
12 minute read
Is PET packaging sustainable?
SYNTEGON LOOKS TO THE FUTURE
In an exclusive interview with Fin Slater, Dr Michael Grosse, Syntegon’s newly minted CEO, talks strategic priorities, sustainability perspectives, and the challenges of rebranding an iconic and established organization.
FS: Until early January, Syntegon had been trading as Bosch Packaging Technology for 50 years. What was the reasoning behind a complete rebrand and what challenges does this pose to an established brand like Bosch?
MG: At the beginning of this year, Syntegon presented itself as an independent company under a new brand. Processing and packaging for a better life – that is our mission. We remain a global partner for the pharmaceutical and food industries and provide our customers with even more intelligent and sustainable solutions.
The main reason for the brand change is that our company is no longer part of the Bosch Group. Our new owner is the private equity and investment advisory firm CVC Capital Partners. With Bosch, of course, we are losing a famous brand with high appeal. However, as Syntegon we will sharpen our profile as a leading processing and packaging company and use the opportunity to optimize our products and services as well as our structures and processes to make them an even better fit for our customers.
FS: Can we expect any significant changes in direction following the rebrand and change of ownership?
Dr Michael Grosse has been CEO of Syntegon since March 2020 (formerly Bosch Packaging Technology).
MG: With up to 150 years of experience in individual machines, systems and services, Syntegon sets standards when it comes to developing innovative packaging and processing solutions and delivering tailored manufacturing processes designed to make high-quality products with utmost reliability. Our customers appreciate us for our reliable machines that enable smooth, efficient and safe production. In the future we want to further extend these close partnerships with our customers.
We will inspire the food and pharma industry with future-oriented solutions and contribute to the overall economic success of our customers. The newly gained independence enables us to be faster and even more flexible. While we used to be part of a large corporation with different divisions and a fixed organizational structure, Syntegon can now create a business framework that is leaner and an even better fit for the industry with a stronger focus on the key challenges and demands of our customers.
FS: What do you identify as your strategic priorities as a business over the coming year?
MG: ‘Customers first’ is our motto. Driven by the spirit of partnership with our customers, we are striving to improve the value of our solutions as well as our processes. We want to become faster and easier to do business with. This ambition includes, for example, reducing response times to customer enquiries or improving our service delivery. We will build on our deep technical expertise and application knowledge, paired with a comprehensive portfolio of products and services, driven by our relentless aim to become better, faster and more efficient in everything we do.
Of course, the coronavirus is on everyone’s mind and unites us in acting safely and responsibly. We have to lead our company, partners and families safely through this unprecedented crisis. Since the beginning, Syntegon has been continuously and closely monitoring the developments related to the spread of the virus. We regularly evaluate and adapt our actions in line with our values to never compromise the health and safety of our people.
FS: Sustainability is a topic that is currently dominating packaging-related discussions. What can machinery manufacturers like Syntegon do to help produce eco-friendly packaging solutions? How is Syntegon contributing to the needs of sustainability in terms of its packaging machinery portfolio and R&D?
HOW DO WE MAKE FLEXIBLE PLASTIC PACKAGING PART OF THE CIRCULAR ECONOMY?
All plastics packaging on the EU market must be economically recyclable by 2030, and major brands and retailers are targeting packaging to be 100% recyclable by 2025. Complex, multi-material flexible packaging is recognized as being challenging to recycle and will have to be re-designed in order to be recyclable.
In this webinar you will learn about how Dow is working together with industry partners to accelerate design for recyclability in food and consumer packaging applications using common processing technologies (e.g. extrusion, orientation and thermoforming) whilst maintaining production efficiency at packaging lines and using less material. Recyclable packaging will continue to support lower EPR fees and is in line with CEFLEX activities. Get inspired through real-life examples, enabled by Dow’s Pack Studios.

Learn more about AGILITY™ CE our high performance mechanically recycled plastic waste resin for industrial packaging that can be incorporated up to 50% to help meet your public commitments to using recycled plastic in packaging.
Gain insights into how we are advancing in our feedstock (chemical) recycling plans to make circular polymers from plastic waste that are equivalent to virgin polymers and which will fulfil stringent food contact regulations.
Finally, you’ll hear from our experts on the benefits of our sustainably sourced, bio-based plastics which offer close to 60% reduction in CO2 footprint versus conventional fossil fuel plastics, require no extra land resources and are not in competition with food. You’ll also gain an understanding of the role of mass balance accounting.
