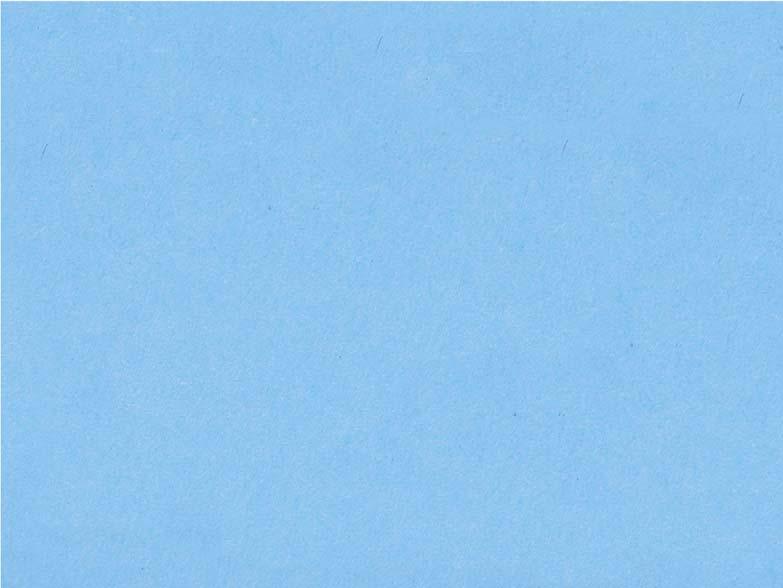
10 minute read
The Key To Grease Selection
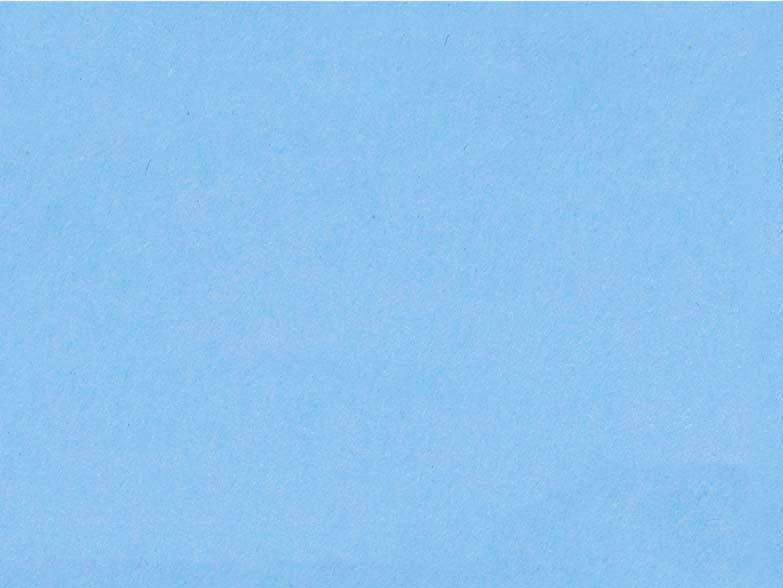
Mark Guenther, A.W. Chesterton Co., USA, advocates for the use of key performance indicators for grease selection in mining applications.
