
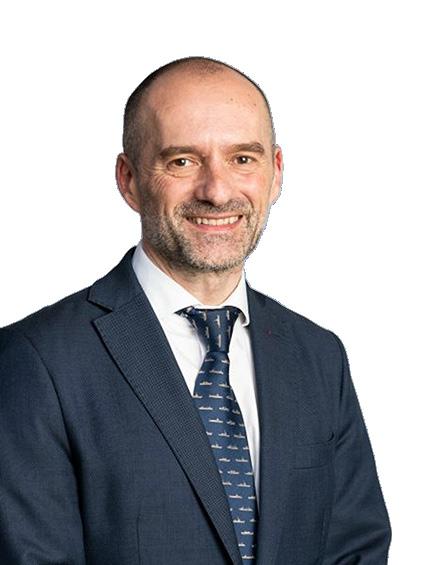
Africa Outlook, APAC Outlook, EME Outlook, North America Outlook, Mining Outlook, Healthcare Outlook, Manufacturing Outlook, and Supply Chain Outlook are digital publications aimed at boardroom and hands-on decisionmakers, reaching an audience of more than 800,000 people around the world. With original and exclusive content compiled by our experienced editorial team, we look to promote the latest in engaging news, industry trends and success stories from across the globe. Your company can join the leading industry heavyweights enjoying the free exposure we provide across our platforms with a free marketing brochure, extensive social media saturation, enhanced B2B networking opportunities, and a readymade forum to attract new investment and to help you grow your business. Visit www.outlookpublishing.com/work-with-us for details on how your company can feature for free in one of our upcoming editions.
EDITORIAL
Head of Editorial: Jack Salter jack.salter@outpb.com
Deputy Head of Editorial: Lucy Pilgrim lucy.pilgrim@outpb.com
Senior Editor: Lily Sawyer lily.sawyer@outpb.com
Editor: Ed Budds ed.budds@outpb.com
Editor: Rachel Carr rachel.carr@outpb.com
Editor: Lauren Kania lauren.kania@outpb.com
PRODUCTION
Art Director: Stephen Giles steve.giles@outpb.com
Senior Designer: Devon Collins devon.collins@outpb.com
Designer: Louisa Martin louisa.martin@outpb.com
Production Manager: Alex James alex.james@outpb.com
Digital Marketing Director: Fox Tucker fox.tucker@outpb.com
Website Content Manager: Oliver Shrouder oliver.shrouder@outpb.com
Social Media Executive: Jake Crickmore jake.crickmore@outpb.com
BUSINESS
CEO: Ben Weaver ben.weaver@outpb.com
Managing Director: James Mitchell james.mitchell@outpb.com
Chief Commercial Officer: Nick Norris nick.norris@outpb.com
REGIONAL DIRECTORS
David Knott david.knott@outpb.com Tom Cullum tom.cullum@outpb.com
PROJECT MANAGERS
Kieron Harvey kieron.harvey@outpb.com
Lauren Robinson lauren.robinson@outpb.com
Kierron Rose kierron.rose@outpb.com
Michael Sommerfield michael.sommerfield@outpb.com
Scarlett Burke scarlett.burke@outpb.com
HEADS OF PROJECTS
Callam Waller callam.waller@outpb.com
Deane Anderton deane.anderton@outpb.com
Eddie Clinton eddie.clinton@outpb.com
Ryan Gray ryan.gray@outpb.com Thomas Arnold thomas.arnold@outpb.com
TRAINING & DEVELOPMENT DIRECTOR Joshua Mann joshua.mann@outpb.com
SALES & PARTNERSHIPS MANAGER Donovan Smith donovan.smith@outpb.com
SALES MANAGERS Alfie Wilson alfie.wilson@outpb.com Krisha Canlas krisha.canlas@outpb.com
ADMINISTRATION
Finance Director: Suzanne Welsh suzanne.welsh@outpb.com
Finance Assistant: Suzie Kittle suzie.kittle@outpb.com
Finance Assistant: Victoria McAllister victoria.mcallister@outpb.com
CONTACT
Manufacturing Outlook Norvic House, 29-33 Chapelfield Road
Norwich, NR2 1RP, United Kingdom
Sales: +44 (0) 1603 804 445
Editorial: +44 (0) 1603 804 431
SUBSCRIPTIONS Tel: +44 (0) 1603 804 431
jack.salter@outpb.com www.mfg-outlook.com
Like us on Facebook: facebook.com/manufacturingoutlook Follow us on Twitter: @outlookpublish
Welcome to our fourth edition of Manufacturing Outlook magazine.
On this issue’s radar is global security and aerospace company and transformative defence technology specialist, Lockheed Martin.
The provider of choice for advanced radars and sensors, Lockheed Martin has a rich history of cutting-edge systems that are the proven, preferred air surveillance solution for more than 45 nations on six continents and counting.
We learn about its broad legacy of producing high-performing, solid-state radars in an in-depth interview with Chandra Marshall, Vice President and General Manager of Lockheed Martin Radar and Sensor Systems.
“Our customers face threats that require us to deliver innovation at scale and with greater agility than ever before to address their toughest challenges,” says Marshall, who is responsible for the company’s entire radar and sensor portfolio for domestic and international clients.
“Over the past 60+ years of delivering radars, we have proven that each system meets the technical requirements defined by the customer.”
Whereas the majority of Lockheed Martin’s business is with the US Department of Defense and federal government agencies, Navantia Australia is dedicated to delivering world-class engineering and design services to the Royal Australian Navy (RAN).
We outline the Design Authority’s commitment to excellence and journey to deliver a sovereign design capability for the country.
“We are responsible for over 60 percent of RAN’s surface fleet,” reveals Israel Lozano, Executive Managing Director.
“Since our establishment in 2012, we have grown and matured to become a strategic defence company and Design Authority for Australia in our own right.”
At the cutting edge of defence in Africa, meanwhile, is Saab Grintek Defence, whose integrated electronic warfare self-protection systems are widely used across the sector.
Indeed, having supplied its systems to over 20 countries around the world, Saab Grintek Defence continues to maintain and expand its success across Europe, the Middle East, Asia Pacific, and Latin America.
“Our extensive global footprint provides us with a distinct advantage, allowing us to deliver unmatched support and solutions on a worldwide scale,” states President and Managing Director, Jan Widerström.
Defence aside, this issue also covers Arrowquip’s leading livestock equipment, Nexus RV’s superior motorhomes, Resonac Graphite Business Unit’s bestin-class graphite electrodes, and much more from across the manufacturing industry.
We hope that you enjoy your read.
Jack Salter Head of Editorial, Outlook Publishing
28 SHOWCASING LEADING COMPANIES
Tell us your story and we’ll tell the world
NORTH AMERICA
30 Lockheed Martin
Ahead of Ready
At the forefront of threat detection
48 Invio Automation
Setting the Future in Motion
Proven automation to accelerate global businesses
48
58 QinetiQ Target Systems
Navigating a Complex Threat
Environment
The next generation of defense manufacturing
66 Nexus RV
Building Your Dream
Superior motorhomes that continue to thrive
74 Waterville TG
Masters in Adaptive Sealing Solutions
Leading the way in value-added weatherstripping
82 Arrowquip
Equipped to Handle Cattle
Best-in-class livestock equipment
88 CPI Aero, Inc.
First-Rate Aerospace Assembly and Integration
Combining a small business culture with global corporate capabilities
94 Kentucky Trailer
Revolutionizing the Road
Providing custom transport solutions
Imagine, Innovative, and Integrate
Product development from conception to industrialization
Avionics Precision, Accuracy, and Support
Providing high-quality, next-generation air data systems incorporating known future requirements
The Perfect Production Platform
Connecting the US with innovative transport
128 Yakima Products Inc.
Designed for Adventure
Traverse the open road in style
132 Dorsey Trailer
A Trailblazing Journey
Over a century of specialty trailer production
138 Navantia Australia
Innovation Where it Matters
World-class engineering and design services
EUROPE &
154 Resonac Graphite
Business Unit
The Power of Chemistry
Supplying best-in-class graphite electrodes
166 Agrostroj Pelhřimov
A Leader in Industrial Production
Comprehensive production solutions for global players
172 Saab Grintek Defence
At the Cutting Edge of Defence
Committed to continuous development and innovation
180 NewSpace Systems
Enabling Exploration Through Innovation
Advancing the aerospace industry in Africa
188 ACTOM
High Voltage Ingenuity
The one-stop shop for global energy
WILL A Labour government affect UK manufacturing, and in what ways?
While the party’s manifesto presents no radical changes in its approach to the industry, it recognises advanced manufacturing as an area of strength and outlines funding for the automotive and steel sectors.
However, there is minimal recognition of the manufacturing sector as a whole, which is only mentioned four times in the manifesto.
Despite not being a major focus, there is an emphasis on the importance of economic stability across the country.
Labour claims to offer a stable business environment for manufacturing businesses that will create a more favourable investment climate.
US ENGINE manufacturer, GE Aerospace, has partnered with NASA on a new initiative to create an electric-powered aircraft. Commercial aviation requires many tests prior to use, including examination of the engine, electrical systems, and developed hybrid technologies.
CARLSBERG HAS agreed to buy UK drinks manufacturer Britvic in a compelling £3.3 billion deal.
A single beverage company called Carlsberg Britvic is to be created by the Danish brewer in order to expand its business in the UK and Western Europe and capture growth opportunities in multiple drinks sectors.
Carlsberg believes that the acquisition will add some diversification to the company’s portfolio as younger age groups today are less likely to heavily indulge in alcohol.
As well as owning popular brands such as Robinsons and J2O, Britvic holds an exclusive licence with PepsiCo. The takeover will give Carlsberg the opportunity to expand its own global partnership with the US drinks giant.
The objective is to increase fuel efficiency and, in turn, reduce CO2 emissions by 20 percent. Phase two of the project, creating compressors and aerodynamic turbines, is expected to take place in 2028.
It is hoped this industry push will aid the process of reducing demand for electric power across the world. A current focus globally is sustainability, which is at the forefront of business development, particularly in the automotive industry. As such, this evolution is a step in the right direction.
BAKER & BAKER, one of Europe’s leading suppliers of bakery products, recently invested £2.9 million to increase the capacity of its cookie production line in Merseyside, UK.
The company supplies a variety of products including doughnuts, muffins, brownies, cakes, and cookies. As well as having an exclusive
manufacturer, Volkswagen (VW), is recalling over 300,000 vehicles across North America due to faulty wiring attached to the front passenger airbag when the seat is occupied, potentially posing a safety risk in the event of a crash.
Specifically, the Atlas and Atlas Cross Sport models, which are among VW’s best sellers in the US, have been recalled as a precautionary measure due to issues in the passenger occupant detection system (PODS).
VW has assured customers that the sensor mat and harness parts will be replaced free of charge.
The National Highway Traffic Safety Administration (NHTSA) has advised vehicle owners to avoid using the front passenger seat when possible until the recall repair has been performed.
licensing contract with The Walt Disney Company, the business has full ownership of all its brands, whilst all bakery products are manufactured across six European countries to be sold across the world.
Baker & Baker’s investment contributed to improved workspaces and machinery, as well as upskilling its teams. In October 2023, it reported annual sales of £480 million, making the company a market leader in the industry.
THE MODERN world relies heavily on digital and technological development. As such, economic growth depends on the power of artificial intelligence (AI) in the manufacturing industry, which aids with optimising operations, reducing costs, and responding to business fluctuations.
This digital era is helping the sector adapt to the current market as it minimises costs whilst maintaining production levels and sustainability requirements.
9.3 percent of economic output and 8.1 percent of employment across the UK comes from manufacturing, and experts are beginning to recognise the benefits of investing in advanced technology for the industry.
THE GLOBAL slowdown in electric car sales is forcing companies in Europe’s nascent battery industry to cancel or postpone projects.
A pullback in investment plans has been caused by slow consumer uptake and competition from Chinese cell manufacturers.
With battery-powered vehicle sales only growing 2.4 percent in the region in the first five months of 2024, European car companies have scaled back their electrification plans. Forecasts for battery-run car sales in Europe have been slashed by 15 percent for 2030 as a result.
Battery start-ups in Europe have been hit by a series of major setbacks in recent months, with Northvolt recently launching a strategic review that could delay new factories in Germany, Canada, and Sweden.
With thousands of global environmental regulations, taking a proactive approach to sustainability is more important than ever. David Evans, Head of Manufacturing at ServiceNow, discusses how digital transformation can revolutionise environmental, social, and governance (ESG) reporting in manufacturing to ensure compliance and meet stakeholder expectations
Writer: David Evans, Head of Manufacturing, ServiceNow
We’ve talked about it, thought about it, and maybe even piloted it, but why are too many organisations still finding themselves in the slow lane when it comes to delivering ESG objectives and becoming a digitally enabled enterprise?
Like it or not, with the first reports under the EU’s Corporate Sustainability Reporting Directive due in January 2025, the time to take action is here and now. Leaders in the sector need to adopt new digital workflows to truly understand their ESG data and make progress on this issue.
With more than 2,400 ESG regulations now in force across 80 different jurisdictions around the world, ESG reporting is right at the top of the corporate agenda for manufacturers. For organisations to get this right and reap the rewards, it requires new, digital ways of working and more collaborative (and perhaps difficult) conversations with suppliers. Investors also increasingly see sustainability and ethical labour practices as being on par with corporate governance and even financial performance when valuing companies.
For manufacturers, the move
towards improved ESG performance is happening in parallel with a shift towards technology-based ways of working, with digital workflows and the adoption of technologies such as sensor-filled ‘smart factories’.
According to KPMG’s Global Industrial CEO Outlook, ESG initiatives now rank among the top operational priorities (15 percent) for manufacturing CEOs, alongside a shift towards digitising and advancing connectivity across the business (22 percent). For leaders in the sector, ESG is seen as linked to the company’s wider performance, with CEOs fearing recruitment challenges if ESG goals are not met (22 percent) and a quarter fearing difficulty in raising finances. However, while manufacturers are aware of the urgency of modernising their approach to ESG, gaps still remain, particularly around the reporting of emissions from supply chains.
Manufacturing accounts for 24 percent of global greenhouse gas emissions, but tracking ESG
compliance amongst suppliers remains a key ‘blind spot’ for the sector, with just 19 percent of manufacturers disclosing full data related to Scope 3 emissions. Digital workflows will allow business leaders to tackle this key issue at speed.
With increasing pressure to deliver on ESG issues coming from all angles, including regulators, investors, customers, and employees, the ‘old ways’ of measuring ESG are simply not enough: a new, digital approach is required. Recording ESG objectives at each stage in the supply chain manually and entering this data into spreadsheets is simply too slow. To fast-track efforts to achieve ESG objectives, business leaders need to embrace automated tools integrated into other systems and dynamic tracking.
Digital workflows and tools to track ESG progress will allow business leaders to track compliance
in real-time right across the supply chain. Leaders in the supply chain sector are also acutely aware of the importance of investing in technology, with 50 percent of supply chain leaders saying they plan to invest in technologies such as advanced analytics in the coming year, according to KPMG’s Supply Chain Trends 2024 report.
Leaders in the manufacturing sector must work closely with suppliers to drive ESG performance. Strategic supply chain management can help businesses cut costs and drive innovation while boosting sustainability. Standardising supply chain reporting is complex, and businesses must work closely with suppliers, adopting technologies to share data and track progress.
Delving deep into the supply chain to ensure that Tier 1 and Tier 2 suppliers use sustainable components will boost the strength of manufacturing companies in the future. Airbus, for example, is digitally optimising its procurement and management processes to boost ESG compliance. It is working closely with its 12,000 global suppliers to choose materials that are sourced ethically and responsibly, which have a lower impact on the environment.
The key to achieving ESG goals is having a ‘single source of truth’ for all ESG and sustainability goals and disclosures. This is why it’s so important to adopt digital workflows which offer a view of the organisation’s past and present ESG story in one place. Adopting digital workflows means that leaders in the sector can aggregate and validate data automatically, making disclosure easier and more reliable.
Business leaders must opt for platforms which link business systems such as enterprise resource planning (ERP), factory systems,
and purchasing together to increase visibility across the enterprise. Armed with this information, it’s easier to oversee operations to increase regulatory compliance and build simplicity into supplier relationships, even when facing unexpected disruptions.
In today’s world, ESG performance is no longer a nod towards a company being ‘good’ on social and environmental issues; it’s key to driving long-term financial performance and satisfying investors. Edelman’s Trust Barometer 2020 found 88 percent of investors say that companies that prioritise ESG initiatives represent better opportunities for long-term results, and 92 percent say that companies with strong ESG performance deserve a premium valuation of their share price.
Manufacturers today are rightly focused on costs, thanks to ongoing pressures such as inflation and energy costs. The adoption of digital workflows to measure ESG performance and to engage and share data across the supply chain can also drive efficiencies across the organisation, boosting growth, reducing costs, and paving the way for future innovation.
Adopting digital workflows will be a key part of every manufacturer’s sustainability journey, with automated tools and dynamic tracking helping manufacturers tackle sustainability, even in the sector’s ‘blind spot’ around the supply chain. To do so requires manufacturers to work closely with suppliers and for both to shift towards smarter digital workflows. This will not only help leaders comply with the thousands of ESG regulations around the world but also drive long-term value for the business.
With over 40 years of experience in the ever-evolving aerospace industry, Unison stands out as a leader of innovation and reliability
Writer: Jack Salter
Every two seconds, an aircraft equipped with Unison technologies takes off somewhere in the world, underscoring the company’s pivotal role in global aviation.
Unison, a GE Aerospace company, has thus established itself at the forefront of providing differentiated controls and engine performance monitoring products in the aviation, defense, and space segments.
Having developed products and services for three generations of aerospace propulsion systems, Unison
is committed to ensuring reliable operation in high-temperature and high-vibration engine environments.
With a robust workforce across several locations worldwide, the company operates seven manufacturing plants and four Federal Aviation Authority (FAA) overhaul/repair stations, ensuring its advanced systems and components maintain the highest standards of quality and performance.
This extensive network enables Unison to deliver unparalleled support and solutions to its customers,
reinforcing its reputation for excellence in the aerospace industry.
“Our customers look to us to solve the toughest problems in advancing the future of sustainable aviation and affordable space,” opens Kranthi Tata, President and CEO of Unison.
“This puts an immense responsibility on us to prioritize safety, quality, and performance for our customers, delivering precise and scalable innovations to tackle their most formidable challenges.”
Unison’s product portfolio includes advanced ignition and fluid delivery systems, thermal management solutions, power generation, sensors and switches, harnesses, and air turbine starters, each engineered to provide the highest level of performance under the most challenging conditions.
Innovation and excellence are exemplified by Unison through its advanced engineering and manufacturing capabilities. By investing heavily in expanding the quality, performance, and reliability of its current products while developing next-generation technologies, the company is committed to enabling the future of flight.
With a mission deeply rooted in ensuring the well-being of every individual, Unison’s portfolio of products is a testament to its values of excellence, reliability, and humanity.
From state-of-theart ignition systems
to innovative components, every product Unison develops is infused with a sense of purpose – to elevate the human experience and ensure a safe return home.
“Flying connects us to the people we love, transports us to the places we dream about, protects and defends us, and brings the world closer together. Our mission is to lift us all to even greater heights,” states Tata, who embodies the company’s ethos of innovation and excellence.
Tata’s journey to the helm of Unison is as inspiring as it is impressive.
Growing up in India, he was the son of a hardworking farmer and a dedicated teacher, both responsible for igniting his passion to make a difference in the world.
With dreams of becoming a naval fighter pilot, Tata charted a path that combined his passion for aviation with his aptitude for technology. He pursued a Bachelor of Science in Electronics and Communication Engineering from Bharathidasan University and later earned a Master of Business Administration from Cornell University.
With nearly 25 years of experience in industrial business, Tata has led teams and managed operations across multiple countries, bringing a wealth of knowledge to his role at Unison.
His leadership is characterized by a deep respect for people, building a culture of continuous improvement, and an
Engineering expertise and customer partnerships are key elements to the success of Unison, whose engineers follow a meticulous and structured design process.
This rigorous approach includes comprehensive design reviews, manufacturability assessments, and project/design tollgates. These stages involve subject matter experts both internally and across the industry, as well as cross-functional business teams to ensure a holistic and thorough evaluation.
Governed by well-defined procedures and instructions, these reviews guarantee adherence to technical requirements, process controls, and configuration management.
One of Unison’s key strengths lies in the colocation of its design engineers at the sites where products are built. This proximity fosters direct interaction between commercial, design, and manufacturing teams, ensuring seamless communication, highquality outputs, and the prompt resolution of any issues that arise.
unwavering commitment to solving tough customer problems with technological advancements and lean operations. He is likewise very committed to diversity, equity, and inclusion, and gets his inspiration from his wife and two daughters.
With Tata at the forefront, Unison is not only shaping the future of aerospace with a safety first approach, but also exemplifying the values of leadership, resilience, and innovation that define the modern aviation landscape.
At the heart of Unison’s success in the aerospace industry is its steadfast
pride in its people. The company recognizes that its greatest asset is not its cutting-edge technology or advanced manufacturing processes, but the dedicated individuals who bring their expertise, creativity, and passion to work every day.
Unison’s commitment to fostering a supportive and empowering environment for its employees is a cornerstone of its business strategy, driving innovation and ensuring sustained excellence.
The diverse tapestry of Unison’s skilled professionals is not only embraced but celebrated, as it brings a wide range of perspectives and ideas to the table.
Unison understands that innovation thrives in an environment where different viewpoints are encouraged and valued. This inclusive culture is instrumental in solving complex problems and pushing the boundaries of what is possible in aerospace manufacturing.
The company therefore invests heavily in the continuous development of its employees to foster a culture of continuous learning and improvement, which is crucial in an industry as dynamic and demanding as aerospace.
Whether navigating the complexities of global supply chains or pioneering new technologies, it is the people of Unison who drive the company forward, embodying the core values of integrity, innovation, and excellence.
Environmental testing is crucial for validating the functionality, durability,
and reliability of Unison’s component designs under the harsh conditions they are expected to endure.
Each engineering site is equipped with in-house test facilities for environmental qualification and product certification, operated by experienced test personnel.
These facilities conduct a wide array of tests, including:
• Vibration testing: To simulate the stresses encountered during operation.
• Mechanical shock testing: To assess component resilience against sudden impacts.
• Thermal testing: To ensure performance across a range of temperatures.
• Electrical testing: To verify electrical integrity and functionality.
• Waterproof testing: To confirm resistance to moisture and water ingress.
• Humidity testing: To evaluate performance under varying humidity levels.
• Lightning and EMI/EMC testing: To ensure electromagnetic compatibility and resistance to electromagnetic interference.
Additionally, Unison utilizes endurance test cells and setups to confirm component operability over extended durations and high cycles. These tests simulate typical and extreme operating conditions, providing assurance of long-term reliability and performance.
The company’s commitment to delivering high-performance solutions is matched by its support for aftermarket mechanical and electrical repairs.
“No one knows Unison better than Unison. Utilizing our original equipment manufacturer (OEM) equipment and expertise, we ensure every repair meets the highest
standards and performs at its best,” prides Engineering and Technology Leader, Josh Friedman.
Over the years, Unison has consistently demonstrated its ability to adapt, innovate, and deliver, cementing its reputation as a leader in aerospace manufacturing.
At the core of Unison’s capabilities lies its commitment to cuttingedge technology and continuous
improvement. The company’s manufacturing processes are infused with advanced automation, robotics, and data analytics, enabling unparalleled precision and efficiency.
This technological backbone ensures that every component produced meets the stringent quality standards necessary for aerospace applications, where even the smallest imperfection can have significant consequences.
Unison’s facilities are equipped with advanced machinery
Unison is comprised of seven key product lines that integrate engineering design, manufacturing, and aftermarket services:
IGNITION SYSTEMS – Unison’s state-of-the-art ignition systems have not only ignited rockets but also played a critical role in bringing astronauts home safely on numerous space missions.
POWER GENERATION – The company’s permanent magnet generators (PMGs) boast millions of hours of proven field experience and deliver best-in-class power density and reliability.
SENSORS AND SWITCHES – Speed and temperature sensors and limit and pressure switches are designed for the most demanding environments and crucial for ensuring safety and performance in critical aerospace operations.
HARNESSES – Engineered for integral applications exposed to high temperatures, vibration, and electromagnetic interference, Unison’s customized harness solutions are a testament to its innovative approach.
FLUID DELIVERY SYSTEMS – Through a design assist program, Unison works closely with customers to optimize designs for producibility, resulting in highly efficient and durable fluid delivery systems.
THERMAL MANAGEMENT SOLUTIONS – In the realm of thermal management, Unison offers advanced air-cooled oil coolers and heat exchangers designed to provide effective thermal regulation, ensuring the optimal performance and longevity of aerospace components.
AIR TURBINE STARTERS – Unison, through its industrial brand TDI Tech Development, is a worldwide leader in the design and manufacturing of unique twin turbine powered air starters.
that support a wide range of manufacturing techniques, from traditional machining to additive manufacturing. This versatility allows Unison to produce complex and high-performance components that are essential for modern aerospace systems.
Moreover, Unison’s workforce is a blend of seasoned professionals and forward-thinking engineers who bring a wealth of experience and innovation to the table. The company places a strong emphasis on continuous
learning and development, ensuring that its team is always at the forefront of technological advancements.
Unison’s relentless pursuit of excellence means it remains a key player in the aerospace industry, capable of meeting the evolving needs of its customers and the challenges of the future.
“FLYING CONNECTS US TO THE PEOPLE WE LOVE, TRANSPORTS US TO THE PLACES WE DREAM ABOUT, PROTECTS AND DEFENDS US, AND BRINGS THE WORLD CLOSER TOGETHER.
OUR
MISSION IS TO LIFT US ALL TO EVEN GREATER HEIGHTS”
– KRANTHI TATA, PRESIDENT AND CEO, UNISON
Today, the mission of Unison is clear – to deliver innovative, reliable solutions that meet the highest standards of safety and performance.
The aerospace industry is proving to be more demanding than ever, requiring the highest level of quality and a future focused on innovation.
“In today’s rapidly evolving aerospace industry, our unwavering
commitment to excellence is reflected in our comprehensive product portfolio, which is designed to meet the rigorous demands of modern aerospace and industrial applications,” affirms Alok Patel, Product Management Leader at Unison.
With modern aircraft and engines becoming increasingly technologically advanced and sophisticated, it necessitates the development of more complex systems and components.
“Now is a pivotal time in the aerospace industry. With travel
continuing an upward trajectory, and the rapid growth of commercial space launches, this further emphasizes the opportunity for emerging sustainable products and technologies,” echoes Tata.
To harness the opportunities ahead, Unison has outlined several key business priorities. Central to its strategy is the development and empowerment of its people through GE Aerospace’s proprietary lean operating system, FLIGHT DECK.
The FLIGHT DECK system is designed to foster a culture of continuous improvement, efficiency, and excellence, ensuring that Unison’s workforce is well-equipped to meet evolving industry demands.
“FLIGHT DECK is the ‘how’ - how we bridge strategy to results, and how we implement over time to deliver sustainable results. That is what matters most for our customers and shareholders,” Tata tells us.
With a mission deeply rooted in ensuring the well-being of every individual, Unison’s portfolio of products is a testament to its values of excellence, reliability, and humanity.
From state-of-the-art ignition systems to innovative components, every product Unison develops is infused with a sense of purpose – to elevate the human experience and ensure a safe return home.
By heavily investing in the expansion and enhancement of its product capabilities, Unison is not only addressing the current demands of the aerospace industry but also paving the way for future advancements.
The company’s dedication to rigorous engineering practices and comprehensive testing reiterates its commitment to delivering safe, reliable, and innovative solutions that will define the future of flight. Through its advanced systems,
global reach, and visionary leadership, Unison is charting a course for a future where aviation is safer, more efficient, and more reliable than ever before.
As the company continues to soar to new heights, its impact on the aerospace industry today, tomorrow, and to come remains undeniable.
“Our ambition is to be the leading provider of differentiated controls and engine performance monitoring solutions in aerospace, defense and space segments, meeting the needs of our customers and supporting the future of sustainable aviation,” concludes Tata.
The executive team at UTS Rapido takes us on a deep dive into the R&D engineering and technology innovation hub at the University of Technology Sydney and how it is making waves by delivering solutions that create industrial and societal impacts
Writer: Lauren Kania
Founded in 2016 by Executive Director, Hervé Harvard, who sought to bridge the gap between academia and industry, UTS Rapido is an impact-focused R&D innovation hub embedded within the University of Technology Sydney (UTS) that is committed to creating a
positive impact and solving real-world challenges.
“By collaborating with research teams, government entities, and clients from diverse sectors, we leverage our R&D expertise in software, mechatronics, and user experience (UX) digital solutions to
innovate new products and services that address specific needs and deliver tangible benefits,” introduces Harvard.
With a workforce of high-level problem-solvers who boast decades of commercial technology development experience, Harvard
leads his team of professional engineers and R&D experts, in collaboration with UTS, to deliver projects for industry and social impact partners.
As an accomplished technology leader and intrapreneur with over 25 years experience in innovation, Harvard is a strong advocate for industry-university collaboration and has a rich background in leading teams in the digital innovation space for large multinationals, including Canon, Siemens, and Philips.
With this vast experience, alongside
the dedicated passion of the UTS Rapido team, the R&D unit utilises customer-centric professionalism and strategic engagement to enable entry into a comprehensive universitywide engineering and IT innovation ecosystem.
The organisation’s unique approach blends commercial R&D experience, academic expertise, and access to state-of-the-art facilities to reliably test, innovate, and commercialise new products and services.
The UTS Rapido team works closely with clients, taking industry ideas and
concepts from the initial research stage to market-ready solutions.
“We provide a multidisciplinary innovation hub with professional R&D engagement and project management, offering the possibility of a fully outsourced R&D workforce,” expands Harvard.
This gateway to a university-wide ecosystem allows clients to take advantage of both the experienced and professional team at UTS Rapido, alongside UTS, a leading technology institute rated among the top 100 universities worldwide and the number one ‘young’ university in Australia.
The mission to bridge the gap between industry and academia has been embedded into the core of UTS Rapido since its inception.
One of the primary ways in which the R&D unit is able to accomplish this goal is due to its location in the Faculty of Engineering and IT at the UTS campus.
“Our professional engineers, R&D experts, and skilled project managers collaborate with UTS’ researchers, facilities, and labs to deliver projects for our industry and social impact partners,” details Harvard.
“Bridging the gap between academia and industry increases the possibilities for external partners to leverage the technical excellence available through UTS.”
Industry partners can gain access to diverse capabilities, funding grants, and collaborative opportunities with a leading university, alongside the chance to harness a commercially focused R&D team.
UTS Rapido offers a variety of services to its clients, with three primary capabilities consisting of software, mechatronics, and UX and digital solutions.
The UX team consists of strategic engineers who spearhead the creation of invaluable methods for
developing real-world, user-centric solutions.
“Our market-driven strategy delivers digital solutions that maximise productivity and engagement. By utilising collaborative design and validation methods, we gain a deep understanding of the needs of our partners’ businesses, segments, workforce, and end users within their specific contexts and environments.” explains Julie Kowald, Principal Delivery Manager UX and Digital Solutions, UTS Rapido.
The engineering team that heads UTS Rapido’s mechatronics service provides expertise in a range of engineering disciplines, including mechanical, electronics, embedded software, and control systems.
“We create innovative and effective solutions for routine and novel mechatronic challenges,” Harvard explains further.
UT Rapido’s software engineering team applies analytical thinking, engineering principles, methods,
“BY COLLABORATING WITH RESEARCH TEAMS, GOVERNMENT ENTITIES, AND CLIENTS FROM DIVERSE SECTORS, WE LEVERAGE OUR R&D EXPERTISE IN SOFTWARE, MECHATRONICS, AND UX DIGITAL SOLUTIONS TO INNOVATE NEW PRODUCTS AND SERVICES THAT ADDRESS SPECIFIC NEEDS AND DELIVER TANGIBLE BENEFITS”
– HERVÉ HARVARD, FOUNDER AND EXECUTIVE DIRECTOR, UTS RAPIDO
tools, and techniques to the design, development, and maintenance of advanced, cost-effective software solutions. It works hard to ensure that large, complex, and critical software systems are interwoven into daily life and accurately fit the intended purpose.
