
8 minute read
Time to transition
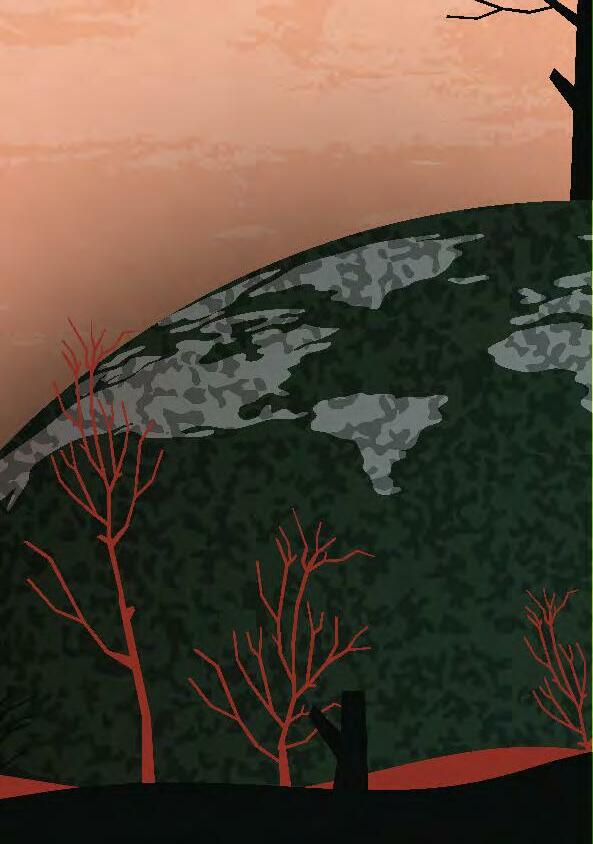

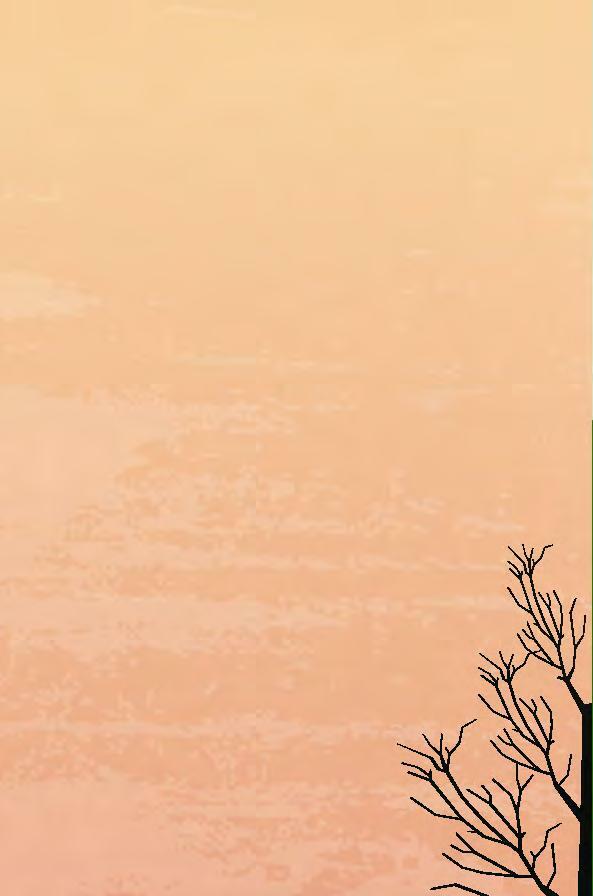


Steve Wirtel, Kore Infrastructure, USA, discusses how converting waste into carbon negative renewable energy will help reduce the need for fossil fuels.
