
10 minute read
ENHANCING THE PROPERTIES OF POLYMERS
ENHANCING THE PROPERTIES OF POLYMERS
As we settle into 2021, we take a glance at how some of the leading players in materials science are continuing to address the need to improve the recyclability and functionality of packaging polymers. Victoria Hattersley spoke with representatives from Covestro, Dow and Imerys.
The wide variety of polymers on the market today go a long way to meeting our many and varied packaging needs. However, as we know not all of them are as recyclable, or recycled, as others – whether because of their inherent properties, the infrastructure isn’t there, or because they consist of multiple layers that can’t be separated in existing recycling streams.
At Packaging Europe we always try to keep on the pulse of ongoing developments in polymer research and innovation. In recent years, we have seen clear recurring themes such as monomaterials, biobased plastics and chemical recycling.
Our industry experts today are all from companies involved in the packaging chain at the materials science level rather than packaging production itself. Here the focus is on enhancing polymer properties to improve recyclability, improve barrier properties, reduce material volume, improve impact resistance and so on.
Maintaining mechanical properties
One way to enhance properties is through including additives to polymers at the start of the manufacturing process – an area where Imerys, which provides a wide variety of mineral solutions to enhance the properties of finished products and address sustainability requirements, is heavily involved.
“The current challenge is to ensure that mechanical properties, which tend to deteriorate during recycling processes, are maintained or even enhanced to enable them to meet ever more stringent specifications and remain cost-effective,” says Kelvin Thomas, Polymers Development Manager at the company. “Talc can be added to recycled plastic compounds to restore mechanical performance – for example, a recycled PP compound containing a 20% loading of Steagreen® talc can match the performance of a non-recycled, talc-filled PP compound and can therefore be used for high performance applications.”


Compatibilization, reprocessing and separation
Another area a lot of big players are investing in when it comes to polymer additives is compatibilizers, which can not only improve recyclability but also, crucially, allow the more efficient use of post-consumer waste – thus contributing to the all-encompassing goal of circularity.
“Where packaging is currently made up of different layers and materials to meet brand owners’ functional needs, it is difficult to separate and break these down for recycling,” says Carsten Larsen, Commercial Director Recycling EMEA & APAC, Packaging & Specialty Plastics at Dow. “That’s why we also offer compatibilizers, which work in a similar manner to a detergent that can combine oil and water, allowing the homogeneous mixing of plastic waste and enhancing its properties. Compatibilized post-consumer waste can be used in flexible film applications.”

At K 2019 Dow showcased its design for recyclability portfolio, where its offerings included concepts for simple multi-layered structures without barriers, more complex packaging with customized barriers for food protection, as well as conversion process redesign – including the use of compatibilizers to help enhance the mechanical recyclability of multilayer packaging and a spout insertion technology.
Dow is also investing in innovation and new technologies to produce high quality resins with plastic waste content. It has been partnering with Fuenix Ecogy Group to recycle plastic waste into pyrolysis oil to produce new polymers which it says ‘will be of the same quality as materials using virgin feedstocks and can be used in all applications, including food packaging’.
Imerys, meanwhile, has developed a mineral-based compatibilizer, ImerLink®, to create effective links between blends of polyethylene and polypropylene – usually incompatible – through a reactive process. This, says Kelvin Thomas, results in a material with improved properties with an optimum stiffness/toughness balance.
“PE and PP are often compatibilized using interfacial agents such as olefin block copolymers (OBCs), but the resulting material can still have two phases. The blend is not truly compatibilized. OBCs can also be quite expensive. ImerLink® is effective because it not only changes the miscibility of the PE and PP phases but also creates a new network of bonds between the phases and the coated mineral. This allows the use of postconsumer plastic waste which is rarely pure PP or PE but more often a mix of both due to contamination.”
Covestro, meanwhile, is involved in a research project, TERMINUS, to investigate the debonding of polymer layers of packaging materials. Its aim is to make the mechanical recycling of laminates less dependent on the adhesive, or in other words, to enable debonding ‘on-demand’ so that layers can be recycled in their material streams to create higher value recyclate.
Recycling challenges
However, there are limitations to mechanical recycling, as Carsten Larsen points out. “For example, you cannot easily recycle many types of food packaging into new applications because of contamination issues and stringent packaging regulations. Mechanical recycling also degrades with each round of recycling. This not only limits what it can be used in, but often requires additional virgin resins to increase its performance – this adds more weight and increases CO2 emissions.”
