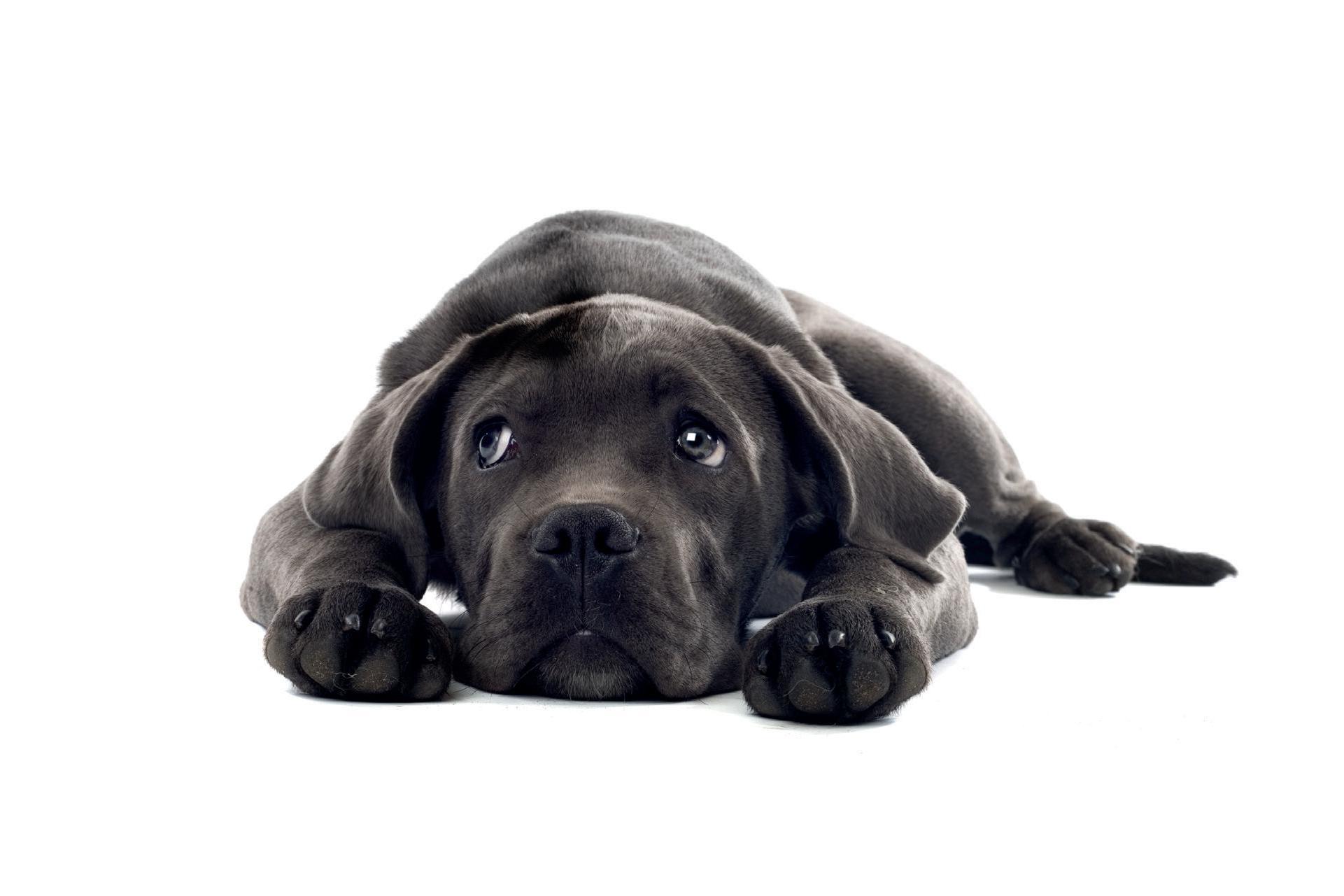
12 minute read
Building Readiness and Agility for the Next Pandemic
“It is not a ques tion of if but when”
Building readiness and agility for the next pandemic or major crisis
Advertisement
By David Primrose, Synergy Food Ingredients Ltd and Dr Paola Cane, Mia Solution
The strong bond between pet owners and their pets and the positive role pets play in supporting mental and physical health are not new phenomena. Pet owners therefore look to the petfood sector to keep our pets fit and healthy through supply continuity of safe, legal, nutritious petfood that meets their quality expectations e.g. palatability, digestibility, texture, authenticity, and price. However, our business and personal lives have been severely impacted by effects of the CV19 crisis and the petfood sector is not immune from this. As seen in the human food industry, its effects are causing disruption to petfood manufacturers, suppliers (ingredients, equipment, packaging, logistics, laboratories etc) and retailers.
