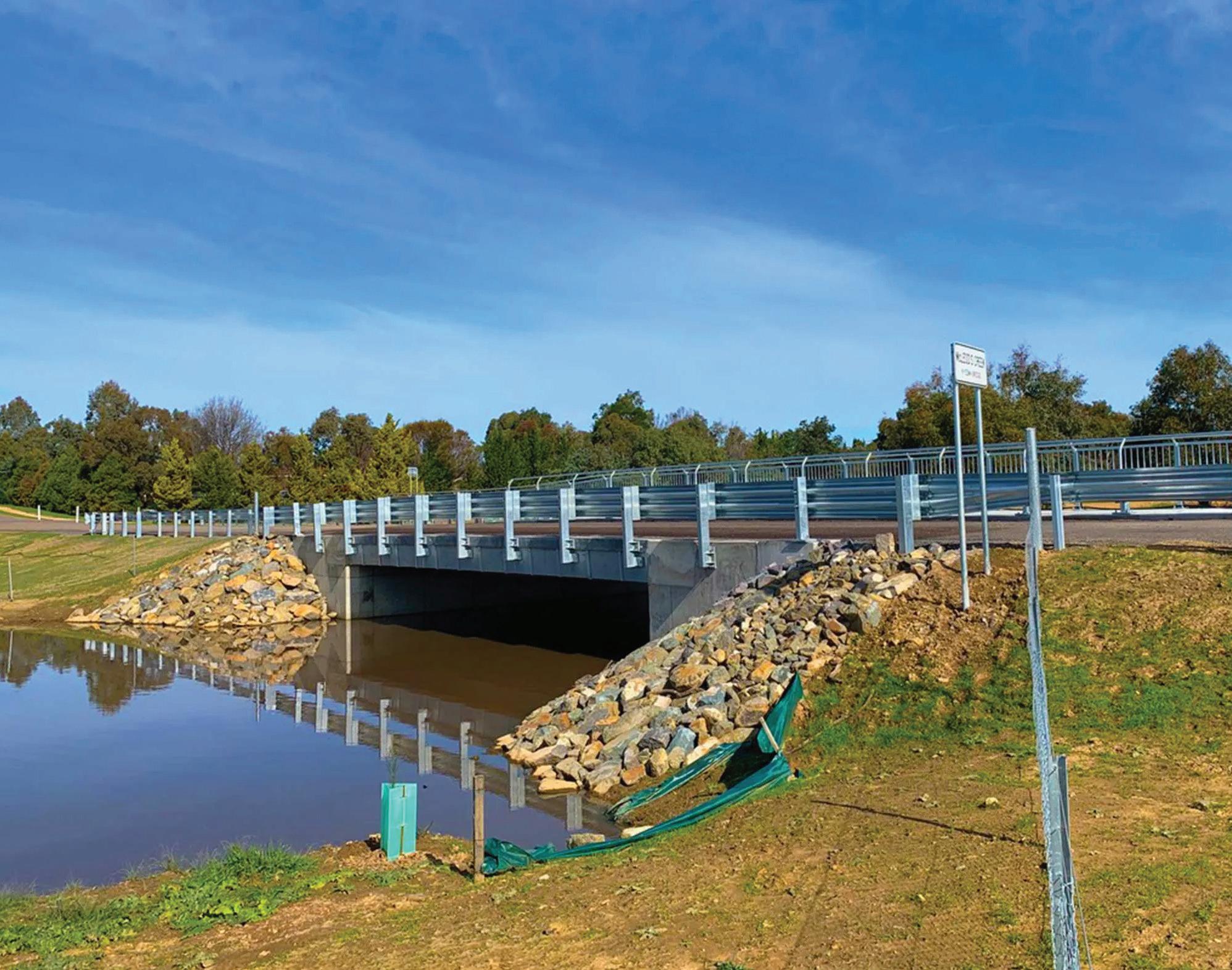
5 minute read
InQuik: Bridging a Gap in the Market
DAVID SPRING PT COLUMNIST Sydney, Australia

Advertisement
ON the banks of the Bio waterway, the Dnk! Dnk! Dnk! of pile driving echoes across the coastal plain. Alongside ulukwalo trees and interested onlookers, the steel and concrete marks a stark contrast with traditional log bridge construction. This is the first of four new bridges on the Malaita North Road under the Solomon Islands Road and Aviation Project (SIRAP). While this is not the first steel and concrete bridge Solomon Islands by any stretch, it’s the first InQuik modular bridge installation in the whole of the South Pacific. InQuik’s technology is uncomplicated. Pre-formed steel moulds are placed as permanent formwork and filled with concrete. They come to site prefabricated, inclusive of steel reinforcing bars and bracing. They’re tied into the abutments and piles and concrete is poured insitu. The design is billed as easy to install and low maintenance. It’s worth comparing InQuik with other modular and rapid bridging options, to understand the advantages this approach.
