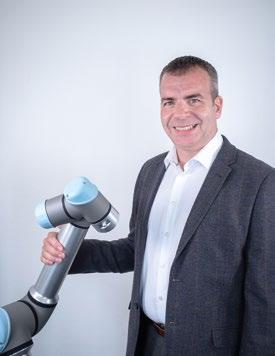
4 minute read
On second thoughts
WE NEED MORE ROBOTS
In the time of the coronavirus, robots can keep workers safe, and boost productivity argues Mark Gray, UK sales manager at Universal Robots.
During recent weeks, the coronavirus pandemic has largely dominated the headlines, impacting every sector and changing the way we work. As many sectors move their workforce online, it goes without saying that this simply is not possible in the manufacturing and packaging industry. The question now, is how can the packaging industry adapt to these new conditions, whilst staying productive and also creating a safe, hygienic working environment for employees?
Whilst the media narrative surrounding robots tends to focus on how automation stands to replace human workers, this couldn’t be further from the truth. In fact, even without a global pandemic, regional labour shortages and the need to up productivity all mean robots will be central to manufacturing in Europe and creating jobs in the sector over the next few years. During these times, protecting jobs should be the highest priority for businesses, and robots can help the industry to stay productive, safe and retain as much of the workforce as possible.
Automation will replace certain monotonous and cumbersome tasks and we do need to be mindful of the impact this will have on specific roles. However, it will also enable the human workforce to upskill and complete more rewarding tasks that offer better job satisfaction. For example, identifying areas where automation can enhance productivity, communicating this to the wider company and completing the final checks in the quality control process. For every task a robot assumes responsibility, several newer jobs can be created. For example, as a robot supervisor, in logistics or quality control.
For the packaging industry, robots offer myriad benefits to deal with coronavirus, from addressing regional labour shortages to increasing throughput. They come in all shapes and sizes, from industrial robots, engineered to lift heavy metal parts, to collaborative robots (cobots), designed to work alongside the human workforce.
If we look at the latter, thanks to their economic size and multiple safety functions, including motion and impact sensors, cobots can be placed directly on the factory floor, next to human employees. Most importantly, during these difficult times, they can remove the need for human contact with packaging, meaning that they not only reduce the risk of contaminating packages and impacting the end user, but also lessen the need for workers to touch contaminated materials. With the capability to complete repetitive, high-precision tasks, cobots can relieve workers of dull, dirty and dangerous work.
With benefits aplenty, it’s no surprise that globally, more and more companies are turning to cobots to better protect their employees and enhance their productivity. If we look more regionally, countries like Singapore and Germany are forging ahead with their adoption of automation, while the UK severely lags behind its G7 counterparts. Some argue that uncertainty around Brexit has contributed to this, others that scrapping the Manufacturing Advisory Service has made it difficult for companies, particularly SMEs, to get help and advice on how to automate. Perhaps the misguided perception that robots require vast sums of money and lengthy implementation downtime has also fuelled a hesitation to automate. Regardless of the reasons, the good news is that cobots are designed to address these concerns head on. Cobots are built with integration in mind. Many come as an out-of-the-box solution, meaning that even an untrained operator can unpack, mount and programme the cobot in less than an hour. For businesses, this means that they can maximise throughput and accelerate time-to-market. For workers, it means they can offload the most menial and repetitive aspects of their role to the robot, freeing them up to perform more varied and fulfilling duties.
In terms of the cost, cobots are an economic option for companies, particularly SMEs, to automate. Some are even available on a leasing programme, designed to offer greater cost control and flexibility to automation without a capital investment. This scheme also has the added benefit of adding units during peak periods to meet a spike in demand. This enables companies to maintain their competitive edge.
