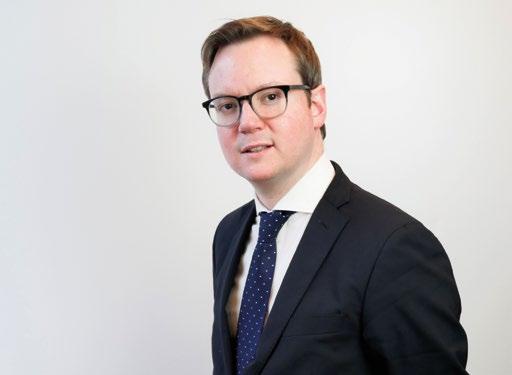
13 minute read
Building a coherent circular economy: The view from the industry
BUILDING A COHERENT CIRCULAR ECONOMY: THE VIEW FROM THE INDUSTRY
Over the past few weeks, we have been asking representatives from key organizations across the packaging industry two questions: What are the biggest roadblocks to a circular economy in packaging today? and How must the packaging sector you represent respond to these in the coming years if we are to achieve circularity? Here is what they had to say.
STEEL: ALEXIS VAN MAERCKE, SECRETARY GENERAL OF APEAL
Recyclability and recycling infrastructure are not given enough thought to landfill. It is an ambitious aim, but if recyclable materials – particularly when packaging is designed, and although the use of reusable pack- permanent materials – continue to be wasted, a truly circular economy aging is growing, consumers are unlikely to abandon the conveni- cannot be achieved. ence of disposable packaging altogether. The 2025 Vision will be underpinned by action in four key areas, including a
The solution is multi-faceted but must include the promotion of materials that focus on optimizing separate waste collection, establishing a scrap quality standretain their inherent properties after recycling, known as permanent materials. ard, the collection and sorting of steel closures, and designing for recyclability. The Circular Economy Action Plan Separate collection is the best way of guaranteeing high-quality input (CEAP) 2.0 – a cornerstone of the into recycling operations, so establishing a scrap quality standard is also European Green Deal – is designed to important. To maintain quality in the steel for packaging scrap value chain, strengthen the economy, protect the quality control must start when the material is at the sorting facility. environment and eliminate waste. It Improving the recycling rate of steel closures will also make a significant recognizes the importance of perma- contribution in the drive towards zero steel packaging to landfill, but there nent materials, as well as the need is currently a lack of clear sorting instructions and low awareness among to increase high-quality recycling and citizens, plus ineffective sorting techniques in a number of facilities resultmove away from landfilling waste. ing in collected steel closures, caps and lids being lost. Reflecting these aims, APEAL APEAL believes designing for recyclability will underpin the successful recently announced its 2025 vision implementation of all these measures, helping ensure every product placed Alexis Van Maercke for recycling – zero steel packaging on the market can be recycled efficiently.
FLEXIBLES: GRAHAM HOULDER, PROJECT COORDINATOR, CEFLEX
Let me cite three roadblocks to circularity that are top of mind today. Firstly, the inertia behind the current ‘linear’ system designed to meet minimum recycling targets – especially for plastic packaging – and speed of transition to circular funding and policies needs to be addressed and corrected. The aspirations and costs associated with circular materials are very different to those in a system designed and funded to meet recycling targets at minimum cost.
Secondly, recognizing chemical recycling as a critical piece of the circular economy for plastics puzzle and commercializing it at scale for required capacity in the coming three years.
Thirdly, the amount of debate and energy still spent on design guidelines for (flexible) packaging plastics. We know what needs to be done here. The focus needs to switch towards developing end market pull for recycled plastics by making them financially competitive against the virgin equivalent.
The true cost of recycling different formats and materials needs to be reflected in the Extended Producer Responsibility contribution, without cross subsidization between materials or formats. EPR fees paid by flexible packaging need to be ring fenced to collect, sort and recycle flexible packaging and not all plastic packaging or collection and sorting of paper, metals and glass.
CEFLEX stakeholders in the front part of the value chain, i.e. material producers, film converters, brand owners, need to accelerate demand for recycled materials by using them in their plastic grades, flexible packaging and products on the market.
EPR needs to facilitate this by ensuring recycled plastics are always a better business
Graham Houlder
proposition than a virgin equivalent by modulating the subsidies for these materials to allow them to do so.
