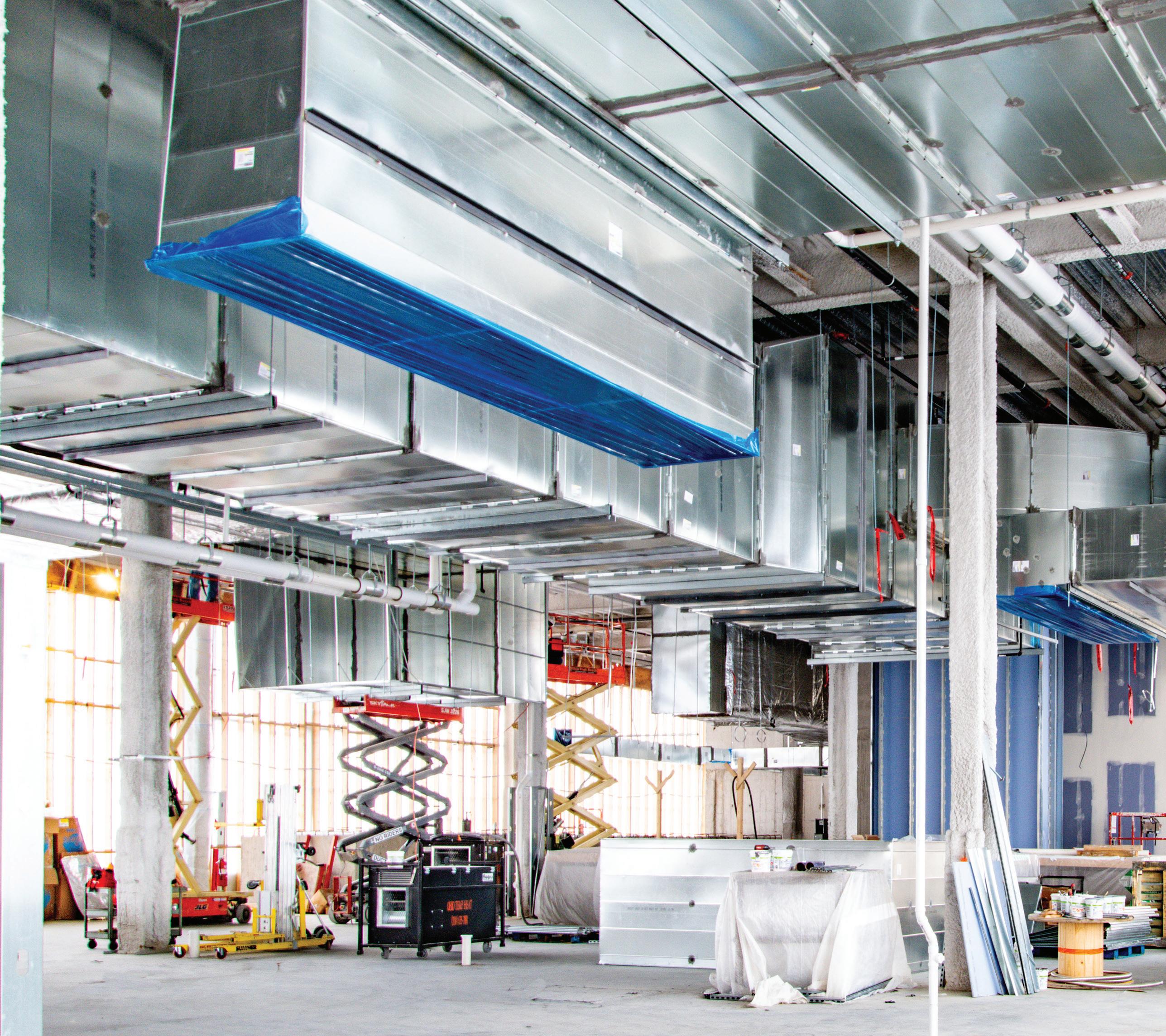
5 minute read
LARGE SCALE PARTNERS
SMACNA Cleveland’s T.H. Martin and SMART Local 33 were the perfect team on Cleveland Hospital, the city’s largest project in 20 years
By / Jessica Kirby • Photos courtesy of T.H. Martin
When it wraps up in April 2022, Cleveland Hospital will have 11 stories, 270 new beds, a 1,500-space employee parking garage, and expanded green space and community programs on its 52-acre campus. If that sounds like a lot, that is because it is. In fact, this project—financed by $946 million in hospital-revenue bonds and a $100 million fundraising campaign by the MetroHealth Foundation—will be the largest project Cleveland has seen in two decades.
