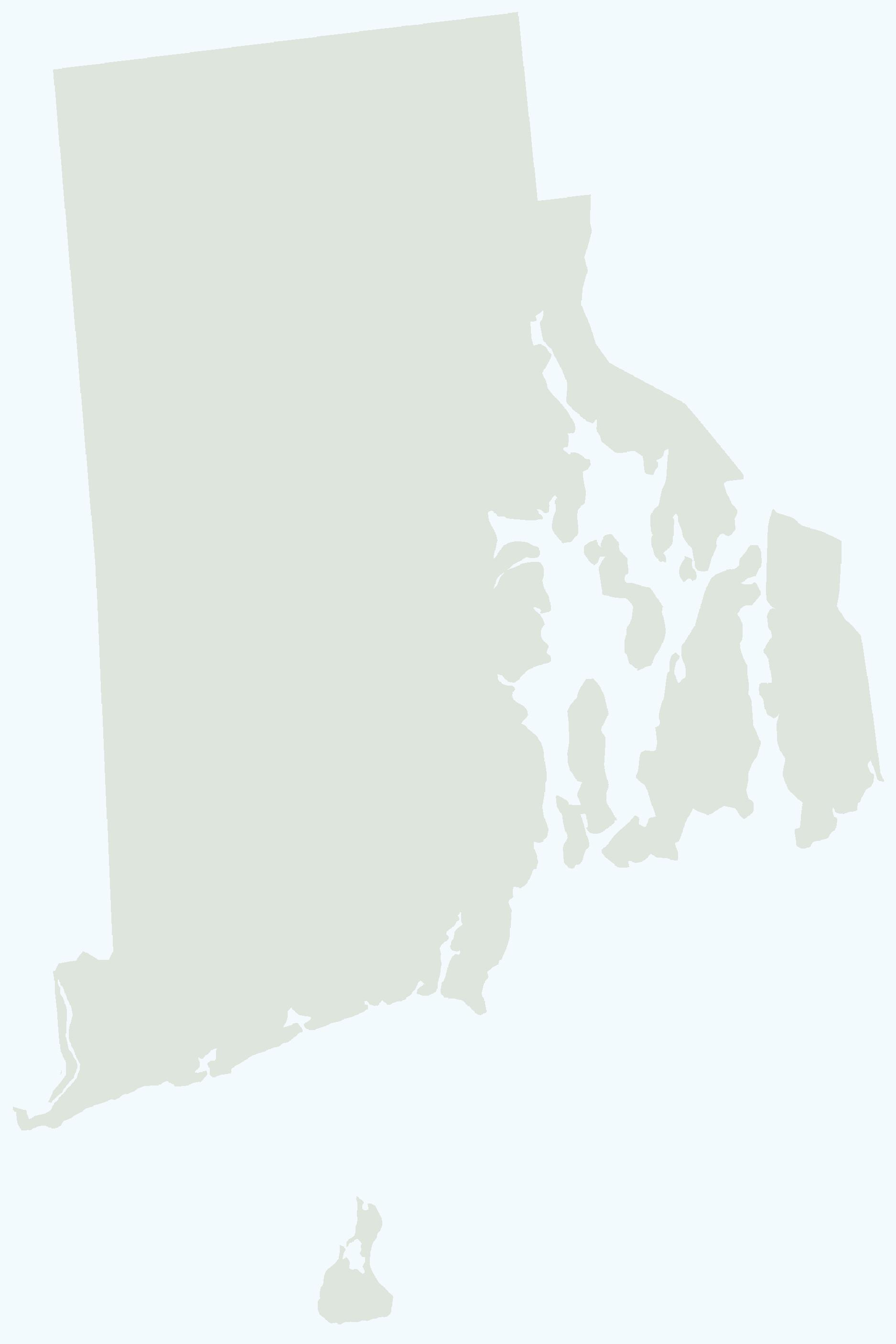
24 minute read
THINGS MADE HERE
Still a sought-after player
Since the late 1700s, Rhode Island has been a major player in traditional and emerging industries. It continues to be home to builders, makers and designers of all stripes, providing an array of products that belie its size. Some help tickle one’s tastebuds on a warm summer day, while others represent substantial advancements in health care and help improve people’s lives. Manufacturers and construction businesses have powered through the COVID-19 pandemic, showing off the resilience and commitment to quality that have helped make “Rhody Made” a sought-after seal of approval. Take a look at a sample of the companies making Rhode Island proud with an array of old-school and “new-economy” products.
Advertisement
CONSTRUCTION
Gilbane Building Co. .......................................................................................................................... 27 Providence Painted Signs................................................................................................................ 27
CONSUMER PRODUCTS
CakeSafe LLC........................................................................................................................................... 28 The Beck Cos. ........................................................................................................................................ 28 Colonial Mills Inc. ................................................................................................................................ 29 Ocean State Shields LP..................................................................................................................... 29 Garland Writing Instruments......................................................................................................... 30
DISTILLERS
Ravenous Brewing Co. ...................................................................................................................... 30 Narragansett Brewing Co................................................................................................................ 31
FOOD/DRINK
Wright’s Dairy Farm & Bakery....................................................................................................... 31 Del’s Lemonade & Refreshments Inc....................................................................................... 32
HEALTH CARE
Rubius Therapeutics Inc................................................................................................................... 32 Northeast Orthotics & Prosthetics............................................................................................. 33
INDUSTRIAL
Magnetic Seal Corp............................................................................................................................. 33 AquaMotion Inc. ................................................................................................................................... 34
MATERIALS
LEIGH ShoeCase Co. ........................................................................................................................... 34 Includesign LLC...................................................................................................................................... 35
TECHNOLOGY
Vitae Industries Inc............................................................................................................................. 35 ALCOR Scientific Inc. .......................................................................................................................... 36 Yushin America Inc. ............................................................................................................................ 36
THINGS MADE HERE
CONSTRUCTION
THE STORY: Gilbane Building Co. was founded in 1870 by two forward-thinking and entrepreneurial brothers as a small carpentry firm constructing custom homes in Providence. Through a hardearned reputation for quality, a dedication to excellence and a commitment to building with integrity, the brothers created what is now a global, comprehensive construction management and professional services firm with over 2,800 employees and 46 offices worldwide. Among Gilbane’s well-known projects include the International Game Technology PLC headquarters, the Dunkin’ Donuts Center renovation, the Interlink at Rhode Island T.F. Green International Airport and the new East Providence High School.
