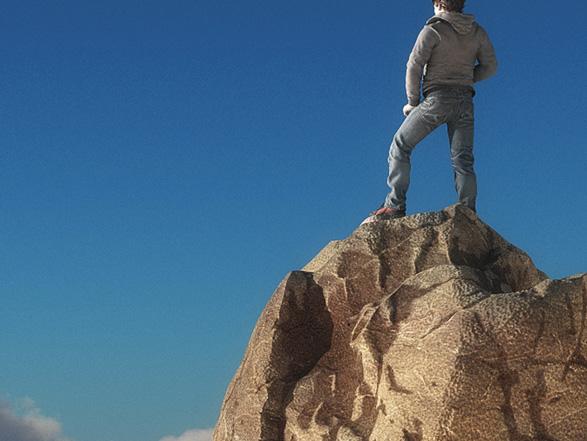
9 minute read
Rise to the challenge
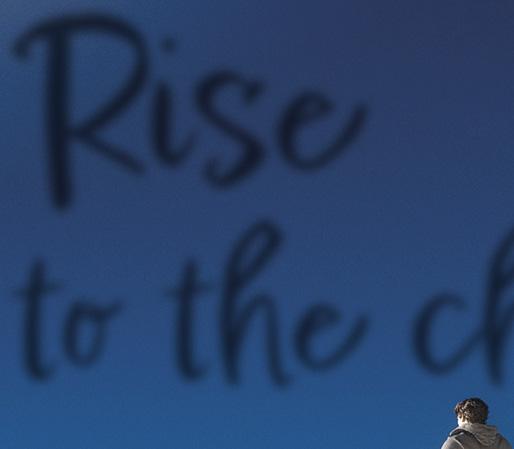
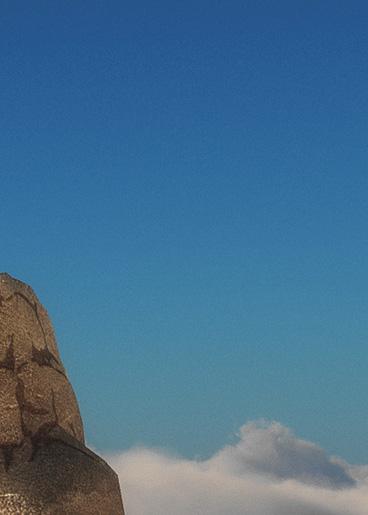
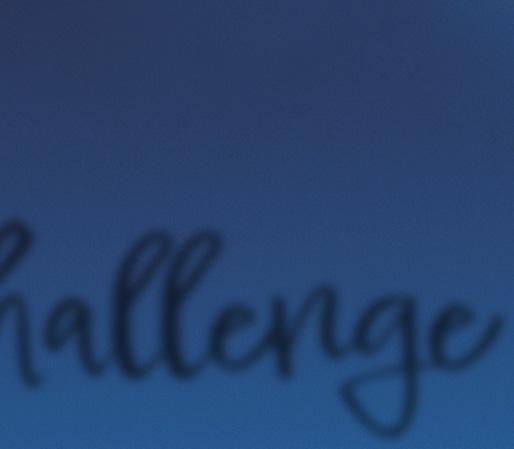
Ingo Emde, R. STAHL, Germany, discusses the challenges of fuel gas supply systems and how these can be addressed through the installation of a remote I/O system.

