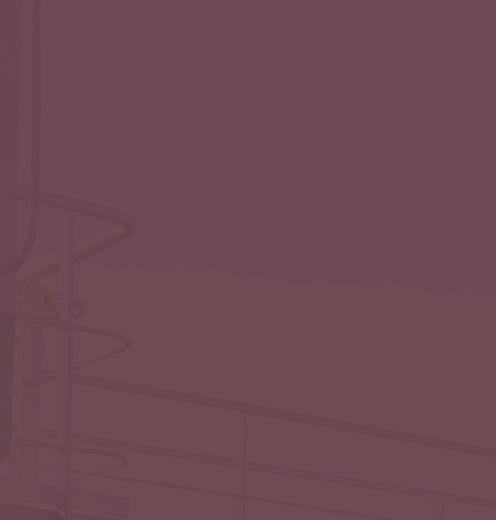
8 minute read
Estimating welding productivity
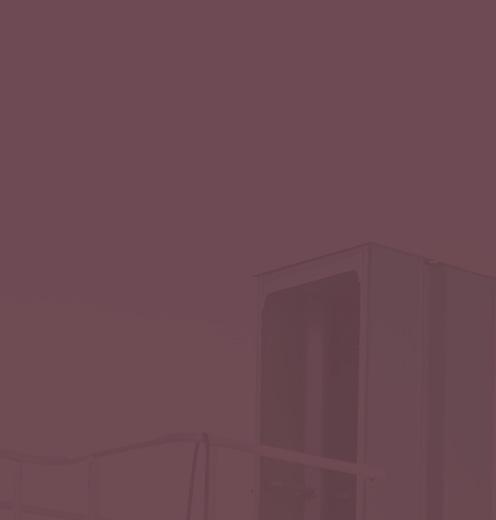
Soroush Karimzadeh, MBA, P.Eng., PMP, Chief Executive Officer and Matt Yarmuch, MSc, P.Eng., IWE, Canada, outline how to find optimal technology to enhance welding automation, as developed by Novarc Technologies.
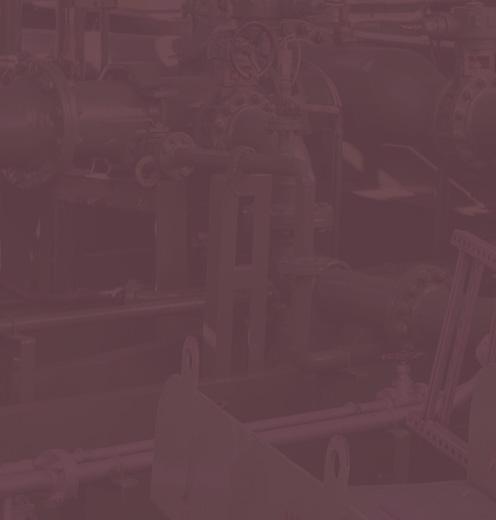
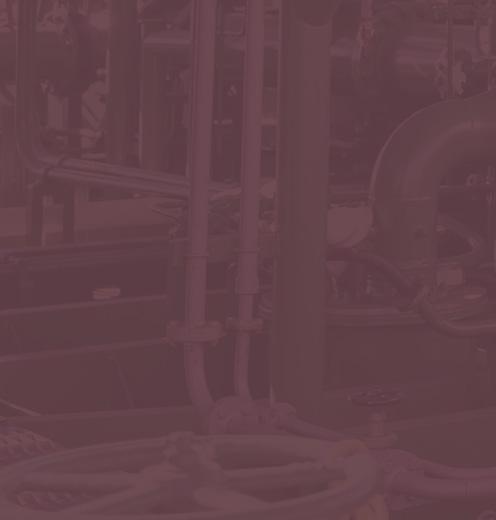
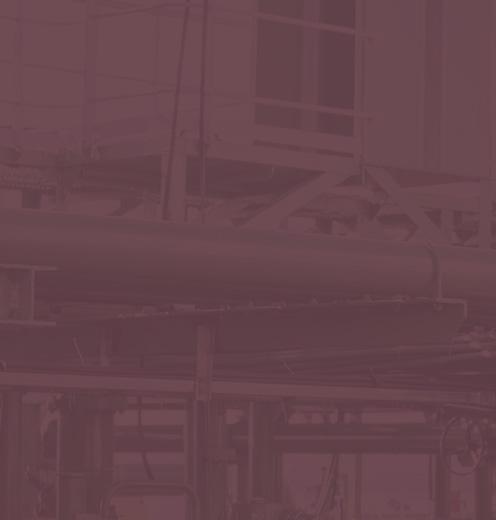
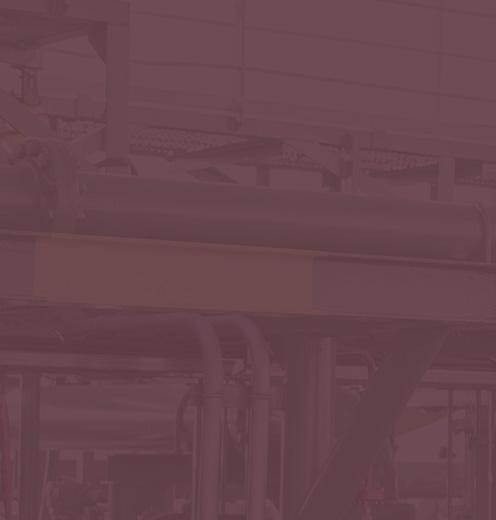
It’s a CFO’s dream: the promise of technology in industry to improve productivity, bring quality up, and costs down. But promises turn into problems when reality gets in the way. There is frustration in finding out that your results in the field, or on the shop floor, don’t square with your expectations. Welding is no exception. Significant differences in the production environment between shop and field welding conditions, or comparing roll welding to welding in position, will often result in difficult comparisons. To fully understand all the facets of welding costs: reliable, accurate and repeatable data collection must be achieved. Novarc Technologies in North Vancouver, British
Columbia, creators of the world’s first collaborative
Spool Welding Robot (SWR), wanted ‘real world’ proof to quantify the productivity and quality improvements that were attainable with its new development in advanced welding processes and automation technologies. Novarc designs and builds robots for industrial applications (pipe welding, pressure vessel manufacturing and other 1G welding applications) using advanced mechanical control and vision based systems. Given the fluidity of the shop floor working environment, the Novarc team has