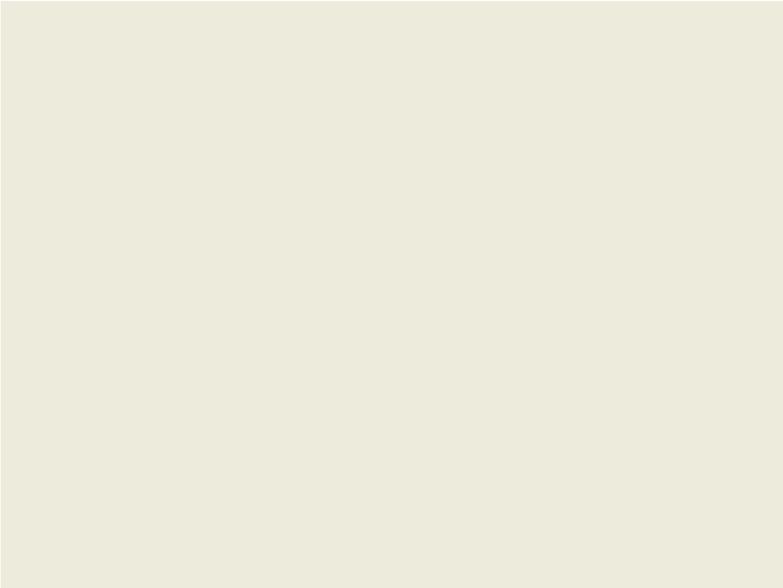
8 minute read
Responding Rapidly To Flotation Variability
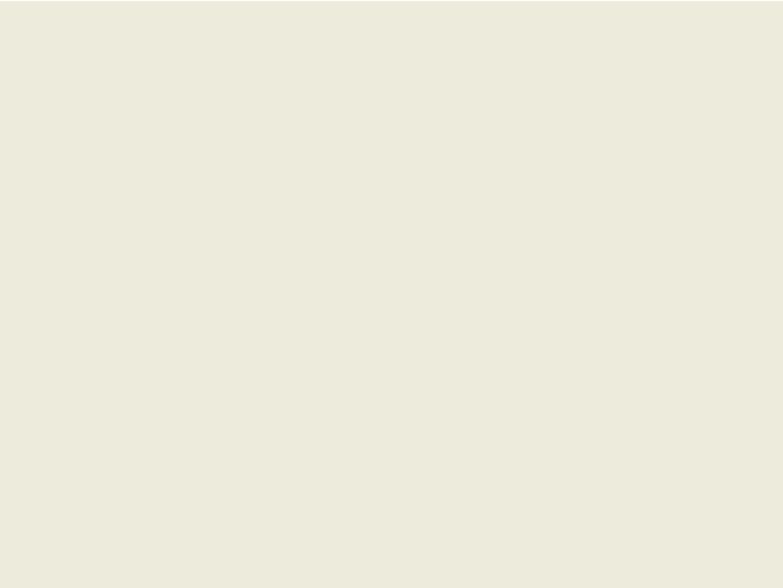

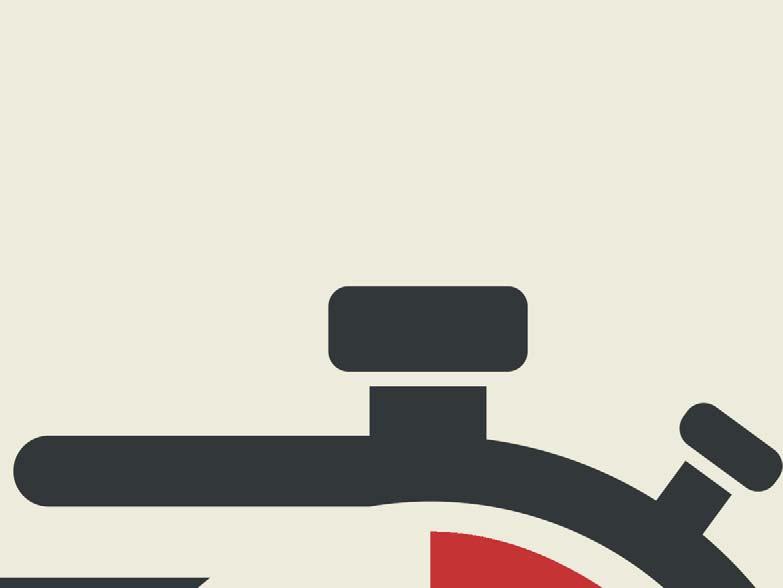
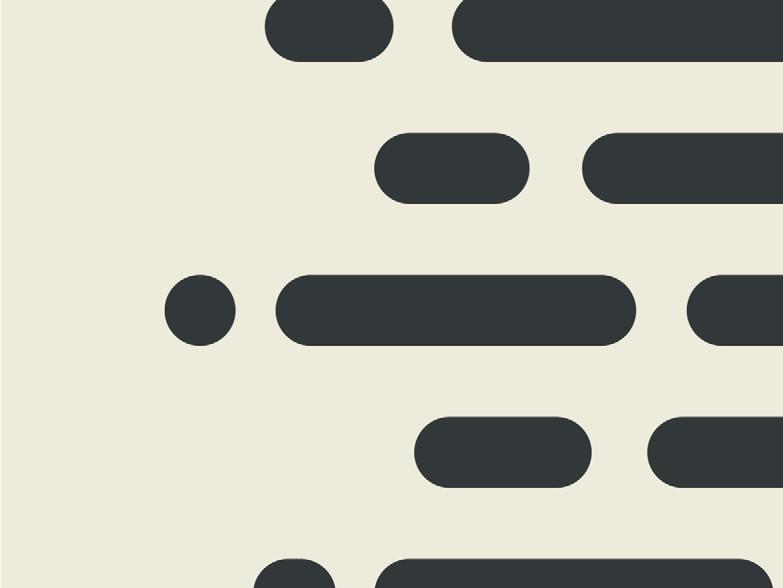
