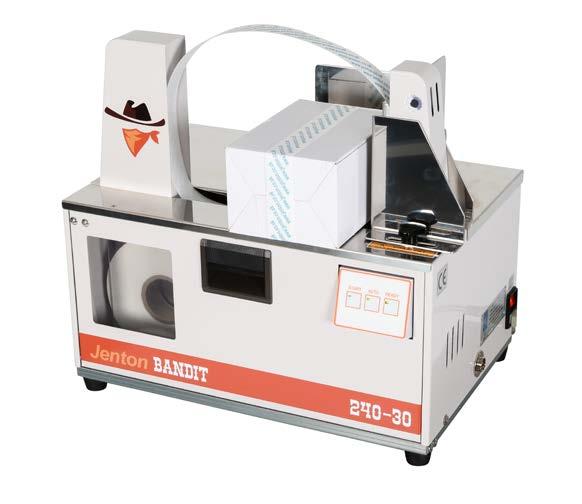
8 minute read
From automate to collaborate: What does
From automate to collaborate What does the future hold for food and beverage packaging machinery?
By Andy Knaggs, Freelance journalist and copywriter
Advertisement
Neither automation nor robotics are new to the packaging machinery sector, but they are becoming increasingly commonplace. Recent events such as COVID-19 have given added impetus to their market penetration, writes Andy Knaggs.
In the normal order of things, packaging manufacturers would always be on the lookout for ways to operate their production lines faster, more efficiently and more cost effectively. Many of them would view automation of aspects of production to be an attractive prospect, and many have already taken steps in that direction.
Times of late have been anything but normal though, and the twin enforcers of Brexit and COVID-19 have further stimulated those impulses that lead inexorably to automation.
Packagers in the food & beverage sectors have responded in kind, according to Graeme Dunn, Managing Director of Mount Packaging, which supplies a range of tailored packaging and liquid filling machines as well as robotics to the industry. “Automation is becoming more and more critical,” says Dunn. “Our customers, at quote stage, are asking for so much more from our machines. Instead of two or three machines doing specific jobs, they want one machine that does the lot, perhaps with some robotics. With social distancing, they want fewer and fewer people running the line. We are a bespoke builder, and we will set it up to meet those needs.”
Lewis Robinson, System Sales Manager at Audion Elektro, which sells automatic shrink, tray sealing and band sealing systems into food and other sectors, is also seeing this acceleration in interest in automation, although it is, to a degree, dependent upon the size and nature of the packaging producer’s business. He told Packaging in Focus: “With bigger companies, the first thing they say is that they are looking to automate. We are taking a lot more calls from companies saying they are looking to remove humans from the production process. Companies are at different stages though, and it’s key to understand where they are in their journey.”
FLEXIBLE APPROACHES COVID-19’s impact globally can scarcely be overstated, but for food and beverage producers it has made 2020 a very interesting year. There has not been a lessening in demand for food, but with evolving consumer habits during lockdown, the pandemic has compelled food and beverage producers to find new, flexible approaches to product offerings. In turn, this is feeding into the requirement for automated machines that, as Graeme Dunn mentioned, are versatile enough to switch between different product formats.
“It’s very important for the machines to be adaptable,” continues Lewis Robinson. “Customers are saying, this is what I need it for now, but can it also do this?”
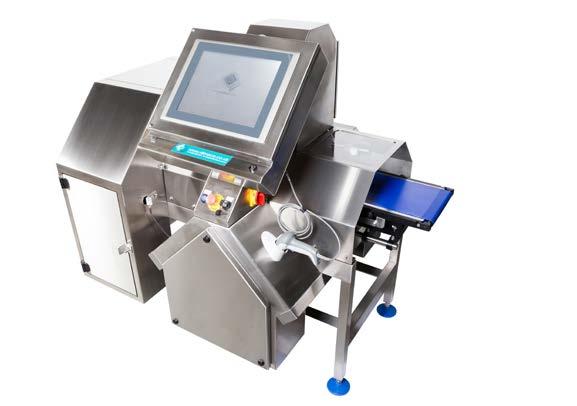
Typically packaging manufacturers are looking to be “faster, cheaper, with less operators, with new materials and product launches, and increased accuracy and better product presentation”, says Barry Cox, Sales Director at FischbeinSaxon, a leading player in bag sealing.
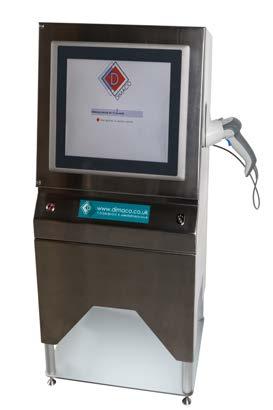
“It’s about factory optimisation and automation – customers want to move faster and more cost-effectively,” he adds. Increasingly this involves moving into robotics also, where Fischbein-Saxon has a global affiliation with Yasakawa. Robots are starting to be used for picking and packing, all the way through to palletising, said Cox, with systems capable of picking and packing volumes of bags per minute faster than any operator could achieve, more accurately, without needing lunch or a comfort break, and, indeed, without passing on a virus.
