
4 minute read
ARCHITECTURAL LAB MEETS MARKET DEMAND
Advancing the industry by providing hands on architectural training
By / Robin Brunet
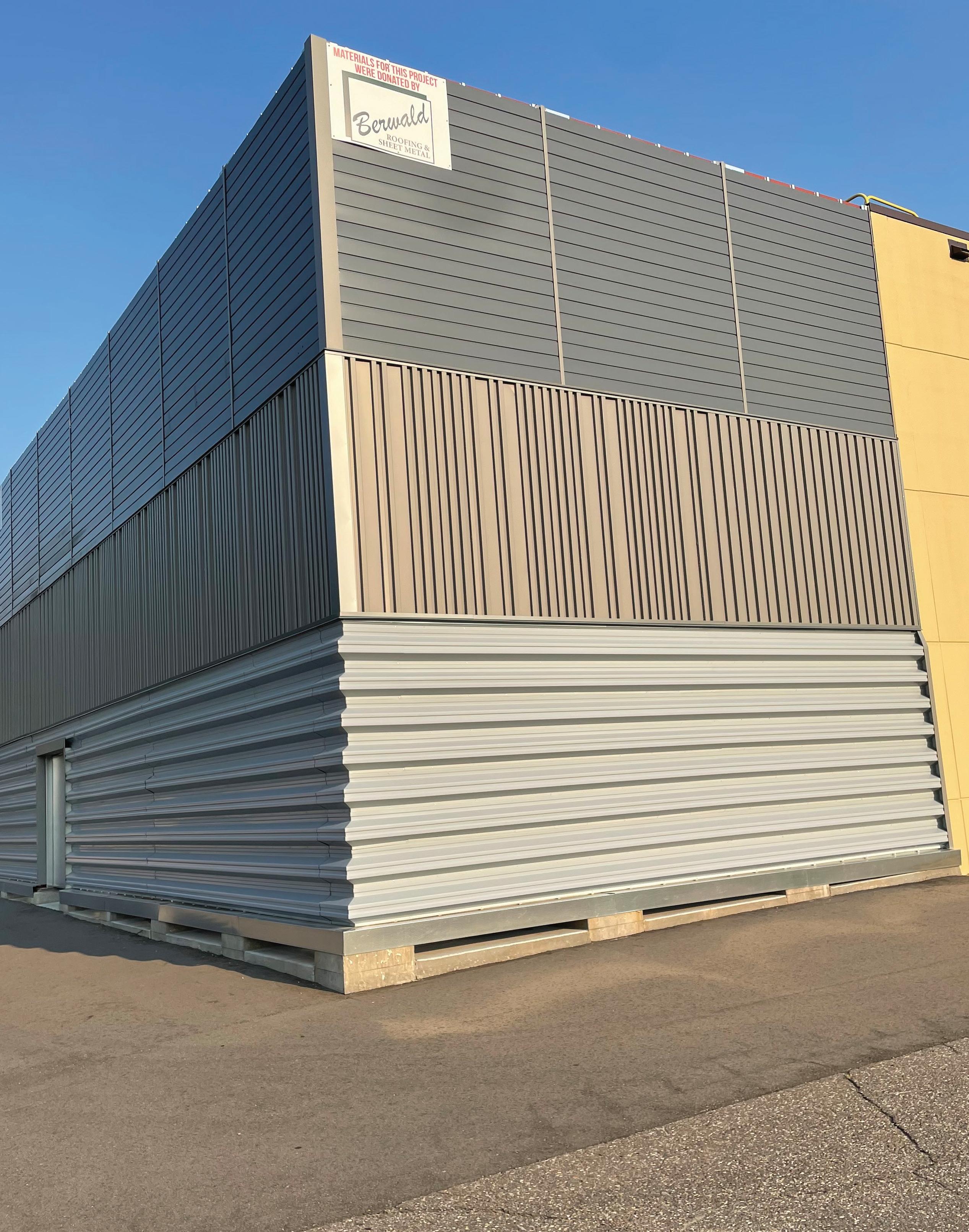
A jointly-funded commercial service and architectural lab in White Bear Lake, Minnesota, serves several key purposes, all under one roof. “We needed this facility in order to build on the work we do in the architectural realm,” says John Quarnstrom, CEO of SMARCA Minnesota.
For Matthew Fairbanks, business manager/president at Local 10, the lab will help his organization get into the commercial service market. “We were holding classes to achieve that goal but didn’t have commercial equipment that newcomers could work on,” he says. “The new lab rectifies that shortcoming.”