I am sorry to disappoint you but it is not a question of if we will face a future major crisis or pandemic but a question of when and survival (commercial and personal) depends on complex, diverse factors both under and outside our control. This requires us all to be prepared and agile to adapt to dynamic challenges. Strong leadership and coherent, clear authoritative communication are also required.
In April 2020, “The Grocer” (UK) magazine reported in a survey that 64% of respondents believe that worker sickness is the biggest challenge to continuity of food supply during CV-19. This is evidenced in June 2020, with temporary closure of a major UK chicken processing plant due to CV-19 worker sickness and cases in other countries including France, Germany, and the US. In the petfood sector, how would you cope with unexpected high levels of absenteeism due to sickness?
It is business critical therefore that we exert control in a way that is positive to help us survive and offers potential business efficiency improvement through new ways of working. We can better prepare for future crises by looking now at what we are doing to combat CV-19 and taking the positives from this catastrophic experience.
Anatomy of a crisis
Typically, a crisis (or major emergency) is defined as:
“an unusual, predicted or unpredicted event, creating an imminent or future significant threat to the business (infrastructure, employees, product supply including raw materials), its products e.g. petfood and its stakeholders (employees, customers, community)”
Threats might be “natural” (e.g. earthquake, animal and human diseases, crop failure) or “man-made” (e.g. war, food adulteration, arson, cyber-crime etc). A crisis might exhibit some common features e.g.
People (including business management) have limited or zero experience of similar events forcing them outside their “comfort zone”
Businesses are taken into the “unknown”, with dynamic, unfamiliar scenarios outside their control, making decision making difficult based on incomplete data and unknown risks
Stakeholders like decision makers experience “high” stress that can affect mental health
Increased consumer concerns e.g. Is petfood safe during the pandemic? Will there be shortage of petfood due to supply chain constraints (e.g. illness resulting in staff shortages or raw material availability problems)? Will the shops be open and have supplies of petfood due to panic buying?
Increased anxiety of staff e.g. Will I be unemployed? Will I be safe to work with other operators?
A crisis typically consists of linked phases, each with different operational challenges e.g.
1.
2.
3.
4.
5. Preparation (“Normality”) – “Normal” stress and anxiety levels exist. Business uses risk management and business continuity plan (BCP) to mitigate against crisis. Planning helps mitigate against future crises and develops the mindset required to adapt to complex, dynamic crisis scenarios. “Crisis” – Abnormal event e.g. earthquake, arson, CV-19 increases stress and anxiety levels to crisis level. Response (“Crisis Relief”) – BCP implementation, leadership and communication start to reduce stress and anxiety from “high” level. Effectiveness depends on BCP preparedness, strong leadership, and communication. Crisis is dynamic requiring agility and ability to act on limited data. Resolution – Depending on BCP effectiveness, leadership, communication, agility, and staff training further reduce stress and anxiety. Recovery – Business continuity is ensured through implementing policies, procedures, and ways of working. For future preparedness and agility, the recovery phase must include analysis of the current crisis, how the business responded and how things could have been done better.
The importance of communication
Clear, effective stakeholder communication from a skilled business leader is a key factor in maintaining trust and in managing mental
A dynamic approach using flavours & aromas to maximise pet food and treat palatability
Unlock the possibilities To find out more about our unique Tastetite and other feed enhancement technologies, visit www.inroadsintl.com, email info@inroadsintl.co.uk or call us on +44 (0) 1939 236 555.
health e.g. anxiety. Communication throughout the crisis cycle from “Normality” to “Recovery” should consider: Preparation – Prepare communication plans (who; how; when) through stakeholder engagement (internal – staff; external – supply chain; retailers; pet owners). Transparency demonstrates leadership, maintains trust, and avoids fear or rumours. Start of the crisis – To reduce anxiety and fear, communication should show empathy and caring but must be balanced against over-promising e.g. explain temporary product deletion, but do not promise date for full range availability. Demonstrate leadership and competence through clear, transparent, open communication. Response / Resolution phase – Expect that frustration and anxiety are likely to increase as a crisis goes on. Continue to manage expectations by showing empathy, giving good news and reassurance e.g. staff, retailer / pet owner concerns about product safety and continuity e.g.
o “Can Covid-19 be transferred through petfood?”
o “Although we have had ingredient supply challenges, we have
o worked to identify and approve new suppliers.” “I wish we were able to supply all of our product lines.