HUMAN CONSEQUENCES It’s impossible to discuss these things, however, without considering the human consequences of increased automation and robotics wherever they might be deployed. Operators are naturally going to feel threatened by these moves. Company directors have their eyes on the benefits that increased throughput and fewer errors might deliver to the business.
People are entitled to make their own minds up about such issues; they have existed for centuries, probably pre-dating the 19th century Luddites, who took to vandalising new machinery that threatened their jobs. Richard Little of Jenton Group, another food packaging automation supplier, points out that the implementation of automation and robotics does not always mean that people will directly be replaced.
“I always think there are three phases of automation,” Little explains “Stage 1 is when a machine simply does what a person does. Sometimes it can do things a lot cheaper. Stage 2 is when a machine does things better or faster than a person can. In packaging, we sell JentonAriana seal testers that can test 16 packs for leaks simultaneously. This would, in theory, replace eight people, except that they would never 32. www.packagingbirmingham.com have justified eight people in the first place, and so it enables 100% testing instead of random testing. Stage 3 is when machines “do things that people could never have been able to do”, he says, citing a vision system that can, at 150 packs per minute, read pack information, compare it with database, compare it with other parameters, collate all the information and compare that with a standard, before deciding whether to reject the pack or let it pass through.
Automation of one function can also lead to automation of another. For example, if no people are involved in packing boxes at the end of the line, then vision systems have to check much more, to ensure that errors are caught quickly.
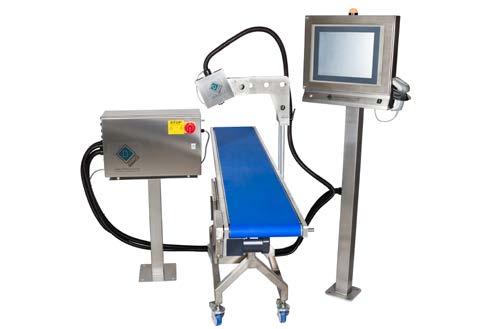
In conclusion, it is already possible for human operators and automated and robotic technology to work together in close co-operation, and the trend towards greater automation in food and beverage packaging could be seen as a relentless path towards “lights-out” automation – a packaging chain that is free of human intervention. Market pressures – which in the case of COVID-19 might have been hard to foresee in their sheer impact – are very often making the business case even clearer. Packaging operators must undertake their own journeys to reach that decision.
A VIEW FROM THE ROBOTICS FIELD: VIKASO The use of robotics in packaging is nothing new, but it is changing and growing, according to Vaibhav Boricha, director at Aylesbury-based robotics specialists VIKASO.
Robots have developed to the stage where they can be deployed in the same workspace as humans in a range of industrial settings. Meet the so-called Cobots: collaborative robots that are equipped with force and
Article continues on page 34.


GRIP® MAKING PACKAGING FASTER
YOU’LL WONDER HOW YOU EVER MANAGED WITHOUT GRIP®
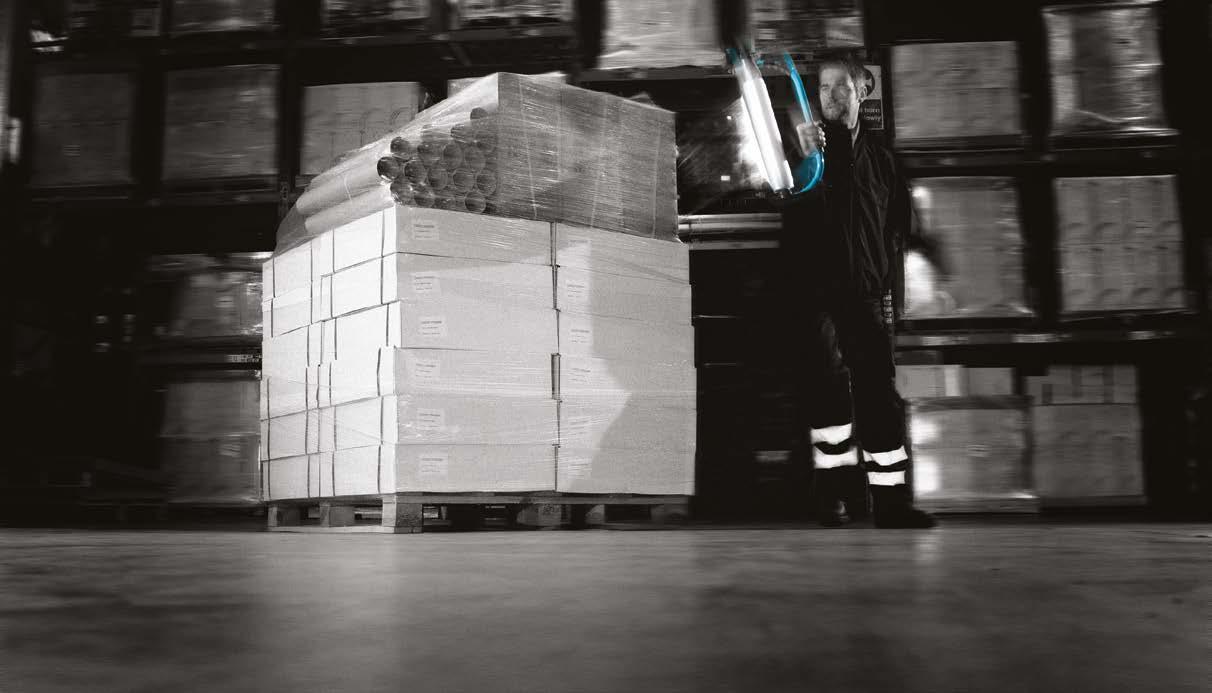

40% SAVINGS...
