
5 minute read
Bongaards
from Progress 2021
by Perham Focus
THE PRODUCT THAT MUST KEEP CURDLING
With a desire to protect employees and as sales were down, Bongards continued processing milk.
The start of the coronavirus pandemic carried a “tremendous decrease in sales” with a 50% decrease from the end of March to the beginning of May, Bongards Creameries President and CEO Daryl Larson shares. The hit followed a recent 10% increase.
By the end of 2020, a small decline in sales compared to 2019 still existed in the value added cheese products, which largely serve restaurants and schools. The sales decline is the first in over a decade, according to Larson and Director of Marketing Evan Carlson. The company has otherwise seen doubledigit sales growth for the past five years. Bongards also sells products in the areas of food processing, convenience stores, delis, and internationally. While experiencing a decrease in revenue, Bongards found itself, along with industry after industry, stretched with high costs for personal protective equipment. At the plants, additional locker and break rooms, masks and thermometers emerged as needs for the safety of employees. “It’s necessary in order to fight the pandemic and keep our employees and their families healthy and safe,” Larson says, “but there’s tremendous cost involved.” The cleaning of the plant and the milk tankers coming in daily was no new change, though. Larson says, “Dairy plants inherently are … clean and sanitary, they’re cleaned up very, very frequently, in some cases every day, but we redoubled our efforts there with cleaning and sanitizing” in the common areas.
Stacks of ways to protect employees rolled out day after day in March.
Joe Nelson works on the block packaging line at Bongards. Submitted Photo
As restaurants and schools had to move to new models, the cheese sales weren’t there.
Larson says, "It really was pretty devastating to our mostly food service and K-12 business.”
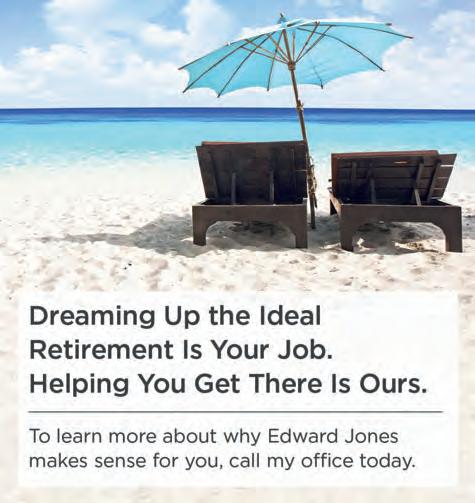
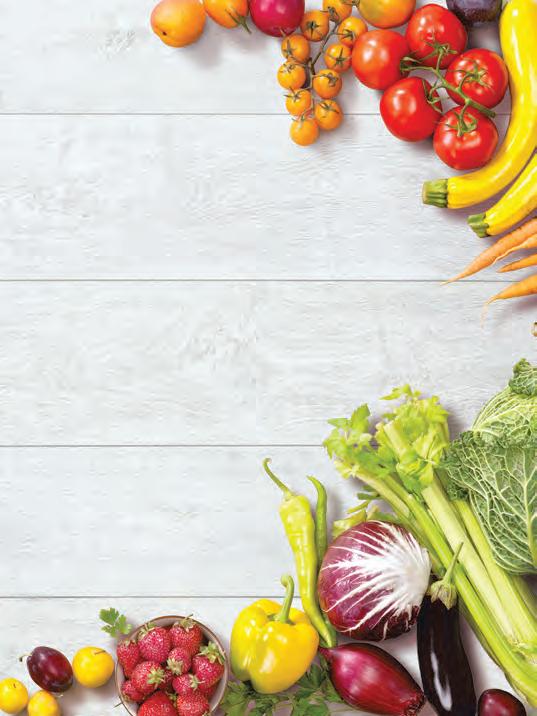
*NOW OFFERING ONLINE SHOPPING WITH CURBSIDE PICK UP. CHECK IT OUT AT SERVICEFOOD.COM
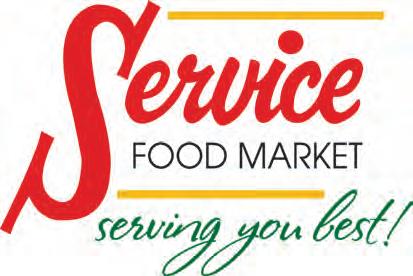
FRESH PRODUCE PREMIUM MEATS DELI & BAKERY WE BAG & CARRY-OUT 250 E MAIN ST Downtown Perham 218-346-7800
Conference calls reviewing the situation formed into decisions intended to limit the spread of the coronavirus from employee to employee and from employee to family members. The enjoyment of being near co-workers during a quick break or lunch time disappeared with the addition of more break rooms for the ever-present need of social distancing.
“Anything we could do to keep someone that might … possibly have the virus from infecting our employees and our facilities we did, basically,” Larson remarks.
The decisions come with the guiding roadmap of “very, very critical” guidelines from the Centers for Disease Control and Prevention and the Minnesota Department of Health as well as employee ideas on safety, as Larson notes.
The protections have included 91 different items as of December 2020. The previously common practice of having sales team members travel to visit customers and other plants across the U.S. was halted due to the risk of spreading or being infected with the virus. Even travel between the three plants in Perham, Bongards, Minn. and Humboldt, Tenn., has been suspended since March 2020.
“We didn’t want to either take something to one of the three plants or catch something at one of the three plants and contaminate our other facilities or our offices,” Larson explains.
The Perham cheese plant kept on curdling cheese, though the processed cheese plants in Bongards and Humboldt had weeks of production reduced with the decrease in sales. The Perham plant produces natural cheeses and whey.
The company also prepared for a possible shutdown: employees trained to be sent to another plant and extra employees were hired. The production line saw increased flexibility with about six additional employees. This way, if employees needed to quarantine or became sick themselves, people were ready to step in and the plant could keep on producing cheese.
The employees keep the plants running, and the employees need the plant to keep running for a job to have. And while the mandatory masks starting in April come as a “not very popular decision” in the warm factory environment, Larson emphasizes the health and safety aspects help keep the plant operational.
“In a lot of cases they don’t like it because it is uncomfortable and it is cumbersome, but they have stepped up and followed … the things we put in place and worked extra hours when we had people that were out for COVID exposure or just normal time away from work,” he says.
With fellow manufacturers in town having similar requirements, Larson says, "There wasn't a lot of, ‘Well why do you make us do this when down the street they don’t have to?’”
The Bongards co-op farmer members total 85 tankers of milk a day at the Perham plant, and “that milk has to get processed,” Larson says. If the plant had to shut down, the region would not have the capacity to process the milk and the milk would be dumped.
“We have not missed any production all throughout this ordeal,” Larson says. “We fared a lot better than a lot of people in that respect, and it’s due to our employees doing what we’ve asked them to do and more.”
As one of their top priorities, Carlson says Bongards always seeks a place for farmers’ milk to go with operations running as smoothly as possible.
“The fact that we are a multi-plant company is a big benefit,” Larson says. “We have the ability, if needed, to take employees from the other plants and have them assist us in Perham to make sure we continue to run that milk that’s going to spoil in two or three days if it’s not processed.”
Throughout the pandemic, the contingency plans have sat shelved. The plans include a list of employees who are willing to come to Perham and run the plant. Larson says he believes it’s a list they won’t need. But until the pandemic subsides, Bongards will keep that plan at the ready.
The Perham Bongards has not missed any production due to the coronavirus, a feat company leaders attribute to its employees following all health and
safety rules. Submitted Photo
