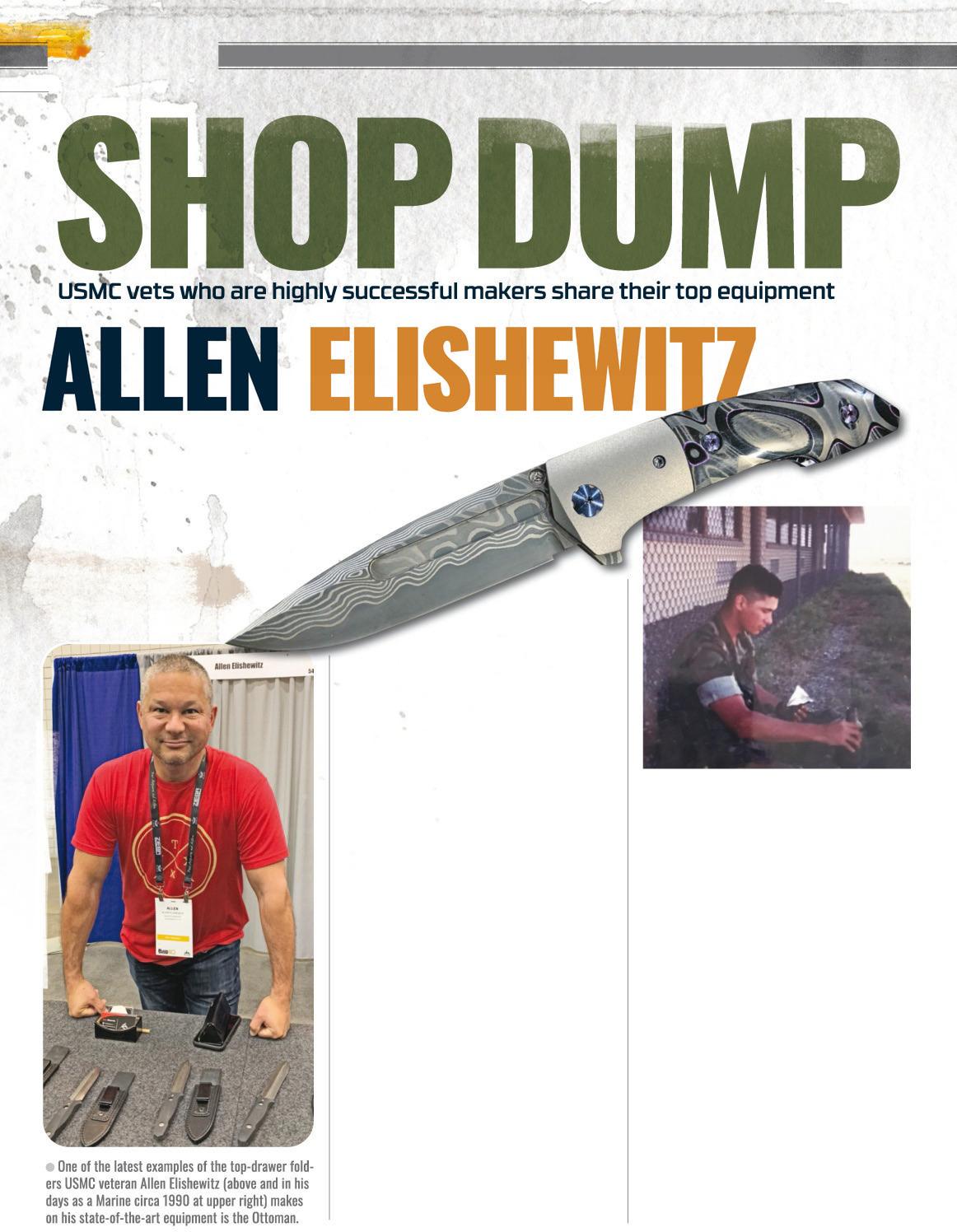
8 minute read
SHOP DUMP
Editor ’ s note: In addition to being an award-winning knifemaker, Allen Elishewitz is a veteran of the United States Marine Corps. A sergeant in 4th Recon Charlie Company, he and his company were eventually activated and deployed during Operation Desert Storm. However, by the time he got to Iraq, the war was over so fast he was out of there before he saw any action of real note. He was kind enough to write the following in-depth review of his top knifemaking equipment.
To be a true
Advertisement
“handmade ” knifemaker, you need a quality saw. It must be rigid and precise for control and to cut precisely.
A quality saw also will help the blade last longer. I add a coolant system to my saw which can almost double the life of the blades. I cut everything from steel, titanium, bronze, carbon fiber to wood on my Enco bandsaw. I bought it new in 2001 and it’ s never let me down. Nothing has ever broken on it and I made my money back within the first few months of buying it.
I bought my drill in the south of France from a used machine dealer in 2001. It is an Aciera 23 jig bore/milling machine. At the time it was developed in the 1980s it was very expensive, and an ordinary machine shop never had something this sophisticated and expensive on the floor. The cross table was made by Fehlmann, a Swiss company legendary for its precision drills and cross tables. I use the machine primarily for drilling because I’ m able to transition from one drill bit to another very quickly. On occasion I use it for milling.
I have owned many grinders throughout my 35 years of knifemaking. The Hardcore QC is by far the finest grinder I have ever owned. It is extremely smooth, quiet and very rigid. Because there are no vibrations when I grind, I don ’t get any stray deep scratches. I have all the accessories available for it and they enable me to have a vertical, horizontal disc grinder, as well as the flat-platen small wheel. The tool rest is quite rigid and adjustable. Switching from one accessory to another is very quick and easy. I grind everything from steel, wood, carbon fiber and titanium on the Hardcore QC.