Parts of the collection, sorting and recycling value chain – now including many material producers – need to invest in the required infrastructure to deliver the CEFLEX circular economy vision. EPR systems (led by the brand owners) need to underwrite these investments in developing the needed collection, sorting, recycling capacities of mechanical and chemical recycling by reducing the investment risk for these companies through longer contracts at a guaranteed rate of return on their investments.
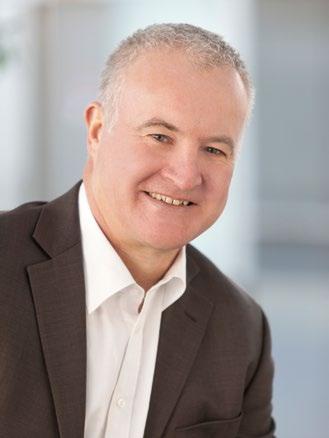
PAPER: ANNA PAPAGRIGORAKI, SUSTAINABILITY DIRECTOR OF CEPI
The Green Deal aims to enhance circularity in all industrial value chains. Meeting this ambition is not a walk in the park, unless the following roadblocks are dealt with: • EU policy incoherence • Failure to recognize the substitution potential of fibre-based products • Lack of harmonized collection systems to further increase recycling of paper packaging • Fragmentation of the EU single market for waste and secondary raw materials • Lack of availability of affordable clean energy.
The pulp and paper industry has achieved a 29% decarbonization from 2005 to date. Paper is recycled at a rate of 72% in Europe, which is the highest recycling rate for paper in the world. Paper based packaging is even recycled at 84.6%. However, we are also tackling the aforementioned roadblocks to continue to achieve circularity.
For example, by substituting fossil products with forest-based products, our industry prevents the use of fossil materials and fossil CO2 emissions in other sectors. Such a reduction can even be multiplied by leveraging our expertise in the circular economy. This combination also makes the pulp and paper industry an important factor in reducing emissions in other sectors.
In addition, the transition to a green and circular economy cannot happen without recognizing the role of the consumer. The European Paper Industry participated in the EU Product Environmental Footprint Pilot project in 2011 and again in 2013-2018: we were one of the 15 sectors that delivered PEF Category Rules. The Intermediate Paper Product PEF Category Rule is a detailed LCA calculation method for paper that will be converted into finalized products such as packaging, print and tissue.
Cepi has developed recyclability guidelines and guidance on how to implement separate collection. Engagement with the value chain is also key to achieving circularity. 4evergreen is a forum to engage and connect industry members from across the fibre-based packaging value chain. 4evergreen members committed to reach 90% of fibre-based packaging recycled by 2030 via design for recycling guidelines and assessment protocol and separate collection.
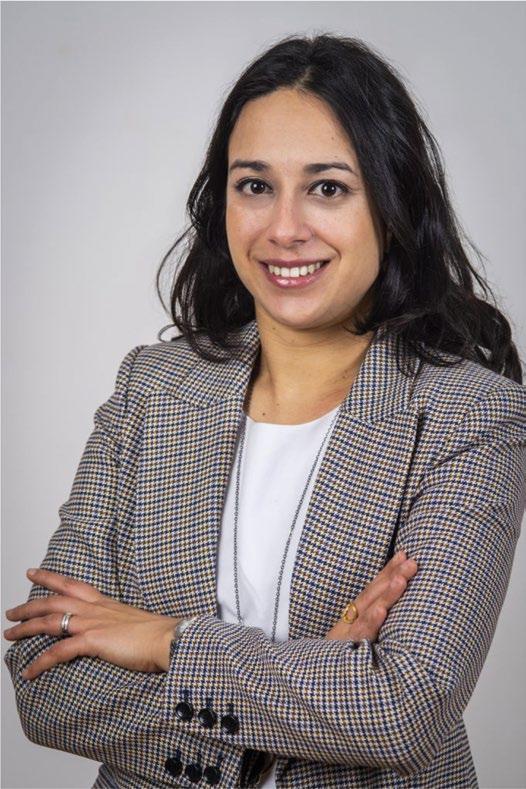
Anna Papagrigoraki
PLASTICS: SANDER DEFRUYT, LEAD, NEW PLASTICS ECONOMY, ELLEN MACARTHUR FOUNDATION
Since 2018, more than 1000 organizations have united behind a common vision and targets for a circular economy for plastic – to eliminate the plastic items we don’t need; innovate so all plastics we do need are designed to be safely reused, recycled, or composted; and circulate everything we use to keep it in the economy and out of the environment.