“Our team members specialise in developing not only industry-ready mobile, web, and cloud solutions, but also more advanced computing technologies such as gaming, data science, artificial intelligence (AI) and machine learning (ML), 3D geometry processing, and computer vision,” asserts Raj Calisa, Principal Delivery Manager Software at UTS Rapido.
In order to develop cutting-edge products and services, UTS Rapido supports start-ups, small to mediumsized enterprises (SMEs), and corporations by providing R&D engineering and technology solutions.
“When we partner with industry, our projects can range from end-toend solutions to smaller projects that fill an expertise gap. We collaborate and apply research findings to our services within world-class facilities to support organisations of all sizes,” details Harvard.
The team’s expertise spans a wide range of industries, including agriculture, healthcare, infrastructure, defence, manufacturing, mining, retail, technology, transportation, and education, allowing it to work with individuals who possess brilliant ideas, community groups seeking solutions,
SOFTWARE – UTS Rapido applies analytic thinking and engineering principles, methods, tools, and techniques to the design, development, and maintenance of bespoke software solutions.
MECHATRONICS – The innovation hub solves industry problems by designing, analysing, testing, and manufacturing intelligent systems using mechanical and mechatronic engineering techniques.
UX AND DIGITAL SOLUTIONS – UTS Rapido creates value-generating digital solutions by identifying the needs of businesses, their markets, and endusers, as well as designing, developing, and deploying innovative solutions in software and hardware.
RESEARCH TRANSLATION – UTS Rapido helps to bridge the gap between knowledge gained through research and its application in practice to help deliver market-ready solutions.
and various other organisations aiming to drive innovation.
UTS Rapido provides additional support by helping not-for-profit partners. Since 2017, the innovation hub has donated significant time and resources to purposeful organisations in order to create positive change.
“The for-purpose sector, which is often limited by budgets and a lack of skilled technical talent, faces challenges in embracing technological innovation,” insights Harvard.
“By leveraging our R&D engineering expertise, academic knowledge, and advanced facilities, we pursue impactful collaborations on projects aimed at developing technology-driven solutions for societal challenges.”
The university-based initiative is passionate about giving back and providing affordable technology solutions for organisations that prioritise making a difference.
Specifically, it helps for-purpose organisations with limited access to
Hervé Harvard, Founder and Executive Director: “We have collaborated closely with Navantia Australia since mid-2020 to deliver R&D projects, with ongoing collaborations around digital twin, ship routing, training gamification, situational awareness systems, and anomaly detection using deep learning models.
“Our software and UX teams are at the forefront of our collaboration, with the aim of developing sovereign digital technologies for the maritime industry. This partnership culminated in the Maritime Institute of Technology (Marintec™).
“R&D collaborations between UTS Rapido and Navantia Australia through Marintec™ are instrumental to our partnership. We contribute software engineers and expert UX teams to enhance user experience and develop cutting-edge solutions. Leveraging Navantia Australia’s domain expertise, mathematical models for naval vessels are developed, forming the foundation for our software architecture.
“The success of our projects hinge on our collaborative efforts as three distinct entities, underscoring the importance of the unified innovation ecosystem we cultivated together.
“Our collaboration on joint projects has spanned multiple years and iterations, drawing input from subject matter experts in the team from both industry and academia spanning multiple fields, including robotics, UX, software engineering, and naval engineering.”
technological innovation to overcome budget constraints or expertise gaps, utilise engineering and technology-based solutions, and leverage cutting-edge technologies.
Additionally, UTS Rapido assists partners in accessing grant funding opportunities to further their research and projects.
“We understand the financial challenges associated with innovation projects. That’s why we have helped our partners access Australian government grants, through which 80 percent of our innovation projects were partfunded in 2022,” prides Harvard.
With a deep understanding of the social impact space, UTS Rapido is committed to driving positive change in the world beyond its campus as it continues to look towards the future.
We examine how artificial intelligence has revolutionised food manufacturing for the better, with enhanced efficiency, earnings, and expansion leading to successful supply chains and accurate product distribution
Writer: Imogen Waters
In the modern world, the phrase ‘less is more’ no longer applies – food manufacturing only wants more.
Artificial intelligence (AI) aids in this process by ensuring efficiency and safety so products fulfil regulatory requirements and make for happy customers.
Today’s extensive food manufacturing supply chain has been streamlined and accelerated as a result, with AI and other technologies helping at every stage.
Food is a necessity for all and, no matter what, shelves must be filled. In terms of aiding production, AI can forecast crop yields and upcoming weather, meaning any eventuality can be prepared for in advance to avoid wasting all-important harvests. Technology is also capable of
tracking distribution and inventories, a laborious job that no longer needs to be carried out by employees thanks to the introduction of viable, smart alternatives.
As of 2024, the global food industry is valued at USD$9.8 billion and is expected to grow to almost USD$50 billion within the next five years.
To bolster this statistic, it is anticipated that AI will be able to reduce costs in the agriculture industry by 20 percent. With growing revenue in the sector and overhead expenditures dropping, profits are therefore expected to increase.
Subsequently, AI understands variables and can therefore anticipate future scenarios to ensure revenue growth is steady across the supply chain.
Data and the manufacturing industry are intrinsically linked; where technology was once prevalent, drones, sensors, and satellites have since become the modern data collection system.
Optimising crop yields relies on detecting pests and diseases. In this way, AI is able to log environmental conditions such as temperature, humidity, soil fertility, and nutritional properties in a process known as smart farming, an automated affair which reduces labour costs and speeds up the collection process.
Globally, one in nine people are thought to be undernourished, whilst one third of food is wasted yearly. Due to analytics previously misinterpreting these statistics, it is hoped that new technologies, including AI, will gather more precise results for crop yields, thereby reducing waste across the
globe and allowing food to be more fairly distributed to those who need it most.
New technologies can additionally determine forecasting to improve storage practices for perishable goods and monitor temperatures to enhance product freshness.
Food safety is an integral part of the manufacturing process that has been improved by the introduction of advanced technologies and AI.
Monitoring and traceability enhance procedures as problems can be prevented as soon as they are flagged. Therefore, issues which were previously complex and time consuming for employees have been simplified by technologies, such as those used to detect and prevent contamination and bacteria.
Critical elements of food
production such as sanitation, humidity, and temperature are under constant surveillance to provide realtime data, alerting of bacteria and any other potentially harmful incidents before they occur.
There is potential to grow the power of AI in the future by improving quality, monitoring, tracing, nutrition, and risk assessments which, in turn, will ensure food safety.
Another element of protection is detecting safety issues amongst staff. For example, not wearing gloves is a problem on the shop floor, which can be detected through cameras to alert supervisors of any health and safety issues.
Furthermore, thermal imaging cameras monitor equipment and its cleanliness, inspect packaging, automate scales to ensure uniform products, and uphold high-quality process controls.
Developments in technology will drastically change the food manufacturing industry, but at what cost?
The first use of automation focused on repetitive tasks so they no longer needed to be completed by humans, which resulted in job losses. Since then, AI has enhanced food manufacturing processes such as packaging and assembly even further, enabling more efficiency but at the expense of workers.
The introduction of AI also presents a financial barrier to the industry. Whilst smaller companies lack the level of data which makes it worthwhile, large businesses with greater quantities of data can incur high costs when implementing AI technologies and systems across the board.
Even then, the cybersecurity of these systems is not always fully secure as they can suffer from data breaches and unauthorised access, meaning their safety is never completely assured.
Finally, due to the complexity of new technologies, professionals in the industry are often required to undertake intensive training to upskill themselves.
Despite these issues, AI has evidently revolutionised the industry and will continue to have a significant impact on food manufacturing.
1950 – AI is conceptualised with the potential to programme a computer to think like a human. A chess computer programme that prefigured AI would eventually go on to beat a world champion.
1970 – AI began to be put into practice through computer assisted design (CAD) and computer numerical control (CNC). An assembly line was created with a robotic arm which was then applied to the manufacturing industry.
1980 – Automated manual processes were developed, increasing efficiency, collecting data, and streamlining production.
21ST CENTURY – Sensors and predictive analytics were improved without sacrificing quality and safety standards.
TODAY – AI is everywhere, from smart speakers such as Alexa to facial recognition technology and interactive chatbots.
IN FUTURE – Machines could be developed to think like humans and have the potential to transform the industry.
MANUFACTURING OUTLOOK is a quarterly digital publication and media brand showcasing the latest innovations, industry insights and corporate stories from across the international manufacturing sector. Its world-class team collaborates with the biggest and most exciting brands to craft engaging and authoritative content for a global audience of industry players.
As manufacturing organisations worldwide confront unprecedented change, embracing technological innovations and incorporating critical environmental sustainability agendas, now more than ever is the time to showcase the strides being taken in this dynamic sector.
The expertise of our in-house design and production teams ensures delivery to the highest standards, as we look to promote the latest in engaging news, industry trends and success stories from the length and breadth of the global manufacturing sector.
As a multi-channel brand, Manufacturing Outlook reaches an international audience through various platforms, with exclusive content distributed through our website, online magazine, social media channels, and bi-weekly newsletter.
Through this compelling venture, we intend to foreground the movers and shakers of the industry. To participate as a featured company and join us in this exciting endeavour, contact one of our Project Managers or our Managing Director, James Mitchell, today.
As geopolitical instability grows, the demand for rapidly evolving technology and maximizing throughput is more important than ever.
Global security and aerospace company, Lockheed Martin, specializes in defense technology, solving complex challenges, advancing scientific discovery, and delivering innovative solutions that help its customers keep people safe.
Lockheed Martin’s all-domain mission solutions and 21st Century Security® vision accelerate its delivery of transformative defense technologies.
“Our customers face threats that require us to deliver innovation at scale and with greater agility than ever before to address their toughest challenges,” opens Chandra Marshall, Vice President and General Manager of Lockheed Martin Radar and Sensor Systems.
The leader in every domain in which its customers operate — air, land, sea, space, and cyber — Lockheed Martin has an unparalleled understanding of client missions.
To meet their needs, the company is digitally transforming its operations throughout the design and production process, ensuring the greatest efficiency without sacrificing quality.
“A joint force is a connected force, and our vision for 21st Century Security® weaves 5G technology through our proven platforms and combines them with the most
Identifying, tracking, and dealing with threats is imperative in national defense. Chandra Marshall, Vice President and General Manager of Lockheed Martin Radar and Sensor Systems, details how the company is at the forefront of threat detection
Writer: Jack Salter | Project Manager: Michael Sommerfield
advanced commercial technologies to increase capability and connectivity,” Marshall outlines.
Lockheed Martin’s business, the majority of which is with the US Department of Defense and federal government agencies, comprises four core areas specializing in defense technology – Aeronautics, Missiles and Fire Control (MFC), Space, and Rotary and Mission Systems (RMS).
Radars and sensor systems fall within RMS’ mission-first portfolio, along with rotorcraft technology, command and control, combat simulation and training, advanced cybersecurity, and undersea systems.
As the global choice for advanced radars and sensors, Lockheed Martin has a rich history of providing cuttingedge systems that are the proven, preferred air surveillance solution for more than 45 nations on six continents – and growing.
The company has established a broad legacy of producing highperforming, solid-state radars required for integrated air and
missile defense (IAMD), long-range surveillance, early warnings, and counter-target acquisition.
“Over the past 60+ years of delivering radars, we have proven that each system meets the technical requirements defined by the customer,” acclaims Marshall, who is responsible for the entire radar and sensor portfolio for domestic and international customers.
“With the incredible growth in our radar line of business, we are always finding ways to improve efficiency, apply digital technologies, and invest in product innovation to outpace the dynamic threats our customers face.”
Evolving threats demand that the company delivers modernized defense systems that are integrated using seamless and resilient networks.
Threat deterrence always begins with detection, and as escalation from bad actors increases, the US military and its allies need expansive radar systems that can adapt quickly to a range of potential threats in various landscapes.
Lockheed Martin is the trusted partner of armed forces across the
Chandra Marshall, Vice President and General Manager of Lockheed Martin Radar and Sensor Systems: “Protecting and supporting our armed forces and bringing them home safely to their families will always be a priority to me.
“Having grown up in a family that served in every branch of the service, this is in my DNA.
“After several years working in state and federal administration, it was time to put that mission into action. When a position opened at Lockheed Martin, I jumped at the chance to be a part of the organization.
“Working in the defense community is my way of supporting the men and women risking their lives for our freedoms.”
world for its reliable, upgradeable systems designed to operate in the digital age.
The company’s advanced radars and sensors, which also work with existing critical defense networks to keep cities, countries, and citizens protected from adversarial threats, perform surveillance, tracking, classification/discrimination/ identification, fire control engagement, and kill assessment.
Keeping the US and its allies safe requires a mature and progressive network of systems that flag incoming threats.
“Threats can mean many things – it could be a missile, unmanned aerial vehicle (UAV), aircraft, rocket, artillery, mortar, or maybe even something else,” notes Marshall.
“Radars are critical components of a defense system; they are the eyes that are responsible for identifying those threats and providing early warnings.”
Today, radars are trusted around
the world by many defense forces and networks on all battlefields – in the air, on the ground, in space, or at sea.
Lockheed Martin delivers systems that focus on situational awareness against the full array of evolving battlefield challenges.
“The capabilities that our radar and sensor systems provide ensure warfighters have full spectrum protection while on the battlefield and for homeland security,” Marshall informs us.
Whilst Lockheed Martin has delivered tailored solutions for the world’s most challenging national security missions for over a century, the company’s heritage of radar and sensor excellence dates back to the 1960s.
Since then, its long-range air surveillance radars have been in continuous service, demonstrating the radar engineering and program management capabilities of Lockheed Martin.
Among the portfolio’s core capabilities are ease of integration, harnessing the most advanced
next-generation technologies, and building modularly with open architecture principles – Lockheed Martin is therefore setting the course for future radar design and development.
“Our radars are also designed with high commonality across the portfolio, leveraging decades of performance, design enhancements, and end-user feedback.”
There are a number of key radars in the Lockheed Martin portfolio, including the new Variable Aperture Digital Radar (VADR), a software-defined sensor that can be reprogrammed to emulate different adversary systems and training events.
In March 2024, the US Air Force Advanced Range Threat System Variant 3 (ARTS-V3) program awarded Lockheed Martin an initial $276 million contract to develop and produce VADR.
This new contract expands the
company’s radar superiority for X-band and C-band radars, which VADR will leverage to train aircrews for engagements against adversarial threats.
“ARTS-V3 enhances our product line and demonstrates that we are continuing to lead the way in next-gen radar capability,” Marshall insights.
“Our radar technology directly contributes to the overall strength of the US military. It continues to be our top priority to focus on 21st Century Security®; this includes training our troops with the most advanced systems to best protect our homeland.”
Elsewhere in the Lockheed Martin portfolio, TPY-4 is a multimission, ground-based radar for air defense surveillance that can operate in contested electromagnetic environments and provides the ability for warfighters to detect and track current and emerging threats.
“Our proven performance and reliability will encourage customers to strongly consider TPY-4 as a solution to augment their existing capability as the threat space evolves,” emphasizes Marshall.
TPY-4 was selected in March 2022 for the US Air Force’s ThreeDimensional Expeditionary LongRange Radar (3DELRR) program, and in November 2022, the company signed a contract with the Royal Norwegian Air Force to acquire
several TPY-4 radars.
Thus, Norway became Lockheed Martin’s first NATO partner outside the US for its TPY-4 radar as part of the P2078 NORSE program, which will replace existing radars as they become obsolete.
The main mission of P2078 NORSE is to enhance the military surveillance capability of Norwegian and adjacent airspace through the replacement of legacy systems with a solution that meets future needs.
“We look forward to offering TPY-4 to solve the evolving challenges of international partners,” Marshall urges.
Norwegian industry has been a crucial partner in the development of the TPY-4 radar, with Lockheed Martin leveraging an extensive supplier base in the Scandinavian country.
In particular, the company’s relationship with KONGSBERG Defense & Aerospace (KDA) resulted in the production of the first TPY-4 that included the Platform Electronics SubSystem (PES) built by KDA, a critical element in the foundation of this next-generation sensor that meets and exceeds current customer requirements for long-range surveillance.
TPY-4 also has the capability to be a solution for the modernization efforts of the North American Aerospace Defense Command (NORAD).
In San Diego, Core Systems is an expert in providing top-of-the-line, rugged industrial and military-grade technology solutions
Whether providing cuttingedge equipment for industrial operations or reliable technology for military applications, Core Systems can meet the unique requirements of organizations with critical needs.
As a reliable partner, the company specializes in manufacturing best-in-class rugged industrial computers, displays, handheld units, and other systems that can withstand shocks, vibrations, humidity, and extreme temperatures.
With two premier vertically integrated production facilities equipped with top-tier engineering and fabrication teams, Core Systems stands out for its comprehensive strategy towards product development and integration. This approach ensures that every aspect of its products is meticulously designed and tested to meet the highest standards.
From the conceptualization phase to the meticulous environmental
testing stage, Core Systems manages every aspect of the process in-house. It also has a complete machine shop on the premises, which enables it to rapidly create prototypes and tailor products to meet clients’ precise requirements.
In addition, it builds and integrates systems with Graphics Processing Unit (GPU) boards, which are used for artificial intelligence (AI) purposes. Moreover, the metal shop executes computer numerical control (CNC), punch fold, paint, and welding, and has its own environmental testing, integration, and cable manufacturing facilities.
Core Systems has achieved a significant milestone by successfully participating in the renowned Lockheed Martin HDR-G program, a testament to its capabilities.
This program, known for its advanced data processing and communication capabilities,
trusted Core Systems’ expertise to deliver robust and reliable solutions.
By being chosen for rack integration, the company played a pivotal role in ensuring the seamless integration and functionality of critical systems. The HDR-G program relies on Core Systems’ expertise to deliver robust and reliable solutions.
Renowned for its distinctive, rugged military-grade versions of the top server brands in the market, such as repackaging Hewlett Packard Enterprise (HPE), CISCO, and Arista, Core Systems stands alone in providing this service. This exceptional offering underscores its engineering prowess and unwavering commitment to delivering solutions that surpass industry standards.
Core Systems is a highly regarded company that specializes in providing cutting-edge hardware
solutions and advanced AI technology to military forces across the globe. We create the only rugged HPE servers that support certain AI capabilities. Furthermore, machine learning (ML) is designed to adapt to ever-changing and challenging environments, enhance security, and safeguard robust encryption for sensitive data. At the same time, AI-powered simulation offers realistic combat training scenarios. Rugged systems are built with extreme durability in mind to withstand harsh conditions.
With its innovative technology, Core Systems has gained recognition and adoption from
military forces worldwide, including the Army, Navy, and other defense agencies. The company’s solutions have proved to be highly effective in enhancing the accuracy, speed, and reliability of military operations, thereby increasing the safety and success of personnel on the ground.
Through ongoing R&D, Core Systems continues to push the boundaries of AI technology, enabling military forces to stay ahead of the curve and maintain a competitive edge. Its commitment to excellence and an unwavering focus on safety and
security make it a trusted partner for military forces worldwide.
With a relentless focus on quality, reliability, and customer satisfaction, Core Systems has a proven track record of success.
A portfolio of groundbreaking solutions ensures that the company is committed to its vision of empowering its customers to achieve their goals.
As an industry leader in technological innovation, Core Systems is dedicated to providing cutting-edge solutions that meet the evolving needs of the industrial and military sectors globally.
Core Systems follows a design strategy that involves collaboration with its engineering team to ensure efficient product realization, whilst its world-class mechanical design engineering team provides product design. The next stage of the process involves a vertically integrated facility that enables rapid prototyping capabilities. After that, an on-site product test laboratory validates each new design to meet military specifications (MIL-Specs). Product assembly occurs at Core Systems’ facility with multiple production floors. Additionally, every product comes with a standard warranty and lifetime support.
Core Systems has extensive experience in commercial and defense programs spanning aerospace, transportation, military, security, and intelligence across the land, sea, air, space, cyberspace, and joint all-domains. The company has expertise in developing mission-critical systems for various applications
designed to meet environmental demands and adapt to an everchanging battlefield. Its history dates back to 2007 when it created sensor signal processing for defense applications, missioncritical airborne systems, and other purpose-built systems that exceeded expectations.
Core Systems provides a diverse selection of top-quality openframe racks, server racks, and enclosures suitable for a wide range of missions. In addition, the company offers integration services that involve assembling a fully configured rack cabinet system ready for deployment on the same day it is shipped. Its team of experts is always available to help select the best
cabinet for specific mission requirements.
Specializing in developing mission-critical systems for various applications, Core Systems’ solutions are designed to meet the environmental demands of each unique mission and adapt to the constantly changing battlefield.
With a strong track record of creating sensor processing systems and designing and developing mission-critical airborne systems for various military and defense applications, the company is a trusted leader in the industry.
Core Systems’ portfolio of rugged solutions and one-off designs is
purpose-built to exceed mission expectations. It adapts to the battlefield’s changing demands to ensure its products perform optimally in any environment. From advanced radar technology to improving intelligence, surveillance, and reconnaissance (ISR) capabilities, it is committed to providing customized solutions that meet the unique needs of military operations. Dedicated to ensuring excellence from start to finish, Core Systems offers a reliable solution for every possible military application with precision, expertise, and unmatched reliability on the battlefield.
Core Systems has a rich experience in creating robust computing solutions for the military. Its portfolio includes a wide range of projects with both commercial and defense programs. The company works closely with all military branches, designing customized solutions that suit specific deployments and ensuring that every challenge is met with innovation.
For years, Core Systems has worked tirelessly to create secure and reliable solutions for military aircraft, navigation, and other airborne applications. The company’s advanced computing solutions, including highdefinition displays and SWaPC-optimized mission computers, are among the most powerful and dependable in the world, designed to withstand the most challenging environments and ensure the safety and security of military personnel.
Taking pride in its commitment to providing industry-leading products tailored to meet specific needs, Core Systems ensures
that customers can complete their missions efficiently and confidently.
Core Systems delivers rugged, reliable technology for multidomain operations worldwide. It showcases its ability to overcome complex problems with versatile systems that thrive in extreme environments. It also has a long history of creating defense solutions for naval platforms built with size and safety in mind.
As the US Space Force continues to make great strides and push
APPLICATION-SPECIFIC DESIGN REVOLUTIONIZING MILITARY APPLICATIONS
Core Systems’ cutting-edge applications include:
• Military aircraft systems
• Training and simulation
• ISR
• Joint all-domain
• Radar
• Land systems
• Unmanned aircraft systems (UAS)
• Signals intelligence (SIGINT)
• Electro-Optical/Infra-Red (EO/IR)
boundaries in the field of space exploration, Core Systems is proud to work alongside NASA in developing cutting-edge computing solutions designed to withstand outer space’s harsh and demanding conditions. The team is committed to providing the necessary tools and technology to support space missions at all orbit levels, ensuring that astronauts and researchers can access reliable and efficient computing resources while exploring the final frontier. The military’s primary concern is the growing speed of cyber threats worldwide. Core Systems has spent years diagnosing, preventing, and solving these threats, providing multi-domain solutions that can operate independently or together across mission-critical infrastructure. The company ensures that systems operate without interruption and that missions are covered at all attack points.
Collaborate with Core Systems to blend cutting-edge technology with dependable systems to meet modern military demands.
The radar represents a leap in performance over Lockheed Martin’s FPS-117 radars, which have been operating continuously in NORAD’s North Warning System for over 30 years, and is well-suited to detect the smaller, faster-emerging threats of today.
“Our radar portfolio thrives on several key attributes, including commonality across radars, softwaredefined architecture, and the ability to easily integrate with existing defense systems,” states Marshall.
Lockheed Martin’s radars are designed with a high degree of commonality to enable sustainment efficiencies and significant cost savings for customers. TPY-4, for example, significantly leveraged the blueprint of Sentinel A4, a highperformance replacement of the aging legacy Sentinel A3 radar.
“Our scalable technology has resulted in significant international interest in both the Sentinel A4 and
TPY-4 radars to replace older assets that simply cannot be upgraded to match what our next-generation systems are offering.”
Sentinel A4 provides significant improvements to its predecessor’s existing capability against cruise missiles, unmanned aerial systems, and rotary wing and fixed wing threats.
This includes the ability to detect rocket, artillery, and mortar (RAM) threats, provide RAM points of origin and impact locations, and add protection against electronic threats.
Sentinel A4 will be incorporated into the National Advanced Surfaceto-Air Missile System (NASAMS) for the National Capital Region (NCR) and is considered the radar of choice for nations looking for IAMD solutions.
In addition to Sentinel A4’s role of protecting warfighters in combat, the new radar has been selected to protect NCR and support the defense
Radars transmit and receive high-frequency radio waves to detect and track things that may not be visible to the naked eye.
The data collected by radars helps operators in the field to make informed decisions about what to do next.
In national defense, radars are imperative to the security of armed forces and civilians because they provide early warnings against adversarial threats.
STEP ONE: TRANSMIT – Radars send out narrow beams of electromagnetic radio waves in short or long pulses via a transmitter.
STEP TWO: REFLECT – Those waves can be intercepted and reflected, which helps radar operators to determine many features of detected objects such as distance, direction, speed, shape, and range, to name a few.
STEP THREE: RECEIVE – The receiver accepts the returned energy of the radio waves and measures the time elapsed since the transmission. The distance, or range, of that object is calculated by measuring the total time the radar signal takes to make the trip to the target and back.
STEP FOUR: DETECT, CLASSIFY, AND ACT – All this digital data is then processed in real time to determine the range and trajectory of detected objects, as well as their threat level.
of Guam, a US island territory in Micronesia.
The new radar’s integration with NASAMS for NCR’s air and missile defense capability will provide critical security to vital strategic assets.
“Sentinel A4 with NASAMS for the NCR will be a tower-mounted, fixed air defense asset to detect the latest threats of our adversaries,” Marshall shares.
“Placing Sentinel A4 radars on towers to detect today’s modern threats and protect high-priority assets can be easily duplicated by other services and partner nations around the world.”
Utilizing the latest in gallium nitride (GaN) technology and a digital active electronically scanned array (AESA) architecture, Sentinel A4 provides both 360-degree and stop-andstare capabilities with a 75 percent increase in range over the legacy system.
It also offers high performance in all conditions with the ability to detect threats amid bad weather, complex terrains, and contested environments.
“Lockheed Martin has been investing in GaN technology for radar applications since 2002 and was the first to produce radar systems featuring GaN with TPS-77 in 2015 and Space Fence, which became operational in 2020,” highlights Marshall.
In order to integrate with a broader defense system, Sentinel A4 interfaces with command and control, and sends collected data to help the user determine the next step in the engagement and protect the defended area.
Sentinel A4 works with the US Army’s current IAMD Battle Command System (IBCS) and Forward Area Air Defense C2 (FAADC2). Providing data to these two C2 systems allows them to leverage critical information to determine the best course of action to address a threat.
The threats to military and civilian assets are advancing every day.
In this volatile global environment, the US military and its allies look to advanced radar systems that can protect them as they perform various missions and adapt to an ever-changing landscape.
Lockheed Martin has decades of experience in developing and delivering ground-based, naval, and aerial radars designed to integrate seamlessly into existing systems.
IBCS talks to the US Army’s Indirect Fire Protection Capability (IFPC) Increment 2, and as the primary sensor for IFPC, Sentinel A4 is integral in supporting critical asset protection.
Then there is the TPQ-53 radar system, which has a rich history of protecting the US for more than a decade.
With proven experience in counterfire support, the solid-state phased array detects, classifies, tracks, and determines the location of enemy indirect fire.
TPQ-53, which can be rapidly deployed, emplaced, and displaced, has consistently maintained greater than 95 percent operational availability, and Lockheed Martin
continues to modernize and increase the capabilities of the radar as threats evolve.
For example, the company has added multi-mission capability, which enables the detection of unmanned aircraft systems (UAS) and other small threats, as well as added air surveillance capability for the medium-range detection of fixed wing, rotary wing, and UAS threats.
“We have been working with the US Army on TPQ-53 for over a decade, and our partnership continues to be one of excellence as we support operations, maintenance, repairs, and upgrades to deliver outstanding performance and reliability,” prides Marshall.
In late 2023, meanwhile, Lockheed Martin was contracted to extend the
Qorvo’s RF MMICs, backed by three decades of GaN/GaAs expertise, redefine radar performance with unmatched reliability and sensitivity for aerospace and defense applications. With Qorvo’s industry-leading design, assembly and test of heterogeneous packaging for superior integration, module solutions meet stringent SWAP-C requirements for your next-generation phased array radar systems. Explore Qorvo’s radar innovations today.
life of the Royal Danish Air Force’s two TPS-77 long-range transportable radars.
Expected to receive a mid-life upgrade by mid-2025, TPS-77 operates 24 hours a day, provides continuous high-quality 3D surveillance on air targets, and offers superior long-range detection and 360-degree azimuth coverage.
“Lockheed Martin was awarded the initial Danish contract in 2005 for two TPS-77 radars to enhance Denmark’s air surveillance capabilities. The systems are stationed at fixed sites but can be quickly redeployed when
Lockheed Martin has a strong history with Core Systems dating back to 2018.
Core Systems represents the epitome of a strong small business partnership, as they provide the back-end command and control for Lockheed Martin’s radar systems.
“Core Systems remains committed and has ebbed and flowed with us through customer needs and industry changes,” attests Marshall.
Beyond delivering on time and to specific requirements, Core Systems has also invested heavily to support Lockheed Martin. This includes a large production facility that has been built in California.
“They know how critical their contributions are to Lockheed Martin and our government customers, ultimately playing a major role in overall homeland defense. Core Systems is a great partner with great capability – they keep coming back and stepping up to help us.”
required,” Marshall expands.
TPS-77 is in service worldwide in Australia, Brazil, Estonia, Indonesia, Iraq, Jordan, Latvia, Malaysia, Pakistan, South Korea, the UK, and the US.
Lockheed Martin’s Long-Range Discrimination Radar (LRDR), designed and developed for the US Missile Defense Agency (MDA), is the next generation of ballistic missile defense. LRDR provides precise tracking and unparalleled discrimination of missile threats combined with simultaneous space domain awareness.
Just recently, LRDR was officially handed over to MDA in preparation for an operational capability baseline (OCB) decision and the final transition to the warfighter.
“This milestone represents years of dedication to MDA’s mission to protect our homeland. LRDR is a cutting-edge asset providing the benefits of both low and highfrequency radars for an innovative approach to searching, tracking, and discriminating targets,” says Marshall.
The radar is able to simultaneously search and track multiple small objects, including all classes of ballistic missiles, at long range and under continuous operation.
LRDR’s discrimination capability allows it to identify lethal objects, such as enemy warheads, and differentiate them from non-lethal decoys. Along with other elements of the Missile Defense System (MDS), which LRDR is integrated into, the radar conserves the number of ground-based interceptors (GBIs) required for threat engagement.
“OUR CUSTOMERS FACE THREATS THAT REQUIRE US TO DELIVER INNOVATION AT SCALE AND WITH GREATER AGILITY THAN EVER BEFORE TO ADDRESS THEIR TOUGHEST CHALLENGES”
– CHANDRA MARSHALL, VICE PRESIDENT AND GENERAL MANAGER, LOCKHEED MARTIN RADAR AND SENSOR SYSTEMS
The highly adaptable LRDR features an open systems architecture designed to be scaled and extended to counter evolving threats without changing the hardware design.
Exemplifying this open systems architecture is LRDR’s added capability in support of hypersonic defense, giving decision makers actionable information to make fast, timely decisions.
In addition to missile defense, the radar system supports space domain awareness by monitoring satellites orbiting the Earth and detecting, tracking, and identifying active or inactive satellites, spent rocket bodies, and debris.
Rightly lauded for its primary mission of missile defense, LRDR’s secondary mission of space domain awareness was once considered a tranquil final frontier.
Now, however, space has emerged as the latest – and arguably the most complex – domain for military operations.
The US faces a number of challenges in this new domain today, from counterspace technologies and space debris to orbital congestion and the rapidly advancing space capabilities of adversaries.
To enable the US to monitor and
safeguard its vital space assets, ensure the peaceful use of outer space, and maintain a technological edge in this critical domain, the need for robust space domain awareness has never been more urgent.
Space domain awareness is fundamental in achieving the cornerstone responsibilities of the US Space Force (USSF) – preserving freedom of action, enabling joint lethality and effectiveness, and providing independent options.
The USSF doctrine, which states that “obtaining and maintaining domain awareness is fundamental to successful operations in any environment”, underscores the importance of SDA.