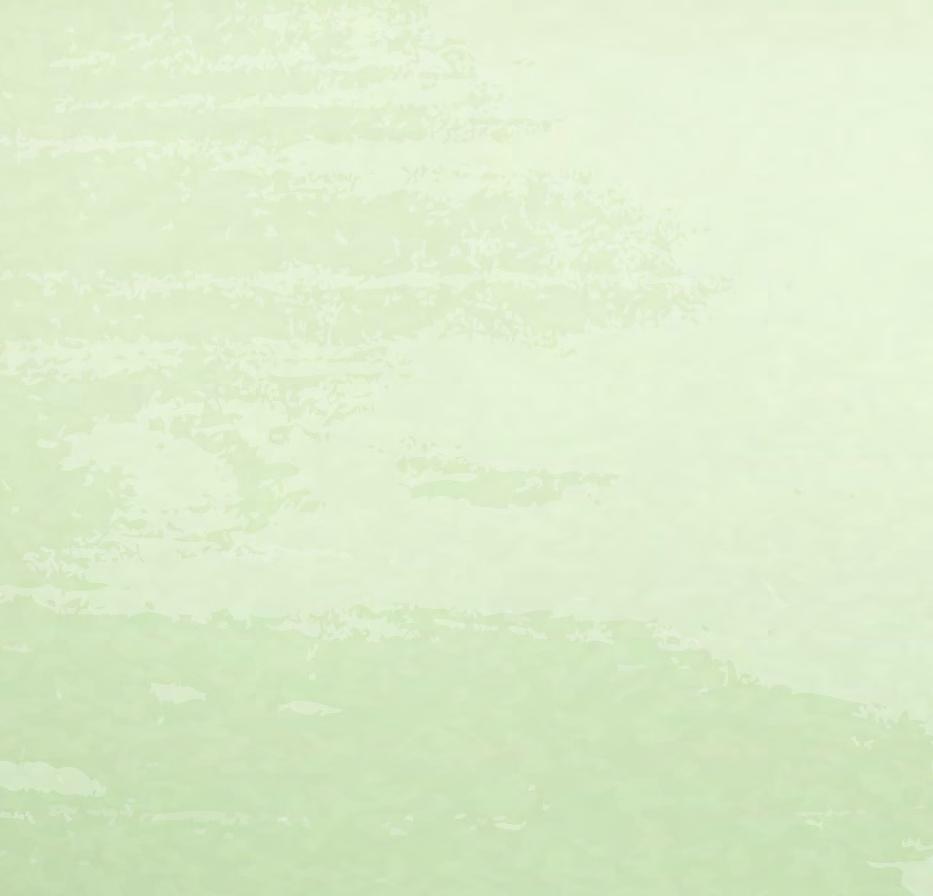
lobally, 65% of greenhouse gas (GHG) emissions are caused by the burning of fossil fuels.1 As the climate crisis intensifies, it is essential that alternative energy sources are searched for. Managing waste contributes to the climate crisis: even in a landfill, organic waste decomposes into methane, a potent GHG, and can leak into the atmosphere. Kore has developed a technology to solve both challenges by converting waste into carbon negative renewable energy, reducing the need for fossil fuels. The process, known as pyrolysis, begins with wastes such as demolition wood, agricultural residuals, forest thinnings (to reduce wildfire risk), and green waste. These feedstocks are continuously fed to the pyrolyser where the temperature is raised to over 1000˚F in an oxygen-free environment. Under these conditions, the feedstock decomposes into a gas and a solid carbon char. The system operates in a closed-loop – the technology produces zero waste, and the feedstock generates heat to power the process without supplemental energy. Since the feedstock is biogenic (it originated as a plant), these products are called biogas and biocarbon. After spending over 60 mins. in the Kore reactor, the biogas is sent to a gas conditioning system where it first passes through a hot cyclone to remove fine solids, then is quenched in a venturi scrubber to reduce the temperature. Finally, the gas is dehumidified before being conveyed into a storage vessel. Condensable gases produced in the venturi scrubber can be recycled to the reactor, used to generate process heat, or upcycled to methanol and acetic acid for offtake.
Biocarbon exits the reactor through dual knife gates to preserve the airtight seal in the reactor. The biocarbon enters a screw conveyor equipped with a cooling sleeve that reduces the temperature to near ambient as it lifts and discharges the biocarbon into a storage and offloading hopper.
Approximately half of the carbon in the feedstock converts to elemental carbon (biocarbon). Biocarbon makes an excellent soil amendment because it retains moisture (less irrigation), retains nutrients (less fertilizer), and improves soil microbial growth, all of which contributes to higher plant yield. Think of biocarbon as a sponge that holds onto water, not only reducing irrigation but increasing drought tolerance. The biocarbon produced by a standard Kore process can reduce irrigation needs by up to 60 million gal./yr. Biocarbon also absorbs fertilizer, allowing the plant to access nutrients when it needs them. This provides two benefits: less fertilizer is applied, and less fertilizer runs off into the environment, causing nutrient pollution.