The momentum behind a circular economy is huge, as seen in the Global Commitment and the Plastics Pact network, but still there is far more that must be done. The vast majority of progress so far is towards a recycling economy, rather than a fully circular economy, and will leave us stuck in our current model of production and consumption, albeit with a recycling loop added at the end. This downstream, end-of-pipe thinking lacks the ambition needed to reach a circular economy and constitutes one of the biggest roadblocks to a circular economy in packaging today.
Recycling is undoubtedly part of the solution, but it will only take us so far. A recycling economy is more costly than a comprehensive circular economy, emits far more greenhouse gas, and is unable to truly address the problem of plastic waste and reduce ocean leakage. Beyond recycling, we need to fundamentally rethink how we make and use plastic and move our innovation efforts upstream, so that rather than focusing on how we are going to deal with a pile of waste, we focus on how to make sure that waste
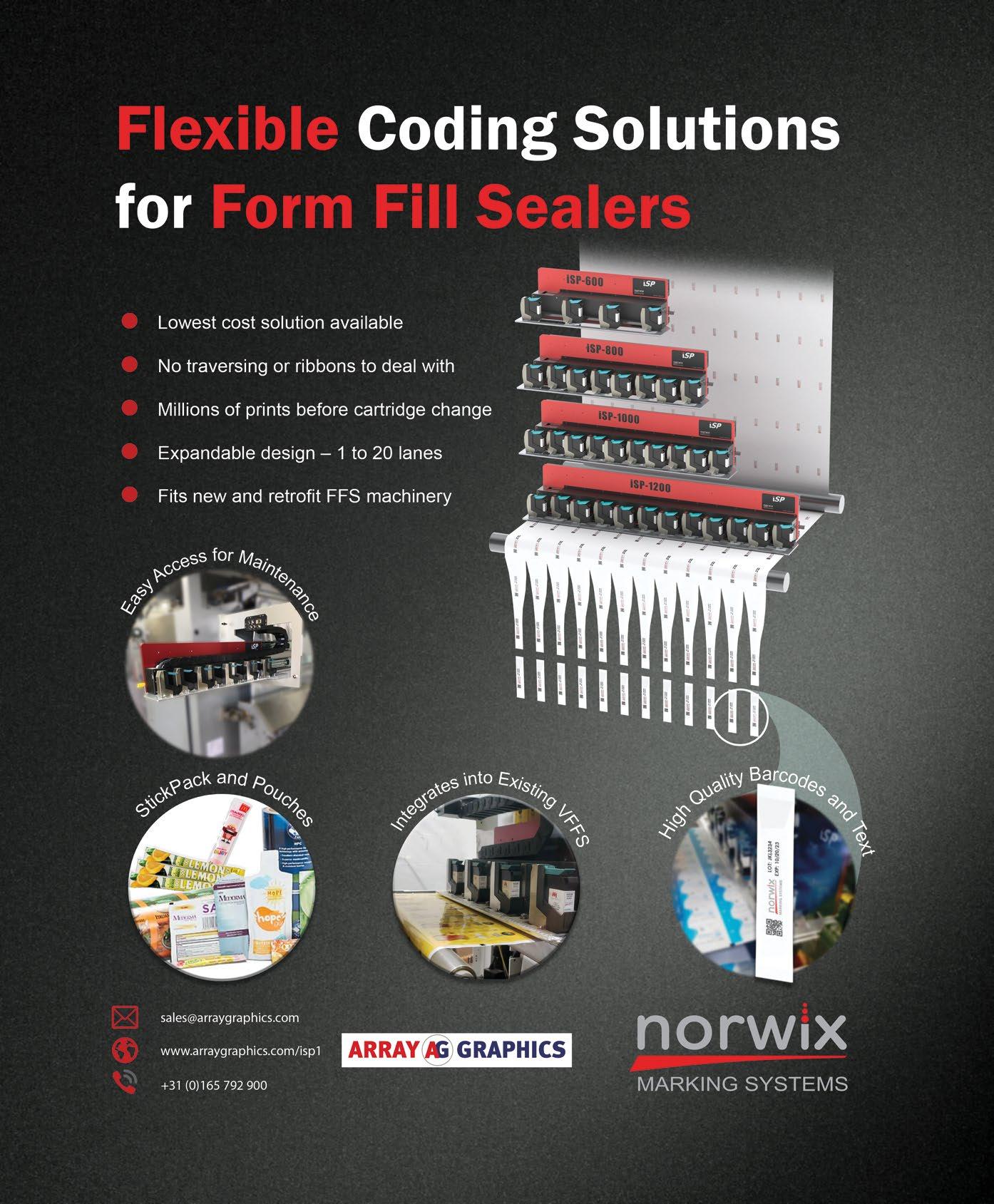
Sander Defruyt
is not produced in the first place. This means moving beyond incremental tweaks to packaging design and rethinking products and business models as well.