THE STORY: Providence Painted Signs was established in 2012 and specializes in creating various painted signs for local businesses. The company creates signs that are visually appealing and eye-catching. Along with wooden signs, Providence Painted Signs also paints murals that splash across buildings. One such mural is on the rear of Trinity Repertory Company’s theater building in Providence.
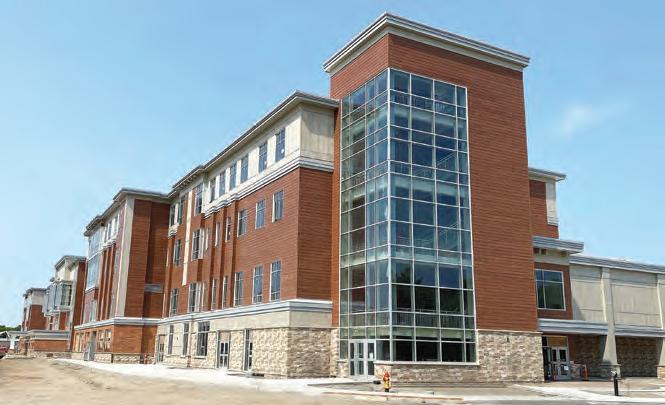
› Gilbane helped provide construction management services for the new $189.5 million, 304,000-square-foot, four-level, comprehensive high school in East Providence.
The new school will serve 1,600 students in grades 9-12 and 400 faculty and staff members.
It is the largest high school in the state. › The new high school will also feature an 800seat performance theater; a two-story health and physical education facility, including an elevated walking track, basketball courts, trainer’s room, coach’s offices and locker rooms; a two-story media center; a student commons area with exterior seating; and a full-service kitchen to accommodate food preparation for the entire East Providence school district. › Features of the new school’s integrated Career and Technical Center will include: automotive space with six lifts and bays; a construction laboratory with six bays and two-story steel structures for construction training; a forensic laboratory; culinary arts space; radio and television broadcasting area; a greenhouse; graphic arts space; and associated support services.
› Steve Duvel, Gilbane’s senior vice president and Rhode Island business unit leader, said the company is thankful for the employees and subcontractors “who worked tirelessly to bring to life East Providence’s vision of a 21stcentury learning environment that will serve generations of Townies for years to come.”
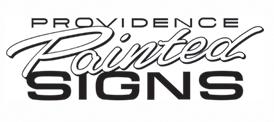

› The company makes approximately nearly 100 signs per year, depending on the scale of projects in a given year. › Providence Painted Signs creates signs for any business that needs signage, with each job being custom to accommodate the client’s needs. Costs for the signs range between $500 to $50,000. › The signs are made with paint, plywood, aluminum, mahogany, cedar and steel. The parts vary depending on the project. › About one to six people are involved in making the signs based on the scale of the sign being made. The time frame on making the signs can range between one day to two months.
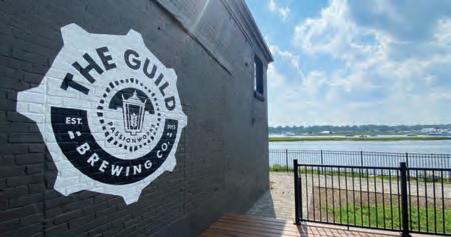
THINGS MADE HERE
CONSUMER PRODUCTS
THE STORY: In 1989, Scott Chapin invented a box to protect the wedding cakes his wife, Juli, made and she used it on a regular basis. Chapin then founded CakeSafe LLC in South Kingstown to sell the boxes, which he continued making in his basement. Still located in South Kingstown, CakeSafe now has a headquarters and production facility, where the company creates many different product lines of tools for bakers and chocolatiers.
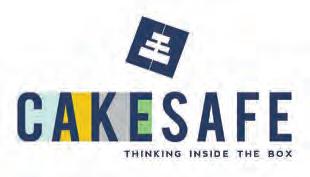
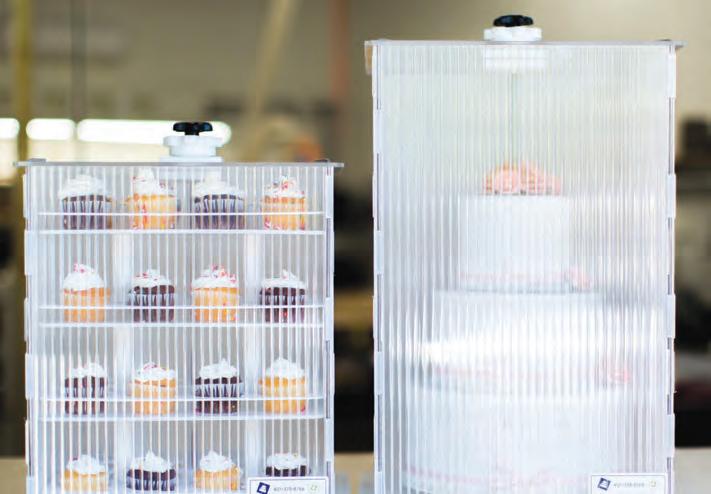
› The CakeSafe Box protects single-tier and multitiered cakes from heat, tipping, bumpy roads, weather, slammed brakes and more.
There are also shelving inserts for cupcakes or multiple cakes that can be put inside the box.
› The company makes 11 different sizes of
CakeSafe Boxes. Approximately 1,000 are made annually. The retail price ranges from $199 to $735. CakeSafe LLC also has a wholesale division of the business and sells to distributors around the world.
› The boxes are made from high-density polyethylene, coroplast, polycarbonate, acrylic, food-grade stainless steel and aluminum. All component materials are food-safe.
› There are nine employees working at
CakeSafe LLC. It takes about 20 to 35 minutes to make a single box, depending on its size.