ON DEMAND WEBINAR
HOSTED BY PACKAGING EUROPE
Key learning objectives:
• Design for recyclability – how we can maintain high packaging efficiency and consumer convenience of flexible packaging while designing it for recyclability • Recycling – state-of-the-art mechanical and feedstock (chemical) recycling efforts of Dow with industry partners • Recycled contents – viable routes to incorporate recycled plastic into non-food and industrial packaging applications • Bio-based Plastics – learn about the benefits of our bio-based plastics offering and understand mass balance accounting
ON DEMAND LISTEN NOW
ON DEMAND
packagingeurope.com/integrate-flexible-plastic-packaging-into-circular-economy-dow-webinar/
SPEAKERS MARCO TEN BRUGGENCATE Commercial Vice President EMEA
ROMAIN CAZENAVE Group Marketing Director Packaging EMEA
KARIN KATZER Marketing Director
Global Pack Studios
CAROLINA GREGORIO Lead Marketing Manager, Food & Specialty Packaging
EMEA
KATE GERAGHTY Director of Advocacy EMEA
JUDITH HICKS Senior Business Communications Manager
EMEA
HOST
TIM SYKES Brand Director Packaging Europe
Packaging and Specialty Plastics (P&SP), a business unit of Dow (NYSE: DOW), combines R&D, worldwide reach, broad product lines and industry expertise to deliver high performing technologies for food packaging, hygiene, infrastructure, consumer goods and transportation. As one of the world’s largest producers of polyethylene resins, functional polymers, and adhesives, and enabled by Pack Studios, we are a leading collaborator and innovator in sustainable application development for a circular economy of plastics. Working across print, digital and live media, Packaging Europe is the leading intelligence resource for European packaging professionals. Our mission is to connect forward thinkers across the value chain with the latest developments in packaging technology and materials, making sense of innovation in the context of the core business challenges packaging is required to meet.
The Shaped Paper Pod prototype ‘Pearl’ is based on the formability of the FibreForm ® material from BillerudKorsnäs and is processed on machinery from Syntegon.

MG: Syntegon’s vision is to develop intelligent and sustainable solutions for everyone. We see it as our responsibility to deliver technology that can process the most environmentally friendly materials as efficiently as possible while using as few resources as possible. We support our customers on the path to a sustainable future with material testing, machine applications, innovative packaging designed to meet the requirements of products, transport modes, and regional circumstances.
In primary packaging, we are pursuing two approaches to produce sustainable packaging: one is to use mono materials rather than conventional multilayer films, and the other is to use paper packaging as an alternative to plastic. By producing narrower sealing seams, we can realize considerable additional material savings. Technologies like amplified heat sealing or ultrasonic sealing support these approaches. Secondary packaging, which is usually made of cardboard anyway, is primarily about making it even more suitable, robust and variable for e-commerce applications. Moreover, we relieve recycling flows by not using glue.
FS: Bosch, Syntegon’s former parent company, has pledged to become carbon neutral by 2020. Does Syntegon have any similar aspirations towards carbon neutrality? “With Bosch, of course, we are losing a famous brand with high appeal. However, as Syntegon we will sharpen our profile as a leading processing and packaging company.”
MG: Our mission ‘processing and packaging for a better life’ also includes keeping our ecological footprint as small as possible. Syntegon has more than halved its energy consumption relative to the value added in the past ten years, and we will continue our efforts to save energy and emissions. Our focus is on further improving energy efficiency and increasing the share of renewable energies. Since this year, for example, all of our European production sites have been sourcing ‘gold standard green electricity’ from renewable energies. In addition, we are continuously working on improving the energy efficiency of our machines. In this way, we also contribute to a better environmental balance for our customers.
FS: Other than sustainability, what are the key market drivers in the packaging / CPG industry to which Syntegon will respond?
MG: Consumer markets are becoming more and more volatile. The number of products that dominate markets for extended periods will continue to dwindle as product life cycles shrink. Competition will intensify as new manufacturers penetrate the food market with innovative products and services.
