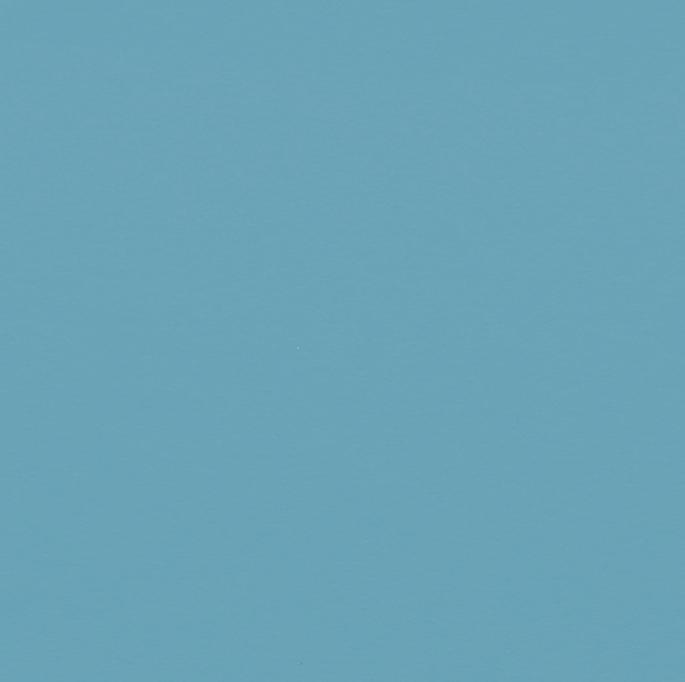
11 minute read
Measure For Measure In Real Time
Henry Kurth, Scantech International Pty Ltd, Australia, provides insight into the role of advanced real-time measurement in mineral processing.
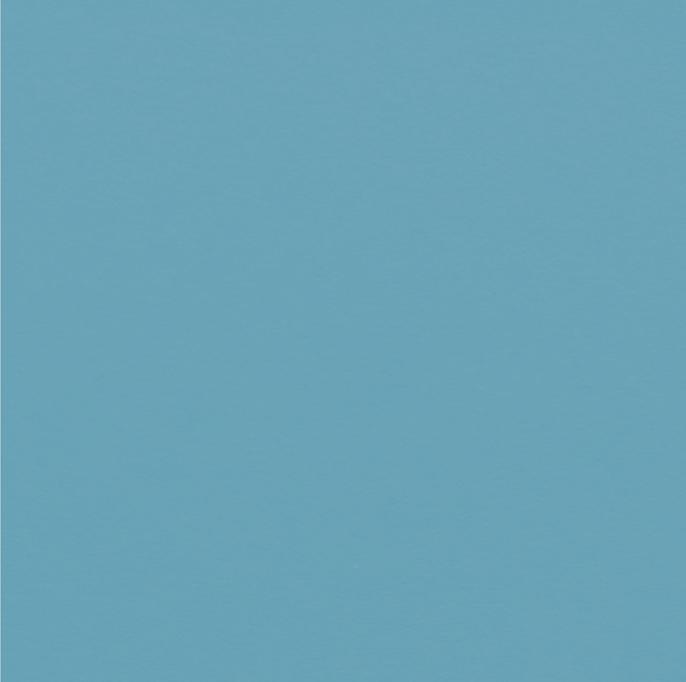
Digital transformation in mining companies increases the visibility of mined ore and product quality to all stakeholders, located both on site and remote to the operations, so that aberrations can be identified and addressed in real time. Digitalisation of feed quality is now providing continuous, high quality data that many operations have come to rely upon.
Proven technologies can be used to improve process performance in mineral processing operations through real-time quality measurement of ore delivered to the plant. Sensors used for blast fragmentation and in pre-concentration are well-proven examples. The key criteria are that analysers should be rugged, suitably designed for optimal measurement, reliable, easy to maintain and data should be easily integrated, readily available, representative, relevant, high quality, and beneficial. An effective due diligence process is essential.
Solutions, such as Scantech GEOSCANs, are now being implemented by global mining leaders as an integral part of their digitalisation strategy.

