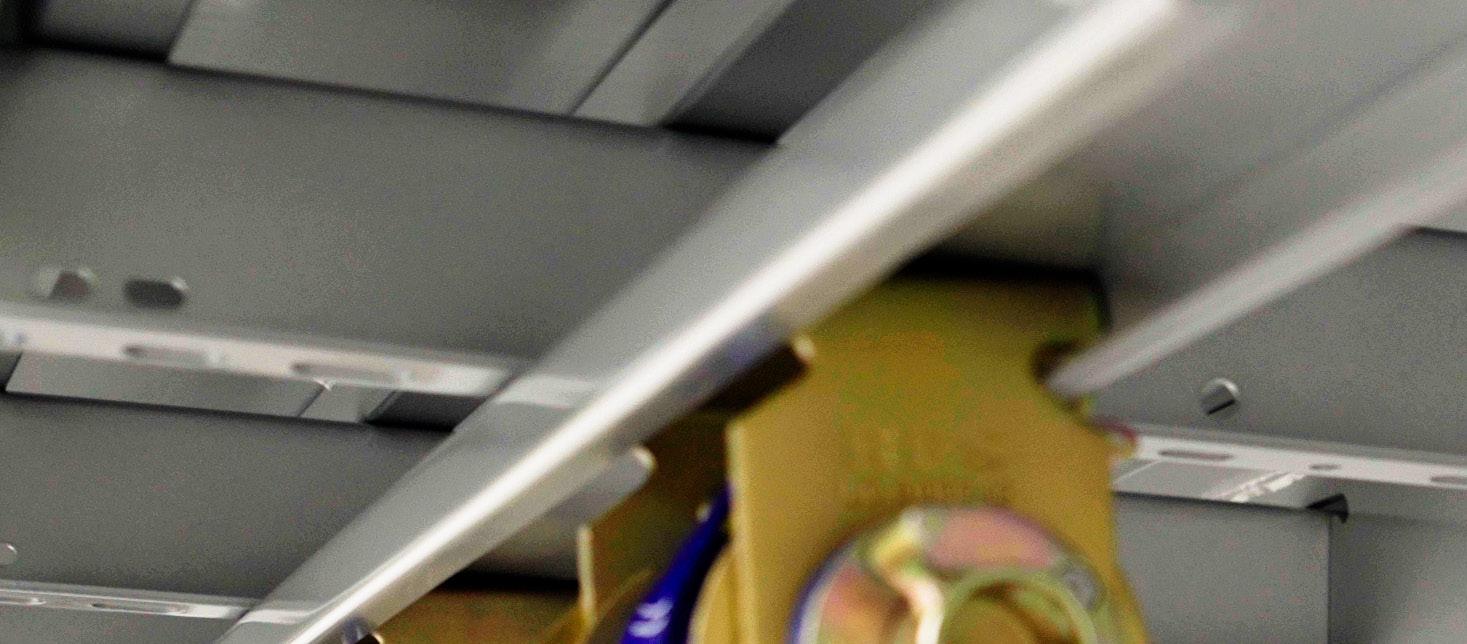
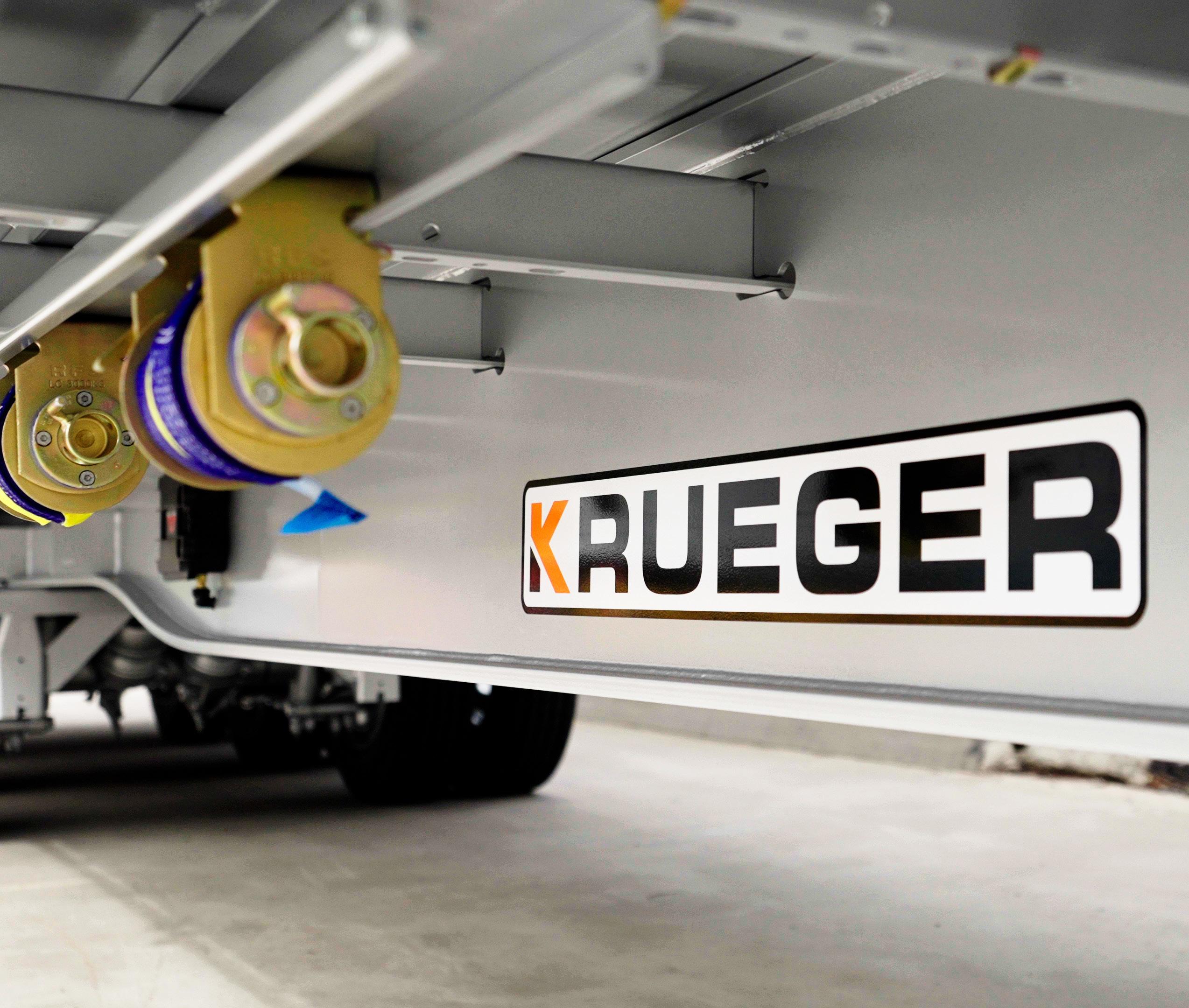
Africa Outlook, APAC Outlook, EME Outlook, North America Outlook, Mining Outlook, Healthcare Outlook, Manufacturing Outlook, Supply Chain Outlook, and Food & Beverage Outlook are digital publications aimed at boardroom and hands-on decision-makers, reaching an audience of more than 800,000 people around the world.
With original and exclusive content compiled by our experienced editorial team, we look to promote the latest in engaging news, industry trends and success stories from across the globe.
Your company can join the leading industry heavyweights enjoying the free exposure we provide across our platforms with a free marketing brochure, extensive social media saturation, enhanced B2B networking opportunities, and a readymade forum to attract new investment and to help you grow your business.
Visit www.outpb.com/work-with-us for details on how your company can feature for free in one of our upcoming editions.
EDITORIAL
Head of Editorial: Jack Salter jack.salter@outpb.com
Deputy Head of Editorial: Lucy Pilgrim lucy.pilgrim@outpb.com
Senior Editor: Lily Sawyer lily.sawyer@outpb.com
Editor: Ed Budds ed.budds@outpb.com
Editor: Rachel Carr rachel.carr@outpb.com
Editor: Lauren Kania lauren.kania@outpb.com
PRODUCTION
Art Director: Stephen Giles steve.giles@outpb.com
Senior Designer: Devon Collins devon.collins@outpb.com
Designer: Louisa Martin louisa.martin@outpb.com
Production Manager: Alex James alex.james@outpb.com
Digital Marketing Director: Fox Tucker fox.tucker@outpb.com
Website Content Manager: Oliver Shrouder oliver.shrouder@outpb.com
Social Media Executive: Jake Crickmore jake.crickmore@outpb.com
BUSINESS
CEO: Ben Weaver ben.weaver@outpb.com
Managing Director: James Mitchell james.mitchell@outpb.com
Chief Commercial Officer: Nick Norris nick.norris@outpb.com
REGIONAL DIRECTORS
David Knott david.knott@outpb.com Tom Cullum tom.cullum@outpb.com
PROJECT MANAGERS
Lauren Robinson lauren.robinson@outpb.com
Kierron Rose kierron.rose@outpb.com
Michael Sommerfield michael.sommerfield@outpb.com
Scarlett Burke scarlett.burke@outpb.com
DIVISIONAL DIRECTOR
Deane Anderton deane.anderton@outpb.com
HEADS OF PROJECTS
Alfie Wilson alfie.wilson@outpb.com
Eddie Clinton eddie.clinton@outpb.com
Ryan Gray ryan.gray@outpb.com
BUSINESS DEVELOPMENT DIRECTOR Thomas Arnold thomas.arnold@outpb.com
TRAINING & DEVELOPMENT DIRECTOR Joshua Mann joshua.mann@outpb.com
SALES & PARTNERSHIPS MANAGER Donovan Smith donovan.smith@outpb.com
SALES MANAGERS Krisha Canlas krisha.canlas@outpb.com
ADMINISTRATION
Finance Director: Suzanne Welsh suzanne.welsh@outpb.com
Finance Assistant: Suzie Kittle suzie.kittle@outpb.com
Finance Assistant: Victoria McAllister victoria.mcallister@outpb.com
CONTACT
Manufacturing Outlook
Norvic House, 29-33 Chapelfield Road
Norwich, NR2 1RP, United Kingdom
Sales: +44 (0) 1603 804 445
Editorial: +44 (0) 1603 804 431
SUBSCRIPTIONS Tel: +44 (0) 1603 804 431 jack.salter@outpb.com www.mfg-outlook.com
Like us on Facebook: facebook.com/manufacturingoutlook Follow us on Twitter: @outlookpublish
Welcome to our fifth edition of Manufacturing Outlook magazine.
Australia continues to be a frontrunner in the international trailer industry, with the increasing adoption of performance-based standards, electric vehicles (EVs), and hydrogen technology.
This extensive issue is towed by Krueger Transport Equipment (Krueger), whose trailers have become the product of choice for leading logistics organisations across the country.
We sit down with members of the company’s leadership team, who provide a comprehensive insight into Krueger’s pioneering designs, constant pursuit of quality, exceptional customer service, and expanding product range.
“Our commitment to excellence, reliability, and customer satisfaction has solidified our position as a powerhouse in the Australian transportation market,” prides CEO, Kevin Dennis.
Positioned as one of the world’s leading manufacturers of forestry equipment, meanwhile, is Komatsu Forest.
Today, sustainable forestry management and timber harvesting is seen as a realistic solution to the use of fossil fuels and single-use plastics.
Thus, Komatsu Forest develops solutions that can support and contribute to the environment during the full forestry lifecycle.
“For sustainable forestry that will continue to add value for generations to come, we believe that forests need to be managed and maintained considerately so that it can keep providing the valuable raw materials,” confirms CEO, Jens Bengtsson.
Elsewhere, Alspec, an industry leader in the design and distribution of forward-thinking aluminium systems, is well positioned to leverage significant developments in smart building technologies and sustainable construction practices, offering products that meet the demands of modern construction while adhering to stringent environmental standards.
Our comprehensive coverage explores how Alspec capitalises on the unique qualities of aluminium, such as its light weight, strength, and recyclability, by offering bespoke solutions that advance sustainability across Australian construction projects.
This final edition of the year also showcases the latest developments from leading manufacturers such as Cold Chain Technologies, Czech Mint, Delco Trailers, HighCom Group, and Trymax Semiconductor Equipment B.V.
We hope that you enjoy your read.
Jack Salter Head of Editorial, Outlook Publishing
Around the manufacturing sector in seven stories…
A GROUNDBREAKING feat in the world of heavy vehicles, Scania has become the first truck original equipment manufacturer (OEM) to reuse components on its main assembly line.
This historic achievement from the major Swedish OEM displays the possibility of integrating remanufactured components into the production lines of new vehicles.
As part of the iReGear joint research project with the KTH Royal Institute of Technology and Scandinavian Transmission Service AB, this milestone gearbox consumed 50 percent less material and caused 45 percent less carbon emissions whilst still being subjected to the same rigorous steps and in-line quality and function tests as gearboxes made entirely from new parts.
GENERAL MOTORS (GM) has been forced to temporarily halt vehicle production at two of its USbased factories due to the onslaught of damage experienced by its suppliers due to Hurricane Helene.
THE UK government’s £22 billion investment into two carbon capture and storage (CCS) schemes has the potential to secure manufacturing jobs for generations to come after Prime Minister, Sir Keir Starmer, and Chancellor, Rachel Reeves, visited the Encirc glass plant in Ellesmere Port, Cheshire.
These two schemes are located in HyNet and the East Coast Cluster in Teesside and the Humber.
The Prime Minister has confidently declared that this investment will provide the industry with the certainty it needs by committing to 25 years of funding in groundbreaking technology alongside delivering jobs and kickstarting growth.
The two plants, located in Flint, Michigan and Arlington, Texas, produce heavy-duty trucks and full-size SUVs, and the workers were notified that shifts would be cancelled for the time being.
GM is working with impacted suppliers to resume operations as quickly and safely as possible in the wake of the hurricane, which made landfall in Florida and significantly impacted the southeastern US.
ACROSS EUROPE, manufacturing activity in September slowed at its most rapid pace yet in 2024 as demand waned sharply despite factories cutting prices.
Europe’s largest economy, Germany, has recorded its most pronounced worsening of conditions for 12 months, further highlighting this challenging outlook and keeping policymakers under pressure to shore up fragile growth.
The Hamburg Commercial Bank (HCOB) Eurozone Manufacturing Purchasing Managers’ Index (PMI),
compiled by S&P Global, dropped to 45.0 in September, just ahead of a 44.8 preliminary estimate but further from the 50 mark separating growth from contraction.
NORTHERN IRELAND’S advanced manufacturing companies are embracing a new era of innovation and growth as the demand for reliable supply chains skyrockets to the top of the agenda. The advanced manufacturing
sector is playing a key role in the changing global supply chain, having taken inspiration from the COVID-19 pandemic to embrace new opportunities by utilising the companies’ knowledge and expertise to create resilient supply chains that have the ability to benefit other industries and expand sectors at a far greater rate than previously seen.
JC BAMFORD Excavators Limited (JCB) has let go of approximately 230 workers amid a global slump in manufacturing.
As the bosses brace for the market downturn, the construction giant cites the UK housebuilding slowdown as the reason why it has scaled back its workforce so drastically.
This decision comes immediately ahead of the UK government’s bid to strengthen workers’ rights, including awarding basic entitlements from day one of employment.
Despite the company’s profits having risen from £557 million to £805 million in 2023, CEO, Graeme Macdonald, states that the business is now expecting an excessive drop-off in activity.
THE NORTHERN Ireland Space Enterprise Lab (SEL), a £100 million project, has been officially opened at Queen’s University Belfast’s Advanced Manufacturing Innovation Centre (AMIC) Harbour site, allowing users to access the latest collaborative technology, resources, and expertise.
This latest addition to the Satellite Applications Catapult’s UK-wide network is connected to other nationwide SELs and ensures that technology and support are accessible to innovators and businesses based in the region.
This expansion marks a milestone in fostering innovation and collaboration, using space data and technology powered locally through the long-standing commitment of the Northern Ireland Space Office.
Chris Hocknell, Director of Eight Versa – a leading sustainability consultancy firm - explores how manufacturing businesses can be more effectively integrated into global policy considerations and the worldwide shift towards renewable energy
Writer: Chris Hocknell, Director, Eight Versa
Sustainability has become a buzzword in the manufacturing sector as businesses worldwide promote their green credentials and commitments to environmentallyfriendly practices.
The prevailing narrative suggests that sustainability and profitability go hand in hand, with claims that eco-friendly practices lead to cost
savings, improved brand image, and long-term viability. However, the reality is far more complex, particularly for industries in Europe.
Sustainability is often presented as both an ethical imperative and a strategic opportunity. Companies highlight benefits such as cost reductions from energy efficiency, waste minimisation, improved brand
reputation, and increased innovation. Adopting eco-friendly practices is also seen as a way to manage risks and ensure compliance with stringent environmental regulations.
In reality, businesses struggle to balance environmental responsibility with economic viability, as transitioning to sustainable manufacturing comes with significant
costs, often hidden or ignored in corporate reports.
The initial investment in new technologies and processes can be prohibitively high, disrupting supply chains and reducing operational efficiency in the short term. Moreover, the ongoing costs of sourcing sustainable materials and renewable energy further complicate the
economic equation for manufacturers.
One major challenge, especially in Europe, is the integration of renewable energy into the grid. While renewable energy is often portrayed as cheaper and more sustainable than fossil fuels, many European countries
have seen electricity prices rise significantly.
Germany and Denmark, for example, consistently report some of the highest prices in Europe. In the UK, electricity prices increased by 60 percent between 2010 and 2020; and in comparison, wholesale gas prices dropped by 40 percent over the same period.
The reality is that there are system-level costs to renewables, often ignored by lobbyists who use metrics that just focus on the generation cost of each technology.
For example, upgrading grid infrastructure to accommodate renewables, as in Germany’s SuedLink project, incurs substantial expenses. Meanwhile, maintaining grid stability becomes a major issue with variable sources like wind and solar that require gas back-up to fill the generation gap, build capacity markets, and for additional energy storage facilities.
Combined with the need to ‘overbuild’ renewable capacity due to its lower load factor, all of these variables aggregate to a higher cost system, which has slowly undermined the competitiveness of European manufacturing.
Rising energy costs affect the manufacturing industry on a global scale. The situation forces energyintensive operations to relocate to regions with lower energy prices and looser environmental regulations.
Markets like China, India, Indonesia, and Vietnam have all experienced substantial growth. The former has taken the mantle of the workshop of the world over the last three decades, often achieving a year-on-year increase in manufacturing output. India and Indonesia are following suit by exceeding five percent growth per annum.
Conversely, we’ve seen substantially reduced investment in European manufacturing and a shift towards less energy-intensive
products and processes. In the best-case scenario, automation becomes the key strategy for European manufacturers seeking to offset rising energy costs, in the worst case, it’s outright offshoring.
This decline has also occurred in other highincome economies like the US and Japan, albeit to a lesser extent in the former as the country is blessed with a bounty of natural resources and prefers to talk a good climate game but let Europe do the bulk of deindustrialisation.
This shift leads to a phenomenon known as carbon leakage, where stricter environmental regulations in one region lead to increased emissions in another.
As manufacturing shifts away from regions with stringent environmental regulations to those with more lenient policies, it effectively outsources emissions.
This phenomenon is becoming increasingly evident in Europe, where rising cement imports have been linked to stricter EU climate policies, and the EU’s share of global production in key sectors like chemicals and steel has declined.
While these trends may seem like progress towards decarbonisation, emissions are mostly being shifted to other regions, leaving the global carbon footprint largely unchanged.
It’s not all doom and gloom: there are currently new technologies and developing sectors that will be crucial to advancing sustainable manufacturing.
We’re slowly seeing lowcarbon, high-performance materials being touted in various sectors. For example, developments in biotechnology and materials science are facilitating the creation of bio-based materials and processes with lower environmental impacts.
Additive manufacturing, or 3D printing, is also increasing, which subsequently reduces waste and enables more localised production, while the industrial internet of things (IIoT) and artificial intelligence (AI), if deployed correctly, can improve energy and resource efficiency across industries.
To maintain a competitive manufacturing sector in the current landscape, and make it sustainable, we need to begin by tackling energy costs.
Governments should look at
reforming the current electricity market design to better reflect the costs and benefits of different energy sources. A reassessment of nuclear power’s role in providing stable, long-term, and low-carbon energy is also essential.
Hydrogen technologies may offer cleaner energy alternatives for heavy industries like steel but remain eye-wateringly expensive. Therefore, continued investment and development will be needed to fully explore what a viable model could look like.
We also need to think globally. The EU’s proposed Carbon Border Adjustment Mechanism (CBAM) could help level the playing field for domestic and foreign producers, or if done badly, could make everything really expensive for European manufacturers and consumers.
As such, international cooperation around clean technology transfer is likely the only way to level the playing field, as this would help resolve the divergence between developed and developing countries and their roles in global manufacturing.