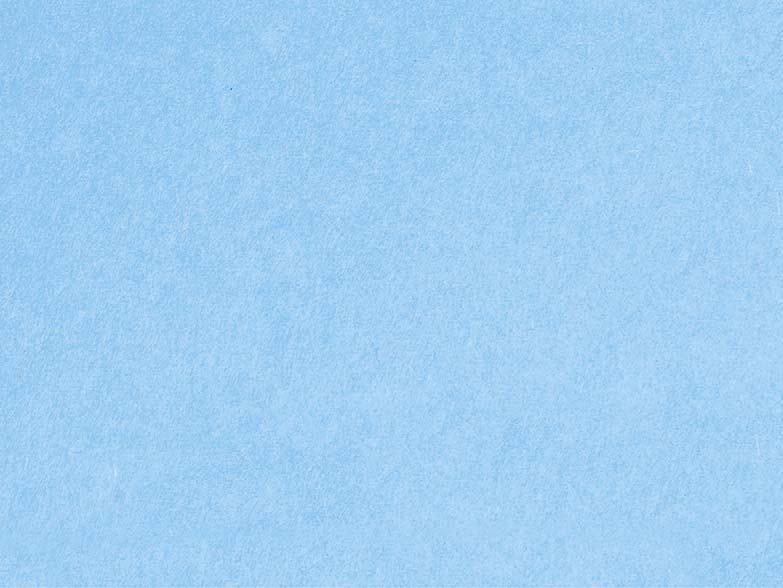
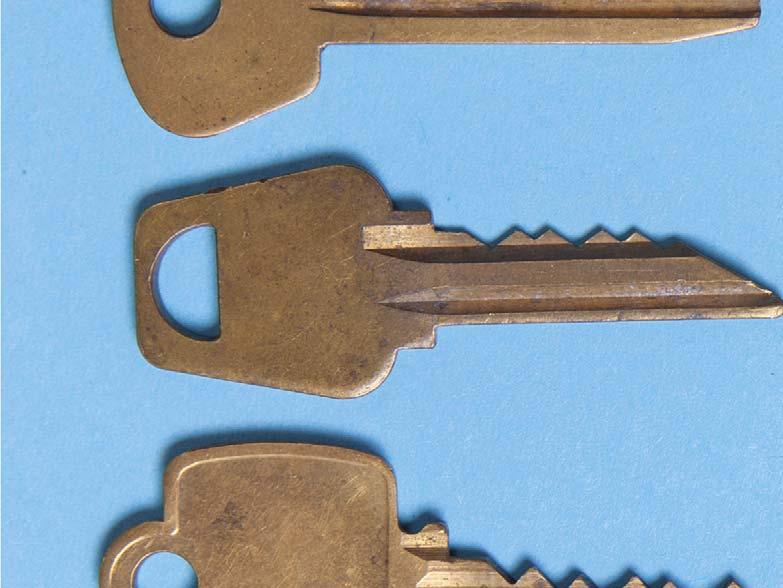


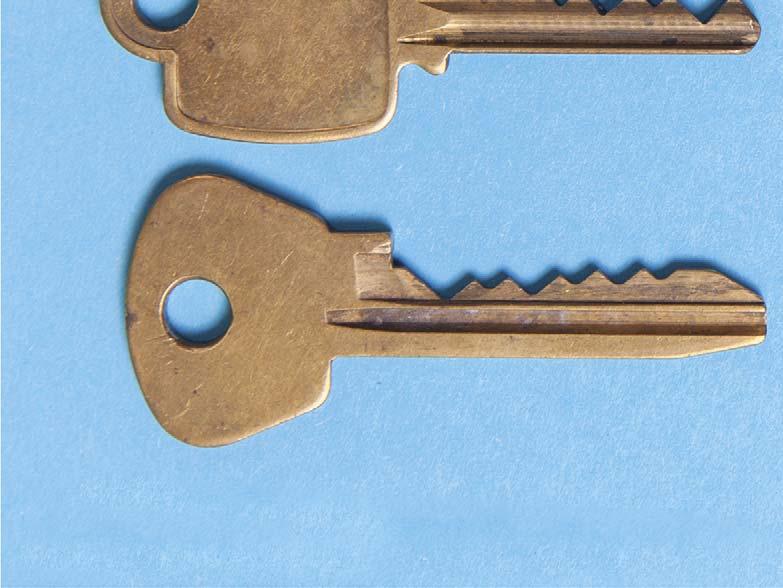
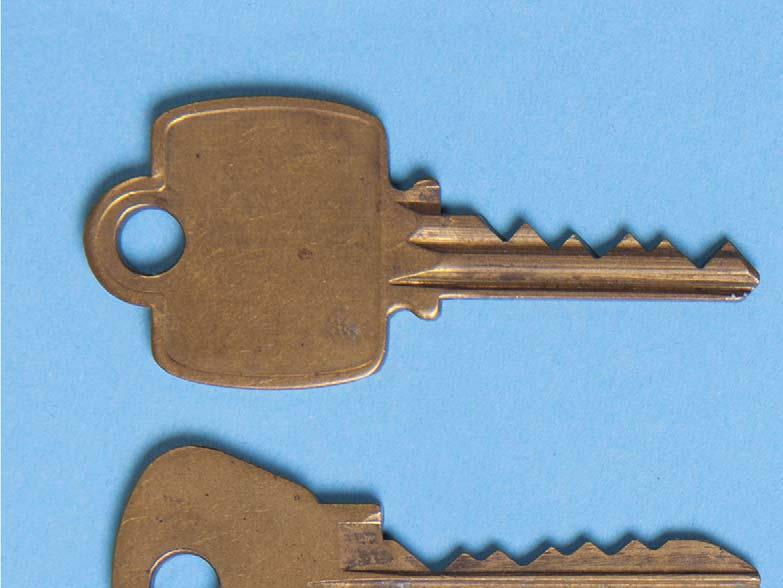
In the mining and mineral processing industry, as well as almost every other industrial operation, proper lubrication is the uncelebrated hero of reliability.
