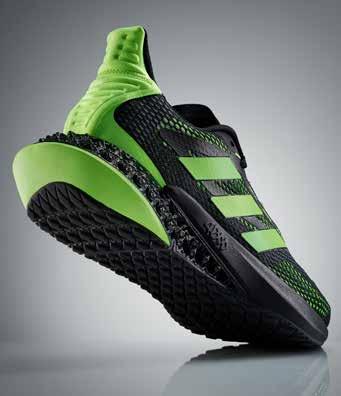
9 minute read
Operations
Elastomers, Lattices and Additive Manufacturing
By Liz Stevens, writer, Inside Rubber
Additive manufacturing (AM), aka 3D printing, has taken hold and is expanding as a viable production method worldwide. While it has primarily been known as a manufacturing method for rigid plastic components, additive technology has applications for the production of elastomeric parts. The recent development and adoption of lattice structures for part design have introduced valuable new capabilities to additive manufacturing, especially for elastomers. With these advances come new opportunities for rubber products manufacturers to consider as they chart their future course of business.
While there is an array of AM hardware platforms, technologies and materials, three types of 3D printers and a handful of materials are geared for use with elastomers. Material extrusion – the printing method that builds a part by extruding from a reel of filament, powder-based printers – including those that work via selective laser sintering technology, and vat polymerization – which uses light to solidify objects within a pool of resin, are the main platforms for elastomers. The materials include digital photopolymers, thermoplastic polyurethane (TPU) and thermoplastic vulcanizate/thermoplastic elastomer (TEP/TPV).
In 3D printing for elastomers and plastics, the concept of lattice structures is the newest idea on the block. Not just new but perhaps poised to be a game changer, lattices call for a fundamental rethink in AM, an adjustment on par with the big rethink that the advent of 3D printing caused in subtractive manufacturing.
In his blog post, “Lightweighting with Lattices,”(1) Timothy W. Simpson, a professor of engineering design and manufacturing at Pennsylvania State, lays out a clear description of lattices and their value in product design and manufacture. “Instead of building components as a solid,” writes Simpson, “building them as a network of unit cells may improve material utilization and performance.”
A lattice is simply a hollow structure with a frame that is made of repeated unit cells. “There are countless options for the size and shape of such a cell and for how it is repeated,” Simpson writes, “and there are a lot of examples of lattice structures being used to provide internal support, reduce the amount of material or improve the strength-to-weight ratio of an AM component.”
The lattice structure in a part can be uniform throughout the part, or the shape, size and spacing of the cells can be varied to provide features and capabilities. “An added benefit of lattice structures is they can be additively manufactured faster,” Simpson writes, “using less material and therefore requiring less build time than fully dense, solid components.”
Lattice structures are finding their way into products far and wide. Oechsler, a German polymer technology group, recently showed off a 3D-printed, lattice structured chair at the furniture fair Milan Design Week.(2) Researchers at UCLA have developed a method for 3D printing an entire minuscule robot in one pass, using lattice-like shapes that give the robot the ability to change its geometry and move in response to an electrical field.(3) The 3D design software firm General Lattice is making waves with its program for
Image, this page: Adidas footwear with midsoles made with Carbon’s EPU 44 elastomer material, a 40% bio-based resin.
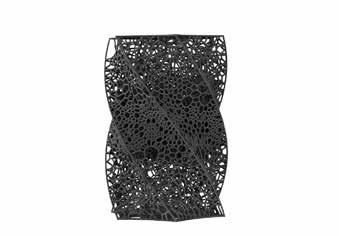
Carbon multi-zone lattice design.
creating complex lattice geometries, and the company has helped the US Army improve the shock absorption of helmets with 3D printing and lattice geometries.(4) Inspired by the 3D printed soles on some of adidas’ running shoes, designer Matt Barnum created the Squishy Mouse, a computer mouse that is 3D printed with lattice structures that conform to one’s hand.(5)
adidas and Carbon – An Example of 3D Elastomer Success
The distinctive midsoles of adidas’ Futurecraft 4D running shoes, which have inspired many a new product, were designed and built in collaboration with Carbon, Inc., a Redwood City, California, 3D printing technology company. The one-part midsole for the shoe, the latest adidas running shoe that utilizes Carbon technology, is made of a stiff elastomer – a blend of UV curable resin and polyurethane – printed in a lattice structure.(6)
Carbon is an industry pacesetter that offers a suite of additive manufacturing hardware, software, materials and training. The company entered the 3D printing business with an interest in leveraging some existing AM materials and processes to greatly expand their use.