Sustainable manufacturing doesn’t have to be a zero-sum game, but these solutions require coordinated action. A fragmented world where polluting economies dominate manufacturing, while deindustrialised economies engage in virtue signalling – is a lose-lose scenario, as it will fail to address climate change and exacerbate economic inequalities and geopolitical tensions.
We must recognise that true sustainability in manufacturing is not about shifting problems from one part of the world to another. Instead, it requires a systemic approach to recognise the global impact of our policies and state investigation into the right clean technologies at the
right pace, reforming energy markets, and creating a more level playing field for manufacturers.
The choice before us is clear: we can either work together to create a sustainable and prosperous future for global manufacturing, or we can allow short-term thinking and national selfinterest to lead us into a fragmented and unsustainable world. The time for decisive action is now.
Chris Hocknell is Director of Eight Versa where he brings over 17 years’ experience in supporting the built environment and corporate world with their sustainability goals.
Specialising in sustainability strategy development, Hocknell works closely with clients to assess and understand their carbon and environmental footprint. Once measured, he partners with organisations to develop practical solutions so that they reach the highest standards and achieve Natural Carbon Solutions certification.
Along with his MSc in Environmental Technology and Energy Policy, Hocknell is a certified member of several associations, some of which include the Association of Energy Engineers (Certified Energy Manager), Chartered Institution of Building Services Engineers (CIBSE) (Low Carbon Consultant), as well as having Leadership in Energy and Environmental Design (LEED) and Building Research Establishment Environmental Assessment Method (BREEAM) accreditations.
South African-based car manufacturer, Mureza Auto Co Pty Ltd, is deeply committed to serving the African market.
Tatenda Mungofa, Founder, outlines the company’s vision to become the country’s leading automotive brand
Writer: Lily Sawyer
Initially founded to address the unique transportation challenges of the African continent, Mureza Auto Co Pty Ltd (Mureza) offers affordable, high-quality vehicles designed specifically for local conditions.
Providing economically viable, sustainable transport solutions is a major part of the company’s strategy, which has led to many customers requesting unique and original vehicle solutions.
“We have fast become the go-to company for bespoke, affordable automotive solutions for the African market,” introduces Founder, Tatenda Mungofa.
As a business-to-business (B2B) company, Mureza’s customer base comprises both new and established automotive dealerships across the country.
“Our main production facility in Pilanesberg, South Africa (SA) is in its early stages of development. This is where the majority of our production will take place,” he sets out.
The company also has plans to set up assembly plants in Zimbabwe and Namibia alongside a West African manufacturing facility in Senegal.
“All our production sites are strategically located, supported by a growing distribution network,” Mungofa adds.
As an exciting and rapidly transforming space, the African automotive industry strives to support local value chains and brands.
“For us, however, the major hurdle is sourcing enough funding to build out capacity,” Mungofa discloses.
in the evolution of the continent’s automotive industry.
Lithium, cobalt, and other raw materials are key to unlocking value for the African industry, and governments across the continent are becoming increasingly aware of the advantages of local beneficiation.
Mureza works hard to promote African industrialisation and the national value chain. As such, its activities are largely focused on telling a story from grassroots to full-scale production.
Nevertheless, he notes how encouraging it is to see local investors support automotive companies like Mureza and anticipates a boom in investments over the next three years.
Meanwhile, electric vehicles (EVs) have become increasingly popular, accompanied by a shift in brand loyalty with many customers opting for newer Chinese brands over those from Europe, Japan, or the US.
Despite the attractive prospects that international competitors present, the recent widespread adoption of the African Continental Free Trade Area (AfCFTA), which seeks to unite the 55 countries of the African Union to create a single trade market for the continent, presents huge opportunities for the local economy.
“This is going to be the biggest market yet for African vehicles. I encourage major international brands to reposition their current investments into upcoming African car manufacturing companies to curb the decline most of them will experience as a result of the AfCFTA,” he advises.
As critical components in car manufacturing, Africa’s mineral resources also play an important role
“Africa needs industrial leadership. What we provide is inspiration to all Africans who dream of building largescale companies within the industrial sector,” Mungofa states boldly.
By establishing a refined and detailed development programme for every supplier in its value chain, Mureza is able to substantiate this claim.
In addition, the company’s database of over 150 suppliers ranges from small to medium-sized enterprises (SMEs) all the way to major Tier 1 contractors. This promotes crosspollination across the supply chain and an environment that supports the growth of smaller companies alongside experienced players with global exposure.
“Our microfactory strategy is a catalyst for rapid industrialisation across Africa and we plan on developing at least four main factories over the next 10 years,” he reveals.
Each of Mureza’s factories will be supported by 15 smaller assembly plants, each complete with a supplier park to support its operations.
Mureza believes that this unique growth strategy will promote local supply chains whilst benefitting surrounding communities with employment and development opportunities.
MANUFACTURING OUTLOOK: AS MUREZA CONTINUES
Tatenda Mungofa, Founder: “As a business, we are focusing on vehicle design and production. This has opened up many opportunities for us within the turnkey consulting space in the automotive sector.
“Therefore, we are willing to onboard clients who are looking for insight on how to set up operations similar to ours or that feed into our workflow. There is a lot of value in what we have built so far, and many investors can benefit from the research we have accumulated.
“Elsewhere, our archive of digital assets is set to be launched as a gaming platform, and we are currently looking for suitable partners to roll this out.
“Another interesting space we are venturing into is property development. This comes on the back of Mureza acquiring a lot of strategic real estate for our manufacturing facilities in SA, Zimbabwe, Namibia, and Senegal.
“We have realised the potential of these assets based on their strategic locations and alignment with the growth plans of these respective countries.”
This will naturally be accompanied by upskilling staff and training suppliers to meet international quality standards for vehicle components.
“The more we achieve our target to set up local factories, the more we are able to help Africa industrialise,” Mungofa asserts.
By creating an internal quality management system (QMS) to ensure vehicle components are compliant with stringent regulatory standards, Mureza guarantees the quality of its vehicles.
“It takes time to develop and produce each of our vehicles because we invest a lot of R&D into each of our models,” Mungofa prides.
Currently, the company is working on rolling out its first EV through its microfactory process. This has so far provided a good benchmark on how Mureza’s strategy effectively reduces production times and costs to ensure affordability.
In terms of product reliability, Mureza carries out careful individual component testing to ensure each element is fully functional before being widely utilised in the production line.
It also homologates its vehicles to ensure they comply with local regulations.
“Before launching a vehicle, extensive tests are done in-house at our testing facility to assess the impacts of real-life conditions,” he explains.
Mureza’s newest vehicle was inspired by an initial internal combustion engine (ICE) model, originally intended for launch in 2019, which became severely disrupted by the onset of the COVID-19 pandemic.
“Having previously shelved the model, we’ve now redesigned it for a new platform that will be
manufactured in Africa from the ground up,” Mungofa informs.
The new sedan vehicle, SHONA, takes its name from native Zimbabwean and has significant alliance with Mureza’s own brand name.
Inspiration was also drawn from one of SA’s great actors and film producers, the late Shona Ferguson.
“Our target retail price for SHONA is ZAR225,000, available in both an EV and ICE model,” he sets out.
The EV model will have a range of 300 kilometres (km), fully charge in just two hours, and reach speeds of up to 180km per hour.
The architecture of the car is inspired by Formula 1 technology, whilst a simplified manufacturing process has been made possible by its innovative design.
“Most of the technology and features of SHONA are new and forward-thinking, providing a memorable driving experience to
each customer,” Mungofa points out.
The petrol ICE version of SHONA will be powered by a choice of three engine sizes – 1.3 litre (L), 1.6L, or 1.8L, some of which will be turbopowered to provide both enhanced performance and fuel economy.
“More details on these engines and power ratings will be shared at our upcoming launch event,” he promises.
Design is at the heart of Mureza, exemplified by the dedicated design studio and R&D centre at its manufacturing site.
“Although still relatively small, supported by a team of just 12, the design studio is the heart of our operation,” Mungofa impassions.
He goes on to explain how multiple hours are dedicated to concept creation for each of the company’s vehicles.
In addition, having recently incorporated artificial intelligence
(AI) into its design process, Mureza makes significant cost and time savings by utilising new technologies as it is able to carefully evaluate each design before proceeding to the development stage.
The company’s design engineers work collaboratively with its fabrication team, specifying colours and materials before the first mock-up.
“A lot of 3D printing is used in this process to make prototype parts. We have eliminated clay modelling at this stage as it adds significant time and cost and is an outdated craft that no longer serves our purpose,” he divulges.
Once a 1:4 scale model has been 3D printed, Mureza can rapidly re-work surfaces using computer-aided design (CAD), building a scale model with a complete interior.
At this stage, the company also simultaneously engages with suppliers to begin work on the
“WE HAVE FAST BECOME THE GO-TO COMPANY FOR BESPOKE, AFFORDABLE AUTOMOTIVE SOLUTIONS FOR THE AFRICAN MARKET”
– TATENDA MUNGOFA, FOUNDER, MUREZA AUTO CO PTY LTD
components required.
“We entrust the drive train to our suppliers and utilise an interactive project development process as a model. From idea to complete
conception, a car takes us around 90 days to finalise, costing at least 60 percent less than that of traditional automotive design studio,” Mungofa highlights.
Aiming to set a new benchmark for the African car design and production process, Mureza seeks to establish a new generation of African vehicles through innovation.
Going forwards, Mureza’s main objective is to commence the delivery of its SHONA sedan to expectant customers.
Despite an influx of demand for SHONA, the company’s current capacity only allowed it to offer 1,000 pre-orders. In order to fulfil this, it aims
to complete production and start rolling off units in Q4 2024.
In addition, Mureza hopes to grow its human resources department from 65 employees to 150, supported by its suppliers’ anticipated workforce increase.
Meanwhile, showrooms and dealerships will be commissioned for 2025, whilst a continental expansion plan will be rolled out to manage the wider distribution of vehicles.
“We also look forward to getting long-term test reviews returned from different stakeholders,” Mungofa
outlines.
Further to this, Mureza hopes to be listed on the Johannesburg Stock Exchange (JSE), which is dependent on it delivering its 1,000 SHONA models within the proposed timeframe.
“We also want to give Africans an opportunity to be part owners of Africa’s flagship automotive brand, and we believe our growth will be faster if we work together,” he reveals.
Overall, the company aims to continue having fun growing the business and bringing its vision to life.
“If we manage to break into international markets beyond Africa, we look forward to collaborating with new prospective partners who share our vision of making the world a better place,” he concludes.
We explore the evolving relationship between infrastructure and manufacturing with Jonathan Edwards, EMEA Market Development Leader at GHD
Writer: Jack Salter
Manufacturing Outlook (MO): Firstly, can you tell us about your extensive expertise in the infrastructure sector?
Jonathan Edwards, EMEA Market Development Leader (JE): As GHD’s EMEA Market Development Leader,
I lead market strategy across our five markets and oversee our client experience and brand growth across the region.
I have built my career in the infrastructure sector, dedicated to driving growth, transformation, and successful project delivery and client
outcomes. My experience spans various sectors, including aviation, highways, and rail, where I have had the opportunity to work with multinational clients and managed some of the UK’s most significant and complex infrastructure programmes.
Major projects I have worked on include the Heathrow West expansion proposal, the Digital Railway programme, and the Thames Tideway Tunnel. These projects all required navigating intricate regulatory landscapes and stakeholder engagement processes, while placing innovation and sustainable practices at their core.
MO: What is your take on the infrastructure industry at this moment? Can you provide some valuable insights into current trends and developments?
JE: I would highlight three significant trends facing the industry right now –our ability to plan, commit, and deliver long term infrastructure; the challenge to attract inward investment and commercially fund and manage major programmes and projects; and the need and demand to do this more sustainably and with greater benefits to communities.
Each is a complex challenge on their own, but the fact they’re intertwined means we need to address these trends simultaneously and the huge pressure on industry.
We saw this play out recently with Chancellor Rachel Reeves’ decision to cancel the Stonehenge tunnel project. The cancellation of this £2 billion initiative, originally approved by the previous Conservative government, raises critical questions about how we prioritise and fund essential infrastructure initiatives while balancing development with environmental concerns and community needs.
This decision, alongside the delayed decision regarding the Lower Thames Crossing and the uncertainty over
the extent of the HS2 project, all have significant implications for the infrastructure sector.
Our decision-making process and commitment to projects is framed against the Chancellor’s statement – “if we cannot afford it, we cannot do it”.
However, recent market intelligence has highlighted a £700 billion infrastructure spending shortfall, so I think we are now at the point where we need to be asking – “can we afford not to do it?”. The long-term impacts on our infrastructure, economy, and communities are only compounding.
As an industry, it illustrates the urgent need for innovative financing and investment strategies to address gaps in funding for vital projects, which have been exacerbated by rising costs and competing fiscal demands.
The current government has made a number of commitments to a future greener economy, and as an industry we need to continue to respond. Delivering new infrastructure and preparing and repurposing existing assets and networks to meet environmental, social, and governance (ESG) commitments and deliver benefits to stakeholders adds another lens at the start and throughout the delivery and operation of infrastructure.
MO: What important role does infrastructure play in meeting the diverse needs of current and future generations?
JE: By improving infrastructure, we create lasting community benefits and make our water, energy, and transport assets and networks sustainable for generations to come.
It’s arguable that we have never faced greater demand and challenges on much of our critical national infrastructure, and as an industry and economy we must rise to the test.
When we talk about infrastructure, it’s essential to recognise that it
should serve both immediate needs and contribute to long-term benefits and be sustainable and resilient to future demands.
Many effective infrastructure projects are designed to achieve one or more Sustainable Development Goals (SDGs) over the long run. This means that it goes beyond mere construction; it is developed with clear social, economic, and environmental objectives in mind.
To effectively manage or mitigate any potential adverse impacts, these projects are commissioned with robust institutional mechanisms, adopt international best practices, and bring best-in-class expertise and innovation throughout the project and via their supply chain.
It also involves a clear business case and objectives and stringent monitoring of the triple bottom line criteria – social, economic, and environmental – throughout the entire project lifecycle.
JE: While the two sectors are intrinsically interlinked, one of the most critical aspects of how manufacturing is dependent on infrastructure is the transportation network.
Reliable systems – such as roads, railways, ports, and airports – are vital for moving raw materials to manufacturing sites and distributing finished goods to markets. Efficient logistics reduce costs and improve delivery times, both of which are crucial for maintaining competitiveness in today’s global market.
Sustainable transportation solutions also play a significant role in minimising the carbon footprint associated with transporting goods. Moving goods by rail, for example, is more carbon efficient than other transport modes.
“WHILE THE TWO SECTORS ARE INTRINSICALLY INTERLINKED, ONE OF THE MOST CRITICAL ASPECTS OF HOW MANUFACTURING IS DEPENDENT ON INFRASTRUCTURE IS THE TRANSPORTATION NETWORK”
– JONATHAN EDWARDS, EMEA MARKET DEVELOPMENT LEADER, GHD
Rail freight produces 76 percent fewer carbon emissions per tonne than heavy goods vehicles, and shifting a greater proportion of freight from road to rail will be key to ensuring the resilience and sustainability of infrastructure. Beyond transportation, manufacturing also relies on other essential infrastructure components. Utilities, including water and energy supply, must be dependable and sustainable to support production processes.
Efficient waste management systems, for example, are crucial for minimising environmental impact and
ensuring compliance with regulatory standards.
MO: How is the critical relationship between infrastructure and manufacturing evolving?
JE: The critical relationship between infrastructure and manufacturing is undergoing a transformation characterised by digital integration, sustainability priorities, and the adoption of advanced manufacturing techniques.
The rise of smart technologies and the Internet of Things (IoT) is transforming manufacturing
operations by enhancing real-time data collection and analysis. This integration enables manufacturers to optimise logistics, streamline supply chains, and improve overall operational efficiency.
For instance, advancements in GPS not only enhance asset tracking but also contribute to the timely delivery of raw materials and finished goods, supporting smoother manufacturing processes.
The need for sustainable manufacturing practices is also reshaping infrastructure priorities, as there is growing demand for greener transportation and energy solutions. This shift is driving investments in sustainable transportation networks and renewable energy infrastructure, which are essential for minimising emissions associated with logistics and production.
We are also seeing the evolving relationship with off-site manufacturing. Modular construction, 3D printing, and the integration of advanced digital technologies, along with data-driven decision-making, are enhancing supply chain optimisation. These innovations reinforce circular processes, prioritise operational efficiency, reduce waste, and drive high-level productivity.
MO: Why is it important to understand this relationship in order to make the right investments in infrastructure?
JE: First and foremost, an understanding of the relationship allows for optimising resource allocation.
By recognising how infrastructure impacts manufacturing processes, policymakers and investors can allocate resources more effectively. Equally, by targeting funds where they will have the most significant impact, stakeholders can ensure that their investments drive economic growth and strengthen competitiveness.
The relationship also has a very visible impact on regional development, employment, skills and training, and community connectivity.
In the UK, the landscape of infrastructure investment is a blend of public and private funding – this ownership model highlights the diverse approaches necessary for effective infrastructure investment.
Ultimately, the government and companies must walk a tightrope to make the right investment decisions every year and they do so in light of competing priorities and internal, external, domestic, and international pressures.
When they make the right decision, the benefits are seen and felt, but when they don’t or we see major disruption, like canal blockages, geopolitical issues, and problems in the supply chain and manufacturing process, they can have an enormous impact on investment decisions.
Given that manufacturing and infrastructure investments have long lifecycles, today’s decisions will shape the economic landscape for generations.
By anticipating future needs and challenges, stakeholders can
ensure that their investments are resilient and adaptable, mitigating risks associated with technological disruptions, demographic shifts, and environmental change.
MO: Finally, how do you see the future of the infrastructure sector developing?
JE: Changes in technology are significantly transforming infrastructure and manufacturing, reshaping production processes, operational efficiency, productivity, and supply chain dynamics.
Emerging technologies such as renewable energy sources, smart grids, and battery storage are changing how energy is produced, supplied, and consumed. This technological shift is vital for manufacturing – as industrial
power users increasingly apply the ability to predict energy demands and manage supply through smart grids, manufacturers can optimise production schedules and reduce costs, ultimately boosting productivity.
We cannot, and companies should not, ignore the huge demands they are placing on our water network now and in the future. Meeting this demand against a backdrop of climate change and increased public consumption is another area where the relationship will need to change.
GHD’s Digital Twin Operations (DTO) technology is an example of how technology is transforming the infrastructure sector. By integrating various smart technologies into a virtual environment, GHD DTO enables users to inspect, manage, and report on multiple assets from anywhere in the world.
Data modelling is particularly vital in transportation mobility. Rapid advances in generative artificial intelligence (AI) allow the creation of new data patterns to simulate scenarios, such as modelling potential traffic patterns under different conditions including population growth or road infrastructure changes.
Through AI, applying quantitative data to manage and optimise train timetables is another example which will keep rail on track.
It’s no secret that advances in technology have the capacity to radically alter the face of infrastructure and its relationship with manufacturing.
Both industries are prone to disruption, but new and emerging technologies and the use of data have the potential to offer ground-breaking opportunities.
However, companies across both industries need to do more to evolve with change, build resilience in their assets and companies, and most critically, not wait for a ‘silver bullet’ to solve the problems we face now or can see coming over the horizon.
Behind the scenes, Halloween is both lucrative and scary. We unwrap the trick-or-treat business and discover how retailers reap the rewards and manufacturers handle increasingly early deadlines, which can be a logistical nightmare
Writer: Rachel Carr
The time of All Saints’ Eve, also known as Halloween, is almost here.
While most people are just starting to consider it, the manufacturing industry has been diligently preparing for this time of year for quite a while.
The origin of the horror-themed holiday can be traced back over 2,000 years to an ancient Celtic festival called Samhain.
In the 1920s, it became more community-oriented with town-wide parades, however it wasn’t until the 1950s that it became commercialised and more closely aligned with how people celebrate it today.
This has led to a shift in focus from its traditional significance to a more consumer-driven event.
The pagan tradition that originally
signified the transition from summer to the darker months of the year has transformed over time into a widely celebrated event filled with extravagant costumes, delectable sweets and treats, elaborate decorations, themed homeware, and a variety of immersive experiences, all of which call for an array of props.
The US is the largest manufacturer of Halloween merchandise, and over the past two decades, the enthusiasm for the macabre fun has spread around the globe, with numerous countries now also embracing spooky season.
In 2023, the National Retail Federation (NRF) projected that spending on Halloween would reach a record high of USD$12.2 billion in the US alone.
As demand increases, retailers prepare to stock their shelves earlier than ever, with the season unofficially beginning in July. This has led factories to ramp up production both in terms of volume and time.
Over time, there has been a rise in innovative methods to spook people who are out and about during Halloween, with animatronic decorations emerging as a flourishing facet of the manufacturing industry.