In addition, because the biocarbon is produced at a high temperature, it is biologically stable – it will not biodegrade to methane (CH4) or carbon dioxide (CO2), and will remain in the soil for centuries. And, because the carbon originated in the atmosphere (biogenic feedstock), the process is carbon negative. Biocarbon also has an energy value comparable to coal, and can be substituted for coal in steel and cement production, both notoriously difficult to decarbonise.
The carbon negative biogas produced has an energy value approximately half that of fossil natural gas. It can replace natural gas to produce heat, power, and/or steam using a client’s existing burner technology. Composed primarily of hydrogen (H2),
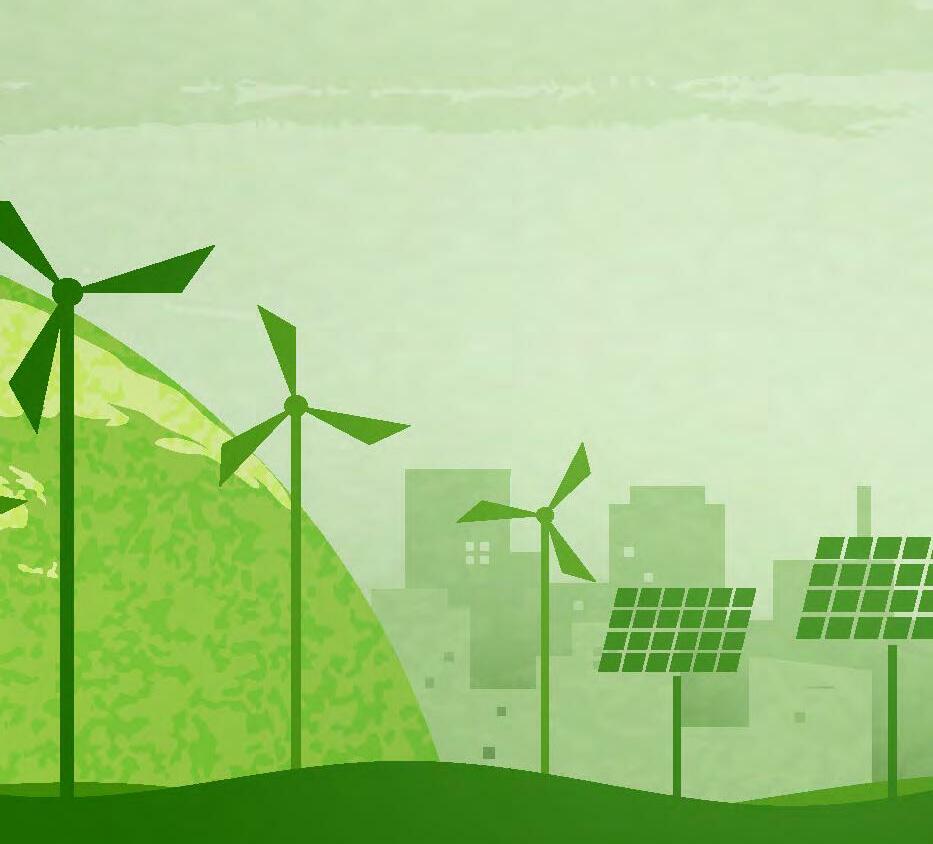
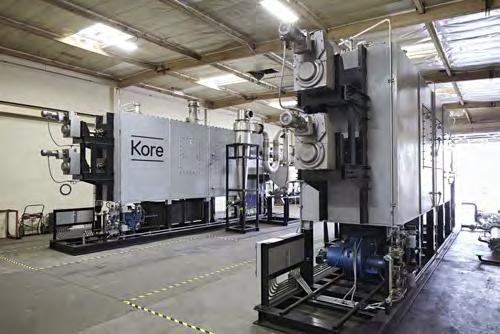
Figure 1. Kore Infrastructure’s pyrolyser that converts organic waste into carbon negative energy. carbon monoxide (CO), CH4, and CO2, the biogas can also be upgraded to carbon negative hydrogen using proven technology such as pressure swing adsorption, or it can be converted into carbon negative renewable natural gas via methanation. Below is a list of typical applications for the energy products derived from Kore’s biogas. F Heat: The biogas and biocarbon can be used to generate heat for heat intensive processes such as cement manufacturing. F Power: The biogas can be used to generate power for electric utilities, college campuses, and factories to help sustainably meet electricity needs. Biogas can also generate uninterruptible power for large server farms and data centres to lessen the burden on local grids. F Steam: The biogas can be converted into steam for applications such as food and beverage production. F Renewable natural gas (RNG): The biogas can be upgraded to RNG which is molecularly indistinguishable from fossil natural gas. This carbon negative RNG can replace fossil natural gas in many applications, including: compressed natural gas (CNG) vehicles, traditional hydrogen produced by steam methane reforming, and natural gas fired power plants. F Hydrogen: The biogas can be upgraded to fuel cell quality hydrogen which is 99.999% pure, also known as 5-9s hydrogen. This UltraGreen HydrogenTM is suitable for fuel cell electric cars, trucks, buses, and trains. Because the carbon intensity of this hydrogen is very low, the credits available through policies such as the low carbon fuel standards (LCFS) in California, the US, and soon other states, are very valuable. Other uses for UltraGreen Hydrogen include warehouse and distribution centre forklifts, steel manufacturing, and ammonia production.