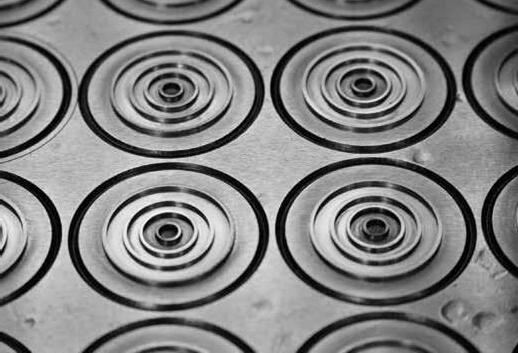
“We asked how do we take additive manufacturing into production applications,” said Jason Rolland, Carbon’s SVP of materials, “and why is additive manufacturing not broadly used as a production technology? The main issues that we identified were printer speed and printer capability, along with materials challenges.” Rolland, a polymer scientist, explained that Carbon was interested in the type of materials used in liquid resin-based systems that operate with patterned UV light (vat polymerization) and the company saw that many of those chemistries were designed for plastics coating applications. For creating its materials, Carbon focused on creating production-grade elastomer materials and targeted the footwear industry as its first industry sector. “We decided on a dual-cure approach,” Rolland said. “We built a platform of dual-cure chemistry by blending UV-curable chemistry into thermally-curable chemistry. That expanded the scope of materials we are able to use in the printer and expanded the range of properties that we can access with a given resin.”
“On the elastomer side,” Rolland explained, “we saw a huge business opportunity for 3D printing. We knew that if we could find a way to make polyurethane chemistries, we would be able to meet the properties required for these products. With our dual-cure approach, we can use high-performance polyurethane elastomers that are a great alternative to the polyurethane foam used in footwear.” The R&D effort helped Carbon land a partnership with adidas. “From there,” said Rolland, “we developed a category of elastomers that are useful for a variety of applications.”
Carbon’s elastomeric materials include EPU 40, a highly elastic, tear-resistant and energy damping material that is comparable to commercial TPUs; EPU 41, a highly elastic,
page 26 u
LET US DO THE DIRTY WORK SO YOU CAN QUICKLY MOVE FORWARD.
Performance release agents and mold protectors for rubber molding.
Let us help you stay lean and clean.
CHEMTREND.COM
t page 25
tear-resistant and energy-returning material (also comparable to commercial TPUs); and SIL 30, a soft, biocompatible and tear-resistant material that is comparable to SEBS TPE. Carbon’s newest elastomer material is EPU 44, which stands out by being 40% bio-based, as well as being highly resilient and tear-resistant.
Carbon offers a line of DLP 3D printers – the M1, M2, M3, M3 Max and L1 – all of which use the company’s high-speed Digital Light Synthesis™ printing process and Continuous Liquid Interface Production™. The printers offer a variety of build volumes, resolutions and print speeds. Carbon’s hardware and software are available on a subscription basis.
In partnering with adidas, Carbon delved deeply into the chemistry of elastomeric materials, the dual-cure process of using UV light and thermal ovens, and the unique capability in AM to create complex lattice structures. Carbon has used this material-lattice-technology combo to create midsoles for advanced running shoes, bicycle saddles, backpack components, baseball gloves, and football and hockey helmets for leading sports manufacturers. Lattice structures were key to the success of each of the new products. “Lattice structures are great,” said Rolland, “and you can only make them with additive manufacturing. This is a super exciting area; by using lattices, we are able to make parts that people haven’t been able to make before.”
In a white paper on the partnership with adidas(7), Carbon describes some of the key benefits of lattice structures that can be designed and produced with the company’s technologies. “Carbon’s ability to create varying lattice structures within the same part or component results in unmatched design. Previously, engineers had to combine multiple components to create different properties within a final part. This complexity requires additional design, tooling and assembly resources and often results in quality issues.” Integrating lattices into parts can simplify the design process, open up performance possibilities, dramatically lighten the weight of a part and yield results that, until recently, were impossible to produce.
In the white paper, Carbon also cites breathability as a key benefit. “Carbon lattice innovation and resulting open-cell structure enables customers to create final products with improved thermal characteristics. In applications such as seats, armrests, headsets, crutch-pads and orthopedic supports for the back and neck, this breathability is especially useful in maintaining a comfortable temperature. Thermal control in these applications is essential for ideal end-user experiences, and heat dissipation via open-cell structures helps with that.”