While classroom training for apprentices is crucial, the lab provides training on the true skills that can only be gained doing the work. The trouble is, on site work must be done more quickly and efficiently than ever, leaving newcomers with little time to cut their teeth. “The new facility allows them to acquire practical skills prior to them venturing into the trenches,” says Scott Grossklaus, superintendent at SMARCA MN member, Berwald Roofing & Sheet Metal.
Equally important, the lab demonstrates what labor and management can achieve in a relatively short time when working together. “The building would not have gone forward without the support of both sides,” Quarnstrom says. “Thankfully, SMARCA and Local 10’s relationship is based
on a mutual determination to solve problems and advance our industry.”
The 3,700-square-foot lab is located behind the Metro JATC’s main school and ties in with the new welding lab. It contains an air handling unit (in addition to a roof-mounted system that services the building), fans, variable speed drives, pumps, and motorized variable air volume boxes, all of which provide the closest possible approximation to what apprentices can expect in the field.
Two sides of the building’s exterior are covered by an iron structure with overhangs and door entrances. “Apprentices can install a variety of exterior panel systems on this structure and fine-tune their coping, flashing, and other skills,” Fairbanks says.
Quarnstrom credits long discussions between SMARCA MN and Local 10 for the facility’s development. “Matt had a wonderful vision for the building, and from our perspective, it was crucial to move forward on this project, because 19% of our sheet metal hours in the Twin Cities region are in the architectural realm,” he says. “There is constant pressure from other trades to take the work we do in this field. The learning lab demonstrates that we’re committed to the highest industry standards.”
Fairbanks agrees. “Our members perform about 800,000 person-hours per year of architectural sheet metal work, so we needed to improve training in a unique and effective way,” he says.
Although it is one of the very few trades to custom-make complex systems out of raw material and then install them, the sheet metal industry is rarely called upon to service what it creates. “The pipe trades have claimed servicing, but really, it should be us doing the job,” Fairbanks says. The lab ensures the workforce is well-trained in service, helping to address this potential market share.
Grossklaus, who has been in the sheet metal industry for 25 years (his father was a 40-year veteran of the trade), also believes servicing would be of enormous benefit to sheet metal contractors’ clients. “By offering servicing and inspection, we would essentially become a one stop shop,” he says.
He also points out that the lab’s ability to approximate work site conditions is an important asset. “Today, more than ever, new talent needs to hit the ground running, and there’s nothing more attractive to me than to have students assess a real life situation and tell me, ‘I’ve done this before,’” he says.
With all parties eager to turn the lab from an idea into reality, the elements necessary for the project came together fairly quickly. “Once we resolved to go ahead with construction, we reached out to local companies for help, including MG McGrath and Berwald,” Fairbanks says.
Grossklaus adds, “We donated composite systems, flatlock metal systems, corrugated systems—about five systems in total that students could work on.” Construction began in March of 2020 and was completed in time for the commencement of that fall’s training season.
While the commercial service and architectural lab may go a long way in fulfilling numerous goals, Fairbanks points out that one of the keys to its success moving forward is contractor input. “Just as foremen gave us input on optimizing the content of our courses while the building was being developed, we need their continued participation,” he says. “That’s because our industry is constantly changing, and the so-called ‘people in the trenches’ can provide updates to our instructors on a variety of training issues.”
Grossklaus and his colleagues are ready to lend a hand when required. “Trends change and so do standards, so we consider this to be a work in progress,” he says. “I only wish I were less busy in the field. I would love to do speaking engagements.”
As of July, the lab was being used several times a week by Local 10’s pool of 500 indentured apprentices. ▪ Robin Brunet’s journalism has been published in over 150 magazines, newspapers, websites, and other media across Canada and the United States since 1982. He is also the best-selling author of two books: Red Robinson: The Last Deejay and Let’s Get Frank, as well as the upcoming The Last Broadcast.