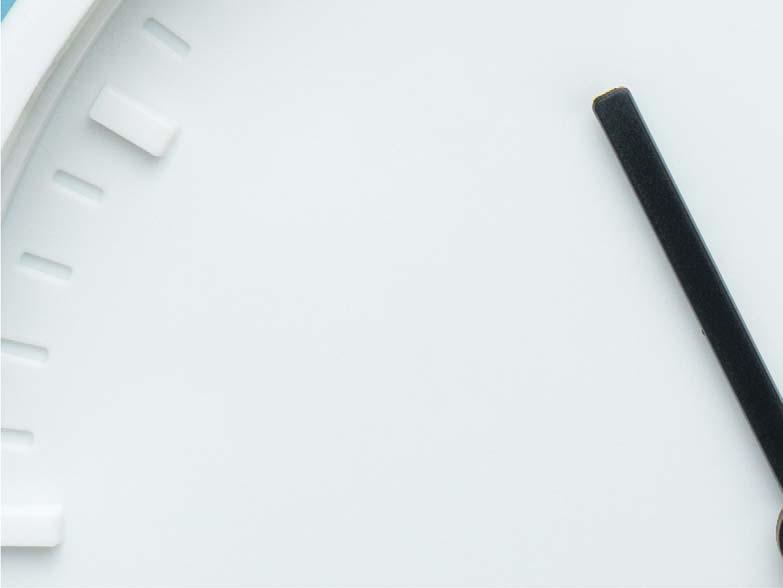
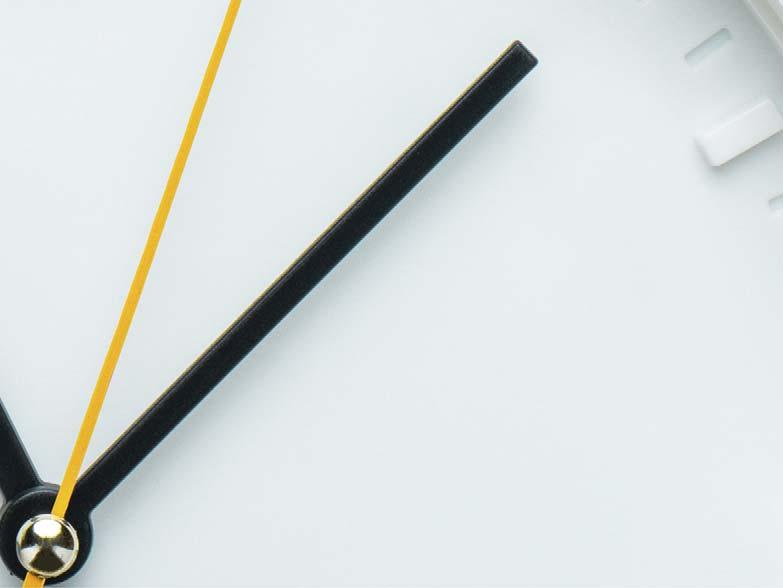
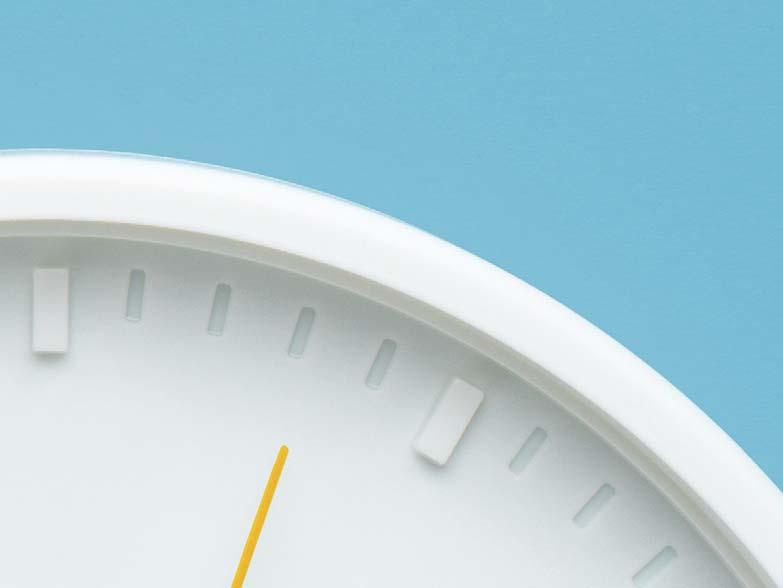
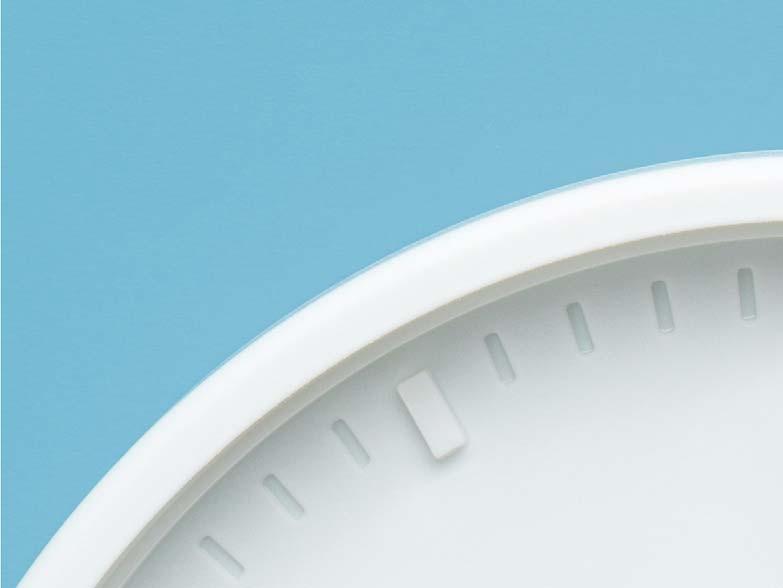
Where to measure
Measurements of ore and waste quality should generally be taken as early in the process as possible, although less representative measurement earlier in the flow may not provide better outcomes than more precise measurements further downstream. Measurement should be representative: so that the data produced has high integrity and relevance, and so that there is high confidence in decisions based on the data.
Experiences from many mining operations suggest that some technologies do not necessarily provide optimal outcomes. Surface analysis of mined faces, or loads in buckets, shovels or trucks, may be useful for ores that are generally considered homogeneous, but these are very rare. For example, porphyry copper-gold ore has proven more variable than expected, so some sensors, such as surface analysis techniques applied to conveyed flows, are proving less eff ective than expected. Quality variability occurs in all commodities and this should be properly quantified before strategies are developed for control.