From raw material to finished final grade ore, plant reliability and profitable operation relies on equipment uptime. Using the wrong grease will shorten equipment life, increase downtime, and cost money. In mining, this impacts everything from crushers and conveyors to sag and ball mills, apron feeders to electric motors and loaders.
Beyond just selecting the correct viscosity and NLGI grade, operators will ideally select the correct grease by using key performance indicators (KPIs) matched to specific application demands.
How well does the lubricant withstand shock load, oil separation, and shear thinning? Does the grease prevent water ingress? Will it passivate the ferrous substrate to reduce pitting corrosion to bearing components? These are attributes that will not necessarily be found by simply selecting Lithium EP #2 grease.
Determining requirements
In general, step one is to identify a comprehensive list of essential technical and non-technical requirements, and can include: Considering the type of system equipment, operating conditions, application methods, and environmental conditions. Finding out whether an original equipment manufacturer (OEM) or industry standard indicates quantifiable performance pre-requisites. Determining if these standards are applicable to a ‘real world’ service condition. Using simulations, models, software, and industry knowledge to estimate both qualitative and quantitative requirements. Complying with federal, local, and company-specific regulations that can impact the transportation, handling, storage, disposal, and legality of specific greases.
Choosing a grease formulation
Industrial greases can be formulated to achieve certain performance attributes measured and documented by ASTM, DIN ISO, and other standard tests. Lubricant manufacturers must conduct these tests to classify the greases they off er. These tests are fully documented and
characterised on the grease manufacturer’s technical data sheet (TDS). If KPIs are not present on a manufacturer's TDS, seek alternative suppliers that fully characterise their grease, in order to best support good decision making (Table 1).
Comparing test standards in the buying process
Manufacturers’ test standards should be compared in order to select the best grease for a specific mining application (Table 2). It should also be borne in mind that the selection of proper base oil viscosity, NLGI grade, and thickener selection based on bearing size, RPM, and pumpability requirement will have already been made.
The column marked ‘optimised’ shows the target rating for specific test standards. Columns three to five show diff erent common technologies in the mining industry. Operators’ own brand contenders should be inserted there for comparison. Equipment bearing grease – performance data comparison
The next section of this article will take a look at how selections can be made based on three equipment types critical to the mining industry.
Conveyor systems
The bearings on conveyor systems handle coarse rock or large heavy raw ore and, as a result, are subject to excess shock, load, and vibration. A critical feature of a high-performance grease for this application would be maximising the four-ball weld load and four-ball wear of the lubricant. This will help ensure that the bearings are adequately protected from shock load, vibrational load, and wear during operation. On sag mill feed conveyors, for example, tension, head, and tail pulley bearings might benefit from a grease optimised to protect against transient loads and vibration.
Table 1. Critical list of tests specifi c to mining application challenges Test standard What it measures How the test is conducted
ASTM D2266 Four-ball wear
ASTM D2596/DIN 51350 Four-ball weld Wear preventative characteristics of lubricating grease (four-ball method)
Measurement of extreme pressure properties of lubricating grease
ASTM B117 Accelerated corrosion test Salt spray corrosion The average wear scar and coefficient of friction are reported using a four-ball wear test machine and a microscope. A rotating upper ball is loaded against three stationary lower balls for one hour, at: 75˚C, 1200 rpm, and 40 kgf load. The extreme pressure properties, including load wear index, last non-seizure, last seizure and weld load, are reported using a four-ball extreme pressure test machine. A rotating upper ball is loaded against three stationary lower balls for 10 seconds, at 27˚C and 1765 rpm, while the load is increased until the lubricant boundary film is lost and welding occurs. The ability of grease to protect steel panels that were sand blasted, coated, and hung over a heated 5% salt solution is quantified by measuring the rust formation over a specified time and film thickness.
