
25 minute read
SO SPIN AROUND TO THIS
HOW MIPS & CO ARE INFORMING THE ESSENTIAL MOTORCYCLE CRASH HELMET
By Adam Wheeler, Photos by MIPS & 6D
Almost eighty years ago Australian neurologist Dr Hugh Cairns published the results of a study into the effectiveness of motorcycle helmets. The document entitled ‘Head Injuries in Motor-Cyclists with special reference to crash helmets’ examined the effectiveness of vulcanised rubber and compressed wood pulp(!) shells of what were the contemporary ‘pudding basin’ products. Head protection or ‘wear’ - like most new-fangled ‘fads’ or developments of motorcycling in the initial throes – had fi rst appeared in wider consciousness at the Isle of Man TT races some twentyfi ve years previously.
Quite a lot has changed since. However, it is only in the last half a decade that the effectiveness and safety performance of motorcycle ‘lids’ has undergone a radical change. Facets of weight, comfort, vision, sound and protective quality all advanced with technology but the pioneering exploits of a handful of scientists and engineers have led to a rethink in how helmets work. In particular how they address concussion and the effects of ‘rotational acceleration’. In short: the consequences of the brain moving inside the cranium upon impact, and how potentially lethal or devastating results can be reduced.
Cairns’ 1943 document was made public two years after his initial curiosity and research into head injuries for bikers had led to the British Army making head protection compulsory for couriers. Cairns himself was allegedly inspired into the field after his treatment of famed and fated serviceman T.E. Lawrence; a staunch motorcyclist who lost his life in May 1935 after crashing his Brough Superior and spending six days in a coma. The Army logged a significant reduction in injuries after adopting the helmet policy. Cairns notes at the end of his follow-up paper in 1943 (having already recorded the location of the majority of blows to the helmet - front and sides – and the better performance of wood as opposed to rubber as well as grim description of facial injuries) that ‘further improvements in the design of helmets offer a profitable field of preventive medicine.’
Medicine was not the only profitable aspect as the speed and popularity of motorcycles climbed steadily, especially in the post-war years and eras of austerity where owning a car was more expensive. Enduring manufacturers like Arai (Japan), Bell (U.S.), Schuberth (Germany), AGV (Italy) soon took note and were fabricating ‘pudding basins’ by the end of the ‘50s. Bell constructed the first full face helmet, the ‘Star’, and launched it in 1967. Safety standard agencies cottoned on. The DOT test morphed from other American standard policies in the 1960s and was established in the early ‘70s. The renowned independent Snell Foundation has been active and very prominent in the industry since the 1960s and the British BSI ‘kitemark’ has been around for almost a century and for bike ‘lids’ specifically since 1953. Australia made the use of crash helmets mandatory in 1961 and the UK followed suit twelve years later. Amazingly less than half of the USA’s fifty states currently have universal helmet laws, the rest have regulations applying to younger riders up to 18 and 21. With regulations comes strict test parameters but this is a field where the work and thinking of innovators such as Sweden’s MIPS (Multi Impact Protection System) and the USA’s 6D Helmets were able to scrutinise and eventually revolutionise.