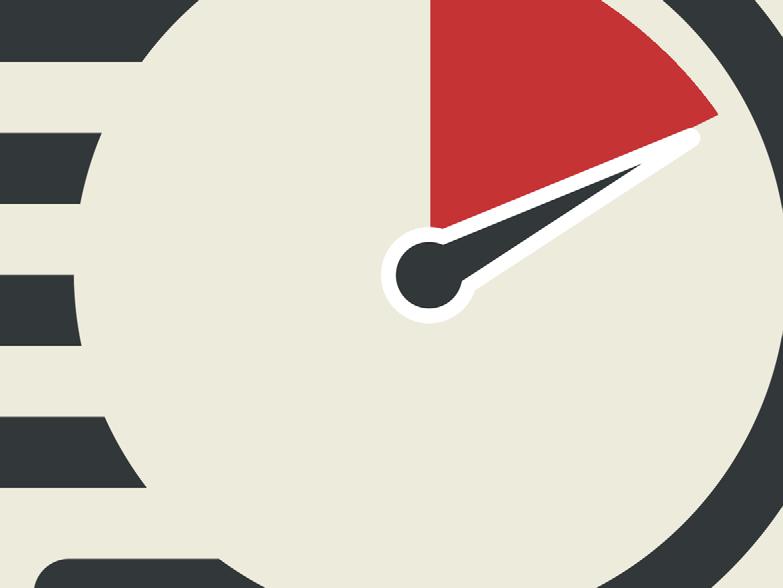
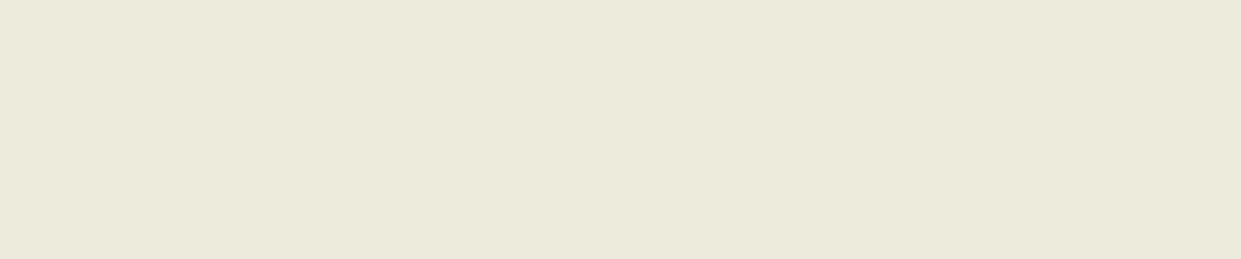


Jacques Bezuidenhout, Nalco Water,
USA, addresses why fl otation circuits have to continually improve and adapt to the changing needs across mineral processing operations.
