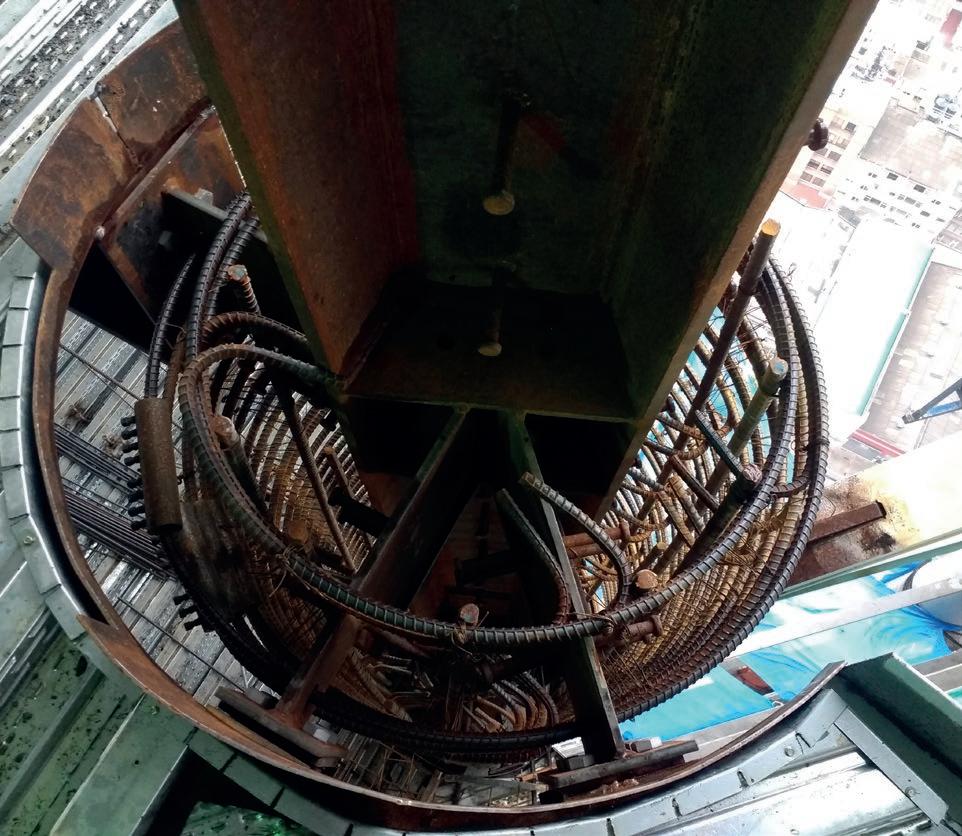
Interacción acero estructural y barras de refuerzo en columnas.
Para producir este tipo de concretos especiales fue necesario un trabajo intenso con el proveedor para determinar conjuntamente las especificaciones de cada mezcla. Hubo que incorporar agregados de altísima densidad que permitieron obtener los altos módulos de elasticidad requeridos. Fue necesario destinar una planta exclusiva para producir este tipo de mezclas y establecer altos controles de calidad en el almacenamiento y manejo de materiales, así como en los procesos de monitoreo y supervisión de la producción de las mezclas, puesto que una pequeña variación en la dosificación podría acarrear desviaciones inaceptables en las propiedades del concreto. Tanto en estado fresco como endurecido se hicieron pruebas preliminares en laboratorio y en prototipos en obra, hasta lograr obtener los resultados esperados.
Control de calidad
Los laboratorios de control de calidad asociados también tuvieron que pasar por un proceso de mejoramiento para ejecutar los ensayos, dando estricto cumplimiento a las normas establecidas. Esto debido a que ensayos poco aplicados en el país como el de módulo de elasticidad y retracción, bajo las normas ASTM C469 (Método de prueba estándar para el módulo de elasticidad estático y relación de Poisson del concreto a compresión), ASTM C157 (Método de prueba estándar para el cambio de longitud de mortero y concreto endurecido de cemento hidráulico) y CSA A23.2-21C (Materiales para concreto y métodos de construcción en concreto / Métodos de ensayo y prácticas estándar para concreto) exigían instrumentos, equipos y procedimientos de altos niveles de control para llegar a las precisiones requeridas.