THE STORY: The North Smithfieldbased and family-owned The Beck Cos. specializes in showroom design, engineering, manufacturing and fabrication. Five companies are under the Beck Cos. umbrella. One of them, Great American Recreation Equipment, manufactures gaming tables, such as shuffleboards, air hockey tables and billiards tables.
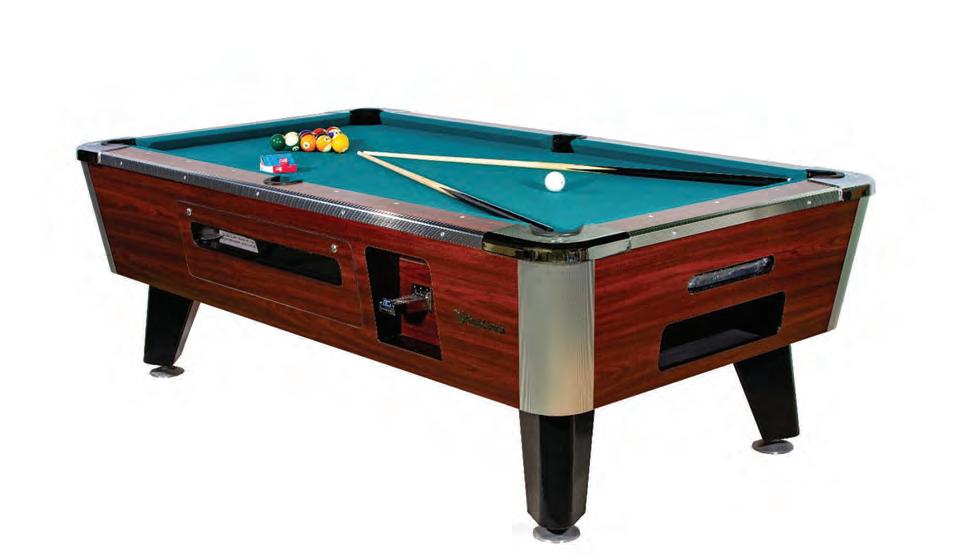
› The company makes approximately 10,000 tables per year, with each unit costing approximately $2,400 for retail. › The billiards tables are sold to distributers who put them in locations to generate revenue as coin-, bill- or card-operated machines. The tables are also purchased for home use for people who want singlepiece slate tables with automatic ball return, and for commercial use by colleges, military game rooms, cruises and hotels. › Each table is made of one piece of slate, laminate, and has metal corners, a coin mechanism, lighting and auto ball returns.
› It takes two days and four employees to make each table.
The company employs seven people total.
› Colonial Mills makes more than 200,000 rugs, home accessories and baskets. The company sells the products to the mid- and high-end markets.
› The products are used for home décor needs, both indoor and outdoor.
› Colonial Mills makes products from all different materials, such as allnatural wools, wool blends, indoor/ outdoor polypropylene, space-dyed wool and nylon, chenille, cottonblend fabric, Sunbrella acrylics, recycled yarns, leather and denim. › The company employs 100 people and has a diverse workforce representing more than 15 countries.
› It takes on average three days to make the products at Colonial Mills.
THE STORY: For more than 40 years, Colonial Mills Inc., a family-owned operation in East Providence, has produced made-to-order wholesale braided/woven rugs, storage baskets and decorative home accessories. The company views braid as a method of construction, not a style, and such thinking allows Colonial Mills to combine the traditional with contemporary.
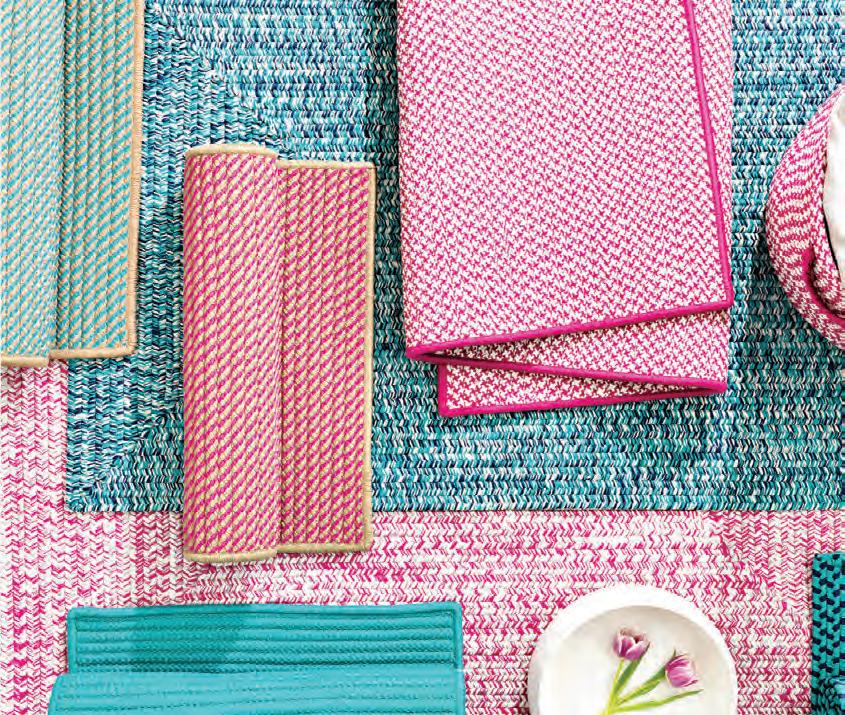
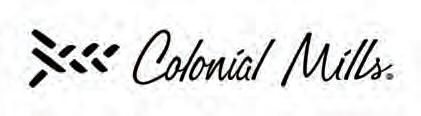
THE STORY: Ocean State Shields LP, based in Providence, was founded to help address the ongoing COVID-19 pandemic. Cofounded by Allyson Cote and Todd Thomas, the company has developed products to safeguard environments from COVID-19, including at public places and restaurants. Among the products developed by Ocean State Shields is the Shell-ter igloo, used mainly by restaurants to help with outdoor seating.