Conveyed flows represent the best opportunity to measure continuously and representatively over much smaller increments than a shovel or truck, as flow rates provide relatively consistent material presentation to penetrative measurement technologies. Technologies unaff ected by particle size, belt speed and composition, segregation, moisture, and dust can provide very eff ective measurement aft er primary crushing. Variability is still significant despite the mining, haulage, and stockpiling performed prior to that point (Figure 1).
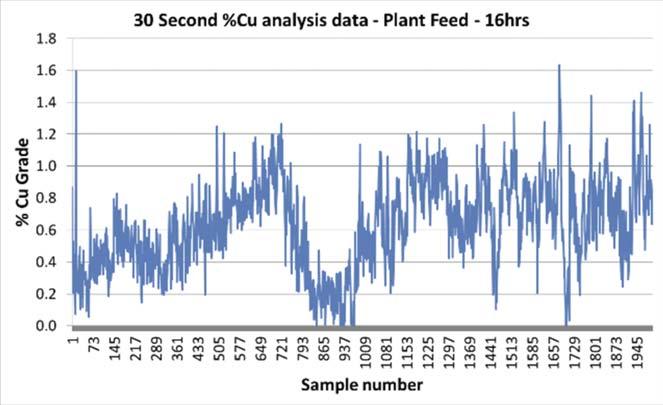
Figure 1. High variability displayed in porphyry copper-gold ore feed to process plant showing 30 second measurement data on 1000 tph conveyed flow.
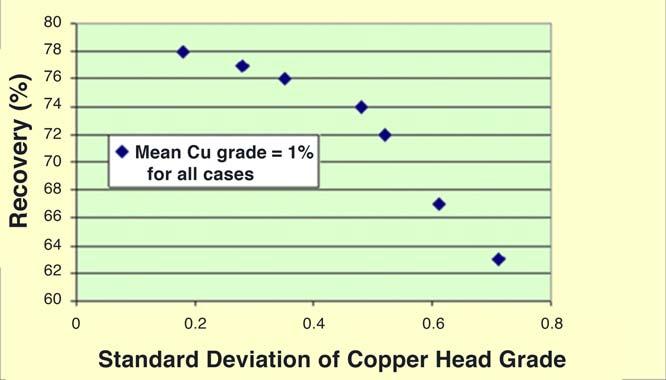
Figure 2. Eff ect of increasing feed grade variability on copper metal recovery in a flotation circuit (aft er Codelco).