That being the case, chemical recycling offers a very promising future alternative for cases where mechanical does not go far enough. Dow sees chemical recycling (or feedstock recycling, to use an interchangeable term) as a complementary alternative to mechanical as it ‘allows waste to maintain its value and become infinitely recyclable’.
“Feedstock recycling is therefore necessary if we are to meet both the EU’s legally binding plastics packaging recycling target of 55% by 2030 and to deliver possible binding European targets on recycled content,” adds
Carsten. “It will also enable recycled content in highly regulated applications such as food contact packaging; and meet our voluntary commitment under the EU’s Circular Plastic Alliance of 100K MT of recycled plastic to European customers by 2025.”
But moving back to mechanical for a moment, it’s no secret that large parts of the industry believe the future lies in the development of increasingly functional mono materials that can increase recyclability in existing waste management systems.
“With polyethylene (PE), for example, it’s possible to offer mono-material solutions that enable high performing packaging which can make recyclability possible,” says Carsten Larsen. “Unlike multi-material conventional packaging, mono-material packaging can offer greater recyclability without losing the benefits such as optimum product protection.”
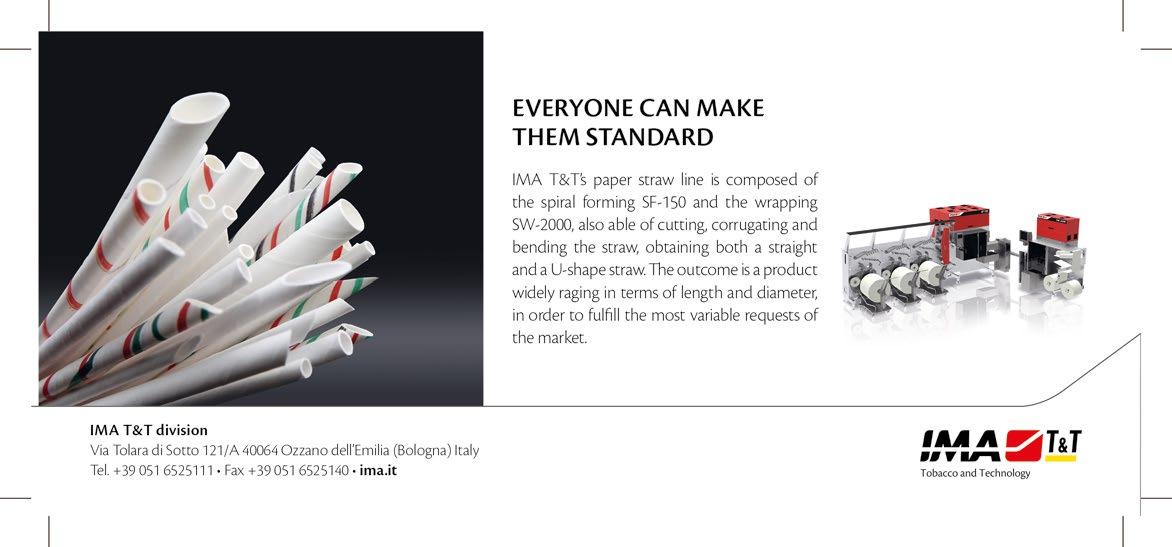
Compostables and biopolymers

Exciting developments in compostable polymers and novel biopolymers are also ongoing. While they do not yet hold a large share of the market – and there are still many challenges to be overcome, as we shall see – it’s undeniable that they offer promise for the future.
There are areas where compostability, in particular, can be very useful – particularly when organic content can be used to bring nutrition back to the soil, such as with coffee capsules. When it comes to biodegradation, Covestro has launched ‘the first raw materials that can biodegrade under different environmental conditions’.
However, Christos Lecou, Marketing Manager, Industrial Adhesives at the company, does draw our attention to an issue with which many of us will now be familiar: “There is a controversy as to whether composting of packaging should count as recycling. Take the example of an empty crisp pack. Here the material is not further used. It gets lost in the environment, forming mainly CO2 and water without giving back nutrition to the soil. Therefore, wherever possible waste materials should be utilized rather than being disposed into the environment. We are participating in several projects to generate precursors for our raw materials back from waste streams. For instance, the project BioCatPolymers focuses on bio-catalytic possibilities to extract polymer building blocks out of woody biomass.”
Our contacts at Imerys also note the rising demand for biobased and biodegradable materials, but highlight challenges such as the current low availability of feedstocks and raw materials, processability windows, a need to improve mechanical properties and thermal resistance for packaging applications, and a relatively low cost-effectiveness.