As early adopters like Europe demonstrate, robots are not something to fear, but welcome. They can drive business efficiencies and maximise productivity all while empowering the human workforce to learn new skills. The partnership between robots and human workers is bright and one that we should embrace with open arms. Universally, businesses may be suffering due to the pandemic, however, in the long-term, robots can provide a means to future-proof business operations in uncertain and fast-moving circumstances. n
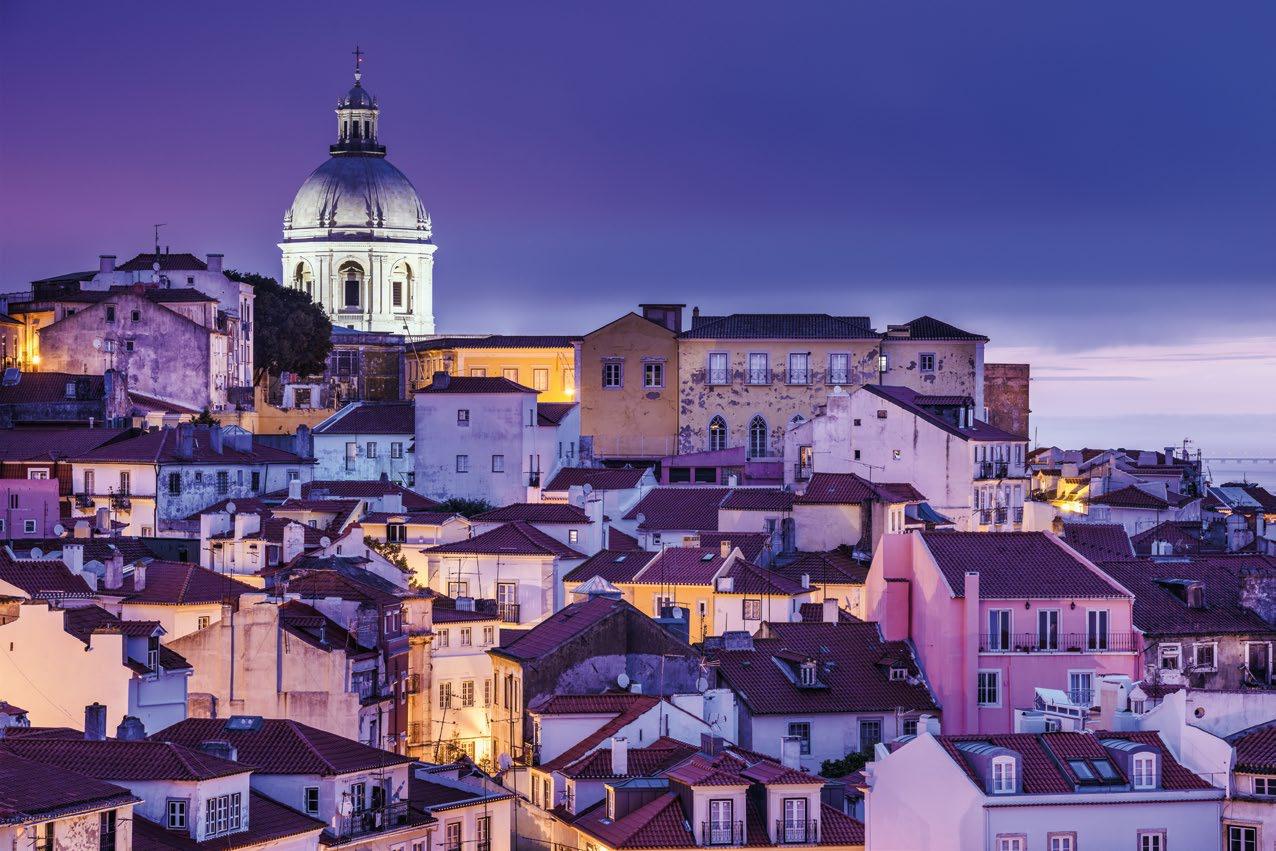
TWO DAYS OF INDISPENSABLE DISCUSSION IN THE EUROPEAN GREEN CAPITAL 2020
We’re bringing the value chain together for an interactive forum to examine new opportunities and explore how we can connect the dots.
Join us for the Sustainable Packaging Summit, featuring the Sustainability Awards 2020.
packagingsummit.earth
In alignment with:
thesustainabilityawards.com
Content partner: