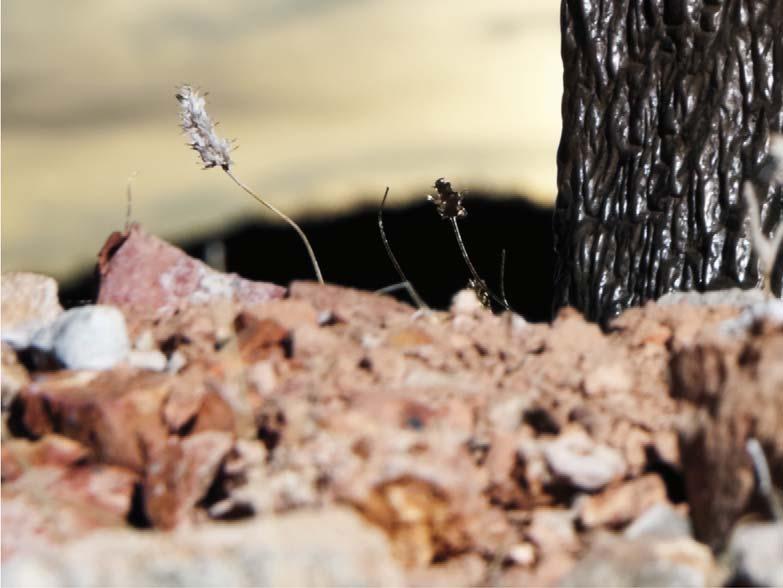
9 minute read
How To Choose The Correct Grease
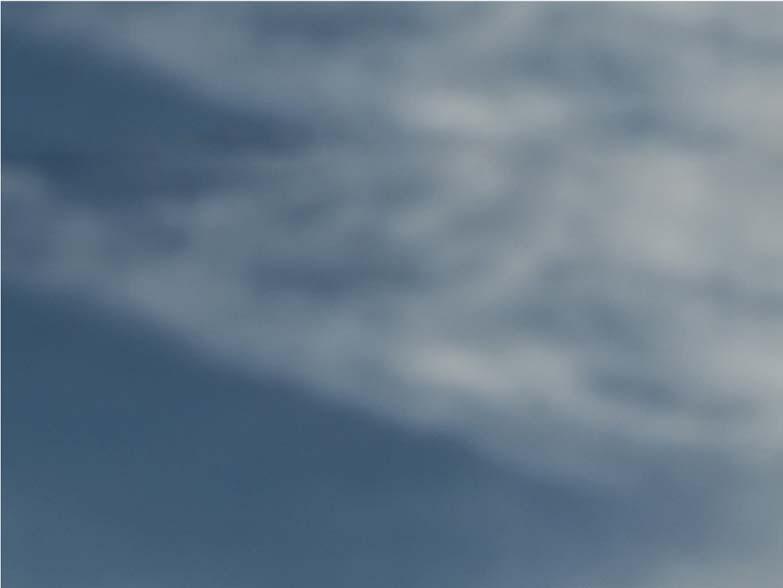
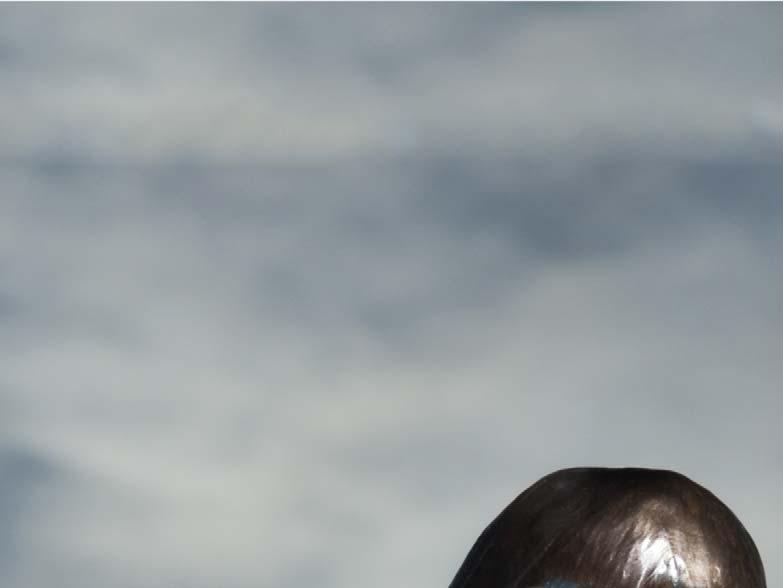
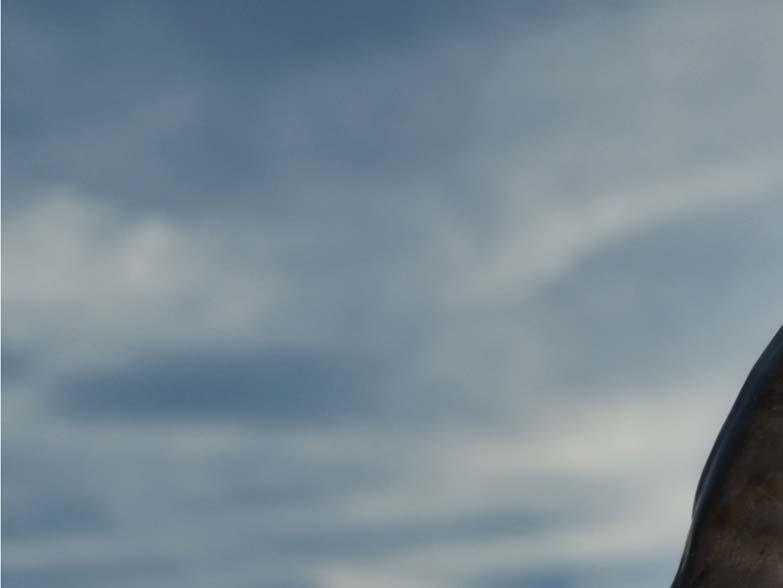


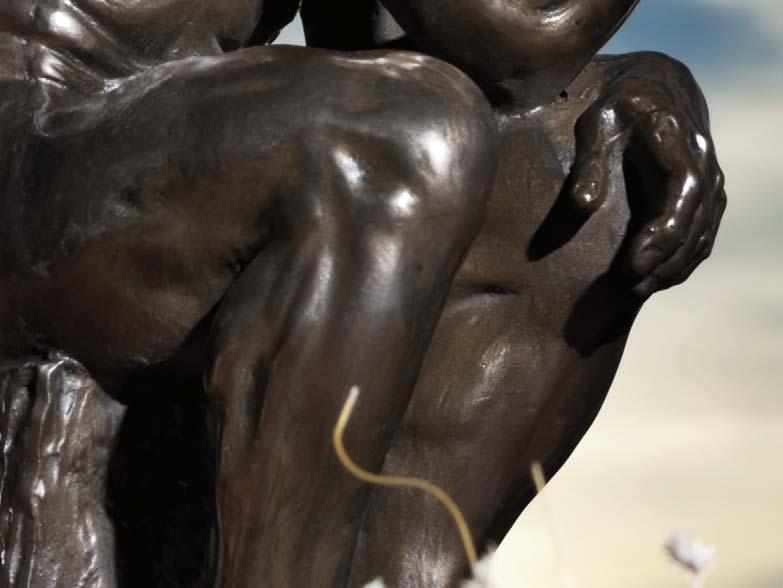

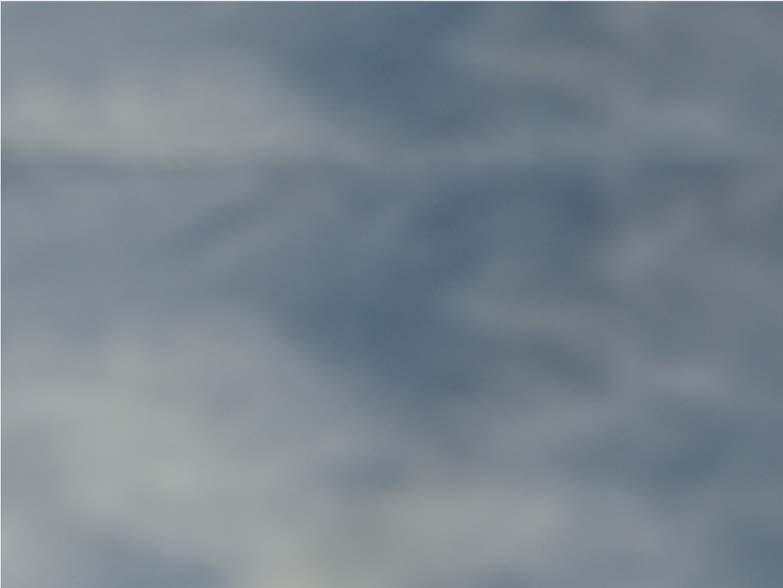



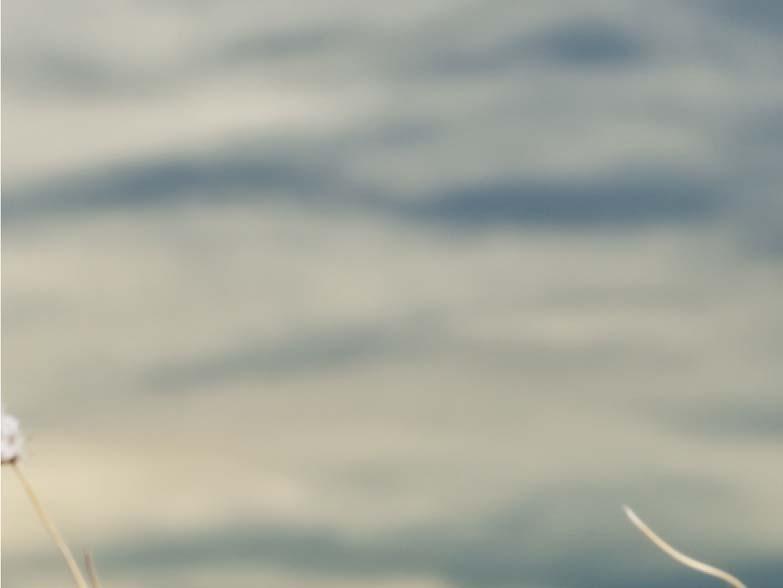



Pierre-Marie Maurice, Gautier Perrin, TotalEnergies Lubrifi ants, Nicholas Thomas, TotalEnergies Oil Asia Pacifi c, and Tony Andreopoulos, TotalEnergies Oil Australia, review the importance of choosing the right grease for mining operations.
High and low temperatures, harsh conditions, heavy loads, high and low speeds, water, shock loads and vibrations, and many other conditions are experienced by mining operations around the world. This means, for the mining industry, greases are one of the key elements to ensure reliability of critical equipment and significant advantages can be gained by choosing the correct grease.
Grease in mining
Mining equipment can be divided into two categories: mobile and fixed plant. This means that greases are expected to lubricate many diff erent types of components, such as bearings and open gears. Depending on the conditions and application, the choice of the right grease is crucial to keeping equipment running reliably for extended periods of time.
TotalEnergies has a full range of greases available for mining operations of all types. The greases range from standard lithium based EP NLGI 2, to specialty open gear greases. This article will highlight the diff erent components that contribute to the composition of a grease and the impact of the process and formulation on the final product.