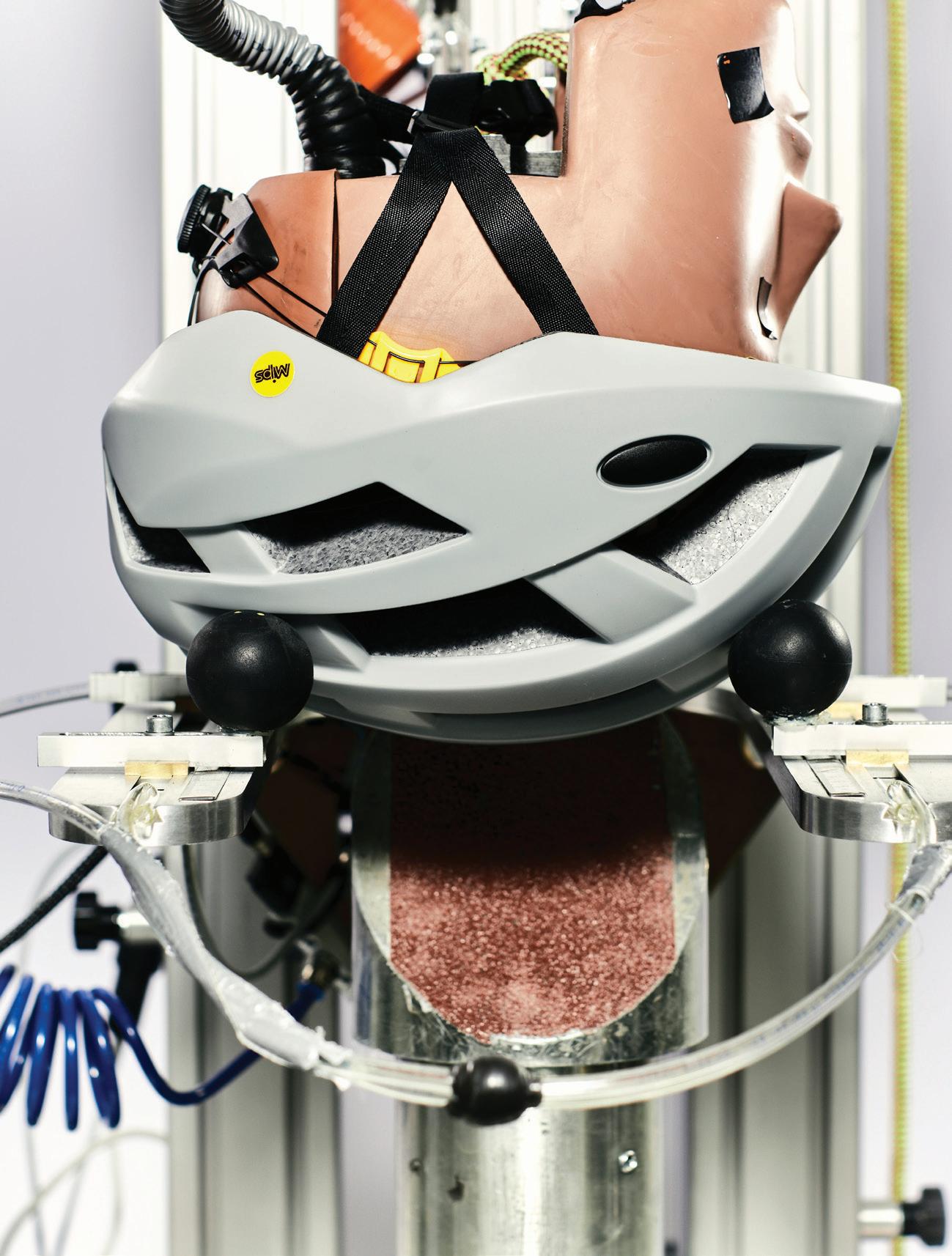
Heading north…
Less than 10km upwards from the centre of Stockholm the principal HQ of MIPS is a small and unassuming semi-circular single-floor building. The premises used to be home to a famous light design firm and 10,000 euro fixings still remain attached to footwell ceilings. It seems apt, considering how MIPS’ R&D has illuminated the helmet industry to the point where the FIM have worked tirelessly and polemically to shake-up their own test protocol and are dragging the majority of brands to renovate and overhaul their catalogues to be present in the vast promotional window of world championship motorcycle competition.
In the cellar the architecture exposes the ‘Cold War’ dating of the structure. We stride through a large bunker door into former ‘Safe Rooms’ (now meeting rooms) and eventually to the pristine lab and at least three testing rigs – home of more than 27,000 procedures - located deeper in the recesses of the facility.
We meet the two key figures behind MIPS, and a company born from the plights of the duo: distinguished neurosurgeon Hans von Holst and his never-ending search to understand and minimise critical head injury, then CTO Peter Halldin whose quest to overhaul and perfect helmet test standards led to the theorising behind the practicalities of the MIPS solution. Plus CEO Max Strandwitz, who has been tasked with expanding the word, the business and the influence of MIPS as far and as effectively as possible, so that the circular yellow sticker can now be found on headwear from skiing to equestrian to bicycles to building sites.