The Aciera F3 is a Swiss mill I bought in England. It is a very small but highly precise milling machine that is sought after by horologists—makers of timepieces. I use it for most of my small machining operations because it has a highspeed head that goes up to 7,000 rpm. The beauty of this machine is it is small, compact and modular. I can remove the head and attach a different one. I have
a slotting head, a horizontal head and a mill head in addition to the high-speed one. The table swivels and is removable, and can be replaced with different types of tables for various operations.
The Deckel GK-21 pantograph allows me to duplicate parts from a pattern. It provides the ability to choose different-size ratios and it has a variety of cutter speeds. This machine or something similar was very common in knife shops that were pre-computer numerical control (CNC) and numerical control (NC). A pantograph allows the duplication of parts easily. I use it to profile liners to maintain a consistency within a particular model. In the past I’ ve also
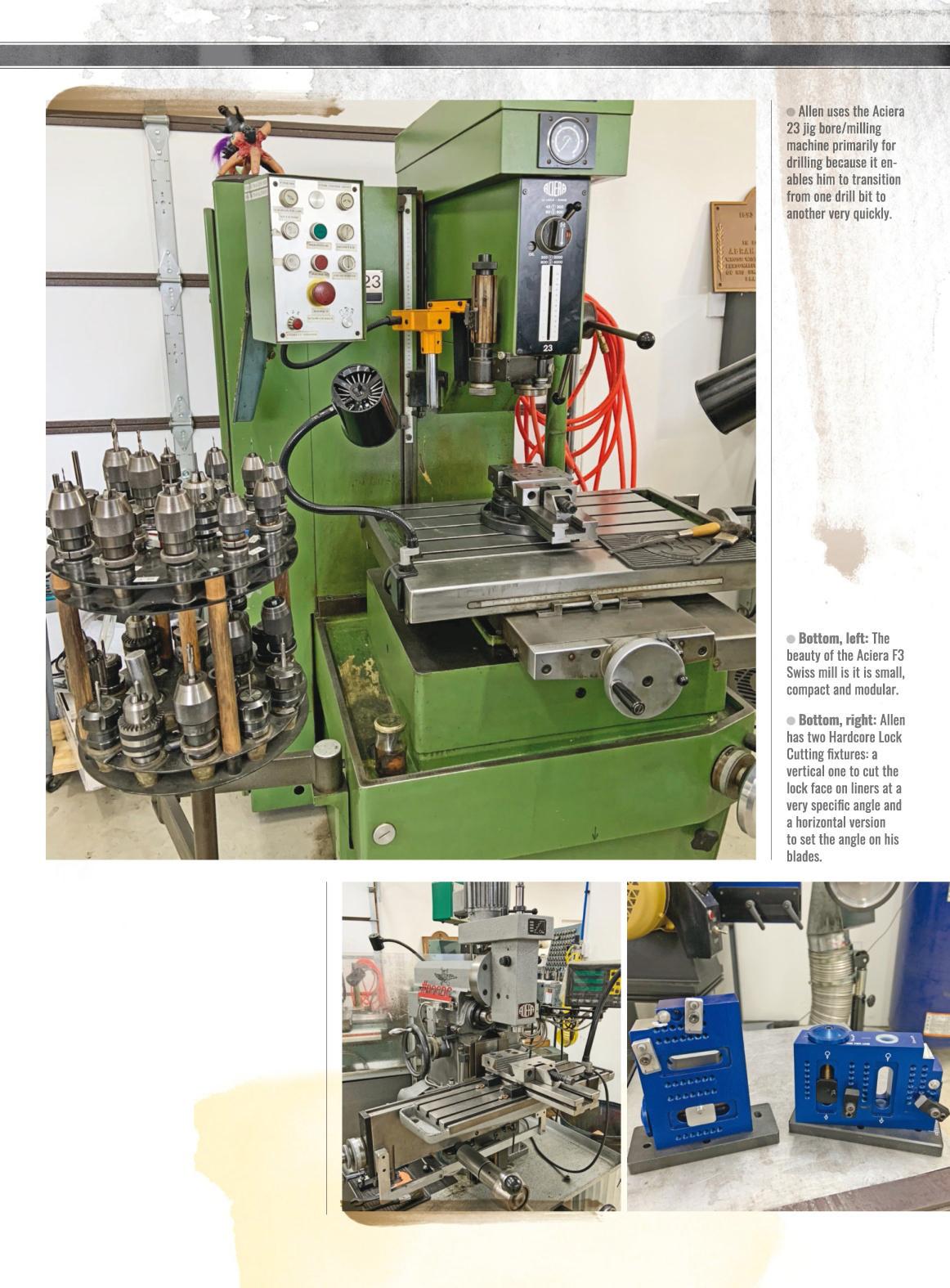
made inlays, complicated bolsters, and fancy blood grooves and decorations using this machine. I bought it 10 years ago from a guy who had it in a barn and wasn ’t doing anything with it.
