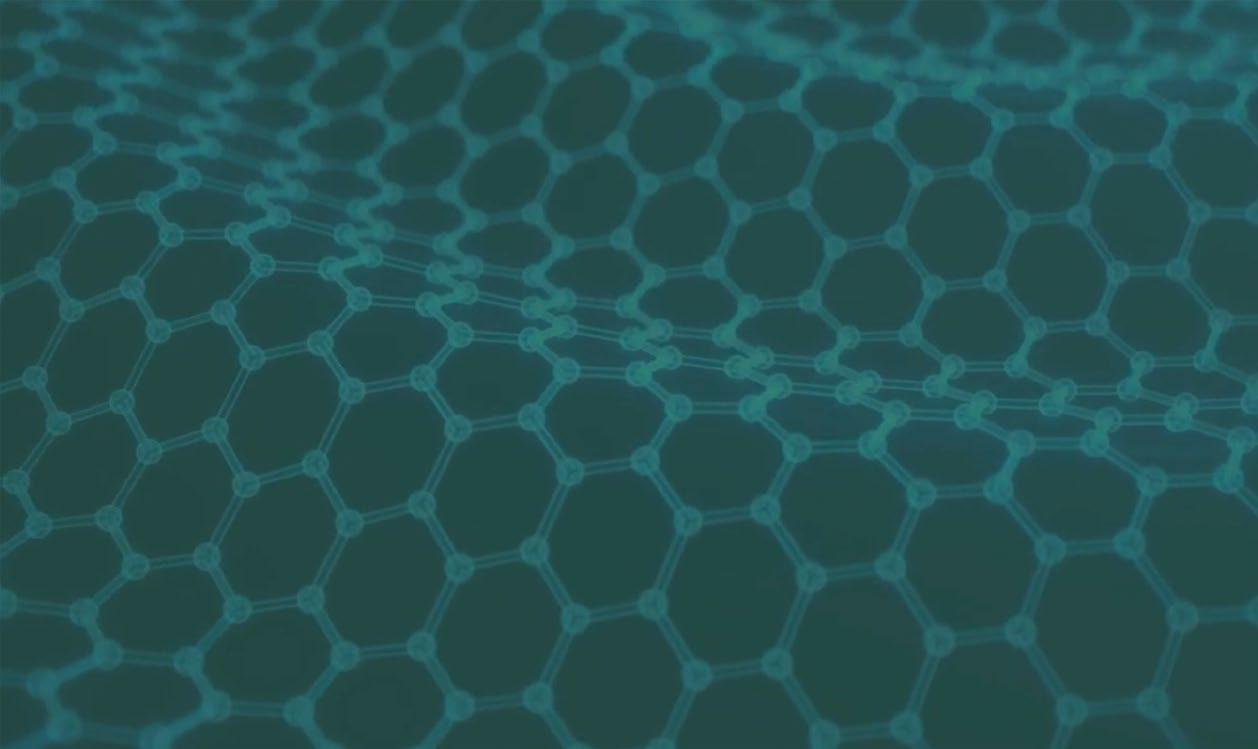
9 minute read
Rovema: Tackling the multi-material and sustainability challenges
ROVEMA: TACKLING THE MULTI-MATERIAL AND SUSTAINABILITY CHALLENGES
Demand for sustainable packaging solutions is continuously growing. Consumers nowadays often demand paper packaging for their products, which poses a range of challenges to packaging machines. Sometimes, of course, flexible plastics packaging, especially monomaterials, remain a better packaging material both from a sustainability and functionality point of view. Here, the flexibility of being able to seamlessly switch between paper and flexible plastics is key.
Elisabeth Skoda discusses the challenges and opportunities when it comes to packaging demanding products in both plastics and paper with ROVEMA, and looks at trends and solutions in the sector.
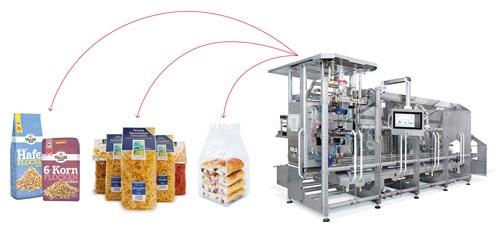
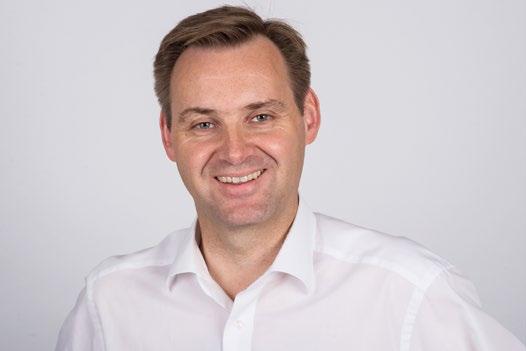
Brands are increasingly concerned about the potential publicity and damage that can result from images of their branded plastic packaging in the waste stream or being featured in discussions of sustainability and waste. As a consequence, food manufacturers face the urgent challenge of reducing plastic, increasing paper and increasing recyclability, while simultaneously mitigating the negative impacts on manufacturing efficiency, logistics and product safety and quality.