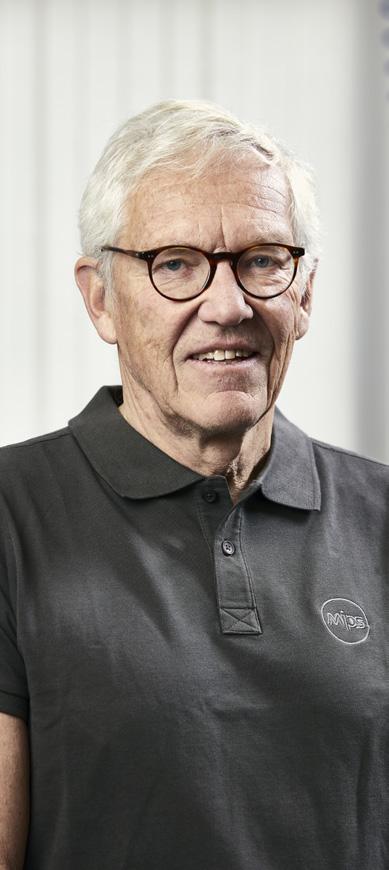
Hans von Holst
STRANDWITZ: “YOU KNOW IT IS NOT ABOUT ‘WHOEVER MAKES THE MOST ADVANCED SOLUTION WINS’...”
Before von Holst gives us a detailed, sometimes daunting but riveting explanation of the complexities of brain injury (scary stuff in some cases) we’re able to see MIPS’ product piled along the lab test workstations. MIPS is staggeringly simple, almost unbelievably so. The minimal low friction plasticky ‘sheath’ that fits inside the helmet is a Brain Protection System (BPS) and it permits 10-15mm of movement or ‘play’ independent of the lid when it strikes an object: this minimal shift works in the first 5-10 milliseconds of the impact and redirects crucial energies that would otherwise induce strain and lead to torn brain tissue. Earlier experimental and numerical studies showed that the brain is much more sensitive to rotation forces compared to linear (impact in one direction).
The yellow BPS’ on the workbench (customised for a particular helmet) look like a thin scalps of a mannequin. Being present at MIPS and watching Halldin dropping a 4.2kg headform (the same weight as the average human head) strapped into a helmet onto the rig and using state-of the-art video equipment and software to register the subsequent results then hearing some of von Holst’s vast bank of knowledge on the most mysterious part of the human anatomy (“we are still in the stone age now compared to the next 100 years”), and lastly absorbing Strandwitz’s account of how hard it was to sell and manage the MIPS patent and philosophy into a business model gives full appreciation of all the effort, expertise and cost that has gone into the BPS.

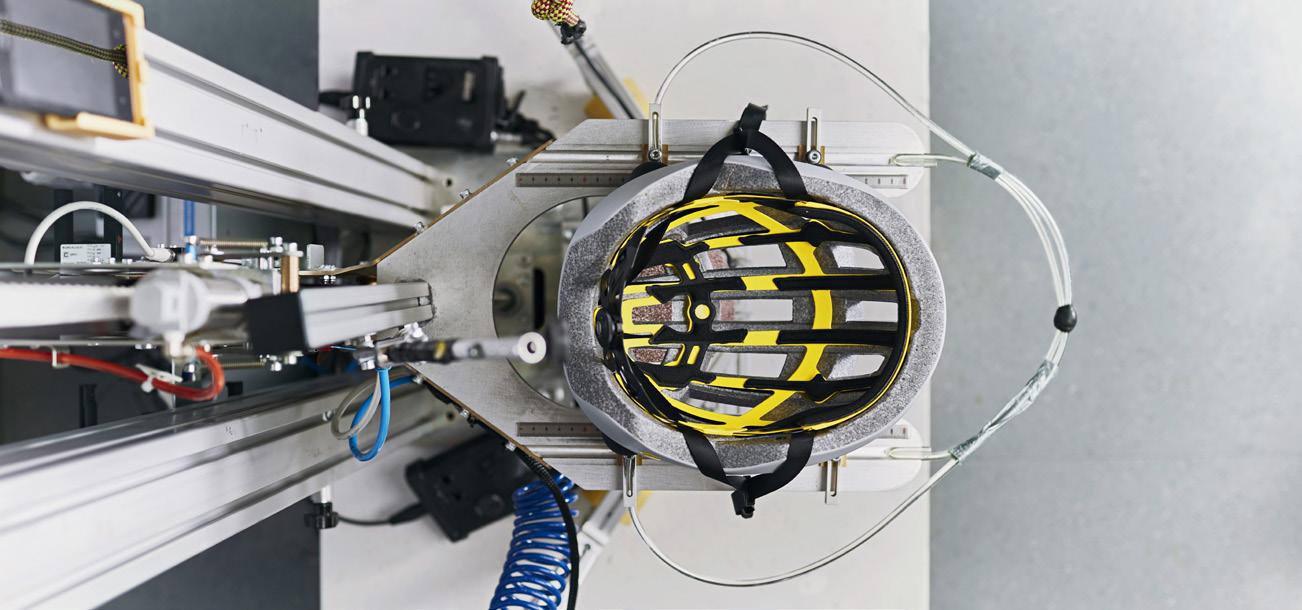
“We do get that comment sometimes,” says Strandwitz on how ‘basic’ the BPS seems. “For me it is an ingenious construction. There is so much money and thinking going into that solution: it is affordable, scalable, can be retrofitted into most helmets. We have looked at so many different materials over time, and so many different technologies and, so far, we haven’t found anything superior to slip-plane technology. Through our testing and technology we have found that you really need this 10-15mm margin of movement to reduce forces into the brain and that’s where we see and feel that most competition falls short. People might say ‘I have a natural MIPS because I have a lot of hair’ but the pressure point you are exposed to during an accident is somewhere between 750 to 1000kg and try to move something with that: it’s impossible. So, it is simple…but that’s one of the reasons we have been able to scale. There is a very long-driven thought process on why it looks like it does.”