One iconic pop-up shop founded in 1983 – Spirit Halloween – has become a seasonal institution whose stores are more popular than ever across the US.
While the brick-and-mortar displays are only open from the beginning of August until the start of November, the website is available all year round.
One manufacturer that produces stock exclusively for Spirit Halloween is Gemmy Industries (Gemmy).
The Texan company is a leader in
innovative seasonal décor known for brands such as Airblown® Inflatable, which changed how the US decorates for the holidays, as well as LightShow® and Big Mouth Billy Bass® – a personal favourite of the late Queen Elizabeth II.
Gemmy’s cutting-edge products, designed and developed with the latest technologies, received an upgrade in 2017 that allowed them to become app-controlled. This enhancement resulted in captivating light shows and made them compatible with smart devices such as the Amazon Echo and Google Nest.
Yard decorations have become a standard feature for various holidays, especially Gemmy’s gruesome and eerie products, which have also been featured in horror movies.
Consumers and film studios are not the only ones who buy scary props and décor. Retailers also incorporate the theme into their marketing strategies by cultivating the holiday spirit and autumnal ambience, using
certain phrases like “scarily good deals”, “spellbinding prices”, and “all treats, no tricks” to create a buzz around Halloween.
Halloween costumes can be pricey, with around 80 percent made from inexpensive materials like polyester, often originating from China.
In our disposable society, costumes are often used only once and end up in landfills due to non-biodegradable materials like feathers, fake hair, and plastic parts, only contributing to the spectre of sustainability.
Environmental matters are a major focus in the retail sector, and Halloween is no exception. With the increasing production of holiday-related products and growing participation, consumers are becoming more eco-conscious, and companies are promoting biodegradable alternatives in response.
Reusable decorations and costumes made from recyclable materials are now available, and many revellers are even creating their own.
As well as costumes, Halloween is synonymous with sweets and chocolate, which are mostly purchased in the six weeks leading up to Halloween. Therefore, some manufacturers prepare up to a year in advance to meet this fluctuation in demand for seasonal stock.
In 2022, Hershey’s CEO reported that the company was unable to meet consumer demand despite producing more chocolate treats than ever. Production for that year started in the spring, but there were capacity constraints.
In the previous year, sales returned to normal levels after the COVID-19 pandemic. However, issues such as the Ukraine conflict, ingredient shortages, labour limitations, and increased transportation costs have led manufacturers to pay more to meet demand.
Forecasting is crucial for inventory management because if sales fall below expectations, manufacturers must quickly find new distribution channels before 1st November to prevent a sharp drop in product value.
Known as the Golden Quarter, the busiest time for retailers starts on 16th September, 100 days before Christmas. However, many holidays, including Halloween, are now rooted in consumerism rather than tradition. Even one of the most important cultural celebrations in Mexico, Día de los Muertos, which translates to Day of the Dead, has been influenced by the phenomenon.
Traditional imagery associated with the holiday, such as sugar skulls and skeletons, has become commoditised and sold in stores worldwide as retailers try to carve out a presence in the market.
Social media also significantly
influences trends, leading to an earlier presence of Halloween on feeds and in stores each year. This extended selling period also begins to impact the Christmas season.
Unlike the family-focused festive months, Halloween capitalises on themes of self-expression and novelty. Fuelled by social media hype, nostalgia, and a yearning for escapism, Halloween has transformed from a one-day celebration to a season-long retail extravaganza, a change evident in consumer behaviour.
The emerging trend of ‘Summerween’ featuring pumpkin spice-flavoured everything – with Starbucks releasing its famous lattes at the start of August this year –illustrates that Halloween is becoming a creeping phenomenon, reflecting a
shift in consumer behaviour and retail strategy.
With Halloween preparations increasingly resembling Christmas, the holiday seasons are blending, presenting the manufacturing industry with a mix of challenges and opportunities.
Effectively navigating supply chain pressures, fluctuations in seasonal employment, and unpredictable consumer demands often necessitates using technology to adapt to the significant impact of the holiday season on the manufacturing industry.
Having a well-defined operational strategy is essential, as inadequate planning and a lack of comprehension of the seasonal market can return to haunt manufacturers long after the pumpkins and paraphernalia have vanished.
• 40 percent of UK consumers buy pumpkins to carve for Halloween, and 60 percent don’t produce any food from the wasted product, meaning the equivalent of 360 million portions of pumpkin pie are thrown out.
• In the US, over 5.4 million kilogrammes of textile waste are produced by manufacturers and consumers throwing away Halloween costumes.
• The NRF estimates that around USD$3.6 billion is spent on sweets and chocolate for Halloween.
• In the UK, Halloween spending is expected to reach over £1 billion this year, rivalling Christmas as a critical retail period.
• Around 76 percent of US pet parents like to dress their fur babies up for Halloween and other fall occasions, and a whopping 82 percent decorate their homes.
• According to the NRF, 47 percent of survey participants begin their sinister shopping activities before October.
• Over three-quarters of those participating in Halloween festivities intend to buy decorations, a figure that has continued to increase in the past five years.
• In the UK, Halloween is the third most popular holiday after Christmas and Easter, respectively.
Aproduct is only as good as its performance in the field. The ATMOS system, designed and manufactured by Core Systems, has been rigorously tested and deployed in some of the most challenging environments. This article explores how ATMOS is being used in real-world military and industrial applications, demonstrating its reliability and effectiveness in critical situations.
Real-World Deployment: ATMOS has been successfully deployed in various military operations, where its rugged design and reliable performance have proven indispensable. From remote field operations to highstakes missions, ATMOS has been a key component in ensuring mission success.
ATMOS has been successfully deployed in military field operations, where its rugged design has proven essential. One example is its use in remote command units, where its onboard UPS battery backup has ensured uninterrupted command and control during critical missions.
Additionally, ATMOS has been used in mobile data centers, providing reliable highperformance computing in rapidly changing environments. Feedback from users has highlighted the system’s durability and reliability under pressure.
Field Performance: The true test of any product is how it performs under pressure. ATMOS has consistently met the demands of military and industrial users, delivering reliable performance even in the most extreme conditions. Its advanced features, such as secure communication systems and enhanced durability, have made it a trusted tool in the field.
ATMOS has consistently delivered 100% uptime in some of the world’s harshest environments. Users in the military have noted that the system remained operational even during power outages and extreme temperature changes.
In industrial settings, ATMOS has performed flawlessly in conditions involving high dust levels and vibrations, such as those found in mining operations.
Case Studies: To illustrate the impact of ATMOS, we present two cases where the system has been critical to the success of military or industrial operations. These examples showcase the system’s robustness, reliability, and the strategic advantage it provides to our clients.
One case study involved the deployment of ATMOS in a remote military base, where it was used to process real-time data for battlefield decision-making. Its modular design allowed the system to scale from a single node to a full stack of five nodes, enabling real-time analytics with increased computational power.
32 Intel® Xeon® Gold Cores, 64 Total Threads per node
• 512GB DDR4 ECC RAM
• Dual 1.92TB NVME Hot-Swap
SSD Drives (OS Drives)
Dual 15.36TB NVME Hot-Swap
SSD Drives (Storage)
• NVIDIA L4 Tensor Core GPU Card
Another example is from the oil and gas sector, where ATMOS was used to control critical equipment in offshore operations, withstanding extreme weather conditions without issue.
Future Applications: As military and industrial needs evolve, so too does ATMOS. Core Systems is continuously refining and adapting the system to meet the emerging challenges of the defence sector. Whether it’s in the battlefield or in industrial environments, ATMOS is ready for the next generation of challenges.
Looking ahead, Core Systems is exploring how ATMOS can be integrated with AI-driven analytics for faster and more accurate decision-making in the field.
Enhanced cybersecurity features are also being developed to protect sensitive data during highrisk operations.
The scalability of ATMOS will also support its use in emerging fields such as space exploration and cyber defence.
Trailers have been a mainstay of the Australian manufacturing and transport industries for decades, offering dynamic opportunities for an abundance of businesses across the nation.
“The boundaries of the country’s transport sector have always been pushed and stretched when it comes to the productivity and design of trailers. For this reason, it is the most talked about, respected, admired, productive, and efficient
We speak to Krueger Transport Equipment’s leadership team about the company’s pioneering designs, commitment to the highest standards of trailer manufacturing, and dedication to achieving customer satisfaction
Writer: Lucy Pilgrim | Project Manager: Nicholas Kernan
transportation landscape in the world,” opens Kevin Dennis, CEO of Krueger Transport Equipment (Krueger).
Indeed, no other country moves as many tonnes (t) per kilometre than transport operators in Australia. Moreover, with the increasing adoption of performance-based standards and the introduction of electric vehicles (EVs) and hydrogen technology, the nation continues to be a frontrunner in the international
Positioned at the forefront of this global landscape, Krueger has maintained its reputation of operating as a premium brand since its founding over 45 years ago.
The company’s capabilities as a leader in innovation and quality are evidenced by the fact it has built over 20,000 trailers in the last four decades, with 14,000 still registered and active today.
“Our commitment to excellence,
reliability, and customer satisfaction has solidified our position as a powerhouse in the Australian transportation market,” Dennis prides.
Krueger’s trailers have become the product of choice for leading logistics organisations across the country as the brand has continuously grown to encompass numerous subdivisions, including but not limited to Krueger National Spare Parts and Advantage Trailer Rental (ATR).
“Our brand voice in the market has never been stronger as we integrate into all the newest marketing channels to create a larger, wider, and more diverse audience who will follow our story and see our quality on a national and global scale, even if they are not in the transport industry,” Dennis expands.
Regarding National Spare Parts, the division stands apart from typical comparable branches. With over 14,000 items in its inventory, the business can support trailers outside of the usual portfolio by offering high-quality products from some of the industry’s top brands, alongside trusted aftermarket services.
“This extensive offering enables our service teams to work on virtually any type of semi-trailer, regardless of the brand. This internal collaboration strengthens the Krueger brand beyond manufacturing, providing value to a diverse array of customers,” opens Ben Raudino, National Spare Parts Manager and Branch Manager for Victoria.
As part of his role in overseeing the Krueger branches in New South Wales and Brisbane also, Raudino works closely with suppliers to secure
competitive pricing and ensure that the division remains a strong player in the market.
ATR, meanwhile, contributes to Krueger’s brand success in multiple ways. First and foremost, the division provides a comprehensive rental service, offering a wide range of semi-trailers including skeletal trailers, fridge units, and curtain siders, available in both A and B combinations. This flexibility allows the division to cater to its customers’ diverse requirements.
The division presents tailored options that not only meet its customers’ current needs, but also provide the flexibility to support their future growth and opportunities.
On top of this, ATR supports customers when their trailers are in for service or repairs, ensuring that they stay on the road without disruption.
“Our strong after-sales service is something customers frequently praise, as we understand the critical importance of keeping their assets fully operational. We know the pressure they face to avoid downtime, since freight never stops,” David Raffaele, ATR’s Rental Manager, comments.
Furthermore, with the constant turnover of trailers, ATR also assists customers looking for second-hand purchases and ensures they find the right solutions for their needs.
This same ethos is replicated by Krueger’s National Services and Warranties division, which guarantees customer satisfaction in the maintenance and repair of all heavy trailer models, not limited to Krueger vehicles.
“Tailoring to the individual needs of customers, the business provides prompt service and support for warranty claims and repairs. This reliability fosters customer loyalty
and long-term relationships,” Service Manager for Victoria and Warranty Coordinator, Brett Tweedly, tells us.
Tweedly’s role at Krueger is to ensure that all workshop operations run smoothly and efficiently by managing maintenance, repairs, and customer requirements.
“My duties include maintaining high levels of customer satisfaction by ensuring timely and effective service delivery, managing costs, and upholding the company’s reputation through after-sales support,” he adds.
Krueger was established from Founder John Krueger’s personal need for greater trailer capacity whilst building his first trailer in his driveway at home in Melbourne’s West. Unexpectedly, John’s endeavours resulted in a design with unmatched efficiency and convenience.
“As far as I knew, there were no truck and trailer combinations in
Australia at the time that matched my rig’s capacity. The longest trailers available were 36 feet (ft), capable of carrying only one 20ft container or 36 general pallets.
“Therefore, the fact that my rig was able to carry two 20ft containers sparked a change in the industry,” John recalls.
The construction process for his specialised trailer-truck combination took six to nine months and involved rigorous testing, undergoing several design changes to ensure that it was easy to tow and could be effortlessly reversed onto docks for loading and unloading shipping containers.
Once the crucial aspect of trailer manoeuvrability had been achieved, thanks to the modification of a 20ft chassis to form a 10ft axle spread, John began to work on a more seamless method of decoupling the trailer from the truck.
Meeting this objective meant that he could reverse the trailer into the
Family owned and operated, Trailer Gates Australia (TGA) is committed to the design and manufacture of high quality, made-tomeasure truck and trailer gates – produced right here in Australia, from locally sourced steel and aluminium.
When current owner of TGA, Duncan Stewart, took over the business in January 2023, his plan was to really shake things up. And he’s done just that, placing a greater focus on the quality of materials used and on providing exceptional customer service.
In TGA’s biggest change to date, the company has moved away from cheaper imported Chinese steel and now exclusively uses quality Australian Bluescope Steel and Capral Aluminium for all its products.
“At TGA, we’re not focused on cost-cutting, instead we’re focused on onshoring –bringing jobs back to Australia. By building with Australian steel and aluminium, it keeps more locals in jobs and keeps the money here in Australia too,” explained Stewart.
“Some of our main competitors offer inferior products imported from overseas; and although these trailer gates might be a little cheaper at the outset, they don’t have the same level of quality and durability that you’ll find in every gate that leaves TGA’s warehouse.”
TGA’s truck and trailer gates are typically made to order, however TGA also offers a range of off-the-shelf gate sizes too, with no wait time.
“We provide a range of services and can custom make any sort of gate for trucks and trailers from heavy duty load racks to lightweight alloy gates, or flat tray tautliners. We build gates for everyone,” Stewart added.
With customers located across the country, TGA ships out hundreds of truck and trailer gates Australia wide, every week.
TGA boasts an impressive list of clientele including major trailer manufacturers.
Some of its major customers include Krueger, MaxiTrans, MaxiParts, Hunter Express, Drake Group, Freighter, Alltruck Bodies, Shepparton Body Builders, Beavertail Trailers, Border Express, Mainfreight, West-Trans, TR Group, NE Engineering, Combined Truck Bodies and Alma.
TGA currently employs seven people, including highly qualified master welders, who specialise in galvanised steel and alloy. Their expertise helps ensure quality is maintained through every stage of the production process.
Based in the Melbourne suburb of Thomastown, strategically located just off the M80 Ring Road, the facility has plenty of room onsite, offering easy truck access, even for B-doubles.
In just over a year at the helm of his new business, Stewart’s leadership has already had a major impact on quality and service –and the future is looking very bright.
“It’s exciting times ahead for us here at TGA,” said Stewart, as he revealed his next big move for the business. “Within the next 18 months or so, we’re also planning on moving towards robotics, which will lead to greater precision, and a greater capacity to deal with larger clients. We believe that by investing in this high tech machinery, we’ll be able to double our current output.”
TGA is ready and capable to take on new clients, including major trailer and truck body builders. Wholesalers are also welcome to contact the team.
For more information, please call 03 9465 3225 or visit trailergatesaustralia.com.au.
www.trailergatesaustralia.com.au
From the company’s ownership and senior management team through to every employee on the factory floor, there is a shared commitment to delivering excellence in goods and services. This dedication is the driving force behind Krueger’s meticulous attention to detail and constant pursuit of quality and innovation.
“My general day-to-day involvement is less than it has been in the past, hence why I have a comprehensive senior management team.
“However, I still involve myself with the engineering team and enjoy the journey of continuous improvement, including upgrading our designs, reviewing raw materials, and working in the background with the sales team and senior management to ensure we meet our customers’ expectations,” John tells us.
“KRUEGER HAS ALWAYS PUT ENGINEERING FIRST, CLOSELY FOLLOWED BY MANUFACTURING EXCELLENCE”
– JOHN KRUEGER, FOUNDER, KRUEGER TRANSPORT EQUIPMENT
next bay, allowing it to be loaded simultaneously with the truck. This doubled the productivity of the trailer, which typically would only be able to transport one container per trip.
Therefore, John’s innovative, firstof-its-kind design marked a turning point in the trailer manufacturing sector.
However, he faced difficulties when the manufacturing company he was working with to create the trailer faced pressure from other drivers over how much he was earning from his innovative modifications, ultimately resulting in the trailer no longer being permitted for use.
“Despite facing setbacks and ultimately parting ways with the organisation that restricted my trailer’s use, I found new opportunities
through subcontracting and witnessed the fruits of my labour seeing local businesses flourish,” John reflects.
Subsequently, after finding that there was not enough work in subcontracting alone, he sold the trailer-truck combination and placed his focus on growing Krueger as a business.
“Though my time as a trailer builder and owner-driver may have come to an end, the lessons learned and the legacy I created live on in the evolution of Krueger.”
John’s pioneering design and subsequent creation of Krueger was inspired by the constant issues he
faced as an owner-driver, witnessing first-hand the numerous safety challenges and operational difficulties associated with towing various brands of skeleton and open flat top trailers.
Indeed, the former proved to be one of the most perilous to drive for John due to issues with excessive rear sloping, leading to cargo instability during loading and unloading and the trailer nosediving to the ground when connected to forklifts.
Additionally, he found that the chassis design of skeleton trailers led to uneven weight distribution between axles, increasing the risk of roll-overs, particularly when navigating corners.
Meanwhile, open flat top trailers, whether in tandem or a tri-axle format, also presented challenges with braking abilities and caused damage to cargo and pallets when utilising twist locks during transportation and unloading.
John’s decades of learning and experience meant that Krueger as a business could address these safety and handling concerns efficiently.
This resulted in the implementation of many adaptations such as reducing rear sloping, optimising chassis lengths
to prevent cargo falling out when the container doors are opened, altering landing leg designs and placements to stop trailers nosediving when being unloaded, and improving suspension setups to share the load across both the axles and landing legs.
Similar efforts were undertaken with open flat top trailers, where the company re-engineered the main beams of the structure to prevent the axle hopping when braking under pressure or on wet or unstable roads. Furthermore, Krueger lowered the trailer’s twist locks, resulting in fewer part replacements.
“This was critical considering the
damage I had seen to twist locks and the importance of the mechanism for holding containers that can weigh up to 30t,” John highlights.
Krueger’s improvements to both skeleton trailers and open flat top trailers subsequently became the industry standard in freight and heavy haulage, culminating in patented designs that minimised cargo damage and enhanced the overall driving experience and public safety.
From here, Krueger launched other transformations such as the Kurtainer and adopted an innovative approach to design, pushing the boundaries of well-known trailer concepts.
Lucidity Australia designs, engineers, and manufactures premium wiring, lighting, DC-DC charging and electrical systems for the Australian transport industry. Maybe a better way to summarise what Lucidity Australia does is act as a ‘Full Service Supplier’ to the transport industry for electrical solutions.
Our relationship with Krueger goes back to 2004. During these early years Lucidity was a supplier of parts, such as lights, wire harness, buzzers and other electrical components. Over time, as this relationship grew alongside the growth of both organisations, this partnership became stronger and more interconnected. Fast forward to today, Krueger and Lucidity’s relationship is as strong as ever, and our proximity to each other helps foster this relationship. Lucidity can be on site straight away for technical support, urgent parts supply and design meetings for next generation semi-trailer applications. Today, instead of parts, Lucidity manages the full trailer electrical supply in kit format which ensures all items for the trailer are included. This leads to: simplifying trailer fit-out as everything is included in one package, reduced purchasing demands as one part number deliveries a complete trailer solution, and guaranteeing everything works ‘out of the box’ via Lucidity’s unique modular harness and lighting design framework.
Further enhancements include the Lucidity Link tail lighting range where no harness is needed as the lighting simply plugs together, making installation simple, robust and quick. In summary, all aspects of Lucidity lighting, wiring, and DC-DC charging solutions are designed and tested to work in conjunction with each other which greatly simplifies trailer electrical installation. Lucidity’s lighting and wiring simplifies installations with 100 percent repeatable designs that are modular, versatile, and adaptable.
Lucidity Australia is a part of a global organisation with design and manufacturing locations in the US, Europe, Australia, and Taiwan. In 2023 Lucidity expanded its Taiwan head office manufacturing location with the opening of the third manufacturing centre of excellence, increasing capacity and capabilities.
Lucidity’s OMP product range provides robust ‘plug and play’ wire harnessing which covers the complete semi-trailer requirements, including road trains, dangerous goods, and standard trailer applications. The wire harness system integrates with Lucidity lighting and electrical systems which provide a complete electrical solution.
Lucidity Australia engages in exporting trailer electrical kits, lighting and our charging range to Europe, China and the US. This provides peace of mind to offshore equipment manufacturers, guaranteeing compliance to the necessary ADRs of the incoming transport equipment into Australia with the added benefit of relying on years of experience working in the Australian transport sector.