I bought my Jones & Shipman 540 toolroom surface grinder from a machine dealer in Rhode Island about eight years ago. It is very compact and fully automatic. It is extremely precise and I use a stone instead of a belt like many other makers. The stone gives you a more precise surface. The finish I get off this machine is almost a 600 grit. It is very slow for surface grinding parts, so I may be standing there for a while. Since the machine is automatic I can do something else while it’ s working, though it is far from being CNC so I still need to attend it. Surprisingly, it is one of the heaviest machines in the shop and movers are always surprised because they think it is lighter.
One of the most important tools in my shop is the Hardcore Lock Cutting fixture, available from Hardcore Grinders. I have two of them set up vertically and horizontally. I use the vertical one to cut the lock face on liners at a very specific angle. I use the horizontal version to set the angle on my blades. These jigs enable me to shave off thousandths of material at a time and adjust the angle as needed.
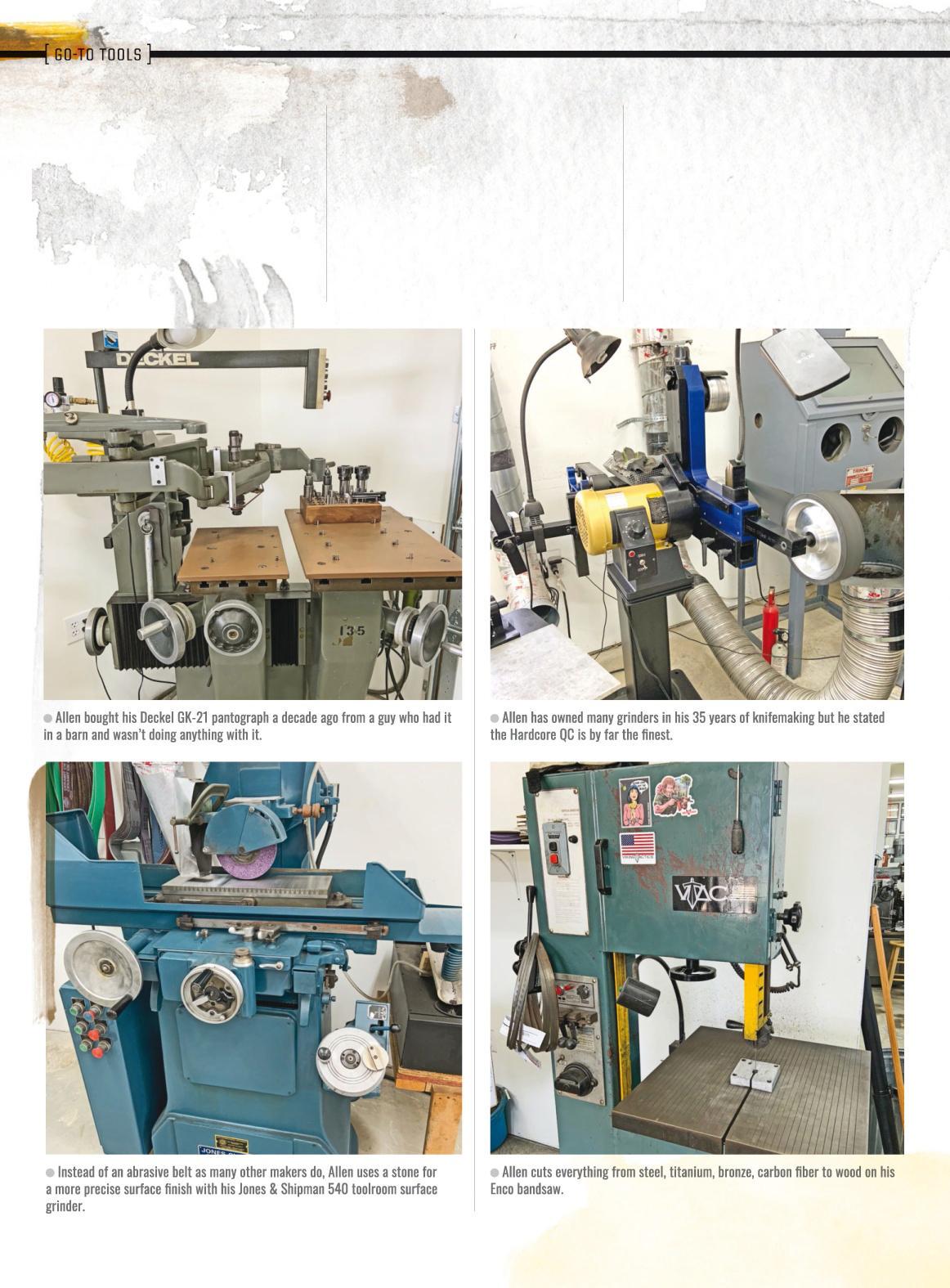
Long-time knifemaker Tim Britton joined the United States Marine Corps in 1959, serving in Force Recon and as one of a very few USMC combat divers. He survived one particularly harrowing assignment helping rescue Army Rangers from an airport under heavy enemy fire in the Dominican Republic.
“We Marines came to their rescue in our Hueys. Insanity prevailed, ” he recalled. “Kids were trying to sell us ‘tortas ’ [sandwiches] while we were trying to avoid snipers. The smell of blood and other body fluids still gives me the shakes. ”
He caught the knifemaking bug in 1972 when he saw knives made by BLADE Magazine Cutlery Hall-Of-
Fame® member Blackie Collins at a Charleston, South Carolina, gun show. Other of Tim ’ s influences include Blackie ’ s brother, Michael, as well as Cutlery Hall-Of-Famers George Herron and Frank Centofante, and also Steve Fecas, Tommy Lee, Paul Fox and Howard Viele, to name a few.
