
8 minute read
Saving money, saving lives
Figure 3. Cellular glass insulation can provide passive fire protection for structural elements and storage spheres even in rapid-rise temperature fires.
US$2.5 trillion in damage every year.2 Carbon steel vessels, piping and supports are vulnerable to corrosion, which can lead to leaks or spills. However, for corrosion to occur, moisture must be present. Using water and vapour-proof insulation can help mitigate the risk posed by atmospheric water in humid conditions, or salt spray in facilities close to the shore or offshore completely.
If the insulation system is penetrated or absorbent insulation is used, moisture can be retained and react with underlying steel. If moisture reaches the underlying metal of a tank or strut, it can promote the development of corrosion under insulation (CUI). Since this damage is hidden, it can remain undetected until a leak occurs. These leaks can be particularly problematic when the materials stored are at pressure, are flammable, or both. If corrosion is not found, it could cause damage to the loadbearing capacity of structural elements.
Correctly designed and installed insulating systems, using waterproof insulation, can help prevent moisture from entering the insulation system. Selecting closed-cell, impermeable, non-absorbent and non-wicking insulation provides a layer of protection, preventing moisture from penetrating to tanks or support structures.
Goal three: reducing the risk of fire damage
Fire is an ever-present risk at facilities that store flammable hydrocarbon and petrochemical products. Steps can be taken to help mitigate those risks and improve facility and employee safety, should a spill or leak occur. In addition to limiting heat transfer for storage spheres and bullet tanks, insulation can be used to provide passive fire protection to the vessel and support structures.
Applying non-combustible, closed-cell cellular glass insulation that will not burn, contribute to fire spread or generate smoke helps to protect both equipment and facility personnel by reducing the rate of heat transfer during a fire.
Hydrocarbon fires can reach temperatures of 1093.3°C (2000°F) very quickly, which is a danger to the integrity of structural steel supports used to hold storage tanks. Structural steel can lose up to 50% of its load bearing capacity when the temperature reaches 537.7°C (1000°F). Weakened supports pose a risk to personnel onsite and the stability of elevated containers.
Cellular glass insulation can be used to extend the time it takes for the steel substrate to reach the structural failure point in the event of a fire. This means that responders have more time to address the fire before the steel support structure holding the tanks in place reaches the point of failure. Third-party testing has demonstrated that a double-layer cellular glass insulation system applied to structural steel will prevent the insulated metal from reaching 537.7°C (1000°F) for up to 180 minutes, based on the UL 1709 Standard for rapid rise fire tests of protection materials for structural steel test method.3 Along with slowing the rate of heat transfer into the structural steel, cellular glass insulation does not burn, generate toxic smoke, or promote flame spread.
Conclusion
The main risk areas for damage that spheres, bullet tanks and the support structures face at an industrial facility include protecting thermal performance, mitigating corrosion and improving fire safety. All of these areas can be addressed using a properly designed and installed insulating system.
Using insulation with consistent thermal performance, which is impervious to moisture and prevents heat gain, helps ensure efficient thermal performance. An insulation system using closed-cell cellular glass insulation that is impermeable, non-absorbent and non-wicking helps to protect against the development of corrosion, and reduces the possibility of flammable liquids being absorbed.
Similarly, employing insulation that is non-combustible will not spread flame or generate toxic smoke and can protect structural elements from heat damage. This helps address fire safety and structural integrity at a facility. Although the list of requirements sounds lengthy, closed-cell FOAMGLAS® cellular glass insulation can address the primary areas of risk faced by storage spheres, bullet tanks, and the related support structures.
References
1. GUSYACHKIN, A.M., et al., ‘Effects of moisture content on thermal conductivity of thermal insulation materials’, IOP
Conference Series Materials Science and Engineering, (2019). 2. ‘Measures of Prevention, Application and Economics of
Corrosion Technologies Study’, NACE International, (2016). 3. ‘Standard for rapid rise fire tests of protection materials for structural steel (UL 1709)’, Underwriter Laboratories, (2017).