Lucidity Australia has seen continual year-on-year business growth, leading to significant investment in equipment to keep up with demand and the addition of new capabilities to the business. New equipment has been added across the manufacturing range, including state-of-the-art automated wire process equipment, additional moulding capabilities, a new ultrasonic welder and testing equipment, with further equipment planned for 2024 and 2025.
Lucidity Australia is a proud Australian manufacturer, supporting the Australian transport industry with passion, expertise, solutions, and really is Australia’s only true ‘Full Service Supplier’ in this sector.
Phone: +61 03 9219 4074
Email: sales@lucidity-au.com
Website: lucidityaustralia.com.au
• Real-time programmes –Ensures customers’ supply chains are fully compliant with the company’s comprehensive practices and programmes.
• Complete solutions – Provides everything needed, including servicing, repairs, and spare parts.
• Innovation – Conducts ongoing R&D and improvements.
• Options – Offers a range of semi-trailer features both for sale and hire.
• Load restraint – Guaranteed compliance with official regulations whilst increasing productivity.
• Exceptional service – Provides professional, hands-on, and personalised customer service.
“Our commitment to a forwardthinking philosophy is underscored by our successful patenting of products such as Slide-a-Gate, addressing local restraint issues and earning accolades for occupational health and safety.”
The ability to produce high-quality engineering and designs is the backbone of Krueger. Since its inception, the company has prioritised R&D, laying the groundwork for its stringent policies and procedures.
Moreover, the business conducts thorough testing of raw materials and components to identify any potential weaknesses before they impact its products in real-world scenarios, thus avoiding unwanted risks for its customers and the general public.
“Krueger has always put engineering first, closely followed by manufacturing excellence,” John asserts.
“Ever since I started employing fulltime engineers, I’ve ensured that we always stay up to date with the latest trends, techniques, and processes whilst guaranteeing we build safe, high-quality trailers that are made to last, offering exceptional resale value to our customers.”
Indeed, John has created a culture of excellence and quality throughout the company, as he ensures that each Krueger trailer is designed and engineered to not only meet but exceed customer expectations.
“Before my time at Krueger, John was extremely hands-on in creating the strategy and procedures for the engineering department, and these are the core values that my team and I work by today,” echoes Adis Selmic, Manager of Projects and Production Engineering.
Therefore, regardless of design complexity, the company’s engineering team tirelessly works on new ideas and components, ensuring that each trailer
In an industry driven by innovation and constant evolution, the partnership between Velocity Tyres, Krueger Transport Equipment, and O’Green has emerged as a model of enduring success and collaboration.
Since their alliance began in 2015, these companies have exemplified how mutual respect, and shared values can foster remarkable growth and achievement.
“Our business philosophy centres on growing alongside our customers. We understand that if our customers do not have the support they need to evolve and advance, we too cannot achieve growth.
Available in sizes: 11R22.5, 275/70R22.5 and 255/70R22.5
Over a decade of partnership with Krueger has presented numerous challenges, but our commitment to this collaborative approach remains unchanged. We view ourselves not just as a supplier, but as an essential contributor to Krueger’s ongoing success.”
With shared business fundamentals, Velocity Tyres and Krueger Transport Equipment remain focused on future innovations, leveraging O’Green’s high-performance products to enhance their offerings. O’Green specialises in sustainable, eco-friendly solutions that meet the rigorous demands of the transport industry. Their products not only align with current environmental standards but also provide exceptionally durability and efficiency, setting new benchmarks for performance.
“We recognize the pressures faced by manufacturers like Krueger to innovate and continuously evolve their products. We believe that addressing these challenges is a shared responsibility. Consequently, we collaborate closely with our manufacturing partners to regularly update our offerings, ensuring that our customers can deliver tailored solutions to their markets.”
As they celebrate a decade of successful partnership, Velocity Tyres, Krueger Transport Equipment and O’Green continue to view each other as integral partners rather than mere suppliers. Their commitment to mutual growth and innovation promises to drive further advancements and achievements in the transport industry.
Available in sizes: 11R22.5, 275/70R22.5 and 255/70R22.5
Available in sizes: 11R22.5, 275/70R22.5 and 255/70R22.5
Available in sizes: 11R22.5, 275/70R22.5 and 255/70R22.5
produced is of the highest quality.
This is further emphasised by Krueger’s dedication to keeping pace with the ever-changing needs and technical advancements of altering market demands.
“While the fundamental principles of engineering excellence have remained constant, the methods and tools used in design processes have undergone a digital revolution,” Selmic informs.
Designs are now created using state-of-the-art computer software, allowing for more precise and efficient developments. The company also ensures that these programmes work efficiently, both within the manufacturing process and in practice.
“With these changes, our dedication to quality and innovation has remained steadfast as we make sure that each trailer reflects the pinnacle of engineering expertise,” Selmic emphasises.
This commitment has not faltered since the inception of Krueger, as the company understands that its responsibility extends beyond simply producing trailers – it is entrusted with the safety and well-being of customers and the general public at large.
For this reason, Krueger refuses to compromise on quality and rejects any materials or parts that don’t meet its exacting standards.
“We recognise the importance of maintaining both our reputation
Grant Krueger, National Sales Director:
“As a second-generation member of the Krueger family, I’ve had the privilege of witnessing firsthand the legacy built by my family and particularly my father.
“Growing up around the business and working in various departments means that my engagement with the company has been hands-on and continues to this day as I lead our sales team into the future.
“Krueger’s legacy is rooted in a commitment to excellence, innovation, and customer satisfaction. My father instilled a dedication to quality and reliability into the business, setting high standards that have defined our reputation for over four decades.
“His visionary leadership and tireless work ethic have shaped Krueger into a trusted name in the industry, leaving a lasting legacy that continues to drive our success today.”
and the trust placed in us by our customers and the industry,” John acknowledges.
Steeped in a heritage of quality and innovation, Krueger ardently prioritises its customers’ needs as a fundamental ingredient to its success.
“We understand that our customers are the lifeblood of our business, as their needs and preferences are central to everything we do,” asserts Grant Krueger, National Sales Director and the son of John.
Indeed, Krueger actively listens to client feedback and continuously strives to exceed their expectations, enabling the company to develop
personalised trailers that meet their specific requirements and deliver exceptional value.
As such, the business has become a trailer industry stalwart thanks to its devotion to fostering strong client relationships built on trust and reliability and remaining the preferred choice for both large and smaller fleet owner-drivers.
Notably, Krueger would not be
able to deliver such exceptional customer service if it weren’t for its unparalleled trailer manufacturing capabilities and after-sales service through its National Spare Parts and ATR divisions.
For starters, its unwavering commitment to quality and durability has meant that the company’s trailers are built to last, with a reputation for reliability that is second to none.
“The durability and robustness of our trailers have earned Krueger a reputation for excellence that spans over four decades, with thousands still actively operating on Australian roads today,” Selmic urges.
Additionally, the company’s outstanding engineering team comprises highly skilled professionals who are equipped to tackle even the most complex design challenges.
“OUR COMMITMENT TO EXCELLENCE, RELIABILITY, AND CUSTOMER SATISFACTION HAS SOLIDIFIED OUR POSITION AS A POWERHOUSE IN THE AUSTRALIAN TRANSPORTATION MARKET”
– KEVIN DENNIS, CEO, KRUEGER TRANSPORT EQUIPMENT
Each engineer actively utilises cutting-edge two-dimensional and three-dimensional software, as well as conducting manual calculations and finite element analysis (FEA).
As a result, Krueger’s customers can rest assured that every aspect of the company’s trailers are rigorously tested and validated.
Moreover, Krueger’s comprehensive record-keeping and preservation of engineering expertise means that the same high-quality standards are maintained across the generations, especially in regard to after-sales and spare parts services.
2024 marks a year of ambition and innovation for Krueger as it is set to deliver its newly released K-Van range into full production by the end of the year, after completing many
successful piloting units with several key customers.
As a result, the company will become a major player in a new market segment as it continues to expand its product range.
Similarly, continuous improvements to its existing products are a benchmark target from year to year, which stems from decades of engineering practice and refinement processes that underwrite the recognised quality of Krueger trailers.
On top of this, the company’s recent investment in advanced technology has been a crucial pillar in the adaption of the business around the growing needs of the industry.
Towards the end of 2023 and the beginning of this year, Krueger has enjoyed major benefits from these investments, such as its newly installed laser cutting facility.
“This advanced technology has provided considerable gains in
quality, time, and efficiency, which is further reflected in our increased manufacturing quality and speed, which ultimately means we get more Krueger trailers out on the road,” insights Kevin.
Above all else, the company’s commitment and dedication to quality will remain unwavering.
“It’s what distinguishes us in the industry and has made Krueger synonymous with excellence for decades. Whether it’s engineering, manufacturing, design, or delivery, quality is at the forefront of everything we do,” John closes.
Tel: 03 8331 6100
sales@krueger.com.au
www.krueger.com.au
Alspec shines as a leading light and market trendsetter in the design and distribution of innovative aluminium systems. We delve deeper into the company’s epic journey from modest inception and innovating with purpose, to becoming a titan of the industry across five decades
Writer: Ed Budds Project Manager: Nicholas Kernan
From humble beginnings in 1974, selling swimming pool handles from the back of a Volkswagen Beetle, Alspec has grown impressively over the course of 50 years to be Australia’s most prominent and largest aluminium distributor.
More broadly, the company’s designated realm of expertise sits at the heart of the nation’s ever-expanding construction industry, which is currently experiencing a dynamic new phase driven by technological advancements and a heightened focus on sustainability.
Alspec stands out in the titanic, competitive world of aluminium systems as a beacon of innovation, sustainability, and excellence.
Today, the business is regarded as an industry leader in the design and distribution of forward-thinking aluminium systems to the architectural, residential, commercial, industrial, and home-improvement markets.
It is an exciting time for the company, with significant developments underway in the fields of smart building technologies and sustainable construction practices.
As such, Alspec is well positioned to leverage these trends, offering products that meet the demands of modern construction while adhering to stringent environmental standards.
Furthermore, as an Australianowned company, it has carved out a significant niche in the aluminium industry, equipping professionals with a wide range of aluminium systems and products designed for commercial, residential, home improvement, solar energy and industrial applications.
The company diligently serves its loyal customer base, providing comprehensive solutions for architects, fabricators, builders, developers, and renovators.
Drawing on over five decades of
experience, Alspec has continually evolved to meet the changing needs of the market, driven by a firm commitment to quality and customer satisfaction.
With locations across Australia and a network of over 800 employees, the company has become well-respected and known for its innovative approach and high standards of service. As such, the company’s in-house design, development, and testing facilities ensure it stays at the forefront of construction standards, technological advancements, and new market trends.
As a leading extruder and distributor in the downstream Australian aluminium value chain, Alspec is resolutely committed to making a meaningful impact on efforts towards combatting climate change and contributing to a more sustainably
built environment across the nation.
Thus, sustainability is not just a buzzword at Alspec; it is a core principle that guides the company’s operations and future planning.
The recent launch of its inaugural sustainability report marks a pivotal moment in the business’ journey towards environmental stewardship.
Notably, during a recent event at Alspec’s Eastern Creek National Headquarters, attended by Chris Bowen, Federal Minister for Climate Change and Energy, the company showcased its firm commitment to driving sustainable outcomes across the nation’s built environment.
Within a sustainable construction landscape, such as the burgeoning Australian space, aluminium has its specific roles to play in maintaining an environmentally-friendly economy.
In this way, aluminium stands out across a multitude of sectors but shines particularly in the realms of
building and construction for its light weight, strength, and recyclability.
Alspec capitalises on these positive attributes by offering bespoke aluminium solutions that advance sustainability across Australian construction projects.
Additionally, the metal can be recycled infinitely without any degradation in quality. This is a unique attribute that sets it apart from many other materials, which often suffer from a loss of structural integrity or quality during the recycling process.
Alongside this, aluminium’s lightweight nature and high strengthto-weight ratio contribute to energy savings, especially in transport applications. Furthermore, the company’s ongoing initiatives in energy conservation align with the metal’s intrinsic energy-efficient properties, further reducing the overall environmental impact across its numerous projects.
• Instead of finding reasons to fail, Alspec finds reasons to succeed.
• The company seeks support from others as it cannot succeed alone.
• A resilient mindset allows Alspec to approach problems with optimism.
• The business takes criticism constructively.
• Alspec is passionate about its people, process, product, and service excellence.
• Excellence is not just a value but a discipline and way of life.
• The company relentlessly seeks ways to improve and perfect all that it does whilst accepting challenges without fear.
• Keeping its people and others safe is the Alspec way of life.
• The company empowers its employees to always place their and others’ safety before profits.
• The safe execution of operations comes above all else.
• Alspec encourages its staff to communicate effectively, openly, and honestly, promising to listen to each other, collaborate, and have fun.
• The company shares responsibilities, successes, support, and a strong sense of family and community, as well as providing career opportunities through continuous training and development programmes.
• Alspec acts as a role model for others, both internally and externally, and in its stewardship of the environment.
• The company always ensures open and transparent dialogue.
• Alspec looks to lead industry competence in the reduction of its carbon footprint by embracing continuous environmental improvement initiatives for businesses.
• The company aims to eliminate non-biodegradable waste through recycling initiatives.
• Alspec always aims to exceed its customers’ expectations.
• Customer loyalty must always be earned and never expected.
• The company commits to and delivers on its promises.
• Alspec acts with absolute uncompromised honesty and integrity.
• The company abides by or exceeds relevant industry legislation and product standards.
• Alspec always adheres to the rule of law.
• The company accepts responsibility for its actions.
Dulux is proud to have all five Alspec sites fully Dulux Accredited.
By being Dulux Accredited, Alspec is able to provide an assurance of quality as they demonstrate the standards through:
• Product testing
• Factory audit
• Following specifications - including vital pretreatment and minimum coating levels
• Maintaining samples, testing results and records
Most importantly, Dulux Accreditation means Altus is able to provide Dulux Alumi Shield™ Warranties for projects.
At Dulux Powder Coatings, we are proud to have been a key partner of Alspec during their 50 years, delivering proven high-quality coatings and leading colours and finishes for their innovative aluminium systems.
But it hasn’t just been our coatings that have enabled us to be a market leader and key partner of Alspec. We partner with architects, interior designers, builders and fabricators to deliver first-class construction outcomes.
Dulux’s innovation pipeline is developed with Alspec in mind and tailored for Australian and New Zealand conditions by its ANZ Innovation Centre. This has resulted in all Dulux finishes being backed by Dulux Alumi Shield™ Warranties, providing leading durability and colour protection. This combination of leading warrantable protection, a focus on delivering products for the design community and a relationship where Dulux is a key partner of Alspec has resulted in Dulux featuring on many projects completed by Alspec, such as the stunning Cannes Waterfront project on the riverfront enclave right in the middle of Broadbeach and Surfers Paradise.
This exquisite project, designed by DBI and built by Condev Constructions, draws inspiration from the French Riviera and features Dulux Charisma Black.
Our technical expertise and colour tools allow us to provide end-to-end support to the design and construction sectors, from the architect through to the builder, to influence the specification of our coatings.
For key customers such as Altus, as a Dulux Accredited Powder Coater, they can confidently meet these specification requirements and issue Dulux warranties for the coatings to win projects.
As a colour leader, Dulux supports the market with leading specification tools so that projects are always specified with Dulux and ensures that Altus, as a Dulux Accredited Powder Coater, is chosen for commercial projects.
Dulux is always developing and innovating in this area and tools currently available include:
• Powder Coated Swatches
• Colour Walls - As a key partner, Alspec AluSpace showrooms all feature Dulux Premium Colour walls and the factory lines have new “On-line”
Colour walls
• Swatch Boxes – Our full offer of architectural swatches are available in swatch boxes for major architects and commercial specification teams
• Custom Colour Service – Dulux custom colour service is targeted to assist Alspec in winning bespoke colour projects
Dulux empowers Alspec and their customers to succeed through advice when they need it. With a key focus on the specification market and ensuring our products work at all Alspec sites, this support includes:
• Online Tools - Provide specifiers and applicators access to specifications to colour, products and technical advice including BIM assets to help generate designs with Dulux colour more easily and accurately
• Advice and Specification Consultants - With Dulux’s support it has never been easier to have powder coating enquiries answered, including product selection advice, specification requests and sample colour swatch ordering support
• Dedicated Powder Coating Commercial Business Development Managers - based in Brisbane, Melbourne and Sydney, this team are ready to assist Below is another great example of a project specified and delivered by Alspec and Dulux.
The Upper House Apartments in South Brisbane delivered a breathtaking design that balanced the extreme wind pressure the building is subjected to with the need to maximise window openings to increase natural light.
A key strength of Alspec’s building prowess is its ability to adapt designs to perfectly suit and complement its customers’ construction designs.
Across Australia, new learning and educational environments are being created by the company with a variety of spaces that are aesthetically pleasing, comfortable, and offer opportunities for important social interaction. Alspec understands that a healthy
learning space plays a crucial part in how individuals learn and develop.
Students spend much of their time looking at screens and boards and therefore often shift their focus to a window and look outside to regain focus, recharge, and hopefully feel inspired.
On top of this, the company has invested in its ability to create safe, comfortable, and welcoming living spaces in aged care facilities that require careful consideration of design
and materials for vulnerable residents.
The company’s speciality aluminium windows and doors perfectly suit these settings, offering a blend of durability, aesthetic appeal, energy efficiency, and functional benefits.
Elsewhere, Alspec’s liveable design initiative encompasses the company’s focus on the inclusion of key easy living features that aim to make spaces more accessible and safer to use for residents.
Kam Kiu Aluminium Group (KAP) is a professional Hong Kong-funded aluminium extrusion company headquartered in Hong Kong with its production base located in Taishan, Guangdong. The main products are 3C electronics, lightweight transportation, construction engineering, life optimisation, industrial production and other aluminium profiles.
Having accumulated 40+ years of experience and as it continues to forge ahead, KAP has developed into a technology-based enterprise, integrating aluminium alloy design and manufacture, mold design and manufacture, aluminium casting, aluminium extrusion, surface treatment and precision machining, which provides customers with a one-stop solution.
KAP takes technology and innovation as the driving force for development, and is committed to designing independent aluminium product solutions to meet the needs of customers.
Website: www.kamkiu.com
Email: info@kamkiu.com
Contact number: 852 2302 0808
The company’s portfolio is a testament to its capability and versatility in delivering unparalleled aluminium solutions. Some of its highlights include:
KALINDA DRIVE RESIDENCE: The modernisation of this 1960s home in City Beach, Western Australia, showcases Alspec’s ability to blend classic architecture with modern design. Expansive windows and doors from the company’s portfolio provide stunning ocean views and enhance the open-plan living spaces.
BROOKVALE OVAL REDEVELOPMENT CENTRE OF EXCELLENCE: Led by architects Hassell Ltd and completed by ADCO Constructions, this project stands as a testament to architectural innovation. The facility includes advanced training and meeting spaces, with Alspec products ensuring its structural integrity and aesthetic appeal.
THE LOCKER ROOM: This construction represents an iconic four-level venue in the Sydney Olympic Park district, designed with a keen focus on sustainability. Alspec’s products were pivotal in achieving a 5-star Green Star Performance rating.
GIPPSLAND PERFORMING ARTS CENTRE: A state-of-the-art facility that required precise window and door solutions to ensure acoustic performance and energy efficiency.
SILKY OAKS LODGE: Nestled in the Daintree Rainforest, this luxury resort uses Alspec’s framing solutions to seamlessly integrate the built space into the natural environment.
ROCKHAMPTON MUSEUM OF ART: Featuring expansive glazing that showcases heritage architecture, this project highlights Alspec’s ability to provide both aesthetic and functional solutions.
This allows for less trip hazards and an improved level of moveability for people with a disability, senior residents, individuals with temporary injuries, and families with young children. As part of this range, Alspec now boasts a selection of products suitable for a flush sill or ramped access for residential and commercial applications.
As Alspec looks optimistically towards another 50 years of success, the company’s priorities include expanding its product range, enhancing its sustainability initiatives, and continuing to lead the way in terms of innovation, determination, and longevity.
Alspec aims to achieve specific targets related to carbon reduction,
Since partnering in 2010, Alspec has been Phifer’s National Distributor of fibreglass, aluminium and specialty insect screening. Congratulations on their 50 years of innovation and service!
With over a century of experience, Schlegel stands for high quality gaskets.
From innovative custom solutions to continuous improvement of existing processes, materials and products, Schlegel offers the very highest standards for every type of aluminium, pvc, timber windows and doors.
• Brush Seals
• Polyurethane Foam Seals
• Extruded Seals
GREENCORE LOW-CARBON ALUMINIUM: Alspec’s GreenCore range represents a groundbreaking shift towards low-carbon aluminium products. With a carbon intensity significantly lower than the industry average, GreenCore products demonstrate Alspec’s commitment to reducing the company’s environmental impact.