Tim ’ s go-to machines are many and varied. His belt surface grinder came from a U.S. Navy surplus auction in Hampton Roads, Virginia, in 1974. “Knifemaker Richard Bridwell made the conversion for me in pursuit of what Jim Crowell claims to be the three most important elements of knifemaking—flat, flat and flat, ” Tim wrote.
Embellishing the flat theme is his 6x48-inch Craftsman belt sander. “It’ s vitally important for flattening scales for knives, ” he noted, and includes a quarter-inch steel plate welded on the surface to ensure “flat. ” Tim got it as part of a trade with Blackie Collins in 1973.
Another machine with a Collins pedigree is Tim ’ s 2x132-inch Bader Space Saver belt grinder. “It was originally sold to Michael and Blackie for use in their
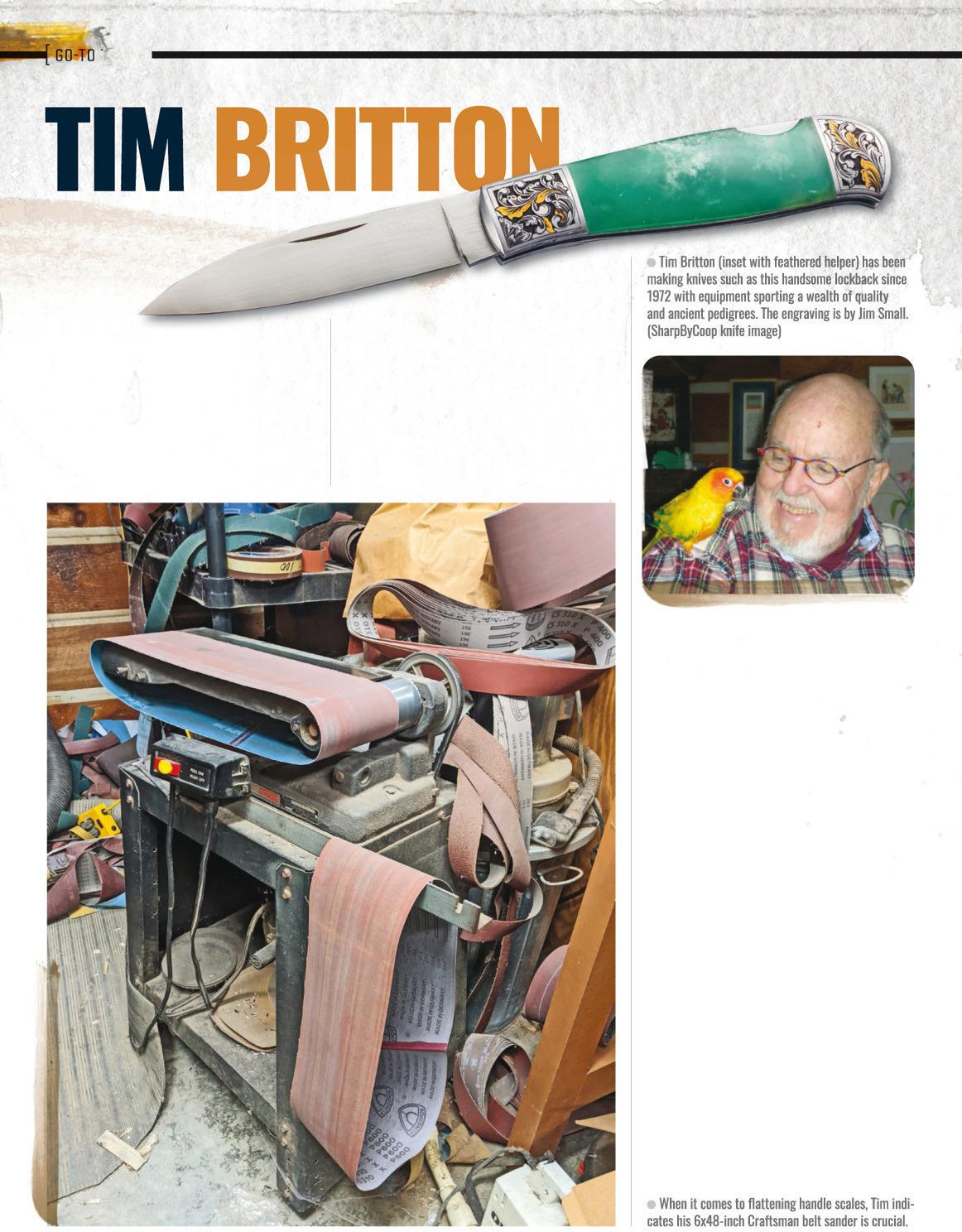
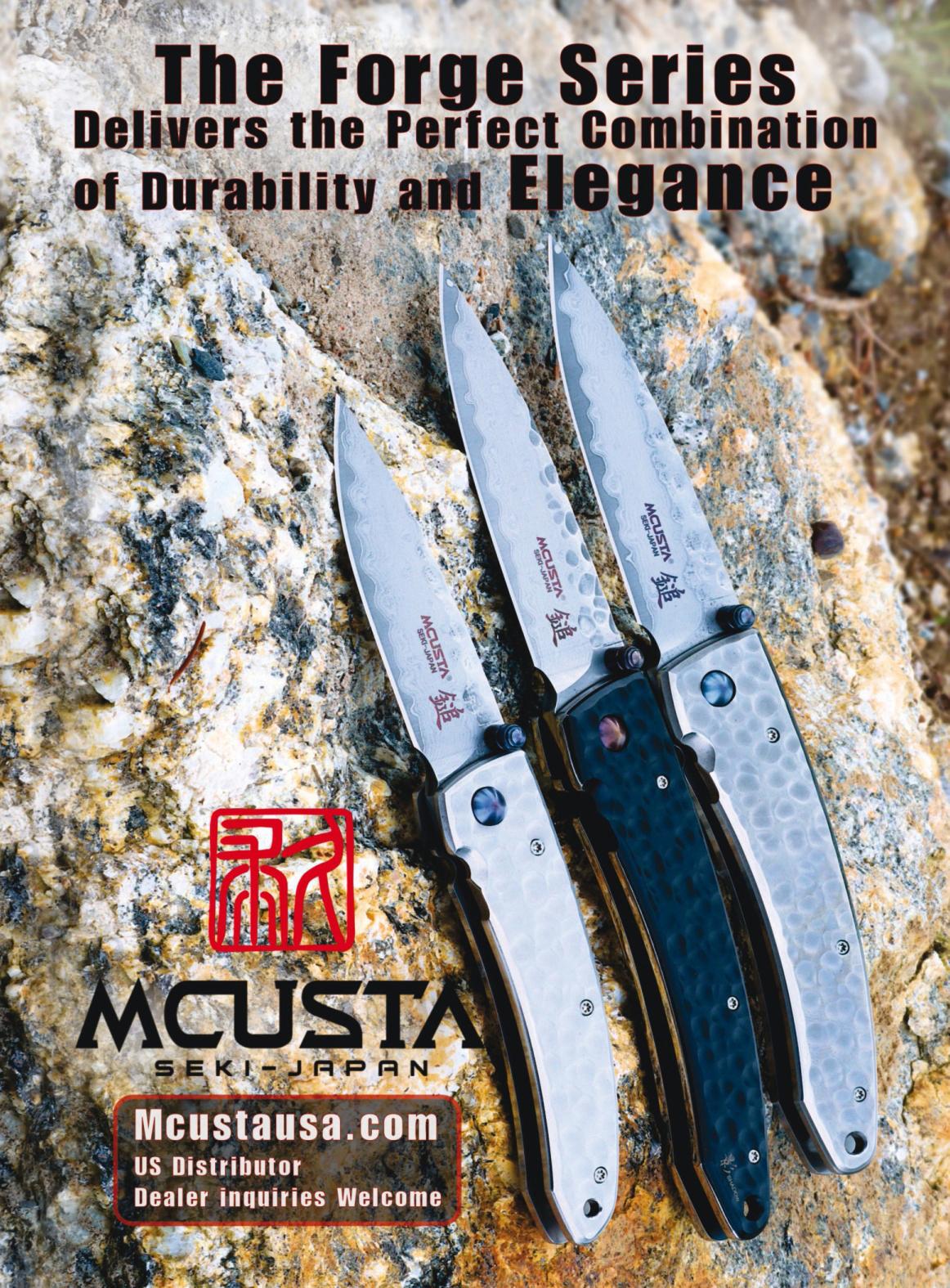
knife shop in Underground Atlanta at least 50 years ago, ” he wrote. “It’ s an awesome machine for grinding handles and blades. ”
Three other “ ancient” Navy surplus items are Tim ’ s Detroit Flame Hardening surface hardness tester, De-Sta-C clamp set and monster Porter Cable disc sander. The former includes a glass tube with an enclosed ball. How high the ball bounces in the tube gives a rough measure of Rockwell hardness up to 65 HRC. The clamps are “1940s era ” and Tim uses them on every knife he makes.