ASTM D6184 Oil separation
ASTM D1264 Water wash out Oil separation from lubricating grease
Determining the water washout characteristics of lubricating greases The bleeding of oil from grease under static conditions at a set temperature, from 150˚F to 450˚F, for typically 30 hours, through a conical nickel sieve with 1 mm holes, is measured.
The percentage weight loss of approximately 4 g of grease washed out of an enclosed ABEC 6204 test bearing, rotating at 600 rpm for one hour after exposure to 300 ml/min. of water, is reported.
Table 2. Typical bearing grease performance data comparison
Optimised AL CPC H1 AL CPX H2 Lith Cpx Consistency, NLGI #0, #1, #2 #1, #2 #0, #1, #2 #0, #1, #2 Oil separation (ASTM D1742) 0.0 – 0.2% 1 – 5% 1 – 5% 3 – 6%
Corrosion resistance (ASTM B117) 1000 hours 50 hours 50 hours 50 hours Heat and speed tolerance
pH, H20, galvanic corrosion resistance
Water washout resistance (ASTM D1264)
Four-ball weld test (ASTM D) weld point Four-ball wear test (ASTM D2266) scar diameter <0.05% 2 – 7% 2 – 10% 5 – 7% Water resistance
620 – 800 kg 250 kg 400 kg 500 kg Shock load and vibration resistance
0.38 – 0.4 mm 0.5 mm 0.4 mm 0.5 mm Bearing wear resistance Electric motors
Several professional organisations, such as EPRI and STLE, have identified that 50 – 60% of motor failures are a result of premature bearing failure, due to inadequate lubrication practices. The frequent presence of vibration diminishes bearing life. Alignment, proper footing, and base plates certainly help extend bearing life. However, the service conditions cannot be eliminated completely. Belt driven equipment puts side load on the bearings and ‘flapping’ V belts send vibration directly to the rotating shaft . The American Bearing Manufacturers Association (ABMA) has estimated that a doubling of vibration can reduce bearing life by 75%.1
If these conditions exist, it may be beneficial to select a grease with higher four-ball weld load rating: ASTM D2596. A typical electric motor bearing grease has a four-ball weld load of 160 – 250 kg, while equipment bearing grease may have typical four-ball weld load values of 250 – 500 kg.
Alternative lubricant technologies are available that can provide 250 – 400% higher load resistance and exhibit four-ball weld load of up to 800 kg. Higher film strength and load resistance reduce the likelihood of spalling. This choice would greatly increase bearing life and result in extended bearing life and extend equipment operational.
Applications exposed to water
Moisture can devastate bearing life. The polarity of water can easily displace grease as the water has a higher aff inity for ferrous surfaces. Furthermore, moisture disrupts the hydrodynamic film due to adiabatic heat vaporising of the water. Lastly, many have firsthand experience of bearing surfaces showing pitting corrosion, black oxide formation on contact surfaces, and red oxide on static surfaces.
SKF indicates that 200 – 500 ppm water ingress can reduce bearing life up to 50%, while levels over 1500 ppm can reduce bearing life by 80%.
Mining applications associated with wet processing such as trommels, wet screens, filter presses, and dewatering presses have bearings constantly exposed to corrosive water and water spray-off . As a result, grease for these applications should have superior water washout resistance and corrosion resistance, in order to mitigate the impact of water ingress by maintaining a protective film on the bearing and passivating the ferrous surface to prevent pitting corrosion.
In this case, the ASTM D1264 Water Washout Resistant Test will be the guide to selecting those greases with the smallest amount of water washout (Figure 1). In this test, a low rating result is considered best. A target might be water washout less than 0.5%.