Bombeo de concreto
El bombeo de concreto a gran altura representó un reto para el equipo de construcción y el proveedor del material: se necesitó una bomba de concreto que permitiera asegurar las propiedades del concreto en pisos elevados, una tarea que no resultó fácil: la alta presión requerida, la velocidad y la fricción con la tubería afectaban las propiedades del concreto en estado fresco. Para controlar las pérdidas de manejabilidad hubo que partir de un plan logístico que asegurara la disponibilidad permanente de concreto fresco, acompañado de un control de calidad exhaustivo tanto al arribo de los camiones mezcladores a la base de la torre como en la descarga en niveles superiores. A partir de los datos obtenidos, y a medida que aumentaba la altura del edificio, se hicieron ajustes a las mezclas para garantizar sus propiedades y su correcta colocación. También se desarrolló y se aplicó un procedimiento estricto de reacción inmediata frente a imprevistos, que permitía dar continuidad a los vaciados mediante ajuste de las mezclas en obra con la adición de aditivos plastificantes y estabilizadores de última tecnología.
Otros controles
Como control adicional para confirmar el desempeño de la estructura se hicieron mediciones topográficas periódicas de alta precisión que confirmaron los cumplimientos tanto del requisito de asentamiento del edificio como del acortamiento de los elementos verticales.
Las mediciones de niveles piso a piso confirmaron que los parámetros de retracción, módulo de elasticidad y fluencia se cumplieron a lo largo del proceso constructivo hasta su culminación.
Proceso constructivo
El núcleo central se conformó en tramos de 4,2 m de altura mediante formaleta autotrepante que soportaba a su vez un brazo mecánico para colocación de concreto (Placing Boom). El proceso de elevación de la formaleta requería una resistencia a la compresión mínima del concreto de soporte; por tal motivo, y para agilizar el proceso constructivo, se monitoreó la temperatura del concreto mediante sistemas de termocuplas conectadas a un sistema de transmisión de datos que generaba reportes en línea al centro de mando. Los datos de temperatura se confrontaban de manera automática con datos obtenidos de una curva de madurez (temperatura vs. resistencia) desarrollada previamente en laboratorio. De esta manera se obtuvieron valores de resistencia a la compresión a edad temprana que permitían iniciar el proceso de trepado de formaleta y armado de refuerzo, en un plazo que no superaba las 19 horas desde el vaciado más reciente.
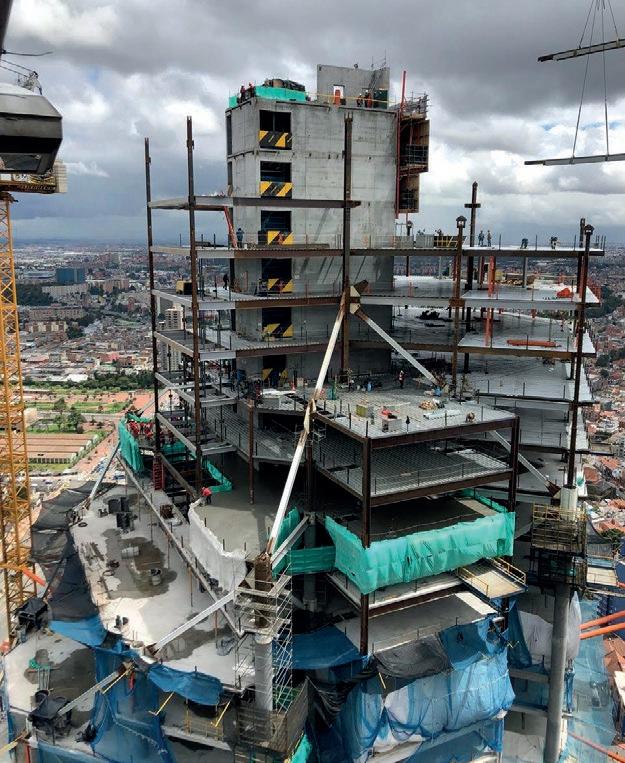
Para conformar las columnas perimetrales de sección circular y altura típica de 4,2 m de nodo a nodo, se empleó un sistema de formaletas metálicas de cierre mecánico hermético. Para manipular e instalar un equipo de estas dimensiones y a esa gran altura –y dado que la geometría del edificio contempla columnas fuera de la placa– hubo que desarrollar una serie de plataformas metálicas móviles que rodeaban la columna, se insertaban en los entrepisos y se fijaban a las vigas mediante gatos mecánicos. Este sistema constituía un área de trabajo estable y segura para los trabajadores y el control de la formaleta.