We need to massively increase our innovation efforts towards business models that deliver products to customers without creating packaging waste, and we should take full advantage of the huge opportunity offered by reusable packaging models. We understand this can pose operational difficulties and takes time piloting and exploring, but it is worrying to see that the majority of businesses are not genuinely exploring these solutions. We urgently need to see that changed.
In order to assist companies with this, the Ellen MacArthur Foundation recently published Upstream Innovation: A Guide To Packaging Solutions, containing practical guidance and real-world examples.
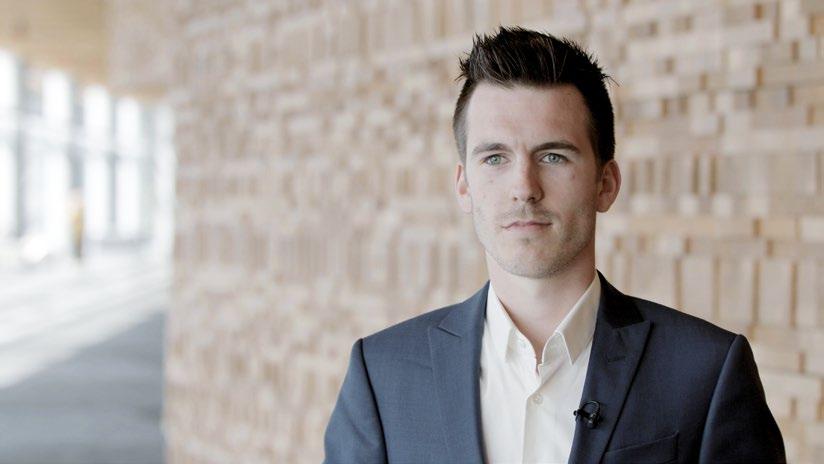
GLASS: MICHAEL DELLE SELVE, HEAD OF MARKETING AND COMMUNICATIONS, FEVE
Areal shift to a circular packaging industry requires investing in Extended Producer Responsibility (EPR) Schemes to supply the manufacturing industry with good quality recyclates. Deposit Return Schemes (DRS) can be an option only for those solutions which are not yet collected in an effective manner, and not to replace systems that work correctly.
No compromise should be made in any instance on consumers’ health and safety. This is a roadblock that must be strengthened to halt any packaging solutions that could become a potential threat because they include recyclates! And finally, a circular economy must be economically viable: circular materials must make business sense.
Glass is already a healthy, reusable and infinitely recyclable packaging and as such we are at the centre of a well-functioning circular business model. To improve it, we must address our major challenge – the high carbon footprint in the production phase.
Today, 80% of our CO2 emissions come from the fossil fuels we use for the melting phase and 20% from the virgin raw materials we use to make glass. Therefore, we have designed a twofold sectorial CO2 reduction strategy to complement individual companies’ decarbonization paths.
Firstly, to address the 80%, we want to scale up the use of renewable electricity in the melting phase. This will reduce CO2 emissions by 60%. The innovative electric melting technology is currently limited to small-scale furnaces for flint (clear) glass with limited recycled glass content. The ‘Furnace for the Future’ industry project should allow us to scale it up, and use it with coloured glass and increased recycled content.
Secondly, to address the other 20% we want to increase to 90% the collection of glass packaging in Europe by 2030 (up from 76% today). This will allow us to increase further the share of recycled glass in the batch and reduce virgin raw materials. We have recently launched ‘Close the Glass Loop’ – a multi-stakeholder platform of local authorities, brands, recyclers, extended producer responsibility schemes and producers.