In 1995 MIPS was founded as a project between von Holst and Halldin and the first patent was lodged in 1998. “The language between us just didn’t match,” smiles von Holst. “MDs [Doctor of Medicine] cannot do everything and engineers neither; it took six months before our dialogue was on the same page.” Von Holst’s research at the time found there were “22,000 head injuries annually in Sweden because of falls,” he says. “65-70% of those involved rotation. The energy is absorbed by the skull but there is always a register for brain tissue and just a little is enough. Even now concussion is still a mystery; we don’t know what it is, and no MD or expert can tell me more.”
“It sounded stupid but we wanted to create the internal helmet…and it might have taken years,” von Holst added before divulging studies of protein impact and how urea and the physiology of Great White Sharks can hold even more secrets for how brain injury and malformations can be treated in years to come.
“With the first tests in 1996 we saw that we could reduce the moment of impact that refers to rotational acceleration,” says Halldin of the idea behind BPS. “We played with prototypes of oil, Teflon and some micro-spheres that left dust all over the lab when we impacted them! We then made a two-dimensional spherical model and went step-by-step. I got a small amount of university funding at the time and then bigger funding so I could go to the UK and the University of Birmingham where I’d heard of a professor [Nigel Mills] who knew how to test helmets for oblique impacts. That was in 2000 and we spent half a year building the test method together. We made the first test with a real MIPS helmet, one with a sliding layer and got great results so I wrote a scientific article on it in 2001. We started the company and went out trying to sell the fantastic MIPS concept…but it was not that easy because it was too expensive at that time.”
It is puzzling as to why von Holst and Halldin’s knowledge and theories were not noticed or discovered sooner by the motorcycle industry. “A lot of the helmet industry has been quite conservative and the test standards themselves have driven the design of helmets,” Halldin references. “Such as the protrusion test – when a helmet is dropped onto a fifteen-degree angle surface – but it is just to see that there is nothing on the helmet that will ‘grab’ into the road. They didn’t measure anything inside the head but rather the impact force on the plate. So, while it has been understood that rotation is something you should avoid it hasn’t really been tested as part of a standard and put into helmet to absorb it. Conservatism is one reason, another is that it takes time to change and to educate people. Others will point to the fact that the way to measure rotational acceleration was not really developed at that time either…but now there are more sophisticated systems to measure acceleration and rotational velocity.”