The 21-inch Porter is also World War II Navy surplus. “The tag on the pedes-
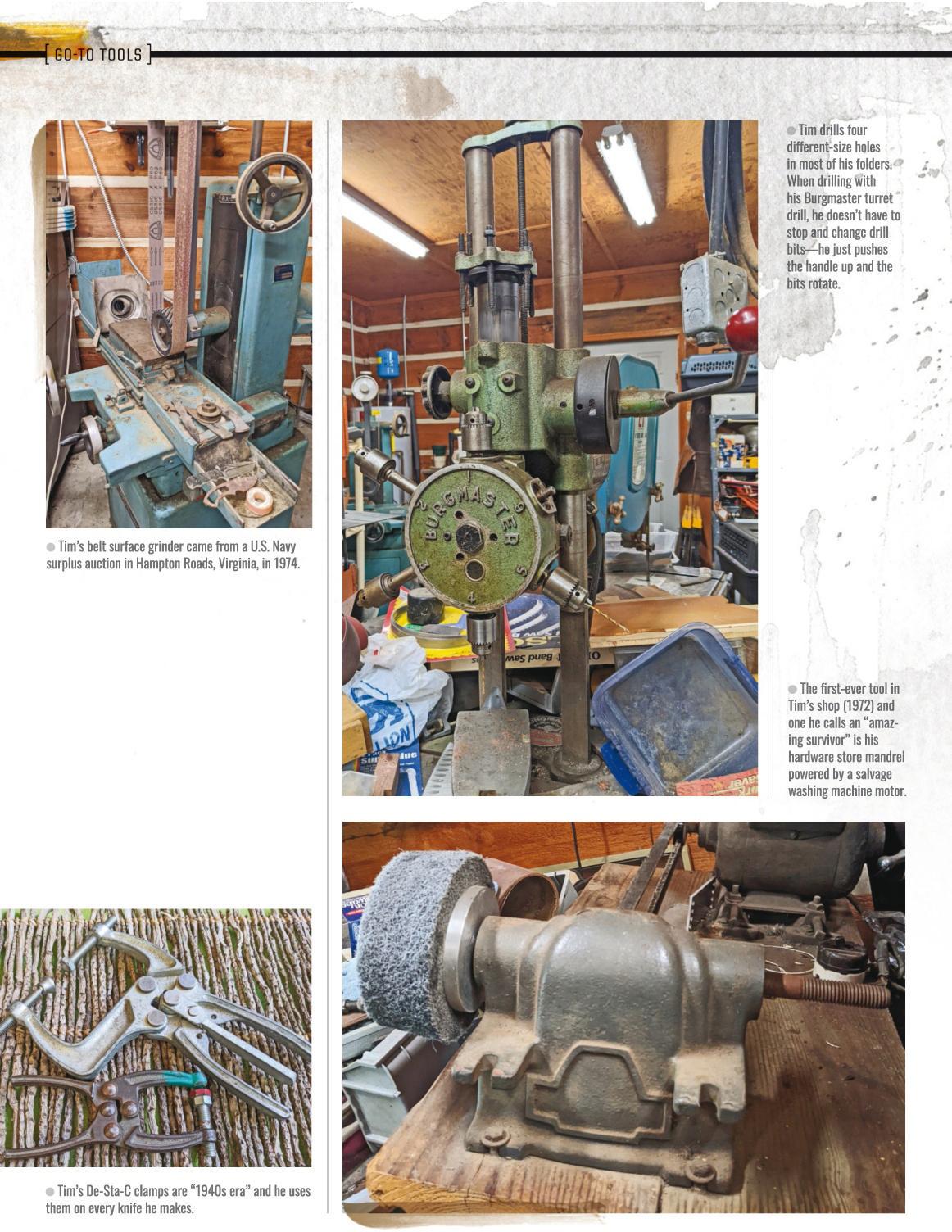
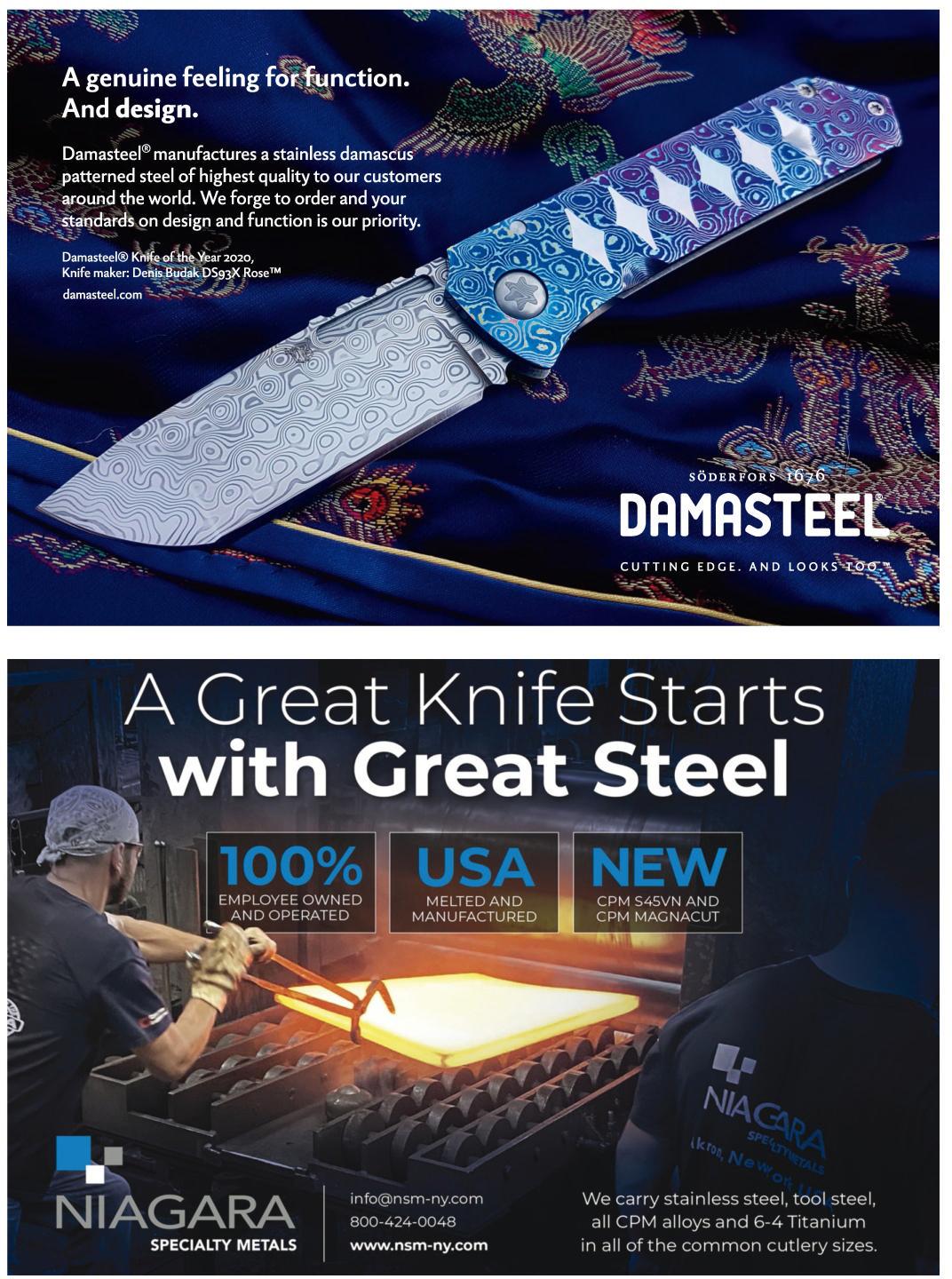
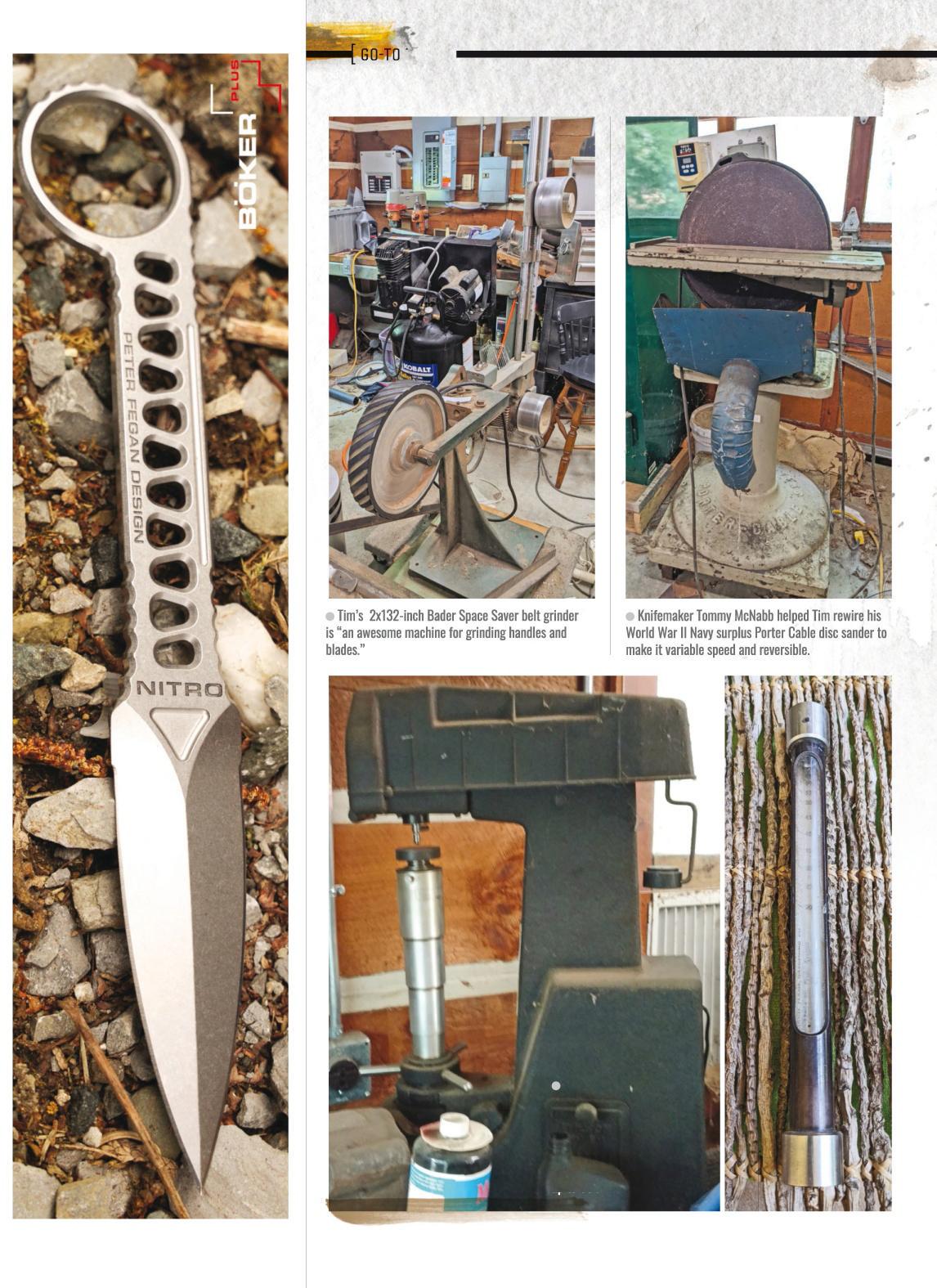
Tim’s “ ancient” Navy surplus Detroit Flame Hardening surface hardness tester includes a glass tube with an enclosed ball to indicate Rockwell hardness up to 65 HRC.
tal reads USS Achernar 53* , ” Tim wrote. “Tommy McNabb and I did some rewiring and it’ s now variable speed and reversible. I use it to grind all my folder blades. The machine and base must weigh 200 pounds. I use a piece of toolbox liner between the metal disc and the abrasive disc. It makes it much more ‘forgiving. ’”
The first-ever tool in his shop (1972) and one he calls an “ amazing survivor ” is his hardware store mandrel powered by a salvage washing machine motor. “I’ ve used two Norton fine Bear-tex wheels for 40 years!” he exclaimed. “Norton designed them for de-burring. ”
Rounding out his top tools are his Wilton metal-cutting bandsaw, pantograph mill and Burgmaster turret drill. The former is at least 40 years old and “ a workhorse, ” and Paul Fox designed and built the pantograph. “We used this together for 15 to 20 years, ” Tim wrote of Fox. The monster arbor is from an IBM shop sale and the table moves on Thompson bearings.