We also just created the Glass Hallmark for brands to communicate with consumers about their packaging choice and to reuse or recycle it as a great action they can do for the Circular Economy.
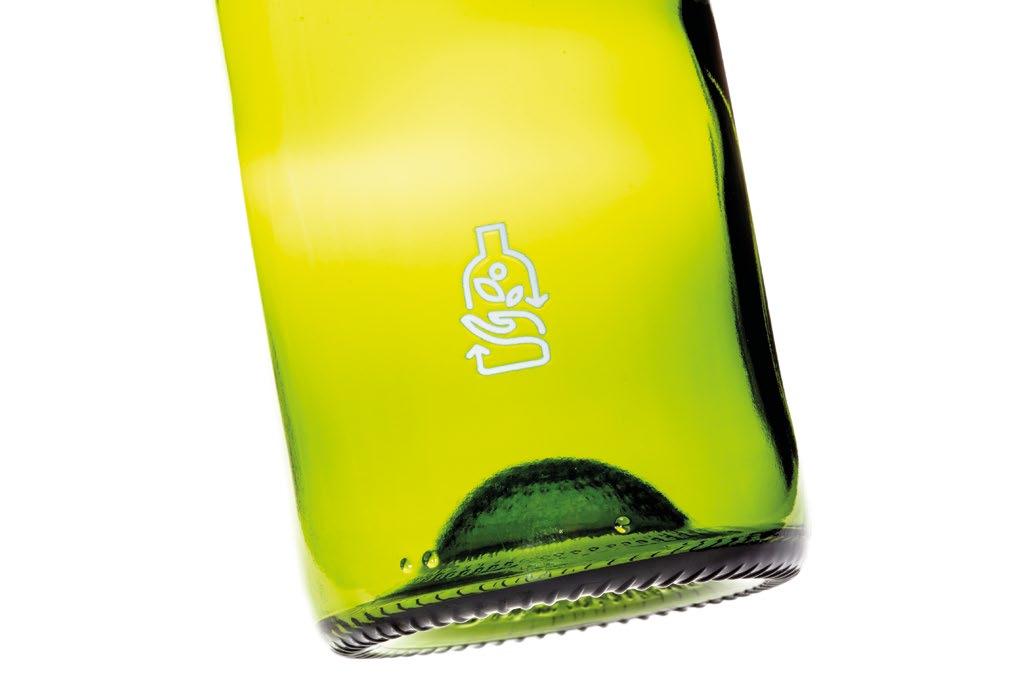
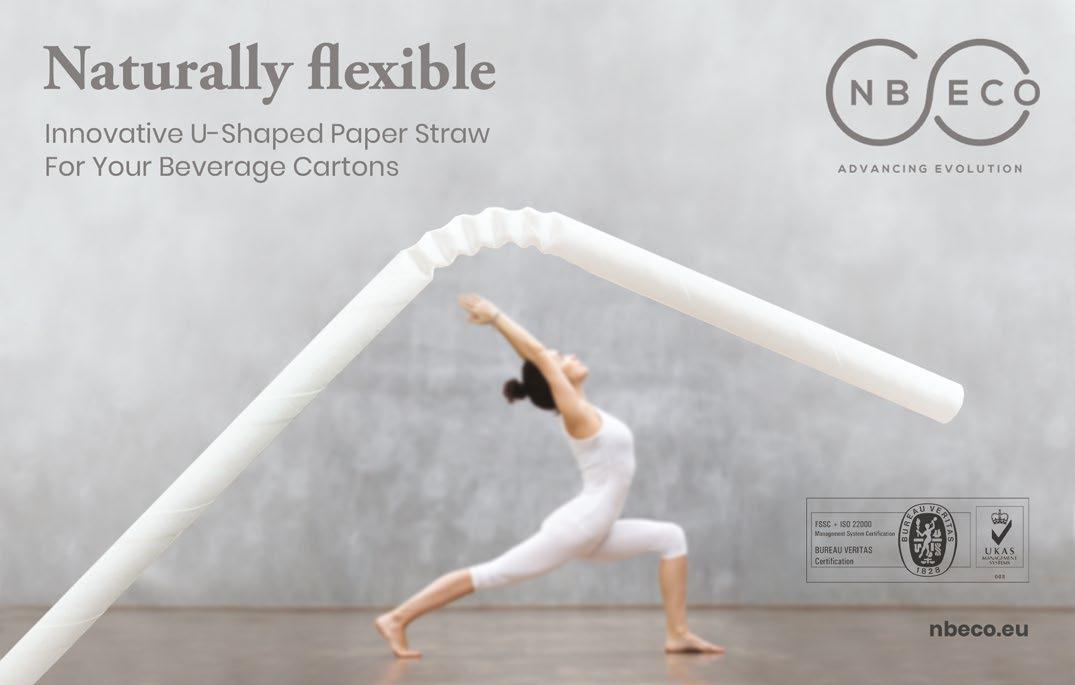
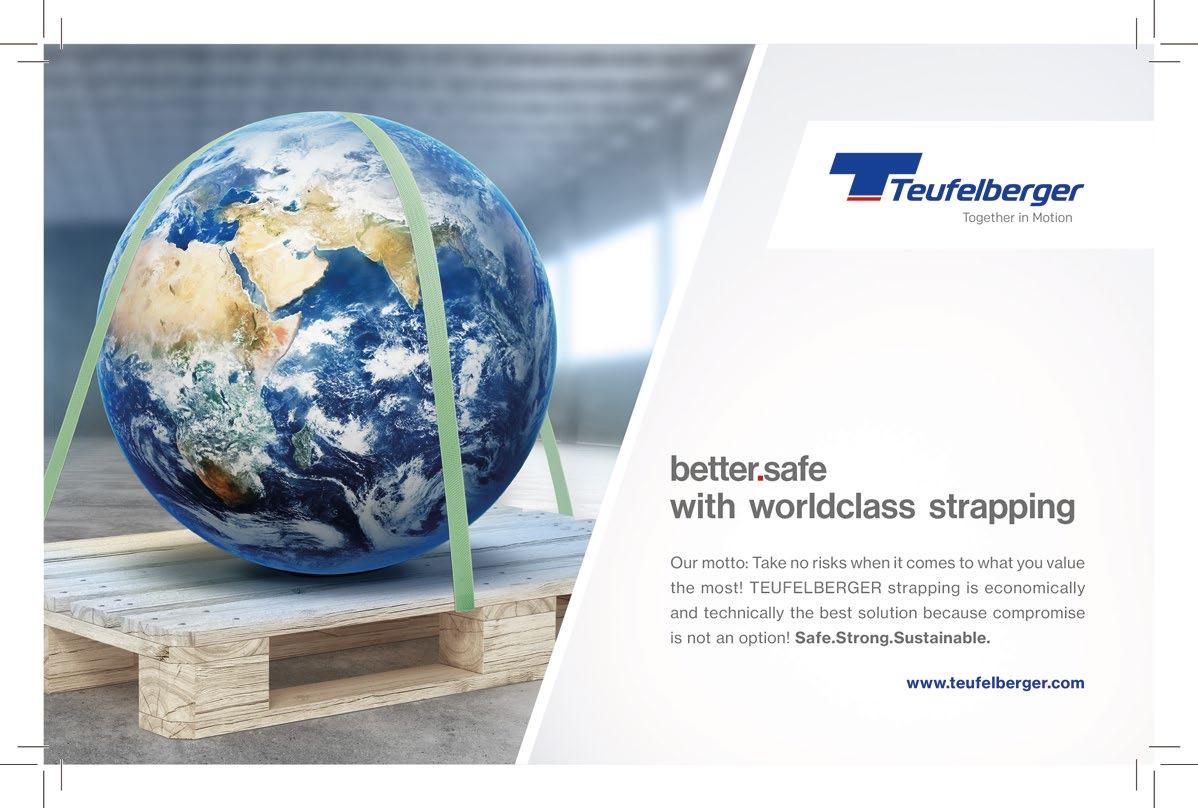
PLASTICS & RECYCLABILITY: PAOLO GLEREAN, CHAIRMAN OF RECYCLASS & PRE BOARD MEMBER
When it comes to moving the needle on making plastic packaging laboratory testing of a product or new technology in a recycling process fully circular one of the main challenges is lack of recyclability. are used to continuously update these documents. These guidelines grant
The priority is, in the first place, to redesign plastic packaging recyclability certification. to be compatible with recycling technologies. This can be achieved with Once the package is recyclable it can be used in high-end applications. Fola common methodology to assess recyclability based on solid scientific lowing that logic, RecyClass developed a scheme to track use of recyclates to results. It must be a dynamic to include any improvements in sorting and boost trust in the use of recycled. It is based on a chain-of-custody concept to recycling technologies as well as allow for coherent monitoring of shares of recycled materials and their origin. new outlets for recycled material. There is no future for plastics without plastics recycling which must be How to put this approach into based on high-quality input materials. The way forward for the industry is practice? That is where RecyClass to re-design plastics by applying