SMACNA Cleveland contractor T.H. Martin and the highly skilled craftspersons at Local 33 Cleveland were the perfect team for taking on a project of this magnitude, where the logistics are challenging, the schedule demanding, and the design complex—all while dealing with a pandemic.
Tom Martin, president at T.H. Martin and Best Practices Market Expansion Task Force member, said the company began the job with 10 to 15 sheet metal workers on site, but throughout, as many as 60 were required on site, with 25 supporting in the shop.
“A project of this size, with a demanding schedule and a complex design, meant additional labor was needed during the rough-in phase,” Martin says. “Because we were extremely busy and had other projects ongoing, we worked with our partners at Local 33 to identify the right personnel and talent for completing this job.”
Local 33 Business Manager Tim Miller says the Local approached the project as a team effort on all fronts, including

securing an adequate workforce. “We had discussions with T.H. Martin about how Local 33 could assist in any way to make the project successful for both organizations,” he says. “Items discussed were workforce needs, safety, training, and PPE when the pandemic began.”
Finding the “right” people for the job meant two things. First, the workforce had to be highly trained in welding, BIM, CAD, and on fabrication and installation of medium pressure ductwork and reinforcements. Second, the project had to meet inclusivity requirements.
“The project required an immense amount of welding, reinforcements, and duct testing, and we were dealing with some huge duct we don’t usually work with,” Martin says. “The complex design involved damper and plenum walls in all the equipment rooms, and huge flue stacks in the central utility plant and above the roof level, which meant it required an enormous amount of collaboration and planning. We had to be sure the men and women on site were comfortable with how this was coming together and were able to complete the work to both meet the design and SMACNA standards. ”