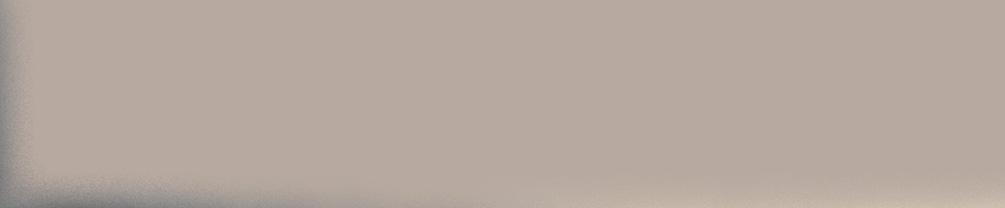
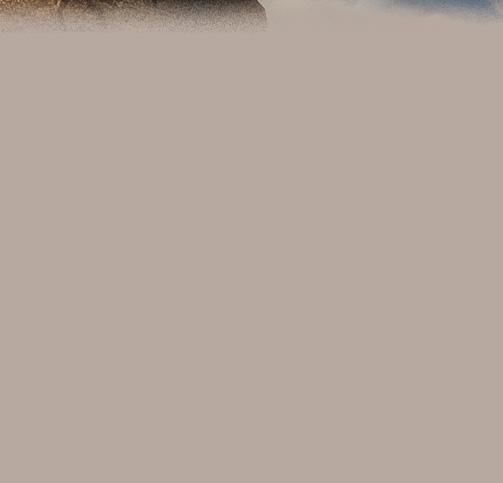
International shipping today remains a growing source of greenhouse gas (GHG) emissions with, according to the International Maritime Organization (IMO), maritime transport emitting approximately 940 million tpy of CO2 and being responsible for 2.5% of GHG emissions. Furthermore, the use of heavy fuel oil not only causes CO2 emissions but also releases fine dust, nitrogen oxide, and sulfur dioxide that significantly contributes to air and water pollution.
To this end, legal restrictions on the use of heavy fuel oil are becoming ever stricter. In 2006, the IMO tightened the specified limiting values for permissible sulfur content in ship fuels and expanded restrictions on the use of fuel in inland waters, in EU seaports, and in Sulfur Emission Control Areas (SECAs) such as the North Sea, the Baltic Sea, and the Californian coastal region of the US.
As a result, ship owners must refuel their ships with much more expensive, reduced-sulfur marine diesel. In January 2020, the IMO introduced even stricter environmental requirements regulating the use of heavy fuel oil.
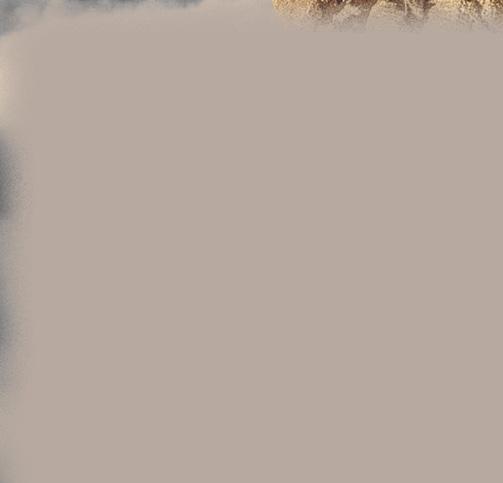
LNG – an environmentally friendly alternative
It is against this backdrop of growing restrictions that the shipping industry has been undergoing significant changes in the way it considers the fuel it uses, with more attention paid to LNG and liquefied petroleum gas (LPG) drives as either an alternative or as a transitional technology that conserves resources.
Compared to conventional maritime fuels, the use of gas-powered combustion engines reduces fine particle and nitrogen oxide emissions by up to 90% and sulfur dioxide emissions by 100%.
LNG fuel also offers benefits in terms of cost. While the type of ship and the speed of the wider gas infrastructure will determine when the retrofitting and installation of LNG drives will yield a profit, current model calculations assume that gas drives on ships will pay off after an average of five years, based on strict environmental requirements, the price of maritime diesel, and decreasing costs of LNG supply.

Other cost benefits include the fact that there is no need to install an exhaust gas cleaning system, which can be expensive. LNG and LPG drives can also be used in ports – a key benefit as more and more port cities consider making the use of costly shoreside power supplies mandatory for marine diesel fuel ships to prevent air pollution. This technique is known as cold ironing (when ships had coal-fired engines) where the ship’s power load is transferred to the shoreside power supply without disrupting onboard service.
