
5 minute read
MANY HANDS MAKE LIGHT WORK
By / Robin Brunet
Tony Stephens recalls an incident at a career center last February, shortly after he became a full-time training director for Local 24 Dayton Area JATC in Ohio.
He says, “A young man approached my predecessor Eugene Frazier—who made our apprenticeship program what it is today—and told him, ‘You gave a talk at my school when I was in grade 8, and it changed me.’ After one year of apprenticeship, this 17 year old was already working for a local company and on track to making $62,000 annually.”
Stephens, 55, who prior to becoming an instructor worked as an estimator and project manager for Budde Sheet Metal Works (and who underwent his apprenticeship back in 1988), pauses to consider the ambitious teenager’s trajectory. “Initially, I was reluctant to become training director because it’s not an easy job. It’s time consuming, and it doesn’t pay what it should. But, that young man is a great example of why it’s important for people like me to give back. It’s not only rewarding to see the younger generation get a firm career footing, we’re also contributing to our industry’s future success.”
Ohio is no different from any other state when it comes to labor pool challenges, but instead of reacting to them, Local 24 has taken a pro-active approach to recruiting and training new blood: by overseeing not one, but three separate apprenticeship programs for three different regions. While Stephens supervises the Dayton JATC, Cort Wayman presides over Cincinnati, and Steve Allen is the JATC coordinator in Columbus.
Apprentices in each of these districts receive classroom instruction for five years, with curriculum covering architectural sheet metal, commercial and residential HVAC, detailing, industrial welding, service and refrigeration, and testing, adjusting, and balancing.
Concurrently, Local 24 partners with ApprenticeOhio by registering its apprentices with the Department of Labor and sourcing contractors who are willing to take on newcomers. “That really is key,” says Allen, who apprenticed after he graduated high school in 1996 and became an instructor in 2008. “We can find young people and train them, but it’s the contractors who give them the foot in the door.”
Doug Mayse, president and managing partner of Rieck Services in Dayton, agrees. Mayse, who apprenticed in 1986 at 18 and who is also the most recent addition to Local 24’s JATC, says, “Fortunately, contractors and Local 24 have always had a close working relationship, partly because both sides understand what the final goal has to be. It also helps that the business agents have all worked in the trade, so they know the challenges we face.”
The demand for apprentices is growing in the face of the so-called ‘silver tsunami’, a large number of retirements in the trades, which could result in the loss of 30% of Local 24’s members in the Dayton district alone over the next few years.
Local 24’s training directors find themselves especially busy in the new year. In Columbus, where 199 apprentices receive training in two different centers, contractors are already in hiring mode. “All of our apprentices are busy—there’s lots of work here, and the growth mode will last for at least another four years, since local construction projects include data centers that are massive in size and take many years to build,” Allen says. “In fact, we’re in the process of purchasing a new training facility to double our capacity.”
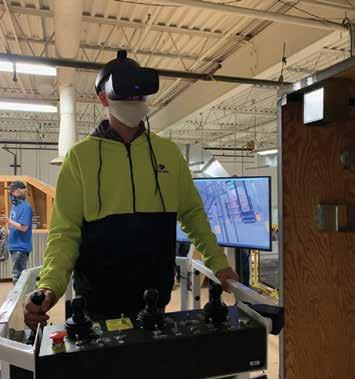
Allen adds that contractors in his region “are willing to take anyone who demonstrates a willingness to learn the trade, including large firms such as TKS Industrial Company, which has a fabrication shop in Columbus.”
Stephens says the market in Dayton is slightly different: “It’s a bit of a catch-22 whereby many contractors have carved out their niche and want to maintain the status quo. However, many want to move on and need more people, but the Local doesn’t have enough workers on tap.”
Still, Mayse thinks the mindset that for an entire generation dissuaded young workers from entering the trades is changing. “From the recruitment end, we’re making major strides with high school principals and guidance councilors, possibly because they appreciate the high cost of college and the fact that a large percentage of enrollees never finish college,” he says. Stephens adds that the average age of his apprentices has gone up because these students have first enrolled in institutes of higher education only to realize they didn’t guarantee better careers.
Another mindset change with the potential to boost recruitment numbers is non-traditional demographics, like women and minorities. Stephens supports the union’s initiatives toward diversity and inclusion and actively approaches females and minorities at job fairs. “I give them pamphlets and other information and tell them to consider a career in our trade,” he says.
As 2022 unfolds and demand growth seems to be largely unaffected by the omicron variant, Local 24 continues to focus its energies on expanding the employment pool. “It’s gratifying that union apprentices are more valued and needed than ever before,” Stephens says. “Thanks to close ties between labor and management, our efforts are paying off.” ▪
Robin Brunet’s journalism has been published in over 150 magazines, newspapers, websites, and other media across Canada and the United States since 1982.