However, making temporary product deletions helps ensure supply continuity of trusted safe, legal petfood of the expected quality.” o
“We are committed to ensure staff employment and safety during the crisis to ensure continuity of supply of our products.
This means running the factory at reduced capacity to allow social distancing and safe ways of working. We continually review risks and will implement any future changes required.” Recovery – Thank stakeholders for their support in dealing with the crisis and engage with them to get their feedback. Acknowledge any mistakes and use quality management “PlanDo-Check-Act” cycle thinking to review the crisis preparedness, what happened and how things can be improved for future crises. To maintain trust and credibility ensure actions communicated during the crisis are implemented or inform stakeholders that based on their feedback and reality, better ways of working have been identified and implemented.
The importance of trust
Demonstrating trust should be a core part of BCP and crisis management. Research by the US based “Center for Food Integrity” demonstrates that trust is driven by three factors: Confidence – Shared values “Do I listen to what stakeholders are saying and share the same values? e.g. commitment to food safety; safe ways of working in the petfood plant” Competence – Skills and abilities “Do we have the skills and ability to produce safe, legal, nutritious petfood of the quality expected by customers, especially if there are staff shortages?”
Influential others – Other stakeholders e.g. consumer groups, regulatory authorities, governmental institutions “Do we actively engage with and listen to what stakeholders are telling us and act on this? e.g. emergency legislation / guidelines on social distancing during CV-19”
Trusted petfood is demanded by stakeholders (customers and regulatory authorities). How do we ensure this if faced with staff shortages because of the crisis?
Although challenging during a crisis, we must recognise that trust takes a long time to build but can be destroyed in a very short time. What happens if consumers lose trust in your ability to supply safe petfood but your competitor has been more proactive to reassure customers and maintain trust?
Practical experience from the Italian food industry on ensuring continuity of food supply during CV-19
Dr Paola Cane (Product Compliance Specialist and Crisis Manager) is Owner of Mia Solution in Italy and has guided the Italian food and petfood industry on their response to CV-19, to ensure continuity of food and petfood supply during the crisis.
Survival in a crisis, like CV-19, requires positive reassurance to maintain customer trust through pragmatic steps ensuring food safety, business reputation and productivity. This requires agility to act on limited, changing information, strong leadership, clear and coherent communication. Key considerations from Dr Cane’s guidance include: No time wasting – In any crisis, information flow changes, requiring fast data collection and analysis enabling risk-based decision making on a dynamic basis e.g. temporary raw materials shortage requiring formulation change might have long-term impact e.g. switching raw material type / supplier might mean their “normal” supplier goes out of business.
Awareness of regulatory / government guidance and
requirements – As the crisis evolves, it is likely that external guidance might change e.g. worker safety, label declarations, product testing etc. This requires a designated person to monitor and communicate this and as part of a team to implement new requirements e.g. use of PPE, social distancing etc. Clear, lucid analysis – Role playing / situation analysis in the planning phase can model the impact of enforced changes e.g. what if your contract laboratory shuts due to illness? This should cover all areas of manufacturing: People (absenteeism; training etc); Product (raw materials e.g. critical raw materials from a country without transport links; finished product); Plant (engineering spares e.g. critical extruder spares) and Processes (procedures, food safety and quality management systems; ways of working e.g. reduced workforce etc). Remote working – What opportunities are there for remote (home office) working? Is IT and communication infrastructure adequate for home working e.g. video conferencing? What about potential negative HR impact on workers e.g. production operators cannot work from home but office workers can stay
Adifo develops and services sector-specific software tools for the international nutrition industry. We enable you to gain maximum control over your core processes and guarantee the protection of critical business knowledge.
www.adifo.com
What are you still waiting for?