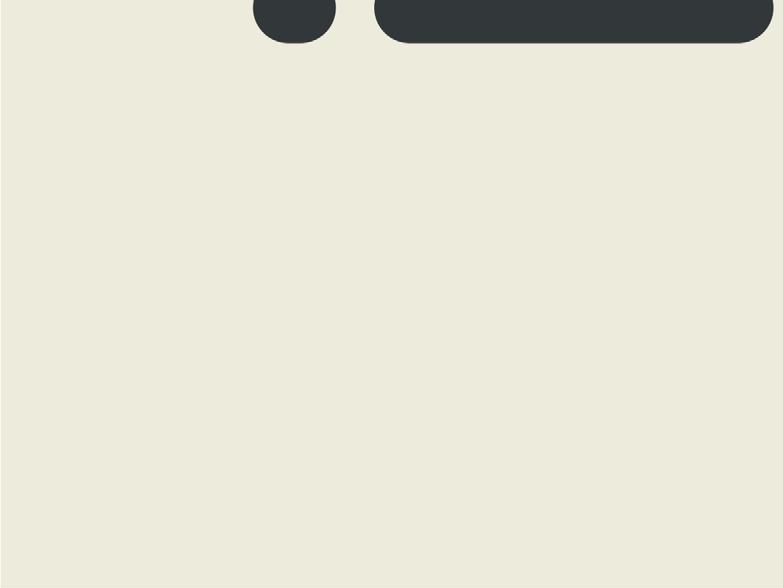
Flotation is at the heart of mineral processing. An optimised flotation circuit can positively impact mineral recovery while maximising grade. Mineral processing plants continue to face challenges with increasing variability in flotation, such as: ore body changes, shift ing customer requirements, and more. Furthermore, mining companies are examining ways to make their flotation processes more eff icient, looking at methods such as coarse particle flotation
to drive operational savings and reduce energy use. As a result, the performance of each flotation circuit must be more agile than ever – continuing to improve and evolve to adapt to changing needs across mineral processing operations.
Flotation variability
Sulfide flotation variability is a challenging yet constant reality that faces every mineral processing operation. Variability can come from a variety of outside influences, including: changes in the ore body itself, shift ing customer demand or quality requirements, focuses on more sustainable operational processes, and more. Mining companies face the dual pressures of responding to an increasing demand for higher production, while adapting to increasing variability that impacts their mineral processing operation. In addition, mining companies are challenged to achieve these demand increases while reducing their environmental impacts for a more sustainable carbon footprint.
Nalco Water, an Ecolab company and a global provider of sulfide flotation solutions, recognises that the challenges are not isolated to a specific region or market. With flotation specialists, on-site sales engineers and support laboratories around the world, the company continues to see variability as a primary challenge for mineral processing operations, across a variety of mineral processing environments and localities. Nalco Water believes that two keys to adapting to variability are knowledge and speed. A rapid response to changes within a flotation process can help a plant maintain operations that are eff ective and productive.
A rapid response to flotation variability requires a mineral processing plant to be keenly aware of the chemical, mechanical, and operational factors that impact their process. Performance monitoring of their chemical reagents, mechanical equipment, control systems, unique minerology, and more can help them mitigate the eff ects of variability on recovery. The company delivers a unique range of solutions to help customers monitor these factors. In addition to off ering advanced frother and collector chemistry, the company takes a unique, wholistic service approach to monitor the performance impacts on a customer’s flotation circuit. The company has also recently launched a digital platform that uses innovative monitoring technology to deliver predictive, actionable insights that their technical service team can use to respond rapidly to changing flotation dynamics. The combined chemical, service and digital solution, called the Flotation 360, helps customers address changes expediently to maximise selective recovery, grade, and, ultimately, profitability.
Nalco Water flotation consultants, engineers, and laboratory personnel monitor a variety of performance indicators to measure the eff ectiveness of a customer’s flotation circuit, such as: froth characteristics, collector formulation, mineralogical characterisation, and more. Emerging technology, such as a mobile bubble sizer measurement system, helps Nalco Water check cell mechanics and troubleshoot issues in real time. As a result, the company can help mineral processing plants implement process improvements quickly to ensure productive flotation performance.
