
4 minute read
Questions to Ask When Upgrading/Building MRI or Radiology Facilities: Part Five
Questions to Ask When Upgrading/Building MRI or Radiology Facilities
Part Five
Advertisement
BY MARK BAY
In our continuing series of MRI Construction articles, we will look at an ongoing case study in which some or all the circumstances may apply in any retrofit or upgrade that you might be considering.
It will certainly add to the list of questions to ask. This case situation began with the addition of a second, new MRI room two years ago adjacent to an existing MRI room that has been operational since the midnineties. Yes, in the last century.
During the construction of the new MRI room and the replacement of the building’s roof (due to leaks and age of the roof) some amount of mold was discovered to be present in the roof cavity above the existing shield. The problem at that time was determined to not be severe enough to be dealt with at that time or due to budget and/or time constraints the decision was made to close the cavity and address this situation later.
Having now arrived at “later” there are some challenges that have arisen that were likely not anticipated when the decision to move on was made. The first of these is how to remediate the mold without damaging the shield as all the work and removal of contaminated construction materials is directly above the shield. Another challenge is that the shield is about 25 years old which means it is a copper shield and not as hardy as a multi-layered steel shield and can be damaged much more easily by the work above. An additional challenge is that now there is an operational MRI room opposite the subject one and the control room is shared. Access to the new MRI during construction for patients who may not be ambulatory requires protecting the approach to this area from dust, debris, personnel as well as noise. Maintaining a comfortable atmosphere is paramount to alleviating patient anxiety which is common with an MRI.
Other challenges this situation poses is the remediation of the mold itself, sanitizing the roof cavity above the shield and removal of the contaminated materials without exposing uncontaminated areas to the debris or allowing the shield to get wet from common mold removing chemicals. Conventional wisdom would lead to removal of the magnet, replacing the dated shield with a new shield and then either reinstalling the existing magnet or upgrading to a new or refurbished magnet. This operation could be cost prohibitive in that the magnet would need to be ramped down and maintained on life support off-site, requiring an opening in the side of the building to allow rigging and transport of the magnet. Because this construction operation likely requires structural design, a design team would need to be hired and a building permit would be required lengthening the duration and the cost of the project considerably. Replacing the shield would be the next step in this process and then returning the magnet to the shield room, completing the shield once the magnet is in place and then recalibrating and recommissioning of the magnet. Along with construction costs involved this would become impractical for most operations and the disruption to patients and staff would be unattractive to most facility managers. Also, transport and storage increases the risk to the dated magnet as well.
The alternative to the above involves choosing the right team first. Having a mold inspection and remediation contractor that is sensitive to the physical environment they would be working in is first and foremost. If there is not an experiential understanding of the sensitivity of a copper shield, the dangers involved in working near a strong operational magnetic field and the physical environment of a hospital then the following methods of remediating this mold condition would be foolhardy.
The first order of business is the base line test to establish the level of RF protection the existing copper shield currently offers. The next order of business is the mold inspection itself. Air quality samples, moisture tests, as well as samples for laboratory analysis would be taken in the MRI room, the cavity between the Acoustic Ceiling and then the roof deck cavity itself where there is known mold. Once the type of mold is identified and the quantity of particulate matter in the air calculated, the extent of the contamination, as well as if there are any areas of moisture present are identified, a remediation plan will be developed. Considering that one does not want to introduce moisture to the copper shield, a dry chemical and mechanical remediation plan is in order in this space. An access in the copper shield can be provided near the front edge of the MRI room
CONTINUED P.13
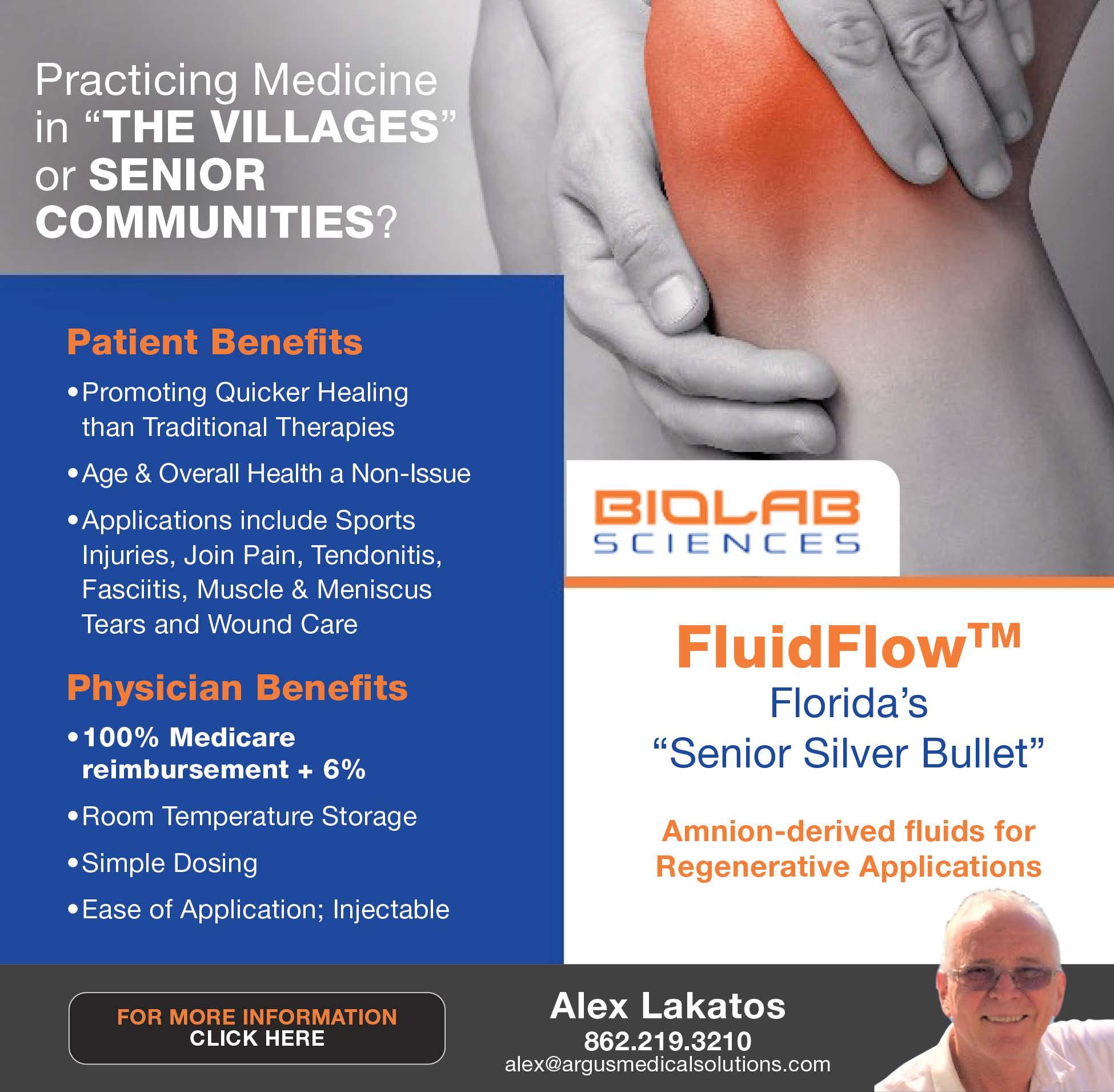