Peter Halldin
“We are seeing a shift of mindset. People used to laugh at rotation as a problem…but now everybody is working on it. We see with our clients that people are more aware and are educating themselves,” asserts Senior Project Manager Daniel Lanner, revealing that while the MIPS story is a success and is being used by almost 80 different brands and in nearly 450 helmets across sports and industries, the story wasn’t always so streamlined. After the first patents and mathematical models in the 1990s the company took the initial steps to their own helmet product. “Equestrian is really big in Sweden,” Lanner recounts “and at one point was the second most popular sport. MIPS was looked up to by many here and the equestrian helmet was a big success.”
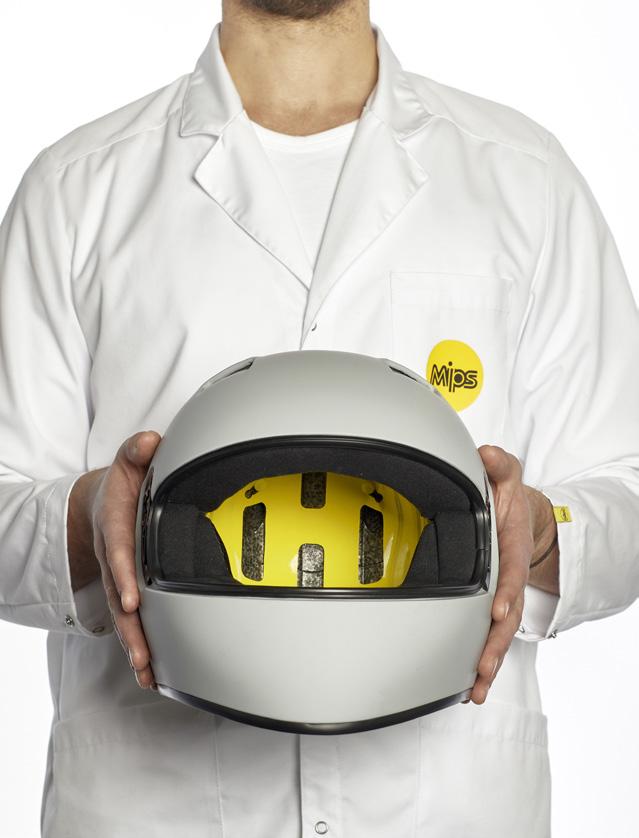
However, due to a design fault of the retention system for the extreme cold of Swedish winters the lid had to be recalled and MIPS faced bankruptcy. “We then became an ‘ingredient’ brand, and not an expert in helmets but in rotation; we knew the idea had so much potential,” Lanner stresses.
Shortly afterwards salvation, growth and an eventual float on the Swedish Stock Exchange in 2017 came about because large-scale helmet companies could not develop their own technology to tackle rotation.

“Investment companies that owned brands like Bell and Giro took two years to do their due diligence and saw that they could not beat the MIPS patent, so they made an investment with us. Again, we had success, this time with the system ‘insert’ into a snow helmet.” Today MIPS belongs to 36 patent families and is present in a number of sports and activities. It is not a ‘one size fits all’ solution though. “It is crucial to know how we should build for certain helmet categories,” says Lanner. “We are extra strict in understanding the requirement before we start with a new category.”
“We usually spend around 120 days on each case,” he adds. “We’ll have the CAD for each helmet model and size. Each helmet has its own tooling and process. They have to match our criteria and we need to see a minimum reduction of strain for our tech to be released and sold as part of the helmet. If we don’t see that then we don’t release until the helmet has been re-designed. We usually see a lot more than the minimum threshold though. MIPS is not just a ‘plug-in and play’ but then I have yet to see one helmet where we haven’t been able to make it work.”
“We customise the MIPS insert for the shape of the helmet, EPS and things like ventilation channels and fixing points but it still needs to move in that 10mm-15mm bracket in all directions,” says engineer Marcus Seyffarth, who is operating a horizontal rig next to Halldin and is one of a team of twelve-fourteen people running up to 6000 tests a year.
Was there a time when MIPS and the BPS wasn’t the solution for a client? “Yes, we had an approach from a company in baseball,” admits Lanner “but we saw that our technology would not have so much effect for those type of injuries, so we had to walk away.”