› Ocean State Shields first made the
Shell-ter in the fall of 2020. About 80 were made that year and the company anticipated that it would fabricate more than 500 units in the fourth quarter of 2021. › The outside-dining igloo has a 9-foot base diameter and is a four-season model that seats between four to five people. The igloos feature high sidewalls, an enormous amount of clear wall, and are built in a commercial-grade fashion, including survivability for up to 70 mph winds. › The igloos include anchoring kits, floor mats, lighting, and provide privacy and sun shading. › The company has six direct employees. It takes between three to four people approximately six to eight hours to make an igloo. Retail costs for the igloos start at around $1,900. › The igloos are made of fabric components that are clear and opaque 10-year awning fabrics with stain and ultraviolet damage resistance. Hardware components are steel, polyvinyl chloride, and fiberglass and resin poles.
Fabrics are sewn with commercial-grade marine threading and adhesives.
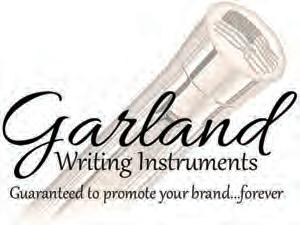
THE STORY: In 1927 when Louis Lanoie founded Lew Manufacturing Co. in Coventry, the company first made small presses that led to the design and development of the internal pen mechanism by other pen manufacturers across the U.S. and Europe. Now, Lew Manufacturing – now known as Garland Writing Instruments – produces eco-friendly pens that have been used in both government and Hollywood.
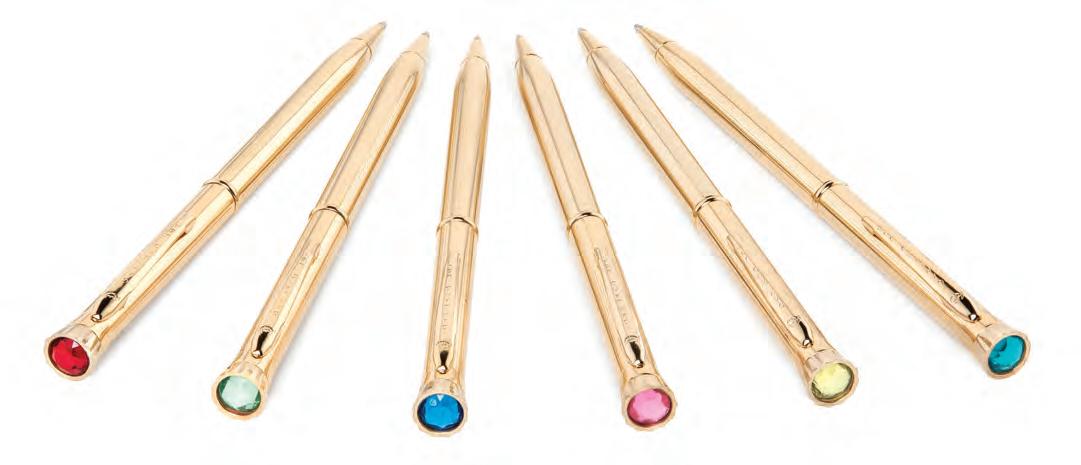
› The pens are made of brass, plated brass, anodized aluminum, stainless steel and resin. › It takes approximately 14-18 employees to make the pens, and a customized product can be delivered in as quickly as one day. › Garland pens are used by presidents, diplomats, governors, senators, Congress members and military leaders throughout the globe. The rollerball pens were used to sign the 2020 articles of impeachment. The pens cost between $10 and $100. › The rollerball pens are also found in television shows, including in the Netflix show
“Designated Survivor” starring Kiefer Sutherland. › At the onset of the COVID-19 pandemic, Garland introduced an antimicrobial pen collection that is coated with Polygiene ViralOff technology. › The company also pivoted some of its operations to produce personal protective equipment in response to the pandemic, including making anti-fog face shields.
DISTILLERS
THE STORY: Ravenous Brewing Co. was established in 2011 in Woonsocket, becoming the first brewery to operate in northern Rhode Island. Despite its small size in producing approximately 800 barrels per year, Ravenous has garnered a large following with its ales. The company recently relocated its operations to nearby Cumberland.
› Ravenous Brewing Co. carries approximately 10 tap lines at its Cumberland brewery, with various ales such as Coffee
Milk Stout, Rhode Haze NEIPA, Blackstone APA and Cogswell
Tower DIPA in the brewery’s regular rotation. › Ravenous’ products have about a two-week turnaround from the time they are made until they are ready for consumption.
It takes between two to three employees to make a single unit of product at Ravenous. › Brewing begins with the grain, which is milled and added to Ravenous’ mash tun. The grain is then steeped in warm water for about an hour, which creates the wort. The wort is then transferred to the kettle, where it is boiled and spiced with hops and other ingredients. Once the boil is done, the beer is transferred to a fermentation tank, where yeast is added and the beer is left to ferment for about seven days. Once the beer is finished fermenting, it is cooled, carbonated and packaged for market. › Ravenous Brewing has two full-time employees and 20 part-time employees.
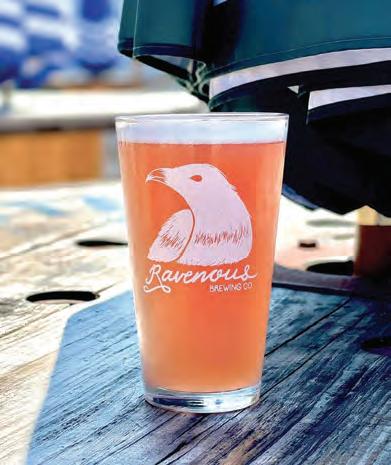
THE STORY: Six German immigrants in 1890 came together with $150,000 and built the first Narragansett Beer brewery building. Within 10 years, Narragansett Beer became the largest-selling beer across New England and was a beverage staple for close to a century. After the brewery shut down in 1982, Rhode Island native Mark Hellendrung in 2005 rallied a group of investors to restart the Narragansett Brewing Co. again. The company opened a new brewery in Providence in the spring of 2021.
