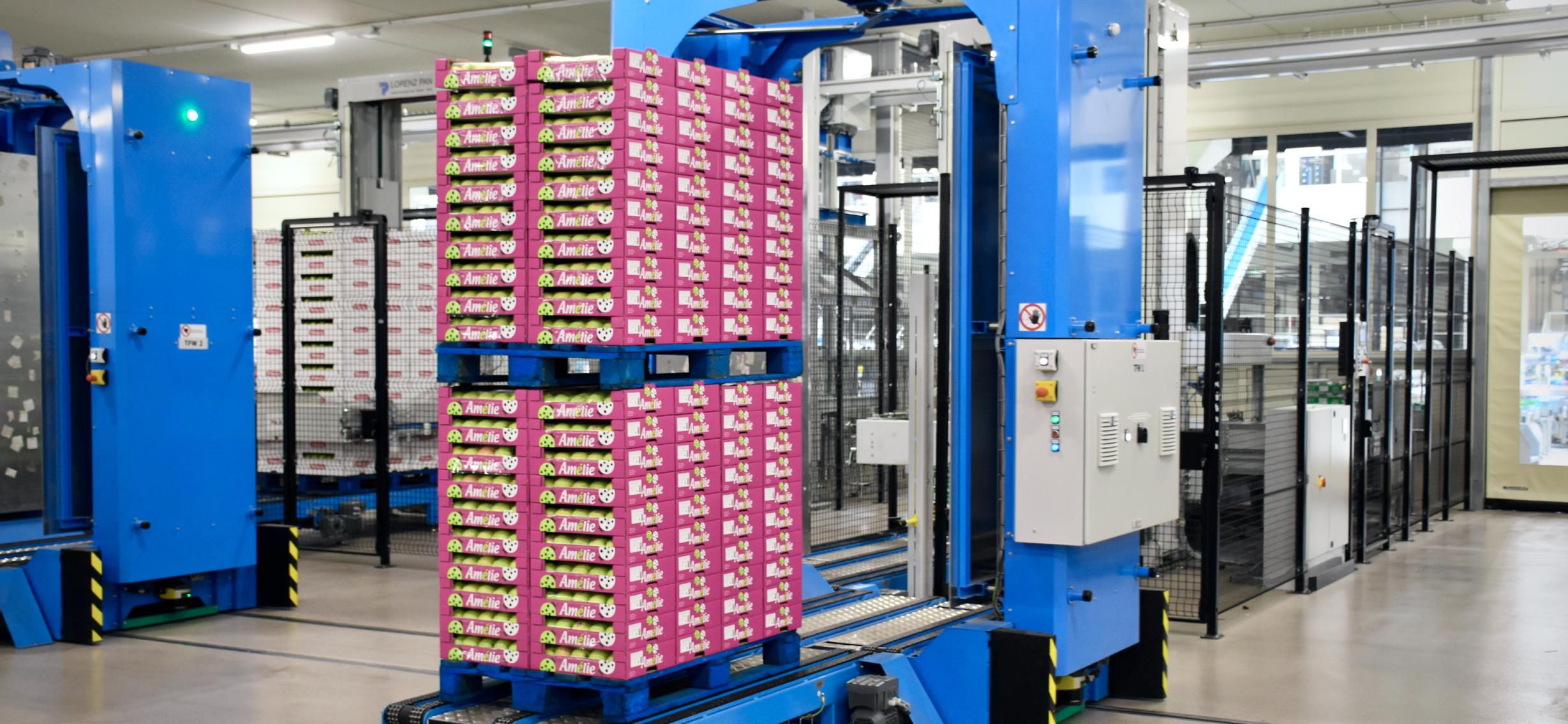
1 minute read
How to Avoid These Three Common Automation Mistakes
Mistake 1 –Going it alone.
Instead: Establish a cross-functional team and be inclusive.
Many organisations underestimate the diverse skillsets needed to extract, share, and apply valuable insights. Often projects are led by a traditional procurement department with a black-and-white mentality, where bureaucratic layers stall critical project progression and momentum. A committed, cross-functional team who are supported to succeed is essential.
Secondly, where an organisation doesn’t employ skillsets such as engineering, or they exist but a large-scale automation project is new, it’s important to engage specialists.
Mistake 2 –Assuming you need to invest big. Instead: Don’t rush and start small.
What, when, and how to automate depends on where you are now and where you want to be in the future. Businesses need to ask themselves: “What is A, what is B, and how do l get from A to B?” Companies may assume automation necessitates long lead times and multi-million-dollar investments.
But, if due diligence is carried out upfront, opportunities for tactical initiatives pop up.
Take the process of selecting an automation vendor or solution: how can an organisation evaluate the options without knowing where they are, where they need to be, and then assessing the costs, challenges, and risks associated with any decision-making?
It does not always have to be a large-scale transformation. Often, incremental change in a warehouse results in automated solutions because they are the optimal choice.