Ingo Hamel, ROVEMA’s Head of Innovation and R&D is keen to point out that ROVEMA has already been involved with paper packaging materials for several years.
“For the past three years, we have had a machine in our test centre dedicated exclusively to paper packaging material testing. Here we test the latest developments both based on specific customer requests or in direct cooperation with packaging material manufacturers. This way we can support customers at an early stage in the decision-making process for machine-compatible paper packaging materials”
A pack is only as good as its seal, so the company also continuously develops them further, for example through special geometries, better heat distribution and heat transfer.
“The optimized motion control of our machines enables us to realize the longest possible sealing times per cycle. We also consistently and continuously adapt our machine software to the special requirements of new packaging materials. The servo-motor drives thus run with even smoother movements to start in a soft manner, reducing forces on packaging material and machine,” says Mr Hamel.
Material flexibility
ROVEMA’s machines have been prepared for processing a wide variety of paper packaging materials, he adds.
“Today, there are paper material options for products that require only low barrier properties, and whose machine processability and output rates are almost equal to plastic composite results.
“In principle, we are able to convert any existing machine to specific bag shapes or to new alternative packaging materials, including papers, at the customer’s site.”
However, as things stand today, paper is not yet the best solution for all packaging tasks, and it is important to understand paper as a packaging material, which differs seriously from plastic packaging materials in terms of handling, look and feel.
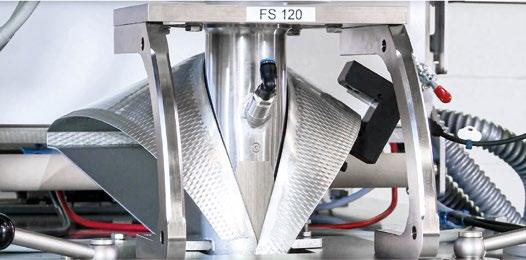
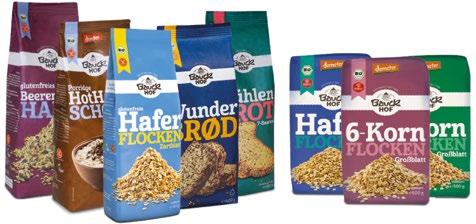
“Current papers, including barrier papers, are not suitable for every packaged product due to limited water vapour, gas and grease barriers. In addition to considering sustainability aspects, product protection also plays an important role. Especially for highly sensitive products such as baby food, grated cheese, coffee or pet food, a recyclable plastic packaging material makes more sense than a non-recyclable paper packaging material with a barrier, as for these products in particular, the barrier layer needs to be very thick and often results in the paper-based packaging being non-recyclable,” says Mr Hamel.
Making the switch
For manufacturers who want to satisfy rapidly shifting consumer expectations without full-scale reinvestment in their vertical bagging infrastructure, ROVEMA in many cases can modify existing equipment to run paper – and even to run both paper and plastic, and the company is on hand to support companies with their switch from plastics to paper, and vice versa.
Mr Hamel explains that if a machine has been prepared for the processing of paper and plastic packaging materials, customers can usually implement a changeover between these two packaging material types themselves within the usual format changeover times.
“Important elements here are the format set, folding and sealing tools, and an adapted motion profile when forming and sealing the bag. The focus is on not damaging the more sensitive paper packaging material. In addition, sealing temperature and sealing pressure must be significantly changed compared to plastic packaging materials. This is easily possible as standard for all ROVEMA machines on the market with servo-motor jaw drive and side gusseted tools (tuck-in fingers). In addition, the changes between the packaging materials can be saved as a recipe in the HMI.”
Different types of food come with their own challenges when it comes to packing them, and each product has certain properties that must be taken into account during the packaging process.
“In the case of pasta, for example, care must be taken to ensure gentle feeding, as sharp edges resulting from breakage can pierce the packaging material, and an excessively high proportion of damaged pasta is not well received by the consumer. Dusty products, like oat flakes, have completely different requirements.” explains Mr Hamel.
Case study – Altmühlthaler Teigwaren
Germany-based company Altmühlthaler Teigwaren recently switched its pasta packaging to paper following consumer demand, and the company chose a ROVEMA SBS system to allow it to grow flexibly.
A single version of the SBS 250 with one Form Fill and Seal machine has been installed, and the company reports that the changeover to paper was managed smoothly.
The compact SBS block packaging machine can offer differentiation of products at the point of sale, flexibility for a wide product range and 40 different bag top shapes. It enables the processing of different packaging materials, is flexibly expandable and offers conveyor filling for fragile products.