Halldin’s work – and he is busy dropping a full-face motorcycle helmet from a hefty height before coming to talk – has been implicit in the modification and advancement of test protocol. “He is part of CEN TC158/Working Group 11 that looks at test set-up, impact materials and developed a new head form; a new version of the Hybrid III for helmet testing, scalp friction and inertia properties…the FIM is setting up its own tests with the same model,” says Lanner. “At MIPS we don’t tamper with standards, we just add protection. It is a severely conservative industry and a sharp change in standards would mean a lot of cost…but we are 100% convinced it will change anyway.”
The discussion…
Both Halldin and Strandwitz appear from busy schedules – Halldin actually stops testing and combines his interview with a lunch break – and present an opportune moment to quiz the pair on various issues on MIPS and also their involvement in motorcycling specifically.
On having to ‘sell’ or explain the rotational aspect of helmet performance…
Strandwitz: We see quite a lot of different attitudes. The first one I think is always ‘not invented here’ syndrome. We also see some brands that still believe that rotational motion is not dangerous…but generally those are less and less. We also see more and more brands that say to us ‘we are late on the train but we understand it’. When we sign a new brand – and this is important for us – we always want them to come to our HQ so we can explain why we really make a difference. Otherwise we are ‘just a product’ like anyone else. So we invest quite a lot of time. There are cases when we don’t see some prioritising safety, and we say ‘it is better you go back and think why you want to include MIPS in the helmet’. They usually return much better equipped to launch MIPS. Some people think it is great we are here because we kind-of set the standard and therefore it’s easy because they don’t need to think about what they have to include. Other people think we are too big and have too much power. When people start to see how much time and knowledge we have invested into this and especially our link to KTH [Sweden’s Royal Institute of Technology] then they say ‘OK… we understand’. We haven’t lost a lot of brands since we started, we have a very loyal customer base and I think this is testimony that we are doing some things right.
Halldin: We contacted a couple of motorcycle brands in Europe and at the EICMA fair in 2002 we had some prototypes and no one at that time really talked about rotation…but at least two of the biggest brands in Europe at that time got interested and we had some projects with them although they ended up stopping because it was too expensive.
Strandwitz: If you look at our customer base then 75% have U.S. origin. They distribute all over the world but we got a bit of a headstart with the Americans because there was an article published in ‘Popular Science’ in 2012, and also because of the whole concussion debate. The average consumer in the U.S. is much more aware of why rotational motion is dangerous. The average European consumer is not. We see some awareness in the UK but generally in Europe they are ten years behind in terms of consumer awareness. They have not had the American Football or hockey injuries and that’s why they are not that developed when it comes to thinking why this is an important subject. stand they realised it wasn’t possible, so they invested in the company and the people and become partners. That is testimony to the IP portfolio but also how the system really works. Strandwitz: We have the ambition to get into as many helmets as possible. If we look at our position in motorcycling it
On working with diverse helmet companies…
Strandwitz: One of the key reasons for our success is that we have been able to retro-fit into helmets. In one way it means we don’t need to be part of the design process. However if we are then this is beneficial…but it’s not a ‘must’.
Halldin: Our spread means what we are doing in the test lab is the right thing. People have been trying to beat the MIPS system for quite a while and work out how they can get around the patents. In the end after a couple of years of research and trying to understand they realised it wasn’t possible, so they invested in the company and the people and become partners. That is testimony to the IP portfolio but also how the system really works.
Strandwitz: We have the ambition to get into as many helmets as possible. If we look at our position in motorcycling it a little bit different. In motocross we have about fifteen brands on board, the key ones, and we are penetrating their assortment quite heavily, which is great. When we look at the more traditional motorcycle helmets then we don’t have the same traction there yet. We are helped by the new FIM standards and so on, but we still have a long way to go. We are constantly developing new solutions and new technologies to always be equally safe and achieve the same thing: to reach the movement of 10-15mm in all directions… but it can be presented a bit differently.