Tony Collins, EonCoat LLC, USA, discusses how a considered choice of tank coating could help to improve workers’ health, as well as limit negative environmental impacts.
Working downstream has always been inherently dangerous, as the industry deals with flammable products. The sector has led society’s efforts to make the workplace safer, with safety equipment, training and procedures. It has saved a lot of lives, and improved the quality of many others.
Half a decade ago, a man walking an I-Beam at 300 ft without a safety belt or a safety line was a common sight, as was pulling asbestos blankets off a tank or pipeline with no PPE other than a hard hat and safety glasses.
Much has changed since then. It was not the case that people did not care about safety 50 years ago, but the information we have today was not available at that time.
Nowadays, everyone is tied off when working higher than 4 ft; no one is allowed in a confined space without a rescue plan; and asbestos is now removed by trained professionals who encapsulate it and safely dispose of it in sealed containers before taking it to landfill.
We are all grateful to those who pioneered safer ways to work, and the pursuit of safer ways of working is ongoing.
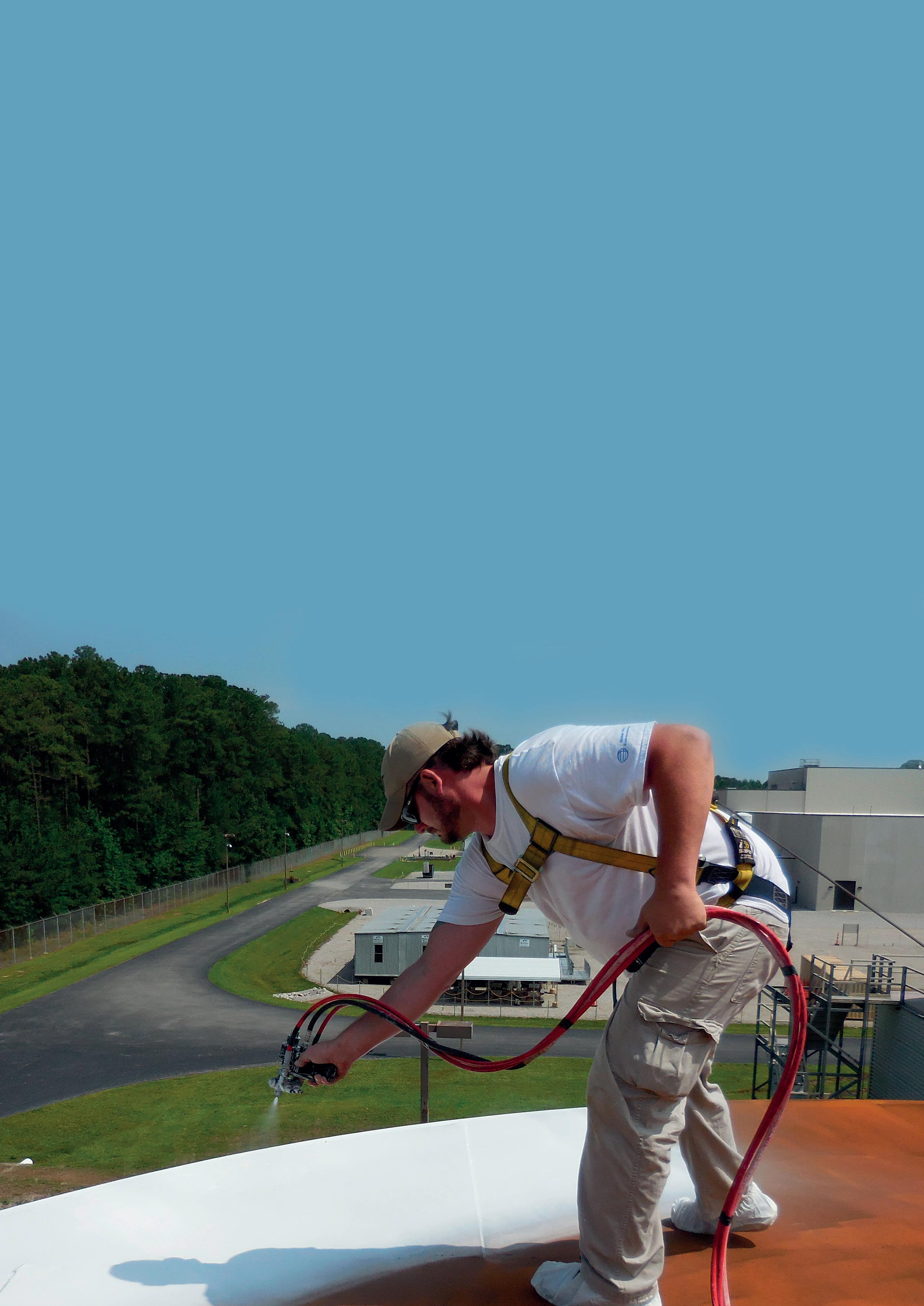
A health and safety hazard that still needs to be addressed
Despite the huge strides that companies in the downstream sector have made in protecting the workforce and the environment, there is a glaring aspect that has not been addressed.
