
5 minute read
REMEMBERING 9/11
On the 20th anniversary of the World Trade Center Attacks, SMACNA and SMART are honored to partner on helping America heal.
By / Sheralyn Belyeu
Like millions of Americans, L. William Zahner, president of SMACNA-Kansas City member A. Zahner, knows exactly where he was during the 9/11 attack on the World Trade Center towers.
“I was in Kansas City, Missouri, meeting with an architect about the Bridge of Glass project in Tacoma, Washington,” Zahner says.
Greg Chastain, business manager at Local 2, was also in Kansas City. “I was an apprentice instructor for our JATC, and I came out to make some copies at the office,” he says. “We turned on the TV after the first plane hit, and I was watching when the first tower fell.”
Mark Stewart, a Local 2 journeyman sheet metal worker with Zahner, was in a Kansas City sheet metal shop when the first plane crashed. He called his wife and was talking with her when the second plane hit. “It was a surreal day, very weird, very solemn,” Stewart says. “When we went outside after work, there were no airplanes overhead, not even near the airport.”
It’s fitting that these three men were hard at work in the Kansas City sheet metal industry when the attack happened because Kansas City sheet metal played a unique role in honoring the lives lost that day. A. Zahner and Local 2 craftspersons produced the metal skin that sheathes the National September 11 Memorial Museum on the site of the former World Trade Center.
“We’re very proud of the fact that our contractor was selected to work on such an important project,” Chastain says. “The September 11 Memorial helps bring healing to our country, and it’s humbling that Local 2 is a part of that healing.”
One might assume that a project as symbolic as the September 11 Memorial Museum would automatically go to a United States firm. In reality, the New York City construction market pulls in professionals from around the planet. Rivalry for the contract was fierce because of the project’s design and noteriety.
But international competition does not intimidate Zahner. “There are fingerprints of Local 2 team members on projects all over the world,” says Chastain. “The members who work at Zahner are some of the most highly skilled in the country.”
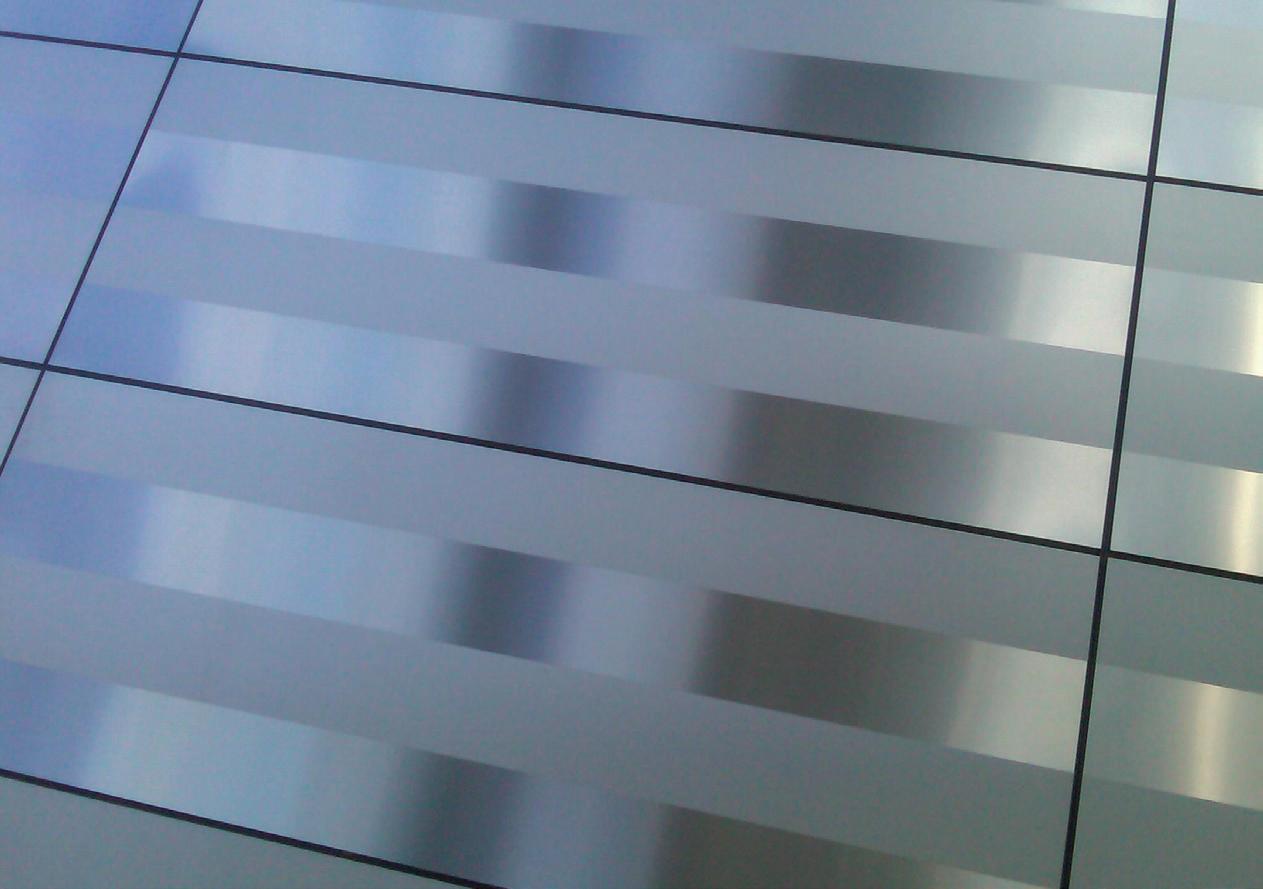
—Greg Chastain, business manager, Local 2
The design called for horizontal stripes across the panels and six different finishes. Zahner took the designer to the shop floor to demonstrate a panel mockup. “When we showed the architect how the light reflected differently in certain aspects, I had my sheet metal team standing right with me, explaining what we were going to deliver,” Zahner says. “No one had ever seen it before.”
Solving an engineering problem that looks impossible is typical for Zahner and the Local 2 workforce. “We never back down from a challenge,” Stewart says. “If somebody else can’t do a project, you need to let us take a look at it, because we probably can.”