While performance monitoring for the flotation circuit is key, Nalco Water also believes that a wholistic approach to the entire mineral processing operation is prudent and necessary. Performance enhancements and operational changes in the flotation circuit can cause downstream eff ects if not carefully assessed before implementation. Nalco Water helps mineral processing plants to examine and evaluate these potential impacts to help mitigate risks from changes in the flotation operation.
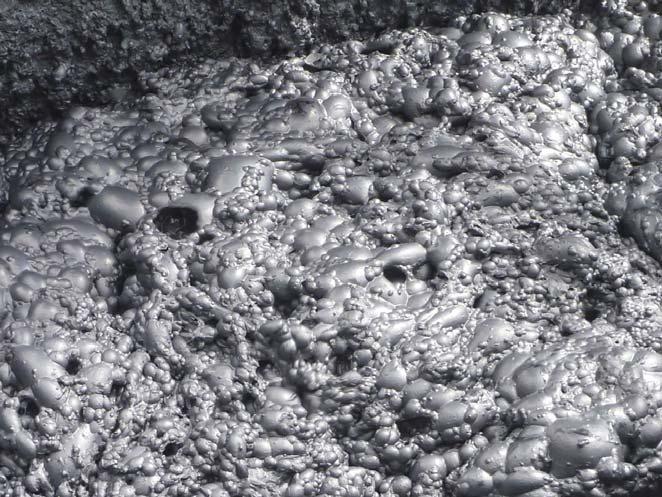
Figure 1. Froth within the sulfide flotation process.
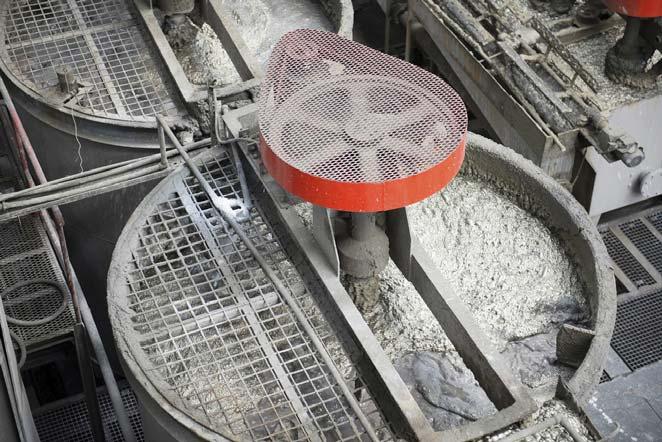
Figure 2. An overhead view of a sulfide flotation circuit.
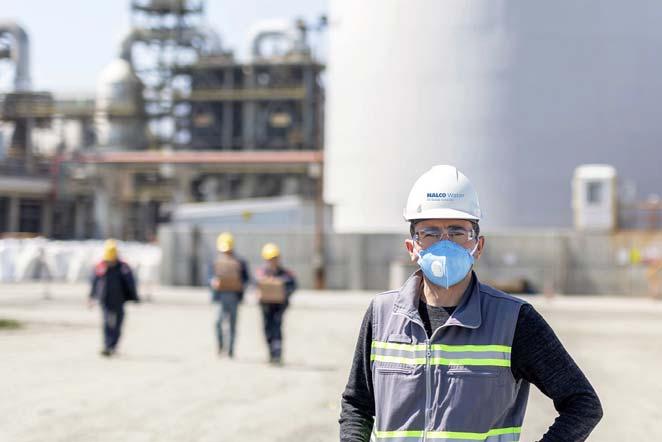
Figure 3. An engineer servicing a plant on-site.
Case study: North America
For a copper mineral processing plant in North America, ore variability became a daily reality as the plant began to
process a more diff icult type of ore. The customer needed a solution that would help them improve overall recovery for more than one type of ore, specifically copper and molybdenum, which would help improve their total operational costs. The ore contained a suff icient grade of molybdenite to concentrate, making it even more critical to increase the recovery for both minerals.