Government agencies lead in space domain awareness with the most discerning radar technologies
and software known to mankind.
LRDR, one of three technologies that are revolutionizing the frontier, has successfully passed several space domain awareness events in recent months, confirming the radar’s warfighter capabilities.
These events, which give information on how the radar behaves during a resident space object (RSO) environment as well as future capability upgrades, are intended to provide early use of LRDR to USSF and US Space Command (SPACECOM) prior to its transition from MDA, which is planned for later this year.
Along with LRDR, Space Fence is another technology that provides crucial support for military and
commercial space operations as well as long-term benefits for the US and its allies.
A key contributor to space domain awareness, Space Fence provides information that USSF needs to make informed decisions and take actions to protect key assets in orbit.
Space Fence is now the world’s most advanced radar, providing detection, tracking, and accurate measurement of space objects, including satellites and orbital debris primarily in low Earth orbit (LEO).
Today, LEO is crowded with active satellites and thousands of pieces of debris due to collisions and the deterioration of defunct satellites and rocket boosters.
That debris threatens both the commercial satellites relied upon for everything from weather
“LOCKHEED MARTIN HAS PIONEERED MUCH OF THE TECHNOLOGY THAT EXISTS IN THE DEFENSE INDUSTRY’S RADAR SYSTEMS TODAY, THEREFORE SETTING THE BAR TO DETER ADVERSARIAL THREATS AND ANTICIPATE EVOLVING BATTLESPACES”
– CHANDRA MARSHALL, VICE PRESIDENT AND GENERAL MANAGER, LOCKHEED MARTIN RADAR AND SENSOR SYSTEMS
forecasting and banking to global communications and GPS navigation, and the military assets that help to monitor and protect nations around the world.
Space Fence is now actively tracking satellites and discovering objects as small as a marble in LEO, making it a key contributor to space domain awareness.
Not only does Space Fence permit the detection of much smaller microsatellites and debris than current systems, but it also significantly improves the accuracy and timeliness with which satellite operators can detect space events and make better informed decisions about how to expend precious resources to maneuver and avoid collisions.
Building Space Fence in the
remote Marshall Islands was a great engineering accomplishment and a huge advancement in radar technology to enable dramatically increased orbital debris awareness, critical to protecting national security assets in a complex 21st Century Security® threat environment.
Lockheed Martin’s iSpace™ software, meanwhile, provides command and control and battle management capabilities for customers in all arenas that operate in the space domain.
These systems, developed by Lockheed Martin, provide the ability to detect far more debris than previous technologies could, and with greater accuracy, providing timely and actionable information to protect key assets in orbit.
LRDR technology has equally been leveraged and scaled for Lockheed Martin’s SPY-7 land and maritime radar product line.
“The SPY-7 radar product line uses LRDR technology to enhance overall strength against evolving threats,” Marshall explains.
“Providing 24/7 coverage, SPY-7 is a superior deterrence asset available for land and maritime applications around the world.”
A software-defined multi-mission radar, SPY-7 allows the rapid and efficient insertion of new capabilities and techniques, offers a threefold improvement in performance compared to current radars, and boasts advanced missile defense features that can’t be matched by any competitor.
Lockheed Martin successfully demonstrated SPY-7 in April 2024 for the Aegis System Equipped Vessel (ASEV), as the radar’s tactical hardware and software tracked objects in space. This served as a critical milestone as the technology will act as the cornerstone for Japan’s national defense.
Approximately 122,000 employees in the US and internationally
345+ facilities
13,300 active suppliers in every US state
890+ suppliers in over 52 countries outside the US
It also verified the maturity of SPY-7, which is fully interoperable through the Aegis Combat System (ACS), and marked the beginning of comprehensive performance testing prior to delivery to Japan. Such vigorous testing will minimize risk and ensure the nation receives a fully integrated and calibrated system as quickly as possible.
“The Japan Ministry of Defense will field two ASEVs equipped with the SPY-7 radar system,” Marshall announces.
SPY-7 has already been radiating and tracking air and space objects at Lockheed Martin’s New Jersey facility since 2018. Japan, Spain, and Canada have also signed up to use SPY-7 in a sea-based capacity to protect their citizens.
“The world is changing rapidly, and countries need a radar that can evolve with it – SPY-7 is that radar,” she affirms.
“We are experts in radars; we’ve
built and fielded them in all kinds of terrain. Wherever a partner may want this capability, we can work with them to realize that successfully.”
In addition to the roll-out of SPY-7, Lockheed Martin is looking ahead to growth through a strong pipeline of business.
One of the company’s top goals is to make sure it delivers quality products when customers require them.
“It’s that simple. Today’s warfighting environment and rogue threats are evolving every single day, and we help our customers bring solutions to the warfighters that will ensure safety and well-being. What we do is critically important, and I’m so proud to be a part of it,” Marshall beams.
“We have worked, and will continue to work, in concert alongside our customers and suppliers to find
creative ways to ensure we can deliver products that keep military and civilians safe.”
To enhance the detection and protection of threats, it is imperative that Lockheed Martin’s systems continue to talk to each other and elevate how they collect and use data to predict and respond to what’s coming next.
“The speed of relevance is what will keep our homeland and our allies’ homelands safe from adversaries, and the Lockheed Martin radar and sensor portfolio is already a center of excellence, prepared to meet and exceed those demands,” she adds.
The company works tirelessly to make sure it is meeting the needs of not only its customers, but also the workforce.
Advocacy is of great importance to Marshall to ensure each individual is challenged, rewarded, fulfilled, and has the chance to grow within the company.
“In an organization as big as Lockheed Martin, it’s critical that we pay attention to all those who are working on our customers’ missions as if they were their own,” she sets out.
Today, supply chain disruption and labor shortages are some of the most challenging issues in the defense industry.
Filling open positions is therefore something that is also focused on daily by Lockheed Martin, who has been collaborating with economic development organizations and industry to address hiring needs and skill gaps.
“We continuously work to ensure competitive salaries, exciting work, and an overall great work environment,” enthuses Marshall.
Furthermore, there are many opportunities for women in the workplace, especially in manufacturing.
Lockheed Martin today is far more inclusive than it was in the past and recognizes the value of having a more
diverse working environment.
“I’ve personally seen a lot more diversity over my career, and with that, I’ve witnessed a direct correlation to the strength and growth of our organization.
“Investment in our teams, whether through our formal mentorship initiatives, apprenticeships, continuing education, or training and leadership programs, is a given here,” Marshall concludes.
We speak to Kevin Wolter, Director of Business Development at Invio Automation, about its proven automation expertise that has accelerated global businesses across a vast range of industries for over 60 years
Writer: Lucy Pilgrim | Project Manager: Callam Waller
Global investment in the North American manufacturing industry has never been higher, encouraging many companies to focus on reshoring their production and supply chain to the US, whilst government incentives have dramatically encouraged domestic production.
On top of this, industry trends such as labor shortages, increased wages,
and a greater desire for improved production consistency and quality have driven manufacturers in the country to implement robotics and manufacturing automation more widely across their organizations.
This presents the industry with an opportunity to source and analyze more data, particularly given the recent rise of the Internet of Things (IoT) – also known as Industry 4.0
– and the evolution of digitalization, which allows for greater real-time monitoring, predictive maintenance, and process optimization.
Within this context, the main focus of Invio Automation (Invio) lies in supplying state-of-the-art manufacturing automation and robotics solutions to its customers, regardless of the project’s size or scale.
Designing, implementing, and sustaining automation services for some of the largest operations in the world, the company permeates a number of key industries, including medical device and life sciences, CleanTech and renewable energy, mobility, industrial, logistics, and much more.
“Invio designs, implements, and sustains automation for operations large and small across the world. Our company history dates back 65 years, and we continue to evolve. We take pride in truly partnering with our customers to solve big challenges by exploring, testing, and customizing the latest manufacturing technology,” opens Director of Business Development, Kevin Wolter.
“The company exists to contribute and participate in one of the great macroeconomic trends of our time
“THE STAFF HERE ARE AMAZING – ONE YEAR AGO, I JOINED INVIO AND WAS FORTUNATE TO BE PART OF A TEAM OF HIGHLY MOTIVATED PROFESSIONALS WHO UNDERSTAND THEIR ROLE WITHIN A COLLECTIVE AND TAKE PRIDE IN GETTING THE JOB DONE”
– KEVIN WOLTER, DIRECTOR OF BUSINESS DEVELOPMENT,
INVIO AUTOMATION
- the increased role of robotics and automation in our daily lives.
“Our work takes us into hundreds of factories and product development organizations every year and we proudly help our customers build meaningful products in healthcare, renewable energy, and
transportation,” he adds.
Invio’s founding principles are twofold. Firstly, it strives to serve as the preferred global automation partner in industries that meaningfully benefit the lives of others.
Secondly, it employs hundreds of engineers, skilled tradespeople, and manufacturing professionals domestically in an effort towards that goal.
Each industry is served across seven production sites in the US, with its primary base located in the Midwest region of the country.
Providing practical and proven solutions for a vast range of industries, the company works with customers to fundamentally understand and take their ideas through an entire lifecycle, manufacturing these products
with industry-leading robotics and automation capabilities.
“A lot of our customers are looking to improve quality and reproducibility while reducing labor,” informs Wolter.
Operating for over 40 years in the medical devices sector, the company possesses more than 500 team members in the US, a third of which are in an engineering role and actively partake in the technological elements of a project.
“As a mechanical and electrical engineer, I find it really engaging to see both elements integrated into these products,” he adds.
Alongside the manufacturing of medical devices, the organization conducts warehousing and logistics practices, whilst a large portion of its business supports the automotive and industrial markets with custom tooling and lift-assist services, as well as top-quality automated guided vehicles (AGVs) and automated mobile robots (AMRs) that can transport heavy pallets throughout customers’ warehouses and production areas.
One particular focus of Invio is known as Factory of the Future Consulting, whose workforce serves as a consultancy agency for their clients. After performing plant-wide greenfield and brownfield automation assessments, the company utilizes production modeling and 3D simulations to help customers determine where automation can have the most cost-effective impact on their return on investment (ROI) and production processes.
As such, Invio’s efforts ensure reliability and digital innovation across the entire manufacturing process.
“Each automation aspect, from factory floor to end-stage enterprise resource planning (ERP), is informed by a certain level of data, which in turn impacts the wider supply chain of any given product,” Wolter highlights.
“In the future, I foresee the same team presenting customers with augmented reality (AR) and virtual reality (VR) models of their facilities.”
Invio stands out in the US automation market due to its dedicated willingness to work with customers throughout their entire manufacturing journey, ranging from smaller operations to complex robotic systems.
“Historically, many of our new customers came to us after other automation vendors had declined requests to quote, because their projects were too intricate or technically complicated. However, we actively engage with these types of customers as we have the experience and capability to undertake complicated, high-precision developments,” Wolter imparts.
“Our customers often return to us after we’ve solved their most difficult automation problems, providing support for their entire manufacturing process. The target is to become their preferred automation vendor.”
Therefore, it is mutually beneficial for the company to support clients in the early stages of their automation journey so that they can become the go-to manufacturer for the entire process.
As such, Invio has built an enviable reputation for small, high-precision products. In the medical devices space, this typically involves the likes of insulin pumps, cardiac implants, catheters for heart disease and stroke support, as well as many other micromanufacturing processes.
With a core market focus and an established manufacturing process, the company has developed a set of flywheels that enable it to provide
incredible solutions and services for customers.
“We continue to reinvest in this approach and cross-pollinate applications across our core markets. For example, we assess who else requires needle bending capabilities to generate a list of customers we can address.
“Meanwhile, for our engineering expertise, we develop specific applications within a certain industry that we can add to our toolbox. This allows us to improve our operations and build bigger machines around that expertise,” Wolter explains.
Furthermore, Invio is committed to providing ‘white glove service’ for all customers, as it aims for the highest degree of professionalism, responsiveness, proactive customer engagement, and support throughout the lifecycle of an automation project.
“Recently, a potential early-stage prospect mentioned that, while they were looking at several potential automation partners, Invio provided the best customer service. We are looking forward to engaging with that customer more formally very soon.”
A critical element of Invio’s longstanding success is its loyal partner and supplier relationships, which keep projects flowing beyond everyday operations.
The company has a unique offering in the form of heavyweight or highcapacity AGVs that fundamentally serve the purpose of transporting product throughout the factory without human involvement.
Prior to the development of automated conveyance solutions, items under manufacture were typically transported manually using carts, trolleys, or forklifts, both powered and unpowered. Over time, many of these manual conveyance platforms, which were inefficient and often dangerous, became automated.
For industries such as electric vehicles (EVs), aerospace, alternative energy, and defense, manufacturing processes often involve the movement of heavy parts, objects in work, and eventually, finished products. As such, the capacity of conveyance automation systems must often exceed 10,000 pounds (lbs). Many manufacturers need to convey and assemble products that weigh from 10,000 to 50,000 lbs, but AGVs with this capacity range are rare.
The unique load requirements for these capabilities are very different from other classes of manufacturers and are a key differentiator when evaluating conveyance automation solutions.
Invio’s AGVs are used to transport pallets of solar panels, recreational vehicles, tractors, construction equipment, EVs, electrical grid equipment, and even the sleeper bunks for large airplanes.
A powerful positioner from ALM delivers up to 40%+ increased welding and assembly manufacturing productivity. You’ll also gain increased safety, quality and ergonomics to ensure maximized throughput is always within reach.
“This has been one of the first times in my career that I have found such a strong collaboration between my organization, suppliers, and customers,” Wolter expresses.
As the company continues to establish its name in the market, Invio works with suppliers to set up joint customer visits, where it can recommend potential suppliers for preferred automation vendors.
As Invio continues to expand its MDLS focus into new geographic markets,
such as the Midwest and Minnesota’s Medical Alley, it successfully leverages its 40 years of experience in the space to support the broader sales, engineering, and operations teams in the industry and related automation and design principles.
“Personally, it has been incredible to work with experts and thought leaders, and I continue to be amazed by the knowledge base they have created and their willingness to share their experience,” Wolter expresses.
“As we build our team, we continue to expand our market presence and add major MDLS customers.”
Within this division of the company,
After 40 years of operating its New England MDLS Center of Excellence, in May 2023, Invio also established its Midwest MDLS Center of Excellence in the heart of Medical Alley in the Twin Cities area of Minnesota. Medical Alley comprises approximately 800 medical device manufacturers, subcontractors, and machine shops that support the industry.
Therefore, the facility has provided the company with the opportunity to establish its own presence in the region and gain traction with the big names in the medical devices space.
One particular business Invio is proud to have acquired is Innovative Products & Equipment (IPE), who has been a market leader in solving the production challenges that commonly arise for advanced manufacturing operations in the New England area, specifically along the Route 128 corridor.
The historical IPE facility in Hudson now serves as a sister facility to the Invio site in Minnesota, bringing the opportunity for many customers in both regions to have their automation needs served locally.
Invio’s central desire is to improve patient healthcare for its customers’ end users.
The opportunity to impact the lives of real people on a global scale is significant. The company’s patented hypotube and needle bending technology was developed to support the rapidly growing diabetes market. Globally, there are 400 million people diagnosed with Type 2 diabetes (T2D), making Invio’s patented needle bending technology increasingly critical.
Therefore, the company’s systems help provide insulin for diabetics and manufacture highly technical catheters, guidewires, sensors, and on-body pumps. Regarding the latter, the equipment is used to create a key part of an insulin pump that is placed on the user to help treat their condition.
“The benefit of having this needle, which has a very unique, spring-loaded shape, is that when it’s time to pump insulin, the needle inserts a cannula that we have also manufactured. This creates a port for the application of insulin into the body,” details Wolter.
Invio’s patented needle bender is capable of bending a drug delivery needle to as small as 1/10,000th of an inch in outside diameter without blocking the drug delivery of the needle. The machine utilizes a highprecision camera and servo motors to ensure the proper needle orientation and position in real-time throughout
Performance Feeders specializes in the design and manufacturing of Vibratory Feeder bowls, Centrifugal Feeder bowls, Step Feeders, Drum Feeders, Flex Feeders, Conveyors, Spring Feeders, Prefeeders, Elevators and Protective System Enclosures with Visual inspection, Part Isolation, with Control packages available.
Our knowledgeable sales team work with our manufacturing technicians to engineer and construct each quality system to create the most costeffective, durable feeding systems to support assembly operations. Advancements in our design process using solid modeling and CAM software, CNC machinery, and 3D printed prototypes enable our team to create customized and repeatable solutions for a variety of industries.
the manufacturing process. Once at the desired angle, the machine bends both sides of the needle to create a specified shape without occluding it.
The standard needle bending module is capable of producing a uniquely shaped needle every six seconds.
However, needle bending is just one stage of the insulin pump product that Invio manufacturers, demonstrating the fact that a small, simple solution can lead to the production of an entire process and an all-encompassing solution.
Invio recently developed an automation project that produces a blood culture collection device, which can be used by medical professionals to draw blood more efficiently and
• The company takes pride in the reliability of its team and the difficult problems it solves for customers.
• Invio delivers real customer value that positively impacts the lives of those around them.
• The business is dependable, as trustworthy relationships matter.
• Its ingenuity and desire to improve life complements its suite of solutions.
• Invio strives to demonstrate that its attention to detail does not start or end with the solutions it engineers and delivers.
• The company believes that exceptional service is better demonstrated than said.
avoid incorrect blood test results.
The machinery for the blood collection device produces 15 parts per minute, translating to 900 units an hour.
“We were able to design, develop, and deliver an incredible piece of equipment for our customer in approximately nine months on our first major MDLS project in our new Minnesota facility,” Wolter proudly tells us.
“This is thanks to our ability to leverage our incredible local engineering capabilities and the vast MDLS expertise available from the broader Invio team.”
In order to further its specialized offerings, the company is currently building an applications lab in Minnesota, which will showcase the key technologies and tools that it integrates into its machines every day. These include robots, ultrasonic
and laser welders, laser markers, lead testers, and much more.
“The intention is for the facility to serve as an additional engineering resource for our customers as they continue to develop these incredible technologies. Additionally, the lab will be an effective marketing tool for our partners and suppliers who can bring their customers on-site as they work through their technical evaluations,” Wolter elaborates.
The extensive size of Invio’s workforce means that it can productively collaborate across a plethora of industries and applications to brainstorm the best solutions for its customers.
“The staff here are amazing – one year ago, I joined Invio and was fortunate to be part of a team of highly motivated professionals
who understand their role within a collective and take pride in getting the job done. I believe we have cultivated an organization that encourages individuals to speak up with recommendations for continuous improvement,” Wolter proudly comments.
The company recognizes staff that go beyond the call of duty with established reward programs and monthly newsletters that highlight hard-working employees, who also have the chance to win prizes.
“I also acknowledge individuals on a more personal level or in small group settings, as it presents an opportunity to further my relationships with the team in a meaningful way,” affirms Wolter.
As Invio continues to expand its business, both organically and through acquisitions, it remains focused on its core mission to be
committed to engineering advanced industrial solutions that enhance quality of life.
Another major priority for the business is the aggressive alignment of the company’s seven production sites across one common platform.
However, one of the most important things for Wolter is that the company and its employees continue to learn and have fun.
“Throughout my 12 months in the role, our team has been incredibly engaged and excited, and I learn more from them every day,” concludes Wolter.
Tel: 517 321 7700
connect@invioautomation.com www.invioautomation.com
Protecting the national security interests of customers, QinetiQ Target Systems delivers industry-leading solutions designed and developed for threat replication, military operational training, and weapon system tests and evaluations. We learn more about the company’s manufacturing excellence with Director of Operations, Alan Short
Writer: Ed Budds | Project Manager: Michael Sommerfield
he ongoing impact of the COVID-19 pandemic has permanently changed how manufacturing organizations
Forced to contend with widespread skills shortages, global manufacturers are finding it increasingly difficult to hire staff in a timely manner, with candidates seeking increased flexibility, enrichment, and development in new roles rather than traditional rewards and remuneration. Elsewhere, the increased digitization and adoption of automated technologies in manufacturing continues at pace, positively impacting responsiveness, productivity, and waste reduction.
Even in manual manufacturing environments, the industry has witnessed growing levels of automation connecting the shop floor with the point of sale, alongside the use of data and analytics which enable modeling and pre-emptive decision-making.
Within the vast defense manufacturing sector, these current trends abound.
As the worldwide threat landscape is constantly evolving, more sophisticated aircraft are being developed, unmanned aerial vehicle (UAV) use is growing, electronic warfare and swarm tactics are on the rise, and supersonic anti-ship missiles are becoming more prolific.
Additionally, with the emergence of anti-ship ballistic missiles and new hypersonic threats, it can seem impossible for defense manufacturers to keep pace.
Using mission-led innovation, the overarching goal for leading North American manufacturer, QinetiQ Target Systems (QTS), is to be the chosen defense partner around the world, helping shape the future of the sector by solving real-world problems.
“As an internationally leading provider of uncrewed air and surface autonomous platforms, we protect
Alan Short, Director of Operations: “I started my career as a graduate recruit in quality and process engineering with a couple of large US-based organizations, where I enjoyed the experience of starting up new facilities in Scotland, the UK, and Mexico.
“I then moved to a start-up medical device organization in the former, spending nine years helping to grow and develop the team. During this time, I was afforded my first exposure to the supply chain, product transfer, and the challenges of bringing a new product to market. Being a start-up company also meant I got involved in many different aspects of the business.
“I then spent several years working in various high-growth medical device organizations, establishing supply chains and manufacturing operations to support their growth, where I learned the value of process disciplines, planning, and risk management before joining QTS in April 2023.
“My interest in manufacturing stemmed from my time at university. While studying engineering, I spent some of my education in industry at a car plant, where seeing a product follow the culmination of many different processes intrigued me.
“I have learned to value the objectivity of manufacturing, the fulfillment of a plan, and the need for teamwork, innovation, and continuous improvement throughout my career.”
the national security interests of customers by delivering top-of-therange solutions.
“Designed and developed for threat representation, our products help ensure operational readiness in militaries across the globe,” introduces Director of Operations, Alan Short.
In this way, QTS expertly designs, develops, and manufactures uncrewed vehicles and supporting equipment for weapon system tests and evaluations. These include aerial and surface targets, customizable payloads and towed targets, launchers, and ground control stations.
Additionally, QTS also offers a range of global field services, including custom target operations, global livefire exercises, and vessel maintenance services for end-to-end training applications.
“With worldwide capability, our customer base is global, with NATO and AUKUS, a security partnership for the Indo-Pacific region between Australia, the UK, and the US, primarily utilizing our product and service offerings,” adds Short.
“At present, we have 150 to 200 employees in the business working both remotely and spread across our two manufacturing facilities in Alberta, Canada, and Ashford, UK.”
Wilson Process Systems, a privately owned UK electronics subcontractor, has been supporting local and overseas customers for well over 40 years. Born in the late 70s from bare PCB fabrication, it has evolved into a well-established CEM.
With this consistent growth, Wilson has continued to expand its footprint into two sites covering 28,000 sqft based in Hastings, East Sussex, where joint Managing Directors, Tim and Nick Wilson, pride themselves on offering an agile and responsive service, with a company ethos of ‘right first time’ and ‘automation where possible’, which has led to proven success over many years. Wilson is also a big advocates of making ‘doing business easy’, which is reflected in its customer base ranging from Cummins, VMS and Kantar, across such industries as industrial control, communications, medical and digital signage.
Key general services include both surface-mount and automated through-hole assembly through a suite of universal equipment, whilst also offering specialist services including automated conformal coating, resin encapsulation and thermal testing where electronic systems require extra protection against ingress and the environmental conditions they reside in. Automated selected soldering is also available alongside a standard reflow process, aqueous washing and AOI (automated optical inspection).
To complement the automated portion of the business, Wilson boasts a 40+ strong team of IPC trained operators, dedicated to the second stage build process. With almost all PCBA’s requiring hand assembly in various forms, Wilson can call upon resources which capture 100 percent component coverage of both PCBA and any ‘Box Build’ system. To enhance this further, tests can be included if required from simple ‘go, no-go’ to full functional tests.With all
this combined, concludes a complete selection of resources, which is invaluable to fulfill Wilson’s core competence when supporting customer needs.
It’s this combined ability to offer a full PCB assembly service that’s able to cope with dynamic demands from clients that has made Wilson Process, one of QinetiQ Target Systems’ UK partners of choice for the past 12 years. Over this time, both companies have experienced changes in technologies, challenges in material supply, and exponential demand due to global politics.The support offered by Wilson has played a key role in allowing QinetiQ to develop, manufacture and release new products where the emphasis has been on economical, ultra-reliable PCBAs.
Tim Wilson commented, “we’ve been supporting all our customers with consistent quality for over three decades, helping engineering teams with DFM (design for manufacture) to improve ‘right first time’ prototypes that lead into volume production. This is especially important when considering maximum productivity for high mix PCBAs, or boards requiring conformal coating.
We’ve also promoted collaboration between our procurement team and partner customers to establish a robust supply chain to ensure continuity whilst helping manage inventory, which over the past three years has seen multiple challenges keeping both materials and assembly flowing”.
Whether it be small batch production, urgent samples or scheduled monthly drops, full procurement or free-issue, Wilson is geared to perform. If you want to know more about how Wilson can support your business, please visit www.wps.co.uk
Towards the end of 2023, QTS reached an incredible milestone in the production capacity of its signature product – the 9,000th Banshee Aerial Target drone. The target formed part of the British Royal Navy’s Project Vampire, providing a low-cost, high-performance uncrewed aircraft system for the program.
“By the end of this year, we are on track to accomplish the landmark of 10,000 units produced! This is a testament to the continued quality we deliver and another achievement
we look forward to celebrating,” Short enthuses.
Furthermore, by meeting the increasing demand for advanced autonomous systems, the development of QTS’ multi-role autonomous boat (MRAB) is progressing on schedule.
This vessel, featuring remote autonomous operation with crewed and uncrewed functionality, is set to be unveiled in late 2025, manufactured in partnership with Zodiac Hurricane.
The boat’s key features include
single-user control with integrated autopilot and antenna farm capabilities, remote access to critical sensors, payloads, engine information, and vehicle command, alongside powered onboard batteries and a robust onboard safety system.
Elsewhere, the company has started to decentralize its manufacturing systems, supporting its single route to market strategy.
“First, we are setting up a North American supply chain for our aerial targets. As we take this forward to other products and regions, this will
“ONE OF THE CHALLENGES I ENJOY AT QTS IS BALANCING THE DEVELOPMENT OF THE MANUFACTURING OPERATIONS AND SUPPLY CHAIN WITH AN INCREASING PORTFOLIO OF PRODUCTS” – ALAN SHORT, DIRECTOR OF OPERATIONS, QINETIQ TARGET SYSTEMS
“AS AN INTERNATIONALLY LEADING PROVIDER OF UNCREWED AIR AND SURFACE AUTONOMOUS PLATFORMS, WE PROTECT THE NATIONAL SECURITY INTERESTS OF CUSTOMERS BY DELIVERING TOP-OF-THE-RANGE SOLUTIONS”
– ALAN SHORT, DIRECTOR OF OPERATIONS, QINETIQ
include developing a nuanced supply chain that has the capacity and capability to support the region with the highest customer demand whilst enabling other areas of less demand to leverage the benefit of investment and lower unit costs,” he explains.
The diverse range of specialist materials and components that are part of QTS’ products means the company heavily relies on its welloiled and efficient supply chain, meticulously compiled over time to
form a smooth, reliable operation.
“Our supply chain partners’ support and performance were a key contributor in achieving a record year in aerial and surface targets. The importance of our partners will continue to increase with the level of technology in our products,” Short elaborates.
This requires a mature relationship in which QTS supports the supply chain’s investment in capability, as the company aims to treat partners how it would like to be treated by its own customers.
TARGET SYSTEMS
“We have focused heavily on building beneficial relationships with our key suppliers in the last year, including exploring mutual sharing of cost and productivity improvements and establishing agreements where risk is shared and mitigated,” he adds.
“We still have a way to go, but we are taking a holistic view of order and inventory management, knowing this will yield long-term benefits. We are already seeing significant improvement in the metric of on-time in-full (OTIF) and working capital.”
As an organization, QTS recognizes
SC Aerofina SA develops research and design, production, testing and evaluation, maintenance and integrated customer support for:
• Devices, equipment, life-saving appliances and pyrotechnical devices for military, aerospace, terrestrial and naval systems. It participates in all major aviation programs: IAR 330 PUMA, IAR 330 PUMA SOCAT, IAR 316, MiG 21 LANCER, IAR 99, and IAR 99 SOIM.
• Structural elements and equipment for rolling stock and railway infrastructure.
that its impact reaches far and wide into the supply chain and is therefore embedding policy and action into its supplier onboarding, contracting, and ongoing governance.
With the leading ability to create and deliver customized solutions and fully integrated systems worldwide, QTS gives its customers the flexibility and futureproofing they need to stay ahead.
This client-focused approach sets the company apart from other manufacturers and industry peers, as it can effectively respond to requirements using the talent and exceptional resources in its state-of-the-art engineering facilities in the UK and Canada.
“One of the challenges I enjoy at QTS is balancing the development of the manufacturing operations and supply chain with an increasing portfolio of products,” references Short.
Sos. Fabrica de Glucoza nr. 2-4, Bucharest, Sector 2, 020332, Romania
Phone: (+40) 21-242.0772 serv@aerofina.ro www.aerofina.ro
“This requires us to continually develop standardization and rigor in our product transfer processes, upskill and progress the team, become more flexible and responsive in manufacturing, and increase supply chain capability. It is a multifaceted challenge, and I am very happy with how we are rising to tackle it,” he acclaims.
Responding to a wide range of world events and continuing to support its customer base compounds QTS’ need for flexibility and responsiveness. To date, the company’s success can be attributed to this adaptability and will continue to be crucial in how it responds to customers’ needs and maintains a respected reputation within the industry.
Moving forwards, QTS’ primary role as an operations team boils down to delivery.
“We are targeting unit output increases of 10 to 25 percent,
depending on the site. We will also build upon the fantastic momentum we made in productivity improvements during the last financial year, continuing our exciting journey in lean manufacturing,” Short concludes proudly.
UK: 01233 505600
CANADA: +1 403-528-8782
qtsmarketing@qinetiq.com
www.qinetiq.com/targetsystems
Manufacturing superior of first-class dealers, fastest-growing motorhome Donati and David Middleton, and outline its plans
Writer: Lily Sawyer |
superior motorhomes and operating through a network dealers, it is no wonder Nexus RV has emerged as the motorhome company in the US. Co-Founders, Claude Middleton, reflect on the business’s recent successes plans for continued product innovation Manager: Michael Sommerfield
The recreational vehicle (RV) industry in the US has witnessed exponential growth in recent years.
An ever-expanding cultural phenomenon that has arguably become as important as baseball or apple pie, RVs are loved across the nation.
Certainly, the COVID-19 pandemic contributed to this unprecedented industry growth, ushering in four years of equivalent sales in a threeyear period.
“During this time, we saw some big shifts in our customer base and the usage of our products,” opens Claude Donati, Managing Member of Nexus RV, which has experienced unmatched growth in the US.
The pandemic witnessed many Americans leave the office to embark on country-wide road trips whilst working from home, creating three record-breaking sales years for the RV industry, culminating in 600,000 vehicles sold in 2022.
“However, the challenging part of this rocket growth is that we are now amidst a correction period,” President
of the company, Dave Middleton, points out.
“There is an old saying in the RV industry - you are either stepping on the accelerator or slamming on the brakes. We are currently slamming on the brakes,” he adds.
Therefore, as Nexus RV operates in a sector currently experiencing increased interest rates and inflationary factors, the business continues to raise the bar by improving product quality and upgrading its units with all-new interior design.
A recent industry slowdown has afforded Nexus RV the time to reflect and adjust to the way it engages with retail customers.
“With this new environment comes new approaches; new floorplans,
chassis, interiors, technologies, services, and warranty support systems are at the top of our to-do list.”
Now, as the industry anticipates an impending revival, the company is ideally positioned to take on more market shares due to its continuous innovation and evolution.
Located in Elkhart, Indiana, Nexus RV is a privately held motorhome manufacturer. The company was founded in 2010 by Middleton and Donati, initially operating directly out of its factory to serve customers for seven inaugural years.
In 2018, Nexus RV elected to update its business model and begin selling through a high-quality dealer network.