RENEWABLE ENERGY INITIATIVES: Alspec Solar is a strategic initiative to install advanced solar panel technology across all its facilities, offering a sustainable, commercial, and environmental solution to its network of fabricators.
COMMITMENT TO THE UNITED NATIONS’ SUSTAINABLE DEVELOPMENT GOALS (UN SDGS): Alspec has committed to six of these goals, ensuring its practices align with global sustainability standards.
ETHICAL SOURCING AND RECYCLING: The company emphasises ethical sourcing of low-carbon aluminium and has implemented comprehensive recycling programmes to minimise waste.
COMMUNITY ENGAGEMENT: Alspec invests in community initiatives aimed at promoting health, safety, and well-being among employees and partners with various charitable causes.
product development, and market expansion, while its focus remains on providing high-quality, sustainable solutions that meet the evolving needs of its range of clients.
Designing and distributing aluminium systems across a number of markets and regions demands a diverse range of skills and talents in customer service, purchasing, warehouse operation, truck driving, area management, and sales and marketing.
Meanwhile, the company continues to invest heavily in R&D to ensure the latest technologies and design principles are applied to its ever-increasing range of advanced systems. This provides Alspec’s customers with fully tested systems that meet or exceed current Australian standards and deliver on fresh trends and aesthetics.
From fabricators to specifiers, working with Alspec ensures easy
access to a team of experienced and technically competent people who are aluminium systems specialists with real expertise in all facets of the industry.
The company is more than just a provider of aluminium systems, it is defined by its innovators, sustainability advocates, and trusted partners in the construction industry.
In this way, Alspec’s epic journey continues as it strives to build a more sustainable and efficient future for the built environment in Australia and beyond.
Building
Delving into the unmatched capabilities of the two divisions that comprise HighCom Group, we speak to Todd Ashurst, Group COO and General Manager of HighCom Technology, and Sally Nordeen, CEO of HighCom Armor Solutions, about how the company provides state-of-theart technological manufacturing capabilities and tailored capability solutions for both the military and industry
Writer: Lucy Pilgrim | Project Manager: Thomas Arnold
The international defence industry becomes more prevalent every day as specialist products are critically required across the world in both domestic and foreign affairs.
HighCom Group, listed on the Australian Securities Exchange (ASX), has grown over the last 40 years to become a global leader in the defence manufacturing sector, operating two distinct divisions – HighCom Armor Solutions (HighCom Armor) and HighCom Technology.
The group provides high-quality, specialist products and tailored solutions for military and law enforcement agencies whilst also expanding its global sales and distribution networks across new
markets of high-performance ballistic products and technology solutions.
Understanding a range of technologies and their integration is imperative to HighCom Group’s work, as it ensures the cohesion of its two entities.
“At the group level, the company gains process efficiencies through knowledge and technology sharing between the two divisions,” opens Todd Ashurst, Group COO and General Manager of HighCom Technology.
“Whether it’s the manufacturing process, an engineering management framework, or a technology or machine that can be utilised by both divisions, HighCom Group always aims to align the two sides of the business where practical.”
With a current focus on representing uncrewed systems and sensor payloads, HighCom Technology serves global defence and security agencies with world-leading solutions from its Canberra – the Australian Capital Territory – facilities.
This includes cutting-edge products from top-of-the-range original equipment manufacturer (OEM) AeroVironment Inc. (AeroVironment) – a US global defence supplier. HighCom Technology is the exclusive Australian representative for small uncrewed aerial systems (SUAS), including the Tomahawk Kinesis Common Control System, and non-exclusive Special Export Sales Representative for loitering munitions, alongside other ancillaries.
As such, the division’s focus on supplying global defence and security agencies highly relies on providing a complete range of services from sales to local programme, project, and engineering management, as well as systems integration, training, maintenance, composite repair and manufacture, and logistics support services.
A key HighCom Technology strength is the ability to integrate cutting-edge payload technology from Australia and overseas for the
Sally Nordeen, CEO: “Composites
One has been a long-term partner of HighCom Armor, supplying ballistic materials and composite consumables crucial to our operations.
“Over the years, the company has developed an in-depth understanding of HighCom Armor’s specific needs, maintaining a well-stocked inventory to support just-in-time (JIT) production and large-volume projects. Its commitment to weekly deliveries ensures a seamless workflow, allowing us to meet our production deadlines consistently. Additionally, Composites One’s assistance with forecasting helps us to anticipate material needs and plan accordingly.
“The partnership with Composites One goes beyond just supply; they provide experts in various areas to deliver tailored solutions for our challenges. This support includes a dedicated team for sourcing new materials and a technical sales team that excels in meeting our requirements. The company’s expertise and proactive approach make them an exceptional material source, consistently contributing to our operational efficiency and innovation.
“Composites One’s reliability and dedication have been instrumental in our ability to maintain high standards and meet production goals.”
local environment while examining opportunities to increase Australian Industry Content (AIC) through options such as local manufacture.
Heralding a 32-year stint as an Australian Army Officer, the diverse roles of Ashurst’s career have equipped him with the best skills to sharpen his strategic acumen and operational expertise.
“My background has shaped my approach to decision-making based on a structured analysis of intelligence, resource availability, risk factors, and objectives.
“The clarity of goals and execution planning is critical to success, especially in high-stake environments such as operations in conflict zones. I have found this mindset translates well to corporate strategy, particularly when making decisions about adopting or expanding technology,” he shares.
Thus, his experience and knowledge provide Ashurst with a greater understanding of the steps that need to be taken in complex defence projects.
For instance, HighCom Technology recently successfully finalised the
delivery of an acquisition contract for a mixed fleet of AeroVironment SUAS for the Australian Defence Force (ADF). This will see the division continue to deliver support services including engineering, maintenance, logistics, flying, and training for approximately four to 10 years.
This long-term contract commitment allows HighCom Technology to directly support the ADF’s mission and purpose: to defend Australia and its national interests to advance the country’s security and prosperity.
The division continues its unwavering commitment to demonstrate how AeroVironment capability product lines, including SUAS, the Tomahawk Kinesis Common Control System and loitering munitions, integrate to form a cohesive and winning capability solution.
“HighCom Technology’s goal is clear: deliver to the ADF common control across all UAS to combine with loitering munitions, thereby expanding the operational response scenarios and range, while reducing the cognitive workload of operators,” affirms Ashurst.
At the same time, the contract reinforces HighCom Group’s long-standing partnership with AeroVironment, of which it has been an exclusive SUAS partner across Australia and New Zealand for a number of years and continues to expand this relationship across a broader range of battle-proven capabilities.
Alongside supporting the ADF, HighCom Technology also supplies and supports defence, security, and law enforcement agencies across the world with leading uncrewed and control systems, as well as sensor technology.
The division continues to provide a range of services, including directly supporting the acquisition process, integrating solutions, project management, engineering, repair and maintenance services, product support, and training.
“HighCom Technology’s goal is to be the trusted partner of choice in supplying, supporting, and integrating capabilities for use by defence, security, and law enforcement agencies,” Ashurst highlights.
For example, the company continues to work closely with the Australian Department of Defence (DoD) in order to meet its current and future requirements in a rapidly changing strategic environment.
This is achieved by the introduction of a new suite of small and medium UAS products, as well as the Tomahawk Robotics’ (Tomahawk) Kinesis controller. This system is part of the Tomahawk ecosystem, an artificial intelligence (AI)-enhanced, open architecture, common control system primarily designed for warfighter aircraft.
“Built for ease of use, the ecosystem seamlessly connects the humanmachine team across the tactical network to enable the execution of
“WHETHER IT’S THE MANUFACTURING PROCESS, AN ENGINEERING MANAGEMENT FRAMEWORK, OR A TECHNOLOGY OR MACHINE THAT CAN BE UTILISED BY BOTH DIVISIONS, HIGHCOM GROUP ALWAYS AIMS TO ALIGN THE TWO SIDES OF THE BUSINESS WHERE PRACTICAL”
– TODD ASHURST, GROUP COO AND GENERAL MANAGER, HIGHCOM TECHNOLOGY
critical missions spanning intelligence, surveillance, and reconnaissance (ISR) to lethal effects,” explains Ashurst.
On top of this, HighCom Technology is excited about representing the Switchblade® 300 and 600 loitering munition systems on behalf of AeroVironment.
Both are man-portable systems that are combat-proven to enhance soldiers’ capabilities in precision flight control, provide greater lethality against fortified targets such as armoured vehicles and tanks, and improve the ability to track and engage moving non-line-of-sight targets.
Given that the Australian government recently publicly announced the acquisition of the Switchblade® 300 precision loitering munition system, which will be delivered in late 2024,
HighCom Technology looks forward to continuing to represent and demonstrate AeroVironment’s capabilities to the DoD.
The same commitment to the advancement of international defence capabilities is reflected by HighCom Armor, the group’s twin division, that designs, develops, tests, manufactures, and distributes state-of-the-art armour and personal protective equipment (PPE) worldwide.
With a 63,500 square foot (sqft) manufacturing and distribution facility in Columbus, Ohio, the division is wellpositioned to meet large-scale and time-sensitive global supply needs. HighCom Armor products include
Ohio’s military defence industrial complex is exceptionally well-positioned due to several key factors that make it a hub for manufacturing and distribution:
STRATEGIC LOCATION: Ohio’s central location in the US makes it a prime hub for distribution and allows military contractors to efficiently deliver products across the country, particularly given the state’s robust infrastructure network.
SKILLED WORKFORCE: Ohio’s deep-rooted manufacturing tradition offers a skilled workforce well-versed in precision manufacturing and advanced engineering – both characteristics that are essential for producing militarygrade equipment.
DIVERSE INDUSTRIAL BASE: The state’s strong presence in industries such as aerospace, automotive, and advanced materials supports the defence sector’s diverse needs, fostering innovation and collaboration.
BUSINESS-FRIENDLY ENVIRONMENT: Ohio offers a competitive tax structure, incentives for manufacturing, and a pro-business regulatory environment, making it attractive to companies looking to invest and grow.
ENERGY RESOURCES: The state’s access to affordable and reliable energy resources, including natural gas, helps maintain lower operational costs for defence manufacturers, making Ohio an economically viable location for largescale production.
GROWING ECONOMY: Ohio’s defence sector is an integral part of its overall economy, contributing significantly to both state and national security. The government’s commitment to expanding this sector ensures a steady demand for military goods and services.
armour plates, plate accessories, soft armour, helmets, shields, and carriers.
Moreover, the division’s vertically integrated approach to ballisticresistant product engineering and manufacturing enables it to maintain strict control over costs and material quality, ensuring that its products consistently exceed the missioncritical demands of end users.
Indeed, Highcom Armor delivers comprehensive capabilities for inspecting, testing, and validating every stage of the product lifecycle, from raw materials to finished goods ready for deployment.
“This rigorous process allows us to achieve a high output capacity, producing tens of thousands of pieces of protective equipment each month,” notes CEO, Sally Nordeen.
Evidently, in just 113 days, the division successfully dispatched over 120,000 pieces of body armour to the Ukrainian Ministry of Defence.
• Extensive Inventory: Gain access to an unmatched range of high-quality composite materials and processing supplies.
• Expert Support: Access to material and process technical experts to help with efficient part manufacturing.
• Reliable Service: Ensuring the right product is in the right place at the right time.
• Unique Partnerships: Experience a partnership that’s designed to achieve your desired goals.
Scan the QR code to visit our website to start your journey towards enhanced efficiency and innovation with Composites One
HighCom Technology engaged many international partners, suppliers, and freight and logistics specialists in order to deliver the substantial order in full and on time.
“Our commitment to experience, reliability, innovation, quality, and collaboration is at the core of everything we do,” she adds.
As the armour manufacturing branch of the group, the integration of technology underpins the division’s day-to-day operations.
From teams of materials scientists and engineers to product solutions produced from its XTclave™ technology, all these inputs need to be carefully managed and integrated to meet the current demand for armour products and expand the group’s market offerings.
XTclave™, in particular, is a proprietary-patented technology
Call 816-283-3330 to connect to a Composites One expert today.
“HIGHCOM TECHNOLOGY’S GOAL IS TO BE THE TRUSTED PARTNER OF CHOICE IN SUPPLYING, SUPPORTING, AND INTEGRATING CAPABILITIES FOR USE BY DEFENCE, SECURITY, AND LAW ENFORCEMENT AGENCIES”
– TODD ASHURST, GROUP COO AND GENERAL MANAGER, HIGHCOM TECHNOLOGY
that is unique in its capabilities. The system includes tooling and system processes as well as fluids and other components that have been specifically designed for the highpressure and heat application of aerospace and armour consolidation capabilities.
The hardware manufactures ultralight, thin, and strong ballistic products highly suitable for military use, government agencies, and specialised police elements.
Additionally, XTclave™ can produce
complex curves combined with ceramic and other facing materials, yielding advanced hard armour products suitable for a broader range of body types, genders, and applications, such as aviation or vehicle armour.
“XTclave™ provides an industryleading advantage in the US market due to its ability to create complex contours and improved consolidation resulting in increased strength and lighter weight products,” Nordeen emphasises.
Australia’s engineering skills and labour shortage have reached their highest level in over a decade, which makes HighCom Technology’s positive work culture even more critical for attracting and retaining highly specialised and sought-after talent.
The division’s engineering team comprises individuals with exceptional skills and capabilities in aeronautical, electrical, radio frequency, systems, and system safety engineering.
Moreover, each member of the engineering team has a diverse background in customer engagement and management roles within the Australian DoD, which compliments their current work in the design, development, and supply of technology, thus having a greater understanding of customers’ expectations.
The team’s variety of skills and backgrounds also enable HighCom Technology to lawfully import technologies and systems into Australia in a way that is compliant with the country’s work, health, and safety legislation, particularly in cases when technologies and systems are developed by overseas partners.
“Our engineers are able to address real-world problems and improve existing systems. They drive innovation and technological advancement within the company and help solve critical problems, enhancing our customer offerings,” Ashurst prides.
In November 2023, after two years of XTclave™ operations being based in the Adelaide manufacturing centre in Australia, the HighCom Group Board of Directors made the decision to close the operation and relocate all the manufacturing processes to one HighCom Armor production facility in Ohio.
“The manufacturing of products in Australia affected our ability to penetrate the world-leading US market with our unique XTclave™made products, particularly the US DoD, which was the main, underlying reason for the facility relocation,” Nordeen explains.
The XTclave™ operation was successfully relocated from Adelaide to Ohio in early 2024, where the reassembly process commenced. This included designing a new cooling system for XTclave™ to operate outside the facility and cater to the contrasting extreme climate compared to the Australian facility.
The relocation has already generated significant interest from various areas of the US military and federal law enforcement, who are willing and eager to discover what is possible with the state-of-the-art XTclave™ technology.
For example, HighCom Armor is
maintaining a cooperative research and development agreement (CRADA) with the US Army Development Command and has also been tasked with funding a ‘special threat’ development contract with the US DoD for the R&D of selected ballistic products.
“By closely working with the US military, there is an opportunity to receive ongoing R&D income
and develop products that will go to tender during 2025, allowing HighCom Technology to compete for major contracts,” she affirms.
Going forward, HighCom Group will continue to diversify both its manufacturing and technological capabilities.
Regarding the latter, HighCom Armor will modernise its capabilities by recommissioning the XTclave™ technology while diversifying other production methods to broaden its product range across multiple markets.
“Our technology makes it possible to manufacture stronger, thinner, and lighter armour solutions. With more armour in development, HighCom Armor will focus on quality and performance as it continues to advance the market with innovative solutions,” emphasises Nordeen.
Indeed, the strengthening of the division’s armour solutions is integral to the solidification of the new US-based production facility and reinforcing the bond between the two nations.
“HighCom Group’s involvement with US-based companies and involvement in integrating their offerings into the ADF and broader security environment is certainly one of our strengths, and we continue to work towards expanding this effort because of the mutual benefits that can be realised,” Ashurst emphasises.
This mutual exchange of value is further replicated by HighCom Technology’s steadfast partnership with AeroVironment, who in turn are learning valuable lessons about employing innovative systems in the Australian context to help advance product designs.
“Knowing that through its supply activities, HighCom Technology is contributing to and supporting closer operational ties between the ADF and its key allies makes us proud and demonstrates how both countries mutually benefit each other in this regard.
“We will continue to do this by working with our commercial partners for innovative ways to explore and introduce more AIC through technology leading locally sourced consumables through to parts
manufacture or assembly,” Ashurst expands.
Additionally critical to HighCom Group’s involvement in integrating US companies into the ADF, the organisation’s activities help drive and test new initiatives such as an Australia, UK, and US (AUKUS) trilateral security partnership, facilitating an export license-free environment.
“The mutual benefits of AUKUS include stimulating innovation in our product range, accelerating advances in capability and technology, and learning from one another –particularly ways to more rapidly integrate commercial technologies to solve warfighting needs,” Ashurst concludes.
Overall, HighCom Group, together with US and Australian-based partner companies, will now be able to get capabilities and equipment into the hands of allies and partner nations’ military, police, and first responders sooner than ever before.
“We will be able to continue to spearhead similar future initiatives as a member of the defence industry for outcomes mutually beneficial to Australian and US companies, as well as allies and partner nations’ militaries, security, and law enforcement agencies,” Ashurst concludes.
As one of the world’s leading manufacturers of forestry equipment and solutions, Komatsu Forest’s ability to offer quality, peace of mind, knowledge, and support to its customers is unparalleled. Jens Bengtsson, CEO, discusses the company’s dedication to both sustainability and continuous innovation
Writer:
Lily Sawyer | Project Manager: Nicholas Kernan
Founded in 1921, global equipment manufacturer Komatsu originates from the Japanese city of the same name –home of the former copper mine, Yusenji, which was once vital to the local community’s economy.
When Meitaro Takeuchi, Komatsu’s Founder, assumed ownership of Yusenji, he became aware that the mine’s copper deposits would soon run out.
However, rather than abandoning the development, he pre-emptively funded projects to upskill the local community, including Komatsu Iron Works – a machinery company for the maintenance of mining equipment.
Today, guided by Takeuchi’s principles – quality first, technology innovation, globalisation, and development of people – Komatsu serves multiple industries as one of the world’s leading manufacturers of forestry, construction, mining, and utility equipment.
Takeuchi’s commitment to local communities remains at the company’s core, influencing everything from the way it thinks about innovation to its onboarding processes and customer relations.
“Ever since the founding of our company, it has been important that we contribute to answering the
needs of society, both today and for generations to come,” opens Jens Bengtsson, CEO of Komatsu Forest.
Manufacturing equipment and products for professional forestry use worldwide, Komatsu Forest, a subsidiary of Komatsu, headquartered in Sweden, provides end-to-end solutions throughout the forestry lifecycle.
Reflected in its evolution as a truly global company with an extensive and diverse workforce, Bengtsson believes that when the people of Komatsu are united by a common goal, the remarkable can happen.
“We believe that value is best created together, and we accomplish more when we factor people, businesses, and the planet into our decisions,” he adds.
As such, due to the rich heritage and underpinning values that the entire group has carried forward for over 100 years, Komatsu Forest is a company poised for success.
Over the years, the European forestry industry has witnessed significant evolution.
Today, sustainable forestry management and timber harvesting, such as that carried out by equipment produced by Komatsu Forest, is seen by many as a realistic solution to the use of fossil fuels and single-use plastics.
“Forestry is an essential business for the lifestyle we lead but also a major contributor to the necessary transition from fossil fuels to more sustainable materials – for example, exchanging plastics for paper or concrete for wood,” Bengtsson outlines.
The global shift towards limiting single-use plastics is very much ongoing, with raw forestry materials undeniably crucial in supplying alternatives.
However, trees themselves have also become increasingly valued and safeguarded for their role as essential contributors to
the environment, from biodiversity to climate change mitigation.
As such, a wide range of EU policies have emerged to protect European forests and sustain their environmental benefits, including the EU’s Forest Strategy for 2030, Biodiversity Strategy, Nature Restoration Law, and Renewable Energy Directive (RED).
Specifically, the Paris Agreement,
which sets out to cut global carbon emissions, directly benefits from living trees as essential mitigators of carbon dioxide (CO2).
“Standing forests are needed to sequester CO2 and thus contribute to achieving the Paris Agreement’s climate goals. As a result, we see new regulations for forestry coming into place all the time,” Bengtsson points out.
“EVER SINCE THE FOUNDING OF OUR COMPANY, IT HAS BEEN IMPORTANT THAT WE CONTRIBUTE TO ANSWERING THE NEEDS OF SOCIETY, BOTH TODAY AND FOR GENERATIONS TO COME”
– JENS BENGTSSON, CEO, KOMATSU FOREST
Could you introduce us to STIGAB Stig Ödlund AB, its locations, facilities, products, solutions, history, etc?