Hot new thing
The InQuik bridge system is competing in a crowded market with various precast and steel truss bridges. To bring some objectivity to the process of bridge selection, in 2019 the World Bank undertook an evaluation of modular bridges. While the value of some criteria or their scoring could be argued, the Implementation of Innovative and Efficient Bridge Technologies project progress report (Rev A) does provide a comprehensive survey of modular bridging systems in common use in the Pacific.
As it turns out, InQuik was ranked first in the assessment. The ranking was based on a weighted multi-criteria analysis for five shortlisted bridge products. At the time, it was a somewhat bold move to rank InQuik first, as the company was only established in 2017 and therefore had a very short track record. In the four years since, InQuik had been specified on several projects, but never actually used for construction. The reasons for this have more to do with contractor preferences and their established suppliers than there being any fault with InQuik.
With the impetus of the World Bank supporting both the efficient bridge report and the SIRAP project, InQuik’s moment had arrived. All InQuik bridge designs are certified by engineering consultant SMEC and SMEC are also the design consultant on SIRAP – a neat synergy. Yet surprisingly, SMEC had designed conventional concrete bridges for the Bio crossings. It was during value engineering with contractor Reeves that InQuik was selected, due to its constructability advantages, namely no need to form and pour thick insitu concrete decks. An experienced contractor such as Reeves can identify these sorts of opportunities very quickly – having them involved at the design stage often derives positive outcomes.
What works
Let’s look more closely at those advantages.
Constructability is the most obvious one – no steel fixing on site (except stitch pours), preformed formwork, no temporary supports, lightweight components for cranage, no bearings, no quality issues with concrete cover. There are time and labour savings over traditional form-and-pour methods, but also over comparative modular bridges. Yet, in the Pacific context, the labour savings made by reducing time on site may not be welcomed. “Local content” is all the rage for donors, but more importantly, employing local labour is one of the greatest benefits a project brings to communities during the construction phase. Program savings are understandably seen as being to the benefit of contractors to increase profits, and of no advantage to communities.
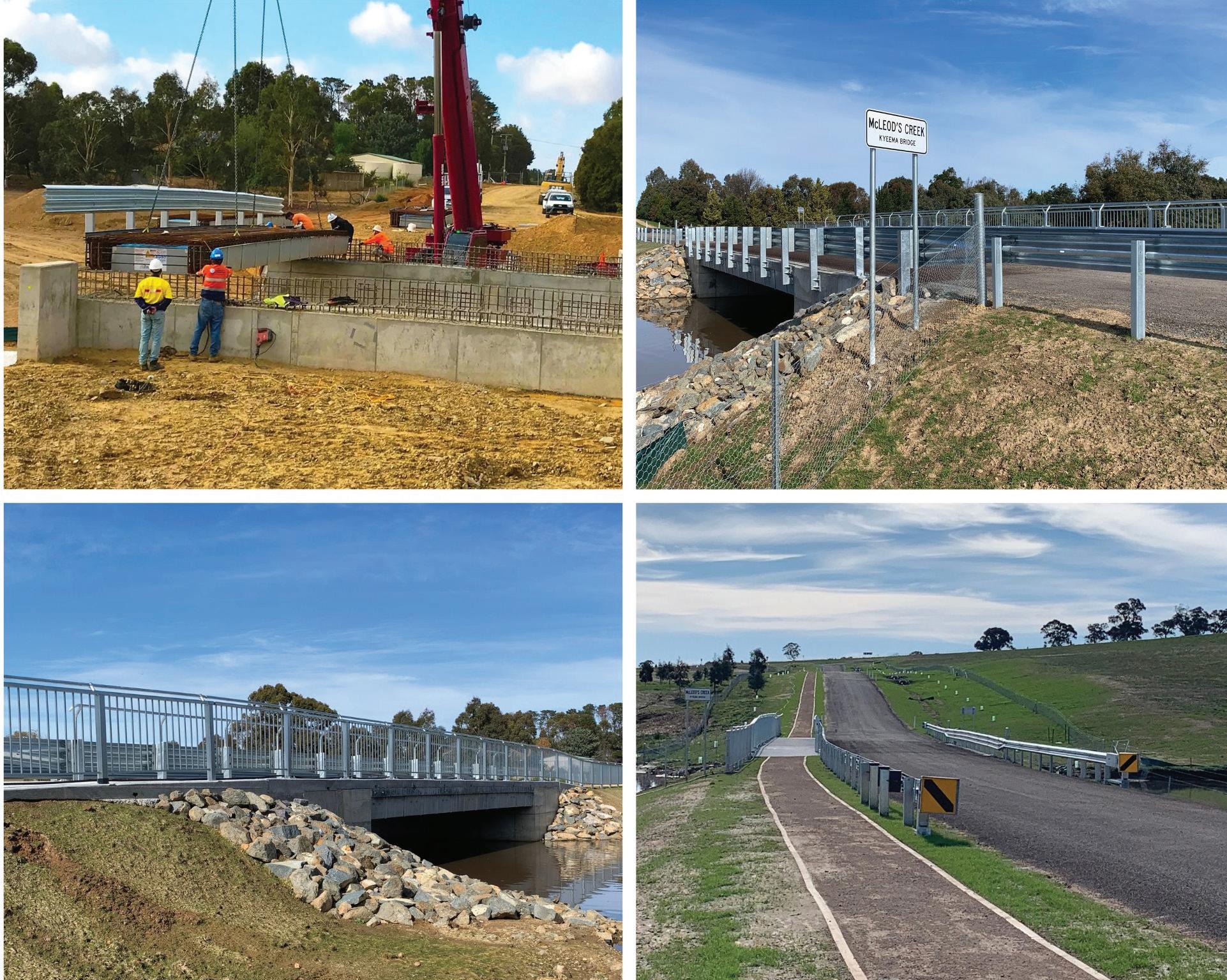
Maintenance
For the first 50 years, the maintenance regime should genuinely only consist of inspections, to ensure that the bridge is performing as expected. There are no bearings or joints or other moving parts that would require an intervention or replacement. This is a significant advantage in the Pacific, where maintenance funding and bridge expertise are hard to find.