› Among the 17 beers that Narragansett Brewing Co. currently makes is Musik Express IPA, which became available in April 2021. › Each six-pack of Musik Express sells for about $11.99 in local liquor stores. The company produced approximately 2,500 case equivalents from April through July 2021. › Narragansett’s IPAs are the largest style in the craft beer segment. The Musik Express, the company said, is an approachable, well-balanced IPA brewed for a variety of beer lovers.
› Musik Express is made of weyerman pale and various other malts, citra, mosaic, el dorado and other hops, and water from the Scituate Reservoir.
› The brew process takes six hours and then the beer ferments for at least two weeks. Four employees help make each unit of the Musik Express. › Narragansett Brewing Co. employs 25 people.
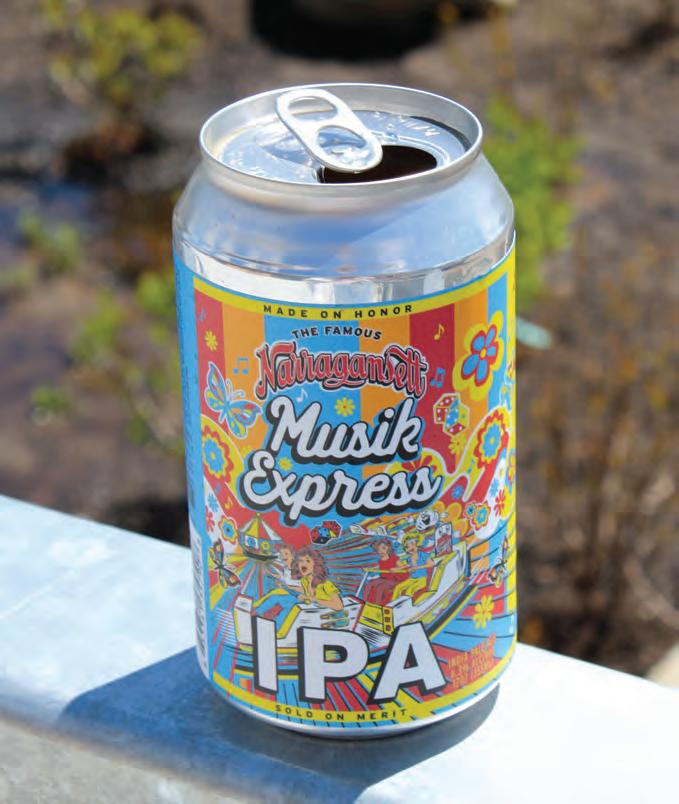
FOOD/DRINK
THE STORY: Family-owned Wright’s Dairy Farm & Bakery in North Smithfield has been producing and baking various dairy products since 1914. Wright’s offers a full line of cream pastries, breakfast items, milk and decorative cakes. The farm includes a 120-cow, free-stall barn and a milking barn. Wright’s also started making ice cream in 2012 and it’s the state’s only cow-to-home ice cream.
› In 2020, Wright’s Dairy Farm & Bakery made approximately 15,000 gallons of ice cream. Packaged ice cream varies from $6.50 to $8.50.
Scooped ice cream varies from $3 to $6.50. › The ice cream is made of milk, cream, sugar, corn syrup solids, egg yolks and organic stabilizer. › There are four people making a single unit of ice cream, but different people are involved in various stages of the process depending on the day. › The cows are milked on the first day, then it is blended with ingredients on the second day to make the ice cream base. The base is homogenized and pasteurized and aged overnight. On the third day, the base is churned into semi-frozen ice cream. This is also when cookies, brownies, cake, or nuts are added. Then on the fourth day, the ice cream is served. › Wright’s employs 120 people.
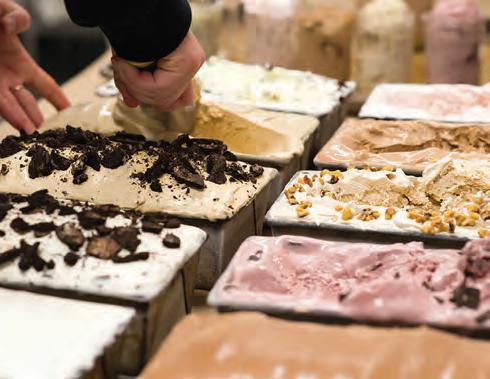
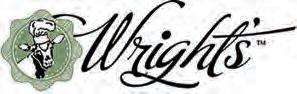
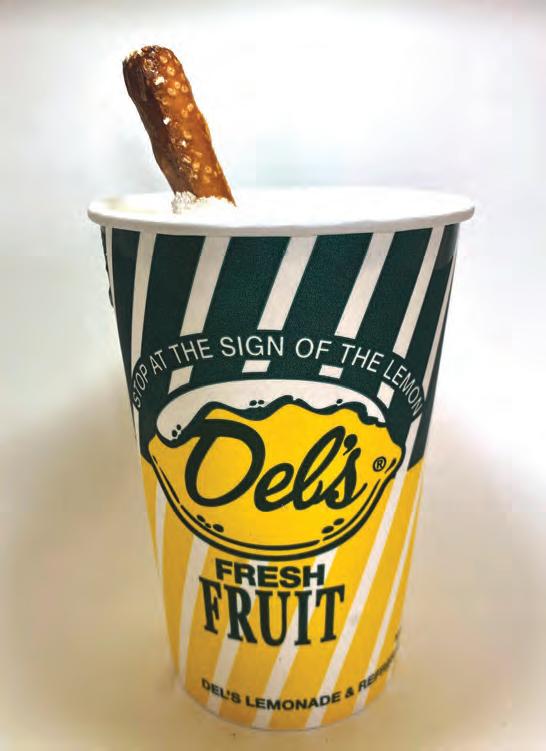
THE STORY: Franco DeLucia’s father began making the earliest Del’s frozen lemonade in 1840 in Naples, Italy. Franco DeLucia then brought his father’s recipe to America at the turn of the century. Franco DeLucia’s son, Angelo, then began work on a machine to produce the frozen lemonade. In 1948, Del’s Lemonade & Refreshments Inc. acquired its name and became the sole product sold at a little stand in Cranston. Soon after, Angelo DeLucia had designed the first mobile units in order to serve the frozen lemonade anywhere in the state.