STIGAB’s headquarter is situated in Huddinge, just south of Stockholm. We also have a facility in Flen where we manufacture marine controls. In total, we are made up of 24 employees. We have a broad range of electrical and mechanical components and solutions for demanding applications in harsh environments, with a focus on human machine interfaces (HMI). We deliver displays, joysticks, pushbuttons, e-switches, keyboards, toggle switches, and FNR-buttons, both as separate components but also in complete solutions combining these parts and cable harnesses. STIGAB was founded in 1984 by the Ödlund family. Since 2017, STIGAB is now a part of the Addtech Group which consists of more than 130 companies.
What is the company vision, and how does it align with clients’ goals?
Our vision statement is “Through personal commitment and long-term relationships, STIGAB’s
vision is to be the preferred partner for technical solutions. With our expertise, innovation and dedication, we aim to challenge industry standards and contribute to a sustainable and efficient future”. We believe we assist our customers to reach their goals by helping them find the best possible solutions for their applications, with a focus on technical support and design ideas, technology, ergonomics, economy, and sustainability.
Following on from that, where do you see STIGAB’s future in the industry?
In these times of changes towards electrification and automation, we strive, together with our partners, to be at the forefront with innovative products and solutions. We are challenged by our customers to constantly meet new demands and techniques. STIGAB has a high focus on sustainability which is also very important for companies today. In 2024 we were awarded a silver medal by EcoVadis which reflects our commitment to environmental, social, and ethical practices.
How about the company’s relationship with Komatsu Forest? When did it begin, and what does it mean in terms of importance?
STIGAB has enjoyed a long-standing partnership with Komatsu Forest. We were supplying to Partek Forest before it became Komatsu Forest so for over 25 years! We have grown to be not only a component supplier but also a system supplier. During the development phase of the pallets we deliver today, there was a very close co-operation between Komatsu Forest’s amazing engineers, STIGAB, and the manufacturer OTTO Controls. We look forward to continuing our successful partnership with Komatsu Forest in the future.
Tell us what your cooperation with OTTO Controls entails and how vital are supplier partnerships to STIGAB?
STIGAB would not exist without the excellent support from our suppliers. OTTO Controls has been our partner for more than 25 years and we have a close relationship that aligns with our goal to be able to support our customers in the best possible way. STIGAB has been awarded their number one distributor worldwide for the last two years and we are of course very proud of that! OTTO Controls also works closely with us and when necessary, also with our customers to suggest, develop, and design customised solutions. They have extensive technological knowledge and experience and a great customer support.
Are there any exciting new plans or innovative products on the horizon for STIGAB?
Since STIGAB now has a production site for marine controls, we expect to be able to make customised solutions in-house in the future.
Apart from that, our suppliers constantly develop and release new products. From OTTO Controls, we have for example the new CAN-based keypad solution. There are also a lot of released products and many on-going development projects to fulfill customer safety demands.
To meet the challenges within automation, STIGAB continue to grow our sensor product line.
Our plan is to carry on doing our utmost to meet our customers’ needs, and through this, we anticipate delivering many new and innovative products in the future!
Website URL: stigab.se
Email address: info@stigab.se
Phone: +468970990
To fulfil its vision of being an indispensable partner to the professional forestry industry, Komatsu Forest meets its customers’ expectations with products and services of the highest quality. To achieve this, it works according to the Komatsu Way:
SAFETY FIRST – The company cultivates safety in its working environment, people, and behaviour.
QUALITY ASSURANCE – Komatsu Forest conducts extensive quality assurance assessments throughout production to ensure high-quality products.
CONTINUOUS IMPROVEMENT – The company seeks continuous improvement in all aspects of its work by following the plan-do-check-act model.
CUSTOMER FOCUS – It is important for the business to fully understand the customers’ working environments to sufficiently meet their needs.
ISO 9001 CERTIFICATION – Komatsu Forest’s structured way of working across the board has earned it ISO 9001 certification. The result of this certification is quality across all stages of production and throughout the company.
Komatsu Forest recognises how both the modern forestry industry and the safeguarding of European forests are important developments that should be supported and believes that they need not be opposing factions.
The company contributes to this equation by developing forestry solutions that can support and contribute to the environment during the full forestry lifecycle.
“For sustainable forestry that will continue to add value for generations to come, we believe that forests need to be managed and maintained considerately so that it can keep providing the valuable raw materials,” he confirms.
To achieve holistic management of the entire forestry cycle, Komatsu Forest, including subsidiaries, offer
Welcome to our “One
Together, KGK and Laitis offer complex solutions through our One Stop Shop concept. We tailor setups that deliver a complete solution, where our local presence, strong brands, expertise, smart services, and fast, sustainable logistics make your everyday life easier in industry, the forest, the mine, or on the road.
“Our common goal is to create a sustainable future.”
This fall you can maintain, calibrate, or repair your equipment, tools, and machines in our joint service center of 500 m2 in Luleå. As part of our commitment to the environment, it is a given for us to offer service and maintenance to increase the lifespan of your equipment.
“Sustainability is not just a trend – it is a necessity in today’s world.”
Smart Forestry allows operators access to a suite of digital services for a safe, smart, sustainable, and productive workplace. Comprising three different applications, Smart Forestry offers solutions for any business:
• Plan for better results
• Work from anywhere with ease
• Access all machine data in one place
• Compare fuel consumption and production
• Create monthly reports with ease
• Get remote support and updates
SMART FORESTRY VISION
• Share information quickly and easily
• Collaborate seamlessly between operators
• Monitor production in real time
• Visualise boundaries and areas on the map
• Access vital information instantly
• Make informed decisions
SMART FORESTRY PRECISION
• Facilitate work with precise positioning
• Navigate with realistic map conditions
• Work with precision in protected areas
• Follow pre-defined paths accurately
• Visualise tracks and progress
• Maximise work efficiency
start-to-finish equipment and solutions, from planting through to thinning, final felling, and logging.
Generally, there are two main methods for logging, cut-to-length (CTL) and full-tree. Komatsu Forest produces CTL machines at its production facility located at its headquarters in Umeå, Sweden.
“Forests can look very different around the world, from hardwood to softwood, to large and small stems, from natural forests to plantations, from hilly terrain to wet ground, and from thinning to final felling,” Bengtsson observes.
To cater to these differences and accommodate clients’ various requirements across the globe Komatsu Forest has developed its product line accordingly.
“For CTL, two types of machines are used in a pair,” he explains.
Komatsu Forest’s harvester, which consists of a base machine and a
harvester head attached to it, first cuts the trees to a length specified by the sawmill, before a forwarder gathers the logs and forwards them to the roadside.
The company’s suite of CTL products ranges from small, nimble harvesters to versatile all-rounders for different types of logging as well as final felling machines.
By offering a broad range of harvesters, harvesting heads, and forwarders compatible with one another, Komatsu Forest is able to provide its clients with maximum adaptability.
Furthermore, each piece of equipment can be fitted with technology and smart digital solutions designed to simplify working in the forest whilst contributing profitability and productivity.
Whilst Komatsu Forest’s vast suite of products is already considered advanced, it constantly seeks
Your reliable partner for transport, contracting, recycling and salvage in Umeå.
Ume Assistance has been part of Umeå’s development for over 50 years. The company was founded in 1967 by Jan Hansson, and has since grown to become a central player in the region in transport, contracting, recycling and salvage.
Today, Ume Assistance is run by Jan’s three sons – Martin, Magnus and Mattias Hansson – who all share their father’s passion for contributing to the city’s growth and sustainability.
With over half a century of experience, Ume Assistance has developed a deep understanding of the transport industry’s requirements and challenges. We offer services that include loading, transport and unloading, guaranteeing efficiency and precision in every assignment. Our modern vehicles and our experienced team ensure that your transports are smooth and punctual, regardless of size or complexity.
In the contracting sector, Ume Assistance has invested in a modern machine park that is ready to meet all kinds of challenges. We offer a wide range of services and equipment that can be adapted to the customer’s specific needs, making us a flexible and reliable partner in all construction and civil engineering projects.
Ume Assistance has always had a strong commitment to the environment. We have been environmentally certified for over 15 years and have extensive experience in environmental assignments and sorting. Our work in recycling aims to minimise environmental impact and promote a circular economy. We take our responsibility to contribute to a more sustainable society very seriously and are constantly working to improve our processes and reduce our climate footprint.
Salvage: Fast and safe help when you need it most
As a representative of the Assistance Corps in Umeå and Örnsköldsvik, Ume Assistance offers professional salvage and rescue services. Our team is always ready to respond and provide quick, safe assistance in the event of accidents and downtime. We have both the skills and the equipment required to handle a range of different situations, from minor breakdowns to more complex salvage missions.
With our broad range of services and our strong focus on quality, the environment and customer satisfaction, we are proud to be able to offer a comprehensive solution that meets our customers’ needs. Whether you need transport services, contracting solutions, help with recycling or salvage, we are here to help. Welcome to Ume Assistance!
When a customer purchases a new Komatsu Forest machine, they are in good hands. As standard, the company provides basic training to give customers a solid understanding for future use of their equipment. It also offers further training and simulation for an in-depth insight into the machine’s features.
BASIC TRAINING – Included as standard when a Komatsu Forest machine is purchased, this training provides customers with an understanding of the machine’s design and functions, the control system, daily maintenance, and more.
FURTHER TRAINING – The company also offers further training where requested, tailored to a customer’s specific needs. This covers anything from electrical and hydraulic systems training to control and information systems, marking for cross-cutting, methodology, troubleshooting, and more.
SIMULATORS – Komatsu Forest’s simulators offer an ideal shortcut to new knowledge and improved skills when it comes to operating machinery, featuring a built-in forest editor to create a realistic work environment. A multi-player feature enables several simulators to simultaneously educate trainees on collaborative features, whilst an instructor station allows the instructor to pause or intervene in training, record videoclips, and create comments with timestamps to advise trainees.
continuous improvements to its reliability and performance to remain at the forefront of the industry.
For example, the Komatsu C124 harvesting head has recently received significant upgrades, including a valve block and enhanced hydraulics for the feeding system.
Following the head’s recent exhibit at major Finnish heavy machinery event, FinnMETKO 2024, Komatsu Forest reports overwhelmingly positive reviews from test customers who noted its smooth operation and efficient feeding.
Sustainability has played an important role throughout Komatsu’s history and today continues to empower its vision for a sustainable future where people, businesses, and the planet thrive.
Thus, it seeks to achieve carbon neutrality across the group by 2050.
“As much as this is an ambitious target, it is very much in line with our purpose and we have a strong dedication to achieving this,” Bengtsson reflects.
One evident contribution to this sustainability target is Komatsu Forest’s new production facility in Umeå. In designing the factory, the company had two important objectives – to build a production facility that focuses on both the environment and workplace.
In accordance with the Sweden Green Building Council’s Miljöbyggnad (MB) certification system, the facility meets its Environmental Building Gold Standard, for which stringent criterion based on energy efficiency, building materials, and indoor environmental quality must be met.
“We had the privilege of starting with a blank sheet when designing our new factory, which meant we could install geothermal heating and solar cells to ensure we use renewable energy,” Bengtsson reveals.
By improving its working processes
within the facility, Komatsu Forest has been able to reduce the number of wheel loaders in operation, whilst all working vehicles are fuelled with hydrotreated vegetable oil (HVO), a fossil-free, renewable alternative to diesel – all of which has contributed to achieving carbon neutral production.
“It is rewarding to see our sustainable vision coming to life in our facility, where approximately 650 of our employees spend their working days,” he prides.
The next milestone for Komatsu Forest is reducing emissions from its machines. Whilst the concept of electrification in forestry is certainly a groundbreaking technological leap forward for the company, it also poses major challenges.
Since its machines work off-grid, there are many aspects that Komatsu Forest must consider as it sets out to develop this machinery.
“For our machines to be able to use different types of energy media, power distribution solutions will be required to achieve such a workplace in a forest setting,” Bengtsson advises.
A major part of accomplishing sustainable forestry management is maintaining an awareness of the environmental impact of the processes involved.
Naturally, practices such as logging can lead to major changes in a forest’s natural composition, which is why thorough planning must be conducted to ensure this is carried out with care.
“To facilitate both the contractor and operator with precise planning, we offer Smart Forestry,” Bengtsson tells us.
A collection of digital solutions, Smart Forestry helps contractors to perform operations in a smart, productive, and sustainable way.
Whether dealing with a large or small fleet, Smart Forestry allows contractors to utilise a large amount
“AT KOMATSU, WE SEE OURSELVES SUPPORTING THE INDUSTRY THROUGH OUR ADVANCED MACHINES AND HELPFUL DIGITAL SOLUTIONS”
– JENS BENGTSSON, CEO, KOMATSU FOREST
of data from machine operations to make informed decisions.
“Smart Forestry currently encompasses three unique applications: Smart Forestry Fleet Monitoring, Smart Forestry Vision, and Smart Forestry Precision,” he surmises.
Smart Forestry Fleet Monitoring utilises geographic information system (GIS) data and mapping technology to plan safe routes for harvesters and forwarders alike.
It also allows operators a comprehensive overview of their machines as it gathers data on fuel consumption and production, with all information logged and stored automatically.
“The ability to plan harvesting assignments remotely, alongside remote-control functions, is a major benefit.”
The Smart Forestry Vision application, meanwhile, enables operators to access layered information on a map, such as operating status, whilst it is able to share information between
functioning machines at any given site in real-time.
Last but not least, Smart Forestry Precision is the company’s newest and most advanced application, providing access to a new range of possibilities.
Utilising the latest satellite positioning technology, it can determine a machine’s exact position with a margin of error of just a few centimetres.
“By being able to pinpoint a machine’s location so precisely, functions to greatly simplify the operator’s working day have emerged,” Bengtsson excites.
For example, operators can create digital boundaries around a work area and receive warnings if a machine comes too close to this boundary, which is very useful when making nature considerations.
Furthermore, thanks to the high precision offered by this technology, machine tracks and stem codes can be visualised, showing the exact position of processed logs.
“At Komatsu, we see ourselves supporting the industry through
Olofsfors ECO-Tracks™ is the original among forest machine tracks. With over 2000 product combinations, we can deliver a product of the highest quality that fits perfectly to your machine and your conditions. Products made from 90% recycled steel and 100% recyclable. We utilize 100% environmentally certified electricity.
www.olofsfors.com
our advanced machines and helpful digital solutions,” he asserts.
Just as environmental responsibility is an essential part of how Komatsu Forest views the world and conducts its business, so is corporate social responsibility (CSR).
Both inform the ‘Komatsu Way’ – a company culture that prioritises safety, quality, and continuous improvement, and always puts the customer first.
“We aim to contribute to society by answering their needs today and for generations to come,” Bengtsson states.
Examples of Komatsu’s CSR include clearing anti-personnel landmines in Cambodia and providing community development support in the Southeast Asian country, demonstrating its strong contribution to society.
Closer to home, Komatsu Forest has focused its efforts on education, including upskilling college students.
“A little more than 10 years ago we saw a sharp decline in applications to technical colleges,” he reports.
Drawing on this statistic, Komatsu Forest recognised how its local educational institutions were not well equipped, whilst the female-to-male ratio amongst technical students was poor.
Therefore, to curb this declining trend, it made a substantial donation to a local school, Dragonskolan, so it could invest in equipment and uplift the status of its technical education.
“Our donation serves to support continuous upgrades of the school’s equipment for the next 10 years and thereafter, whilst we also offer yearly scholarships to students,” Bengtsson elaborates.
Though the scholarship programme, select students are able to visit Komatsu’s headquarters in Japan to bolster their technical education.
Over the years, Komatsu Forest has received many accolades and recognitions, including the recent KWF-Tagung Members Award for Forestry Innovation, awarded in June 2024.
“It is always rewarding to be recognised for our work and especially our innovative products, since this is an integral part of who we are,” Bengtsson imparts.
The company is also keen to emphasise the importance of its dedicated staff in achieving such awards.
“We are very thankful and consider the KWF-Tagung Members Award for Forestry Innovation as a token for all our employees’ dedication.”
Awards aside, Bengtsson points out that the best recognition the company could receive is from its employees and customers, many of whom spend most of their working life using Komatsu Forest products and machinery.
“Earning that trust and creating those long-lasting relationships is the best reward we could ever earn,” he concludes.
Going forward, the company seeks to continuously improve its suite of products, which is reflected in recent updates to the Komatsu 895 forwarder.
Its strongest forwarder yet, the Komatsu 895 combines a powerful transmission with a brand new 205F crane, capable of carrying loads weighing up to 20 tonnes.
Equipped with the newest Smart Forestry technology, the forwarder is also both durable and smart.
Smart Forestry is very much an ongoing development that continues to evolve, with Komatsu Forest implementing updated features to the suite of existing applications as new technologies come to the fore.
info@komatsuforest.com www.komatsuforest.com
are a Swedish supplier and we are experts in turning, milling and grinding of both simple and complex components with the most modern machines. We focus on the customer to meet their requirements for competence, quality, environment and flexibility.
Dafo Vehicle has over a century of experience in vehicle fire safety. Our solutions are designed to meet the unique demands of the forestry industry, providing robust protection for your equipment and personnel. As every forestry operation is unique, our fire protection systems are tailored to fit the specific
Dafo Vehicle’s systems are easy to maintain and refill on-site, reducing downtime and operational costs. We are proud to work with key OEMs in the industry, like Komatsu Forest.
A country rich in tradition and silver, the Czech Republic boasts a vast and intricate history of minting. Michal Voborník, CEO of Czech Mint, tells us more about the tradition behind the process and the ways in which the company is innovating for the future
Writer: Lauren Kania | Project Manager: Nicholas Kernan
Czech minting has a tradition of more than 1,000 years. Our country was not only rich in milk and honey – as legend has it – but also had an abundance of
“This provided an opportunity for ancient mint masters to express themselves through art which is still admired
This history, as illustrated by Michal
Voborník, CEO of Czech Mint, has empowered those at the company to be proud of the long-standing legacy that has formed the country’s flourishing minting industry.
Having been a symbol of luxury for thousands of years, precious metals have provided people with power, enabled colonies to be built and destroyed, and fulfilled the wildest of dreams.
• Suppliers of Czech coins: Czech Mint’s work is internationally recognised and it has the honour of being responsible for the production of all coins for the Czech National Bank.
• Masters of the craft: Czech Mint offers traditional but also original and unusual products made in cooperation with a variety of artists.
• Traditional Czech society: Czech Mint has been on the market since 1993 and respects the tradition of coin minting while at the same time supporting intelligent innovations and using the most modern technologies.
• Memories for a lifetime: Customers will find a varied selection of commemorative, investment, and gift coins and medals. Czech motifs and worldclass themes are available.
Thanks to Czech Mint, founded over three decades ago in Jablonec nad Nisou, an individual doesn’t have to be a pharaoh, pirate, or gold miner to enjoy the beauty and endless benefits of precious metals.
Minting not only the entirety of circulating coins in the country, but also all Czech commemorative coins alongside a number of investment and gift products made from precious metals, the company represents a proud tradition and love for the art of minting.
“The entire nation appreciates Czech Mint’s work. Having been a reliable partner of the Czech National Bank since 1993, we produce all metal coinage clinking in the pocket of our citizens – i.e. Czech Koruna (CZK) 1, 2, 5, 10, 20, and 50 piece coins,” prides Voborník.
With an interesting start to his minting career, Voborník travelled around the world to gain experience in different industries and positions, with time spent in the US and the UK before returning to the Czech Republic and working his way to CEO of Czech Mint.
Aside from manufacturing for the country, the company prepares its own issue plan every year, boasting dozens of products that have become notable for their artistic value, craftsmanship, excellence, and strictly limited mintage.
“Customers can find a range of emotions and 1,000 years of love for the craft in our products’ reliefs.”
These products can be accessed by anyone; from history experts and sports fans to art lovers or those looking for a unique present, investing in Czech Mint’s mintage provides alternative precious metal investments for those who want to own items of artistic, collector, and emotional value.
Currently, he surmises that the precious metals industry is going through an uncertain time.
“There are different societal pressures for cashless payments. However, we believe there is still great potential for the innovation, development, and education of our partners and customers. We are confident we will remain a partner, supplier, and employer in the years to come,” dictates Voborník.
What sets Czech Mint apart as a unique entity is the combination of its incredible history and dedication to constant innovation and creativity.
“Every coin or medal is a result of a long chain of successive crafts –some are modern, using the latest technologies, while others are more traditional, applying handcraft
chain, from sourcing to final product. As part of Heraeus Precious Metals, we are one of the world’s leading companies in the industry.
Argor-Heraeus is the preferred choice for all your precious metal needs, offering comprehensive solutions and a longstanding dedication to trust and excellence. Established in 1951, and located in Mendrisio, Switzerland, Argor-Heraeus has been for decades at the forefront of the precious metals industry, covering the entire precious metal supply chain, from sourcing to final product. As part of Heraeus Precious Metals, we are one of the world’s leading companies in the industry.