science-based tools. This means that any comes into play – a cross-industry innovative packaging must be tested before being placed on the market. initiative, led by recyclers, convert- Encouraging innovation while ensuring compatibility with recycling will ers, brand owners, raw material build a reliable circular economy where recycled plastic is used for the same producers and waste management applications as primary plastic. companies, working on advancing A harmonized, factual approach would ensure the credibility of the plastic packaging recyclability and environmental claims for plastic products and the credibility of the plastics uptake of recyclates. industry while creating a level playing field for recycled plastics. In line with RecyClass is based on scientifi- that RecyClass works on harmonizing recyclability definition, design-forcally elaborated Design for Recy- recycling guidelines, recyclability assessment methodologies and recycled Paolo Glerean cling Guidelines where findings from content calculation methods.
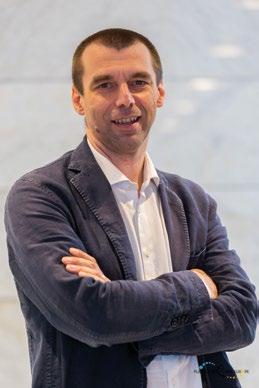
POLYOLEFINS: VENETIA SPENCER, SECRETARY GENERAL, PCEP
One of the immediate roadblocks to polyolefin packaging circularity is the disconnect between available recyclates and the demands of the end markets. This is true for both quality and quantity. The variety in collection and sorting infrastructure is a clear roadblock to large-scale recycling of polyolefin waste streams and generation of high quality secondary raw materials. Greater implementation of design for recycling is also vital to improving quality of the recyclates. On top of which there is already a significant gap between the quantity of post-consumer polyolefin packaging collected (c.12.5MT in 2019) and the current installed recycling capacity in Europe of just c.4.5MT (when operating at 100% capacity) for all polyolefins.
That is why PCEP has called on the European Union, member states and all economic actors to use the €1.8 trillion pandemic recovery package to invest in forward-looking infrastructure that will accelerate the transition to circularity.
At PCEP, the entire value chain is collaborating to transform the polyolefin system from one designed to collect for disposal, into one that collects to keep. Collaboration throughout the polyolefin value chain is vital if we are to achieve our goal of systemic transformation. We need transformative action based on three principles: designing out waste; keeping products and materials in use; and increasing the volumes of polyolefins recycled into high-quality new raw materials. All of which requires a supportive enabling policy framework.
A priority area that PCEP is actively working to address is the use of recyclates to establish circularity for food contact and similarly sensitive applications such as cosmetics and personal care packaging. The legal framework needs to evolve to support all recycling technologies, and the value chain needs to establish the scientific basis for evaluating the safety of recycled polyolefins.
Another important aspect of circularity for polyolefins is to explore and evaluate the business models, infrastructure needs and environmental impacts of reusable and refillable packaging.