created an innovative solution using a floating long reach manipulator, with a three-axis cobotic arm at the end. Novarc’s breakthrough welding cobot, the SWR, increases the dexterity and flexibility of the human operator, improving productivity on the shop floor and reducing costs for the pipe shop. Contrary to some public concern that automation technologies are taking jobs from humans, Novarc’s SWR is actually assisting less-skilled workers to work alongside the robot, allowing highly-skilled welders to extend their careers. This is helping the welding industry to solve a huge problem: the severe global shortage of highly skilled welders impacting numerous industries such as process piping construction for oil and gas, energy utilities, water and wastewater and shipbuilding, to name a few. Pipe shops serving these global industries require highly skilled welders, and according to the American Welding Society, this is a looming labour crisis that will escalate to a shortage of about 400 000 welders in the next three years.
Maximising productivity Given this industry challenge, as pipe welding is an integral process to a myriad of construction projects, Novarc invested in research to determine how to improve and extend the capabilities of its SWR. Implementation of the SWR had already shown a 3x - 5x increase in pipe welding productivity, potentially recouping costs in six to 18 months. But Novarc wanted to do further research to develop ways to expand the capabilities of the SWR for pipe fabrication shops.
The result was SWR+HyperFill®, a highly efficient, fully integrated dual torch system that utilises Lincoln Electric’s patented twin-wire GMAW solution, HyperFill, that maximises productivity, and profitability.