Before sale, 100 percent of Nexus RV’s vehicles go through a ‘camping simulation’. This is a 6-hour process which ensures that all systems are operational on both generator and shore power, includes a full plumbing test of the gas and water as well as a drive and rain test. In addition, each Nexus RV vehicle benefits from the following:
• HSLA steel, which is proven to be 72 percent stronger than aluminum.
• Exclusive double AZDEL Onboard® composite materials used in the sidewalls and roof, as opposed to wood.
• A one-piece wrapped fiberglass roof, which ensures no seams from fasteners on the vehicle radius.
• Gel-coated glass, fused with a composite backer for durability.
• Each opening framed in HSLA steel to minimize squeaks and leaks.
• Sherwin Williams RV-specific primer, paint, and clear coat applied, to ensure there is no flaking or dripping.
• A galvanized steel storage compartment with rubber storage mats installed, providing protection for your personal items.
Furthermore, each vehicle’s sidewalls, floors, and slide pieces are vacuum bondlaminated and constructed with HSLA.
HSLA is a type of alloy steel with low carbon content which provides superior mechanical properties and resistance to corrosion.
“YOUR FAMILY WILL FEEL SAFE WITH OUR PRODUCTS. WHEN YOU DRIVE OUR UNITS, YOU DON’T GET THE ‘WOBBLY BOX’ FEEL YOU MIGHT GET WITH UNITS THAT USE LIGHTWEIGHT ALUMINUM”
– DAVE MIDDLETON, PRESIDENT, NEXUS RV
“This change allowed us to grow exponentially and become the fastestgrowing motorhome company in the US,” prides Donati.
With a clear focus on Class C and Super C product manufacture, the company’s range today includes vehicles built on chassis manufactured by Ford, General Motors (GM), International®, and Freightliner Custom Chassis.
Known for having the best built motorhomes on the market, Nexus RV
proudly implements a best-in-class construction philosophy, epitomized by its high-strength, low-alloy (HSLA) steel-framed units.
“No other manufacturers use this framing strategy, which creates a 72 percent stronger structure when compared to aluminum, awarding our units with higher safety standards and enhanced driving quality,” he asserts.
In addition, by using no wood products in its vehicles’ roofs and
sidewalls in favor of AZDEL Onboard® composite, a lightweight alternative, Nexus RV offers its customers improved insulation and higher R-values, and lower road noises. By using true heating, ventilation, and air conditioning (HVAC) ducting, Nexus RV is able to transfer air from the front to the rear of the unit for continuous ventilation. Moreover, this system allows for the easy cleaning of ducts for those that battle with breathing issues.
“IF WE’RE ABLE TO EXPAND AS A BUSINESS, THIS WILL INCREASE OUR BUYING POWER AND ALLOW US TO LOWER OUR OVERHEADS TO ACHIEVE MORE COMPETITIVE PRICING”
– CLAUDE DONATI, MANAGING MEMBER, NEXUS RV
“We are also the only manufacturer using galvanized storage bins and wrap-round fiberglass roofs in our Class C Mini Homes.
“Better materials last longer and work better for our customers,” Donati emphasizes.
As a company that prides itself on building the best-constructed, safest, and most durable motorhomes in the industry, Nexus RV is dedicated to delivering a broad range of vehicles to its audience.
“Overall, your family will feel safe with our products. When you drive our vehicles, you don’t get the ‘wobbly box’ feel you might get with units that use lightweight aluminum,” Middleton outlines.
The quality of Nexus RV’s products can be attributed to its constant dedication to innovation and ability to adapt to needs and trends within the industry.
As such, for the first time in 15 years, the company is building on the SRV2 chassis from Freightliner for its Wraith Super C unit.
“This project seeks to provide the best alternative for our customers to buy Super Cs under $200,000,” excites Middleton.
In fact, Nexus RV boasts the number one best-selling Super C under this price point, chosen by 54 percent of the market, which positions the company as a strong option for first-time RV buyers or those impacted by recent market inflation.
In addition, the business is considering entering the Class B market, which will provide customers with even more cost-effective options.
inquiries@efpcorp.com
efppackaging.com
Nexus RV does whatever it takes to ensure its customers remain happy. As such, it has tripled its workforce of late, whilst Middleton has focused his time investing in customer care.
“We’ve added some software components to our customer care activities, and we monitor social media like a hawk to ensure we can immediately address any potential issues,” he expands.
In addition, the company’s strong supplier relationships have helped it remain at the top of its game by providing access to global market information.
WHAT CORPORATE SOCIAL RESPONSIBILITY (CSR) PRACTICES DOES THE COMPANY PARTICIPATE IN?
Claude Donati, Managing Member: “In 2021, we established a company-wide goal to give back to the community.
“We committed to a local domestic shelter, Safe Haven, that is run by the Young Women’s Christian Association (YWCA). Recently, our 100-strong team of associates attended the facility to take part in a renovation of the entire shelter.
“As a result of our involvement in this important community project, we spend a lot of time collecting clothes, food, and raising money to support the shelter.
“When we first made the announcement of our commitment to Safe Haven, I had several employees notify me how happy they were to help as they had used the shelter during difficult times in their life.”
“Our local vendors are an incredible source of information, and their proximity allows us to rely on their expertise to improve our design.”
Recently, some of Nexus RV’s biggest suppliers have become global, adding value by way of international reach.
Furthermore, exclusive relationships, such as the company’s work with Navistar on the MV chassis, allow the company to benefit from healthy and multifaceted industry connections.
Going forward, Nexus RV recognizes that future innovation must start with its chassis manufacturers, such as Ford, GM, and International®.
Currently, it is also taking small steps to prepare for the electrification
of the RV market, but until then, it remains in wait.
“The stumbling block for transitioning towards the electric vehicle (EV) market continues to be the range of vehicle. Currently, there are several chassis’ companies building electric chassis, but due to the limited battery supply, these can only go around 100 miles before recharging is required. The recharging takes around eight hours making this application unrealistic to RV users,” Donati notes.
Having grown exponentially since its inception in 2010, Nexus RV plans to expand its current portfolio to provide the company with alternatives should one market experience a downturn.
“If we’re able to expand as a business, this will increase our buying power and allow us to lower our overheads to achieve more competitive pricing,” he concludes.
Tel: 574-970-0848
cdonati@nexusrv.com www.nexusrv.com
We revisit Waterville TG with Sylvain Dube, General Manager of Business Strategies, as he tells us about the company’s vast history of innovation and leadership and how it continues to design high-performance vehicle sealing solutions that exceed expectations
Writer: Lauren Kania
Project Manager: Kieron Harvey
With a proud history marked by a constant search for the best solutions, Waterville TG has been guided by the bold and visionary spirit of its founders since its inception in 1952.
Beginning with sponge rubber products in Quebec, Canada, the company has worked diligently over the past seven decades to become experts in the development of custom sealing systems for vehicles whose quality and performance have since become recognized globally.
This international recognition stems from the technical expertise, R&D investments, and experienced employees that Waterville TG prides itself on.
To this day, the company continues to rely on these assets to support each customer in the design and manufacturing of sealing systems that improve comfort for vehicle occupants.
Since last speaking to Waterville TG in October 2022, the business has progressed even further in evolving its product offerings, creating positive environmental contributions, and
developing investments towards automation within the manufacturing industry.
“We are a supplier of dynamic and static weatherstrip systems for the automotive industry,” reintroduces Sylvain Dube, General Manager of Business Strategies at Waterville TG.
“We offer a turnkey service to our customers, from the custom design to material development and manufacturing process up to the mass production of these parts.”
Amongst the company’s vast client base, it can count major automotive manufacturers such as Ford, General Motors (GM), Honda, Stellantis, and Toyota for both their mass-market and premium brands.
Waterville TG has expanded across Quebec and Ontario with the construction of three production plants and one distribution center, and now boasts over 1,000 dedicated employees who work daily to showcase the reason behind the company’s long-standing global reputation.
Initially hired at the end of the 1980s, Dube quickly rose through the ranks at Waterville TG and was eventually trusted with the audacious mission of creating a sales office in the heart of Detroit, Michigan.
After seizing the opportunity to relocate to Belgium to work for TG
Sylvain Dube, General Manager of Business Strategies: “Since last year, we have been awarded multiple new contracts. Our customers recognize the benefits of an experienced team, our ability to launch new vehicles flawlessly, and the importance of quality weatherstrip systems.
“In 2024, we are planning to continue to deliver excellence by supporting new vehicle launches, most of which will be available in hybrid, plug-in, or BEV variants. These products are crucial for our customer product portfolios, and we are glad they trust us to support these next-generation vehicles.”
Europe, before moving back a few years later to gain experience as a Sales Manager for other companies in Quebec, Dube returned to Waterville TG in 2022 as the General Manager of Business Strategies.
“Having grown from my experience as Product Line Director at Michelin, my strategic vision, leadership, and passion for sustainable development are undoubtedly assets that will ensure the future of Waterville TG,” he enthuses.
One of the investments the company highlighted previously was its push towards automation, specifically its heavy investment in manufacturing robotics with the goal of increasing automation by 2030 in order to remain competitive.
“We are continuing our efforts towards process automation. We’ve invested in manufacturing robotization over the past few years to improve our process from an ergonomic standpoint while improving our global standing,” insights Dube.
Since 2023, Waterville TG has been delivering parts from automated
“FOR US, SOCIAL RESPONSIBILITY IS THE POSITIVE IMPACT OUR COMPANY CAN HAVE ON PRESERVING THE ENVIRONMENT, CREATING PLEASANT WORKSPACES, AND BUILDING COMMUNITIES PEOPLE WANT TO LIVE IN”
– SYLVAIN DUBE, GENERAL
MANAGER OF BUSINESS STRATEGIES, WATERVILLE
TG
processes to its customers. The company has faced some challenges due to the nature of its parts being soft; despite this, it managed to retain strong support from clients during this transition as they understand the long-term benefits of automated production.
“We have even served as a good example of a business case for original equipment manufacturers (OEMs) by ensuring the safe launch of production during the technological transition,” furthers Dube.
In addition to advancing automation, Waterville TG has also continued to accentuate its focus on supporting battery electric vehicle (BEV) customers in a disruptive industry environment.
As analysts are describing the uptake of BEVs as ‘cooling’, with less demand from customers and a slower adoption rate, the company has observed reduced vehicle output, a slow down in the BEV product cycle plan, and a hold on investments.
“As a supplier, we are closely monitoring the variation in volume forecasts and customer cycle plans, and subsequently aligning our product portfolio to the market.”
With natural disasters occurring at a rapidly increasing rate due to the effects of climate change, automakers recognize the socioeconomic impacts of these events and therefore quickly shifting to zero-emission vehicles such as BEVs and fuel-cell electric vehicles (FCEVs).
Waterville TG is a frontrunner in these global efforts, working to combat the large amounts of CO2 emitted over the lifecycle of automotive products.
“Previously, we mentioned that we had adopted the philosophy of a circular economy, and carbon neutrality is a part of this global initiative,” insights Dube.
“We were already closely tracking the carbon emissions of our activities and reporting in Manufacture 2030, a platform that works to empower manufacturers and suppliers to cut emissions by at least 50 percent by 2030, which our customers can access to achieve their carbon neutrality goals.”
Progressing these targets even further, the company became carbon neutral for its direct operations in 2023, alongside the energy it purchases for its Quebec and Ontario sites.
Its mid-term vision includes contributing to local projects to offset its emissions and investing in
infrastructure to continue to reduce emissions at the source.
“Our long-term goal, meanwhile, is to ensure full carbon neutrality across our entire value chain, including suppliers, customers, and the use of our products, which is an enormous challenge for any company with sustainability objectives,” details Dube.
In addition to Waterville TG’s carbon neutrality goals, it has also introduced a new automated ethylene propylene diene terpolymer (EPDM) molding process for opening trim weatherseals, a world first.
This innovative leap marks a significant milestone in
“ULTIMATELY, I SEEK TO EMPOWER MY TEAM TO IDENTIFY AND ADDRESS INEFFICIENCIES, CULTIVATE A MINDSET OF CONTINUOUS IMPROVEMENT, AND DRIVE SUSTAINABLE GROWTH AND INNOVATION”
– SYLVAIN DUBE, GENERAL MANAGER OF BUSINESS STRATEGIES, WATERVILLE TG
Milan Conception was founded in 2007 and specializes in the design and manufacturing of automated industrial machines. The founders, Steeve Michaud and Benoît Langlois, along with their team, quickly revolutionized the automotive sealing sector by creating the first High-Speed ICM (Insert Clip Machine) with a cycle time of less than 0.5 seconds per clip. This innovation propelled the company onto the global stage, ensuring significant success.
Milan Conception places innovation, research, and development at the heart of its mission. The introduction of the ICM FLEX version has successfully disrupted market standards by allowing tooling changes and infinite versatility, all achieved in a simple and efficient manner.
Do you have needs? We have ideas!
The company extends beyond the automotive sealing domain, developing products for various sectors such as recreational vehicles, automated saws, and a diverse range of testing machines, to name just a few.
Since 2021, with the introduction of TransMetal, its new division, the company has significantly diversified its range of offered services. Through advanced equipment provided by a renowned company, they are now able to offer laser cutting and metal bending services with exceptional precision. This collaboration not only enhances the company's ability to produce high-quality results but also strengthens its operational efficiency, reducing production times and optimizing production processes.
Milan Conception considers customer satisfaction as a fundamental concern, the basis of its success. With the aim of establishing lasting and fruitful relationships, ensuring mutual long-term success, each team member fully invests time in thoroughly understanding the specific requirements of each customer.
Teamwork equals success.
Milan Conception also places great value on its employees, fully recognizing their essential role in the company's continued success. It provides a professional environment focused on well-being, recognition, and skills development, significantly fostering motivation, productivity, and the fulfillment of each individual.
Milan Conception is committed to continuing its exploration of innovation to contribute to the evolution of the global industrial market.
1,000+ employees
FOUR sites in Canada
70+ years of expertise and innovation
manufacturing, revolutionizing the way weatherseals are produced by using a fully automated robotic cell.
“Traditionally, weatherseal production has been a labor-intensive and time-consuming process, often prone to human error, efficiency, and variability,” informs Dube.
“However, with the implementation of an automated molding process, we have effectively streamlined
production operations, minimizing manual intervention while maximizing output consistency.”
This adoption of new, industryshaping technology underscores Waterville TG’s commitment to innovation and excellence in the automotive sector that will redefine the manufacturing landscape for years to come.
In an effort to reduce waste and minimize the company’s environmental footprint further, Waterville TG is working towards reusing reclaimed EPDM in compound mixing.
“We have a new mantra of ‘cradle to cradle’ instead of the typical ‘cradle to
grave’, meaning that the end goal is to revalorize products by reintroducing them inside new production,” expands Dube.
There are some challenges to this new venture, including the reclaiming process itself, designing the product with reuse in mind, and collecting material following the usage.
However, despite these obstacles, the company’s intent is to increase the ratio of recycled material inside new batches of rubber while still keeping the same physical properties compared to a ‘virgin’ recipe.
“Additionally, since 2007, we have been an active member on the Board of Directors of Foundation Estrienne en Environnement, which promotes environmental protection and sustainable development in the
Eastern Townships region,” asserts Dube.
In parallel to furthering environmental sustainability, being a respectful corporate citizen is a priority for the company as it sincerely believes in local community involvement.
Waterville TG plans to continue to support local organizations such as Centraide Estrie by taking part in its awareness campaign every year, along with making donations – both financially and materially – to organizations and institutes, including École de la Passerelle, Bishop’s University, Course Unis Pour la Cause, Collège François-De La Place, École des Enfants-de-la-Terre, and Équipe Élite alpin de l’Estrie.
As the company looks ahead, it
envisions a future where Waterville TG continues improving its efficiency, quality, and agility.
“Ultimately, I seek to empower my team to identify and address inefficiencies, cultivate a mindset of continuous improvement, and drive sustainable growth and innovation,” concludes Dube.
The company has proven over its 72-year history why it has been chosen by the biggest names in the global automotive industry to develop and manufacture their sealing systems, regardless of the type of vehicle.
As Waterville TG continues to provide tailor-made sealing systems that exceed even the highest customer demands, its future promises further innovation, growth, and international recognition.
Tel: (819) 837-2421
serviceressourceshumaines@wtg.ca www.watervilletg.com
From chutes to custom cattle working systems and pens, Arrowquip has been creating best-in-class livestock equipment since 1988. The company’s executive team come together to tell us more
Writer: Lily Sawyer | Project Manager: Michael Sommerfield
Guided by its mission to influence the global cattle handling industry through the practical application of animal science and welfare standards, and to increasing producer safety and profitability with innovative equipment, Arrowquip emerges as a cattle handling equipment company with a difference.
Deeply invested in its vast dealer network, Arrowquip provides ongoing support for each of its partners by
equipping them with the tools that they need to thrive.
Supported by a 160-strong base of dedicated employees, the company produces manual and hydraulic cattle chutes, alleys, tubs, feeders, and more for its global market.
“We manufacture equipment at our head office in Manitoba, Canada, then send it off to our various dealers across North America and Europe to sell to ranchers,” introduces CEO, Mark Firth.
Arrowquip’s core company values are rooted in fairness, togetherness, and industry agility, whilst the business strives to continue to help the cattle industry to succeed through its products.
As beef is a mainstay of the world’s current food ecosystem, Arrowquip is trying to improve this important industry.
As such, potential challenges that arise are tackled by the company with a sense of excitement and a growth mindset.
“Something can only be exciting if it is challenging! Maintaining the status quo only drives complacency, low energy, and a mood of losing,” outlines CIO, Jerry Langrell.
With herd cow inventories at an alltime low and the highest cattle prices the industry has ever seen, Arrowquip
Jerry Langrell, CIO: “Inspiration at Arrowquip is not just from one source. We get it from each other – we’re a group of people with similar passions that align around a few core values, and that creates inspiration!
“Our end users’ shared experiences, combined with interactions with clients during our after-sales service, have provided great insight and endless inspiration for our teams.
“But that’s not all we have. As we observe the global industry, we look into the future and that provides timely inspiration.
“Furthermore, there are a few world-renowned cattle handling experts that have committed their life to enhance and educate this industry. Their knowledge and insights have been a great inspiration, propelling us to design systems that are built for cattle, not just the operator. In other words, we create something where you get voluntary movement from the animal as opposed to using force or fear.
“Beyond that, it’s just plain hard work and our daily commitment to ensuring a better future for ranchers. It’s what gets us out of bed in the morning and provides that sense of worth when the day is done!”
recognizes that this makes for a challenging business environment, however, it is also a landscape with great opportunities for those that can see ahead.
“The introduction of beef production at small levels is gathering momentum, attracting newcomers to the industry,” Langrell points out.
Local production and supply is currently flourishing across the world, which gives producers more control over their product and drives forward their marketing efforts.
This, in turn, brings higher quality food into the hands of consumers and provides larger returns for local producers.
“Further to this, it is exciting to see the dairy industry partnering with the beef industry. This will grow our overall reach and ensure our voice in the world is heard,” he enthuses.
Arrowquip’s constant exploration of the market, coupled with its interactions with end users, brings the company real-life feedback in order to
30 Harvest Drive, CentrePort, Manitoba, R4B 0A6 204-296-8422 nji@shaw.ca njindustries.ca
NJ Industries is a custom metal fabrication facility located in Winnipeg, Manitoba, Canada, servicing all North America for the past 16 years. We have years of experience in laser cutting, bending, welding, fabricating, and assembly. We also have the capability to quickly meet your production requirements and timelines.
NJ Industries currently provides services to many different areas such as the agriculture, automotive, railway and marine industries. In addition, we offer warehouse protection and storage solutions such as custom rack guards and custom storage cages. Finally, we offer research and development services to create a suitable product for your needs. At NJ Industries the possibilities are endless. Get in touch today, and we’ll work with you to ensure our manufacturing capability exceeds your requirements.
• At Arrowquip, a dedicated client care team works hard to ensure every customer is satisfied with the equipment they receive.
• The department is quick to get to the bottom of an issue and fix it promptly – for example, if a customer calls and they have an issue with their chute.
• Arrowquip recognizes that an issue can usually be resolved through a phone call, but it goes to great lengths to assist customers when this is not the case.
• For example, the company has seen recent instances of the client care team engaging in video calls with customers to help them resolve their issue.
stay relevant in today’s ever-changing industry environment.
“If it’s not broke, we fix it! We have global thinking and access to best practices, learnings, and new developments. Furthermore, our ability to network across the globe is a catalyst for change,” Langrell elaborates.
In addition, Arrowquip has taken an automotive approach to manufacturing of late, as it builds quality and repeatability into every product it manufactures. In this way, the company is able to provide an industry-leading warranty for every product.
Ensuring the safety of both the animal and the operator is of utmost importance to how Arrowquip develops and services its equipment. Therefore, the company leaves nothing to chance and creates immediate action when it receives feedback from customers.
In late October last year, Arrowquip launched a line-up of over 30 new products, a step change that had never before been achieved in the company’s history.
Impressively, Arrowquip was able to implement its new product portfolio in less than two weeks.
“Our ability to integrate our continuous product innovation is one of our key differentiators,” says Chief Manufacturing Officer (CMO), Dallas Cornell.
The company’s new line-up of Arrowlock cattle chutes is drastically different when compared to its previous line of Q-Catch chutes.
Firstly, the Arrowlock chutes are longer, taller, and wider. The head gate is also now designed using a ratchetlooking mechanism that gives users a more secure hold on their livestock
and requires less force.
“A manual cattle chute that can truly do it all is available for your ranch!” Cornell declares.
Arrowquip’s suppliers and valued dealer partners are considered the backbone of the company, and its chutes are all built at its headquarters in Canada with exclusively North American-made parts.
“We value our suppliers’ commitment to providing quality parts on time and their flexibility to our changing
demand,” he enthuses.
Primarily due to its dealers’ timely and reliable services, Arrowquip is able to maintain its noteworthy commitment of a four-week turnaround from order to delivery.
Product placement is also important to the company, whilst dealers across North America, the UK, and France allow Arrowquip to touch the lives of ranchers around the world.
“Our impact on this industry would not have been possible without our network of dealers. They not only make the equipment accessible, but are passionate advocates for ranchers,” Cornell imparts.
As a company deeply involved in all things cattle, over half of Arrowquip’s innovation team currently either have a family ranch or have been personally involved in the agricultural industry at some point in their careers. As such, its know-how in this sector is unparalleled.
“Two of our engineers actually test our products on their own ranch!” Langrell reveals.
With an engineering team that boasts both hard and soft skills, Arrowquip is able to relate to both its customers and internal departments on several levels.
“While many engineering teams isolate themselves and let their hard skills and personalities take precedence over communication and collaboration, our engineers are fully integrated and involved in every
department,” he prides.
The company believes that this integrated approach breaks down walls, builds trust, and leaves egos at the door, which has given Arrowquip the ability to build speed, creativity, and fun into its operations whilst solving its customers’ challenges on a daily basis.
Going forward, the company’s key priorities include continuing to innovate and improve its products, expanding its market reach, and maintaining its commitment to exceptional customer service in the agriculture industry.
“We aim to hit specific growth targets and goals, expanding our presence in both new and existing markets. We aim to reach 50,000 ranches and offer families a product they can be proud of for generations to come,” Firth summarises.
Diversification and expansion into new product lines or markets are also part of the company’s long-term growth strategy.
Of late, an upgraded manufacturing facility has provided Arrowquip with the capacity to meet growing demand and innovate its product offerings, and it is excited about the opportunities that lay ahead.
“We will continue to inspire tomorrow’s rancher by solving problems today,” he concludes.
Tel: 1-866-383-7827
marketing@arrowquip.com
arrowquip.com
Combining a small business company culture with global corporate capabilities, CPI Aero, Inc. is diligently solving the needs of North America’s defense and commercial aerospace sectors. We find out more from members of the business’s senior leadership team
Writer: Lucy Pilgrim | Project Manager: Michael Sommerfield
We are a small business with a family atmosphere, but the company behaves and is organized as a large corporation.”
The opening words of Dorith Hakim, CEO, President, and Board Director of CPI Aero, Inc. (CPI Aero), perfectly encapsulate the ethos and
world-renowned capabilities of the aerospace manufacturing company, operating in the upper echelons of the sector in North America.
CPI Aero’s outstanding presence in the industry is underpinned by the legacy of its founder, Art August, whose humble family business
worked hard to serve the growing aerospace sector in the early 1980s.
August subsequently grew the company’s order book before deciding to go public in the early 1990s, approximately a decade after CPI Aero’s inception.
“The heritage of our founder is still present; his name remains attached to the facility, and his legacy is still evident in CPI Aero today,” states Jay Mulhall, Vice President of Business Development.
When taking the company public 30 years ago, the abbreviation CVU was used as its stock ticket number, referring to a long-standing aviation term: ceiling and visibility unlimited – the optimum conditions for flying a plane. This was subsequently
used as the theme for growing and developing the business and has remained CPI Aero’s stock symbol to this day.
Being a small business allows the company to be flexible and nimble
in its operations, while its structure, similar to those found in much larger organizations, means that it can meet the demands of its customers on relatively large, complex contracts.
“We like the fact that we’re a lot faster than a larger corporation and able to react to issues ahead of time,” Hakim highlights.
CPI Aero primarily operates as a buildto-print manufacturer, specializing in the assembly and integration of complex mixed commodity aerostructures and aerosystems for the US Department of Defense (DoD) and other defense and commercial customers.
“We work mainly in structural assembly, which means we build all kinds of assemblies that go on or in fixed and rotary wing aircraft,” Mulhall informs.
The company’s primary operations include the mechanical assembly and integration of aircraft components into a larger structure.
CPI Aero assembles the structure from components or sub-assemblies –such as sheet metal parts, composite assemblies, machined parts, and hardware - procured from suppliers before integrating other components, also either procured directly from suppliers or manufactured at the company.
This includes wiring harnesses, hard tubing, insulation, ducting, actuators, sensors, or heating and cooling systems. This allows CPI Aero’s customers to take its products and integrate them immediately into their next higher assembly.
The integrated and assembled parts include wing, fuselage, and engine structures, doors and control surfaces, fuel system components, airborne pods, and much more, which are structurally built up from both metallic and composite parts.
Across the commercial arm of CPI
Aero, the company primarily works with aircraft structures in support of the business and executive jet market. The scope and scale of these aerostructure and aerosystem assemblies are perfectly aligned with CPI Aero’s capabilities and facilities. In support of the defense market, the number of aircraft CPI Aero’s customers produce per year is also well aligned with the company’s capabilities.
“The defense market is really in our wheelhouse, particularly as the business continues its growth into airborne pods, unmanned and autonomous vehicles (UAVs), and missile systems,” offers Mulhall. These products are primarily used on aircraft that support intelligence, surveillance, and reconnaissance (ISR) missions.
The US DoD and the defense sector’s original equipment
“WE ARE PURPOSEFULLY ORGANIZED TO SUPPORT OUR CUSTOMERS AND THE PROGRAMS THEY HAVE TRUSTED US WITH AND MAKE THE NECESSARY INVESTMENTS TO BE CONSIDERED LONG-TERM PARTNERS”
– DORITH HAKIM, CEO, PRESIDENT, AND BOARD DIRECTOR, CPI AERO, INC.
manufacturers (OEMs) sell products across the US and international markets through allied nations, thus expanding CPI Aero’s geographical reach.
Indeed, a large majority of the company’s overall revenue is generated through its presence in the defense sector.
“We track the important programs of the US DoD and identify the awarded prime OEM companies as potential customers of CPI Aero. We have good insight into this market and
are already supporting the US Air Force directly and most of the major OEMs,” Hakim outlines.
Another discriminator for the business is its manufacturing engineering organization and organic expertise in tool design and fabrication.
Whether it’s responding to new product development by leveraging 3D printing for rapid prototyping or coordinating the fabrication of CPI Aero-designed large assembly tooling, the company is ready to partner with customers on products
that span the production lifecycle, from new designs through full-rate production and into sustainment.
CPI Aero is likewise very wellversed in cybersecurity, making all the necessary investments to comply with required standards. This is a particular focus in the defense sector due to the associated high cybersecurity risks.
CPI Aero nurtures a special relationship with customers, as it supports them in design specializations as they execute new concepts.
The company provides its customers with design for manufacturing and assembly (DFMA) expertise, allowing them to focus on their design of products that best accomplish the mission at hand.
“Our clients know that they can count on CPI Aero’s experience in building and integrating products, and we are often an extension of their integrated product teams (IPTs). These partnerships become very important and the foundation of wellexecuted programs,” Mulhall adds.
“We love when a customer comes to us with a new product so we can help
them mature the design and make it more affordable and faster to produce while maintaining the highest quality.”
Because CPI Aero is wholly dependent on the supply chain to feed the detailed parts that it assembles and integrates, supply chain management is at the heart of everything it does, from sourcing and kitting for the assembly floor to selling kitting and supply chain management as a service to OEM customers and the US Air Force.
“We manage large, complex bills of material in support of new aircraft production or repair and overhaul programs for several of our customers.
We become a one-stop shop for thousands of part numbers, aggregated into hundreds of kits, which get delivered to their factories or repair depots at just the right time to get integrated onto the aircraft,” expands Mulhall.
“It also means that we see the full lifecycle of a product, making it easily maintainable after it’s delivered to an end user,” explains Hakim.
The company has witnessed the industry’s technological advancements, progressing from its initial workings with two-dimensional
DEVELOPING A TALENT PIPELINE
CPI Aero takes a proactive approach to developing a talent pipeline and hiring individuals based on their personality and determined work ethic.
“We often consider whether they fit into the culture and the type of environment they need to work in. That way, we can always train them with the necessary skills,” divulges Mulhall.
Regarding the structural mechanics segment of the company, CPI Aero runs a series of apprenticeship programs in which it hires students who have recently graduated from high school and introduces them to a specialized program. Here, graduates spend several weeks learning the basic skills and nurturing the right mindset and mechanical abilities to complete the job efficiently.
Additionally, CPI Aero’s small business ethos means that its workforce is maintained through talent retention and fostering a family culture.
drawings and incredibly simplified technical information.
Today, CPI Aero utilizes threedimensional electronic mediums that have eliminated many timeconsuming steps, thus speeding up the sourcing of complex engineered components and the methodization of the assembly and integration of finished products.
“It mitigates mistakes and misinterpretation, making it faster and easier to create a high-quality product through a seamless process that connects customers to CPI Aero and CPI Aero to its suppliers digitally,” Mulhall adds.
Moreover, aircraft design has adapted to industry changes since the company’s inception over 40 years ago, as evidenced by the types of materials that are used to create component parts including lightweight composites and metallic alloys that provide greater strength. There has also been a considerable
A significant portion of CPI Aero’s aerosystems assembly and integration product line is airborne pods.
Some pods are delivered to customers with just the structural assembly while others are fully integrated into a turnkey deliverable product, which means that the customer only has to install their proprietary payload – such as a camera, radar system, or other prime mission equipment - and then deliver it to their end-user customer.
CPI Aero puts its pod products through rigorous testing that includes pressure testing, electrical testing, and full dimensional tolerance control.
The pod offerings come in a range of sizes and maturities. For instance, a few of the company’s pods are at the end stages of the program, while some are in the design, first article, or flight-testing stage, and others are moving into full-rate production. CPI Aero is able to leverage the lessons learned on earlier programs and apply them to the newer programs.
“We are recognized in the industry for supporting these types of integrated products, not just because of our technical expertise, but because of our consistent quality delivery to our customers,” notes Hakim.
effort in the sector to design larger parts to cut assembly costs. One example is the move from sheet metal build-ups to larger machined metallics and engineered composite parts. Indeed, aerospace manufacturing has moved toward simplification, waste
reduction, and faster manufacturing processes.
“It has been incredible to see the industry evolve, and CPI Aero has been front and center on this journey to faster, more streamlined manufacturing,” insights Hakim.
Valco is a service-disabled, veteran-owned aerospace company located in Southwest Oklahoma. Since its founding in 1989, Valco has supplied Military, commercial, and general aviation needs worldwide. AS9100 and NADCAP accredited,Valco specializes in aerospace sheet metal forming, component assembly, and heat treatment.
CPI Aero’s success in staying up to date with innovation can be attributed to the fact that it is not afraid to invest in the right opportunities to support burgeoning market growth.
“This is something that I’m very passionate about. We are purposefully organized to support our customers and the programs they have trusted us with and make the necessary investments to be considered longterm partners,” affirms Hakim.