Quality variability
Material quality variability is a major challenge in process control. Despite mining, beneficiation, materials handling and blending, there is still considerable variability when materials reach the next stage in the process. Quality variability is well accepted as having a major impact on process performance and managing quality requires high quality, representative measurement systems. Rather than taking samples containing significant sampling error, the smarter solution has been to measure quality continuously, using appropriate technologies. Real-time measurement is an obvious method to achieve this, with typically short paybacks, sometimes a few months or weeks.
Physical sampling of coarse flows following primary crushing requires significant eff ort and cost expenditure to be eff ective, and assay results are not available until well aft er the material has been processed or stockpiled. Conveyed materials segregate due to particle size variation and vibration, with finer material migrating downward and coarser material over-represented toward the upper surface. Moisture content can also be variable with depth and particle size distribution. Moisture can also cause materials to become sticky and lumpy, causing fines to coat and obscure coarser particles. Layering can be due to additional material loaded on top of prior material. Surface analysis techniques can exacerbate measurement bias by measuring material aft er segregation has occurred. These variations can be overcome through the use of well-designed and appropriately configured and customised transmission analysis techniques.
The impact of quality variability on process performance is well documented, and various work has been undertaken to understand how process recoveries can be aff ected. Figure 2 shows an example of copper metal recovery significantly reducing with increasing feed quality variability. This has major economic implications to operations and should be addressed by measuring and managing plant feed quality consistency.
Using data for improved control
Quality variability cannot be controlled if it is not measured. If it is not controlled, then it cannot be improved. Even the best performing plant can be improved through real-time measurement of ore quality.
Real-time data has many uses, particularly on plant feed material. Immediate responses include diversion of short conveyed increments (also referred to as bulk ore sorting), or changes to the feed blend to improve grade or quality consistency. Sepon Copper-Gold mine justified an analyser on copper grade, but substantially enhanced its benefits by then using iron, sulfur, calcium, magnesium, and manganese for acid-consuming gangue content monitoring for acid addition control in a leach circuit feed.
Measurement data is increasingly being used to generate additional benefits: Immediate feedback to mining operations helps confirm the grade delivered against the expected grade, so that schedules can be adjusted as needed in real time.
Feed forward control is used to identify quality parameters in real-time that affect processing, including: Hardness for mill feed rate adjustment. Mineralogy and deleterious content for reagent dosing to optimise metal recoveries and reduce concentrate contamination. Sulfide content for diverting ore to flotation while oxide is diverted to leaching, etc.
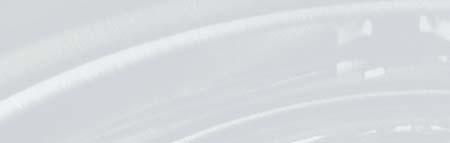
Measuring and managing conveyed flows at full throughput rates has proven to be very eff ective where is has been implemented. Customised measurement solutions providing the quality of data required for optimal process control have generated the greatest benefits. Data is used concurrently for other data-based applications such as ore reconciliation, metal accounting, input to digital twins for performance simulation and optimisation, in addition to the immediate response activity of controlling feeders or diverters or changes in feed rate.
The application of high-quality representative measurement systems provides a new level of feed quality data visibility to all levels of the organisation at very low cost and for very large benefit. Most analysers integrate seamlessly with plant control systems ensuring data is easily accessed on site or remotely in real time. The availability of high-quality measurement data enables operations to respond decisively and eff iciently to unexpected variations in quality, and to automate process responses where needed.
Technologies
Composition measurement using high specification Prompt Gamma Neutron Activation Analysis (PGNAA), e.g. GEOSCAN GOLD, to measure the elemental composition through the full conveyed cross section continuously and representatively in real time, over short time increments, has proven exceptionally eff ective. Individual elements are measured directly and independently, and these systems have been used for diff icult mineral applications where analysis is required each 30 seconds of flow, as well as for ores where the trace elements are of interest – e.g. gold, platinum, etc. Low specification systems needing 10 minutes or longer to produce reliable measurements are not useful for many applications requiring timely responses.
Through belt moisture (TBM), microwave transmission provides free moisture to precisions typically better than 0.5% moisture as a standalone system, or integrated with GEOSCAN. Fast neutron and gamma transmission measures hydrogen content directly with high precisions (usually better than 0.2% moisture) and can be used on materials not suited to the microwave technique, such as: coke, magnetite, or some metal concentrates.