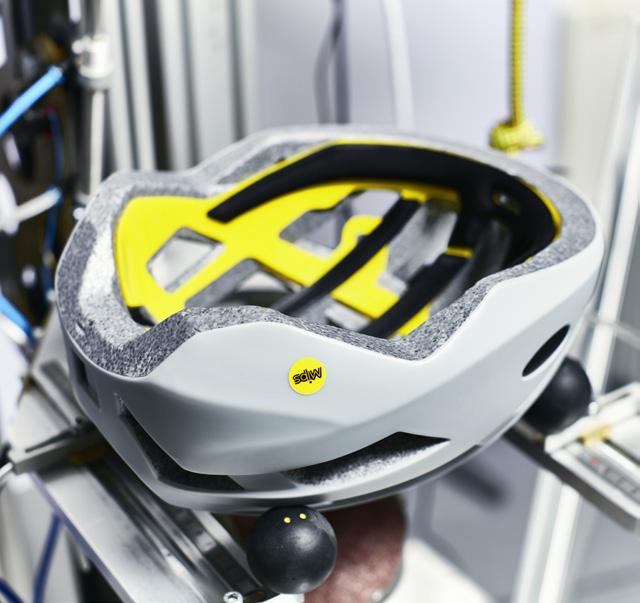
On standards and testing and the FIM…
Halldin: Now that EC 22-06 has met and started the revision of the motorcycle test standard they looked at the FIM, and for that the FIM has been very important. When it comes to the test standard then the ball had already been rolling. We started our work in 2012 and the FIM started theirs in 2014, I believe, and the good thing is that they came to more-or-less the same conclusion as we did within CEN TC158/Working Group 11, except that they choose a slightly different test headform. Both of us have made the same decisions when it came to simplifications for what is needed; like both test methods do not have or include the neck… which people could question because everybody in the world has one! But we both concluded that the existing neck form – Hybrid III - is not designed for the testing of helmets.
Strandwitz: We never publish our own test results because we think it is wrong for us to say ‘see what we have done at home…’ We rely very much on third party testing to make sure they communicate results. While there is no standard [for rotational acceleration] and people publish their own test results then I think it will confuse the consumer rather than educate them.
Halldin: I know the FIM have been working a lot to make this happen. Even though it is not perfect it is a very good first step and important for the whole helmet industry. The fact that there is a rotational element of the test standard for MotoGP is an important thing: that there is another dimension to helmet testing. There are other examples on the bicycle side. Now there is more of a debate about test points, impact angles, pass/fail criteria – but I think the most important thing right now is discussion, and that we are using the same or similar metrics for manufacturers when their design is being done and optimised. That optimisation should be done against the pass/fail metric that is used.
On the wide road for MIPS…
Strandwitz: Before we go into a category we always look for relevant injury criteria: can we make a difference or not? We are now entering construction. We have looked at how you actually hurt yourself on a construction site; what kind of damages or dangers are you exposed to? It is not only falling objects. You can trip, you can slip, you can fall, and you work at heights. We have validated our solution against those types of accidents and we see that we can make a big difference. We see a lot of interest from that category and a lot of construction companies coming to us to say: ‘how can we have solutions with MIPS?’ We looked at injury statistics in Europe and especially in Sweden because they are very well documented to see where we can make a difference and then we model those kinds of accidents in our computer system to make sure that we would add brain protection. We have that capability, which means a big advantage.
Halldin: We spent some time getting into the NFL Head Health programme – I or II – and we did not get any prize or funding at that time. They have been asking us to join again but it takes quite a lot of time. I have chosen to work on other matters. I would love to join that programme but the days are full enough already! Also, it is about building a full helmet…and we are about adding protection to an existing helmet. We’d need to team-up with a helmet manufacturer to participate.
On dealing with competition…
Strandwitz: I believe that competition is good because it makes you more agile, and that you always need to develop. I don’t think there are any industry benefits from the lack of competition. I think as long as people are trying to address a safety issue then this is great; it can be presented in a lot of different ways. Of course, we think we have a superior technology and have spent a lot of money trying to develop it. What I am more worried about is someone launching solutions that do not work that doesn’t enable the redirections of forces that would otherwise go into the brain. Other than that…if it works then I think it’s great.
Halldin: It’s fantastic. There should be competitors to MIPS. Comparing MIPS with others then I can only judge on what I have seen in other helmets on the market. Some of the other technologies don’t have that 10-15mm movement or full coverage. I am sure there are some solutions that will have all of this in their system but right now I cannot see it on the helmets on the market.