The company’s workforce is specifically organized into programled integrated product teams that are focused on customer requirements and staffed by all the required subject matter experts in areas including program management, engineering, production control, supply chain management, and quality.
This ensures that resources are used effectively and professionals remain focused on their mission to support bespoke manufacturing
Our customers include: CPI Aero, Lockheed Martin, Northrop Grumman, Bell Flight, Sikorsky, and Piper Aircraft.
Phone: 580-255-4300
Website: www.valcomfg.com
Address: 1009 Boren Rd, Duncan OK 73533
offerings. It also provides an easy point-to-point interface with various functions within customers’ organizations, making for more timely and efficient communications and issue resolutions.
This particular structure also removes all communication barriers as managers are located in close proximity to the manufacturing process and can physically see the product being built, which means they can address any potential issues quickly and are held accountable for their program performance.
“The beauty of being a small business is we don’t have to worry about functional barriers. We’re a program-led company that focuses on individual strengths and functional skillsets,” observes Hakim.
With this clear mindset and devoted mission, CPI Aero will continue to invest in the company and its people going forward as it witnesses abundant future business opportunities.
Additionally, its flourishing reputation has helped drive its growth and ability to exceed customer demands while also maintaining the highest standards.
“We’re not so hyper-focused on growth that we’re going to take our eyes off flawless execution,” ends Mulhall.
“I joined the company two-and-ahalf years ago, and in that time we have turned the company around. CPI Aero is a different business from what it was five years ago, and the journey doesn’t stop today,” Hakim concludes.
Tel: (631)586-5200 jmulhall@cpiaero.com www.cpiaero.com
Revving up the industry with its specialty trailers and truck bodies, Kentucky Trailer is a leader in designing and manufacturing custom transport vehicles. President, John Kwapis, discusses the company’s skills, services, and solutions
Writer: Rachel Carr | Project Manager: Michael Sommerfield
Along the west side of the Appalachian Mountains lies the US Commonwealth of Kentucky, hemmed by the Ohio River on its northern border, which flows directly next to the major urban center of Louisville.
The Bluegrass State’s largest city is home to Kentucky Trailer Manufacturing and Kentucky Truck Body (Kentucky Trailer), founded in the Gilded Age of 1879 and known
at the time as the Kentucky Wagon Manufacturing Company.
Impressively, it originally produced some of the nation’s most popular horse-drawn carts and became the largest wagon manufacturer in the world. Indeed, its unmatched quality and workmanship still stand today.
The company acquired the assets of Hercules Motor Cars in 1916 and moved its production to Louisville, becoming the first automobile
manufacturer in the city, where its primary facility remained until 2009.
“In 2009, we relocated to a new 240,000 square foot (sqft) facility specifically designed for mixed-model trailer production. Additionally, the truck body division has a 100,000 sqft facility with dedicated space for decal installation and a paint booth for trailers and truck bodies,” introduces John Kwapis, President of Kentucky Trailer.
John Kwapis, President: “The KT Leadership Operating Model emphasizes the importance of championing our associates with a focus on delivering results.
“By encouraging open communication and transparency, team members feel heard and understood. This creates a healthy and positive environment where associates can contribute their unique insights to the business. This commitment to working together leads to innovative solutions that benefit the company and its customers.
“Kentucky Trailer’s KT Leadership Operating Model emphasizes operational excellence and social responsibility with a focus on ethical business practices. Thus, it facilitates decisions that improve the well-being of its communities and the environment, creating a positive impact.
“Our company culture is defined by a commitment to ‘Safety First and Always’ — our goal is to remain completely accident-free. Each associate is empowered to make a difference and contribute to maintaining a safe and secure work environment.”
“We produce composite, sheet and post trailers, and truck bodies for dry freight transportation, moving and storage, packaged delivery, and highly specialized transportation needs. If a company needs a customized vehicle with doors, windows, heavy-duty floor rating, interior buildouts, etc., we are the go-to solutions provider,” he continues.
Kentucky Trailer’s moving and storage clients include Allied, Atlas, Mayflower, North American, United Van Lines, and many more. Other specialty-application customers encompass the largest snack food producers and top package delivery companies in the US.
Furthermore, the company is known for extending the life of its trailer and truck bodies beyond their original purpose. Many of these moving and storage trailers are repurposed into tractor pullers, marching band equipment, football equipment, and workshop trailers.
These advantageous elements make Kentucky Trailer a prominent player in the competitive US market and a leading global manufacturer of trucks and trailers.
The manufacturing industry has experienced significant change over the years. However, with technological advancements and the recent transition to electric vehicles (EVs), Kentucky Trailer is determined to remain competitive.
“The focus on EVs adds an exciting new dimension to the production process, which includes training employees, engineering drawings, power stations, and lightweight designs. This alters the fleet owners’ needs and makes multiple power options available,” Kwapis observes.
As the US EV industry evolves, Kentucky Trailer is rapidly expanding and providing solutions to exceed its customers’ expectations.
“An important customer is using our trailers in its sustainability efforts as the company incorporates electric trucks into its fleets,” he reveals.
Indeed, Kentucky Trailer is constantly developing its products to outpace a competitive market and is launching a new plate truck body designed using state-of-the-art technology later this year.
“The plate truck body will be lighter and easier to repair, with an aerodynamic corner design that maximizes the space inside the body for many use cases to deliver products and services. Our panels exceed our leading competitors for density and resistance to delamination,” prides Kwapis.
In addition, the body will feature brighter, damage-resistant panels for increased visibility. The vehicle’s structural integrity is maintained with a robust aluminum corner cap and an extruded front-corner vertical post that allows for easy repairs.
“We offer different mounting options that are easy to affix to your chassis or can be delivered to you, as well as multiple chassis power options. In addition to gas and diesel, we also have EVs, hybrid vehicles, compressed natural gas (CNG), liquefied natural gas (LNG), and liquefied petroleum gas (LPG) available.”
Thanks to its fully galvanized frame and cross-members, the truck body structure and side walls are incredibly durable, likely to render the industryleading five-year warranty redundant.
“With all Kentucky Trailer products, our durability delivers a low total cost of ownership, and representatives deal directly with our factory to experience unparalleled customer service and delivery performance,” outlines Kwapis.
Kentucky Trailer often needs to make modifications for specialty sectors due to its diverse client base.
“WITH ALL KENTUCKY TRAILER PRODUCTS, OUR DURABILITY DELIVERS A LOW TOTAL COST OF OWNERSHIP, AND REPRESENTATIVES DEAL DIRECTLY WITH OUR FACTORY TO EXPERIENCE UNPARALLELED CUSTOMER SERVICE AND DELIVERY PERFORMANCE”
– JOHN KWAPIS, PRESIDENT, KENTUCKY TRAILER
“Our innovative trailer design offers a platform that provides a 20 percent increase in cargo capacity in comparison to a straight floor trailer, a perfect solution for the moving and storage industry due to its highquality fit and finish,” Kwapis points out.
Similarly, the extreme durability and maximum interior heights improve the speed of loading and offloading for the package delivery sector, last mile delivery, less-than-truckload (LTL), and third-party logistics (3PL).
While Kentucky Trailer Specialty Vehicles (KTSV), in Michigan provides commercial transport for mobile data centers, kitchens, workshops, classrooms, and marketing activities, it also supplies the medical industry and the US government with even more specialty modes of transportation.
“KTSV and our AMST division in Illinois facilitates the provision of medical services to hospitals and underserved areas by transporting both equipment and people.
“To ensure the safety, comfort, and security of patients and staff, we implement radiofrequency (RF) shielding for diagnostic imaging systems. Additionally, we design vehicles for sterilization, mammography, endoscopy, mobile laboratories, and workshops to meet the necessary standards,” explains Kwapis.
The US government, meanwhile, requires a mobile sensitive compartmented information facility (SCIF) and includes disaster response, recovery, national defense, communications, training, and laboratories through KTSV.
“KTSV also provides enclosed
transport delivery vehicles for luxury automobiles, motorcycles, snowmobiles, and other high-end applications.”
Regarding its manufacturing procedures, Kentucky Trailer employs automated processes and pioneering equipment to build sidewalls and floors to attach key components.
“Telematics and smart trailer assist devices are becoming more prevalent in the industry, such as back-up cameras, vehicle diagnostics, and tire pressure monitors, with many more options becoming available each year,” he divulges.
Since its inception 145 years ago, Kentucky Trailer has undergone many transformations.
Its latest incarnation occurred in 2014 when the company became a majority-owned subsidiary of Alleghany Capital Corporation (Alleghany).
The Tway family, whose bold vision led to truck-drawn trailer production when R.C. Tway purchased company assets in 1936, retained a minority stake after Alleghany was acquired by the Berkshire Hathaway Group (BHG). Kentucky Trailer is now part of Marmon Holdings Inc., which is owned by BHG and includes 11 industry groups.
2001 – Kentucky Trailer Services opened an 80,000 sqft facility in Louisville, offering complete trailer and truck body repair, reconditioning, and aftermarket support for modifications.
2003 – Kentucky Trailer Specialty Vehicles opened in Michigan, heralding the start of its journey into the specialty segment. It moved to its current 132,000 sqft facility in 2018.
2010 – Kentucky Trailer Services opened a facility in California with the purchase of Western Truck and Trailer.
2014 – The company acquired AMST in Illinois and moved to its current 85,000 sqft facility in 2020 to expand its finish, calibration, and reconditioning capacity. Products and services include manufacturing mobile imaging trailers for MRI, PET/CT, and CT specialty vehicles for healthcare systems in North America.
2015 – Kentucky Trailer acquired SMIT Mobile Equipment B.V., a global manufacturer of mobile medical imaging trailers and solutions for the medical sector in The Netherlands and the UK.
2018 – Kentucky Trailer reached a definitive agreement to acquire a majority interest in CEI Equipment in Iowa. CEI Equipment has rebranded as KT Pacer.
2019 – KT Pacer acquired Warren Manufacturing Inc.’s animal feed transport division. It provides fabricated parts for various Kentucky Trailer divisions and
“BHG and Marmon Holdings Inc. have positioned the company for growth and expansion with new products,” according to Kwapis.
Going forward, the company’s focus is on the Lean 5S methodology, the 80/20 strategy, continuous improvement, resources for automation and innovation, and training and education opportunities for its associates.
Furthermore, Kentucky Trailer prioritizes product durability over cost-cutting measures.
“Our goal is to provide the highest
quality product at the best price possible; that model requires a constant focus on improvement and supply chain excellence,” he emphasizes.
Kentucky Trailer centralizes supply chain operations for its Louisville locations to leverage group spending, and various support personnel are available at each of its individual sites.
The company uses over 50 supply chain sources, with most partners based in the US, including divisions outside Louisville.
“Although we have some strategic
offshore resources, we are proud to possess a strong group of domestic partners. It is important to remember that your supply chain’s strength relies heavily on robust alliances. As a company, we take great pride in developing and nurturing our relationships as our partners are the backbone of what we build,” concludes Kwapis.
In the future, Kentucky Trailer will remain a significant player in the truck plate body business by focusing on innovative solutions that meet customers’ specific requirements.
Tel: 502-637-2551 marketing@kytrailer.com www.kytrailer.com
PALFINGER USA is the premier and cost-effective provider for all your liftgate needs. We offer a full range of products for all applications, since our beginnings in 1993.
As fleet operators in auto parts, beverage, food service, rental, studio rental, general and special freight, you can rely on our liftgate technology to help keep your trucks on the road.
Innovative liftgates from PALFINGER are available in a complete range of styles to suit your specific needs: Folding, Rail, Slider, Cantilever and Cargo Van solutions. As the industry innovator in operations and safety, our high standard commitment helps confirm that your transported goods
DEMAND THE ONE BRAND WITH DECADES OF PROVEN PERFORMANCE.
For over six decades, Truck-Lite products have delivered market-proven reliability for maximum uptime, ensuring that your operations run smoothly and confidently.
Crafted from impact-resistant polycarbonate and epoxy-sealed electronics, our lights provide the ultimate protection against the elements. Our 88- and 99-Series wiring harnesses are meticulously designed with cutting-edge technology and rugged materials for enhanced performance and durability.
Whether it’s our premium signal and marker lamps, custom designed headlamps, or wiring harnesses, Truck-Lite products have set the standard for the industry, ensuring unparalleled visibility and safety for every journey on the road.
Learn more about these products and our warranty at truck-lite.com.
Mi Integration is an innovative and efficient partner offering collaborative and integrated engineering services through a wide range of products, tooling, and polymer injection procedures, mainly for automotive sealing systems and multi-material products. We unpack the company’s story with President, Vincent Houle
Writer: Ed Budds | Project Manager: Kieron Harvey
Founded in 1984, Mi Integration (Mi), a family business born in Sherbrooke, Quebec, shines brightly through its value-added and innovative products, which are used by the automotive industry around the world.
Over the last three decades, Mi has distinguished itself through its top-tier expertise, natural creativity, and the thoughtful manner in which it efficiently solves complex design and performance needs.
Vincent Houle, President
“As a manufacturer always on the lookout for new opportunities, we pride ourselves on our ability to quickly and effectively adapt our service offering,” introduces President, Vincent Houle.
In the face of the COVID-19 pandemic, a difficult period that seriously affected the automotive industry, Mi demonstrated its resilience by capitalizing on its established expertise in sealing and product development.
In this way, the company has managed to respond and diversify its portfolio in personal protective equipment (PPE) and the healthcare sector, where a new division, Mi Protection, was created to offer high-performance products that improve safety for all while remaining environmentally responsible.
Houle believes that the automotive industry in general is a highly interesting and rigorously challenging landscape where participants must embrace innovation and endeavor to make and do things differently.
“I like to be connected to the market and clients’ needs, then transpose this internally to our team to get the best out of them and realize great projects and harness innovation,” he sets out.
“I have worked in business development for many years, and in 2017, I
became President of Mi, where my role is to find the right balance between strategy, organizational development, and lean manufacturing.”
A truly game-changing development for the company was the creation of its own Mi lab in 2015, which exists as an R&D center for innovative new products and technology integration.
“Our dedicated people in the Mi lab work very hard as we want to position ourselves as the first point of contact when clients need to improve their working cell process or product performance,” Houle affirms.
As more complex and innovative designs continue to evolve throughout the industry, the company must stay agile and respond to new trends and developments.
Undoubtedly, there are many
exciting projects taking shape across the entire automotive manufacturing market, and Mi continues to establish itself as a partner looking to add as much value as possible to its assembly operations.
“We like to simplify something that might look complex at the beginning, and if Mi can help to enhance a demanding trend in the market, this is where we become an accelerator,” Houle tells us.
Another important trend Mi aims to play a more significant role in relates to sustainability.
“This is difficult to position ourselves within as a small player in the value chain, but obviously, the interest in developing products, materials, and processes that help our planet is an axis that we will emphasize in the coming months and years.”
Mi’s involvement in Mexico began in 2011, and its total investment in the country to date totals $6 million, which has been poured into the company’s facilities in San Luis Potosi.
“All of our units are important, and this new geographical expansion represents a good growth opportunity for us. There are countless talents in Mexico as they
have been thriving in the automotive market for many years now and have felt the level of maturity and expertise emerging from this,” Houle expands.
By adapting the culture and leadership style to Mi’s new colleagues in Mexico, the company is developing true synergy between its Canadian and Mexican operations.
Today, Mi’s Mexico plant mainly focuses on the mass production of thermoplastic injection molding,
VISION
The company aims to become an integrator of innovative solutions in order to optimize the internal performance of its global clients by concentrating on high-quality designs and customized production.
GROWTH STRATEGY
Mi is aiming to establish a global presence, as each day, its dedicated team works with diligence to earn its status as a global leader in the automotive industry. The company’s footprint continues to grow at an international level, so Mi looks to ensure a good understanding of the market and remain close to its clients.
but the company is increasingly developing autonomy in terms of engineering and product development.
Furthermore, Mi estimates that up to 75 percent of its new business will be produced in Mexico, mainly because of its proximity to clients.
Beginning as a localization strategy at first, the San Luis Potosi facility is a strategic location that will continue to help Mi enhance its business.
For Mi, the investment has been worth it. About one-third of the company’s revenue is now earned through its Mexican operations, and as further investment is realized, this number is expected to grow. Mi will also launch a new facility of close to 100,000 square feet in Ramos Arizpe, which aims to be fully operational in October 2024. This will be delivered to better respond to the company’s needs in the northern regions of Mexico and the Southern US.
The power of the company’s dedicated and hard-working staff is the most important tool at Mi’s disposal.
“RIGHT NOW, ACROSS NORTH AMERICA, THERE IS A REAL OPPORTUNITY TO POSITION OURSELVES AS A STRATEGIC PARTNER FOR MANY COMPANIES”
– VINCENT HOULE, PRESIDENT, MI INTEGRATION
“We try to empower our staff with a sense of purpose by utilizing our corporate strategic plan and bringing this to all members so they can understand the reasons why they are carrying out a specific action,” Houle tells us.
Mi has curated a thriving culture where it encourages and celebrates staff achievements, from the smallest
milestones to the biggest wins, alongside inviting its people to lead a project they feel passionate about and develop within the organization.
Concurrent to this, Mi works with colleges and universities to provide a chance for young professionals to experiment and develop a project within the company that enlightens them.
“I am personally involved in a new foundation to develop the leaders of tomorrow. This is a fresh but promising initiative, as I find it interesting to help people from ages 15 to 17 explore new pathways and provide access to leaders who manage companies and teams so they can better understand leadership concepts that are often neglected in broader education programs,” he excites.
Moving forward, Mi’s key priority is to organize the business in order to effectively scale its operations. With many new and exciting clients in its portfolio, customer satisfaction is therefore the company’s major focus, and its team is aligned to develop and create numerous successful projects.
Alongside the aforementioned launch of Mi’s new manufacturing
plant in the north of Mexico, the company recently opened a new sales and engineering office in Detroit at the beginning of 2024 as part of an objective to become more widely known and develop a better relationship with the entire value chain, which in turn will help Mi to drive innovation faster and more efficiently.
“We need to understand our clients’ challenges and personalize
WITTMANN BATTENFELD CANADA INC.
35 Leek Crescent | Richmond Hill Toll free: +1 888 466 8266 Christian Weiss christian.weiss@wittmann-group.ca info@wittmann-group.ca
our approach and development to meet these communicated and latent needs,” Houle acclaims.
“Our service offering is vertically integrated from product design to mass production, passing through a rigorous product development process to build optimal capabilities.
“Right now, across North America, there is a real opportunity to position ourselves as a strategic partner for many companies. Cost reduction,
@WittmannBattenfeldCanada
Tel: +1 514 355 8907
Stefan Tremblay stremblay@anplastps.com Quebec Representative www.wittmann-group.com
localization, and technology integration are all opportunities where we could potentially play a significant role in the automotive industry,” he concludes.
This exciting landscape promises to open up multiple opportunities that Mi could not necessarily have accessed if the sociopolitical climate was the same as 10 years ago.
While this evolving sector still exists parallel to countless
uncertainties, the company must now take advantage of the current trends and remain agile with further evolution on the way.
Tel: 819-822-3697 info@mi-integration.com www.mi-integration.com
Since last speaking to Aerosonic, the company has progressed in its provision of complete air data systems to meet the demands of the biggest aerospace organizations. Alexandre Lebeau, Vice President of Sales and Marketing, and Greg Van Bemden, Vice President of Engineering, delve deeper
Writer: Lucy Pilgrim | Project Manager: Michael Sommerfield
The last 12 months have witnessed considerable turbulence in the aerospace sector, following significant global supply chain constraints arising from the aftermath of the COVID-19 pandemic, compounded by increased military demand from multiple global conflicts and recent issues found in Boeing aircraft fleets. These challenges have highlighted
the growing need for a robust supply chain of dependable parts manufacturers.
“Supply chain delays and issues with original equipment manufacturers (OEMs) have provided Aerosonic with an opportunity to gain additional market shares across the entire commercial transport segment, with our expanded Federal Aviation Administration (FAA) Parts
Manufacturing Approval (PMA) product line for the Airbus and Boeing family of aircraft,” introduces Alexandre Lebeau, Vice President of Sales and Marketing.
Furthermore, the growing level of worldwide conflict has caused the increased use of unmanned aerial vehicles (UAVs), thus increasing the demand for lighter and flexible air data products that can be utilized on smaller and more constrained aircraft.
Ongoing conflicts around the world have also raised global defense spending, as aircraft manufacturers use proven technology to accelerate the entry of new aircraft into service and bring new capabilities, which is well suited for Aerosonic’s secondgeneration of integrated multifunction probes (IMPs).
In the past year, Aerosonic has substantially increased its avionics capabilities, fortifying itself as a bestin-class provider for notable names in the industry.
For instance, the company recently received an FAA PMA for an updated pitot probe that met the latest AS5562 icing standards for all A320s, A330s, and A340s aircraft types. This probe is now available as a one-to-one replacement for any OEM products onboard these Airbus fleets.
Meanwhile, the company’s legacy pitot probe on the 737 family was also approved by the FAA to cover the 737 MAX family of aircraft, which is set to resolve recent OEM reliability issues.
“Additionally, the PMA of the pitot probe was expanded to cover the latest Boeing 737 MAX aircraft without modifications to the legacy design. This is thanks to its superior design and robust service history, thus complementing the overall Boeing PMA portfolio,” highlights Greg Van Bemden, Vice President of Engineering.
On top of this, the company recently completed the Preliminary Design Review (PDR) of the latest generation of multi-function probes. The resulting new product line, MULTISENSE™, consists of a family of probes and mating Air Data Computers (ADC) that are aimed at smaller aircraft, such as UAVs and electric vertical take-off and landing (eVTOL) aircraft, alongside a fully integrated version for regional and business aviation.
The customer benefits of MULTISENSE™ include optimized weight and size, fewer parts on the aircraft, higher reliability and availability, and lower integration and maintenance costs translating into the improved total cost of ownership for the operators.
“As aircraft continue to fly higher and faster, the requirements for more robust air data systems are steadily
increasing. As a result, Aerosonic has developed an air data flight test boom capable of surviving the extreme environments found in modern military aircraft,” opens Greg Van Bemden, Vice President of Engineering.
The air data flight test boom measures total and static pressure, total air temperature, angle of attack (AoA), and angle of sideslip (AoS). It is then used during test flight campaigns to calibrate the aircraft’s integrated air data systems.
A highly significant ongoing project for Aerosonic is the expansion of its multi-function fixed air data probes for UAVs and eVTOLs. The company recently developed a modular architecture for the quick customization of probe bases to match unique aircraft mounting requirements.
The modular architecture extends to design assurance level A (DAL A) air data computers to reduce the amount of testing required for new multi-function fixed air data probe configurations.
The Technical Standard Orders
(TSO)-certified MULTISENSE™ provides Aerosonic with the unique ability to offer any aircraft a multi-function solution, whether integrated or federated, with lower integration costs.
On top of this, the second generation of IMPs for military fighter jets and trainers have been flying for more than a year, with the products nearing the final approval stage for low-rate initial production (LRIP), ready for four new aircraft platforms being fielded across Europe and Asia.
The organization continues to differentiate itself through strategic partnerships that elevate its capabilities to meet growing demand.
“One of Aerosonic’s strengths is its ability to focus on the projects that yield the most return for our customers and shareholders,” states Lebeau.
For example, leveraging its extensive air data solutions portfolio, the company has partnered with
With engineers who engage directly with global aircraft manufacturers, Aerosonic aims to attract aerospace enthusiasts who are keen to take part in delivering safety-critical air data solutions to the next generation of aircraft.
The company’s business units are co-located in its Clearwater facility, which means that buyers, planners, manufacturing, quality and design engineers, and sales leaders are all under one roof, something the company is very proud of.
“Co-location improves communication amongst the business and solidifies ‘One Aerosonic, One Team’. We constantly highlight to our workforce that what we do matters,” Van Bemden proudly states.
• Aligning with the government’s green initiatives for the civil market to replace traditional powerplants with electricpowered aircraft, which has driven the demand for lighter air data systems that require less power.
• Development and production of wind tunnel capabilities.
• Advancing its environmental testing ability to support the development of environmental stress screening (ESS) capacity, with a new ESS chamber being delivered at the end of 2024.
another major air data system provider to enable the sale of complete air data systems to its evolving customer base.
“Safety regulations require dissimilar air data systems as primary and back-up systems. Few companies can offer both for every aircraft,” affirms Van Bemden.
The company is equally a step ahead of its competitors in supporting its customers’ aircraft-level critical point analysis (CPA).
Aerosonic recently made a significant capital investment to increase its computational capability, enabling it to place air data products in optimum positions on aircraft and determine the concentration factors needed to safely test products according to the latest standards.
Another differentiating factor is the further expansion of Aerosonic’s flight test boom product line, which now possesses a larger range of AoA and AoS capabilities. Its portfolio
was also expanded to include a new line of booms for high-stress military environments as well as smaller booms to support aircraft production purposes.
In addition, the company has significantly invested in automating critical steps in the probe manufacturing process, such as brazing and polishing. This will improve the overall quality and on-time delivery of its core products whilst preparing for the ramp-up of advanced air mobility.
“By investing in the automation of the brazing and polishing processes across our probe product lines, we expect to see significant improvements in the overall quality and delivery of our core products,” details Van Bemden.
To add to this, Aerosonic also consistently commits to high standards of health and safety.
“Lastly, we increased our contributions to multiple SAE Air Data Working Groups by hosting
two of their quarterly meetings at our Clearwater facility in Florida. The groups are creating and improving standards to maintain the safety level that everyone expects from the aerospace industry,” voices Van Bemden.
Looking towards the future, Aerosonic has a number of projects in the pipeline that it is eager to commence once resources are available. For instance, the company’s main focus includes designing products for efficient heating and aerodynamic performance.
“Our future project funnel leverages these core competencies to expand our traditional offerings and grow through adjacent product lines,” reveals Van Bemden.
Another priority for the company is innovating its manufacturing processes.
Family owned and in business for over 40 years.
Van-Ess Manufacturing, Inc. Brooksville FL 34604
352-754-3060
Email: Quotes@Van-Ess.com
“We’ve demonstrated success in implementing new automation solutions for our legacy and nextgeneration processes, which allow Aerosonic to insource more subcomponents and increase our capabilities and capacity,” concludes Van Bemden.
This ultimately allows the company to better serve its customers with less volatility within the supply chain, providing shorter lead times.
With a stringent target to achieve continuous growth year on year, Aerosonic is also investing heavily in productivity improvements to steadily increase its quality and on-time delivery.
These elements facilitate the organization’s foundation of trust with customers, which allows the company to bring in new businesses from a focused portfolio of new projects.
In 2024, Aerosonic is looking forward to delivering the first shipsets of MULTISENSE™ to its launch
customers in order to support their test flight campaigns and type certification efforts.
Finally, this year also sees the company transitioning its second generation of IMPs and integrated static ports (ISPs) into low-rate initial production, further pushing the boundaries for aerospace innovation.
Tel: (727) 461-3000
Revolutionizing rail travel, Stadler US is making its mark with its state-of-the-art facility, which manufactures cutting-edge trains that are not only tailored to meet the unique needs of customers but also set new standards in the industry
Writer: Rachel Carr | Project Manager: Kieron Harvey
Since the 1820s, railroads have played a pivotal role in US transportation.
Initially, horses and steam engines pulled rudimentary wooden freight cars, but as the industry evolved, the US soon began developing its own rail manufacturing capability as early as the 1830s.
During the Industrial Revolution, railroads advanced significantly, becoming a critical mode of transportation for raw materials over long distances. Since then, trains have undergone major improvements, a testament to the innovation and growth of the rail travel industry.
Not only did this progress shape the nation’s infrastructure and economy, but it also laid the foundations for companies like Stadler US to thrive.
In 2023, Utah State University (USU), the ASPIRE Engineering Research Center (ASPIRE), and Stadler US collaborated to develop and test a battery-powered passenger train.
Based on the Fast Light Intercity and Regional Train (FLIRT) Akku concept, it has been successfully implemented in the US as the first multiple-unit train with a battery drive.
However, adapting the project to US infrastructure and national regulations requires extensive R&D.
Despite starting as a transport pioneer, the US railway system has been deteriorating for decades with almost no upgrades. As a result, only one percent of rail lines are electrified in the country. However, years of neglect have created the ideal conditions for Stadler US’ battery-powered passenger train, which provides a zero-emission alternative to dieselpowered vehicles.
ASPIRE is developing the trackside charging infrastructure for the train, which will enable emission-free rail transport on nonelectrified routes in the US.
An ideal transportation solution for areas without overhead electric infrastructure, it also allows for longer routes, as the FLIRT Akku train has demonstrated a range of 185 kilometers.
Stadler US is the stateside division of Swiss manufacturer, Stadler Rail, whose rich history dates back to 1942 when Ernst Stadler founded an engineering office in Zurich.
Three years later, Stadler Rail began producing battery and dieselpowered locomotives, with its first passenger vehicles rolling off the production line in 1984. This history of innovation and expertise has been a cornerstone of the company’s success and earned it a reputation for reliability and trust in the rail travel industry.
In 1989, Stadler Rail made a groundbreaking contribution with the introduction of the first modular vehicle. This innovation paved the way for successful business development and solidified the company’s position as the world’s leading manufacturer in the rack and pinion sector.
These lightweight vehicles, equipped with various rack and pinion systems as well as track gauges, are designed to handle extreme landscapes and gradients, showcasing Stadler Rail’s longstanding leadership in the industry.
Today, Stadler US has a varied product range of rail cars and rolling stock for the North American market, spanning from trams to high-speed trains.
Although the company has been operating in the country since 2002, it wasn’t until 2019 that Stadler US opened its first production site in Salt Lake City, Utah.
The facility imports car shells and bodies from Europe, but Stadler US plans to change this to reduce its carbon footprint.
In the rapidly evolving landscape of Smart City Transportation, the r2p Group stands out as a beacon of innovation and excellence. Founded with the mission to design and develop intelligent technology systems that set the highest standards in quality and safety, r2p has become synonymous with cutting-edge solutions for the mobile transport sector. Our collaboration with Stadler US is a testament to our shared values of innovation and excellence, marking a significant milestone in our journey to redefine transportation.
Since its inception, r2p has embarked on an extraordinary journey of growth and innovation. Our comprehensive portfolio includes CCTV, Passenger Information Systems, Network Audio Solutions and Automatic Passenger Counting, all equipped with real-time data transfer capabilities for rail and road vehicles, as well as fixed infrastructure.
Headquartered in Flensburg, Germany, the rapidly growing r2p Group operates internationally in 45 countries with competence centers in Australia, Canada, Malaysia, Denmark and the United Kingdom. With additional subsidiaries and offices in the US, Spain, Italy, Switzerland and Brazil, r2p takes pride in being a truly global company.
The r2p NetSpire solution redefines flexibility and scalability in Passenger Information System applications. As a clienthosted, networked IP-based system, it offers unparalleled modularity, allowing for easy configuration and integration with existing infrastructure. From integrated public address systems to passenger information displays and passenger emergency intercoms, r2p NetSpire delivers a comprehensive integrated solution that enhances passenger experience and safety, supported by a robust web interface for effortless transit operator management.
Our flagship CCTV software solution, r2p HORIZON,
Passenger Information System
epitomizes innovation by unifying our entire CCTV product portfolio under one intuitive, modular platform. Designed for efficiency and ease of use, r2p HORIZON allows for seamless remote management and maintenance of r2p CCTV services, ensuring our customers can enjoy reduced operational costs and enhanced fleet availability. r2p Horizon is available as a highlysecured Software-as-aService or on-premise hosting solution, with our experts’ user support and software maintenance. All options comply with our high GDPR and security standards.
Our newest subsidiary, r2p USA Inc., harnesses the r2p Group’s unparalleled global depth of knowledge in OEM
hardware manufacturing, software development, and systems integration. As a wholly owned subsidiary of T.G. Baker Americas Inc. (part of the r2p Group, headquartered in Toronto, Canada), who has been delivering major transit projects for many years, r2p USA Inc. is equipped with the tools to successfully support the full turnkey project delivery of our integrated Passenger Information Systems, mobile CCTV and Automatic Passenger Counting solutions across the US. Our state-of-the-art manufacturing facility in Buffalo represents our commitment to delivering Buy American Act (BAA)compliant products that exceed industry standards. Our involvement in several major existing US CCTV and Passenger Information System projects including
the MARTA Metro Train Replacement Project (Atlanta, GA), the KCATA Streetcar Project (Kansas City, MO), the HART LRT Rail Project (Honolulu, HI) and the MBTA Green Line Project (Boston, MA) underscores our dedication to excellence and innovation as well as signaling our intent to expand our presence in the US market. With the implementation of our strategic sales presence in Chicago, IL, and our BAAcompliant manufacturing facility in Buffalo, NY, r2p is poised for further growth, ready to forge new partnerships and explore new opportunities in the North American market.
