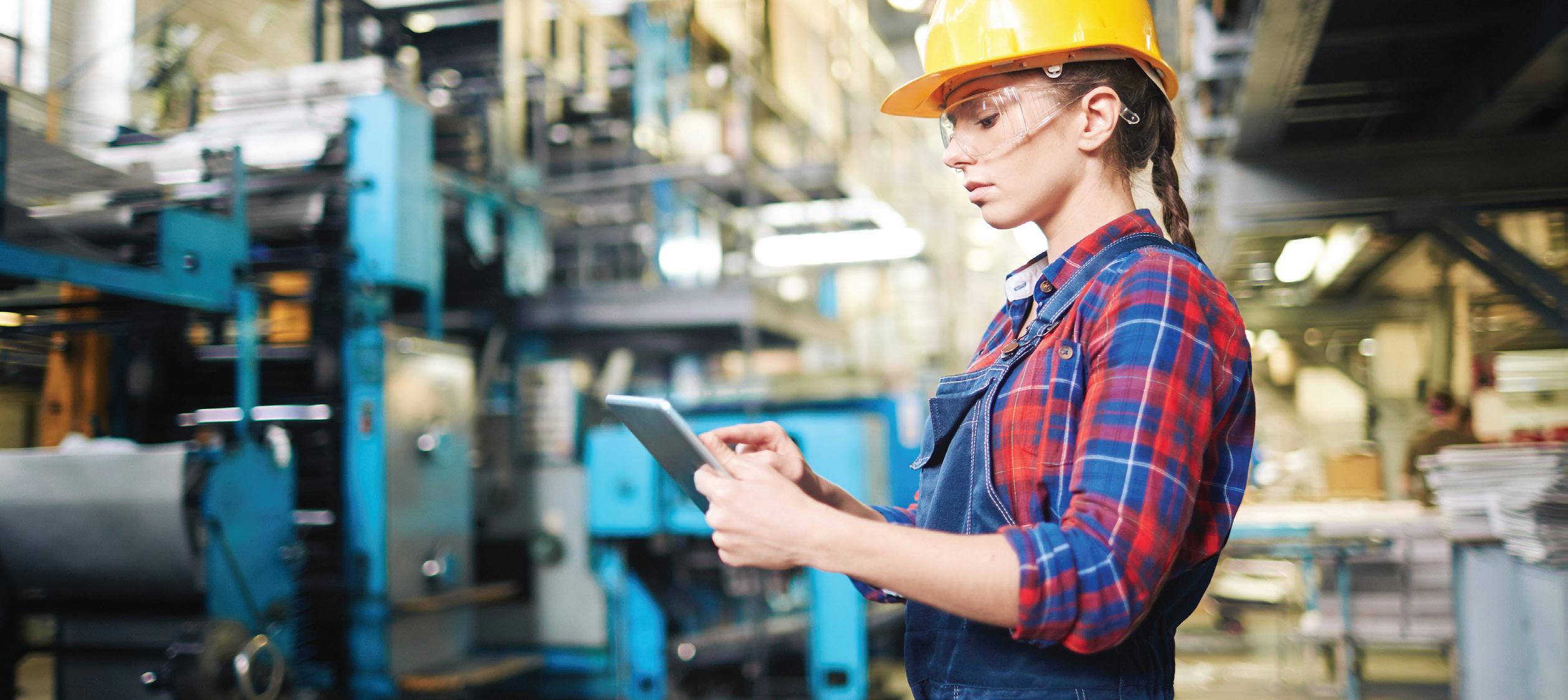
7 minute read
Outlook
Reshore or Not?
By Hallie Forcino, writer, Inside Rubber
With rising costs and the supply chain disruptions caused by COVID-19, the idea of reshoring is gaining momentum.
In 2021, the private and federal push for domestic supply of essential goods propelled reshoring and foreign direct investment (FDI) job announcements to a record 261,000, bringing the total jobs announced since 2010 to more than 1.3 million, according to the Reshoring Initiative 2021 Data Report: Essential Product Industries Drive Job Announcements to Record High, a report published by the Reshoring Initiative, Sarasota, Florida.1
For the second year in a row, reshoring exceeded FDI by 100%, in contrast to the 2014 to 2019 period when FDI exceeded reshoring. Additionally, the number of companies reporting reshoring and FDI set a new record, with more than 1,800 companies. Reshoring was the key to the US manufacturing and economic recovery in 2021 and is expected to remain strong in 2022.
“We publish this data semiannually to show companies that their peers are successfully reshoring and that they should reevaluate their sourcing and siting decisions,” said Harry Moser, founder and president of the Reshoring Initiative. “With five million manufacturing jobs still offshore, as measured by our $1.1 trillion/year goods trade deficit, there is potential for much more growth,” he added.1
The idea of bringing manufacturing back from overseas appeals to national pride; counters increasing costs offshore; minimizes risks related to lack of domestic production, geopolitical uncertainties and currency fluctuations; protects intellectual property; shortens supply chains and eliminates quality issues and communication difficulties.