Focusing on responsibility, with cutting-edge technology and strict compliance frameworks, we are able to to provide full traceability of precious metals, to meet your specific needs and ESG goals. With our expertise in delivering personalized 360° precious metal services, we can accommodate varying production volumes and provide precious metal trading services for a complete solution that will suit the most demanding requirements.
ARGOR-HERAEUS SA
Via Moree 14 | CH-6850 Mendrisio +41 091 640 53 53
Focusing on responsibility, with cutting-edge technology and strict compliance frameworks, we are able to to provide full traceability of precious metals, to meet your specific needs and ESG goals. With our expertise in delivering personalized 360° precious metal services, we can accommodate varying production volumes and provide precious metal trading services for a complete solution that will suit the most demanding requirements.
info.argor@heraeus.com | www.argor-heraeus.com
As a confirmation of our high standards, Argor-Heraeus is one of the five LBMA “Approved Good Delivery Referees” worldwide.
We offer a comprehensive product range that extends to investment bars, minted bars and coins, bespoke alloys, raw materials and both semi-finished and high-precision finished products crafted specifically for the luxury and watchmaking industries.
Our longstanding reputation as a trusted refinery is built upon our core values of responsibility, excellence, trust and innovation. These values resonate through every product and service we offer, assuring you of our commitment to not only meet but exceed expectations.
As a confirmation of our high standards, Argor-Heraeus is one of the five LBMA “Approved Good Delivery Referees” worldwide.
Our longstanding reputation as a trusted refinery is built upon our core values of responsibility, excellence, trust and innovation. These values resonate through every product and service we offer, assuring you of our commitment to not only meet but exceed expectations.
ARGOR-HERAEUS DEUTSCHLAND GMBH Ostendstrasse 12
D-75175 Pforzheim +49 7231 139360
techniques perfected over centuries,” prides Voborník.
This cooperation with leading academic sculptors, painters, renowned medal makers, and talented young artists results in customary, original, and extraordinary products.
One example of this collective artistic work comes in the form of the Crystal Coin series.
Inspired by the importance that the small Bohemian town of Jablonec nad Nisou played in the expansion of glassmaking towards the end of the 19th century, this special series of coins combines the strength of both the glassmaking and minting industries.
“The wealth of shapes and unique lustre please the eye and the soul, demonstrating that Czech glassmakers, cutters, engravers, and minters are true masters of their crafts.”
“Through the coins, Czech Mint and Preciosa – the top supplier of high-quality crystal components –wish to tell the story of our region and present the traditional crafts
“EVERY COIN OR MEDAL IS A RESULT OF A LONG CHAIN OF SUCCESSIVE CRAFTS – SOME ARE MODERN, USING THE LATEST TECHNOLOGIES, WHILE OTHERS ARE MORE TRADITIONAL, APPLYING HANDCRAFT TECHNIQUES PERFECTED OVER CENTURIES”
- MICHAL VOBORNÍK, CEO, CZECH MINT
of Jablonec nad Nisou to the world,” explains Voborník.
One of the primary reasons Czech Mint is able to consistently produce such memorable and distinctive coins, as well as other products made from precious metals, is due to its wellestablished supply chain partnerships.
“High-quality and reliable suppliers are the basis for the proper functioning of a manufacturing company such as Czech Mint,” informs Voborník.
“In addition to our specific partnerships for precious metals, our suppliers of machinery, equipment, and associated services are crucial as they directly impact our ability to deliver to our customers.”
These positive relationships result in the creation of myriad new products and internationallyrecognised innovation.
Specifically, Czech Mint recently broke the world record for the largest milled coin in the world, having produced a 535-millimetre (mm) gold coin for the Czech National Bank, which weighs 130 kilogrammes (kg) and boasts a nominal value of CZK100 million. This coin also holds the title
of the largest gold coin in Europe and second-largest in the world.
“This truly unique issue is a symbol of the 100th anniversary of the establishment of the Czech crown and can be adored by visitors in the vaults of the Czech National Bank,” enthuses Voborník.
Additionally, as the mint continues to look towards the future of the industry, it is embarking on new endeavours such as the Incuse Czech Lion, which will be presented in September 2024 at the annual Prague Collector Fair – the largest collectors’ meeting in Central and Eastern Europe.
“Compared to classic coins where the relief protrudes from the coin field, the new incuse coins’ motifs are sunk into the field. “Such curious coins first appeared in the Middle Ages and were either the result of unintentional minting errors caused by a coin getting struck in the press and then imprinted on the next piece
“CZECH MINTING HAS A TRADITION OF MORE THAN 1,000 YEARS. OUR COUNTRY WAS NOT ONLY RICH IN MILK AND HONEY – AS LEGEND HAS IT – BUT ALSO HAD AN ABUNDANCE OF SILVER”
- MICHAL VOBORNÍK, CEO, CZECH MINT
or were done deliberately for aesthetic reasons and to make the money less worn in circulation,” expands Voborník.
In the 21st century, incuse minting is rarely seen and is thus considered a technological and artistic rarity.
By featuring the heraldic beast of the world-renowned Czech Lion on a special commemorative mintage, the
company serves to further its longlasting legacy and continuous artistic innovation.
As Czech Mint continues to invest for the future, it is highlighting the
THREE BILLION PIECES
Since its inception, Czech Mint has minted over three billion pieces of Czech circulation coins with a total value exceeding 13 billion crowns.
150 AUTOMOBILES
Coins are minted using up to 150 tonnes (t) of pressure – equivalent to stacking 150 cars on top of one another. When minting heavyweight bullion coins, a hydraulic press exerts a force of more than 1,000t.
In 1993, the CZK50 crown coin was declared the most beautiful circulating coin in the world. In 1999, the award for the most beautiful gold coin in the world went to the Czech commemorative coin with a motif of Charles IV.
13 PIECES PER SECOND
The coining presses are capable of striking 13 coins per second at a maximum capacity of 500 million pieces per year.
500 TRAIN WAGONS
With a total weight of over 9 million kg,, it would take 500 railcars to load and transport all the coins Czech Mint has minted thus far.
Made from 10kg OF pure gold, the Czech Lion bullion coin is the largest gold coin minted in continental Europe. The coin bears the minted Czech Security Check hologram, a security feature made up of microscopic reliefs with detail starting at just one nanometre, which is 1,000 times less than the thickness of a human hair.
steps it is taking to implement new technologies, specifically those of digitalisation.
“We take great pride in developing new technologies in the field of coin production and are always striving for further innovation,” dictates Voborník.
In 2020, in cooperation with IQ Structures, Czech Mint created Czech Security Check, a security hologram that protects selected high-mass Czech Lion coins from counterfeiting.
As holograms are not only a protective element but an ornamental one, both companies decided to go even further in 2023, devoting the entire surface of the reverse side of the
coin to an embossed hologram.
Furthermore, by the end of that year, the business minted the first Czech Lion 2023 hologram in the world for the palladium ounce investment coin.
Equally significant to the longevity of the company are its hardworking and dedicated staff and corporate social responsibility (CSR) practices that Czech Mint engages in.
“Our goal is to motivate our employees so that they enjoy their work, and the company continues its reputable guarantee of good earnings and a healthy atmosphere,” states Voborník.
To give back to the community it symbolises in its coins and precious metals products, Czech Mint partakes in Project Babybox – a programme which provides a safe place, i.e. a baby hatch, where people can anonymously leave babies to be found and cared for.
“In 2019, we partnered with the programme and pledged to donate a gold ducat to each child found in a babybox in the country. Since then, we have donated more than 50 gold ducats to the babybox children,” details Voborník.
With over a millennium of history and artistic development, the Czech minting industry is one of the most
notable throughout the world. Czech Mint has carved a name for itself as a premier minting manufacturer who creates pieces that are not just visually stunning, but memorable and priceless for centuries to come.
Tel: +420 800 225 228 info@mint.cz mint.cz
Semiconductors are the backbone of modern technology, facilitating advancements across myriad sectors. Indeed, from telecommunications and electronics to the automotive industry, these solutions are instrumental in the development of cloud computing, 5G infrastructure, electric vehicles (EVs), and more.
Innovative plasma-based solutions remain the core business of Trymax Semiconductor Equipment B.V. (Trymax), who stands as a
shining example of ingenuity at the crossroads of innovation and entrepreneurship in wafer manufacturing.
Originating as a small spinoff company founded by two former Philips engineers in the Netherlands, the Dutch company designs, manufactures, and markets its NEO series, a product line of leading-edge plasma equipment to meet the most stringent requirements and deliver advanced processing capabilities to customers.
The NEO series, which can process various materials, wafer sizes, and thicknesses, addresses a number of applications during the semiconductor manufacturing process, including ashing, descumming, light etching, and surface preparation and cleaning. It also offers ultraviolet (UV) solutions for built-up device charge erasing and photoresist curing, which exhibit various benefits over baking the photoresist such as improving critical dimension (CD) control,
Peter Dijkstra, CCO, updates us on the latest developments during the past year at Trymax Semiconductor Equipment B.V., including the company’s ultraviolet solutions, notable expansion in the US, and economic mission across the pond
Writer: Jack Salter | Project Manager: Nicholas Kernan
uniformity, selectivity, and overall stripping.
UV is an area in which Trymax has evolved to meet significant demand since we last spoke to CCO, Peter Dijkstra, in August 2023.
“Last year, we discussed the etching, stripping, and removal of the sensitive photoresist layer. At the same time, we also started up a new machine using UV light,” he recounts.
“If the photoresist layer has been spun on the wafer, you need a lot of water in order to equally dispatch it,
but once you’ve done that you want to remove the water to get a hard crust on top.”
To achieve this, Trymax uses UV light to quickly evaporate the water, a new tool that is replacing a lot of those currently found in the market and builds on the company’s remarkable culture and journey towards semiconductor innovation.
Trymax’s high-throughput NEO 2000UV system features the latest and fastest UV curing and charge erasing technology, offering
exceptional performance to meet today’s semiconductor fabrication requirements.
In January 2024, after overcoming a number of hurdles, Trymax successfully launched a start-up business in the US.
Located just outside of New York, Trymax USA Incorporated complements the company’s service office in Dallas, Texas.
Having also hired an experienced
Sales Manager and service personnel, Trymax’s operations are now fully up to speed in the country.
“We see that we are getting a lot of traction in the US at the moment,” notes Dijkstra.
The company’s expansion to the US follows the recent introduction of the Creating Helpful Incentives to Produce Semiconductors (CHIPS) and Science Act in August 2022.
The CHIPS and Science Act intends to boost American semiconductor R&D and production, ensuring US leadership in the technologies and industries of tomorrow.
Semiconductors are a US invention, however the nation today only produces around 10 percent of the world’s supply, whilst East Asia is responsible for three-quarters of global production.
“The industry in China is booming at the moment; if you look worldwide, more than half of business is coming
from China,” Dijkstra informs us.
With this in mind, the CHIPS and Science Act aims to maintain and advance the US’ scientific and technological edge by unlocking significant private sector investment in semiconductors from the likes of Trymax.
“The CHIPS and Science Act is putting quite some money on the table, so I think we are on the right track in the US at the moment,” he assures.
As well as successfully expanding in the US during the past year, Trymax was proud to be part of an economic mission on semiconductors, which took place in Arizona and California in early December.
A delegation of 45 Dutch and Flemish companies and knowledge institutes specialising in the semiconductor industry participated
in the mission along with the Dutch Prime Minister at the time, Mark Rutte.
The goal of the mission was to connect with the semiconductor and technology industry in Phoenix and the San Francisco Bay Area to exchange knowledge, seize opportunities, and accelerate innovation.
This visit coincided with rising employment numbers in the US, with more than one million American jobs supported by Dutch trade and investment, of which 78,000 are in California and 15,000 are in Arizona.
These numbers illustrate the vibrant role that the Netherlands plays in supporting a robust US economy.
“I’ve been on economic missions before, but never with the Prime Minister, and I can tell you it’s a big difference!” Dijkstra tells us.
“When the Prime Minister is incorporated, the red carpet is rolled out, all the CEOs and marketing
people are present, and you get much more traction and information than without them there.
“I think for the whole industry it was very successful, and it was nice to experience all the American policemen, the sirens, and the blue lights; it’s quite impressive to see what’s happening,” he adds.
Whereas Trymax was more equipment-oriented in the early
“THE CHIPS AND SCIENCE ACT IS PUTTING QUITE SOME MONEY ON THE TABLE, SO I THINK WE ARE ON THE RIGHT TRACK IN THE US AT THE MOMENT”
– PETER DIJKSTRA, CCO, TRYMAX SEMICONDUCTOR EQUIPMENT B.V.
days, the company has step-by-step become more process-oriented during the last 12 months.
“The customer is looking for a process solution, not an equipment solution, so little by little we are making that change,” states Dijkstra.
In this way, Trymax is now talking more about its process and application specifications with customers, rather than equipment.
One major ongoing process development at the business is what
Dijkstra refers to as ‘bowl’ or ‘wine glass’ etching.
“Silicon wires need to be cleaned but also filled with copper afterwards, which can be difficult, but if you make a wine glass opening then they’re easier to fill, so we see a lot of traction in the market for doing that,” Dijkstra explains.
The company additionally works a lot with silicon carbide wafers and is now one of the key players in this area, having supplied equipment for
Trymax has developed strong expertise in plasma equipment and processes over the last 20 years.
With more than 300 NEO systems installed worldwide, Trymax solutions are:
• High performance
• Low maintenance
• Extremely reliable
• Affordable to own
• Compact with reduced footprint
• Capable of managing multiple wafer sizes and substrate materials
• Built with state-of-the-art components, interfaces, and software
“I’VE BEEN ON ECONOMIC MISSIONS BEFORE, BUT NEVER WITH THE PRIME MINISTER, AND I CAN TELL YOU IT’S A BIG DIFFERENCE!”
– PETER DIJKSTRA, CCO, TRYMAX SEMICONDUCTOR
EQUIPMENT B.V.
multinationals in Europe, the US, and Asia.
“We are also now the number one supplier of silicon carbide equipment in China, so we are doing very well in this market segment,” he acclaims.
Acknowledging the importance of being as responsive as possible, Trymax also sets up technical review meetings (TRMs) in which the company and its customers share their respective road maps.
This makes it easier for Trymax to anticipate future requirements and have the hardware and processes ready for when customers need them.
“The whole team is very happy that we get a lot of recognition and respect in the market and that more and more people are contacting us, so we are on the right track,” Dijkstra concludes.
Tel: +31 24 350 0809 info@trymax-semiconductor.com www.trymax-semiconductor.com
Scope of Application:
• Photoresist stripping
• Isotropic etching
• Surface cleaning and conditioning
Typical etching rates are:
• Photo resist 5µm/min
• Silicon 3µm/min
• SiN and BPSG 1µm/min
• Thermal Oxide 250nm/min
eeplasma produces microwave plasma sources for Trymax for the photoresist strip and isotropic etching processes for semiconductor production.
• The plasma sources have a maximum power of two or three kilowatts (KW) and the plasma chamber can be equipped with quartz, ceramic or sapphire tubes.
• The plasma source is characterised by its very compact design, its high level of service friendliness and its very large process window.
not
At Mupa, we passionately design and assemble high-quality control cabinets.
We deliver this on a project-based basis as well as in repetitive (series) work.
Our aim for simplicity and perfection in product and process, results in structural and long-term partnerships and added value in your process.
Mupa Schakeltechniek B.V. Meerheide 208, 5521DW, Eersel The Netherlands www.mupa.nl
It
of
emphasizes how the company not only produces cuttingedge packaging for transporting biopharmaceuticals and vaccines but also plays a pivotal role in saving lives by ensuring the safe and effective delivery of vital drugs
Writer: Rachel Carr | Project Manager: Michael Sommerfield
The US boasts the world’s largest pharmaceuticals market, with more leading companies than any other country.
The drug industry is supported by a robust pharma services sector, which includes packaging manufacturers.
The BioTech, pharmaceutical, and medical technology industries are experiencing significant growth in the healthcare sector. Therefore, specialized transportation methods, advanced thermal packaging, and digital monitoring solutions are vital to maintaining the efficacy and safety of pharmaceuticals and vaccines globally.
Crucial to a delivery network of lifesaving care from the doors of specialty pharmacies, life sciences distributors, and manufacturers to patients is Cold Chain Technologies (CCT).
Pharmaceuticals must be transported under controlled conditions and temperatures, which is where CCT’s products, services, and digital solutions come in.
“We played a significant role in developing thermal packaging for the global transportation of the mRNA COVID-19 vaccine. In addition, we now provide this service for a broader range of biopharmaceuticals,” opens Ranjeet Banerjee, CEO.
Headquartered in Franklin near Boston, Massachusetts, and operating for over five decades, CCT has focused on driving innovative life sciences solutions and products for the last 25 years.
“We have multiple ISO-certified locations, including manufacturing facilities, distribution centres, and offices in the US, Europe, Latin America, and Asia,” Banerjee adds.
The team at CCT partners with customers to understand problems and potential challenges and they collaboratively select the appropriate packaging solution tailored to their needs.
“We provide two options: a comprehensive portfolio of existing products, or, as we have the capabilities to do so, we can
On a journey to become the trusted knowledge partner for life sciences customers, CCT offers expertise in products and services, understands its clients’ needs, and delivers comprehensive solutions to address those needs.
“It is challenging to maintain every individual product at a specific temperature, as there are millions of shipments happening around the world and each one has to be delivered while meeting the right conditions.
“If that fails, not only are millions of dollars at stake but more importantly, someone’s life could be at risk. A key motto at CCT is “Our Work Matters”, Banerjee points out.
CCT prides in being a trusted and knowledgeable partner through advanced products, services, and global presence. It strives to be the top choice for customers by leveraging its expertise in collaboration with companies that excel in drug development.
“We specialize in ensuring that drugs are maintained under the right conditions to the very end. As someone said during the COVID-19 pandemic, having a vaccine available is not the same as being vaccinated, because the entire endto-end process, from factory to patient or recipient, needs to have a high level of assurance,” he notes.
design something tailored to the needs of our strategic partners. Any product undergoes testing, and our customers will be provided the validation documents for quality and compliance purposes,” he elaborates.
Banerjee is excited about the global and complex aspects of supply chain trends and the new therapeutics in drug development are experiencing significant innovation.
“Biopharmaceuticals, such as vaccines, antibody drugs, and cell and gene therapy, are large-molecule formulations that require special temperature monitoring and control during transportation.
“Companies can excel in drug development and manufacturing, but if the transportation isn’t handled properly, the drugs could lose their efficacy and safety, which impacts patient outcomes – this is where we come in,” Banerjee voices.
With many years of experience working with multiple large global pharmaceuticals, medical technology, and diagnostic companies and distributors worldwide, CCT offers its expertise through a comprehensive product portfolio and service as well as providing consulting expertise.
Through advanced product design and digital capabilities, CCT delivers high-quality solutions to track, trace, and predict, which can often prevent any temperature excursions before they occur.
“Ultimately, we aim to assure customers that the lifesaving vaccines and other pharmaceutical products transported in our advanced solutions are maintained under the precise conditions required throughout their journey from lab or plant to patient.”
Acutely aware of compromising patient safety, CCT ensures efficient deliveries through digital solutions for remote tracking, tracing, and monitoring with state-of-the-art
Empower your business with DaVinci’s cutting-edge sustainable packaging solutions tailored for the medical industry. Elevate your brand by partnering with us for expert design, precision automated manufacturing, and efficient delivery of sustainable packaging, parts, and components.
At DaVinci, we go beyond traditional engineering. Our team of experts brings a wealth of knowledge in raw materials, design, prototyping, testing, and validation to ensure your products not only meet but exceed industry standards. We pride ourselves on being your strategic ally in the pursuit of innovative and eco-friendly solutions.
Together, let’s revolutionize your products, reduce environmental impact, and boost your sales with the power of sustainable innovation.
Materials
• FDA compliant
• Sustainable
• Reusable/Recyclable
• Cost Effective Packaging Expertise
• 40 Years of Plastics Engineering Experience
• Automation
• Thermoforming
• Blow Molding
• Injection Molding
Customer Solutions
• Diagnostic Reservoirs
• Sterile Barrier Packaging
• Heat Seal Systems
• Contract Packaging
• Cold Chain Packaging
• Validation Services
Internet of Things (IoT) devices.
“Our data and digital tracking platforms go one step further by predicting issues such as interruptions in the supply chain and assist in decision making. For instance, if there is a delay in air freight, we can remotely detect it, which will lead to an alert, and that in turn could lead to an intervention if necessary,” explains Banerjee.
While technology can lead to substantial cost savings, Banerjee acknowledges that what is more important is the benefits of improving patient safety and driving better patient outcomes.