› Del’s serves lemonade to more than 2 million people per year, with prices ranging from $1.50 per mini cup to $25 per gallon. › Along with it being made in Cranston, Del’s produces its lemonade in Massachusetts, Connecticut and New Jersey. › The company mixes filtered water with sweetener, fruit concentrates and citric acid to make the lemonade.
Del’s sometimes also adds natural color for watermelon and peach mango. It takes between four to five people approximately two hours to make a batch from start to finish. › The lemonade is made with freshly squeezed lemon juice and lemon juice concentrate.

HEALTH CARE
THE STORY: Cambridge, Mass.-based Rubius Therapeutics Inc. was founded in 2013 with the aim to transform cancer treatments and autoimmune diseases through new cellular medicines. In 2018, Rubius purchased a 135,000-square-foot manufacturing facility in Smithfield to produce red cell therapeutics. The company planned to invest up to $155 million over five years and expected to hire 150 employees at the facility.
› Red cell therapeutics are allogeneic cellular therapies for the potential treatment of cancer and autoimmune diseases. Product candidates are currently being evaluated in clinical trials for the treatment of solid tumors, acute myeloid leukemia and cancers caused by a strain of the human papilloma virus, including cervical cancer, anal cancer, and head and neck cancer. › The first engineering runs of the red cell therapeutics were completed in late 2019. Billions of cells per dose are made annually. › Rubius Therapeutics CEO and President Dr. Pablo J. Cagnoni said the company earlier this year presented preliminary clinical results that provided initial validation of its proprietary cell therapy platform for the treatment of cancer. “We are extremely excited about the potential of using engineered red blood cells to treat disease,” he said. › The therapeutics are genetically engineered red blood cells that express combinations of molecules on the cell surface. The entire process for each batch takes approximately three weeks to make.
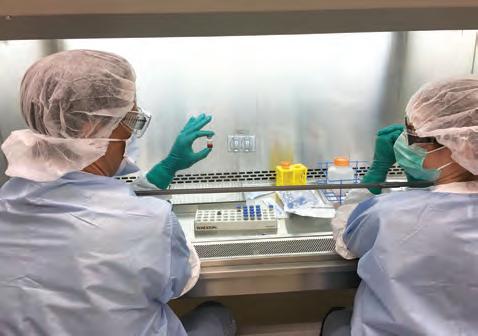
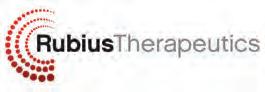
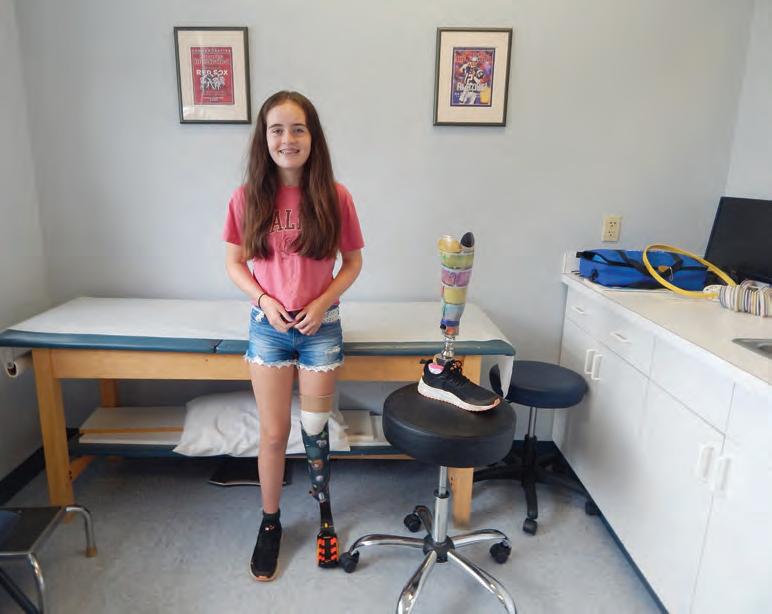
THE STORY: Mark Marich, an above-knee amputee since the age of 18, founded Northeast Orthotics & Prosthetics, which specializes in custom made prosthetic (artificial limbs) and orthotic devices for people of all ages, in Providence in 1985. His experience both as a patient and a prosthetist has given him firsthand personal knowledge and understanding of everyday life as an amputee. Marich was also the first person in the United States to use the C-Leg System, one of the world’s first microprocessor-controlled prosthetic knee units developed by Otto Bock.
› The company provides many custom fabricated items for patients at Rhode
Island Hospital, such as custom fabricated ankle-foot orthotics, thoracic lumbar sacral orthoses for trauma and postoperation, as well as protective helmets for post-craniectomy and cranial remolding orthoses for infants suffering from plagiocephaly. › Northeast Orthotics provides thousands of custom fabricated devices a year. More than 250 are lower-limb prostheses.
Amputees, people with disabilities, people who have had accidents or significant trauma, or those in need of custom realignment or support within the skeletal system use Northeast Orthotics’ prosthetics. › Each prothesis is made out of a nyglass (nylon fiberglass fabric), carbon fiber, aluminum and a two-part resin. The protheses costs are based on complexity.
It costs $650 for a partial toe prosthesis to $60,000 for an above-the-knee prosthesis with a computerized knee unit.
The majority of the cost is paid for by insurance companies. › It takes on average four to five weeks for a prosthesis, which includes evaluation, measurement, casting and multiple “test” fittings. In emergency cases, the company provides same-day turnaround for custom ankle-foot orthotics, thoracic lumbar sacral orthoses and protective helmets.