Prior to the product launch this spring, Novarc did extensive research and conducted a productivity study to review the SWR+HyperFill capabilities.
There are various methodologies for estimating welding productivity, costs, quality and efficiencies. Many companies have sophisticated programmes based on specific applications and equipment, while others

Figure 1. Novarc’s SWR is used in a number of industries requiring process piping construction.
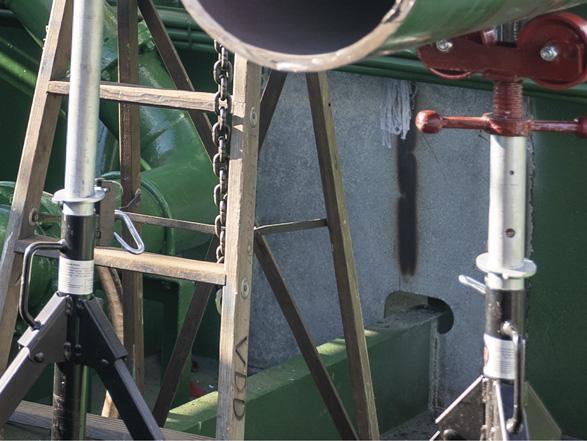
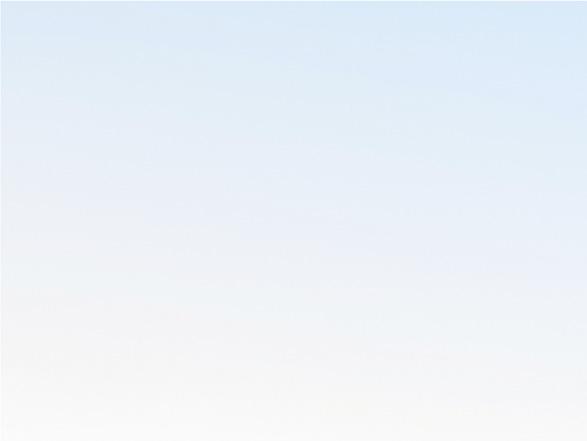
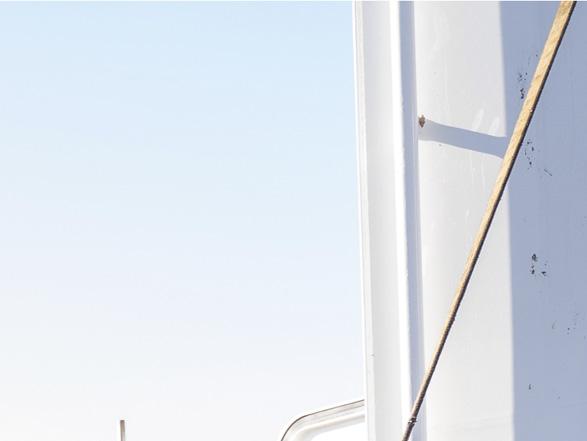
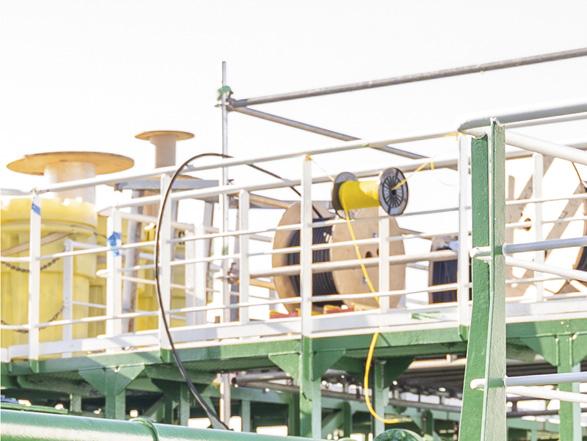
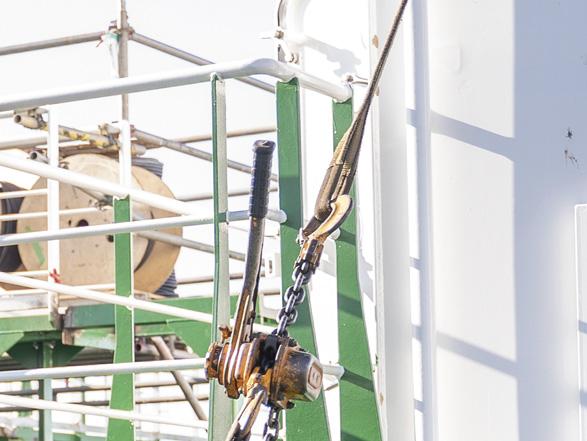
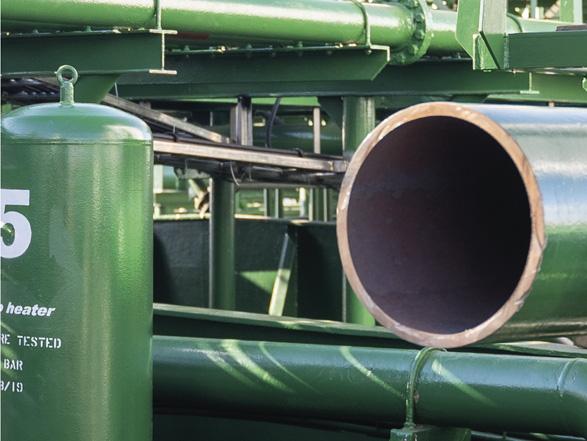
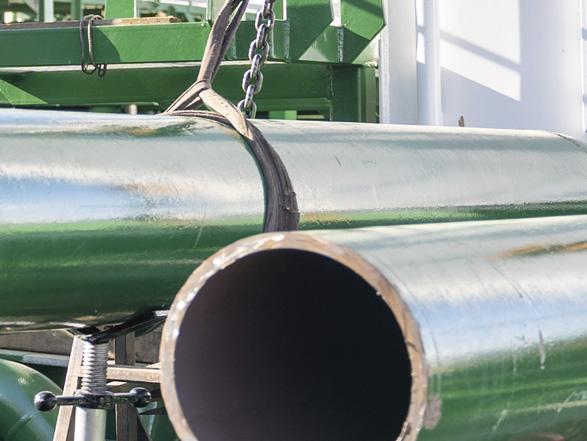
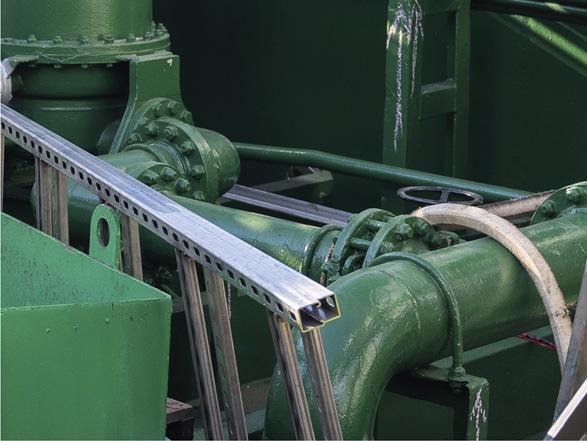
will complete only rough estimates. But an accurate assessment demands that a full range of deposition rates, efficiencies and duty cycles be considered.
The evaluation compared Novarc’s mechanised SWR, integrated with GMAW-MWSC (STT) and GMAW-P (HyperFill) twin-wire technology, against typical historical processes (baseline processes) such as manual (SMAW), semi-automatic (GMAW) and mechanised (SAW) processes. Productivity studies were done in an actual shop production environment following typical practices and welding procedure specifications.
A full productivity study will access multiple factors and metrics. To simplify the relative comparison of welding and automation technologies, three major factors were considered: ) Duty cycle – the ratio (percentage) between arc time and the total time spent by the welder or welding operator completing a joint.
