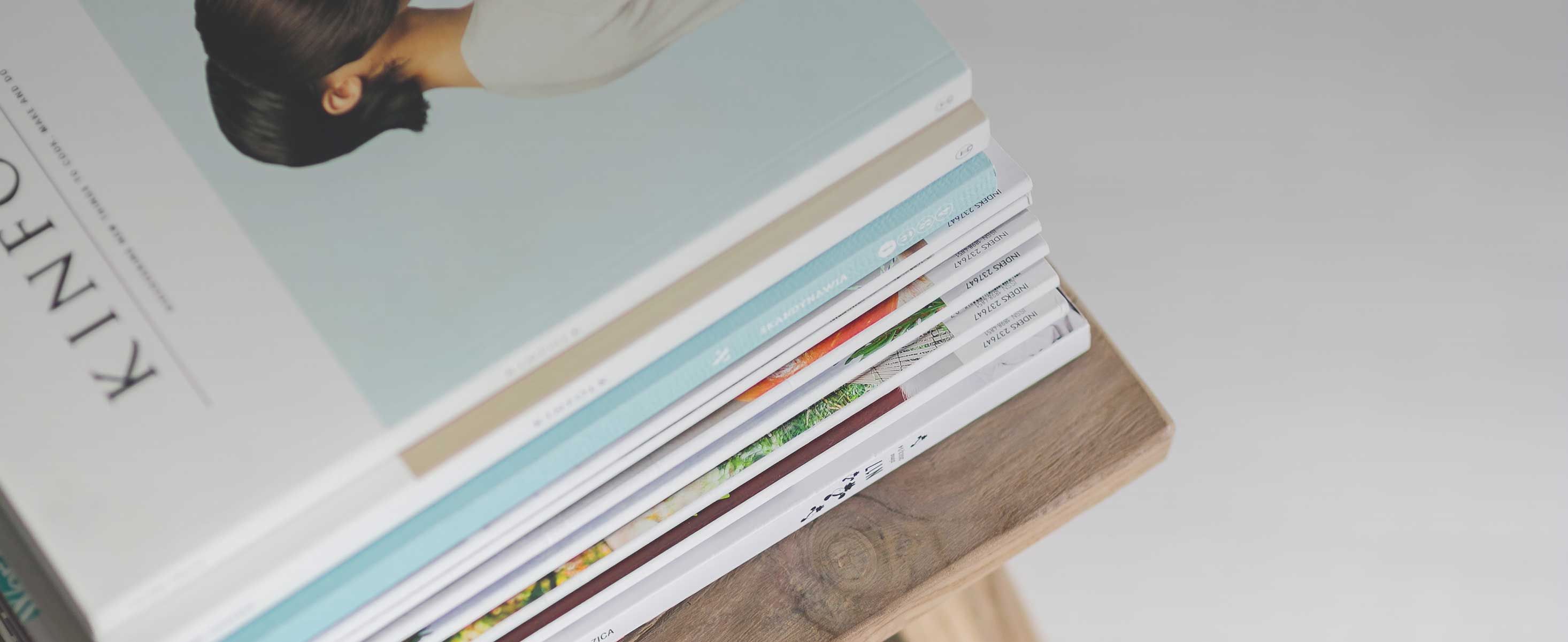
5 minute read
BESPOKE BUSINESS SAVES MONEY ON BILLS WITH WOOD WASTE HEATER
Bespoke furniture manufacturer, PR Bespoke Interiors has purchased a wood waste heater from Wood Waste Technology to save money on its heating and waste disposal costs.
PR Bespoke Interiors Ltd is developing a reputation for offering luxury high-end furniture to its clients, including those involved in commercial and manufacturing projects as well as private customers and interior designers.
Advertisement
When the business launched in 2019, the team moved into a workshop in Bredbury, near Stockport that had no heating. Having previously worked for a company that used a wood waste heater, directors Ryan and Patryck knew that investing in a wood waste heater was the perfect solution for their new business due to the amount of wood waste generated, so started to research some options.
Office Manager, Holly Wallis explains: “When we moved into the building in spring, we knew one of our first investments needed to be a wood waste heater, so we could burn all our waste wood to create free heating for the factory in winter, and also save money on waste disposal. We were recommended to speak to Wood Waste Technology due to the quality and durability of its heaters by a trusted colleague, and we’re so pleased we did!”
After speaking with Kurt Cockroft at Wood Waste Technology and arranging a quote and site survey, PR Bespoke Interiors ordered a WT15 which was installed by Wood Waste Technology’s experienced engineers, who managed to vent the heat generated to key areas of the workshop.