INDUSTRIAL
› The MagSeal utilizes magnets, creating mechanical seals that prevent water or oil used by rotating equipment from leaking into the external environment, as well as preventing foreign debris from entering the system. › The company makes approximately 50,000
MagSeals per year. Retail prices for the seals are between $300 to $5,000 depending on the size and specifications. › Boeing, Safran, Pratt and Whitney, Airbus,
Honeywell, Rolls-Royce and General Electric are among the companies that use seals made by
MagSeal. › The seals are made of AlNiCo magnets, specialty alloys, O-rings and various grades of carbon graphite. Making the seals involves machining and grinding processes to achieve very tight tolerances required for performance of the part. › It takes more than 23 people, depending on specification, between 26 to 38 weeks to make the seals. MagSeal currently employs 65. THE STORY: In 1954, George E. Colby and Robert L. Stevenson founded Magnetic Seal Corp. in Smithfield, or MagSeal, and subsequently patented the first magnetically energized rotary seal in 1958. Now, close to seven decades in operation, MagSeal still is family owned, now based in Warren and routinely applies its technology and advances power systems in the aerospace, performance automotive, marine and other diverse industries.
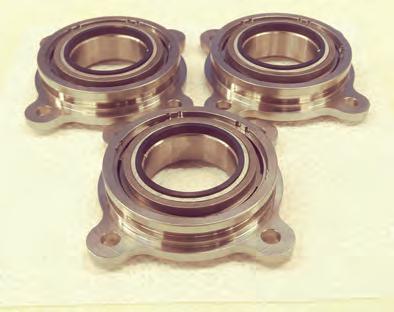
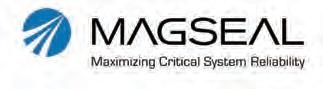
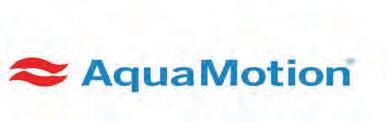
› The AquaFlash was first introduced to market in 2017 and approximately 10,000 are made annually. Each product costs about $310. › The product was created for homes and businesses that have a single pipe system with a hot water tank and don’t have electricity under the sink and can’t install a pump there. This kit has a pump with a built-in 24-hour mechanical timer with 15-minute increment tabs. Setting the timer limits the operating cost to when hot water is desired.
› The kit is made with a stainless-steel pump with 3/4-inch Female National Pipe
Thread union, built-in timer that is made of composite, 10 feet of line cord, bronze bypass valve (with check valve that is made of composite), 2 feet of National Sanitation
Foundation stainless hose and brass tee.
› The valve uses a forged brass body with compression fittings for ease of installation in 10 minutes. The internal temperaturesensing bi-metal coil is calibrated in a controlled temperature environment to maintain 93 degrees Fahrenheit water temperature at the sink. No more waiting for hot water, no more wasting of treated water down the drain. Instant hot water comfort. A circulator is required to work in conjunction with the Aqua Flash valve. › AquaMotion employs 20 people. THE STORY: Hans Kuster incorporated AquaMotion Inc. in Warwick with the vision of designing the most energy efficient, high-performance circulator line on the market to compete with the world and U.S. market leaders. The company developed the Green ECO-Cartridge design, which has the only field-replaceable and field-serviceable cartridge on the market. Another product the company produces is the AquaMotion AquaFlash, which is used to recirculate hot water.

MATERIALS
THE STORY: Tracey Cungo listened to many who were on a quest to find the perfect travel bag, especially ones that best pack shoes. So Cungo chose to design all her bags to have separate, adjustable compartments to pack a few more pairs of shoes and keep them away from clothes. The bags provide functionality needed by experienced travelers and commuters to safely pack tech and have luggage pass-throughs in a modern aesthetic that is sleek and stylish. Cungo then formed LEIGH ShoeCase Co., based in Newport, to create eco-friendly travel bags as part of the LEIGHWay Collection.

› The LEIGHWay Collection bags were first made in 2017. Each bag costs between $200 and $250. › Seasoned travelers, commuters, people who work out and students are ones who regularly use the LEIGHWay bags, which help pack shoes away from clothes. › The bags are made out of antimicrobialtreated recycled nylon made from plastic bottles, nylon lining woven with Ionic metallic silver yarn (antimicrobial and odor-free) and rubber. It takes eight hours and eight employees to make a single bag. › LEIGH is currently developing bags that have odor-free antibacterial lining to help carry diapers and pets.
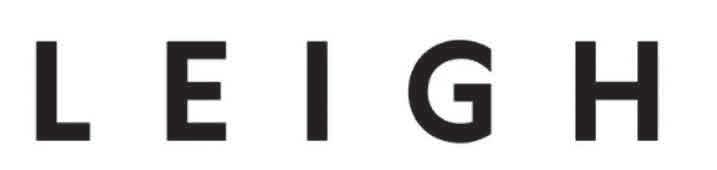
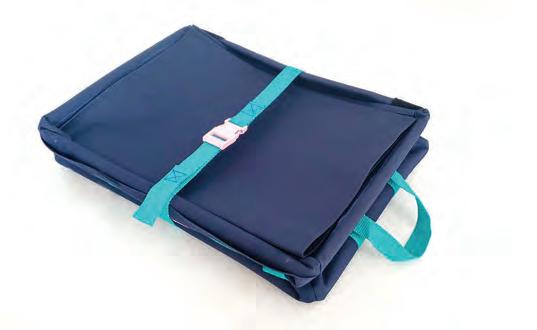
THE STORY: Includesign LLC founder and CEO Diana Perkins wanted to help a professor of hers who used a wheelchair. She worked with her professor throughout the design process to create a collapsible carryall that would help those in a wheelchair with shopping and other everyday tasks. The school project, called the LapSnap, subsequently turned into a business for Perkins. The LapSnap is the first of many products the company hopes to develop to help people with disabilities.