IN...STORAGE SPACE, TRANSPORT COSTS, ROLL CHANGE TIME, + DOWNTIME
FASTER WRAPPING
REDUCED ‘NECKING DOWN’ MEANS FEWER WRAP CYCLES PER PALLET
INCREDIBLE SELF GRIPPING FILM
AUTOMATICALLY CONTRACTS WHEN APPLIED, PROVIDING EXTRA STABILITY
IMPROVED ERGONOMICS
RELIEVES STRESS ON LOWER BACK AND SPEEDS UP THE WRAPPING PROCESS.
Also available from GRIP®

VISIT US AT PACKAGING INNOVATIONS & EMPACK NEC BIRMINGHAM 17TH-18TH JUNE 2021 STAND C90
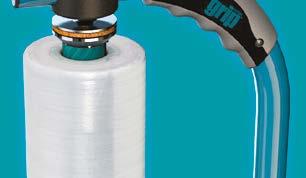
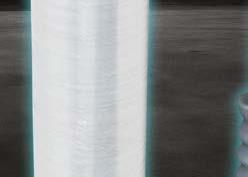

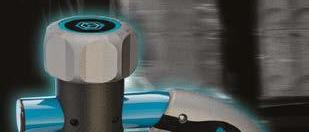


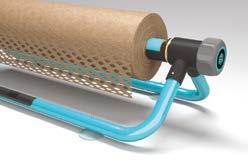
GRIP® PAPERFLEX
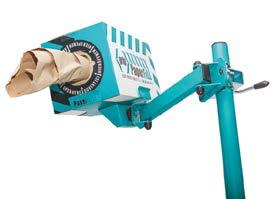
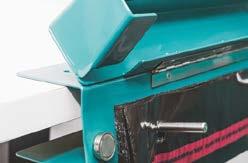
Advanced mailbag system - making packing more effi cient, never select the wrong bag size again! Environmentally friendly paper voidfi ll and dispenser system, revolutionising packing operations in cost, speed and effi ciency. Environmentally friendly, wateractivated, handheld tape dispenser - the future of smart and sustainable packaging solutions. Save valuable space, improve your workfl ow, and protect your goods the eco-friendly way with our all new recyclable, biodegradable and compostable paperfl ex wrap.
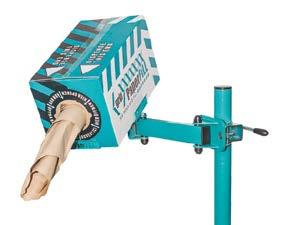
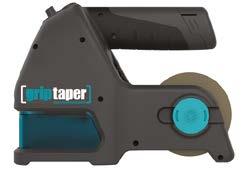
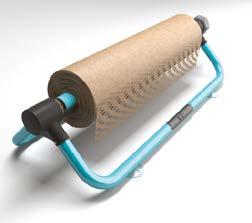
torque sensors to detect collisions with any part of the robotic arm. These sensors also gather data that can be used to improve automation performance.