“Any time you have a project of this size and technical nature, including the need to use the Trimble system, BIM programming, and complex logistics, you need a quality contractor, such as T.H. Martin, and you need the well-trained work force Local 33 provides,” Miller said. “It was essential that the team of BIM and CAD professionals was strong and understood job and the 3D modeling dynamic of the project.”
Where they could, the team prefabbed the duct and sent it out to simplify the process for field workers, but that wasn’t always possible, depending on the schedule or the floor where the duct was needed.
“It was a challenge for the men and women in our shop and in the field to manage the logistics,” Martin says. “Success in that regard came down to having good communication with our Local workforce and their ability to manage the scope and scale of a project like this.”
The changes and requirements associated with the pandemic were a challenge, but solid communication between T.H. Martin and Local 33 served to mitigate extra costs and delays.
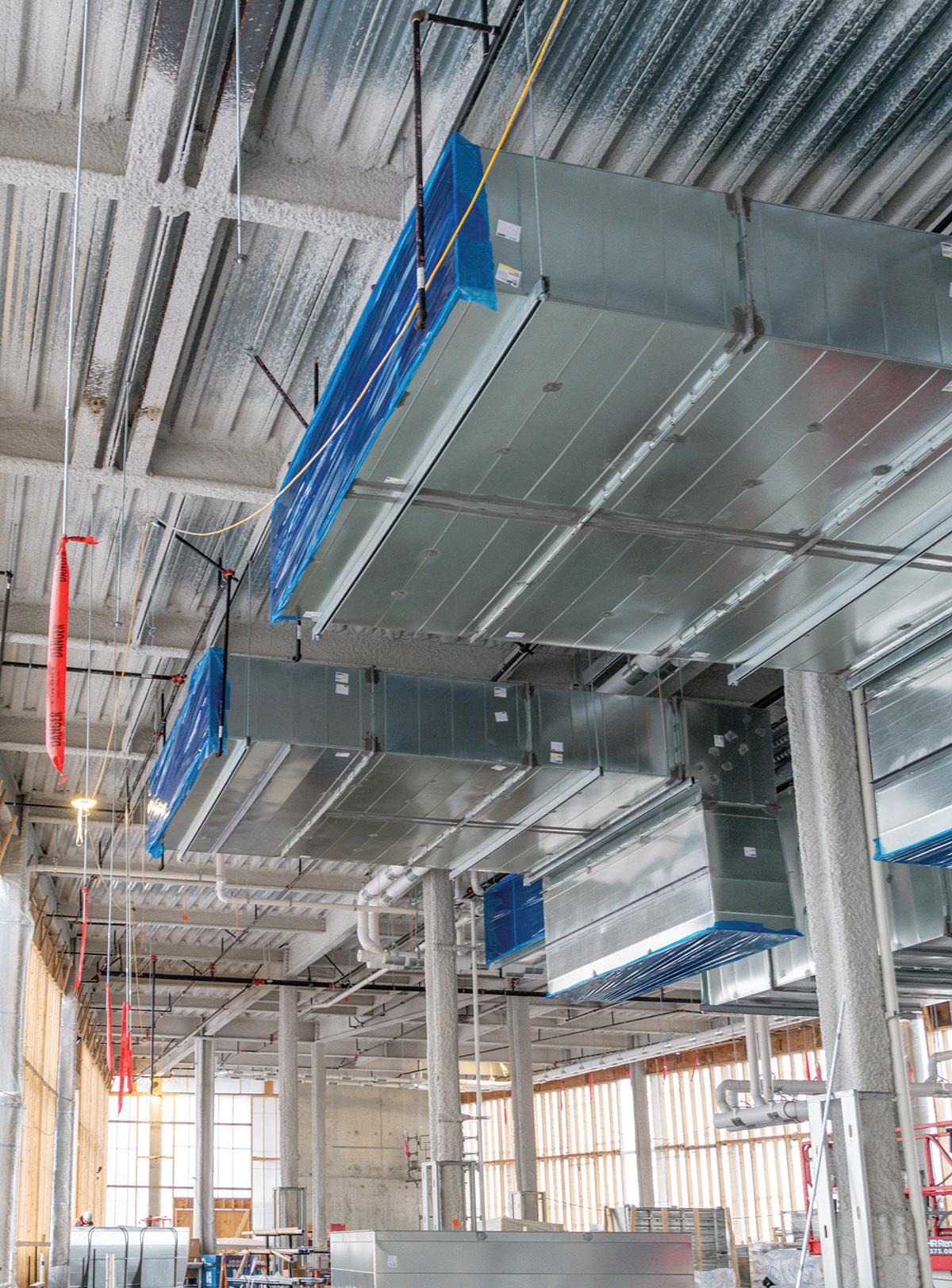
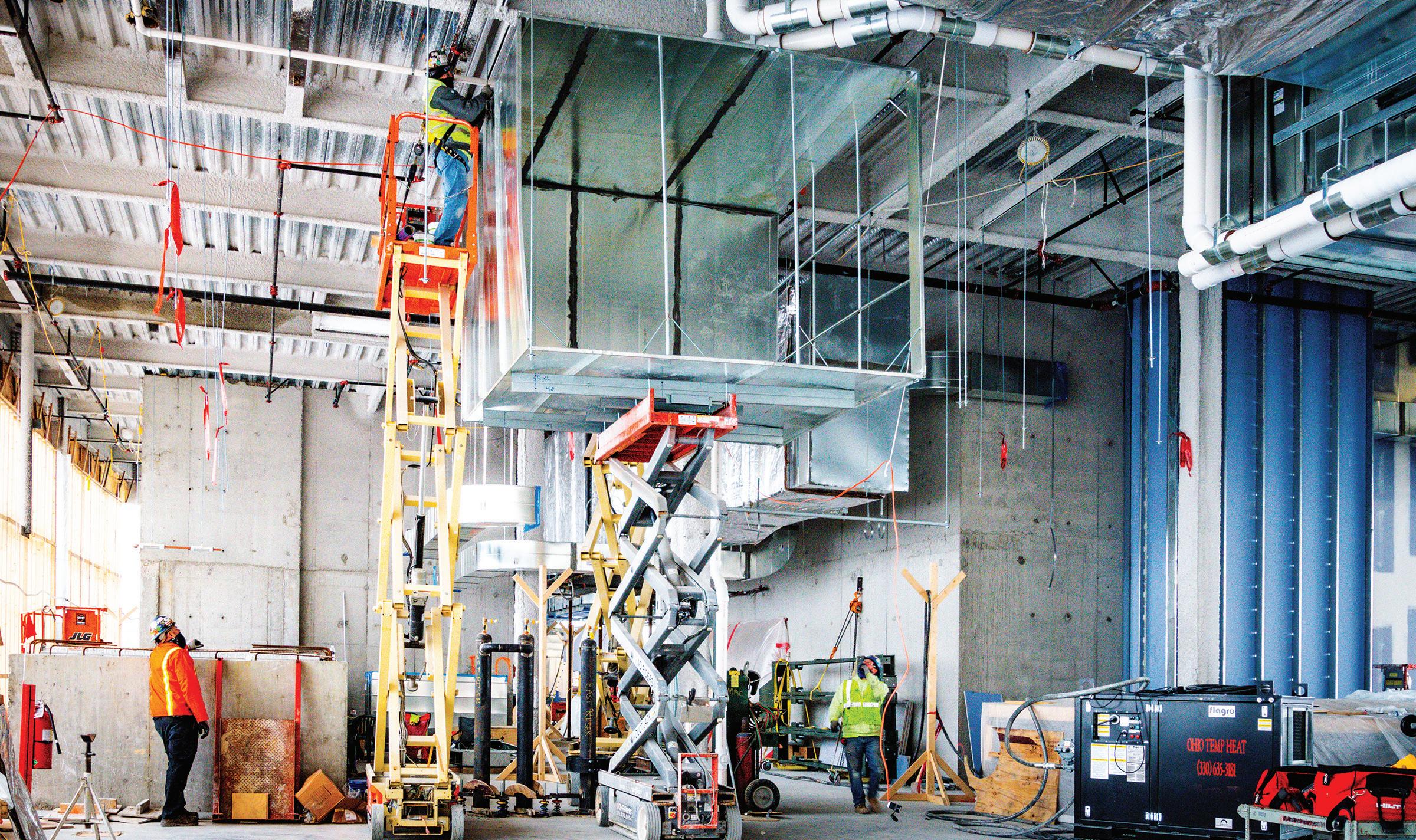
Local 33’s labor management cooperation committee worked with T.H. Martin and other contractors to assist in acquiring and distributing the PPE required to maintain a safe work environment and meet the CDC guidelines throughout the project.
“When job sites mandate certain criteria—like masks, gloves, PPE, temperature checks, wash stations, and staggered lunches and breaks—you would normally get pushback,” Martin says. “But we didn’t, partly because of our workplace culture, but also because our relationship with the union allowed us to communicate and make sure everyone understood the mandate. When we told them what we had to adhere to, they made sure the information was disseminated to members and employees.”
Because the project is a county hospital and because of how it is funded, the team had to meet inclusion workforce goals. An overall total 15% of the workforce on the project had to be females and individuals of Hispanic origin, and 20% of the total workforce had to be residents of the city of Cleveland.