Grease development
In the last three years, TotalEnergies Research and Development Centre has explored and tested hundreds of formulations of mining greases. The mining industry might seem like a mature market with proven solutions for equipment lubrication, however this is what Kodak thought in 1975 when digital photography appeared on the market. They thought hard printed film photography was the most proven and eff icient technology and that there was no need to continue innovating.
Likewise, mining operators are still challenging greases that have been in use for decades and are constantly asking questions such as: Are lithium complex greases really needed for mining equipment? Is 5% molybdenum disulfide (MoS2) content really necessary to protect the equipment or are operators paying for a useless add-on? What is the real influence of the National Lubricating
Grease Institute (NLGI) grade on performance?
The absolute truth, which every grease manufacturer would agree to, is that mining greases are full of compromises.
Unlike multipurpose applications, mining equipment is subjected to extreme loads, shocks, vibrations, dust and water contamination, and huge temperature variations. Because of slow movement, hydrodynamic lubrication is almost never achieved, meaning that metal to metal contact is almost inevitable. Furthermore, diff erent circumstances require grease-based lubrication to be delivered in diff erent forms. As an example: in winter, greases need to be pumped eff ectively from service trucks, through 20 m long pipes; and in summer, they are expected to stay in place in pins and bushes or on girth gears in 40˚C conditions. For this reason, many mining companies use diff erent products during the winter and summer seasons. Occasionally, even three diff erent NLGI grades of greases may be used.
The problem is that the perfect grease does not exist and when a choice of thickener, base oil and additives is made, it will not achieve full performance for every criterion – as seen in Figure 1, which shows two mining greases formulated in the Total Energies laboratory. These criteria are the translation of requirements for equipment protection and eff ective grease delivery.
To illustrate the compromise that must be made, Figure 2 shows each parameter placed opposite of its counterpart. For example, by improving adhesiveness by adding heavy polymer or increasing soap content, the pumpability will decrease accordingly. Certain polymer technologies can help to reduce the counter eff ect on pumpability, but they do carry a high cost and may have other limitations.
Extreme Pressure (EP) additives will also compete with anti-wear additives on component surfaces. For example, adding too much EP additive to achieve maximum protection will decrease the eff ect of the anti-wear additive, as is shown in Table 1.
For this example, the Load Wear Index (LWI) is also an important parameter to review when looking at four-ball weld load results. LWI is a measure of the relative ability of a lubricant to prevent wear under applied loads. TotalEnergies has observed greases that do not pass 500 kg four-ball weld load but then do not weld at the higher 620 kg. This ‘hole’ in the EP performance can be spotted by looking at LWI results that will be relatively low.
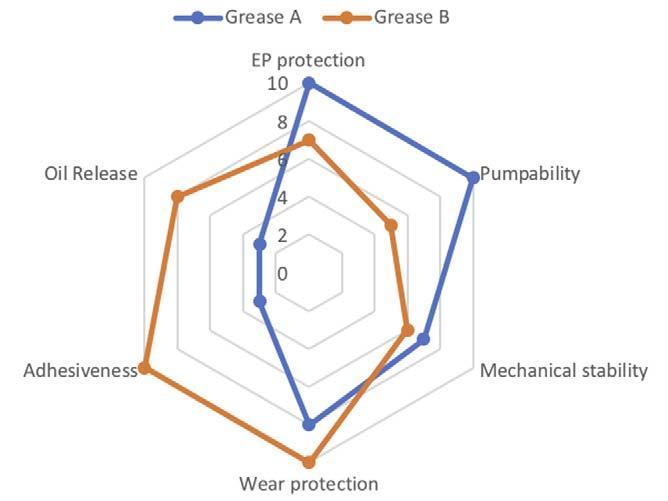
Figure 1. Performance of two diff erent mining greases formulated in the TotalEnergies laboratory.
Figure 2. Four-ball weld testing results on two diff erent mining greases, as tested by Total Energies laboratory.
Figure 3. Percentage of mass of lithium soap in the grease.