Nalco Water applied a comprehensive approach to the challenge, surveying the ore minerology and operational conditions of the flotation circuit, as well as obtaining a deeper understanding of the plant’s metallurgical objectives. Through extensive laboratory testing and a thorough plant trial, Nalco Water was able to design a tailored frother programme that improved metallurgical performance while reducing reagent consumption and minimising volatile organic compounds for copper sulfide and primary molybdenite. The technology also demonstrated the unique ability to capture ultra-fine molybdenite not recovered using traditional flotation reagents.
The optimised frother programme ultimately helped the mine to significantly improve both copper and molybdenum recoveries using the same dosage as the previous frother programme. As a result, the customer was able to improve their overall productivity and total operational cost.
Case study: Latin America
For another copper mineral processing plant located in Latin America, ore variability was an influencing factor behind over-foaming events, which was ultimately impacting production capacity and total operational costs. Additionally, the customer had a number of sustainability metrics to achieve and wanted to find a solution that would help achieve their process eff iciency goals. The customer needed a frother solution that would reduce over-foaming events in an eff ective way, driving reduced operational costs, increased productivity, and improved operational eff iciency to meet their sustainability and business objectives.
The regional Nalco Water flotation team developed a study to reduce over-foaming events and optimise the frother blend. Through a robust process working with the customer’s metallurgical team, Nalco Water was able to develop an optimised frother formulation that produced significant productivity benefits, while also delivering on the customer’s sustainability and business performance indicators.
To build the solution, Nalco Water, plant management, and plant engineers collaboratively performed a market study on similar challenges and designed a unique laboratory screening process before ultimately developing the specialised frother formulation. The team performed in-plant trial testing to validate the benefits of the frother over an eight month period. During the trial, the Nalco Water technical team was tasked with reducing over-foaming events without impacting metallurgical performance. The trial period yielded several positive results, specifically reducing over-foaming events by 33% and their subsequent impacts on production by 44%. By reducing the challenges with over-foaming, the technical team was also able to mitigate health and safety risks for plant associates who were responsible for cleaning the plant aft er an over-foaming event. Moreover, the optimised frother blend allowed the plant to reduce overall consumption by 3%, resulting in cost savings and a more eff icient process.
The optimised frother solution ultimately helped the customer achieve significant cost savings and realise key sustainability benefits. From a cost perspective, the customer ultimately saved over US$7 million in production losses from over-foaming events. The exponential return on investment (eROI) for the customer was US$2.4 million in overall savings. From a sustainability perspective, the customer reduced their carbon dioxide emissions by 11 000 kg, due to the movement of fewer trucks to deliver frother reagent and over-foaming cleaning supplies. As a result, the customer has been able to maintain their desired production capacity while meeting their business and sustainability goals.
Sustainable fl otation operations
In addition to solving variability issues, many mineral processing plants are looking to make their flotation operations more eff icient and sustainable overall, as outlined by the case studies. One of the drivers behind this shift is the sustained focus on environmental stewardship within mining, which has resulted in a specific focus on reducing carbon emissions across mining and mineral processing operations.
The industry continues to look for dynamic solutions that will help them recover more valuable minerals while using less energy. Coarse particle flotation can help mineral processing plants save energy while still recovering what they need for production. A finer ore grinding requirement uses more energy and requires more operational investment, and a coarser grinding requirement can help a plant reduce both its operational costs and its overall carbon footprint, while still maintaining optimal production.
Mineral processing plants are looking for innovation to push today’s boundaries on coarse particle flotation. Nalco Water has observed a number of trends across its global customer base, including the use of larger flotation cells and adoption of digital technology to monitor and measure performance. Today, the company helps customers selectively recover relatively coarse particles (between 200 – 250 μm) and continues to develop solutions for where the industry is heading overall, which is to selectively recover 300 μm particles. As the industry evolves, coarse particle flotation will continue to emerge as a driving force for greater eff iciency and plant sustainability.
Conclusion
The challenges created by variability and a need for greater process eff iciency will continue to persist. Mineral processing companies will need to continue to develop innovative solutions and work with agile partners to be able to respond to these challenges and meet an ever-growing demand for their products. It is recommended to work with a partner who can use a variety of chemical and digital monitoring solutions to ensure the continual performance of a flotation circuit. From the partners’s perspective, the key is to have a strong service partnership that off ers the support needed to implement process improvement projects in a way that maximises recovery and grade, while mitigating operational and environmental impacts.