And, as compared to foam, elastomeric lattice structures outperform in cleanliness. “Cleaning materials such as foam is cumbersome. Additionally, water retention and slow drying with foam are not desirable. In contrast, applications using Carbon’s lattice structures are easy to clean, do not retain water and can be utilized post-wash almost instantaneously.”
There have been many advances and improvements in additive manufacturing. New chemistries are being created for elastomeric materials for 3D printing, and there is growing adoption of AM products and components in industrial production and the consumer marketplace. Elastomers and 3D printing are proving to be a viable and innovative combination. Rubber product manufacturers that have not yet gotten on board would be wise to start looking at how this type of production might benefit them and their customers. u
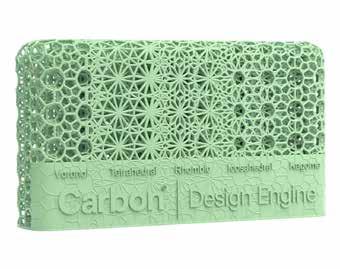
Carbon’s Design Engine lattice demo. Patentpending technology to seamlessly blend zones, producing attractive, functional lattices ready to use in real-world applications.
References
1. Simpson, Timothy W. “Lightweight with Lattices,” Modern
Machine Shop. January 20, 2018. https://www.mmsonline.com/ blog/post/lightweighting-with-lattices 2. Sher, Davide. “Some great examples of 3D printed furniture seen at Milan Design Week.” 3dprintingmedia.network. June 11, 2022. https://www.3dprintingmedia.network/some-greatexamples-of-3d-printed-furniture-seen-at-milan-design-week/ 3. Sertoglu, Kubi. “UCLA researchers 3D print entire microrobots in a single pass.” 3dprintingindustry.com. June 19, 2022. https://3dprintingindustry.com/news/ucla-researchers-3dprint-entire-microrobots-in-a-single-pass-211026/ 4. Hanaphy, Paul. “General Lattice to ‘facilitate the widespread adoption of AM’ after raising $1M.” 3dprintingindustry.com.
September 29, 2021. https://3dprintingindustry.com/news/ ucla-researchers-3d-print-entire-microrobots-in-a-singlepass-211026/ 5. Sheth, Sarang. “Inspired by Adidas, this wireless mouse is redefining ergonomics with its soft 3D printed mesh design.” yankodesign.com. December 30, 2021. https://www. yankodesign.com/2021/12/30/inspired-by-adidas-this-mouseis-redefining-ergonomics-with-its-soft-3d-printed-meshdesign/ 6. Adidas. “From Futurecraft to 4DFWD and Beyond: The
History of adidas 4D,” adidas.com. August 2021. https://www. adidas.com/us/blog/737899-from-futurecraft-to-4dfwd-andbeyond-the-history-of-adidas-4d. 7. “Carbon Lattice Innovation — The adidas Story.” Carbon3D. com. https://www.carbon3d.com/resources/whitepaper/theadidas-story
STRIP DOWN
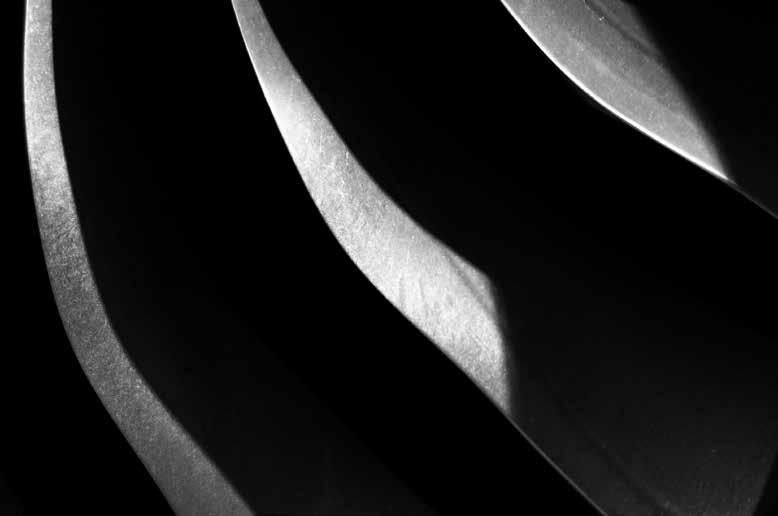
YOUR COSTS

PART OF THE BARWELL FAMILY
• A quick and automated method of cutting rubber strips from rolls or sheets • Weigh scale feedback system for volume cut or simply set strip/pad length • Significant cost, time, and quality advantages over manual methods of cutting • Easy to operate and maintain
info@barwellusa.com +1 330 225 9557 www.barwellusa.com ...a lifetime of reliability and support