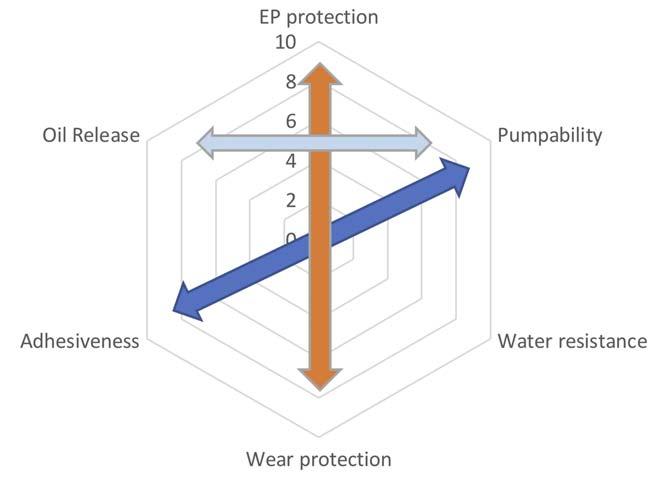
Table 1. Four-ball weld test results
Four-ball weld load – ASTM D 2596 (EP performance)
Four-ball wear scar – ASTM D 2266 (Anti-wear protection) Grease A 800 kg 0.71 mm Grease B 620 kg 0.58 mm
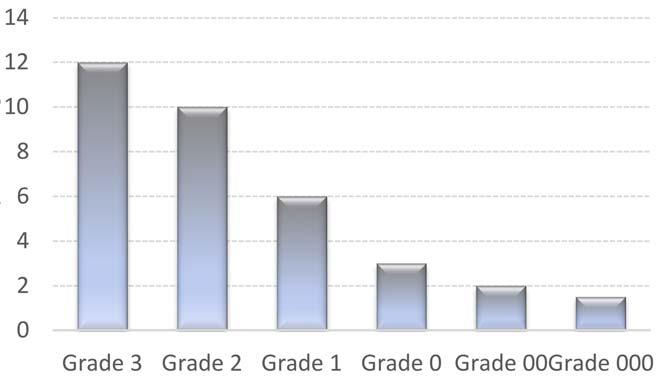
Soap content
Although the amount of soap contained in the grease never appears on the technical data sheets, it does however have an enormous influence on the NLGI grade, pumpability and adhesiveness, as well as other characteristics. The percentage of soap is directly linked to the consistency of the grease, i.e the NLGI grade. Figure 3 shows the typical quantity of lithium soap used for manufacturing diff erent grades of straight lithium, EP grease.
Manufacturing process
Manufacturing a grease is a lot more complicated than blending a lubricant, even engine oils. Just like baking a cake, timing is everything. Many grease manufacturing plants try to reduce their production time to maximise volume output, but every respected chef in their kitchen will tell you that not heating and cooling eff ectively can have a significant eff ect on the overall quality of the final product. Similarly, for greases, the same rule applies to get the perfect reaction between the alkaline (lithium, aluminium,
calcium, etc.) and the acid components. For this, the temperature needs to be controlled down to within +/- 2˚C and the cooling rate must be managed minute by minute, for every batch. TotalEnergies is one of the world leaders in grease manufacturing and pioneered the Calcium Sulfonate Complex grease, namely the CERAN range.
Compatibility
Unfortunately, no additive can protect a grease against cross-contamination. In the mining industry, aluminium greases are the most common types of greases for girth gears (TotalEnergies COPAL OGL and GRAFOLOG H range) as they have a great rheological behaviour, ensuring good pumpability and good adhesiveness. On the other hand, lithium-based greases are used predominantly in pins and bushes and bearing applications (MULTIS MINE range).