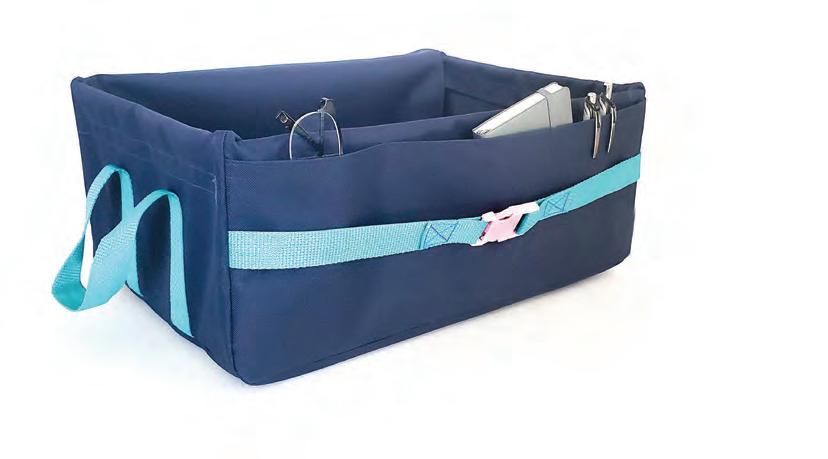
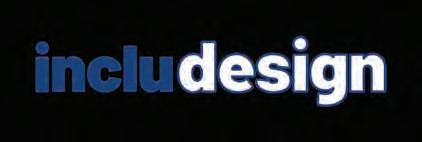
› The LapSnap helps wheelchair users perform everyday tasks more independently by enabling them to carry their belongings hands-free, from shopping to gardening, as well as transporting pets and picking up packages. › The first prototype was created as a part of
Brown University’s engineering capstone course. In order to facilitate user testing,
Perkins sewed 10 prototypes to send to wheelchair users nationwide. Professionally manufactured products were then produced at the beginning of 2021. › The lead time for a new run of LapSnaps is approximately eight to 12 weeks depending on manufacturer commitments. Raw materials are purchased and sent to the company’s manufacturing partners. Each manufacturer creates a portion of the product and sends them to includesign’s main facility, where employees assemble the
LapSnaps and distribute them to customers. › Includesign employs 11 people. The company is currently designing a version of the LapSnap specifically with quadriplegics in mind, which will have magnetic clasps and other features for those with limited upper-body mobility.
TECHNOLOGY
THE STORY: Vitae Industries Inc. in Providence began helping the pharmaceutical industry become more efficient when the company introduced its AutoCompounder product. Pharmacists would program the AutoCompounder to create actual medicine doses and the 3D printer will print the doses depending on the medication that is prescribed for patients.
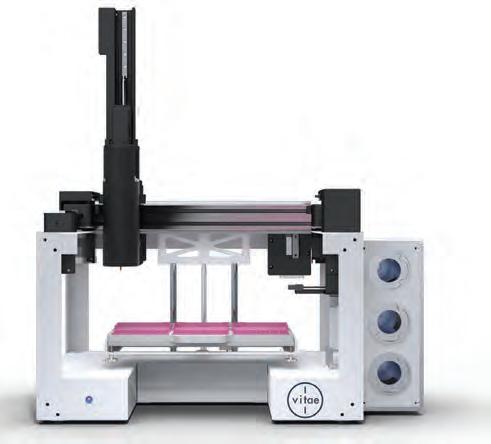
› Vitae first created the AutoCompounder in 2018. Currently, the company makes more than 25 units per year but expects to increase production fourfold over the next year. › Each AutoCompounder costs between $15,000 and $20,000. › Vitae sources materials and custom components from machine shops and manufacturers around the Northeast and the country to help build the
AutoCompounders. The final assembly and testing of the platform happens in-house.
› It takes approximately seven days and two employees to make each
AutoCompounder from start to finish. › Vitae Industries employs six people.
THE STORY: In 2001, ALCOR Scientific Inc. was formed after Diagnostic Systems Corp. and OST Medical merged into a single entity. According to the company, ALCOR’s name is derived from one of the two binary stars in the Ursa Major constellation – meaning that the potential for innovation is infinite. Two decades later, ALCOR’s market for medical devices has focused on historically inefficient, underserved health care segments of society. It has two different product lines, the Sentinel brand enteral feeding pumps and the iSED and miniiSED Automated Erythrocyte Sedimentation Rate Analyzer.
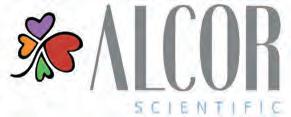

› The SentinelPlus is a feeding pump that delivers all enteral feeding formulas. The iSED and miniiSED ESR analyzers perform tests that are helpful in evaluating and monitoring the progress of conditions associated with acute and chronic inflammation. It can be used as a screening test, to aid in diagnosis, to aid in differential diagnosis, and to monitor response to therapy. › ALCOR manufacturers more than 5,000 such devices annually. The feeding pumps are used in hospitals and skilled nursing facilities to support critically ill patients. The iSED and miniiSED are used in clinical diagnostics laboratories of all sizes. › ALCOR employs more than 50 people in North Smithfield, with about 20 of them being on the production team. › ALCOR analyzers use quantimetric photometry to capture the impact of the early phase of red blood cell sedimentation – the rouleaux formation. This is the most critical stage of the
ESR because the size of the red blood cell aggregates in direct proportion to ESR values. ESR values increase according to the presence and intensity of inflammation.
THE STORY: Established in 1988, Yushin America Inc. is the oldest and largest subsidiary of Kyoto, Japan-based Yushin Precision Equipment Co. Ltd. The Cranston-based manufacturer operates out of a 70,000-square-foot facility, and specializes in building robots and custom downstream automation for injection moldings found in the plastics industry.

› The robots made at Yushin are used to automate plastic injection molding processes in the manufacturing sector. The robots are matched and mounted with the right injection molding machines and are utilized for multiple applications and systems to fully integrated factory automation such as pick and place of plastic parts, assembly of molded parts, packaging and inspection. › The robots are used by the automotive, appliances, medical, consumer products, industrial construction, food and beverage packaging, and electronics industry markets. Smaller robots start at $6,000 and some of
Yushin’s traverse robots can cost between $30,000 and $80,000. › Yushin’s robots are mainly built out of steel and various aluminum parts. The robot arm wrist flip unit (the arm end that enters the mold) is optimally designed to be slimmer/thinner. The main arm is incorporated with carbon fiber reinforced plastic panels, which helps shorten mold openings and allows accelerated molding cycle times. › It takes between two to three people to complete a robot from start to finish. Sprue pickers take about a week to finish, while it takes between eight to 10 weeks to construct a traverse servo robot. Custom-engineered automation systems may take up to six months.
› Eighty employees work for Yushin America in Cranston.