Holly explains: “We’re delighted with our new wood waste heater. We’d hate to have to heat the building any other way, as the open plan nature of the workshop and high ceilings would be awful for retaining heat and our heating bills would be a fortune! Wood Waste Technology’s installation team was exceptionally helpful, in that the engineers were able to direct the majority of the heat to the areas we need to keep warm the most. The advice and help from the team at Wood Waste Technology has been excellent, and we’ve been really impressed with how the heater operates and how easy it is to use.”
MD of Wood Waste Technology, Kurt Cockroft says: “We’ve been delighted to help the team at PR Bespoke Interiors and are so pleased they’re delighted with the results. We’re very grateful to the people who help to spread the word about Wood Waste Technology by recommending us to others – and are proud to be manufacturing such high quality heaters here in the UK.”
Wood Waste Technology offers a full range of wood waste heaters, from small hand fired units to larger fully automatic systems, and offers site survey and design, as well as manufacture, installation and on-going maintenance. The company also services all types of wood waste heaters and supplies genuine spares up to 60% cheaper than other suppliers.
In addition, Wood Waste Technology is the UK’s official distributor for Gross Apparatebau GmbH, a German manufacturer of dependable, precision engineered shredders and briquetters. The company is also a distributor for Putzmaus boiler tube cleaning systems - a powerful but gentle routine maintenance solution that is quick and easy to use, and helps to increase boiler efficiency and lower operating costs.
Case Study
SJG INTERNATIONAL IMPROVES EFFICIENCY & ACCURACY WITH AAG
AAG is a leading global manufacturer of CNC routers and waterjet cutting solutions, focused on helping companies of all sizes improve their automation.
With over 30 years of experience, they have built and installed thousands of CNC and waterjet cutting systems across a wide array of industries. From metals, plastics and foams and everything in between, they are a world leader in producing cutting system that will help your business grow and expand to exciting new levels. One of the companies that they have supplied is SJG International Ltd, an award winning, marketleading manufacturer of rubber extrusion, gaskets and foam conversions. The company supplies gaskets, washers and sheeting material to a wide range of customers including military and defence to automotive and rail, sports and leisure and many more who need sealing solutions for various applications. They work with their customers to produce rubber and foam solutions that seal, insulate, protect and cushion in often difficult and challenging environments and can assist at every stage of the process, from designing a first prototype to choosing the right materials.
Employing 50 staff, everything that is produced is designed, tooled and manufactured at their custom-built unit in Alcester. SJG International Ltd have full CAD design capabilities in-house and can work from a drawing supplied by the customer or create one to their specifications and requirements. For this to happen they required a machine supplier that had the same exacting standards that they themselves have achieved. They chose AAG, and use AXYZ Routers and WARDJET Waterjets as part of its manufacturing process for rubber extrusion, gaskets and foam conversions. The use of these advanced technologies from AAG allows SJG International Ltd to produce high-quality components with improved efficiency, speed and accuracy.
When asked why they chose AAG as their preferred supplier Rachel Russell (Purchasing Director) explained: “We have a close relationship with AAG and that has made it easier to work with them to bring new machinery and ideas into the business. As the machines are versatile with cutting, routing and knife cutting it has allowed us to be more flexible and this has made it easier in attracting a wide variety of clients. Thanks to the continued innovation such as 5 Axis cutting, made possible using our WARDJET cutter from AAG, and our customer service, we have built a loyal customer base across the world”.
There are five models in the AXYZ Routers range; all with their own unique options and versatility to cross over infinite markets. The routers are controlled by AAG’s A2MC controller or the industry leading control interface MOVE that drives all machine tasks and is designed to optimise the operation of the CNC machines, perform tool changes, set up your work offsets, call up a new file or optimise the cutting speed. MOVE is designed to make machine operation easy and intuitive. Currently SJG International Ltd has four AXYZ routers in its portfolio of machines which has enabled SJG International Ltd to produce components with improved accuracy and consistency, reducing the risk of errors and improving the overall quality of its products and reducing lead times and costs.
Also, in the machine make up of SJG International Ltd is the J-Series WARDJET waterjet - a high-precision cutter that enables them to produce components with complex shapes and designs, with minimal waste and improved accuracy. The WARDJET series are offered in varying sizes to adapt to the customers’ floor space. The versatility at the manufacturing stage means that machines can be bespoke and built to customers’ precise requirements - be it the need for a greater Z-travel or custom fixturing in the table or tooling configurations - WARDJET can incorporate the customer’s needs.
The use of these advanced technologies helps SJG International Ltd to meet the growing demand for high-quality components that make industries safer and drive innovation. The combination of AXYZ Routers and WARDJET Waterjets allows the company to produce components that exceed industry standards and customer expectations whilst, at the same time, improving its efficiency and competitiveness in the market.