Case study – Bauck
Looking at another example where ROVEMA’s SBS is successfully used, the Demeter farm Bauck packs gluten-free flakes and flours in paper bags. The different products have different requirements, and with the help of the ROVEMA SBS Twin packaging machine, it is easy to switch between different bag top shapes, packaging materials and format sizes – including block bottom bags. Bauck uses pre-made paper bags and paper bags from flat film web. The latter are also produced with SBS packaging machines from ROVEMA. Bauck worked on testing and optimizing the system with ROVEMA at their technical centre ‘Technikum’. In this instance, Sappi Guard Nature 1-MS was used, a paper based packaging solution with integrated barrier against mineral oil (MOSH/MOAH) and grease and heat sealable properties. Production started with block-bottom bags after Easter 2021, a format that is still quite rare on the market. This bag shape posed a technical challenge and adjustments of downstream process steps. However, this was outweighed by the fact that the compact block-bottom bags saves transport and storage costs. Bags and cartons become flatter, more units fit on the pallet.
The company switched to paper bags for the majority of their product range, but stuck to plastic for products such as oat pops, as they absorb moisture, which makes them less suitable for using paper. Product protection is key here.
Both paper bags and plastic bags can be produced on the SBS Twin from ROVEMA, at Bauck in formats from 250 grams to 1-kilogram bags.


Before the oat flakes fall into the bags, they are transported directly from the silo to the auger feeder, a special feature, as flakes are often dosed with multi-head weighers.
Filling expertise
As mentioned above, packaging in bags from the flat film can be significantly more efficient and cost effective than using pre-fabricated bags. This is supported by the method of low-dust and compacted dosing through the VacuumPowder Filler (SDH), which results in a substantial increase in dosing accuracy of up to 50%. In addition, the compression of product allows a reduction of bag size – this saves packaging materials and improves transport volumes.
Sealing challenges
Mr Hamel points out that particularly in the case of recyclable paper packaging materials, for which only minimal amounts of sealing medium are used, dust particles in the seam are an important quality criterion.
“Due to the thin sealing layer, these often cannot be compensated for and then lead to lower bag tightness. Knowledge of product properties and suitable dosing and packaging technology is therefore very important, especially when selecting an alternative packaging material.”
It’s not always obvious at first glance whether paper or flexible packaging is the better packaging solution for a particular product. ROVEMA works with customers to help them determine what solution will work best for them.
“We advise the customer on machine processability, bag tightness and output rate, and work out parameters based on packaging material tests in our technical centre. In this way, our customers can usually anticipate what additional costs will be incurred by the change, or whether a possible lower output resulting from the alternative packaging material is acceptable within the framework of the overall project and will be supported by the consumer. All other requirements such as barrier properties, migration values, handling behaviour in the distribution channel and optical appearance/market appearance are clarified directly between our customers and the respective packaging material manufacturer. The final evaluation of the packaging material in terms of recyclability is usually carried out by the customer with institutes,” explains Mr Hamel.
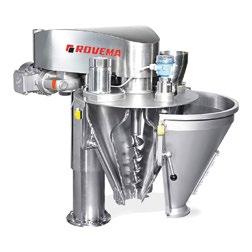
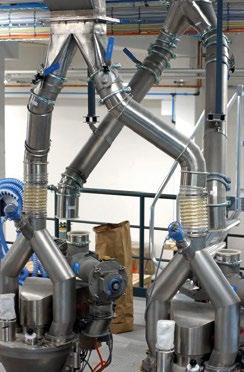
Paper requirements
ROVEMA can process a wide range of papers on its machines, as long as they fulfil a certain set of criteria. The packaging material must be machine-compatible, i.e. formable, which generally excludes paper qualities over 150 g/m². In addition, the packaging material must be coated with a sealing medium. This can be a PE film or a sealing compound that can be melted in the heat-sealing process and ensures the seam strength.
“We have a large selection of sealing tools in our technical centre for this type of testing in particular. As part of these tests, we also coordinate with packaging material manufacturers to make the respective packaging materials even more efficient to process on machines. In this area in particular, we have had some very fruitful collaborations in recent years with large international suppliers of materials, but also with smaller, very specialized ones,” says Mr Hamel.
In conclusion, while it is safe to assume that demand for paper packaging is set to grow further in the future, it is important to remember that plastics, especially monomaterials, also have their merits when it comes to functionality, especially product protection. Packaging machines and upgrade kits that offer the flexibility to work with a wide range of paper materials as well as plastics can offer companies the choice that they need. n
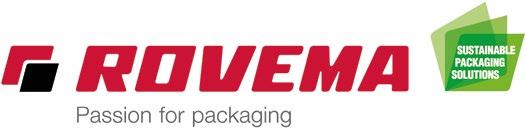