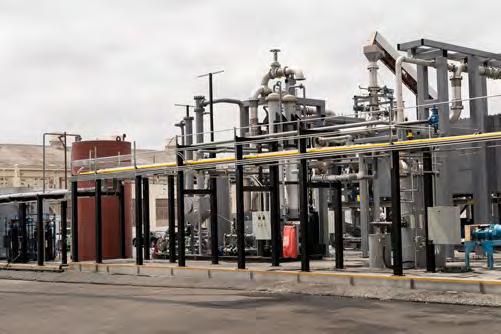
Figure 2. A side view of Kore Infrastructure’s system in operation, moving renewable energy through a series of pipes.
Figure 3. An aerial view of Kore Infrastructure’s facility commissioned for a project with SoCalGas in downtown Los Angeles, USA.
Hydrogen
Hydrogen is one of the more interesting energy products that Kore can produce. Hydrogen use is rapidly growing in California, where policy is driving the transportation sector to decarbonise. The state currently has 54 light-duty hydrogen refuelling stations,
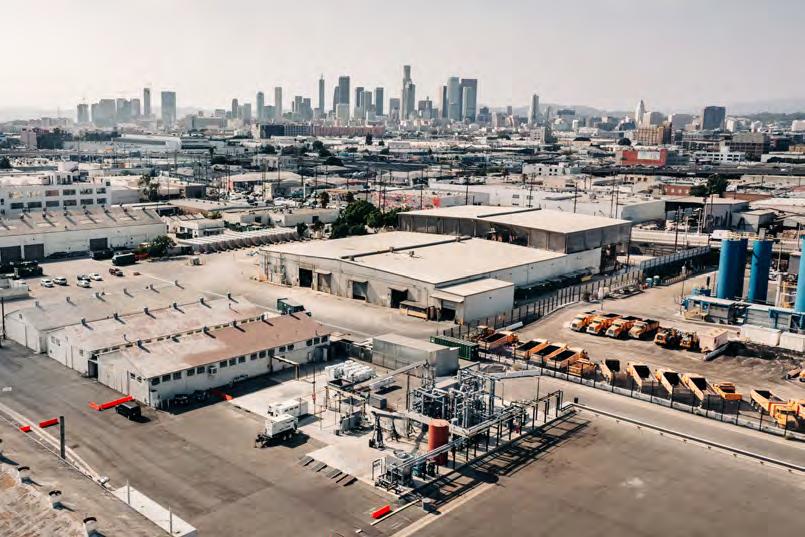
with another 117 in development. A standard Kore system can produce up to 1000 kg/d of UltraGreen Hydrogen, enough to fuel over 1400 fuel cell electric cars. This standard design, skid-mounted technology can fit into tight spaces almost anywhere, reducing feedstock and hydrogen transport costs and increasing accessibility to low-cost green vehicle-grade hydrogen. UltraGreen Hydrogen can also be used by warehouse operators to power quick fuelling, zero-emission fuel cell electric forklifts and Class 8 heavy-duty trucks.