The wider pool…
MIPS are ground-breakers and the forefathers of addressing the seriousness of rotational acceleration, but they are not the only specialists trying to tackle the issue. Bell Helmets invented a three-layered EPS ‘Flex’ system in 2014, that borrows similar thinking to MIPS. 6D Helmets, based in California, fabricated an advanced Omni-Directional Suspension [ODS] construction that causes a series of dampers to shear as part of their radical energy management. Neck brace innovators Leatt worked on the same lines with their 360 Turbine tech.

6D Helmets ATR-2
“MIPS is doing great as a company and have had much success licensing the technology to many brands in a variety of different verticals, and that is good for the consumer,” says founder and MD Bob Weber. “There is not a lot of cost associated to the system, so it doesn’t impact the selling price of the helmet that much, and also there is not a lot of engineering required to insert it in a helmet. As a simple shear-plane within the helmet’s comfort liner it can provide reductions in certain impact scenarios and does make for a safer helmet offering compared to a traditional monolithic liner design utilized in most helmets out there.”
6D manufacture both street and off-road helmets and gathered significant praise and awards with their successful presence in the high-profile NFL Head Health campaign. The Americans have noted MIPS’ prolificacy as an ‘ingredient’ brand and are currently working to develop ODS as a more modular and ‘transportable’ entity. It is a mission that has seen some positive traction in their bicycle range but ODS is far more complex than MIPS’ BPS.
As staunch purveyors of the merits of ODS, 6D naturally believe MIPS broke the mould but there are slithers of cracks still visible. “MIPS is constrained to some degree by the shape of the human head and does not provide any improvement in low-threshold linear energy management,” opines Weber “which is very important when it comes to increasing a helmet’s capability to manage energy over a broad range of impact demands.”
Debate over the technicalities of systems to combat rotational acceleration and to ensure even more versatility of a crash helmet is – at this stage – to miss the point of what the likes of MIPS and 6D are fighting for, and that’s even more realisation of how a motorcyclists ‘lemon’ can be protected beyond the strength of some fancy-looking carbon. Helmet firms are taking note and are either embarking on their own expensive solutions or, like Troy Lee Designs, putting all their chips behind MIPS because it is the definitive reference.

Understandably the greatest degree of innovation is being seen in the discipline of motocross or off-road riding where crashes – usually from height – are more prevalent. 6D’s fi rst helmet was the ATR-1 MX model, Leatt placed the issue of rotational acceleration front-and-centre with their slim and narrow GPX 5.5 and Fly Racing’s Formula helmet caused sizeable ripples in the American market with the AIS (Adaptive Impact System) formed from Rheon technology. Fox, one of the most famous apparel companies in off-road and bicycle, were part of the MIPS programme and still have the yellow ‘dot’ on some of their helmet catalogue but their premier V3 moto helmet was relaunched in 2019 with Fluid Inside; a network of tough gel pods in the helmet that mimic cerebral spinal fl uid. Again the ‘movement’ philosophy paying a debt to the work of MIPS. The Swede’s curiosity with the Canadian product led to MIPS acquiring the company. R&D doesn’t stop.
“The primary reason to take on that technology is because they had some patents that we thought were quite interesting and we see a lot of entries into sharing patents and so-on,” Strandwitz explains. “We want to increase our patent protection and we see they have an interesting technology but we need to spend a bit more time on developing it before we want to include it into our MIPS assortment.”
Think of the motorcycle crash helmet since the 1980s and many areas of progression are visually obvious (aerodynamics, materials, visor, padding, emergency release systems, straps) but internally it could be argued that construction has not advanced at the same rate as other technological aspects of biking. MIPS has been a vanguard in this sense. For an appreciation of how this company has evolved awareness and protection of your brain then consider their position as winners of the Polhelm Prize; an award that ranks close to the Nobel prize and previous winners include creators of the zip, the refrigerator and the GPS. “It is a big recognition for Peter,” claims Strandwitz. “He has been instrumental to the whole industry through his work with MIPS but also KTH and has really educated the industry quite a lot. Peter and Hans got a lot of recognition and we piggyback on that when it comes to the company. They have worked more than twenty years developing this.”
Mercifully there is a better choice between rubber or compressed wood for crash helmets these days and, thankfully, as another decade starts there is every reason (and possibility) to think more about protecting the critical part of the body that bubbles all the chemicals generated by motorcycling.