According to the World Bank’s report (which oddly doesn’t make like-for-like comparisons for several of the key criteria, including cost), indicates that the cost of InQuik is comparative though not the cheapest. Unfortunately, the costs quoted are supply-only costs, not giving a true comparison of the difficulty or duration of a build. It scored well on-whole-of-life costs, but that was simply of function of low maintenance costs, not a true whole-of-life inclusive of demolition and re-use opportunities.
InQuik design complies with AS5100 (2017). In Solomon Islands, only T44 loading is required, but even that is overkill on a road that sees very few heavy vehicles. However, with a 100-year design life, having a structure of this quality opens up transport possibilities and access provisions for the unknown future.
We mentioned quality (steel fixing and concrete cover) is a constructability advantage, but to achieve B2 classification, which is needed for coastal areas, 50MPa concrete is required. That’s true of all concrete structures in this environment, but precast concrete may have an advantage here – namely that there’s no need to transport and mix high strength concrete on site, and the curing regime is better controlled. However, precast concrete’s major disadvantage is the transport challenges of moving large, non-containerised masses and the size of the cranage required to lift it on site. Stitch pours between precast slabs can also be a point of strength vulnerability, due to concrete variability between insitu and precast.
Specific to the Pacific
Some issues that will be faced in the Pacific that would not even be on a risk register for bridge construction in a place like Australia, are discussed below:
• Concrete batching – due to the volume and quality of concrete required, even if the site is close to a main town or city such as Honiara, mobile batching on site is recommended. Setting up a mobile concrete batching plant is only economical for larger projects
• Vandalism – how easy is it to remove railings – maybe railings, but other parts are less vulnerable to vandalism than other bridges. Vandalism of remote road furniture in the Pacific is less about wanton destruction and more about finding better uses for those assets
• Design interface. InQuik provides proprietary designs for the abutments, piers and superstructure. The piling and geotechnical design are the responsibility of “others”. This makes sense because there’s no such thing as a proprietary design for foundations. This design interface is not obvious in the InQuik materials and the need to engage another designer, one with piling expertise, could prove difficult.