Unlike typical water resistance tests by EMCOR, the ASTM B117 Accelerated Corrosion by Salt Fog can be used to validate the grease’s ability to prevent corrosion in a wet, exposed condition under harsh corrosive salt conditions. This test is used extensively by the paint and coatings industry to measure the corrosion resistance on paints, primers, and other coatings. A rating of 50 hours is estimated to equate to three months of real-world exposure, while 1000 hours equates to approximately five years.
In corrosive wet conditions, the choice of a grease with a longer salt fog test duration may certainly help extend bearing life and improve reliability.
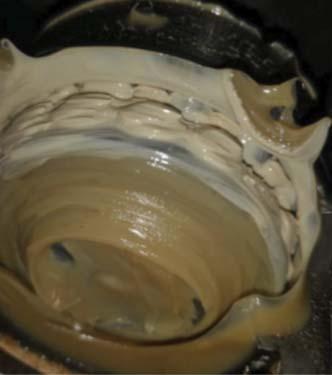
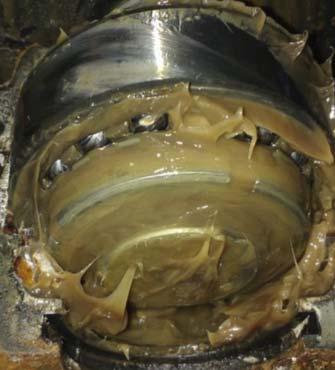
Figure 1. Water has displaced the grease from the bearing race and rotating components (left ), while grease remains in contact with bearing components (right).
Figure 2. Dewatering presses components are exposed to aggressive wet conditions.
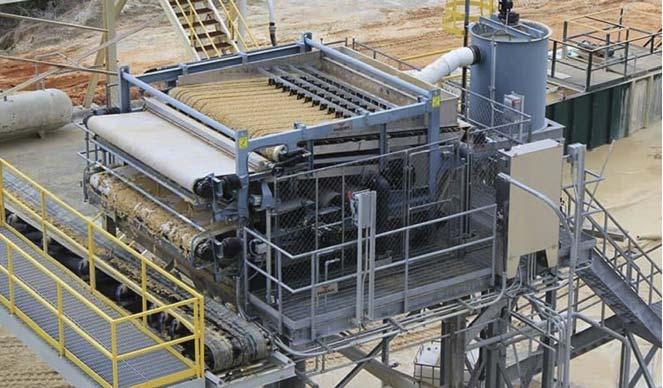
Case study: Improving the reliability of mining conveyor bearings
Challenge
A mining facility wanted to increase reliability and lower maintenance expense of its conveyor belt filters, which included primary and secondary rollers and bearings. The filter press involved 18 bearings and 20 belt support rollers involved another 40 bearings (Figure 2). The bearings were all heavily corroded due to mine water.
The bearing on the left (Figure 1) was re-greased monthly and with a complete change frequency of the bearing unit every four months due to pitting corrosion. During monthly inspection, the grease separated from the bearing components and the initiation of pitting/rust was observed in the housing. The bearings were lubricated with a lithium complex grease with low KPI’s, 5% water washout, and 50 hours Salt Fog. This type of lubricant is not suitable where there is excessive humidity.
The average bearing cost was US$350 each, and the total bearing cost equalled US$60 900/y. The total three-press cost of US$367 000/y included all labour and materials to maintain operation.
Solution
The bearing assembly was lubricated with Chesterton 615 HTG 2 – 460. This grease is well suited for large bore bearings in severe conditions. This lubricant has improved four-ball load and wear resistance of 620 kg , a low 1% water washout, and over 1000 hours of Salt Fog corrosion resistance.
Results
The grease was changed every four months and with a complete frequency of change of the bearing unit every eight months, a 200% increase in bearing life was achieved.
During the five-month inspection, the new grease remained in full contact with the rolling elements of the bearing with no separation or water displacement. The rolling elements of the bearing were also not contaminated with water. There were no indications of pitting corrosion.
Furthermore, the three-press annual cost of operation was reduced to US$198 201/y, a saving of US$168 799/y, and there was a notable increase in up-time of 200%.
Conclusion
Selecting the proper grease to use for specific mining equipment and applications is critical to reliability. Learning how to use KPIs can assist in selecting the best grease for mining applications.
References
1. American Bearing Manufacturers Association, www.americanbearings.org/