The benefits of LNG-fuelled shipping are also being seen in the market and commercial decisions. In March 2021, E&P major Shell signed an agreement to charter 10 new very large crude carriers (VLCCs) powered by dual-fuel LNG engines. By the end of 2021, the operator will have 14 LNG-fuelled carriers in service. This is in addition to the hundreds of retrofits expected.
Fuel gas supply systems – a sophisticated network
A key element of LNG-powered ships is the fuel gas supply system (FGSS) that supplies fuel to the motors and comprises the gas tank itself, as well as evaporators, compressors, pumps, and heat exchangers.
FGSSs provide a sophisticated network with temperature, pressure, and flow value data provided to the ship control system and alarm control monitoring system (ACMS), if present.
Yet, FGSSs come with challenges as well, particularly because of the hazardous areas in which the systems operate due to the high volatility and ignitability of the conveyed gas.
Retrofitting ships powered by heavy fuel oil to use FGSSs will therefore mean that there will be additional hazardous areas onboard that require the integration of explosion protected input/output (I/O) and display systems in the ship’s control system and onboard alarm control monitoring. In such cases, the measured values must not only be accurate but also be determined and transmitted using explosion-protected, intrinsically safe sensors and network components.
The rest of this article will examine how these challenges can be met and how an effective, resilient, and safe FGSS can be put in place, thereby powering not only ships but the growing uptake of LNG in marine transportation.
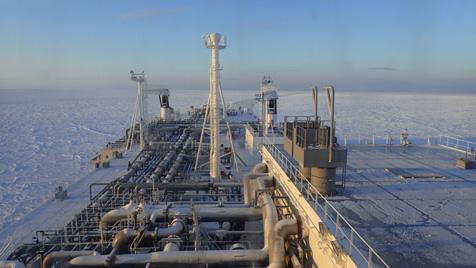
Figure 1. A key element of LNG-powered ships is the fuel gas supply system (FGSS) that supplies fuel to the motors.
Figure 2. The IS1+ Remote I/O system for modern process automation offers support for PROFINET, EtherNet/IP, Modbus TCP, and PROFIBUS DP.
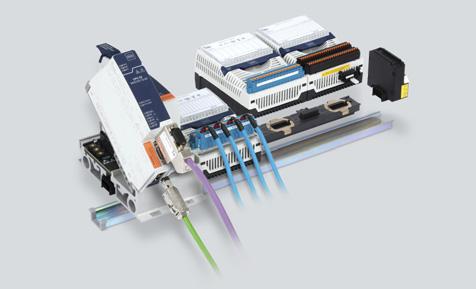
FGSS challenges – data flow, flexibility, and resilience
Yet, what are these challenges?
Data flow is one such challenge with the need to not only transmit the sensor data from hazardous zones to the ship’s control centre without interruption, but also generate recorded data, visualisation, and monitoring for the ACMS. This is complicated by the additional hazardous areas onboard and the need to integrate hazardous areas in Zone 1 and 2 into the control systems.
Other data flow issues include electromagnetic compatibility (EMC) where it is vital that devices do not interfere with other devices through electrical and electromagnetic interference.
A flexible system is also important with the need to add or replace modules as needed in hazardous areas as well as expand the installation at any time.
Finally, resilience and reduced maintenance is also vital with the need for the infrastructure around FGSSs to perform at all temperatures and to be made of resilient materials.
A remote I/O system
With these issues in mind and the importance of safe networking in hazardous areas, R. STAHL, a supplier of explosion-protected components and customer-specific system solutions, has developed a solution for intrinsically safe sensor/ actuator networking around its IS1+ Remote I/O system.
The system is designed for Hazardous Zone 1 – an area in which an explosive gas is likely to occur in normal operation and is particularly suited to FGSSs due to the additional hazardous areas onboard that require the integration of explosion-protected I/Os and display systems in the ship’s control system and onboard ACMS.
The IS1+ Remote I/O system, which has all required ship approvals and certificates according to the EU RO Mutual Recognition Group, combines a series of robust human machine interfaces (HMIs) which are linked up with explosion-protected versions of all required network components. The result is problem-free, convenient access to process data in the environment immediately surrounding the applications and an addressing of the challenges of FGSS deployment.