For the pharmaceutical industry, we see two major developments: on the one hand, specialized drugs will be produced in lower quantities for small patient
SUSTAINABLE & RESEALABLE FLEXIBLE LIDDING SOLUTIONS FOR FRESH FRUITS & VEGETABLES (PRODUCE)
A collaborative approach to A collaboration between Bostik and improving consumer safety, Terphane aimed to address these convenience, and reducing both challenges for the produce market and food & plastic waste offer a resealable lidding solution with
Flexible, resealable lidding offers lower costs to manufacture, shorter many advantages for consumers lead times, fewer manufacturing steps, including food safety, convenience, and and a lower environmental impact. reduced food and packaging waste.
While there are resealable lidding options available on the market today, few have been successful in offering an economical and effective reseal lid for the produce market, where high moisture resistance and tamper evidence is important.



A BOSTIK
ON DEMAND WEBINAR
HOSTED BY PACKAGING EUROPE
Learning Objectives:
• Learn about the sustainable and convenient benefits of resealable, flexible packaging • Listen to an overview and comparison of today’s resealable lidding options for produce • Hear how collaboration between
Bostik and Terphane addressed gaps in current resealable lidding solutions, such as limited tamper evidence, complexity to manufacture, and poor moisture resistance • Discover a novel resealable lidding film design that meets consumer preferences and is producible without laser scoring equipment
ON DEMAND LISTEN NOW
ON DEMAND
https://packagingeurope.com/sustainable-resealable-flexible-lidding-solutions-for-fresh-fruits-vegetables/
SPEAKERS HOST
KASRA MIRMESDAGH Technical Service Engineer Bostik
ELLEN SMITH Senior R&D Engineer Terphane
Bostik, an Arkema Company, is a global leader in bonding solutions. Bostik’s Advanced Packaging Global Business Unit offers a comprehensive portfolio of bonding solutions to the packaging industry including lamination adhesives, heat and cold sealing, reclosing solutions for lidding films, adhesives for tapes & labels, hot melt adhesives for case and carton sealing.
VICTORIA HATTERSLEY Senior Writer
Packaging Europe
Terphane, a subsidiary of Tredegar Corporation (NYSE:TG), is a vertically integrated specialty PET film manufacturer with over 40 years of film production expertise. With a core technical competency in resin technology and co-extruded films, Terphane is addressing the changing demands of the flexible packaging and industrial markets with an expanding range of valueadded films and metalizing proficiencies.
populations. On the other hand, the price pressure on generics will continue to rise, as will regulatory quality and data standards. The challenge for our customers is to respond quickly to changing requirements, bringing products to market much faster without jeopardizing quality and their long-term planning.
Syntegon provides the right answer to these challenges with highly flexible equipment. Designed to start manufacturing immediately without long lead and delivery times, they are ready to accommodate additional options and retrofits. We offer flexible machines that process a wide range of packaging materials. Whenever the need arises, we can respond to changing customer requirements for materials, product formats, volumes and speed. We have modular systems at our disposal that facilitate fast delivery and immediate commissioning. Our teams of experts advise and assist customers in the design of production lines, materials, and product flow.
FS: We’ve previously reported on Syntegon’s collaboration with BillerudKorsnäs. What is the importance of partnerships like this to accelerating innovation for the packaging industry, and can we expect more of the same from Syntegon in the coming months?
MG: Of course, we are working closely with leading packaging material suppliers – in both paper and plastic. We believe that solutions can only be developed in close cooperation with material experts as well as users and brand suppliers. Together with our Swedish cooperation partner BillerudKorsnäs, we have developed a new packaging concept called Shaped Paper Pod, which enables creative and sustainable packaging solutions made of paper.
The Shaped Paper Pods are produced with BillerudKorsnäs’ FibreForm paper on a newly developed Syntegon paper form machine. Based on organic materials, the FibreForm paper enables up to ten times deeper embossing than conventional paper. This creates eye-catching 3D effects. Sandwich spreads, confectionery, cookies, facial cream – the possibilities are many and diverse. Manufacturers are moving towards plastic-free solutions with predominantly fibre-based packaging materials that are tailored to their given product. “Consumer markets are becoming more and more volatile. The number of products that dominate markets for extended periods will continue to dwindle as product life cycles shrink.”
FS: You were previously on the board at Tetra Pak – what learnings from that role will you be bringing to your new role as CEO of Syntegon?
MG: During my almost 17 years at Tetra Pak, I had the privilege to deepen my understanding of the key challenges of the food production industry and how to leverage technology, innovation and services to address them. Knowhow is the entry ticket, but the passion, the focus and mindset of the people really make the difference.
FS: You’ve talked about your desire to focus on improving customer satisfaction and profitability – do you have any particular initiatives/strategies in mind to help you do this?
MG: Everything we do according to our mission ‘processing and packaging for a better life’ is about creating value for our customers and will determine their satisfaction with our products and services. That is why we are focusing even more on the value and reliability of our services and want to deepen the spirit of trustworthy and caring partnerships with our customers.
Profitability is a key aspect of a company’s future viability. Our financial strength through sustainable profitable growth determines our ability to attract the best talents and to invest in our own and our customers’ future. We therefore have to sharpen our focus on what really matters and simplify our operating model. n
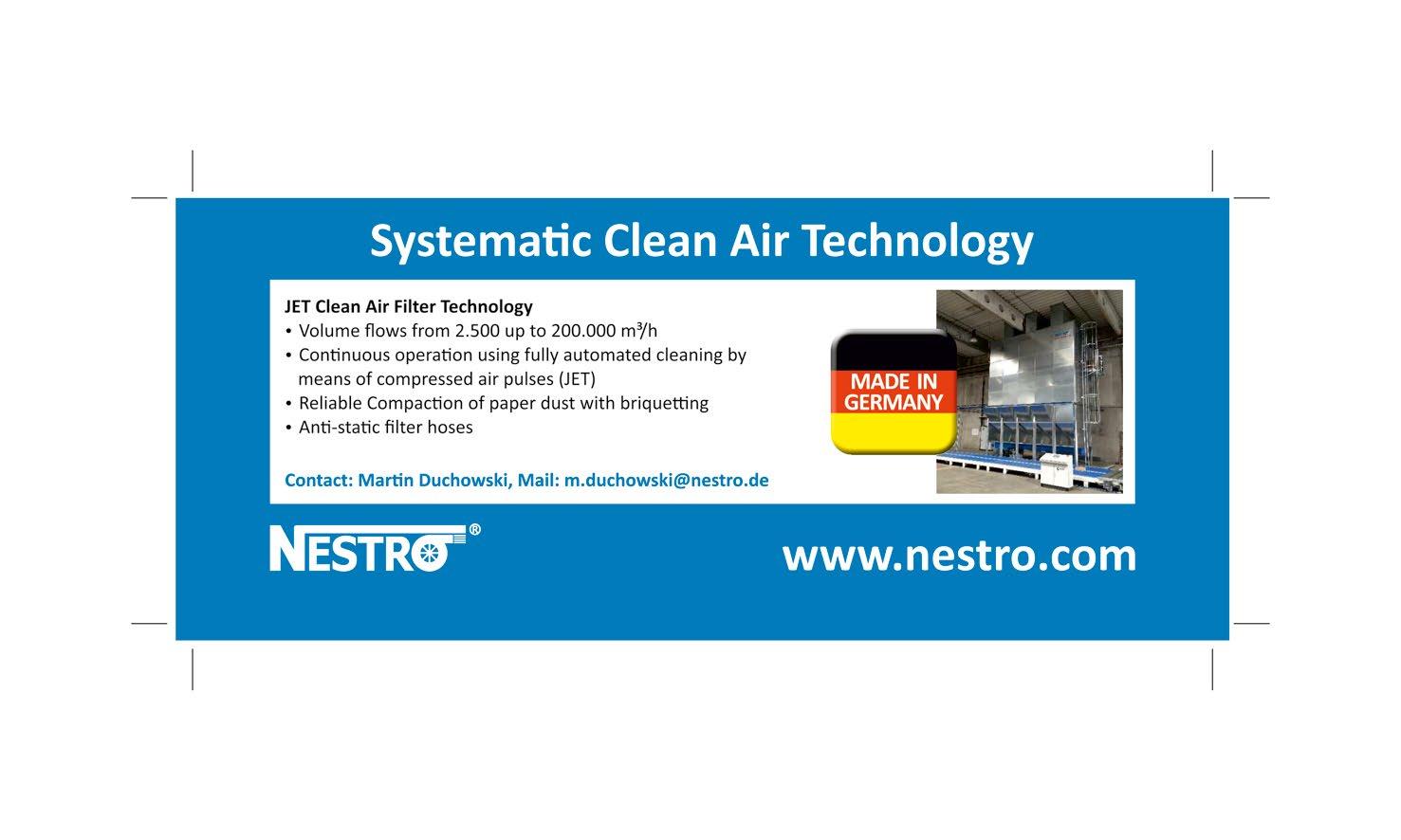