Transportation is always a challenge when working in the islands – import of plant and materials and utilising a private barge. It is expensive and each time an item is handled it runs the risk of damage or loss. InQuik’s products are no doubt robust for transport, but the risk remains.
Does it go “in quick”
The InQuik bridge system does have advantages for time savings over traditional bridge construction. There are a few risks in using it that can be managed, if parties are aware. It does indeed go in quickly. This could make it of particular interest for disaster recovery jobs, especially for existing bridge locations with known geotechnical conditions. The onlookers will observe SIRAP’s InQuik trial with great interest.
The InQuik system is an innovative solution that has revolutionised the way bridges are built and replaced. This in-situ poured semi-modular concrete bridge was invented and commercialised in Australia and is now available internationally.
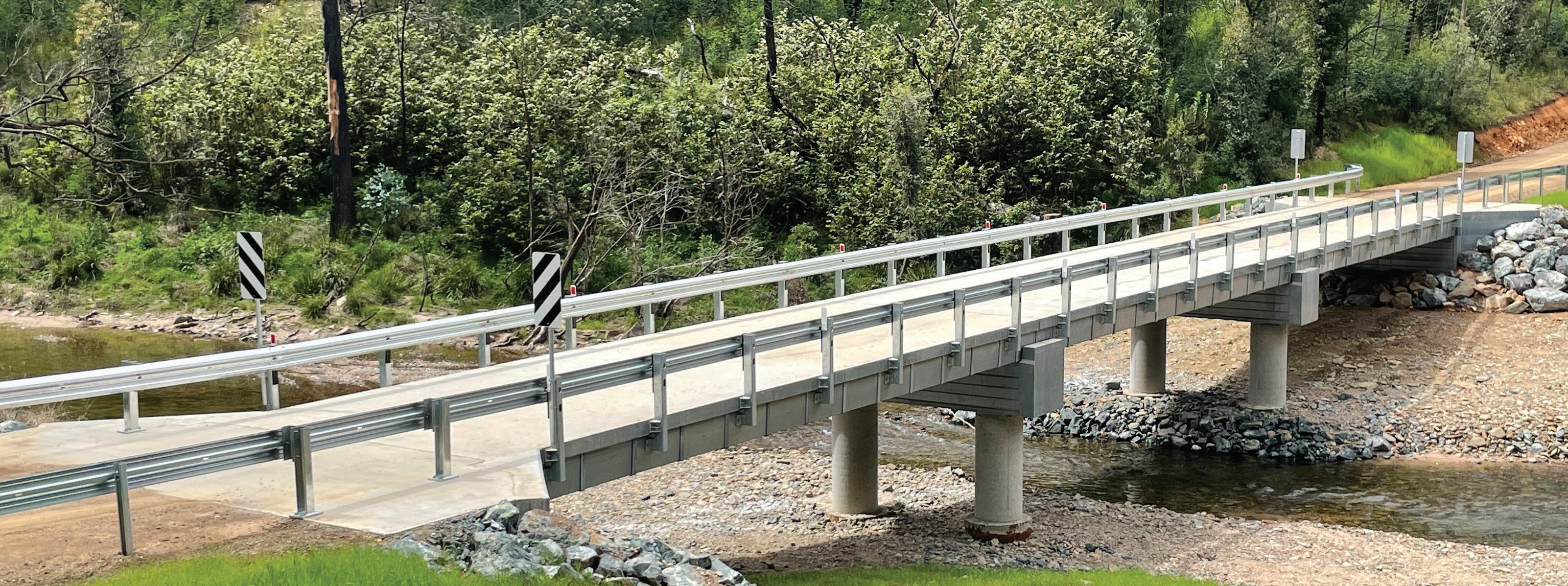
Suitable for single and multi-span bridges
enquiries@inquik.com.au
Reduces complexity and accelerates the bridge construction
Exceptional resilience and requires minimum to zero maintenance
Features an integral bridge design with no joints, enhancing its strength and durability
Can be built by low-skilled labour using only small cranes www.inquik.com.au enquiries@inquik.com.au www.inquik.comcoau