Succeeding on a world stage demands the highest levels of performance from everyone at A. Zahner Company. Zahner has personally written seven books on architectural metal. But he and the engineering team depend on world-class labor to bring their plans to reality. “The people who work here want to know things and they want to keep learning,” he says. “Sometimes other contractors ask me how I get such good people.”
An extraordinary labor force starts with the Local. “We’re able to recruit some of the best, highest skilled, brightest people in the area,” Chastain says. “We have a great training program that helps with the process, and the on-the-job training and mentoring that our members provide for our apprentices is second to none.”
The result is craftspersons prepared to meet any challenge. “Our team had to make these panels really well because the surface would show any flaw,” Zahner says. “When we V-cut and fold the panel edges, we get to within tenths of millimeters.”
Every panel was distinct, with a unique combination of finishes and angles. “The depth of each V-cut had to be exact or it would break through to the face,” Stewart explains. “The location had to be right on the money because if it was off, it would change the angle of a tapered panel.”
The striped finishes added another layer of complexity. “When you do a differential finish on a plate of stainless steel, it’ll change its shape,” says Zahner. “Each panel had to be perfectly flat, so we had to do the reverse and take the stress back out.”
Shipping also had to be exact. “I was in charge of making sure all the hardware was put on correctly, and that the correct panels went into the correct crates,” Stewart says. “When we build crates for international shipping, we make sure they can go overseas and not be damaged, so everything will arrive looking exactly the way it looked when it left our shops.” Decades of experience with international delivery have honed Zahner’s quality control processes. “We take pictures before they ship, so we verify that the material’s good when it leaves here.”
Attention to detail pays off in the satisfaction of a job well done. “The September 11 Memorial is probably the top on my list as far as being proud of a job,” Stewart says. “When they showed it on the news for the 20-year anniversary, it still looked beautiful.”
Zahner loves seeing his staff’s joy in the project. “The best thing that ever happens for me as the CEO is when the people in the plant or our engineering group take their families to look at the Memorial. You know they take pride in the work when they send me pictures.”
Zahner has advice for anybody who visits the Memorial in person. “Look at the Memorial in different lights to see the way light reflects off the material and the metal. Every change in the light changes the appearance of the building. It’s a little jewel in that area. There’s reflective stainless steel on the surrounding buildings, but that one’s the jewel.” ▪ A Colorado native, Sheralyn Belyeu lives and writes deep in the woods of Alabama. When she’s not writing, she grows organic blueberries and collects misspellings of her name.