La formaleta de columnas representó un reto no solo por sus grandes dimensiones sino por su geometría compleja. La conexión con nodos metálicos requirió un control de calidad estricto por parte de los fabricantes y el constructor. Se debió asegurar el cumplimiento preciso de las tolerancias geométricas en la fabricación e instalación de los nodos y de las carcasas de la formaleta para asegurar su correcto ensamble y hermeticidad. Desde el punto de vista estético, la instalación de la formaleta de los nodos representó un gran reto puesto que son elementos permanentes y juegan un papel de gran importancia en el aspecto el edificio. De igual forma, fue necesario elevar las tolerancias típicas de la obra de concreto hasta las tolerancias del acero estructural.
El concreto de las columnas queda a la vista, por lo cual fue necesario desarrollar e implementar una serie de procedimientos de control de la formaleta en su fabricación, manejo, mantenimiento e instalación. Hubo un exhaustivo control geométrico de la formaleta para asegurar su correcto ensamble y estanqueidad, así como un seguimiento al número de usos y estado de desgaste para programación de reparaciones o reemplazos. De igual manera se implementaron procedimientos de limpieza de formaleta y aplicación de desmoldante, acudiendo a las mejores prácticas y procurando la menor exposición de la formaleta a agentes ambientales como polvo y agua antes del vaciado del concreto.
Interacción estructura metálica y de concreto.
Ensamble de fachada.
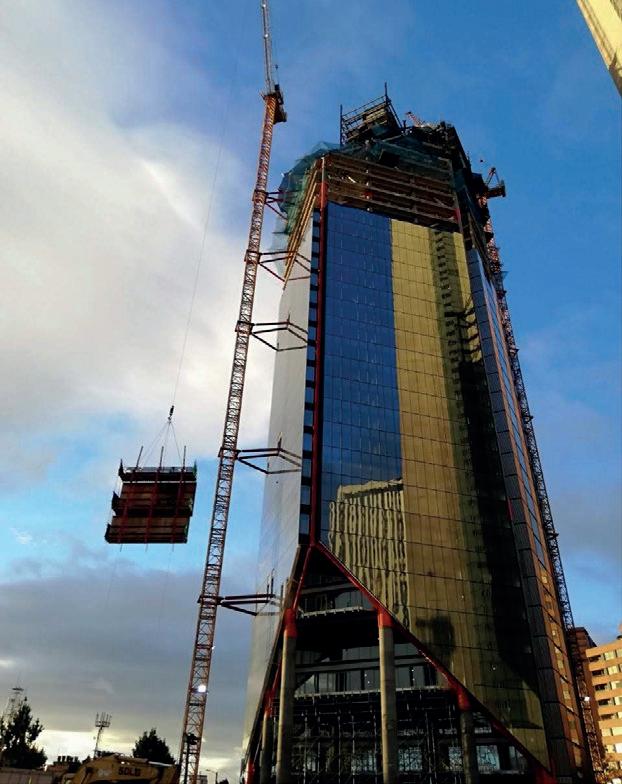
La fachada
Es relevante mencionar que Atrio Torre Norte tiene una fachada envolvente de vidrio y aluminio de alta tecnología, importada de Europa. Su diseño garantiza que el ambiente interior sea confortable y eficiente en temperatura y acústica. La fachada está integrada por alrededor de 6.000 módulos independientes que se adosan a las placas de concreto mediante brackets que permiten nivelarlos y absorber movimientos en la estructura. Empaques y sellos en las juntas de los paneles aseguran la estanqueidad de la fachada, la cual, de acuerdo con las pruebas realizadas en sitio, es capaz de resistir caudales de agua de 5 L/min/m a presión de 3 bar.
Sostenibilidad
Atrio fue galardonado con la certificación LEED® Gold que lo reconoce como una construcción sostenible de alto desempeño ambiental. Su diseño y equipamiento de alta tecnología se ven reflejados en ahorro energético del 14,58 %, ahorro interno de agua del 40,63 % y en paisajismo del 65,61 %. Para alcanzar tan alto logro se destaca –entre otros factores– que el proceso constructivo tuvo un estricto control ambiental en materia de monitoreo de ruido, control de emisiones y manejo responsable de residuos de construcción y demolición.
El proyecto Atrio tiene previsto consolidar el Centro de Convenciones y la Torre Sur en los próximos años, para entregar este ícono urbano y arquitectónico a la ciudad de Bogotá antes de concluir la década.