8 reasons to choose BESTMIX software for PETFOOD
• Take the right purchase decisions: which raw materials, when and at what price • Meet marketing claims (non-GMO, gluten free, …) from recipe development to declaration • Guarantee the best quality at optimization level, through the optimal management of moisture loss during the extrusion • Avoid adapting your packages by formulating recipes according to label declarations • Retain an overview over the different production stages thanks to the multilevel product design • Avoid recalls by integrating quality control from the intake of raw materials to the delivery of the final product • Generate dietary guidelines for packages in a controlled way • Compare the calculated nutritional quality of the recipe with guidelines (AAFCO, FEDIAF, NRC, …) Request more information on our new website: www.adifo.com
safe at home? Leadership and training – Leadership helps relieve anxiety through the crisis. Training on new ways of working and reasons for ensures compliance and reduces stress. Update staff – Provide a designated person to receive feedback, give good news e.g. sales position and provide regular updates to staff on new ways of working e.g. social distancing and shift pattern changes. Communicate, communicate, communicate – Regular, open, consistent, transparent internal and external communication to reassure stakeholders on how the business is dealing with the crisis but do not over-promise on what will be done as this can undermine trust. Re-evaluate company policies and working practices – Engage with staff to get feedback on existing policies and help shape new ways of working. Some UK food service businesses are enabling greater customer satisfaction and increased sales through changed business models and business efficiencies from CV-19. Predict absenteeism – As seen in many countries, staff shortages are one of the greatest risk factors in ensuring continuity of food supply. Reinforce the steps taken to ensure worker safety e.g. PPE, personal hygiene, social distancing and that they are “key workers” ensuring supply of petfood.
“It will never happen here” kills people and businesses.
Nobody likes talking about the tragic consequences of war but this helps businesses develop preparedness and mindfulness against future crises by teaching us about “complacency bias”.
Failure to detect incoming threats e.g. enemy submarine torpedo attack, resulted in large loss of shipping and lives in World War 2 and highlighted the importance of detection systems. To reduce the risk WW2 warships were equipped with Asdic and radar detection equipment. Imagine you are operating this equipment and do not detect any incoming threats, day after day.
This leads to “complacency bias” a belief that you will not be attacked. One day this “It will never happen here” behaviour results in not detecting an incoming torpedo which sinks your ship killing many people.
This complacency bias illustrates how we can fail in our future threats horizon scanning and are ill prepared when a crisis happens. To mitigate against this, we need to build vulnerability assessment into our crisis management planning (BCP). For example, CV-19 has identified many vulnerabilities including:
Raw materials supply and quality risk management – Generally we benefit from “open borders” and freedom of trade but CV-19 raised the threat of some countries banning food exports to protect their home market. Any resulting shortages increase risks of quality failure and food fraud, where ingredients fail to meet “normal” standards. What are your raw material risk management systems and how can they operate on a remote basis? Staff shortages – CV-19 illness has resulted in food supply chain staff shortages and vulnerabilities that affect ability to supply petfood including:
o
o
o Shortage of drivers in logistics supplier Abattoir closes due to staff shortages Training temporary labour to work safely and to the expected
o standard
Multiskilling within our workforce to enable flexibility in the jobs they do Contract services – Our pre-requisite program might fail putting food safety at increased risk e.g. How do we ensure food safety and production if our contracted-out services e.g. maintenance, laboratory, hygiene, and pest control etc are shut or working at reduced capacity? Food fraud – Recent (May 2020) incidents of adulteration of human meats with horse meat highlights that fraud of all types increases during a crisis. Not all food fraud causes a food safety issue but results in loss of consumer trust. Are our food fraud systems (VACCP) up to date and do we have appropriate controls in place?
Taking positives from a crisis to increase preparedness for future crises
Nobody wants a crisis, due to economic and societal costs but experience from crises like CV-19, earthquakes and Ebola helps us to prepare for the next crisis. In general terms, survival is improved when we learn and develop these key attributes: Preparedness - including horizon scanning and vulnerability analysis Agility Leadership Communication
In a famous quote attributed to Darwin,
“It is not the strongest of the species that survive, nor the most intelligent, but the one most adaptable to change.”
The question is, “How well prepared are you for the next crisis?”
About the authors
David Primrose, Managing Director of Synergy Food Ingredients Ltd, is a petfood industry technical consultant specialising in raw materials development and quality risk management to ensure compliance with legal, food safety, quality, and authenticity requirements. www.sfi-ltd.com
Paola Cane, Ph.D., CEO of Mia Solution, is a regulatory and marketing senior advisor and author, expert in compliance issues, product recalls and product safety crises. www.miasolution.it