The issue is that these two thickener types of grease are completely incompatible. So, what does happen when incompatible greases are mixed? Table 2 reflects what happens to some of the key properties of greases when mixed with an incompatible grease type. Indeed, Table 2 shows that the grease resulting from mixing both greases together is completely out of line with specifications. This is why it is crucial to have a dedicated field engineering team, such as that which TotalEnergies has implemented for its mining customers, to help and guide clients on the right path to eff ective grease lubrication.
Base oil
The viscosity of the base oil used in the formulation also plays a role in the performance of the grease, but it should not be the main criteria for selection. Yes, high viscosity protects against low speed and high load conditions, but TotalEnergies’ research centre also has formulated greases with a 460 cSt (when tested at 40˚C) base oil that have better EP performance and anti-wear protection than a 680 cSt base oil grease. Most of the company’s formulations are a blend of mineral and highly refined base oil, but synthetic base oils are also used mainly for arctic product applications, as well as locations where high temperatures are experienced for extended periods.
TotalEnergies is also currently working on bio-based formulations with excellent performance to fit the higher demand for such products.
Table 2. Testing results when mixing thickeners
Aluminium based grease 50/50 mix of both greases Lithium based grease
Penetration after 60 strokes 371 412 280
NLGI grade 0 00 2
Dropping point (˚C) 195 156 201
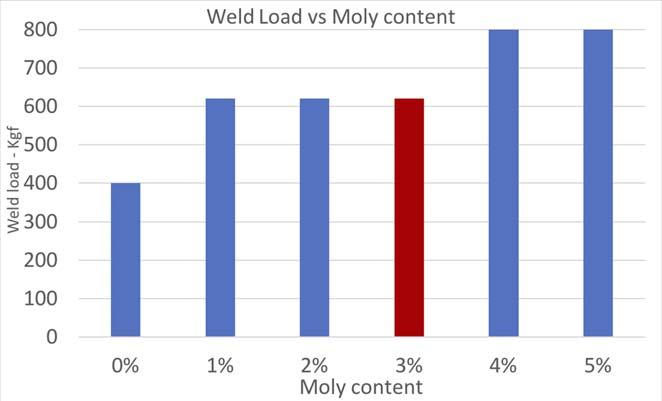
Figure 4. Weld load vs Moly content.
What about the content of solid additives?
Here again, less is not more, but what is enough is important. MoS2 prices are skyrocketing and this is making the industry review the 5% MoS2 content imposed by certain manufacturers.
A recent internal study on TotalEnergies MULTIS MINE lithium grease showed that with the right mix of EP and anti-wear additives, 3% of MoS2 is largely suff icient to ensure a result of 620 kg on the four-ball weld load test – ASTM D 2596 – and to keep the wear scar low.
Adding more than 4% allows grease to potentially reach 800 kg, and could be considered an ‘extra safety layer’. However, this is over engineering, as this level of performance is not required in this type of heavy-duty mining equipment.
Performance
Performances that are mentioned on a technical data sheet (TDS) are not always directly transferable to the equipment. For instance, if the automatic greasing system is injecting grease in the application twice as oft en than the necessary amount, long lasting EP and anti-wear protection are irrelevant. The grease will be replaced long before these additives are depleted.
Case Study
There is a common saying among grease customers, “it is better to over-grease and be on the safe side”, but this is not entirely accurate. TotalEnergies advises its customers on how to use the right quantity of grease depending on their circumstantial constraints – promoting greater eff iciency in grease usage, whilst maintaining productivity. The benefits of this practice are illustrated by a recent example of the company being able to facilitate a decrease in the number of pins and bushes utilised by a major Australian mining customer by 25%, in addition to a decrease in grease consumption. The customer had been used to seeing grease overflow out of components when they were greased with their current product, and it was initially a challenge for them to accept TotalEnergies’ proposal. However, demonstrations showing that the new grease would stay in place longer in the application, thus providing a better level of protection with lower grease consumption, proved convincing.
The best choice and use of a grease can only be made with a strong maintenance programme that will follow closely the wear of the equipment and detect any over or under performance of the set-up over time.