SizeScan measures particle size distrubtion (PSD), volume and belt speed using 3D infrared camera technology and advanced algorithms to overcome segmentation soft ware limitations on images from 2D cameras, and can be configured for foreign
Visit us! MINExpo, Las Vegas, Nevada, USA September 13– 15, 2021 Central Hall, Stand 8471
SOME THINK THAT RAW MATERIALS TRANSPORT REQUIRES TRUCKING. WE THINK DIFFERENT.
object detection. It is used in oversize detection and fragmentation analysis in dusty and humid environments where other systems have proved unsuitable, and does not require specific lighting. It has also been demonstrated to measure mass flow to within 1% of a nucleonic weigh scale. It is easily integrated with other sensors.
The aforementioned technologies provide results in real time directly to the plant control system and all analysis data is owned by the client with no accessibility issues. There are no cloud platforms to negotiate or ongoing costs to access data, which can be accessed on remote devices in real time.
Analysers should ideally possess the following: Remote access to minimise on-site time, but with remote support readily available when needed. Installation during planned shutdowns and no interruptions to operations. Non-contact with no wear components or consumable spare parts. Immediate benefits to site.
A good example is that a 1 million oz + gold operation in North America increased ore throughput by 3%, within one month of installing a moisture analyser, by replacing a higher assumed average moisture content with actual measured moisture content, in order to remain within dry tonnage processing license limits.
The choice of technology should be carefully considered, as should the choice of vendor and product, as no two off er the same performance, services, or price. Seek a vendor who: Has minimum ISO 9001 quality accreditation. Has a history of success, innovative R&D, and their own analyser IP. Provides reference contact details, not installation lists – sales alone are not proof of performance. Offers testing at no cost to confirm performance before purchase, as well as proof that it is achieved on site. Listens and understands the problems at hand, in order to recommend appropriate solutions. Understands relevant technologies in the market. Has technical professionals recommending solutions on value, not salespeople selling on price. Has a strong safety culture, with analysers requiring no external access restrictions during operation. Has proven precisions over measurement time increments relevant for each application. Offers customised solutions (specification and calibration), not one-size-fits-all. Provides published papers, preferably case studies written by clients. Takes responsibility for analyser performance – e.g. offers money-back guarantees. Offers 24 months’ equipment warranties, and appropriate support response times.
Performance evaluation should follow international standards and any penalties for non-performance should be agreed prior to the purchase of the analysers. The rule of thumb is that analysers should be precise, fast and cheap, but that only two of these are available in reality.
Measurement precision on conveyed flows varies widely, even for the same technology. The diff erences in measurement performance, for example in a bulk sorting application, may be equivalent to over US$10 million/y in a contained metal feeding a mill.
Ongoing support
Following initial factory QA acceptance, the installed analysers should have their field calibrations verified and performance expectations met before handover. Installation support services should be off ered to facilitate smooth integration of the analysers into plant operations, expediting their benefits. Analysers supplied by reputable vendors should achieve claimed performance shortly aft er initial commissioning and calibration. Online elemental analysers typically require calibration checks every six months. Any sampling required can be made manageable through good planning and need not interfere with normal production.
Ongoing technical support and regular analyser access, via remote connection or through site visits, should be off ered as appropriate. Technical concerns should be resolved promptly. Well-designed and properly installed analysers should require minimal maintenance, particularly those without contact with the conveyor belt or material. Most analysers should perform better over time as they are fine-tuned to the material they are measuring. A vendor committed to further collaboration with a client to improve measurement capabilities, such as developing capabilities for more elements (at no added cost), can add significant value to a process operation. A good example is the retrofitting of a phosphorous measurement calibration to multiple iron ore customers at no charge.
Conclusion
On-belt or through-belt analysers are available from many vendors and in diff erent configurations. Publicly available feedback from customers is rarely provided, as many see successful implementations as a competitive advantage and failed implementations as an indication of poor due diligence.
Companies considering an analyser should ensure the correct solution is purchased. References should be contacted, as installation lists on their own do not indicate acceptable performance.
Higher quality measurements – i.e. precisions – enable tighter process control and improved outcomes, typically providing additional value worth many millions of dollars per year.
Customised analyser configurations and calibrations for specific applications produce the most useful, timely data possible to meet each client’s measurement requirements for eff ective process control.
Many of the world’s largest resources companies have adopted the technologies in various applications to not only improve sustainability, but also to demonstrate responsible resource management to their stakeholders.