In often-futile efforts to protect steel assets, chemicals that are toxic, flammable and bad for the environment are regularly used: paint and coatings. The unpleasant smell associated with paint is toxic chemicals. They are organic and intended to be volatile, so they evaporate into the environment to enable paint to cure.
Construction and maintenance painters have one of the highest injury rates among any profession. These professionals face multiple health and safety risks, but the most prevalent is exposure to toxic fumes.
Exposure to toxic fumes from high levels of volatile organic compounds (VOCs) can lead to neurological problems, known as ‘painter’s dementia’. Cancer and other health issues are also common. There is a direct correlation between VOC exposure and cognitive ability. A drop in IQ of 10 points or more is common.
Painters are regularly required to use coatings that are both toxic and flammable. Often, they enter confined spaces with these chemicals. They are provided with PPE to wear, but given the choice, eliminating the risk of exposure in the first place would always be the preferred option.
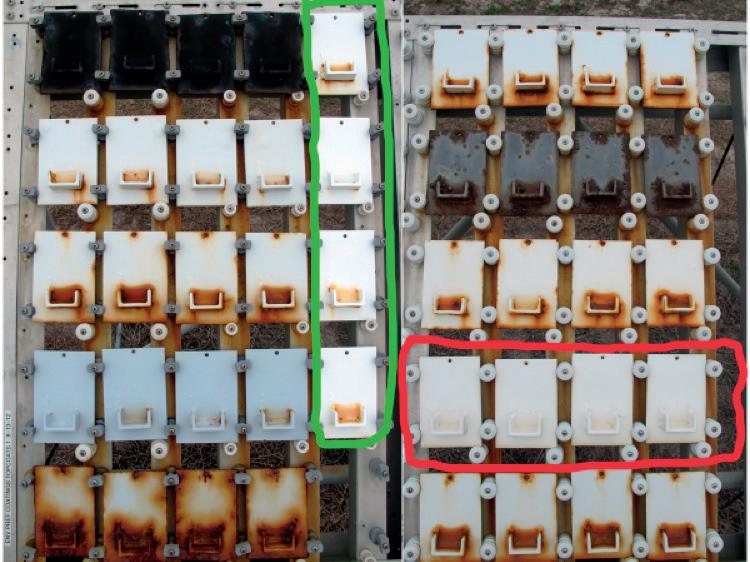
Figure 1. 10 environmentally-friendly coatings after 18 months on the beach, alongside the standard NASA uses to compare all test subjects. The standard, which scores 9.2, is in green. The coating in red is EonCoat.