Data transmission
The devices within R. STAHL’s system use multi-mode fibre optics for data transmission, offering a simple solution for all control systems or ACMSs, enabling signals from hazardous areas to be connected to the distributed control system via PROFIBUS DP, Modbus RTU, or Ethernet Modbus TCP, EtherNet/ IP, and PROFINET.
The IS1+ Remote I/O system features eight-channel analogue I/O modules with HART, 16-channel digital I/O modules, four- and eight-channel digital output modules, and eight-channel temperature modules for resistance temperature detectors and thermocouples.
On analogue modules, line faults are indicated by a red LED. On digital modules, the switching state is also indicated by a yellow LED.
Resilience and maintenance
When it comes to resilience, the IS1+ series Remote I/O systems feature seawater-resistant enclosure materials, a vibrationresistant design, and resistance to electromagnetic influence – very important in the maritime industry and a challenge already mentioned where there are strict EMC requirements, due to the mission critical nature of onboard wireless equipment and sea rescue call frequency.
Due to the low-power technology designed specifically for the IS1+ I/O level, the modules are also suitable for an extended temperature range between -40˚C and 75˚C and reach a service life of 15 years.
All modules are equipped with additional self-diagnostics functions based on NAMUR NE 107 and as a result, the ‘maintenance required’ warning message is sent 12 months before the end of the expected service life. A blue LED on the module also clearly indicates when maintenance is required.
The importance of flexibility
Another key challenge that is being addressed through the I/O system is that of flexibility. Installation is seamless with the remote I/O systems coming in suitably sized enclosures ready for installation with the central processing unit (CPU) modules and used as gateways for connecting the remote I/O systems to the wider automation system.
In addition, the remote I/O system provides the option to expand the installation at any time using the plug-and-play principle. If required, all modules can be added or replaced on-site without interrupting operations. Expanded diagnostics also provide other options, which is why all Zone 1 modules feature one or two LED displays per channel.
End users applications
Many customers today are requesting an FGSS connection that works with remote I/O systems for quality assurance and safety reasons.
R. STAHL has been implementing remote I/O installations on ships and offshore platforms for 30 years, and this experience is vital when installing the new IS1+ Remote I/O system, with the solution already tried and tested on several hundred LNG tankers and other oil and gas applications.
The company initially received an order at the end of 2019 to outfit four freight ships, one tanker, and five container ships and business has built up from there – sometimes in particular regions.
In South Korea, for example, shipyards are recording increasing demand for LNG-powered ships and many shipbuilders have opted for R. STAHL’s remote I/O system for sensor data transmission from the FGSS to command levels and alarm control monitoring systems. Over the past year, two of the largest shipyard operators in South Korea (as well as also being renowned companies in heavy industry) have approached R. STAHL. In these cases, the requests involved adjusting the specifications of existing ship control systems and the FGSS connection for use with R. STAHL products.

Figure 3. R. STAHL has been installing remote I/O systems on ships and offshore platforms for over 30 years.
Rising to the challenge
While there is a long way to go with LNG-fuelled shipping (in 2019, of the approximately 60 000 cargo ships in operation around the world, only 321 were powered by LNG drives, with orders in place for a further 510 ships), there is little doubt that the effective retrofitting and operation of FGSSs in hazardous areas will become even more important. Companies, such as R. STAHL, are rising to the challenge.
ACUUM JACKETED P VACUUMJACKETEDPIPE
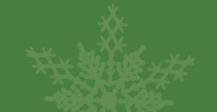

THE MOST COST-EFFECTIVE WAY TO TRANSFER CRYOGENIC LIQUIDSTHE MOST COST-EFFECTIVE WAY TO TRANSFER CRYOGENIC LIQUIDSTHEMOSTCOST-EFFECTIVEWAYTOTRANSFERCRYOGENICLIQUIDS

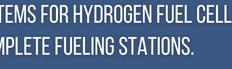