Why reshore now?
Labor rates are moving up internationally, narrowing the gap between domestic and offshore prices – although higher US labor costs still result in US manufacturing costs being, on average, 40% higher than in China and 10 to 15% higher than peer countries. Tariffs have risen.
Perhaps most importantly, “international supply chains have proven to be less reliable in the last decade, particularly since the pandemic, and with shortages of both equipment (containers and trucks) and labor, logistics complications have increased risks,” said Tom Rimel, president of Stockwell Elastomerics, a Philadelphia, Pennsylvania-based supplier of specialty components.
“We have had a consistent strategy to produce only in North America, and 95% or more of our raw materials are North American sourced (and always have been),” reported Rimel. “Our components are relatively small in size and specialty (high value in use) so that labor rates and transportation costs (in the markets we have selected to serve) have never been the primary decision factor,” he explained.
“Everyone is excited about buying American again,” noted Richard A. Balka, president of The Home Rubber Company and its Ivanhoe Rubber division. The manufacturer of hoses, belts, gaskets, sheet rubber and more ships products worldwide from its operations in Trenton, New Jersey.

t page 32
However, the decision to reshore should not be made lightly. Reshoring is an extremely complex endeavor that ties into almost every current political issue – immigration, environmental sustainability, war, inflation, globalization, tariffs and trade deficits.
“Although international logistics problems have shown us that wholly relying on goods and transportation that we don’t control is risky, I’m not convinced reshoring is a sustainable answer,” said Balka. He explained, “As soon as we’re back on normal footing, everyone will return to buying solely on price. It’s a nice thing to advertise you’re selling a domestic product, but very few end users are willing to absorb additional cost. Plus, I don’t believe the US has the capacity to reshore more than a very small percentage of the goods and services needed to drive our GDP. Even if we could build more plants, where are we going to get the people to run the plants? If wages continue to grow, are we as an economy going to be able to be competitive with the rest of the world? If I look at the cycles of the past 50 years, more and more has gone offshore. What is my basis for the confidence to invest huge sums of money on domestic production?”
Successful reshoring
Being competitive is key. “Competitive means price competitive,” stated Moser. To become price competitive depends on automation, workforce development, higher productivity levels, supply chain resilience and governmental action.
Although reshoring may not be practical for every product and service, it does make sense for agricultural products and products that: • Serve a niche • Were developed domestically and are highly engineered • Are produced in a highly automated process • Require minimal secondary operations and assembly • Are expensive to transport due to size, weight or other feature • Have a high freight cost relative to labor cost • Serve critical applications that require a level of quality difficult to duplicate offshore • Rely on raw materials available locally • Are essential to national security • Can improve lead time by reducing transit time/distance
Although neither Stockwell Elastomerics or Home Rubber are reshoring (they never offshored), they are expanding domestic operations to accommodate new business. Home Rubber currently is putting together a significant equipment investment package.
“We are getting sales as a result of import products not landing as quickly as end users need them,” said Balka.
Rimel of Stockwell Elastomerics, reported, “Since January 2021, we have increased labor (employees) by 26%, we have added capacity (seven new pieces of equipment) and have nearly doubled the size of our engineering team to support our customer demand for high-performance gaskets and sealing materials. Five years ago, we also added a third building to our campus to support future growth.”
For manufacturers that want to help their customers reshore, several steps can be taken to ensure a successful transition. First of all, Moser recommends “doing the math.” This means considering total cost of ownership including factory price plus duty, freight, carrying costs and inventory. What investment in infrastructure, equipment, hiring, training, operation and shipping will be required? Can tooling be recovered? Are current prints and process specs in-house? How much time will each step toward reshoring take? Moser advised also streamlining and automating processes. He said, “The old system was not competitive. The new system must operate smarter.”
Implementing higher levels of automation is imperative since it can minimize headcount and help control labor costs. Automation also positively impacts productivity, which Moser said has only increased 0.5% per year for the last 12 years in the US vs. 6% per year in China.
Other recommendations include checking in with existing customers that also rely on offshore production to provide them with a path to bring back business. Moser says it’s important to discuss what-if scenarios like “What happens if China tries to take over Taiwan?” or “What happens if Germany’s factories encounter a shortage of natural gas this winter due to the Russian invasion of Ukraine and related trade sanctions?”
Rimel explained, “With geopolitical risks (China, Russia) seemingly increasing, regional manufacturing strategy and developing additional ‘local’ supply chains reduce risks. These risks are both from logistics (goods being able to pass through hotspot areas) and supply of base/raw materials.”
Once business has been reshored, its essential to tout the success. Public acknowledgement not only proves competitiveness but demonstrates also to employees that the company is stable and not losing work to offshore operations. This knowledge has also a positive impact on potential workers.