As for the Burgmaster, Tim ’ s had two—a compact model and another “the size of a Bridgeport mill. No question, it’ s the most important tool in my shop. ”
*Editor ’ s note: USS Achernar AKA-53 was an Andromeda-class attack cargo shop launched Dec. 3, 1943, designed to support amphibious warfare operations of the U.S. Navy during World War II and thereafter. She served as the command post of Gen. Omar Bradley, commander of the U.S. First Army, for the D-Day invasion of Normandy, June 6, 1944. She also saw action during the Korean War.
For the contact information for the makers in the story, see “Where To Get ’Em ” on page 47.
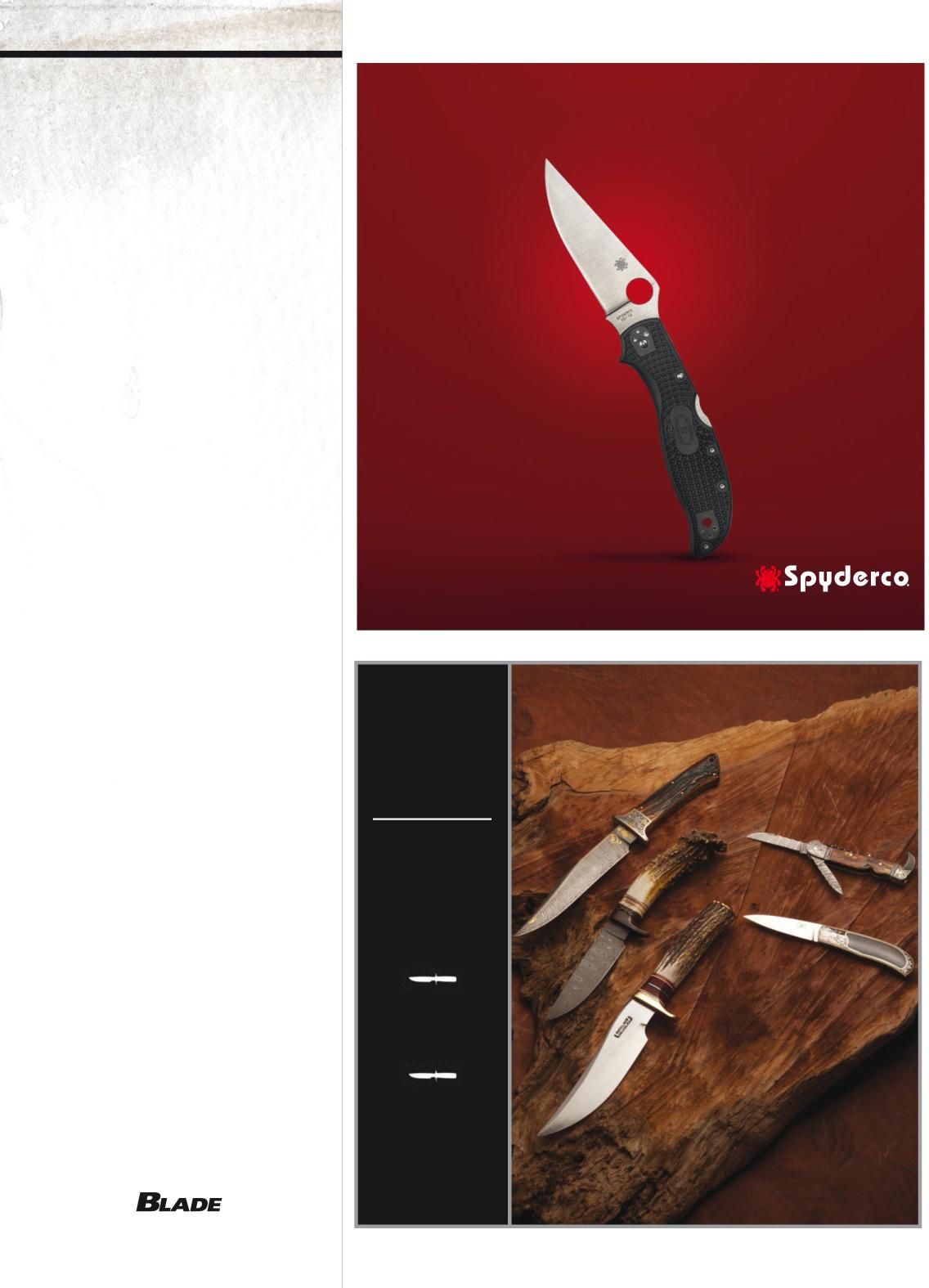
For the latest knives, knife news, trends, and more, visit blademag.com, BLADE®’ s popular Instagram page @blade _ magazine, and on Facebook and Twitter.
SIZE DOES MATTER...
SO DOES WEIGHT, EXPERIENCE, and PERFORMANCE...
Luckily, the
StretchTM 2 XL has it all.
Delivering extra-large-sized cutting performance in a package weighing less than three ounces, the Stretch 2 XL Lightweight is the pinnacle of almost 40 years of design evolution. spyderco.com 800 525 7770
NORDIC KNIVES
See our Gallery on 8th Street, Boise, Idaho
Featuring the finest in Custom & Randall knives since 1971
We buy, sell & consign entire collections
Buy with confidence, your satisfaction is guaranteed