At r2p, we are driven by a vision to revolutionize the landscape of intelligent transportation solutions.
Our commitment to quality, innovation, and customer service is unwavering, as we continue to push the boundaries of what is possible. We invite you to join us on this exciting journey to explore the possibilities and shape the future of Smart Mobility in
Rob Little Senior Account Manager - Integrated Systems
T: +1 312 771 028 6 | M: robert.little@r2p.com
Sean Coster Managing Director
T: +1 843 907 2085 | M: sean.coster@r2p.com
the US. Let’s embark on this road to innovation together, with r2p leading the way. To learn more about our capabilities, discuss partnership opportunities, or schedule a visit to our manufacturing facility, please contact our dedicated team.
r2p USA Inc.
50 Fountain Plaza Suite 1400
Buffalo 14202
USA
T: +1 905 669 8422 M: usa-info@r2p.com
Modular vehicle concepts
HIGH-SPEED – SMILE
INTERCITY – FLIRT200, KISS200
REGIONAL TRAINS – GTW, WINK, KISS, FLIRT160
CITY TRANSPORT – TINA, TANGO, TRAMLINK, VARIOBAHN, METELITSA, CITYLINK, underground trains
LOCOMOTIVES – EURO9000,
EURODUAL, EURO6000, EURO4001, EUROLIGHT, SALI, Central Cab, customized locomotives
TAILOR-MADE – Multiple unit rail vehicles, rack railways, carriages
Alternative drive solutions
BATTERY ELECTRIC DRIVE – FLIRT Akku
HYDROGEN DRIVE – FLIRT H2
In 2022, the company also signed a Memorandum of Understanding (MoU) with the California State Transportation Agency (CalSTA) and the California Department of Transportation (Caltrans) for the design and delivery of four zeroemission trains, with the option to purchase up to 25 units.
FLIRT has been successfully operating in extreme climates worldwide, from Africa to the Arctic
Circle. As part of the company’s range of alternative solutions, the FLIRT H2 model utilizes hydrogen fuel cells as its energy source. The train operates entirely on electricity and stores kinetic energy in batteries under braking. The electricity generated is then used to power the train, charge the lithiumion traction batteries, and feed the onboard heating, ventilation, and air conditioning (HVAC)
system. The propulsion system, meanwhile, allows FLIRT H2 to operate throughout the day without refueling.
Stadler US delivered the first hydrogen-powered train for passenger rail transport in 2019, selling its first FLIRT H2 vehicle in the country. The lightweight aluminum single-decker model can be arranged in two to four-car compositions.
This year, Stadler US proudly announced that the FLIRT H2 was entered into the Guinness World Records database for the longest distance achieved by a pilot hydrogen fuel cell electric multiple-unit passenger train without refueling or recharging – 1,741.7 miles.
The company’s innovative strength and technological prowess in sustainable rail transport have been highlighted by this impressive achievement.
Knowledge Architects Inc. and Stadler Rail are set to revolutionize workforce development training and its delivery through the implementation of advanced training aids to support transit agencies across the US. Sheila Jordan, Knowledge Architects Inc.’s CEO, reflects on how this strategic partnership represents a significant leap forward in the realm of transportation training.
Step into the future of transportation training with Knowledge Architects Inc. (KA) and Stadler Rail as they embark on a groundbreaking partnership to redefine workforce development in transit agencies across the United States. Sheila Jordan, the visionary CEO of KA, shares insights into this exciting collaboration and its transformative potential.
At the heart of KA’s mission is a dedication to leveraging cuttingedge technology and
innovative instructional design to empower the workforce. Renowned for their expertise in crafting immersive training solutions, KA is teaming up with Stadler Rail, a global leader in railway
The partnership kicks off in Atlanta, GA, where KA and Stadler will deliver over 3,000 hours of training content specifically designed for the new rail cars being delivered to MARTA (Metropolitan Atlanta Rapid Transit Authority). Sheila Jordan emphasizes the importance of imparting technical knowledge
vehicle manufacturing, to elevate training standards to unprecedented heights
and instilling practical skills for real-world scenarios. With over two
decades of experience in organizational development and learning technology, Sheila is passionate about nurturing the talents of the next generation of workers. KA and Stadler’s collaboration extend to Boston, MA, where they’ve developed interactive 3D models and 4K simulation video content for the Massachusetts Bay Transportation Authority (MBTA), focusing on the innovative Green Line Train Protection System (GLTPS) designed exclusively for MBTA. This system incorporates cuttingedge Assisted Braking and Collision Avoidance functionality. Through engaging video content, KA demystifies the intricacies of GLTPS, emphasizing safety and operational excellence, thus reassuring the transit agency leaders, and making them feel confident in the training initiatives.
But their vision doesn’t stop there. With the opening of a new office in
Chicago, IL, KA is poised to make a nationwide impact. As Chicago’s Metra invests in Stadler’s Battery Electric Multiple Units (BEMUs), KA stands ready to provide tailored training solutions, ensuring that Metra has access to the latest advancements in technology and instructional design. This nationwide expansion should make the employees in the transportation industry feel proud and part of a larger mission.
These exciting transit projects cement KA’s solid
partnership with Stadler to revolutionize transportation training and set new standards of excellence and innovation. With each partnership, they’re not just shaping the future of workforce development –they’re driving it forward with passion and purpose.
“We are delighted to partner and collaborate with Stadler on projects in Atlanta, Boston, and Chicago
Sheila Jordan CEO, Knowledge Architects Inc.
“WE ARE CONSTANTLY IMPROVING THE PERFORMANCE AND EFFICIENCY OF OUR TRAINS USING STATE-OF-THE-ART TECHNOLOGIES”
– STADLER US
Stadler US is happy to create custom vehicles to suit each customer.
After starting with the production of single vehicles and small-batch series, the company now offers many years of experience and engineering expertise to meet specific needs, guaranteeing flexibility and quality.
Rail operators benefit from Stadler US’ personalized approach, allowing for tailor-made locomotives
to meet special requirements in construction, shunting, and journeys with combined gear wheels and adhesion.
Alongside trains, Stadler US offers customized signaling and digital solutions and services to ensure efficient and sustainable rail operations. It also provides continuous customer care beyond train delivery, ensuring reliable and safe rail operations.
HaslerRail is the market-leader and innovative supplier of performance and safety-relevant on-board electronics, sensor, software and data management products and solutions for the railway industry.
Our on-board product range includes event recorders, speed and odometry sensors, energy measurement systems and HMIs. For operators of passenger and freight services connectivity and information are key.
By combining our on-board technology and software solutions we unleash the full power of Big Data analytics to uncover trends, patterns, and correlations in large amounts of raw data. This provides operations and maintenance teams valuable insights and empowers them to make data-informed decisions.
Our products and solutions are available for new build or retrofit projects.
We can specify, manufacture and deliver field-proven solutions that enable the safe, efficient and sustainable operation of intercity, regional and light rail vehicle fleets.
And our worldwide network of manufacturing and customer service facilities means that we can provide support swiftly and locally.
Elliot Flores, Sales & Business Development Manager - elliot.flores@haslerrail.com
Monica Morgan, Project & Site Manager - monica.morgan@haslerrail.com
Robin Foreshew, RailData Sales & Business Development Manager - robin.foreshew@haslerrail.com
As a specialist in the design and manufacture of highly complex assemblies for rail vehicles, we offer customized solutions of the highest quality. Our lean organizational structures enable efficient production and short communication channels, resulting in rapid implementation of your projects.
We understand our customers’ requirements and offer assemblies that can be supplied with fire protection certificates, insulation and other specific requirements on request.
With our many years of experience, state-of-the-art technology and infrastructure, we are your reliable partner for complex assemblies in rail vehicle construction. Place your trust in the expertise of Letrona AG for highquality, customized solutions that meet your exact requirements.
Stadler US trains are produced in small series and optimized for individualization and quality, in contrast to the model series of tailormade multiple units. The company offers custom-made carriages for driving trailers, passenger cars, panoramic carriages, and sleepers with a wide range of interior design, HVAC, and technology options. Furthermore, its trains are
cost-effective and cutting-edge, providing passengers with maximum comfort.
In 2019, Stadler US was also contracted by the Dallas Area Rapid Transport (DART) to build eight FLIRT trains and design the equipment maintenance facility (EMF) for the Cotton Belt Regional Rail Project.
In the same year, the Metropolitan Atlanta Rapid Transit Authority (MARTA) awarded Stadler US a contract worth over $600 million to build 127 metro trains for the Atlanta area.
The contract specified that the new trains must be based on the previous models and required the integration of modern technology into the old specifications.
Stadler US has implemented a Youth Apprenticeship Program inspired by the Swiss model to handle the high volume of contracts it receives.
This program is designed to ensure that the company has the necessary talent to complete the orders. In the first year, students can choose between the Automatic Technician (electrical) and Production Technician (mechanical) tracks.
In the second year of their apprenticeship, trainees attend courses at Salt Lake Community College, receive supplementary training from Stadler US, and are integrated into regular production.
In the final year, advanced lectures are conducted at the college, whilst more skilled, practical training continues at the company. To graduate from the program, apprentices must successfully complete final testing and a final project.
The purpose of the intensive training is to ensure Stadler US maintains the high standards of the long and illustrious history of Stadler Rail.
Transforming Transit with New CQ400 Trains
Thanks to Stadler, MARTA will provide a safe, modern ride, moving millions of people through our region and propelling transit into the future.
Swiss Quality Rolling Stock Cables for sustainable mobility
www.studercables.com
Worldwide, BETAtrans® GKW-ENX cables are selected for their low LCC. They offer outstanding performance with their lightweight design, low fire-load and high L.O.I., providing additional advantages.
Allowing customers to focus on what matters most – the thrill of the outdoors – Yakima Products Inc. has a proud history of providing trusted solutions that transform the way people travel and enjoy the open road
Writer: Lauren Kania | Project Manager: Kieron Harvey
Whether you are heading out camping, biking, hitting the water, or taking the family on a holiday road trip, Yakima Products Inc. (Yakima) believes that any adventure, regardless of the destination, creates shared experiences and memories between loved ones that last a lifetime.
Having begun as a passion project in 1973, Otto Lagervall, an avid inventor and paddlesports enthusiast, began creating handmade foot braces for canoes and kayaks in his family’s small machine shop, located in the company’s namesake city in Washington, embarking on a 50-year journey that would take Yakima across the globe.
Boasting a history of making bold moves in the name of new horizons, the company has worked hard, embraced challenges, and taken risks to continue to lead the niche market with the same enthusiasm and innovative mindset it was conceptualized with.
Yakima’s trusted solutions have transformed the way people travel. Indeed, the company is a trendsetter in its sector, packing heritage, safety, design sensibility, and street smarts into every product.
Together with its network of respected retailers, the business proudly provides its customers the freedom to wander, the right to be unruly, and the confidence to go rogue.
Traveling the winding road home, the memories and connections made with friends and family remain long after the trip ends. Yakima handles roof racks, LocknLoad systems, and roof boxes in order to keep its customers’ minds on the joy of the journey.
For over five decades, Yakima has placed a high emphasis on the design philosophy behind its many product offerings.
Its first consideration when formulating a new product is the
people using it. The company contemplates the possible challenges individuals may face when carrying their favorite gear and focuses on creating innovative solutions to solve these hurdles.
Due to this well-rounded approach, Yakima’s products are intuitive, longlasting, and easy to use by all.
When finding a perfectly fitted roof rack or box, the company’s dedicated in-house team is committed to fitting vehicles no matter the shape, make, or size to ensure rack solutions are available for nearly every car on the road.
Yakima even goes as far as to offer
Vehicle Finder, a customizable online tool that allows its users to visualize which product will work with their vehicles, making the perfect choice
Regardless of the destination or adventure, Yakima helps to get its customers, their friends, and all of their gear to the desired spot, allowing people to focus on what really matters – creating memories to last a lifetime.
easy and navigable.
While it is one thing to design a great rack, it’s quite another to build one.
That is why the company has highly skilled design engineers who pair years of mechanical experience with expert-level material knowledge to ensure that the best performance and longest lifespan can be guaranteed.
With the motto of tried, tested, and true, once Yakima has built a roof rack, the product goes through rigorous and merciless testing in order for the company to confidently say it will stand up to whatever a customer puts it through.
From snow-peaked mountain passes to rural dirt roads, the business has tested and fine-tuned every one of its products to last. That’s why Yakima can offer all of its bike racks, ski racks, roof boxes, and other products with a five-year limited warranty.
Yakima offers a range of products and services to its wide customer base, including crossbars, LockNLoad roof racks, bike racks, winter sports racks, water sports racks, roof racks, accessories for camping, and 4x4 racks and accessories.
1973 – The company was founded by Otto and Jeanne Lagervall in Yakima, Washington. Otto’s first claim to fame was the invention of the foldable metal music stand. Yakima introduced its first national product, the Gold Rush Bar.
1979 – Steve Cole and Don Banducci purchased Yakima, envisioning a better future for hauling recreational sporting equipment. They moved Yakima to Arcata, California, and began fitting gear on cars.
1984 – Yakima’s brand promise held true when it built aerodynamic fairings for all race vehicles at the 1984 Summer Olympics. Yakima was also the official rack supplier for the 7-Eleven cycling team, who won nine gold medals.
1995 – Yakima’s first locking fork bike mount, SteelHead, was introduced.
2005 – The company moved its headquarters to Oregon and vowed to keep friends in cars and keep Portland weird.
2008 – HoldUp and SwingDaddy, two new hitch racks, were released to the public and received critical acclaim. Yakima engineers soared 62 feet to win Red Bull Flugtag in Portland, going down in history.
2010 – Kemflo Group purchased Yakima, Whisbar, and Prorack, with all three brands then selling in North America, Australia, and New Zealand.
2018 – Yakima US and Yakima Australia exist as sister companies. The former continues to produce cargo management systems products while the latter engineers off-road capabilities. The brand now sells in North America, Europe, Australia, New Zealand, South Africa, and the Middle East.
“OUR STORY IS MORE OF A JOURNEY, BECAUSE WE’VE NEVER BEEN GOOD AT SITTING STILL. AFTER ALL, WE DON’T HAVE WILD SIDES; WE HAVE WILD SOULS”
– YAKIMA PRODUCTS INC.
LockNLoad roof racks, in particular, are the strongest and quietest heavyduty roof rack systems on the market, with a load rating of 75 kilograms (kg) per bar and end caps featuring a tiedown point rated at 100kg each.
With an aerodynamic shape and rubber load-protector strip, the LockNLoad roof rack is designed in Australia with the idea being that if it can survive the harsh outback touring conditions Down Under, it can survive anywhere.
The result is a heavy-duty roof rack that can handle endless highways, gravel roads, rugged deserts, and steep mountains without breaking a sweat.
Most importantly, the LockNLoad roof rack features a built-in bottle opener, allowing customers to crack open a cold drink after a long drive.
Complementing the gamechanging innovation of the LockNLoad roof racks, Yakima offers
additional accessories for all kinds of camping trips.
The company provides roof boxes and racks to ensure customers don’t have to worry about getting their gear, friends, and family safely to the campsite, allowing them to truly enjoy all the outdoors has to offer.
The roof box allows experienced and novice campers alike to take all the equipment they need in a safe, secure, and efficient storage box that boasts a sleek, aerodynamic design and is compatible with nearly all car models.
For those who love to go off-road, reliable materials and products are a necessity. As such, the company’s roof racks and accessories are timetested and built not just to last, but to thrive.
From curving mountain roads to long stretches of isolated highways, Yakima products endure when the going gets tough.
Greenline Outdoor is a professional company specializing in designing and manufacturing outdoor products, such as rooftop tents, folding gazebos, camping products, etc.
Our company possesses an incredible team of professional designers, structure engineers, and samplers who have proudly been involved in this line of work for more than 20 years.
We are the first manufacturer in China to produce rooftop tent products since 2004 and have the most complete serials of soft top and rooftop tents, alongside newly developed models. Our vast experience allows us a strong ability to innovate all kinds of new outdoor products. Many professional clients for roof tents are OEMs due to our reliable quality and services.
Tel: +86 15558191380 | Whatsapp: +86 13606618436 | greenline@greenlineoutdoor.com | greenlineoutdoor.com
brought the Dorsey Trailer dream to life. enables it to go from strength to strength the demands of the road every time
Manager: Michael Sommerfield
Since its founding in 1911, Dorsey Trailer (Dorsey) has established itself as one of the premier trailer manufacturers in the US.
Over 110 years ago, a pioneering company set out on a mission to create the most resilient custom trailers. This unwavering commitment continues today, with highly skilled artisans in Elba, Alabama, devoting themselves to manufacturing an extensive range of trailers built to withstand the exacting standards of the open road.
With a long-standing reputation for innovation, high performance, great value, top-notch quality, and exceptional durability, the Dorsey brand continuously evolves to cater to its customers’ diverse needs.
Leveraging extensive experience, cutting-edge computer-aided design (CAD), knowledgeable employees, and a state-of-the-art facility, the company prides itself on producing trailers that are not only safe but also highly reliable.
Its reputable and enduring features anchor Dorsey’s long-standing presence in the local community and have contributed to its status as an esteemed company that has played a vital role in the area for many decades.
Elba, a city in a picturesque landscape, boasts a rich and diverse history intricately entwined with the Dorsey narrative.
The company’s presence has its roots deeply embedded in Elba and spans back to the 20th century, shaping and sustaining the city’s economy.
Furthermore, Elba was established by residents who have called it home for generations, while many businesses in the area play a crucial role in fostering vibrant and sustainable communities.
What started out as a small machinery repair shop quickly flourished, gaining a reputation for reliable and efficient service in the booming timber industry.
With the rise of automobiles and the decline of horse-drawn buggies, the shop seamlessly transitioned to become the city’s go-to destination for car maintenance.
By 1920, Dorsey was producing 20 to 30 logging units a day and soon began designing and building its own products. In the 1930s, the company’s engineers developed its first commercial freight trailers.
Even during the Great Depression from 1929 to 1941, Dorsey’s sales increased every year, and by the end of the decade, the Dorsey name was synonymous with durability and safety from coast to coast.
The Korean War in the 1950s saw the plant relocate and expand to meet military and commercial demands.
In the 1960s, as the Cold War plunged the US into the missile age,
ALUMINIUM – Giant flatbed and drop flat
STEEL – Flatbed, drop flat, beavertail, lift hauler, extendable steel flat, and extendable steel drop
COMBO – Giant flatbed series, ultra-light series, giant drop deck series, giant beavertail series, giant lift hauler series, and extendable combo flat
CHIP VANS – Open top, closed top, and walking floor
LOWBOYS – LB55-detach, LB35detach, LB35-33CS fixed neck, and LB35-38CS fixed neck
stopped producing reefer trailers and vans and focused on the growing demand in the flatbed market.
By 2022, Propst Companies had gradually taken over Dorsey. The following year, it invested in new equipment, and several office and plant upgrades, including a new webbing plasma machine, and 401(k) plans were added to employee benefits packages.
Dorsey is recognized for its unyielding quality, reliability, and commitment to advanced design and precision engineering.
trailer perfectly matches the buyer.
The company recently unveiled a brand-new 55,000 square foot (sqft) manufacturing facility strategically positioned just a mile from its corporate headquarters.
This has propelled Dorsey’s total footprint to over 850,000 sqft, enabling it to meet the surging demand for its trailers. The increased production capacity not only fulfills market needs but also creates 50 new job opportunities.
Dorsey was called upon to design and build rocket transporters and electronic vans and erect equipment to support various missile programs on the ground.
In 1980, Dorsey built a variety of reefer and van trailers, including notable and recognizable products for the country band Alabama, hauler vans for NASCAR, and perhaps most famously, the Dorsey Van in the hit TV show Knight Rider.
However, Dorsey changed direction in 2007 when Jeff Pitts, Owner of Pitts Enterprises, purchased the company.
Over the next few years, Dorsey
Its specialist technicians, who are trained and registered to meet customers’ needs, also offer expert advice and trailer maintenance and repairs. Moreover, a portion of Dorsey’s success can be attributed to its focus on specialty trailers and customization, with optional toolboxes, dunnage racks, ramp kits, and lift axle kits being offered.
Dorsey also provides accessories such as lights, fire extinguishers, fenders, and mud flaps, while decals, paint, and other finishing touches can be implemented towards the end of the production process to ensure each
The primary emphasis is on utilizing the facility to build 53-foot (ft) refrigerated aluminum trailers to transport perishable foods, as well as open-top wood-chip trailers designed for specific transportation needs.
A dedicated dealer network has also contributed to elevating Dorsey to the status it enjoys today.
Dorsey has strong roots in Elba and a solid relationship with its residents. As one of the fastest-growing platform trailer manufacturers in the US and an industry driver for the rest of the state, the city appreciates its accomplishments and the value it adds to the community.
Together with the Elba Public Library, Dorsey has teamed up to support the Dolly Parton Imagination Library of Coffee County, which provides free books to children in the area.
In May, Dorsey discovered that the way to the heart is through the stomach, with pizza delivered by one of the company’s employees to Elba Elementary School and Elba High School as a thank you during Teacher Appreciation Week.
As a company that stocks a wide selection of essential semi-trailer repair parts, joining the Dorsey Parts Club is a must for customers who want to take advantage of deals for their vehicles. A premium membership guarantees exclusive access to early bird sales, new arrivals, and other special offers.
Joining the community means being part of an insider group that shares extensive industry knowledge about semi-trailers, drawing from over 110 years of experience.
Dorsey Parts Club offers a comprehensive list of vendors, providing nearly every part for all different types of semi-trailers, making networking easy. Members also get priority access to great deals.
Meanwhile, special events offer significant savings, and the list ensures members have early
“PEOPLE MAKE A DIFFERENCE AT DORSEY, PUTTING QUALITY FIRST IN EVERY STEP OF THE MANUFACTURING PROCESS”
– DORSEY TRAILER
Contributing to the Elba economy by employing team members in and around the area, Dorsey incentivizes its staff to achieve production goals.
Reaching these objectives is reflected in employee benefits and each paycheck.
Dorsey exceeded its targets in 2022 as a result by producing 3,025 trailers, 14 percent more than the predicted 2,650.
Last year, Dorsey hosted an
and production achievements but also highlighted the collaborative efforts that solidified the company’s position as an industry leader.
From raising funds for Dorsey employees and their families battling cancer and saluting veterans to celebrating work anniversaries and handing out candy at the annual ‘Pumpkins on the Square’ in downtown Elba, the company engages with its crew and citizens
A Design Authority dedicated to delivering world-class engineering and design services to the Royal Australian Navy, Israel Lozano, Executive Managing Director, outlines Navantia Australia’s commitment to excellence and journey to deliver a sovereign design capability for Australia
Writer: Lily Sawyer | Project Manager: Thomas Arnold
The Australian defence industry is an exciting space to be involved in.”
As someone with considerable exposure to global defence markets, Israel Lozano, Executive Managing Director of Navantia Australia, can say this with some authority.
“The industry can present some challenges, but these are part of life and should be embraced. Challenges are what encourage people and businesses to continue to evolve and innovate,” he adds.
As an industry that offers longterm career opportunities as well as
avenues for highly skilled professions, defence is also a sector that promotes innovation and leading-edge technologies. With many defence projects being long-term, this provides assurances for the industry to invest in developing its people and capabilities.
Navantia Australia is an Australianled and operated company that delivers world-class engineering and design services to the Royal Australian Navy (RAN).
Established in 2012, the company’s team of 300 local experts based in Sydney, Melbourne, Canberra, and
Perth is dedicated to ensuring the technical integrity of RAN’s surface fleet.
“We are responsible for over 60 percent of RAN’s surface fleet. Our parent company, Navantia, has transferred the Design Authority delegations for all four classes of vessels delivered to RAN to us,” Lozano informs.
Today, Navantia Australia ensures the design integrity of each of these naval ships throughout their life, guaranteeing safety and performance during operation and sustainment.
The company’s Australian
workforce is responsible for all engineering and platform design changes, whilst its engineers are supported by equally committed and hardworking corporate teams.
In November 2023, Navantia Australia launched its Technical Partner Network (TPN) to provide RAN with the engineering services capabilities and capacity that it requires now and in the future.
“TPN began with a cohort of 14 companies, which has now expanded to 24 Australian businesses. Together, we have 800 engineers at our disposal to support naval ships,” he outlines.
While the company continues to grow in the field of engineering for the support of RAN ships designed by Navantia, it has begun to develop ships of its own for the Australian Defence Force (ADF) and expanded its portfolio of digital services.
With the different types of naval ships currently in service with RAN totalling 110,000 tonnes, having the know-how on such a large capability differentiates Navantia Australia.
Possessing this expertise is a discriminator, not only for providing design support services, but for designing new ships best suited for Australian operations.
“As the Design Authority performing the work locally, we understand the design basis of all these platforms; our work evolves from that understanding,” Lozano reflects.
Understanding its products to such an extent also allows Navantia Australia to contribute to other activities in the value chain, such as new ship designs and the supply chain.
Navantia Australia also provides RAN the opportunity to evolve ship design, in-country using the design baseline in direct collaboration with the designer, which is a first for the industry in Australia.
“Since our establishment in 2012, we have grown and matured to become a strategic defence company and Design Authority for Australia in our own right,” he asserts.
This status was acknowledged in 2020, when the Australian Department of Defence signed a Strategic Agreement recognising Navantia Australia as a Design Authority for RAN, and now with the Designer Support Contractor contract, it plays a critical role under Plan Galileo, an Australian government-run naval shipbuilding programme that prioritises consideration of a vessel’s sustainment needs at the design stage.
“We are agile and have proven our ability to engage with defence, with industry, with academia, and with large and small organisations.
“I sincerely believe that Navantia Australia is a perfect example of how industry contributes to Australia’s goal of building a sovereign naval shipbuilding capability,” Lozano prides.
Like the Australian population, which contains more than 300 different ancestries, Navantia Australia’s workforce also demonstrates a rich cultural diversity. Together with Aboriginal and Torres Strait Islander peoples, its local employees represent 40 different ethnicities.
“We have grown organically by over 30 percent year on year since 2019. The average age of our workforce, 39 years, is reflective of our efforts in growing our capability through investment in graduates and early career workers,” Lozano highlights.
The company has strong relationships with Australian universities such as the Australian Maritime College, the Royal Melbourne Institute of Technology (RMIT), the University of New South Wales (UNSW), and the University of Technology Sydney (UTS).
It also offers internships and graduate positions, primarily in engineering disciplines. Indeed, since 2019, Navantia Australia has employed 58 graduates and 33 interns.
Navantia Australia’s supply chain is localised and managed from Australia. Inheriting ship design knowledge from its parent company, Navantia, it also gained easy access to the original equipment manufacturers (OEMs) whose equipment and systems are incorporated in the platforms.
The company seeks to maximise opportunities for Australian industry to participate in the sustainment of Navantia-designed RAN assets, increasing sovereign capability in the country. It has established relationships with over 840 Australian suppliers and identified a comprehensive list of components and systems to localise.
Working collaboratively with local industry to identify solutions to further Australianise the supply chain for Navantia-designed ships, the company recognises that obsolescence and national support are key drivers to developing Australian Industry Capability (AIC) for the design services contract. This, in turn, creates sustainable and reliable support for the platforms and for developing industry in the longer term.
The company’s teams have supported the development of relationships between international and Australian suppliers to enable local manufacturing and support service delivery partnerships.
Navantia Australia is aiding the nation’s industry participation via a dedicated TPN. Engagement of its TPN enables greater opportunities for Australian industry participants to be involved in the delivery of services.
Can you briefly introduce us to Griffin Marine Services?
Griffin Marine Services (GMS) is a proudly Australian owned and operated company, employing 120 permanent staff around the nation.
GMS is a national leader in ship building, repair, maintenance, and management and offers a comprehensive suite of services including:
• Ship construction and repair (steel, aluminium, and composite).
• Marine engineering and associated trades.
o Above and below water line preservation.
o Insulation fabrication and installation.
o Mechanical fitting.
• Maintenance delivery and project management.
• 24/7 emergency response. GMS operates across Australia with workshops and teams strategically located in each regional maintenance centre, including Perth, Sydney, Darwin, and Cairns.
GMS has also supported repairs in the Pacific region in support of cruise liners and patrol boats. This international presence allows GMS to service clients effectively, efficiently, and provides an unrivalled response capability.
GMS’ diverse range of clientele includes:
• Defence prime contractors (Navantia, Thales, Babcock, Austal, BAE Systems).
• Commercial shipping companies (Bhagwan Marine, Teekay Shipping, RCL, P&O, and Mediterranean Shipping Co.).
• Major marine operators (Sea Swift, Serco, Transdev).
• Private vessel owners.
What are some of the ongoing or recent projects that you are most interested in showcasing?
GMS recently completed multiple major projects in support of its auxiliary oiler replenishment (AOR) fleet in New South Wales (NSW) and Western Australia (WA), demonstrating the breadth of
skills the company offers to its clients and the national reach utilised to manage repairs around the nation.
GMS Sydney has provided four mechanical fitters to assist Navantia Spain rebuild the port main engine on the ship HMAS Supply. The scope was to disassemble the main engine, check all components and tolerances, and rebuild with new or overhauled parts; GMS also took carriage of all heavy rigging.
This task was completed on time, to GMS’ usual meticulous standards, and allowed work that would typically require specialist foreign labour to be completed locally, thereby delivering exceptional value for money and a vessel back to operational readiness in a much shorter period.
At Fleet Base West, GMS’ commitment to excellence shone during HMAS Stalwart’s maintenance period. The GMS team earned high praise for completing a package of both scheduled work and rectification of a lateemerging water-mist system malfunction that threatened the ship’s departure.
Highly qualified welders were mobilised from all four states and the team was
What, for you, differentiates your business from
Nationwide and international reach is what separates GMS from the competition. Unlike regional operators, GMS has strategically located workshops and teams in Perth, Sydney, Darwin, and Cairns to provide unmatched accessibility across Australia and in the Pacific. This international footprint ensures a rapid response, minimising downtime for clients.
GMS goes beyond just geographic reach, as it was founded on exceptional customer service and prioritising the building of strong relationships, meaning all clients experience proactive communication, timely project completion, and a relentless pursuit of exceeding expectations. So, whether you’re a government contractor, commercial shipping company, or private vessel owner, GMS offers the combined advantage of national expertise delivered with a local touch.
assembled with incredible speed, and then fabricated and installed a new 120-metre DIN150 316 stainless steel water-mist line spanning multiple compartments and levels. Thanks to the team’s dedication and expertise, HMAS Stalwart sailed on schedule, fully operational, earning the GMS team a commendation from Navantia, and a letter of appreciation from the Commanding Officer.
‘‘Thanks to the team’s dedication and expertise, HMAS Stalwart sailed on schedule, fully operational, earning the GMS team a commendation from Navantia, and a letter of appreciation from the Commanding Officer.’’
Tell us about some of the major challenges faced within the industry and the business itself and then detail how these have been overcome?
A skilled workforce is the lifeblood of the maritime industry, and GMS recognises the challenges of attracting and retaining top talent, particularly when we are directly competing with the resources sector for that same talent. However, GMS have not shied away from these challenges; rather, the company has proactively implemented solutions to build a strong and sustainable workforce.
One key strategy is our commitment to growing our own talent. GMS offer comprehensive apprenticeship programmes across various disciplines, providing a clear career path for individuals passionate about the
maritime industry. GMS is also a proud participant in the Defence Industry Pathways Programme, and the Defence Industry Internship and Graduate scheme.
Continuous learning is another pillar of the GMS approach. GMS invests in extensive technical and non-technical training programmes for all employees, regardless of experience level. This not only enhances the skillset of the GMS staff, it also demonstrates a level of commitment to professional development, fostering a sense of loyalty and career progression.
Finally, GMS understands the importance of workplace mobility. Offering opportunities to work across our national network of workshops provides employees with the chance to broaden their skillsets, gain new experiences, and advance their careers within GMS.