) Deposition rate – a measure of the rate of weld metal deposition (this (lb/hr or kg/hr) for the welding processes and/ or automation system.
) Deposition efficiency – the ratio (percentage) of weight of deposited weld metal as compared to the weight of filler metal consumable used.
Results The results of the comparison illustrated that substantial productivity improvements can be realised on the shop floor with Novarc’s SWR+HyperFill platform. Improvements in deposition rate, deposition efficiency, and duty cycle, compared to the baseline processes, were consistently achieved, demonstrating that the Novarc SWR+HyperFill is capable of reduced welding times, achieving higher production rates (lb/hr) and excellent weld quality when compared against historical pipe shop practices.
The productivity data for the GMAW-P (HyperFill) fill/cap passes is summarised in Table 1. For comparison, manual SMAW E7018 and mechanised Submerged Arc Welding (SAW) results are included.
A summary of time to complete the 24NPS Schedule 40 pipe coupons is provided in Table 2. The time to complete the weld (including arc and non-arc time) is shown; no consideration of time for hoisting, fitting, equipment preparation, etc. was given. The results demonstrate that welding production time was reduced using the mechanised SWR as compared to manual, semi-automatic and other mechanised solutions.
The SWR+HyperFill uses the Lincoln STT GMAW-MWSC process on the root, and twin wire GMAW-P (HyperFill) on fill and cap passes. It can be used on carbon steel pressure process pipes or vessels with 0.5 - 2.5 in. thickness and as low as 6 NPS in. in diameter. The system also has the flexibility of using root to cap GMAW or seamlessly switching to FCAW or MCAW for the fill and cap passes.
Besides achieving higher deposition rates and deposition efficiencies, SWR+HyperFill can increase factored diameter inches (FDI) to 350 - 500 per shift on carbon steel pipes, meeting ASME Section IX and B31.3 WPS qualification requirements and achieving high toughness test results down to -50˚F (-45˚C).
With the SWR+HyperFill Solution, there are a number of benefits beyond the original features of the SWR (namely, small footprint, integration with up to five positioners, assisted seam tracking and height control, welding vision system NovData™). These additional benefits include: ) Deposition rates of 15 lbs/hour or higher on fill and cap passes.
) The root, fill and caps can be welded for up to 2.5 in. thick materials in the same welding cell using the SWR.
) Flexibility to use GMAW or MCAW process on the root.

Figure 2. SWR in action.
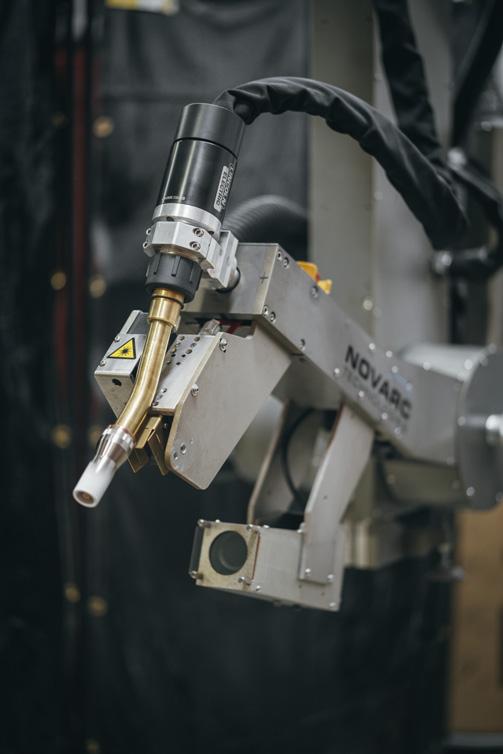
Figure 3. Dual Torch.
Table 1. Productivity data for the GMAW-P (Hyperfill) fill/cap passes
Process & consumable Deposition rate lb/hr Deposition efficiency (%) Duty cycle (%) ) Flexibility to use FCAW or MCAW process on the fill and caps instead of HyperFill (with the right tip and drive rolls).