Finally, it is key that we bring players from across all packaging types together, to ensure that the new, transformed system works for everyone involved. n
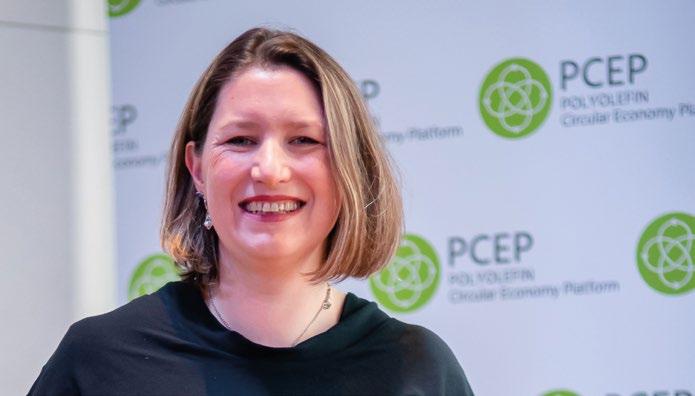
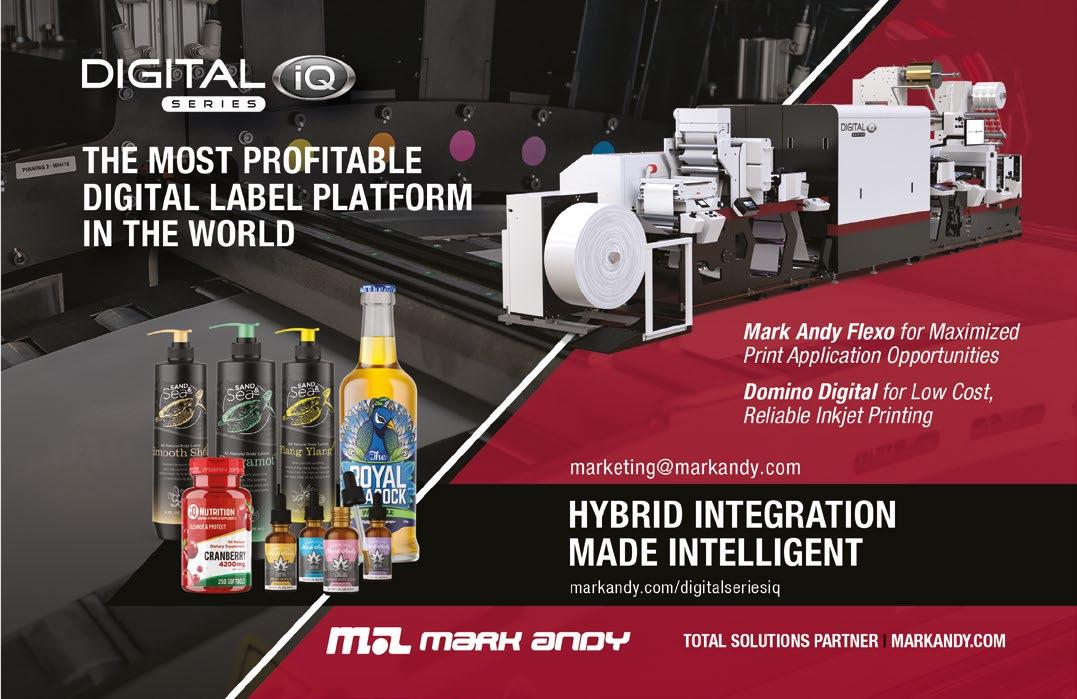

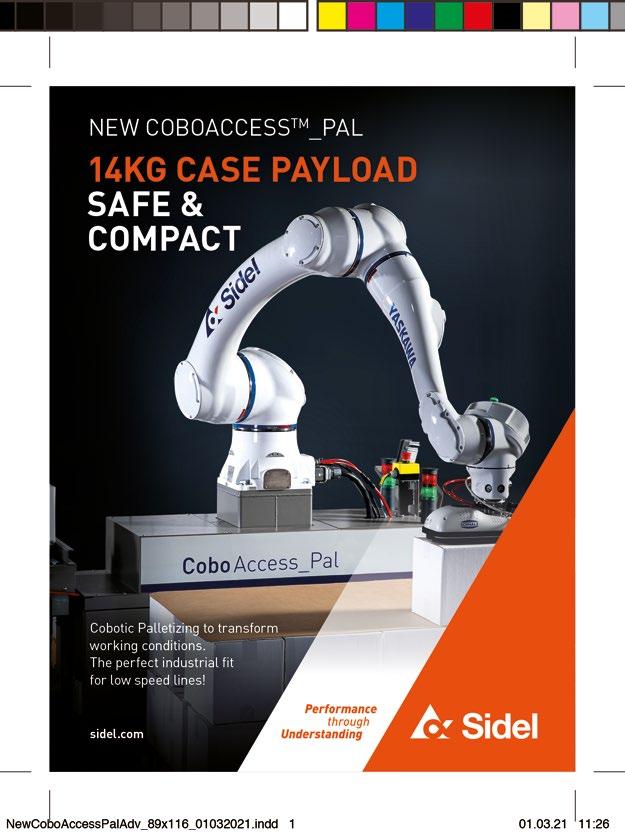