“According to an independent study,
$35 billion worth of pharmaceutical products are wasted yearly due to temperature fluctuations. Ensuring the safe administration of drugs and vaccines is a significant and challenging task as it involves transporting them from A to B and then to the recipient,” he shares.
With diverse core competencies and a broad portfolio of solutions, customers can confidently approach CCT with unique challenges.
“During the COVID-19 pandemic, a vaccine manufacturer approached us with a product that required
DID CCT’S ROLE IN THE COVID-19 PANDEMIC INCREASE ITS VISIBILITY WITHIN THE LIFE SCIENCES INDUSTRY?
Ranjeet Banerjee, CEO: “We have spent the past 25 years establishing trust in the healthcare sector; it is ingrained in our company culture to prioritize the well-being of our customers and the wider industry.
“We never cut corners, especially considering we transport life-saving drugs and vaccines. This trust has only continued to strengthen over the past four years as we supported the COVID-19 vaccine distribution, demonstrating the reliability and quality of our work during a crisis.
“We were featured in the national news and showcased on primetime television when the first shipments of the COVID-19 vaccine began. As a purpose-driven organization, our role served as a reminder that there is a patient at the end of everything we do.”
transportation at ultra-low temperatures. We collaborated with the company, leveraging our thermal design and engineering capabilities to solve the issue,” Banerjee reflects.
Another facet of CCT is its material science capabilities, including its proprietary phase-change materials (PCMs), a thermal energy storage and release technique.
The company utilizes cuttingedge insulations, and the interplay of thermal design and engineering ensures that the temperature is maintained for extended periods.
Subject to rigorous testing, CCT also adheres to industry standards to validate products.
“In our R&D centre near Boston, we operate one of the largest ISTA-certified testing laboratories for thermal packaging solutions worldwide. The reports from these tests are often included in regulatory submissions,” he notes.
Moreover, customers are continually supported during onboarding to ensure they use the products correctly. Additionally, digital tracking and optimization provide customers with package location updates.
“Even though carriers can provide package tracking information, what sets us apart is our ability to monitor temperatures accurately. We can also predict temperature excursions, offering a comprehensive range of capabilities from design and selection to manufacturing and tracking,” Banerjee emphasizes.
Addressing important challenges in manufacturing, CCT offers sustainable packaging solutions that also meet customer performance and cost requirements.
“Our extensive line of reusable products features EcoFlex™, a parcel shipping solution that includes a fully capable monitoring platform, allowing us to track and trace the location
of items and monitor the temperatures they are exposed to,” Banerjee enlightens.
The company took its first significant step towards sustainability four years ago when EcoFlex™ was extensively used for transporting the COVID-19 vaccine.
“We were a large part of the Operation Warp Speed program for the US federal government. The product is performing exceptionally well, and as a result, we have expanded our product line to include an ultra-low temperature range of -80°F,” he divulges.
“ULTIMATELY, WE AIM TO ASSURE CUSTOMERS THAT THE LIFESAVING VACCINES AND OTHER
PHARMACEUTICAL PRODUCTS TRANSPORTED IN OUR ADVANCED SOLUTIONS ARE MAINTAINED UNDER THE PRECISE CONDITIONS REQUIRED THROUGHOUT THEIR JOURNEY FROM LAB OR PLANT TO PATIENT”
– RANJEET BANERJEE, CEO, COLD CHAIN TECHNOLOGIES
Furthermore, CCT has the industry’s largest fleet for EcoFlex™, reducing fossil fuel-based raw material use through container reuse. The other element of sustainability is high-quality, high-performing, yet affordable
single-use sustainable products. Two years ago, CCT acquired Packaging Technology Group (PTG) and subsequently gained capabilities in using cellulose, a naturally occurring material, in thermal packaging.
Creating high-quality, highperforming insulation from cellulose, which can be transformed into singleuse packaging using automated programs, results in cost-effective products.
“We have successfully launched our cellulose-based eco-friendly packaging in Europe and the US,” states Banerjee.
The EcoFlex™ and cellulose packaging options both aim to provide customers with sustainable solutions. CCT also equips customers with data to support environmental benefit claims from using their products.
Continuing the development of sustainable products and reducing reliance on fossil fuel-based materials are two important goals for CCT.
“Initially, we wanted to avoid 50 million pounds (Ibs) of landfill by 2025, and we beat that ahead of time because our reusable products started taking off. We extended our goal to 75 million lbs, and now we are on track to eliminate 100 million lbs through sustainable products and solutions. We have the largest fleet, and as we keep growing, so do the sustainability benefits,” Banerjee explains.
Furthermore, CCT is excited about assuring customers with sophisticated digital solutions. Predicting an excursion and intervening before it happens is a powerful tool that the company can achieve through automated monitoring.
For more than five decades, DonahueCorry has been a trusted name in the packaging industry.
Our partnership with Cold Chain Technologies exemplifies our dedication to the pharmaceutical sector. Together, we provide cutting-edge flexible packaging solutions that guarantee the safe transport of critical pharmaceuticals, reflecting our unwavering commitment to quality and reliability.
495 Business Center
44 Central Street Berlin, MA 01503
+1 978-838-0255
Donahue-Corry.com
“WE NEVER CUT CORNERS, ESPECIALLY CONSIDERING WE TRANSPORT LIFE-SAVING DRUGS AND VACCINES”
– RANJEET BANERJEE, CEO, COLD CHAIN TECHNOLOGIES
“We are also incorporating decision support capabilities that can reduce waste in last-mile delivery, create value, and improve patient safety,” he points out.
This convergence of IoT and artificial intelligence (AI) in data sciences means CCT now collects and utilizes data from its packaging.
“Our packages transmit data – the ‘intelligent connective tissue’ across the last mile from manufacturer to patient. The information we receive from this can be used to support decision making,” outlines Banerjee.
CCT, therefore, uses data to minimize waste in the system,
enhance patient safety, and is planning to roll out intelligent applications on an ongoing basis.
The company continues to expand globally and is currently building another plant to complement its multiple locations in Europe, as well as the recent acquisition of a company in Europe.
“We recently established a new manufacturing facility in Breda, Netherlands, which is now up and running. Additionally, we are expanding our operations in São Paulo, Brazil – there is a lot of expansion occurring
within the pharmaceutical value chain worldwide,” concludes Banerjee.
Demonstrating a commitment to patients, CCT takes pride in addressing the unique challenges faced by the life sciences sector. Through innovative packaging technology, it ensures that products receive the correct care throughout the cold chain journey, thereby entrusting the future of healthcare to the vanguard of the manufacturing industry.
+1 (800) 370-8566
Growing from a small, family-run business to an expert trailer organization, Delco Trailers has quickly become a titan of the industry. William Dyck, COO of the company, reveals the secret to its success
Writer: Lucy Pilgrim
Project Manager: Michael Sommerfield
The light to medium trailer market in the US has experienced considerable turbulence in recent years, particularly after the onset of the COVID-19 pandemic, when many companies raced to maximize their capacity and meet increasing demand. However, market demand significantly decreased in the following years, whilst production capacity remained at an alltime high, resulting in fierce competition across the trailer industry.
Meanwhile, myriad new companies have entered the sector during this time, with many originating from Mexico, where lower labor and material costs make the US trailer industry an attractive venture, consequently further increasing the competition.
“While we notice the influx of trailers from Mexico, we are confident that manufacturing in Texas is alive and well, and with an emphasis on efficient manufacturing, we continue to thrive,” opens William Dyck, COO of Delco Trailers (Delco).
However, the benefit of increasing industry players is that companies are encouraged to evolve and develop their products and capabilities.
So much so that over the last 10 to 15 years, Dyck has observed an increased output across the board as businesses continue to improve.
“Many manufacturing organizations, including ourselves,
Headquartered in Paris, Texas, Delco thrives in a city at the center of the black-iron trailer country.
The business specializes in light to
hotshot trailers, and offers tailored equipment and steel cargo.
Delco consistently endeavors to work with its clients to create the perfect custom order.
“As the manufacturer, our mission is to create the best possible product and support our incredible dealer network, consisting of approximately 180 independent retailers that span the country,” Dyck informs.
This is supported by a dedicated team of nearly 200 staff members who care deeply about their work, the trailers the company creates, and the customers it serves.
Established as a one-man show operating from a small, 4,800 square foot (sqft) facility in 2006, Delco has experienced organic growth. By 2014, it evolved from a small-scale operation to producing six to eight trailers a week. Three years later, the company explosively expanded by diversifying its product line to
“AS THE MANUFACTURER, OUR MISSION IS TO CREATE THE BEST POSSIBLE PRODUCT AND SUPPORT OUR INCREDIBLE DEALER NETWORK”
– WILLIAM DYCK, COO, DELCO TRAILERS
Increase your shop’s productivity by choosing from a wide range of cutting machines, offering multiple process options of plasma/laser bevel cutting up to 20kW, oxyfuel, and marking. By adding material handling solutions you can save time and money. From dual pallet shuttles or intelligent sorting, conveyors, to fully automatic storage towers and retrieval systems, you can dramatically increase your shop’s throughput.
Could you introduce us to Messer Cutting Systems and its services, facilities, products, and processes?
Messer Cutting Systems is a global leader in computer numerical control (CNC) cutting systems, providing advanced solutions for metalworking industries.
Our core services include sales, installation, training, and support for CNC plasma, laser, and oxyfuel cutting machines. We operate state-of-the-art facilities worldwide, producing high-quality cutting equipment and software solutions.
Our processes emphasize innovation, precision, and customercentric service to ensure optimal performance and reliability in all our products and services.
By leveraging cutting-edge technology and a deep understanding of our customers’ needs, we strive to deliver solutions that enhance productivity and efficiency in metalworking operations.
What type of industries and clients does Messer Cutting Systems serve?
We serve a diverse range of industries, including automotive, aerospace, shipbuilding, construction, and metal fabrication. Our customers range from small workshops to large manufacturing enterprises seeking high-quality, efficient, and reliable cutting solutions for their metalworking needs.
Our cutting systems are used in the automotive industry to create precise vehicle components, ensuring high performance and safety standards.
The aerospace industry relies on our technology for producing lightweight, durable parts that meet strict regulatory requirements. In shipbuilding, our machines facilitate the construction of robust, seaworthy vessels by enabling accurate cutting of large metal sheets.
Our solutions benefit the construction sector, as they are utilized in the fabrication of structural components for buildings and infrastructure projects.
Large and small metal fabrication shops depend on our cutting systems to deliver precise cuts and high-quality finishes for a wide range of applications.
Our OmniWin, OmniFab, and OmniBevel software solutions streamline processes by integrating advanced cutting technologies with intuitive user interfaces.
These software packages enable efficient machine operation, real-time monitoring, and seamless automation, which significantly reduces setup times and minimizes errors.
The result is enhanced productivity and consistent, precise results across various cutting applications.
OmniWin focuses on optimizing cutting plans and improving material utilization, while OmniFab provides a comprehensive solution for managing the entire production process.
OmniBevel offers specialized tools for creating complex bevel cuts with high accuracy.
Our software allows customers to achieve greater operational efficiency, reduce waste, and improve overall production quality.
Is there any innovative or state-of-the-art equipment or technology the company uses or is planning to invest in?
We continuously invest in innovative, state-of-the-art equipment and technology to stay ahead of the competition and meet our customers’ evolving needs.
Our advanced CNC plasma, laser and laser beveling solutions, along with our oxyfuel cutting machines, represent the pinnacle of cutting technology. We are also developing and integrating cuttingedge software solutions to enhance material handling, precision, and efficiency in our processes.
This commitment to innovation ensures that our customers benefit from the latest advancements in cutting technology, which translates to improved productivity, higher-quality products, and greater operational efficiency.
Our research and development team works tirelessly to explore new technologies and incorporate them into our product offerings.
What does 360° service mean, and how does it benefit your customers?
Our 360° service means providing comprehensive support throughout the entire lifecycle of our products, from initial consultation and installation to training, maintenance, and upgrades. This ensures our customers receive continuous, reliable assistance, maximizing their equipment’s performance and longevity and ultimately enhancing their operational efficiency and productivity.
Our service team is dedicated to providing professional support to address any issues that may arise, minimizing downtime and ensuring that our customers can maintain their production schedules.
We offer a range of service plans tailored to meet each customer’s specific needs, including preventive maintenance programs, emergency repair services, remote support, and virtual support options.
In addition to technical support, we provide extensive training programs to help our customers get the most out of their equipment.
What sets Messer Cutting Systems apart from the competition?
Our unwavering commitment to innovation, quality, and customercentric service sets us apart.
We offer a comprehensive range of cutting solutions backed by advanced technology and a global support network. This ensures our clients receive tailored, reliable, and efficient solutions that meet their unique needs.
Our focus on continuous improvement drives us to develop new products and enhance existing ones, ensuring we remain at the forefront of the cutting industry.
Our customer-centric approach means we listen to our clients’ needs and work closely with them to develop solutions that address their specific challenges.
Our global presence allows us to provide localized support and services, ensuring our customers receive prompt, personalized assistance regardless of location.
Is there anything you would like to pay special mention to?
I’d like to highlight our dedication to continuous improvement and customer satisfaction. We always look for ways to innovate and enhance our products and services, ensuring we meet and exceed our customers’ expectations.
Our global team of experts is committed to providing exceptional support and delivering cutting-edge solutions that drive our clients’ success.
Our commitment to excellence extends beyond our products and services to every aspect of our business, from our internal processes and corporate culture to our interactions with customers, partners, and the communities we serve.
We are proud of our legacy of innovation and customer satisfaction, and we look forward to continuing to lead the industry and deliver exceptional value to our clients.
Despite small year-on-year additions that solved immediate capacity restraints, the business did not anticipate its long-term growth.
For instance, by 2020, Delco worked in a 180,000 sqft facility that was completely maximized and had little room for capacity development. Therefore, the space was inefficient for housing new additions, which resulted in a disjointed and inefficient manufacturing process.
“We started envisioning our dream space, taking our years of experience and lessons learned from elements that didn’t work so well in order to create our new facility,” Dyck explains.
The result was the introduction of a 600,000 sqft manufacturing facility in 2023 that placed an emphasis on production flow, new machinery, automation, and fixtures, enabling the company to produce 150 to 200 trailers per week with a production capacity of 500 units in the same timeframe.
The new facility enables Delco to build better, more consistent
Positioned at the forefront of the metal working industry, Messer Cutting Systems is a global supplier of top-of-the-range equipment, tailored service packages, and state-of-theart technologies that exceed international standards.
Levering the expertise of approximately 1,000 experienced employees across five production sites, the company is proud to provide value-added solutions for the international thermal cutting sector.
Messer Cutting Systems’ unparalleled product portfolio includes spare parts, repairs, retrofitting, maintenance and service, environmental technology, and in-house software solutions.
products and increase production and efficiency.
Delco stands out in the industry thanks to its unwavering commitment to customer service.
“Being a family-owned and operated business deeply invested in our craft, we extend our passion and values to every customer interaction, striving to enhance their success,” highlights Dyck.
The company’s strengths also lie in the diversity of its product offerings, which include comprehensive steel trailer solutions ranging from 53-inch cattle trailers to rugged enclosed and 10-inch light-duty utility trailers.
“We prioritize quality and consistency, leveraging automation and standardization methods to ensure each trailer produced maintains our hallmark of being well built and high quality, every time.”
Moreover, as a family-run organization, Delco’s relationship
“BEING A FAMILY-OWNED AND OPERATED BUSINESS DEEPLY INVESTED IN OUR CRAFT, WE EXTEND OUR PASSION AND VALUES TO EVERY CUSTOMER INTERACTION, STRIVING TO ENHANCE THEIR SUCCESS”
– WILLIAM DYCK, COO, DELCO TRAILERS
with its clients is crucial. Every trailer component, including steel, axles, wheels, lighting, and decking, is sourced from a variety of vendors, making supplier relationships invaluable.
Moreover, the recent appointment of Dyck’s brother as Purchasing Manager has strengthened the company’s supplier relationships, some of which have lasted for nearly 20 years. This ultimately ensures the timely procurement of quality products.
Additionally, Delco is further differentiated by its staff base, who
are at the heart of the organization and have unwavering dedication and talent.
“As a family-run business, we hold dear the values of trust, respect, and support, which extend to every member of our team.”
The company empowers its employees by fostering an inclusive environment where everyone’s voice is heard and respected, with each team member encouraged to take ownership of their work and contribute their unique skills and perspectives.
As such, recognition is a
cornerstone of Delco’s approach, celebrating both big and small successes.
“Our organization thrives because of the dedication and passion of our team. They are not just employees; they are integral members of our work family, and their commitment drives our daily mission,” prides Dyck.
Presently, Delco is focused on its automated powder coating line.
“When seeing a trailer, the first thing anyone will notice is the finish.
With that in mind, we’re putting a lot of effort into our finish line,” Dyck points out.
This means that automated overhead trolleys meet the unfinished trailer at the end of the welding
process and are immediately attached to the overhead rail, which transports the trailer through the final operations.
“Before this process, we were manually moving the trailers to a
Delco is deeply committed to making a positive impact in the local community. The company actively supports initiatives such as breast cancer awareness campaigns, which raise funds to help those affected.
Beyond fundraising, Delco encourages its team members to devotedly engage in community activities, fostering a culture of giving back and volunteerism.
Additionally, the company proudly sponsors and participates in events that benefit local charities, including Court Appointed Special Advocates (CASA) For Kids, Boys & Girls Clubs of America, and United Way. These partnerships allow the business to directly contribute to important causes that improve the lives of individuals and families in the area.
“Being involved in our community isn’t just a responsibility; it’s a core part of who we are as an organization.
“We believe in making a difference through our business practices and active support of community entities that share our values and goals.”
storage location before moving them again to the finish line; therefore, we have now eliminated two touches,” he expands.
The overhead trolleys are also moved mechanically instead of being manually pushed by forklifts or hand, as they were previously. With over 2,500 inches of rail, this innovation has eliminated significant amounts of manpower.
Meanwhile, the company is currently in the process of the construction and implementation of automated wash bays projected for functionality at the end of Q3 2024, significantly improving efficiency and consistency.
Alongside product and manufacturing innovation, Delco is looking inward to refine its processes to maximize the company’s organization.
“We are working on many initiatives, such as fine-tuning our forecasting to ensure a lower material inventory whilst streamlining our warehouse procedures to better keep track of trailer components, eliminating inefficiencies and missing parts,” explains Dyck.
The company has also implemented an internal ordering system for in-house parts and sub-assemblies, which allows departments to better enter and keep track of these different processes.
As such, Delco is focused on streamlining its operations to
maximize its new facility space and ensure it is well-positioned for growth.
“As a company that started from scratch, we learn something new every day, and we are constantly focused on improving the little things, knowing that they make up the bigger picture,” Dyck closes.
chain, from sourcing to final product. As part of Heraeus Precious Metals, we are one of the world’s leading companies in the industry.
Argor-Heraeus is the preferred choice for all your precious metal needs, offering comprehensive solutions and a longstanding dedication to trust and excellence. Established in 1951, and located in Mendrisio, Switzerland, Argor-Heraeus has been for decades at the forefront of the precious metals industry, covering the entire precious metal supply chain, from sourcing to final product. As part of Heraeus Precious Metals, we are one of the world’s leading companies in the industry.
Focusing on responsibility, with cutting-edge technology and strict compliance frameworks, we are able to to provide full traceability of precious metals, to meet your specific needs and ESG goals. With our expertise in delivering personalized 360° precious metal services, we can accommodate varying production volumes and provide precious metal trading services for a complete solution that will suit the most demanding requirements.
ARGOR-HERAEUS SA
Via Moree 14 | CH-6850 Mendrisio +41 091 640 53 53
Focusing on responsibility, with cutting-edge technology and strict compliance frameworks, we are able to to provide full traceability of precious metals, to meet your specific needs and ESG goals. With our expertise in delivering personalized 360° precious metal services, we can accommodate varying production volumes and provide precious metal trading services for a complete solution that will suit the most demanding requirements.
info.argor@heraeus.com | www.argor-heraeus.com
As a confirmation of our high standards, Argor-Heraeus is one of the five LBMA “Approved Good Delivery Referees” worldwide.
We offer a comprehensive product range that extends to investment bars, minted bars and coins, bespoke alloys, raw materials and both semi-finished and high-precision finished products crafted specifically for the luxury and watchmaking industries.
Our longstanding reputation as a trusted refinery is built upon our core values of responsibility, excellence, trust and innovation. These values resonate through every product and service we offer, assuring you of our commitment to not only meet but exceed expectations.
As a confirmation of our high standards, Argor-Heraeus is one of the five LBMA “Approved Good Delivery Referees” worldwide.
Our longstanding reputation as a trusted refinery is built upon our core values of responsibility, excellence, trust and innovation. These values resonate through every product and service we offer, assuring you of our commitment to not only meet but exceed expectations.
ARGOR-HERAEUS DEUTSCHLAND GMBH Ostendstrasse 12
D-75175 Pforzheim +49 7231 139360