Could you tell us more about any technological initiatives that you have in place or are exploring?
GMS is actively developing several innovative technologies for defence applications. One key area is utilising laser ablation machines for surface preparation on hulls and tanks before painting. This method offers a safer alternative to traditional methods, while achieving a higher quality finish. Laser ablation reduces surface contaminants, leading to significantly longer-lasting paint adhesion, minimising the frequency and duration of dockyard visits.
Furthermore, GMS is implementing a fully digital welding quality management
system. This system integrates real-time data collection from welding machines, enabling the rapid and accurate provision of object quality evidence to all clients. This digital format offers superior searchability, traceability, and trust for the ADF. Furthermore, GMS is committed to accelerating innovation and delivering solutions that enhance the capabilities and effectiveness of the Australian Navy.
What are you most proud of in relation to the company overall?
At GMS, a source of immense pride is the dual commitment of being a wholly Australianowned and operated company
What are your major future ambitions going forward and how will these goals be achieved?
The GMS ambition is clear: become the preeminent ship repair service provider across all our locations in Australia. GMS remains dedicated to being the trusted partner of choice for each of the Regional Maintenance Centres (RMCs).
GMS also recognises that achieving these goals requires a multi-pronged approach:
• Investing in People: GMS continues to prioritise its workforce by fostering a culture of training, development, and career advancement. This ensures a highly skilled and qualified team to deliver exceptional service.
• Continuous Improvement: GMS is relentlessly committed to optimising processes and embracing innovation. This means constantly challenging the status quo and finding better ways to operate while ensuring efficiency, safety, and quality remain at the forefront.
• Exceeding client expectations: Building strong client relationships is paramount. GMS achieves this by exceeding expectations consistently, through transparent communication, high-quality work, and a commitment to on-time project completion.
and to delivering the highest quality workmanship.
Being Australian-owned fosters a deep sense of responsibility. GMS understands the critical role a strong maritime industry plays in Australia’s security and economic prosperity. This fuels the dedication GMS holds to exceeding expectations and ensuring every vessel repaired is in top condition.
The Australian roots and dedication of GMS go hand-inhand. It’s a combination we’re incredibly proud of and allows us to contribute meaningfully to Australia’s maritime future.
What do the next 12 months look like for the business?
The next year at GMS is
brimming with excitement, as we are gearing up to support the increasingly complex fleet sustainment needs of the Royal Australian Navy (RAN) under Plan Galileo’s regional maintenance construct. This new model presents a unique opportunity, and GMS is perfectly positioned to excel. GMS’ extensive experience working on every class of vessel in the RAN and
Australian Border Force (ABF) surface fleets speaks volumes. Furthermore, the established workshops and seasoned personnel strategically located within each Regional Maintenance Centre (RMC) locations – Henderson, Sydney, Cairns, and Darwin – solidify the company’s commitment to seamless integration with CASG, the RAN, and all RMC providers during this transition.
In the coming year, GMS will focus on:
• Leveraging our national network: Optimising resource allocation and expertise across RMC locations to ensure efficient and timely service for all vessels.
• Building strong partnerships: Collaborating closely with CASG, the RAN, and other RMC providers to ensure a smooth transition and effective regional maintenance delivery.
• Investing in technology: Continuously improving processes and tools to enhance efficiency, data collection, and communication throughout the maintenance cycle.
Graduates are given ownership of end-to-end project work with Navantia Australia as part of a structured, supervised process which delivers on-the-job training until they are sufficiently experienced to deliver inputs on their own.
The company also offers employees the option to participate in formal mentoring programmes, run both internally and externally, to assist graduates in acquiring the requisite skills to succeed in their careers.
Attracting more women to the Australian defence industry is also something Navantia Australia is deeply passionate about.
“We have a strong belief that there is a large percentage of talent not currently working in defence, and that will enhance our industry,” Lozano comments.
Since 2023, Navantia Australia has been an active supporter of the Sir Lawrence Wackett Defence and
“I SINCERELY BELIEVE THAT NAVANTIA AUSTRALIA IS A PERFECT EXAMPLE OF HOW INDUSTRY CONTRIBUTES TO AUSTRALIA’S GOAL OF BUILDING A SOVEREIGN NAVAL SHIPBUILDING CAPABILITY”
– ISRAEL LOZANO, EXECUTIVE MANAGING DIRECTOR, NAVANTIA AUSTRALIA
Aerospace Centre: Young Women in Defence STEM programme.
Run in conjunction with RMIT, the 2024 programme will see 50 female students at secondary schools across Victoria introduced to career opportunities within defence, aerospace, and industry.
“We have also introduced For the WIN (Women in Navantia), an internal, female-led networking community which aims to provide a supportive environment that enhances the role and contributions of women within the business,” he outlines.
In addition, Navantia Australia is committed to supporting veterans and their families through employment opportunities and supports veteran-focused charities and programmes.
“We are a recognised ‘Veteran Employer of Choice’ by the Australian Department of Veteran Affairs’ Veteran Employment Programme. We offer veterans tailored onboarding processes, mentoring, and have a specific veterans’ employee policy and strategy,” Lozano confirms.
HVAC IS CRITICAL TO ACHIEVING THE ROYAL AUSTRALIAN NAVY’S INTENT OF MAINTAINING SUSTAINED COMBAT OPERATIONS AS PART OF A JOINT FORCE. *
IN AUSTRALIA’S TROPICAL ENVIRONEMENT, A LOSS OF COOLING RESULTS IN A LOSS OF CAPABILITY AND POTENTIALLY AN INABILITY TO REMAIN ON DEPLOYMENT.
NAVANTIA, MARENAV AND CHILLFLOW ARE WORKING TOGETHER TO DELIVER AUSTALIAN MADE, AUSTRALIAN DESIGNED, WHOLE OF SHIP SOVEREIGN HVAC SYSTEMS THAT CAN KEEP OUR FLEET AT SEA.
*Plan Pelorus – Royal Australian Navy
Navantia Australia is currently investing in R&D projects to advance smarter solutions for ship sustainment and design.
“We are walking the path to progressively incorporate the digital tide in our processes and innovative solutions,” Lozano enthuses.
This will allow the company to deliver various services to avoid time and cost-consuming transactions and mistakes in the design or service delivery processes.
The same applies when it comes to the development of digital services. The company’s know-how, together with data gathered from the Integrated Platform Management System, provides the basis for developing innovative digital technologies.
With the support of academia and a focus on technology-led outcomes, Navantia Australia is establishing a project pipeline that will deliver advancements in operational, sustainment, and workforce development activities.
As an RAN-focused company, Navantia Australia is responsible for the evolution of the designs of more than 60 percent of the navy’s current fleet.
This means that it is committed and dedicated to ensuring that RAN has its most lethal and capable ships ready to conduct sustained combat operations as part of the Joint Force.
As Navantia Australia’s only customer, maintaining a positive, collaborative, and productive relationship with RAN is paramount. On a daily basis, it works closely with the System Programme Offices, the Capability Development Group, ship crews, and members of the Naval Shipbuilding and Sustainment Group.
With the delivery of more classes of ships to RAN, the company has grown its workforce accordingly in the locations and capability areas that RAN requires.
Navantia Australia’s growing digital capabilities blend its design and engineering know-how to enhance the services the company provides to its customers.
“Because of our unique position of being both the designer, OEM, and digital developer, we know what we
are talking about – our technology is supported by deep knowledge,” he expresses.
In 2022, Navantia Australia announced the establishment of the Maritime Institute of Technologies (Marintec™), formed with UTS. Through Marintec™, the company
Chillflow Solutions (Chillflow) delivers comprehensive Marine HVAC and Refrigeration specialist engineering solutions for the defence, commercial, industrial and offshore sectors.
From design, manufacture, supply, installation to service, maintenance and ongoing life-cycle support, we offer tailored demand-led, integrated services to meet your requirements.
We provide deep expertise, quality assurance, and certification to help solve your Marine HVAC and Refrigeration challenges.
Our mission at Chillflow is to bring innovation to the marine HVAC industry through collaboration with our clients and partners to deliver comprehensive, specialist HVAC and refrigeration engineering solutions.
We are experts at navigating complex defence platforms, providing technical assurance for our capability outcomes.
Chillflow are the sole appointed Australian distributer for J&E Hall Ltd (member of the Daikin Group) marine and industrial products
• Design and manufacture
• Project management
• Procurement
• Service and maintenance
• Replacement and upgrades
• Commissioning
• Ventilation
• Control and data acquisition systems
• Refrigeration
• Sea water systems
• Heating and cooling solutions
• Sea trials
• Deployed operations
• Sustainment
• Temporary cooling solution
• Fault finding and diagnostics
• ACSSPO & AORSPO
• Babcock
• Atlantic and Peninsula Australia
• Navantia
• Teekay
• J&E Hall Ltd
• ADROITA
• Sydney City Marine
• Halliday Engineering
• Daikin Australia
• Marenav
• John Crane
• Danfoss
• Aircon rentals
• HydroChem
• Mak Water
• Environmental Management system ISO 14001:2015 Quality
• Management systems ISO 9001:2015
• Health and Safety Management System ISO 45001:2018 DISP Member
• ARCTICK - Australian Refrigeration Council - AU54434 NSW
• Contactors Licence - 389231C
• Electrical Licence - EW182875
Thermal management is critical for warships today and in the future. A loss of cooling can readily cascade into a loss of combat capability.
Marenav, an Australian HVAC OEM, System Designer and Integrator is delivering intelligent, high availability, Australian-made HVAC systems and equipment to keep your fleet at sea.
has been funding several areas of collaborative R&D, focusing on advanced software engineering, user experience (UX) digital expertise, game design, and artificial intelligence (AI).
With its sights set on becoming Australia’s centre of excellence for maritime digital technology solutions, Marintec™ is charting a course for a brighter, more innovative future.
However, Marintec™ is not just about technology – it’s also committed to developing the workforce of the future. With PhD programmes, internships, and employment opportunities for graduates, the partnership is cultivating a skilled future workforce while addressing the Australian maritime skills gap shortage.
“In November 2023, we entered additional partnerships with Australian universities including
HVAC-CBRN-RADAR COOLING
“WE ARE WALKING THE PATH TO PROGRESSIVELY INCORPORATE THE DIGITAL TIDE IN OUR PROCESSES AND INNOVATIVE SOLUTIONS”
– ISRAEL LOZANO, EXECUTIVE MANAGING DIRECTOR, NAVANTIA AUSTRALIA
RMIT and the Australian Maritime College – University of Tasmania (AMC-UTAS),” Lozano informs.
RMIT, AMC-UTAS, and Navantia Australia were together successful in securing federal funding through the Next Generation Graduates Programme (NGGP), offered by the Commonwealth Scientific and Industrial Research Organisation’s (CSIRO) Data61 initiative, to support PhD projects that explore hydrodynamic effects for uncrewed surface vessels (USVs) and the optimisation of hydrogen power
plants for USVs.
In addition to the NGGP, Navantia Australia is working with the universities on other independent projects. The company also recently renewed a strategic partnership agreement with the Defence Science Technology Group.
The implementation of the Commonwealth’s Plan Galileo Maritime Sustainment Model, which highlights sustainment as a key enabling sovereign capability in naval
shipbuilding, heralds an exciting new era for Navantia Australia.
“We are excited about this new model. The Design Support Contract (DSC) is vital to the success of the new model, as our deep product knowledge and baseline management will facilitate design integrity throughout sustainment and continuous improvement activities,” Lozano shares.
This, combined with the company’s capability to collaborate and effectively communicate within the enterprise environment, will contribute to the assurance of RAN’s fleet, the availability of its ships, and reduced costs throughout the life of the vessels.
The long-term DSC enables Navantia Australia to continue to invest in enabling and developing sovereign naval design and engineering capabilities. A critical element in achieving this is through local partnerships.
With operations across the country, Navantia Australia seeks to provide support for defence industry veterans throughout the community. As such, it supports various schemes and organisations, alongside some of its own.
• Navantia Australia is an annual sponsor of the Prime Minister’s National Veterans’ Employment Awards, which recognise remarkable accomplishments within the veteran community.
• The company is a platinum sponsor of Soldier On, a not-for-profit organisation that offers support to current and former ADF personnel and their families.
• Navantia Australia is an active supporter of the Returned and Services League of Australia (RSL) Veterans’ Employment Programme and other initiatives which assist veterans in securing employment.
• The company supports OPK9, the flagship programme of See Differently that provides highly trained assistance dogs to veterans with posttraumatic stress disorder (PTSD).
• It also supports Remount, an equine-based therapy programme for veterans and first responders suffering from PTSD and/or receiving physical therapy.
• Navantia Australia supports Keeping Watch, RAN’s perpetual charitable fund that helps serving members and their families in need of financial aid.
Naval Ship Design and Engineering since 1987
The Design Technology Company (DTCo) is proud to be recognised as a member of Navantia Australia’s Technical Partner Network, highlighting the initiative as a key measure to build sovereign capability. DTCo provides a trusted, collaborative integration service for engineering projects and access to cutting-edge design technologies.
We combine vast industry experience with a skilled team to ensure rapid iteration within projects, fostering early stakeholder engagement, design confidence and optimised workflows. DTCo is committed to an easy to engage, scalable platform to enhance outcomes for Navantia, the Commonwealth, and sovereign manufacturing.
ausmarinetech.com.au | info@ausmarinetech.com.au
“These partnerships include collaboration with other Australian companies to expand, which is why we established our TPN,” he details.
“The DSC is not only an opportunity for Navantia Australia, but for the TPN to also benefit from the certainty of workflow, enabling members to invest in capability development,” outlines Lozano.
The maturing of the company’s local end-to-end design capability is another important area of growth; in addition to the engineers who are working on sustainment programmes, Navantia Australia is investing in developing new ship designs.
The company’s first complete design is a medium landing craft that is optimised for riverine and littoral operations. This design, the Kodal LMV-M, was originated and developed by its Naval Design and Engineering Centre in Melbourne.
“We are receiving a high degree of interest in the platform, and it
has been accepted into Navantia’s global portfolio, which is a major achievement,” Lozano prides.
Another significant project underway presently is the capability upgrades to RAN’s Hobart Class Guided Missile Destroyers.
“Supporting these upgrades has created 60 full-time design and engineering jobs with Navantia Australia in the fields of combat systems interface into the platform, naval architecture, outfitting, electrical, mechanical, structural, design drafting, and systems engineering,” he shares.
Going forward, Navantia Australia hopes to continue to deliver what RAN needs now and in the future.
The company aims to keep growing its Australian capabilities in support of the government’s objectives for achieving a sovereign continuous naval shipbuilding and sustainment industry, whilst ensuring that delivery is done in accordance with its
strong corporate values and ethical behaviours.
“We are continuing our journey to deliver design sovereignty to Australia to enable the design of future complex warships to be developed locally. It’s a path we must walk together with RAN and defence,” Lozano concludes.
Driven by its mission to change society through the power of chemistry, Resonac Graphite Business Unit (RGBU) is part of Resonac Holdings Corporation (Resonac), headquartered in Tokyo, Japan.
The corporation came about as a result of the acquisition of Hitachi
Chemicals by Showa Denko K.K., and officially gained its Resonac moniker in January 2023. The name is a combination of ‘resonate’ and the ‘c’ from ‘chemistry’, in acknowledgement of the corporation’s history as a chemicals company.
Boasting over 1,600 employees and a global footprint, with manufacturing
facilities across Asia Pacific, Europe, and the US, RGBU strives to maintain integrity and a solid vision across its numerous iterations.
RGBU is acutely aware of the valuable properties that graphite offers. Indeed, with its growing use in electric vehicle (EV) batteries, the mineral is playing a significant role
As a company acutely aware of global decarbonisation efforts, Resonac Graphite Business Unit leverages sustainable production processes and a robust continuity framework to present a comprehensive product and service offering to the steelmaking industry. César Castiñeira Diaz, President and CEO, tells us more
Writer: Lily Sawyer | Project Manager: Nicholas Kernan
in changing not just the chemicals industry, but society as a whole.
As such, graphite today is in high demand, and so are the companies who produce it.
“Our graphite electrodes are helping us to change society through chemistry in a meaningful way,” introduces César Castiñeira
Diaz, President and CEO of RGBU.
Historically, the steel industry, RGBU’s primary customer, has been responsible for approximately seven percent of global greenhouse gas (GHG) emissions, and 11 percent of global CO2 emissions.
However, RGBU’s sustainable steel production process, which involves
remelting scrap steel in an electric arc furnace (EAF), saves up to 80 percent of CO2 emissions compared to traditional blast furnace methods.
“As steelmakers around the world seek to reduce their carbon footprint, they are opting to replace their blast furnaces with EAFs,” he reveals.
In this way, RGBU considers its products and services to be essential contributors to the global decarbonisation effort.
Undeterred by a saturated and constantly evolving landscape, RGBU has seen its competitors in the graphite electrode industry remain fiercely active.
“This continued competition creates an environment in which we are forced to focus on constant improvement,” comments Diaz.
As a result, the company has fostered a sense of urgency towards innovation in this traditionally conservative industry. For example, RGBU’s contributions to the electric steelmaking sector are now more efficient, customer focused, and environmentally friendly to remain competitive.
To achieve this, the company has leveraged strategic partnerships up and down the value chain to co-create solutions and incubate innovation.
Notably, RGBU believes that innovation is not measured by R&D budget alone, but includes conscious decision-making to cultivate a culture in which people can grow.
As such, the company seeks to create an atmosphere conducive to creative innovation and a working environment in which its people are not afraid to challenge the status quo.
“It is the people and their mindsets that produce ideas, so the environment is important. In turn, these ideas create the type of radical innovations that will make lasting changes,” Diaz asserts.
RGBU’s Employer of Choice (EoC) programme seeks to further its ability to radically innovate by making the
company a benchmark within local labour markets, enabling it to attract and retain the best talent whilst fostering a culture of excellence, diversity, inclusion, and commitment.
The company’s overall goal for the EoC programme is to offer its employees a unique and differentiated experience where they can be part of something bigger than themselves.
“In the long run, you find that the people who feel empowered to change the world are the ones who actually do,” he states.
Despite its significant size, RGBU believes that a company can never be bigger than the value it provides its customers and stakeholders.
Therefore, it aims to be resilient and sustainable in the sense of remaining
present for its customers in the long run.
“We believe we owe it to our employees, customers, suppliers, and stakeholders to be a business that can be trusted,” Diaz imparts.
As such, RGBU retains strong corporate governance and visionary leaders who safeguard key aspects of the company’s ongoing sustainability.
Resonac’s large global platform also provides a considerable advantage to RGBU as customers begin to evaluate the impact of Scope 1, 2, and 3 emissions on their operations.
“In this case, our sizable platform is aiding our sustainability efforts, both economically and environmentally,” he explains.
In addition, RGBU implements a business continuity framework in which it keeps significant inventories of key components and raw materials, ensuring it can always fulfil partner commitments and further cementing its ongoing sustainability and resilience as a business.
In recent years, global disruptions such as war, natural disasters, and political conflict have presented potential obstacles to fulfilling business commitments, yet the company’s continuity framework prevents this eventuality.
“We live in a volatile, uncertain, complex, and ambiguous (VUCA) world, but RGBU is well-positioned to uphold its commitments regardless of these circumstances.”
Accordingly, based on its strategy to eliminate the probability of business interruption, RGBU’s production facilities have achieved the sought-after status of ‘highly protected risk’ from its regional insurance partners.
RGBU believes it is people that make the difference. If a company can be an employer of choice, then it can attract and retain the right people and increase its likelihood of being successful.
César Castiñeira Diaz, President and CEO: “I was raised in Ferrol on the north-western coast of Spain, where I earned a degree in electrical engineering from the University of A Coruña.
“Around the time of my graduation, a local employer, SGL Carbon (SGL), asked the university for a list of young engineers to interview for a vacant position in supply chain management. I applied for the role and earned the job, officially starting my career with SGL in November 2000 as Packaging Department Supervisor.
“Since then, I have worked in the graphite electrode and cathode businesses, and been fortunate enough to experience several different facets of the industry.
“I served an expatriate assignment in Germany for three years, whilst many of my roles have provided opportunities to work in a global capacity, including my stint as COO of Showa Denko Carbon, a subsidiary of Showa Denko K.K.
“Effective from 1st April 2024, I am excited and honoured to accept the position as President and CEO of RGBU.”
“OUR GRAPHITE ELECTRODES ARE HELPING US TO CHANGE SOCIETY THROUGH CHEMISTRY IN A MEANINGFUL WAY”
– CÉSAR CASTIÑEIRA DIAZ, PRESIDENT AND CEO, RESONAC GRAPHITE BUSINESS UNIT
To change the game, we need
In today’s world marked by unpredictability and continuous change, organizations face constant challenges. Global disruptions – such as wars, natural disasters, political instability and, more recently, deliberate attacks on vital infrastructure – coupled with fierce global competition, have taken the veil off the volatile, uncertain, complex, and ambiguous (VUCA) environment that businesses have to navigate. This scenario, in which customers also switch loyalty easily in pursuit of the best value per dollar, puts immense pressure on companies with capital-intensive inventories and a dependence on global supply chains. These conditions require a strategic pivot towards resilience and adaptability, particularly for industries that rely on precise logistics, such as graphite electrodes and steel production. Facing these challenges head-on, and navigating the turbulent waters that come with them, highlights the need for robust contingency planning and flexible operating models to ensure stable and reliable supply chains. This is even more true for the so-called ‘traditional companies’. Entities that have long been established within their markets, have profound industry knowledge, and have implemented solid structures and processes. In the new global environment, it is these companies to whom resilience is not just beneficial but essential for healthy growth and future success. At the same time, it is these companies that are struggling the most in delivering a successful transformation.
Their once-effective organizational structures, decision-making hierarchies, and legacy systems now hinder agility, resilience, and overall organizational excellence in today’s VUCA world. A transformation geared towards success is an in-depth, systemic re-orientation of the entire enterprise. It challenges and changes the foundational, often unspoken rules, beliefs, and paradigms that heavily influence perceptions, behaviors, decision-making, and interactions. In this effort, mere incremental efforts and increased hard work cannot address the need for change sufficiently.
After all, a transformation aims to fundamentally change the way a company does business.
Think Fosbury Flop in high jump: Before the 1968 Olympics, high jumpers typically used and improved upon techniques that all shared going over the bar face-down.
Dick Fosbury, however, ran towards the bar in a curve, then leaped backward and head-first, allowing for a significantly higher jump and an unrivaled competitive advantage over conventional methods. By overcoming the belief that you need to run straight and jump forward, he changed the entire game. As a paradigm, this belief was almost considered a rule in high jumping, determining the sport like the hidden part of an iceberg determines the visible one.
When talking about transformation, it is this level of paradigm shift that should be the North Star.
In general, the success rate of transformation initiatives is very low and most efforts fizzle out during implementation. The authors, with their broad experience and expertise across multiple industries, have seen many initiatives come and go again very quickly. So-called ‘traditional companies’ are especially prone to failure in their transformation attempts. These organizations face unique challenges and hurdles when attempting to navigate the complexities of a transformation. Symptoms of these difficulties include, but are not limited to, the following:
• Resistance to Change: The success of transformations is hindered by employees’ and management’s reluctance to adopt new practices, leading to skepticism and disengagement.
• Traditionalist Culture: Deeply ingrained cultures that value stability and predictability in traditional companies can conflict with the adaptability needed for successful transformation.
• Legacy Systems and Locally Optimized Processes: Traditional companies’ reliance on outdated systems optimized for siloed functions complicates updating efforts. These require a holistic reenvisioning of processes and structures fitting end-to-end perspectives.
• Lack of Agility: Traditional companies struggle with responsiveness due to hierarchical decision-making and bureaucratic processes in a rapidly changing business environment.
• Insufficient Skills and Capabilities: Traditional companies often lack the skills necessary for transformation, including digital literacy, innovation, agility, and project management.
• Poor Alignment and Communication: Often, these companies face a disconnect between strategic objectives and their execution, along with issues in cross-hierarchical communication.
• Underestimating Transformation Complexity: Underestimating the complexities and interdependencies in transformations leads to inadequate planning and resource allocation. These symptoms make the transformation complicated and multifaceted. It is undoubtedly challenging, presents numerous challenges on several levels simultaneously, and requires a significant effort from every single part and member of the organization.
It is in view of these basic challenges that most transformations start to fail: C-level executives have announced their vision and provided resources, focusing on surface-level items like changing technologies, behaviors, processes, and structures. They then delegate the execution of change but do not address the unspoken and often invisible rulesthe beliefs - of the organization. In highjump terms: Executives continue running toward the bar in a straight line, jumping forward, but expect the company to do a Fosbury Flop. No wonder it fails.
It is clear: If you want to change the game successfully, you need to fundamentally change the rules. The ‘iceberg model’ connects the surface level of observable behaviors, practices, processes, and structures with the underlying rules in the form of beliefs, values, and mindsets that are hidden from plain sight. They, however, determine every other of the visible aspects of an organization. This means leaders need to change first. Before anything else, it is their responsibility to enable themselves to create the new culture and embody it. They have to understand what beliefs and values need to be changed and define what the new paradigms are. These, along with a new vision, then need to be embedded in a compelling story so that management and the rest of the organization are deeply willing to adopt the new mindset needed for transformation and future success. Designing a vivid picture of potential futures and pointing out individual benefits excites people and helps turn concerns and apprehensions into ambitions, motivating employees to embark on the transformative path.
The transformation, however, requires more than just desire. It can only be successful if desire, capability, and permission, the three dimensions of the ‘triangle of transformation’, are synchronized and in balance. Capability means that people not only want to but also possess the individual skills to operate in the transformed organization. Methodologies, knowhow, and practical capabilities to drive and sustain the change need to be built within the company across all levels, from the leadership team to the frontliners. Specific trainings that follow accepted standards and are tailored to the needs of a transformed organization need to be conducted. A potential that is created this way then needs permission to act to be unlocked. Therefore, decisions need to be enabled and taken at the right level. A fitting operating model and the right set of KPIs that are aligned throughout the company guide the creation of supportive structures and processes.
During the transformation, ensuring symmetry between desire, capability, and permission as well as exemplifying the new values, beliefs, and mindset is paramount and a continuous effort of leadership. Only then can the enterprise succeed. In other words: Only when C-level leaders run to the bar in a curve, turn and jump, can they expect the company’s body to provide the energy and the complex motion needed to do a Fosbury Flop, get over the bar, and land the right way.
In 2024, UMS Consulting GmbH & Co. KG celebrates 40 years of successfully supporting organizations in setting up and implementing change towards resilience. We have built extensive expertise in understanding and navigating the complexities and challenges of transformations in the segment of heavy and process industries and are happy to share it. Our holistic Transformation to Excellence program bundles this wealth of experience and offers it as a comprehensive service, ensuring your people and organization are energized for the future.
Frank Oliver Rill Senior Partner
Frank.Oliver.Rill@ums-gmbh.com
Renata Meran Senior Manager
Reneta.Meran@ums-gmbh.com
Dr. Sebastian Bondzio Senior Consultant
Sebastian.Bondzio@ums-gmbh.com
UMS GmbH & Co. KG
Hanauer Landstraße 291B D - 60314 Frankfurt am Main Germany contact@ums@ums-gmbh.com T: +49 69 91 30 680
“When it comes to business, wanting to be the employer of choice seems obvious. Implementation can be challenging, but the concept is simple,” Diaz explains.
Being a supplier of choice, however, is more nuanced for RGBU, as it seeks to be customer-centric without commoditising its products and services.
“Unfortunately, due to a proliferation of new market capacity in recent years, complex, value-adding products such as graphite electrodes have been downgraded by way of commoditisation,” he reveals.
On the whole, despite a significant increase in supply from emerging markets threatening to undermine RGBU’s products, its customers remain loyal and continue to value the company’s characteristics of quality, reliability, and stability.
However, there are some cases in which more economical applications are sufficient to meet customer needs.
Guided by its mission to change society through the power of chemistry, Resonac believes being a good corporate citizen goes much further than merely ensuring it pays taxes and doesn’t pollute the environment.
The corporation’s corporate social responsibility (CSR) team, supported by 1,600 community ambassadors from across the globe, partners with local communities to co-create solutions with not only a regional impact, but a global one.
For example, RGBU’s Omachi plant in Japan has established a regional community water utilisation system that has been operational for over 70 years. The system supplies water to the local towns and villages of Ikeda, Matsukawa, and Ikusaka for irrigation, domestic use, and power generation.
In addition, the company’s plant in Steeg, Austria uses recycled plant process water to supply the local district’s heating system, benefiting 400 residents, and supplying over 100 gigawatt hours (GWh) of heat to date.
Currently, the team at RGBU’s Ridgeville facility in the US is partnering with local schools to promote the benefits of environmental stewardship in a national recycling contest.
Such diverse CSR initiatives have helped the corporation to illustrate its mission of actively changing lives through the power of chemistry.
We keep a constant focus on safety, quality and teamwork and proudly boast to have one of the best safety ratings in our industry. We are currently at around 200 employees and with a strong workforce and the ability to do almost any job, we are a one stop shop for anyone in need!
Carolina Contracting Solutions has been doing business with Resonac since 2008. We are a family owned and operated company in Dorchester County South Carolina. In 2023 we branched off our Industrial Division in its own company called Carolina Reeder Industrial. During this time, we also acquired an already established Industrial Company that had been operating in our area since the 90’s. By doing this we created a larger work force with many years of skill and experience that allowed us to better serve our customers and expand our business. Carolina Reeder Industrial focuses on any and all Industrial Plant Maintenance Needs.
We work daily on contract and cost work at many plants located in the Lowcountry. From welding and fitting, to construction and piping, all mechanical work including: concrete construction, cranes, rigging, painting, blasting, specialized Industrial equipment setting, and boiler work, is the reason for our ASME accreditation.
Murray - Owner|Steven Murray Jr. - President
In this instance, and to meet this need, RGBU developed and launched ΩMEGA – an electrode specifically designed to compete with market suppliers whilst being produced in a factory with 100 percent renewable electricity.
“With ΩMEGA, our aim was to
develop a competitively priced product in a traditionally lowpriced market, but do it in an environmentally-friendly manner, and I am happy to say we have done that. To us, this is innovation,” Diaz prides.
In addition to the development of ΩMEGA, the recent acquisition of AMI
Automation (AMI), a Mexico-based technology company, has bolstered RGBU’s status as a supplier of choice and optimised its EAF capabilities.
“Our customers deeply value technology and service, and AMI is a world-leader in EAF optimisation. As such, RGBU’s purchase of AMI is
Operating since 1943, Química del Nalón is a family-owned company and a major manufacturer of foundry coke and coal tar distillates in Europe.
QN supplies to several key industrial sectors, such as graphite, primary aluminium, carbon black, iron, and construction.
Avenida de Galicia, 31. 33005
Oviedo, Spain
+34 985982600
Three strategic levers:
• Digital transformation: Organic growth and diversification
Biotechnology and circular chemistry
gonzaga.gomez-albo@nalonchem.com nalonchem.com
Química del Nalón
• Sustainability: A key player for the decarbonization of the steel industry, supplying Resonac with binders for the production of electrodes
another example of innovation and our focus on customer centricity,” he expands.
In the face of the steel industry’s notoriously cyclical nature, RGBU anticipates a challenging year ahead, especially as it experiences an ongoing downturn.
“Our goal is to navigate challenging times without negatively affecting our quality, efficiency, or service,” Diaz asserts.
To do so, RGBU ensures that its customers’ operations and value chains are not impacted by geopolitical conflict, economic downturn, or natural disasters through its robust business continuity framework.
Furthermore, although it has no plans to expand its manufacturing capacity going forward, the implementation of products such as ΩMEGA has diversified the
company’s portfolio, whilst an uptake in solutions-oriented technical services following the acquisition of AMI has seen the company grow its capabilities.
“With these improvements, RGBU can be considered a one-stop shop for steelmakers. We ensure that each product and service required for melting steel is managed by a company with a robust business continuity framework, accompanied by a long history of reliability and integrity.”
In addition, Resonac’s recent land purchase in A Coruña, Spain acknowledges the future potential for synthetic graphite production.
RGBU views this as a direct investment in the expertise of its graphite team, leveraging over 100 years of manufacturing experience to produce sustainable options to overcome challenges faced by the EV supply chain.
“We see this recent land purchase
as a complement to our existing graphite electrode business,” Diaz enthuses.