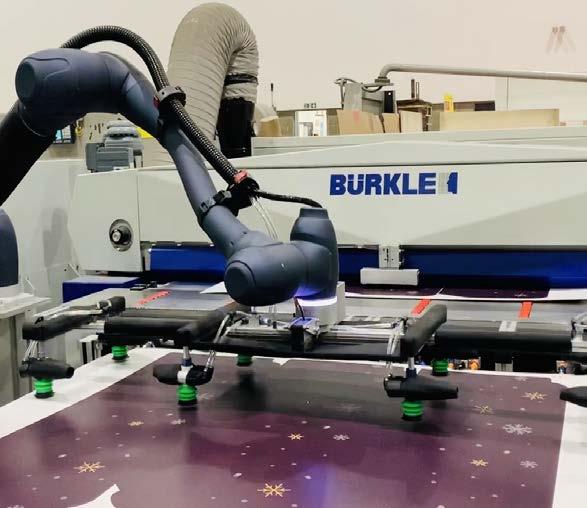
“Collaborative robots, or Cobots, are much easier to programme, configure and run cost-effectively, and their implementation time is much shorter,” Boricha told Packaging in Focus. “Cobots have a robot arm that is lightweight, that’s built with safety sensors so they can work alongside operators without safety guarding, and are designed as force-sensitive, so they can feel or sense if they are picking up the object properly.” VIKASO works with its customers, including those in packaging, to develop solutions around the basic Cobot technology. Boricha likens this to an iPhone: without its apps, the device is of little use. He sees two main applications that provide the biggest opportunities in food & beverage: box erection, filling and sealing; and palletising.
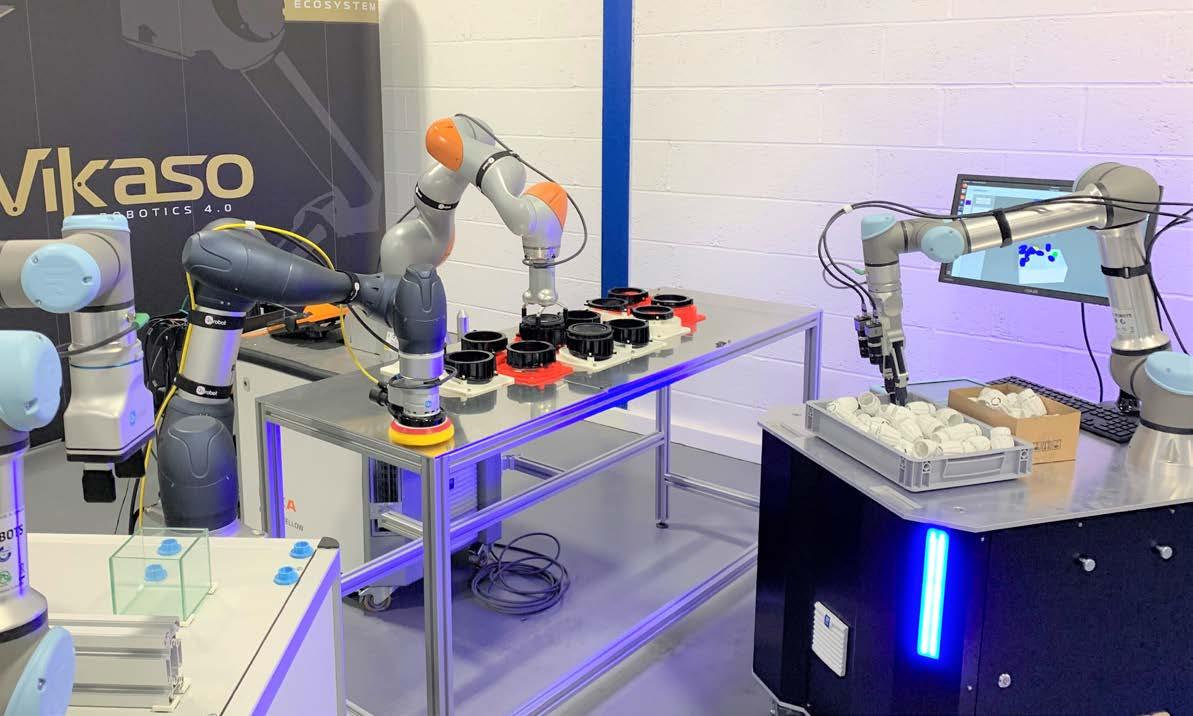
“Those are very good use-cases for robots,” he continued. “It’s still very early days, but there has been a huge increase in awareness of this technology in the industry. COVID and Brexit are prompting food and beverage companies to take on automation in their operations.”
He predicts “lights-out” full automation of the entire packaging production line in the future, and the increasing intelligence of collaborative robots within this process will become more and more significant: “The future is very much technology- and datadriven,” Boricha said “and towards the latter half of this revolution it will be data driving automation, rather than people driving automation.”
VIKASO exhibited at Packaging Innovations & Empack Birmingham for the first time in 2020 and had this to say “we had an excellent show, meeting a big client at the event. This was a company looking for a sheet sorting solution that we created for them. The technology can be applied to any converting house whether commercial or packaging (and applied to food)”.