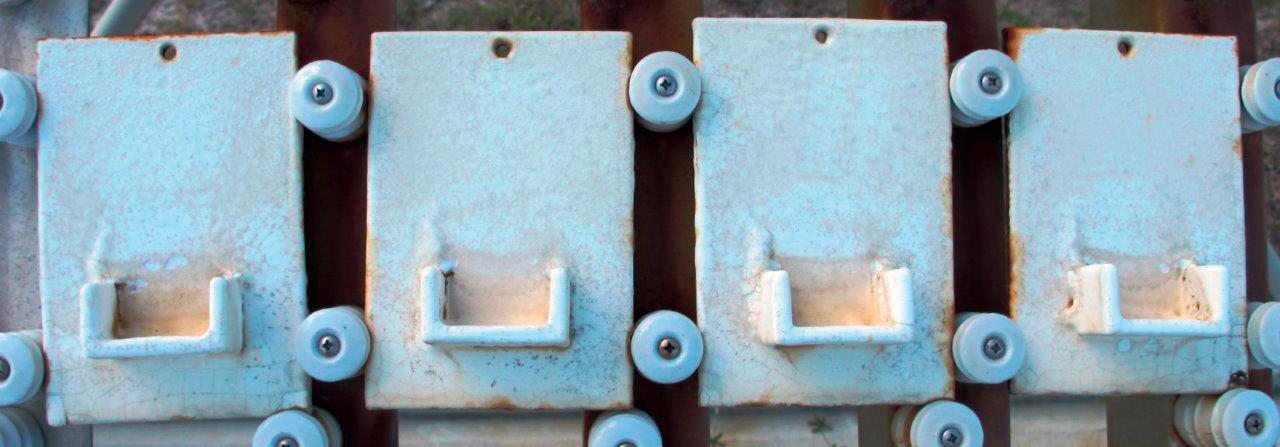
Figure 2. EonCoat four years later, having maintained a score of 10.
A better way
In 2013, NASA wanted to find a coating for its launch pads that was safer for people and less toxic to the environment. As such, the agency conducted a study called ‘Validation of Environmentally Preferable Coatings for Launch Facilities’.
The specific dangers that NASA wanted to minimise were those fundamentally inherent in solvent-borne coatings, and present to a lesser degree in today’s waterborne coatings, including:
VOCs
VOCs damage cognitive ability. They cause cancer, central nervous system damage, headaches, nausea and dizziness, which may be why more falls are recorded by painters than by any other professionals. Additionally, they affect global warming by absorbing ground radiation and by creating greenhouse gas.
Hazardous air pollutants (HAPs)
HAPs are pollutants that cause cancer or other serious health effects, such as birth defects. Additionally, they have adverse environmental and ecological effects.
Isocyanates
Isocyanates, classified as potential carcinogens, are used in polyurethane paints. They irritate the eyes, nose, throat and skin, and can cause breathing difficulties.
Heavy metals
Zinc is toxic at high exposure levels. It can cause metal fume fever. The US Environmental Protection Agency (EPA) lists zinc as a priority pollutant. Waste inorganic zinc (IOZ) paint (and anything that it comes into contact with) is considered hazardous waste. Zinc impacts the environment by entering the water supply at levels which are toxic to fish and potentially to humans.
Low VOC coating performance
Many reading this will believe that while low VOC paints may be good for health, safety and the environment, they will not protect assets. NASA’s test data does not support this conclusion.
NASA identified and tested at least 10 paints and coatings without isocyanates and with low toxins, HAPs and VOCs, and even a few without zinc. Testing was completed using NASA’s Beachside test (Figure 1).
NASA has been conducting coating tests at Kennedy Space Center for many years. All manufacturers test there because it is the most corrosive location in the US, and the Beachside test is generally accepted as one of the world’s toughest real-world tests. No coating passes this punishing 18-month test next to the high tide mark on the beach. It is usually just a question of how well a coating performs on a score of 1 – 10.
In all the years of testing at NASA, the highest score ever recorded was 9.2. However, in 2014, one coating did not rust at all, earning the first ever score of 10. NASA continued to expose those same panels for more than four years, but they continued to score 10 (Figure 2).