As always, RGBU will continue to innovate tirelessly, as it anticipates this investment will further solidify the company as a world-leader in the graphite industry.
info.graphite@resonac.com
www.graphite.resonac.com
With an extensive history in the agricultural sector, Agrostroj Pelhřimov has grown to become an industry leader in machinery manufacturing. We explore how the company provides comprehensive production solutions for global players
Writer: Lucy Pilgrim | Project Manager: Nicholas Kernan
Founded in 1896, Agrostroj Pelhřimov (Agrostroj) has firmly established its roots in agricultural machine manufacturing and production, having grown from a family-driven culture and a passion for the industry in Czechia.
Today, the company has expanded its repertoire to become an engineering manufacturing titan that caters to
the entire design and production process of each project, operating as the largest manufacturer of agricultural machinery in the country.
Agrostroj has achieved its enviable position by offering endto-end machine solutions that are specialised to its clients’ individual requirements. The company’s turnkey services include project feasibility
studies, production preparation and construction, as well as tool manufacturing.
Providing solutions for a vast range of agricultural machinery, including combine harvesters, soil propagation machines, industrial racks, earth moving equipment, and more, Agrostroj has evolved to become a major supplier to some of the largest
organisations in the world.
To maintain its position as a major supplier, Agrostroj strictly follows high-precision procedures and stringently controls each project stage through to final production and after-care service.
PROJECT SATISFACTION – The company endeavours to meet its customers’ requirements as much as possible and create highprecision products according to their needs.
DESIGN AND DEVELOPMENT – A specialised team of experienced and highly trained staff is involved in every stage of the design and development process.
TECHNOLOGY – Agrostroj’s reputation for exceptional workmanship is achieved using cutting-edge manufacturing capabilities and state-of-the-art technology.
SERIES PRODUCTION – Thanks to the company’s unique technologies, it can produce products that are unmatched by competitors.
In fact, providing complete turnkey solutions that meet customer requirements is at the core of the business, as Agrostroj prides itself on ensuring the entire project timeline, from project inception through to planning, design, development, and delivery, is meticulously streamlined and efficient.
Unlike other competitors in the agricultural manufacturing sector, the company also offers rigorous post-production services as part of its portfolio, alleviating any further difficulty for clients as they continue to utilise the machinery. This also ensures that the equipment retains its initial quality, providing long-lasting utility value.
Furthermore, Agrostroj’s technology capabilities are key to its unwavering success. Using advanced, environmentally-friendly equipment, its machines operate with the utmost precision.
Indeed, the company’s inventory of machinery is extensive; across its 23 hectares of production halls, Agrostroj possesses modern robotic painting lines, 3D laser workstations, 250
computer numerical control (CNC) machine tools, 44 fully automated laser lines, more than 100 metres (m) of assembly lines, as well as special aluminium welding technology.
Meanwhile, the company also boasts a modern, universal paint shop that is the largest in Europe. As a recent addition to the business, the facility began operating in 2020 and has an impressive annual capacity of five million square metres.
Akin to the company’s other capabilities, the paint shop has great versatility with the ability to apply all types of paints. The facility is equipped with everything that its clients might require, including a cataphoretic dip coating (CDC) system, a wet paint box, and three powder paint boxes for larger requirements. Additionally, the paint shop also has a state-of-the-art wastewater treatment plant that further increases its capabilities.
With its headquarters situated in Czechia, Agrostroj possesses
• Hydraulic Cylinders
• Hydraulic Hoses
• Manipulated Tubes
• Hydraulic Power Units
• Hydraulic Components – fittings, pressure valves, quick release couplings, etc.
•
•
•
• Serial production
•
• Subsidiaries in Germany, Croatia, and Ukraine
• Network of distributors across Europe
MATERIAL SEPARATION
- Lasers
- Burning machines
- Punching machines
- Saws for cutting material
MACHINING OF PARTS
- Lathes
- Milling machines
- Drilling machines
- Cylindrical grinding machines
- Housing centres
WELDING
- Welding sources and robots
- Hanging point pliers
- Pneumatic scoring machine
PRESSING
- CNC press brakes
- Robotic bending cells
- Mechanical presses
- Hydraulic presses
HEAT TREATMENT OF PARTS
- Annealing of parts without protective atmosphere
- Heat treatment line
- Isothermal refining
- High-frequency quenching of rotating parts
- EFD medium-frequency quenching
SURFACE TREATMENT
- Blasting of parts
- KTL foundation
- Powder coating plant
- Wet painting
manufacturing facilities across the breadth of the country, with one plant in Pelhřimov and two other centres in Humpolec and Počátky.
However, the company’s overarching mindset is integral to the international portfolio that it has amassed over the past century, in which reliability, flexibility, and premium product quality are critical.
Currently, the company supplies parts to 21 agricultural machinery and utility vehicle businesses who rank highly in the European markets for their respective fields.
Regarding the provision of utility vehicles, Agrostroj diligently supplies complex products that can be directly used in the production of trucks, buses, heavy-duty machinery, forklifts, and injection molding machines.
The company holds many major international partnerships with the likes of CLAAS, John Deere, Scania,
Krone Agriculture, Volvo, Fendt, amongst others.
To meet the demands of these globally illustrious organisations whilst supporting its domestic facilities, Agrostroj operates subsidiaries in Poland, Germany, and the US, as well as sales offices in Russia and France.
To further bolster its international footprint, the company acquired German machinery company, STOLL, who owns two factories in Germany, and one a piece in Poland and the US.
The acquisition marks a partnership between Agrostroj and the world’s second-largest manufacturer of agricultural front loaders, with an annual production capacity of 22,000 units.
This has helped Agrostroj greatly expand its production capabilities, employee strength, and worldwide presence.
Agrostroj’s employees are a central focus of the company, cultivating a modern working environment for the team, whilst also maintaining their health and education through a plethora of benefits.
Indeed, the education of its staff is very important to Agrostroj, to the extent that the business provides in-house learning initiatives as well as a welding school, which offers renowned courses in its specially-built training centre.
New employees can learn the ins and outs of welding, machining, and assembly operation, and must take an exam at the end of the programme before entering the main production line. By passing the school, team members also receive a certificate that enables future job security within the EU.
Owing to Agrostroj’s collaboration with vocational schools and training centres, as well as its own training facility, 46 percent of the company’s staff have secondary, higher, or university education.
Meanwhile, the business is also proud of its extended, close co-operation with technical schools in the local areas in which it operates, allowing students and teachers alike from technical schools to partake in practical training with Agrostroj.
In aid of this, the company regularly organises individual and group events, as well as open days, that allow younger generations to experience the realities of the manufacturing industry. The latter also allows parents to understand the environment where their children may work one day, thus solidifying the future of the industry and the company.
On top of this, Agrostroj also offers its staff internal English, German, and Russian language courses to further build their skill sets and provide career advancement opportunities.
Alongside a multitude of career and personal development advantages, the team also receive a plethora of employee benefits such as free transport to work, meal allowances, healthcare amenities, staff housing, and much more.
As leaders in industrial production and agricultural manufacturing for over a century, Agrostroj continues to pave the way for the world’s leading global businesses by providing premium quality products with enduring high value.
Committed to continuous development and innovation, Saab Grintek Defence manufactures and develops integrated electronic warfare self-protection systems widely used across the global defence sector.
Jan Widerström, President and Managing Director, explains how the company plans to remain at the forefront of the domain
Writer: Lily Sawyer | Project Manager: Thomas Arnold
As a dynamic and multifaceted space dedicated to keeping people and society safe, Africa’s defence industry presents both opportunities and challenges.
“The complexities of the geopolitical landscape and the difficulties associated with exporting from the continent can create hurdles. However, it is important to acknowledge that Africa possesses the necessary tools for success,” opens Jan Widerström, President and
Managing Director of Saab Grintek Defence
As a South African defence company that specialises in electronic warfare systems, sensor technology, and avionics across various domains, SGD, a subsidiary of Saab, emerges as an industry leader. SGD’s electronic solutions also encompass self-protection systems for aircraft, helicopters, land vehicles, naval vessels, and submarines.
Widerström was appointed as President and Managing Director of SGD in March 2023.
He previously held the position of Deputy Head of Electronic Warfare and Aircraft Systems (EWAS) for Saab as part of its surveillance business unit. Prior to this, he headed up Saab Avionics Systems, which is focused on developing safe, sustainable, and efficient aviation solutions for civil and military aircraft.
In his stint as Chairman of Saab India Technologies, he oversaw Saab’s operations in the country to deliver success and growth within the Indian market.
Widerström’s extensive experience within the global defence industry, including his work across Asia Pacific, Europe, Singapore, and the US, has imbued him with the unparalleled expertise and industry know-how to continue to lead SGD on an upward trajectory.
Having supplied its systems to over 20 countries around the world, SGD continues to maintain and expand its success across Europe, the Middle East, Asia Pacific, and Latin America.
“Our extensive global footprint provides us with a distinct advantage, allowing us to deliver unmatched support and solutions on a worldwide scale,” Widerström outlines.
In addition, the company offers signals intelligence systems for the passive interception and analysis of radar and communication signals, providing improved situational awareness from airborne, land-based, and naval platforms.
“We are a world-leading centre of competence for digital processing, microwave components, and antenna technology,” he enthuses.
At the core of SGD’s success is its approximately 400-strong staff base, who work across the company’s two campuses in Pretoria and Cape Town.
Driven by a shared passion for creating a safer world, SGD’s staff leverage their deep domain knowledge and technical expertise to develop state-of-the-art systems that enable effective communication, gather critical intelligence, and neutralise threats.
As the African defence industry witnesses widespread advancement, particularly in R&D, technical progress continues to be made.
“Our cutting-edge technology considerably sets SGD apart from the competition and positions us at the forefront of the industry,” Widerström comments.
In addition, with a legacy of over 50 years in the electronic warfare (EW) domain, SGD’s deep-rooted expertise and wealth of industry knowledge ensures the company’s robust and trustworthy reputation as a trusted partner, whilst its rich history speaks volumes about its dedication and proficiency.
“Our customer-centric approach enables us to adapt to and anticipate the evolving needs of our clients,” he continues.
Furthermore, as a company dedicated to remaining at the forefront of progress and innovation, SGD notes the importance of staying abreast of defence in Africa.
“Given the evolving nature of threats and the development of advanced missile systems globally, it is imperative that we are equipped to
effectively address and counter these emerging challenges.”
Therefore, SGD’s advanced MAW-400 missile approach warning sensors provide early threat detection in order to allow the timely deployment of decoys to maximise platform protection.
“The sensors have been designed to enhance survivability in combat situations, particularly those installed on helicopters, which can be considered airborne military platforms,” Widerström details.
SGD based the development of the MAW-400 sensor on prior experience with its predecessor, the MAW-300.
As a company committed to nurturing its employees, clients, and suppliers, SGD firmly believes that corporate social investment (CSI) plays a crucial role in shaping the environment in which it operates.
“Over the past few years, we have allocated resources to various CSI initiatives strategically aligned with poverty alleviation, education enhancement, and reducing unemployment across the country,” Widerström reveals.
These include community upliftment initiatives and support for educational programmes, such as the company’s adoption of the highperforming Ribane-Laka Secondary School, which is now transitioning to a school of specialisation (SoS) in maths, science, ICT, and engineering.
The company also provides bursaries and scholarships for
student programmes, mentorship, and coaching initiatives, whilst participating in Disability Connect and the Workplace Acceleration Programme, to name a few.
“SGD believes that CSI is about changing the environment for the betterment of the business and broader industry, which builds future employees, clients, and suppliers,” he elaborates.
Another of the ways SGD is actively working towards its goal of becoming a greener company is through a selffunded solar project.
“This initiative is testament to SGD’s commitment to sustainability and reducing our overall environmental impact as a business,” Widerström expands.
Sustainability is deeply ingrained within SGD’s business strategy, and it believes that the solar project will not only benefit the company but contribute to a cleaner and more sustainable future for all.
As a business operating within the niche of self-protection and against a backdrop of a constantly changing defence landscape, keeping ahead of evolving threats remains a top priority for SGD. As such, investing in advanced technology has become an increasingly important factor.
“We pride ourselves on being a true engineering company, with technology serving as the
cornerstone of our operations,” emphasises Widerström.
Ensuring it delivers solutions that not only meet but exceed the expectations of customers, partners, and suppliers is crucial, and advanced technology enhances SGD’s ability to adapt and innovate.
“When considering the significance of meeting our customers’ evolving needs, technology plays a vital role.”
Evidently, SGD values its relationships with partners and suppliers highly and views them as strategic assets that help the company maintain its position as a leader in the EW domain.
Features and benefits of the new generation MAW-400 missile approach warning sensors for airborne platforms:
• The MAW-400 utilises solar-blind ultraviolet (UV) technology, which is extremely costeffective when compared to the likes of infrared (IR) approach warning sensors.
• It is one of only two similar products designed and manufactured outside the US, operational in multiple air forces, and capable of pre-steering Directed Infrared Counter Measure (DIRCM) systems.
• The sensors are built to withstand harsh operational environments found on helicopters, transport, and fighter aircraft. They can be supplied as an integrated part of IDAS-310 or as a standalone technology, seamlessly integrating with any host EW system.
“WE PRIDE OURSELVES ON BEING A TRUE ENGINEERING COMPANY, WITH TECHNOLOGY SERVING AS THE CORNERSTONE OF OUR OPERATIONS”
– JAN WIDERSTRÖM, PRESIDENT AND MANAGING DIRECTOR, SAAB GRINTEK DEFENCE
“OUR EXTENSIVE GLOBAL FOOTPRINT PROVIDES US WITH A DISTINCT ADVANTAGE, ALLOWING US TO DELIVER UNMATCHED SUPPORT AND SOLUTIONS ON A WORLDWIDE SCALE”
–
JAN WIDERSTRÖM, PRESIDENT AND MANAGING DIRECTOR, SAAB
GRINTEK DEFENCE
“Our partners and suppliers are instrumental in providing the necessary support to enable us to widely deliver cutting-edge defence solutions,” he notes.
To achieve this, SGD prioritises maintaining open lines of communication with partners and suppliers.
This is especially important in today’s ever-evolving supply chain landscape, where demands are constantly changing.
Going forward, SGD plans to focus
on driving sustainable growth for the company whilst expanding its market presence.
“We are committed to strengthening our recruitment base in South Africa, ensuring that we have the right talent to drive our business forward,” he concludes.
Finally, the company is working towards cultivating a work environment that nurtures employee development whilst fostering a sense of fulfilment in their roles.
By prioritising these areas, SGD aims to position itself for continued growth and excellence.
Tel: 012-492-3837
refuwe.makhubo@za.saabgroup.com www.saab.com
At the forefront of the African aerospace manufacturing industry, NewSpace Systems is breaking boundaries and pioneering new frontiers in technological advancements while contributing to economic growth on the continent. CEO, James Barrington-Brown, tells us more
Writer: Rachel Carr | Project Manager: Thomas Arnold
Born out of humanity’s insatiable curiosity to explore the cosmic expanse, the NewSpace Systems (NSS) narrative launched in 2013, when its CEO, James Barrington-Brown, recognised the untapped potential of manufacturing precision spacecraft components and sub-systems technology in South Africa (SA).
“I spearheaded the establishment of a European-class hub, and since then, NSS has been committed to the continuous expansion of manufacturing capabilities and R&D,” Barrington-Brown opens.
Evidently, the trusted multinational company continues to push the boundaries of innovation in the aerospace industry.
“Our products have been utilised on more than 2,000 spacecraft, and with over a decade of expertise in manufacturing guidance, navigation, and control (GNC) products, we have solidified our position as the largest exporter of spacecraft-utilised hardware on the African continent,” affirms Barrington-Brown.
To support its position, NSS’ headquarters are located in Somerset West, SA, employing over 100
skilled professionals. The company has additional strategically located branches across North America, Europe, and Oceania to bolster its global operations, alongside a diverse client base, ranging from commercial entities to government agencies.
“We’re supporting the majority of spacecraft manufacturers, encompassing esteemed blue-chip companies, constellation builders who comprise 500 or more satellites, and more than 17 national space agencies, including NASA.”
As experts in GNC technology, NSS products are integral for various
Barrington-Brown’s journey into the aerospace industry began during his electronics degree Within his chosen study subject, developing and manufacturing space technology appealed to him as the most cutting-edge developments at the time were in two main sectors: space and defence.
“Opting for the former, I quickly transitioned into the space domain after spending three years in the high fidelity (Hi-Fi) industry. My career trajectory unfolded progressively, starting with roles in electronics design, before advancing into project management. Eventually, I became part of a management buyout and secured a directorship.
“What consistently captivated me was the untapped potential in the market for smaller, more costeffective satellites. This realisation prompted the establishment of NSS just over a decade ago.”
Recognising the significant advantage of operating in a lowercost environment in SA, NSS aims to produce high-performance and reliable spacecraft components at an economical price.
“It’s been an exciting journey, driven by the vision of making space missions more accessible through innovation and costeffectiveness,” Barrington-Brown reflects.
satellite missions. In the realm of communications and radar satellites, its equipment ensures precise antenna alignment, while for Earth observation satellites, it facilitates accurate camera pointing.
“What sets NSS apart is its adaptability to different satellite types, catering to both commercial and government needs. The success of our products is grounded in this versatility,” Barrington-Brown elaborates.
As the space industry undergoes a transformative shift, NSS is witnessing an increased focus on game-changing
constellation use. For certain missions, this translates to a higher frequency of captured images throughout the day, but this is not the only benefit.
“In communications, having a satellite constantly overhead enables seamless connectivity globally. Our primary focus is to align with the sector’s shift, contributing to the evolving landscape of space initiatives by enhancing our production volumes to meet the growing demands of these innovative mission profiles,” Barrington-Brown outlines.
Regarding spacecraft navigation control, the initial challenge lies in determining a position, considering there is no concept of up or down in space.
Retronix has significantly expanded its tinning service, which already included a wide range of component types, such as BGA, QFP, leaded devices, and QFNs, and has now incorporated chip capacitors and SOTs as well.
This expansion is a response to the industry's persistent concerns about tin whisker growth, particularly in space, avionics, and defense sectors where tin whisker failure is unacceptable.
RETRONIX BENEFITS
The automated tinning process developed by Retronix has made a remarkable advancement in the electronics industry, especially in the tinning of chip components to GEIA standards. Previously, the small size of components like capacitors and resistors posed a challenge for automated tinning.
However, Retronix has uniquely positioned itself to process all components from lead-free to tin/lead in accordance with the GEIA standard, providing customers with a comprehensive solution.
“To address the navigation issue, we utilise guides such as the Sun, which serves as a stable reference, along with the stars and the Earth’s magnetic field. This involves the use of Sun sensors, magnetometers, and stellar gyroscopes.
“Once the spacecraft’s position is established, the orientation is managed using Earth’s magnetic field, employing electro-magnetic rods and reaction wheels that utilise accelerating rotating masses.
“This approach minimises fuel consumption and ensures operational longevity. For orbit position, we incorporate Global Navigation Satellite Systems (GNSS) to precisely locate the spacecraft relative to Earth,” explains Barrington-Brown. On the production side, NSS
“ROBOTS EXCEL IN REPETITIVE TASKS FOR MASS PRODUCTION, BUT WE RECOGNISE THAT SPACE-RELATED MANUFACTURING REQUIRES A MORE NUANCED APPROACH”
JAMES BARRINGTON-BROWN, CEO, NEWSPACE SYSTEMS
has invested in a unique, clean manufacturing facility in Africa. Drawing inspiration from the automotive and aviation industries, it implements controlled and repeatable processes.
“We house our production machinery in a dust-free, humidity and temperature-controlled environment, crucial for spacecraft manufacturing where reliability and longevity are paramount.”
The company has also invested in environmental testing capabilities that simulate the launch and orbital habitat in space, such as vibration machines to test mechanical robustness and thermal cycling ovens.
Accurately reproducing and testing components on the ground that have previously been qualified
for use in space is essential, given the impracticality of on-orbit maintenance or repairs.
“We employ a highly skilled product development team alongside our manufacturing capability, designing new products based on market demand and advances in available technology and material,” notes Barrington-Brown.
The space activity landscape has recently undergone a profound transformation. Initially solely government-funded, it was mainly science-oriented and supported long-distance telecommunications. However, the industry has now moved significantly towards a commercially financed model.
“Companies are leveraging private investments to create services centred around supplying imaging data or global internet and mobile communications. However, the historical challenge has been the high cost of space infrastructure, making it difficult for these business models to formulate a viable plan,” he explains.
To tackle the problem, notable examples such as SpaceX have successfully reduced the cost of launching satellites. Similarly, NSS has played a crucial role in lowering the cost of manufacturing spacecraft platforms, enabling these spacebased services to compete effectively with their terrestrial counterparts.
“Once launched and deployed, satellites operate from solar power and maintain orbit with virtually no fuel consumption. This results in a very low-cost resource for many years of service. Therefore, the primary challenge lies in the initial price of building and launching
Executive Engineering was established in 1995, and with 29 years of experience, we are one of the top Precision Engineering companies in South Africa. We offer fully integrated, end-to-end, engineering component solutions. We pride ourselves in the supply of innovative precision machined components and sub-assemblies with fine tolerance restraints. While we are able to provide one-stop manufacturing and engineering solutions, we are willing to source any requirements that we do not offer.
Upholding our well-established philosophy of engineering brilliance, collaboration and adaptability in our manufacturing techniques, accompanied by the ability to machine a variety of material types, has enabled us to produce components that are suitable for almost any request. We are committed to investing in and staying abreast of the latest developments and innovations in the manufacturing industry.
11 Barlinka Saxenburg Park, Blackheath, Cape Town, 7580
www.execeng.co.za
these assets into space,” informs Barrington-Brown.
Nevertheless, a notable surge in private investment and venture capital (VC) has been pouring into the space industry in the last five years, with a particular focus on constellations and lower-cost satellites.
This trend has created growth opportunities for prime and Tier 2 contractors, such as NSS.
“We liken ourselves to the shovel providers in the gold rush, as we supply essential components for the industry’s expansion,” he points out.
With a considerable influx of funding at the service level, there is a positive flow-down effect throughout the supply chain, benefitting prime and secondary contractors.
“At NSS, our role as suppliers to prime contractors has contributed to our success in this dynamic and growing industry, particularly in the field of GNC technology,” BarringtonBrown reports.
Early on in its journey, NSS was selected for the OneWeb programme - a global broadband satellite constellation featuring 650 spacecraft. The network provides the unique aspect of continuously operating a spacecraft overhead at any given point on the planet. This breakthrough allows for low latency global broadband and voice communications.
“In the context of Africa, this holds tremendous potential as, previously, rural communities outside the range of traditional cell phone towers could not access fast communication services,” enlightens Barrington-Brown.
Another benefit of the OneWeb programme is its impact on education and businesses, with advantages extending to telemedicine, enhancing health services, and contributing to overall societal well-being.
• To meet the escalating market demand for products, NSS aims to double the number of production lines and quadruple production rates. This will be achieved by building a brand new, world-class production facility.
• Introduce radio frequency (RF) products, specifically in satellite communications. This expansion allows NSS to diversify its product range and cater to a broader market.
• Optimise products to align with next-generation standards, boasting enhanced performance and reliability in higher orbits. NSS believes these advancements will support current market needs and position it favourably in the rapidly evolving space industry.
“In essence, broadband serves as a critical enabler. It’s not just about connectivity; it’s about empowering people at the grassroots level and transforming society by bringing the benefits of space technology to everyday lives.”
It is important to note that NSS isn’t just a manufacturing entity; equally, it’s a product development company, necessitating a diverse skill set across engineering and industrialisation. Consequently, continual upskilling is a vital component of NSS’ workforce development.
“On the artisan side, we tap into a rich pool of skilled individuals who exhibit manual dexterity, patience, and precision qualities essential for producing high-quality and reliable products. We invest in their development by providing six months of training to meet international space standards.”
“WHAT SETS NSS APART IS ITS ADAPTABILITY TO DIFFERENT SATELLITE TYPES, CATERING TO BOTH COMMERCIAL AND GOVERNMENT NEEDS. THE SUCCESS OF OUR PRODUCTS IS GROUNDED IN THIS VERSATILITY”
JAMES BARRINGTON-BROWN, CEO, NEWSPACE SYSTEMS
Many employees embrace the space industry after joining NSS, which Barrington-Brown finds rewarding.
“Their contributions to space exploration can be truly inspirational; a mother returning home after a day’s work can share with her children that she played a part in building something destined for the Moon or Mars.
“Not only does this instil a sense of pride, but it also encourages the next generation to dream beyond their current circumstances, fostering aspirations to become astronauts, rocket scientists,
spacecraft designers, and builders,” he exclaims.
With the rise and emergence of constellations entering the market, NSS focuses on scaling up its ability to produce high-reliability equipment in large volumes.
While there is a strong push towards Industrial Revolution 4.0, which emphasises replacing people with automation, artificial intelligence (AI), and robotics, Barrington-Brown advocates for a concept he terms Industrial Revolution 4.1.
“Rather than replacing people, we aim for efficiency by employing flexible, rapidly adaptable production lines that integrate human skills. This unique approach aligns with our vision for a more globally minded and game-changing manufacturing process,” he shares.
While NSS is introducing automation, it remains committed to preserving the human touch in the production process.
“Robots excel in repetitive tasks for mass production, but we recognise that space-related manufacturing requires a more nuanced approach. Space projects often involve small
batches, and humans offer a costeffective and efficient solution, especially in a low-cost environment like Africa,” details Barrington-Brown.
NSS’ investment strategy includes ongoing efforts to enhance its workforce’s skills, acknowledging that space manufacturing’s intricacies demand precision and customisation.
“In this pursuit, we have acquired advanced equipment, such as optical
inspection tools, designed to enhance the abilities of our skilled workforce instead of replacing them.
“These investments underscore our commitment to maintaining quality and reliability in the face of the challenging space environment, aligning with our goal of advancing space technology in a uniquely African manner,” Barrington-Brown concludes.
Tel: +27 21 300 0160
mark@newspacesystems.com newspacesystems.com
ACTOM offers a winning and balanced combination of manufacturing, service, repairs, maintenance, projects, and distribution of electromechanical equipment through its 33 outlets across sub-Saharan Africa
Writer: Ed Budds | Project Manager: Joshua Mann
The ongoing adoption of Internet of Things (IoT) and artificial intelligence (AI) technologies is driving a profound transformation in South Africa’s electromechanical equipment sector.
This significant upgrade is subsequently giving rise to smart grids and the optimisation of energy generation, distribution, and consumption across the continent.
Key to this digital transformation is the demand for intelligent equipment capable of remote monitoring and control, ushering in unprecedented efficiency and resilience.
To this point, the uptake of digital transformation within South Africa’s industrial sector has been rapid, with leading equipment manufacturers realising the importance of giving their equipment a voice through IoT.
As a result, this burgeoning industry is seeing a significant amount of smart development by leveraging real-time
data for condition monitoring.
For the entire sector, this remains key to enhancing the performance and efficiency of equipment and enabling remote monitoring that benefits both manufacturers and clients, as downtime can be prevented by tracking the health and other parameters of components and infrastructure.
As a key player in this evolving landscape, energy behemoth ACTOM has diligently helped power the African continent for more than a century.
Today, ACTOM is an industry leader and the largest manufacturer, solutions provider, repairer, and distributor of electromechanical equipment in Africa, employing around 5,550 people.
The company exists proudly as a Black-empowered organisation with
34 operating units, 53 production, service, and repair facilities, and more than 30 distribution outlets throughout Southern Africa.
With more than 100 years of experience in energy, the company has continually evolved its product and service offerings to meet the world’s energy needs.
Undoubtedly, ACTOM’s innovative, cutting-edge technology has helped it to provide reliable, environmentallyfriendly energy solutions for both consumers and businesses.
ACTOM is also a major local supplier of electrical equipment, services, and balance of plant to renewable energy projects.
Alongside this, it holds numerous technology, distribution, and valueadded reseller agreements with various partners, both locally and internationally, where the company has grown its capabilities to now act as a leading supplier of premium and standard low-voltage motors, gearboxes, speed reducers, and motor starters.
ACTOM strives to improve the quality of life of the communities in which it operates.
The company is achieving this through its socioeconomic development investment initiatives:
• Supply of IT infrastructure and other educational materials.
• Training technical talent.
• Direct and indirect job creation.
• Donations and charity work.
• Supporting schools with maths and science tutoring programmes.
• Research partnerships with universities.
As social and environmental factors vary from area to area, ACTOM adopts an approach that respects and embraces South Africa’s rich cultural diversity.
In this way, ACTOM custom designs and manufactures mediumvoltage motors for the mining, industrial, processing, and utilities markets in South Africa and across the globe.
Alongside this, the business now also manufactures laminated components and tooling for the electric motor sector.
Dedicated to ensuring a greener future for all, ACTOM is committed to meeting its own needs in a sustainable way that doesn’t compromise future generations.
The company’s carefully monitored strategy aims to create shareholder value and ensure that all business units are delivering a positive return on capital employed (ROCE) and therefore employing capital in the most attractive opportunities.
As part of ACTOM’s ‘Just Transition’ phase, the company seeks growth and sustainability for its vast array of divisions and business units. This indicates the organisation’s adaptability to support the industry as it moves away from carbon intensive energy production to sustainable methods.
As part of this strategy, the company’s Static Power business unit completed a 200 kilowatt (kw) photovoltaic (PV) rooftop installation at the ACTOM Turbo Machines facility in April 2022.
This has resulted in the need to increase the system with another 200kW PV installation, which will include a battery with a standby time of eight hours for energy storage.
All transformers produced in the ACTOM portfolio, meanwhile, are now also designed to operate with both natural and synthetic ester oils.
As a key part of this transformation, ACTOM retrofills existing transformers with ester oil in-situ within a matter of days and discards the old oil in a responsible manner.
Elsewhere, in terms of transformer oil regeneration, ACTOM remains focused on returning used transformer oil to international standards.
Today, the company’s Denver
facility boasts a SANS 555 accredited oil regeneration facility, which returns used transformer oil to internationally specified standards for re-use. This practice negates the need to produce new oil, thus reducing the burden on the environment.
This impressive facility has a Section 20 waste permit from the Department of Environmental Affairs and all quality tests are performed on-site by a fully comprehensive accredited laboratory.
John Thompson is now one of the leading divisions of ACTOM, and the company’s proud history of boiler design and manufacturing supports its principal focus – to be a global leader in energy and environmental solutions through value engineering and innovation.
Firmly focused on serving its global customer base, the products
and services ACTOM offers include boilers, environmental solutions such as air pollution control, engineering, energy management, manufacturing, spares, maintenance, and training.
To provide its customers with the best solution to any engineering challenge, ACTOM can now accurately simulate virtually any scenario using the latest computational fluid dynamics technology.
Furthermore, ACTOM’s capabilities in finite element analysis and thermal, circulation, and solid modelling enable its range of solutions to be custom-fit for purpose every time.
When maintenance is needed, ACTOM’s electromechanical maintenance, service, and repairs specialist, Marthinusen & Coutts, carries out the servicing of machinery and equipment for the mining, rail transportation, utilities, marine, and oil and gas industries.
The company is a specialist repairer of power generation equipment and medium and low-voltage AC and DC motors, manufacturer of transformers and coils, and has a full range of engineering, testing, diagnostics, balancing, and maintenance services at its disposal.
ACTOM’s success stories are evident in its completed projects, such as the Ngodwana Biomass Power Station, established under South Africa’s Independent Power Producer Programme, which was completed as a joint venture between John Thompson’s Industrial Watertube Boilers, a further ACTOM division, and Lesedi Nuclear Services.
The power plant is adjacent to the Sappi Ngodwana pulp mill in Mpumalanga, the installation of which took 20 months.
Moving forward, John Thompson will operate and maintain the entire plant over a five-year period.
Furthermore, ACTOM is involved in many power projects in the African market, including the Ingula and Drakensberg Pumped Storage Schemes.
This impressive portfolio reaffirms ACTOM’s position in the power island supply chain and broader industry.
The Outlook Creative Services Division provides a complete web design, build and delivery service that leverages the expertise of our in-house production team. Complementing Outlook Publishing’s portfolio of esteemed global publications, our specialist skills cater to clients around the world with a fully bespoke service.
If you would like us to bring your digital story to life with passion and purpose, visit www.outlookcs.com or email hello@outlookcs.com