) Flexibility to weld stainless steel with the second torch (with the right tip and drive rolls).
) Elimination of the hot pass common with manual or semi-automatic welding.
If high-productivity technologies such as the SWR+HyperFill’s solution are implemented with proper adaptation of the upstream and downstream activities, then the ‘pipe dream’ of full performance utilisation is achieved along with the targeted return on investment. Essentially, this means that pipe fabrication shops will be able to increase their heavy fabrication productivity by increasing weld deposition rates while delivering excellent weld quality; lower their cost by reducing weld and material handling costs compared to the sub-arc process; and streamline and simplify production. All of this is good news for pipe fabricators serving the oil and gas industry, pressed to increase margins on existing projects, and bid with increased competitiveness on new projects.
SMAW – E7018 (manual hot pass) Min. Max. Min. Max. Min. Max.
1.5 5.1 18 54 40 54
SMAW – E7018 (manual fill & Cap) SAW – DC (5/32 in. single electrode, mechanised)
SWR GMAW-P Hyperfill (0.035 in. twin wire) 5.2 6.5 55 57 71 77
12.6 12.9 89 95 97 100
15.4 15.5 99 100 98 100
Table 2. Summary of time to complete the 24 NPS Schedule 40 pipe coupons
NPS schedule Process combination Time to complete weld (min.) Percent difference
24 S40 SMAW & SAW-DC (manual & mechanised) 95.4 --
GMAW-MWSC & SAW-AC (single 5/32 in,) (Semiautomatic & mechanised) 52.4 45%
GMAW-MWSC & GMAW-P Hyperfill (twin 0.035 in.) (Spool Welding Robot) 42.1 56%


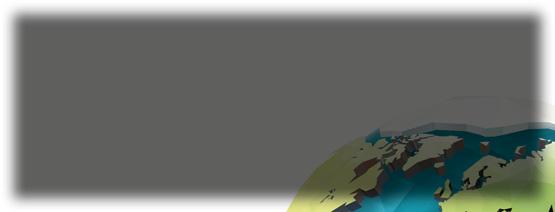
The print issue is distributed to a global audience of industry professionals (verifi ed by ABC). Register to receive a print copy here: worldpipelines.com.magazine/worldpipelines/register
Prefer to read the issue online? The digital fl ipbook version is available here: worldpipelines.com/ magazine/world-pipelines Download the World Pipelines app for Android (Google Play) or iOS (App Store) to access World Pipelines from your mobile device.
Wherever you are, World Pipelines is with you.
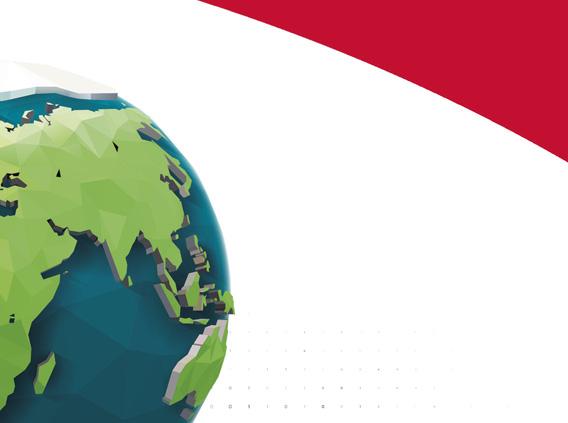

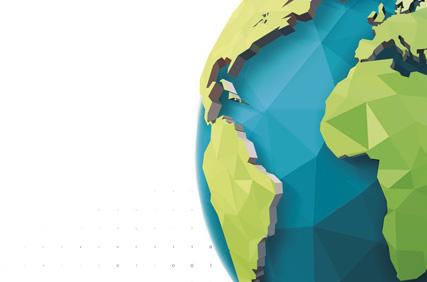
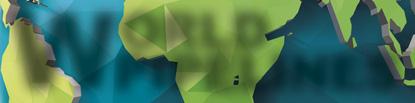