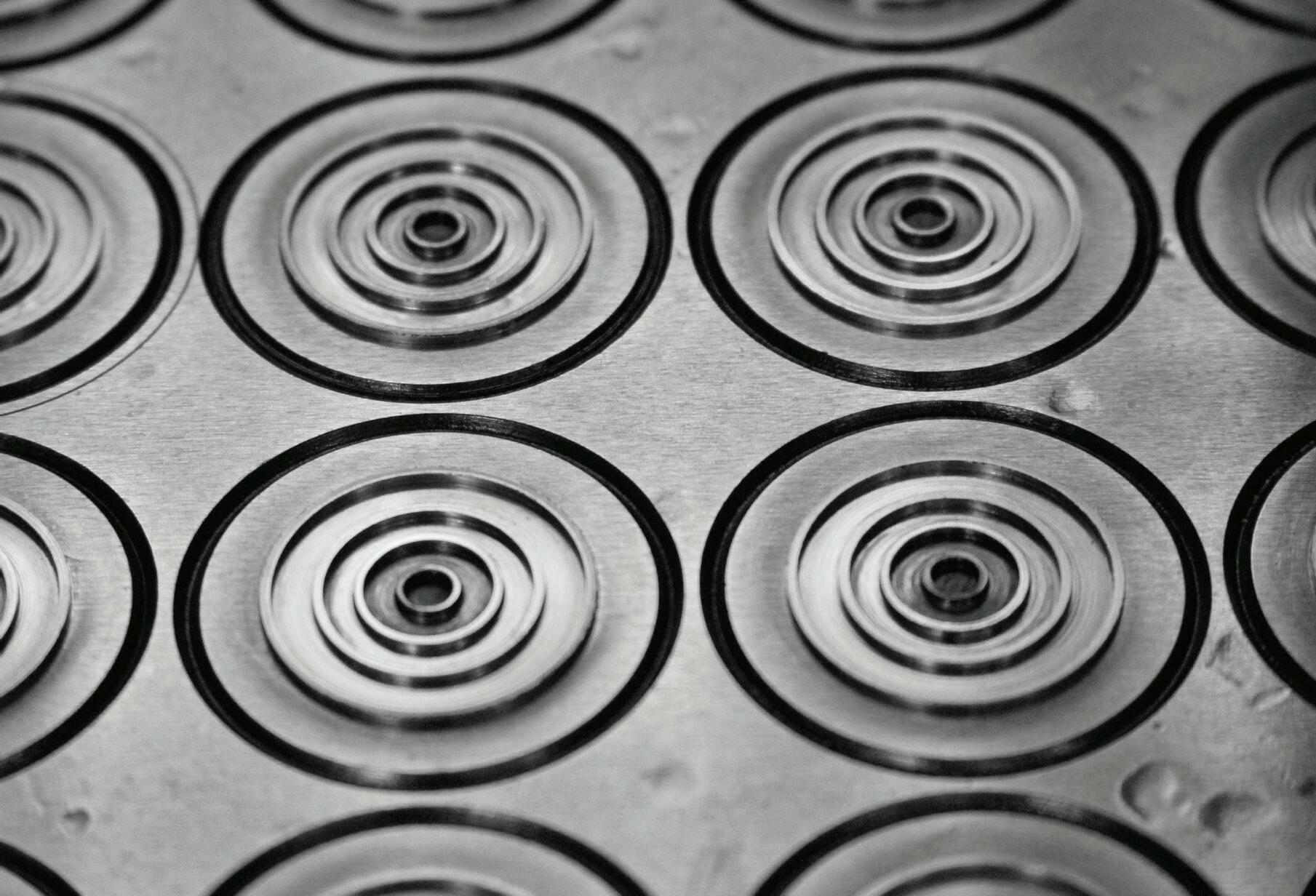
From a national perspective, Moser explained successful reshoring depends on the federal government taking steps to: • Encourage apprenticeships and workforce development • Maintain the current corporate tax rate • Retain 100% immediate expensing for equipment • Establish a value-added tax • Change interest rates in step with global markets • Reduce the value of the US dollar vs. other currencies
Moser concluded, “Reshoring helps the country. It restores the American dream.” u
Resources
1. Reshoring Initiative, “Data Report: Essential Product
Industries Drive Job Announcements to Record High,”
Press Release, May 31, 2022.
LET US DO THE DIRTY WORK SO YOU CAN QUICKLY MOVE FORWARD.
Performance release agents and mold protectors for rubber molding.
Let us help you stay lean and clean.
CHEMTREND.COM
RUBBER IN MOTION
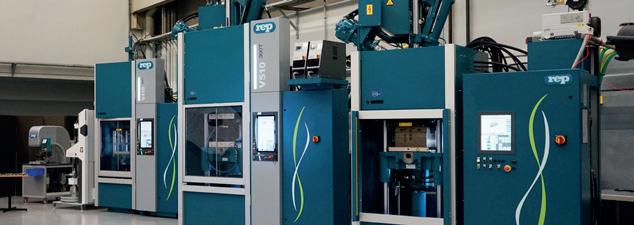