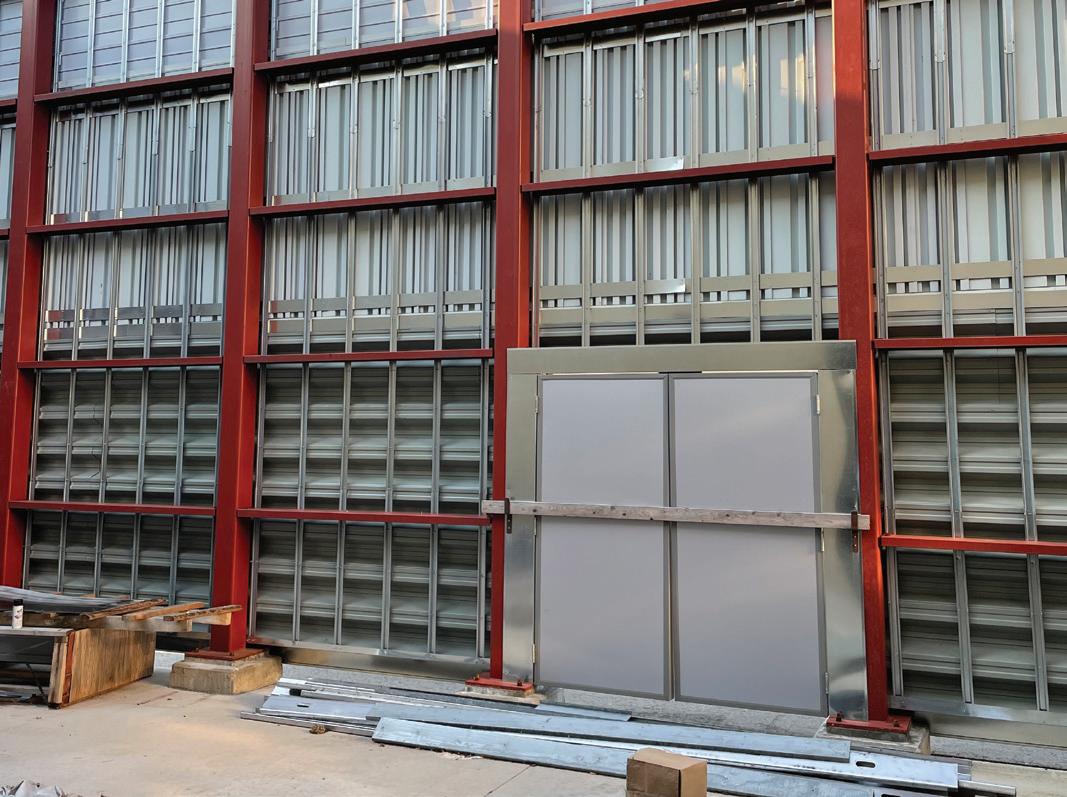
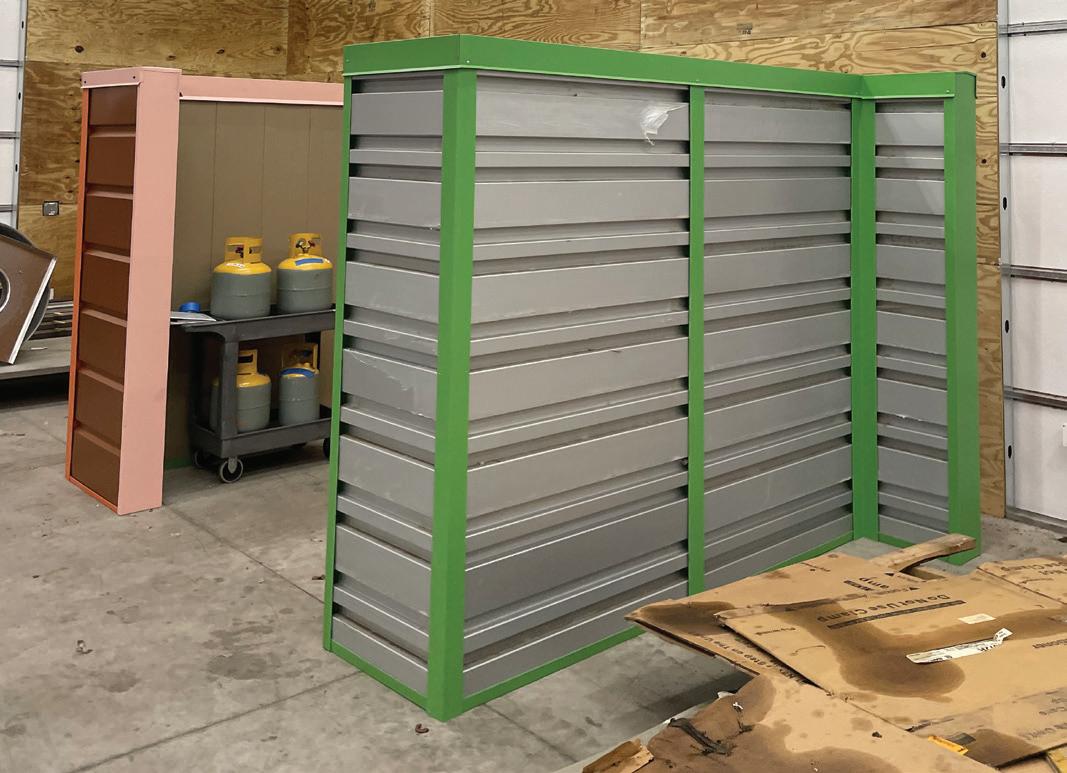