“For rigid applications, process-wise, talc improves PLA and PHA (and that’s a non-exhaustive list of examples) melt strength, eliminating strand breakage during cooling and facilitating compound granulation. As an effective nucleating agent, the use of talc can also significantly increase the crystallization speed of some biopolymers,” explains Anaïs Berjeaud, Polymers Technical Support Manager.
Being a mineral solutions provider, Imerys has developed Eco-Delink™, an engineered calcined kaolin, in order to enhance compostability. “At 20% loading, in PHA, Eco-Delink™ provides faster degradation as well as improving processing conditions,” explains Mike Bird, Development Manager Plastics & Rubber.
Our industry insiders have given us much to consider here. But all of this is a mere snapshot of the ongoing innovation in packaging polymers. Whether it’s the growing use of polymer nanocomposite packaging materials or increased interest in biobased materials such as PEF (a durable plant-based polymer) as a potential alternative to conventional plastics, there is much on the horizon. n
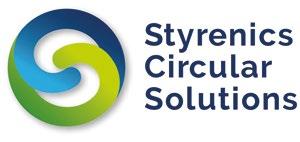
TRUE CIRCULARITY. FOOD CONTACT. POWERED BY STYRENICS.
ON DEMAND WEBINAR
HOSTED BY PACKAGING EUROPE
How can circular polystyrene best meet the growing demand for high quality recyclates suitable for food contact applications? What are the achievements so far in fulfilling the intrinsic circularity of styrenics and what are the milestones? Which environmental footprint of the different polystyrene recycling technologies can be expected? How does recycled polystyrene compare with virgin polystyrene in the production process of food packaging?
These issues are addressed in an online event by Styrenics Circular Solutions (SCS), the value chain initiative to increase the circularity of styrenic polymers, together with Packaging Europe. The event is now available to watch on demand. Featuring:
• Delivering on the unique circular potential of polystyrene
– Jens Kathmann, Secretary-General,
Styrenics Circular Solutions
• On track with food contact mechanical recycling of polystyrene
– Herman Van Roost, General Manager
Feedstock & Mechanical Recycling
• Advances in depolymerisation food contact recycling of polystyrene
– Dr. Norbert Niessner, Global Head of R&D, INEOS Styrolution and Chair
Technologies, SCS
• First insights into a comprehensive
Life Cycle Analysis for polystyrene
– Regino Weber, Research Associate
Division Polymers, Neue Materialien
Bayreuth GmbH
• Recycled polystyrene as a drop-in solution – the converters’ perspective
– Anabela Ferreira, Co-owner and
Executive Board Member, Intraplás; Iain
Sturges, Chief Procurement Officer,
COEXPAN; Tobias Strasser, Managing
Director, Greiner Packaging
• Circular roadmap for styrenics – a look ahead
– Jens Kathmann, Secretary-General,
SCS
• Q&A session
ON DEMAND LISTEN NOW
https://packagingeurope.com/advances-in-the-closed-loop-recycling-of-polystyrene/
ON DEMAND
HOST CHRISSI SCHOENFELDER Styrenics Circular Solutions, Chair Advocacy & Communications
SPEAKERS JENS KATHMANN Styrenics Circular Solutions, Secretary General
HERMAN VAN ROOST Styrenics Circular Solutions, General Manager Feedstock & Mechanical Recycling
DR. NORBERT NIESSNER INEOS Styrolution/SCS Global Head of R&D, INEOS Styrolution and Chair Technologies, SCS REGINO WEBER Neue Materialien Bayreuth GmbH, Research Associate Division Polymers
ANABELA FERREIRA Intraplás, Co-owner and Executive Board Member IAIN STURGES COEXPAN, Chief Procurement Officer
TOBIAS STRASSER COEXPAN, Chief Procurement Officer
Styrenics Circular Solutions is the value chain initiative to make the circular economy a reality for styrenics through game-changing plastics-to-plastics recycling technologies and partner-driven solutions. It aims to transform the styrenics industry by engaging with the entire value chain to realise polystyrene’s unique circularity capabilities and to extend closed loop food contact recycling beyond bottles to new food grade applications. Working across print, digital and live media, Packaging Europe is the leading intelligence resource for European packaging professionals. Our mission is to connect forward thinkers across the value chain with the latest developments in packaging technology and materials, making sense of innovation in the context of the core business challenges packaging is required to meet.