“We tried to do that within our company, and when we needed people, we communicated and worked with Local 33 to meet the goals of the job site from the boots on the ground perspective,” Martin says.
“T.H. Martin and Local 33 identified the need for inclusion on this project, and we worked as a team to meet those needs and goals,” Miller says. “T.H. Martin and Local 33 identified the workforce needs and used our Partnership Development Department and JATC as means of meeting those needs with a well-trained workforce capable of completing the project. Inclusion is also our goal as an industry and something Local 33 is committed to on a larger scale.”
The project is nearing completion and weekly updates from Metro Health and the general contractor indicate construction is on schedule and carrying forward smoothly.
“I am very proud of our members and our employees for their resilience in fighting through the pandemic,” Martin says. “They had to work overtime, and we needed to find people to work on a second shift in the shop because of social distancing requirements. This can be challenging because everyone wants to be at home with family.
“It is the biggest project in the city in 20 years, it is a high profile project, and a lot of men and women wanted to be on it. Executing almost all of the rough-in and the majority of the job during a pandemic is challenging, but they were up for the task, and I appreciate that.”
“This project was successful because labor and management worked together, not only through a difficult project, but also through a pandemic while addressing the project needs and the needs of our organizations,” Miller said. “We accomplished this in an effort to make the customer glad they chose a union contractor with well-trained union workers.” ▪
Jessica Kirby is a freelance editor and writer covering construction, architecture, mining, travel, and sustainable living for myriad publications across Canada and the United States. She can usually be found among piles of paper in her home office or exploring nature’s bounty in British Columbia’s incredible wilderness.