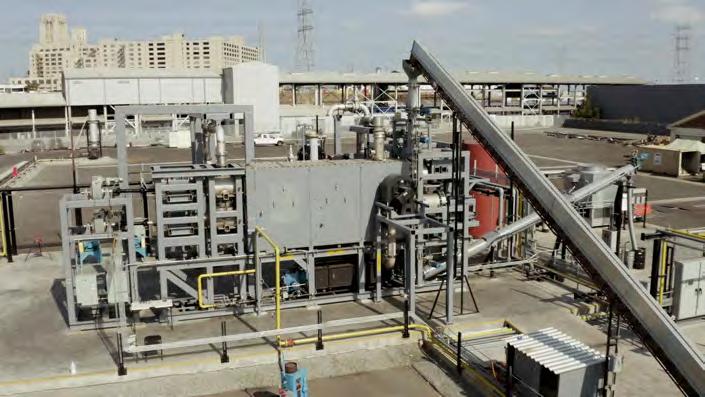
Anaerobic digestion
Figure 4. Part of Kore Infrastructure’s facility where organic material is continuously fed into the system.
The Kore process also complements other waste management technologies such as anaerobic digestion. Anaerobic digestion converts high moisture organic wastes such as food waste, animal manure, and wastewater treatment sludges into biogas containing methane and carbon dioxide. The methane can be separated and processed into RNG. But the anaerobic digestion process is incomplete – approximately 40% of the incoming waste remains as a semi-solid digestate that must be managed, typically by land application. However, the presence of dangerous chemicals and excess nutrients limit the options available for land application of digestate. The Kore process can use this digestate as feedstock, increasing the overall RNG production by 50% or more and eliminating digestate management problems.
Energy transition technology
The Kore process is a true energy transition technology. The technology can be implemented initially to provide biogas for heat, power, and/or steam generation. Then, a hydrogen separation process can be added to separate UltraGreen Hydrogen from the biogas. The gases left after hydrogen separation are still very energetic, so they can continue to produce heat, power, and/or steam. Hydrogen production can start small and increase as demand grows. Eventually, the facility could convert entirely to hydrogen production, with the tail gas used to meet the process energy demands.
The key to the Kore process is maintaining the feedstock at a very high temperature in the complete absence of oxygen – easier said than done. The Kore system has been mechanically proven to withstand the rigours of continuous, high temperature, 24/7 operation, with an airtight reaction zone. Kore has been successfully operating a commercial demonstration facility for over a year on a site in downtown Los Angeles, the US, owned by Southern California Gas (SoCalGas) to prove the mechanical integrity of the equipment.
“SoCalGas will continue to support companies developing innovative technologies to help achieve carbon neutrality,” said Neil Navin, Vice President of Clean Energy Innovations for SoCalGas. “The production of carbon-negative RNG and hydrogen could help provide energy security and decarbonise California in our energy transition.”
This demonstration project has been fully permitted in downtown Los Angeles. The South Coast Air Quality Management District (SCAQMD), the air quality regulator for southern California, one of the most restrictive air regulators in the country, issued some of the many permits for the facility. As a show of its support, the SCAQMD is also supporting the project both technically and financially.
The only emissions from the process is flue gas that exits the pyrolyser after indirectly heating the feedstock. These emissions are tightly controlled by the burner design and operation.
The demonstration facility processes 1 tph of feedstock, producing approximately 10 million Btu/hr of renewable energy. Biocarbon production is approximately 20% of the feedstock flow. Because this is a research project, none of the energy products are sold, but instead they must be carefully disposed of. The biogas is completely combusted in a flare, and the biocarbon is removed by a waste management company that uses it as an asphalt additive.
The next steps for the company’s demonstration project is to test a wide variety of feedstocks to collect performance data for commercial applications. Kore will also begin testing hydrogen production using pressure swing adsorption technology. The UltraGreen Hydrogen produced will be available to fleet, retail, and other off-takers in southern California for testing and use.
Kore believes in circular solutions that benefit a wide range of customers and industries. The company’s technology is at the cutting edge of the energy transition and is changing the way people think about waste.
References
1. ‘Global Greenhouse Gas Emissions Data’, United States Environmental Protection Agency, (February 2022), https://www.epa.gov/ghgemissions/globalgreenhouse-gas-emissions-data.