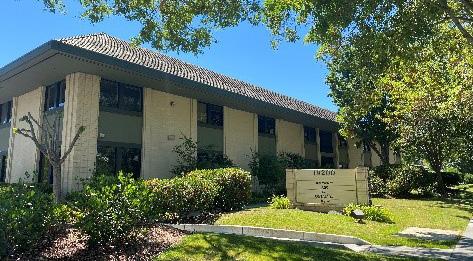
5 minute read
Machine Lead and the Failure of Radial Lip Seals
By Greg Vassmer, technical coordinator, ARPM
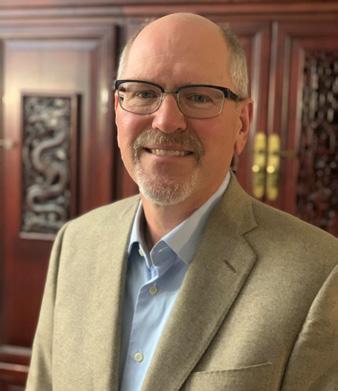
This is part one in a two-part Tech Corner. In this issue, the column looks at shaft machine lead and its impact on radial lip seals. Next issue, new technologies will be discussed that are going to help robustly detect the problem.
So, what is machine lead and why do rubber processors care?
Machine lead or “twist” is a surface finish pattern inadvertently created on a shaft surface during manufacture that acts like a screw thread. This pattern can cause an oil seal to prematurely leak.
So how does this come about, and can it be detected before a product fails at the consumer level? First, look at how a shaft is made.
In the simplest case, a shaft is a steel cylinder with a tight tolerance outside diameter and a controlled surface roughness. The right size and finish are needed for the seal to properly fit on the shaft and to work and wear as expected while running. There is a lot going on in the tiny space near the seal.
To get the shaft to the correct size and roughness several machining steps are used. The best way to imagine it is that first, a single-point tool moves along the shaft, cutting to get the exact size. Then, using the preferred technique, a grinding wheel plunges straight into the surface, grinding to a desired finish. Either of these steps can leave behind a dreaded screwthread-like lead. In fact, any axial motion along the shaft axis cuts a helical pattern. There are other ways to finish a shaft, and unfortunately, most have the potential to cut a helical pattern.
Our good friend Archimedes in 234 BC discovered that if such a thread pattern is rotated it will act as a pump and transport material down the shaft – like a fence post auger digging a post hole.
Rubber processors do not want the shaft to act as a pump because …
A rubber radial lip seal works by acting as a small pump specifically designed to keep a sealed fluid on the correct side of the seal. This ability to pump can be demonstrated by putting a drop of oil on the air side of a seal in operation and watching it disappear as it gets pumped back where it belongs. Machine lead on a rotating shaft either will work with or against the radial lip seal depending on which way the shaft rotates. Either way shortens the seal’s life. In one direction the lead overcomes the seal pumping and allows oil to leak, while in the other direction, the enhanced pumping sucks air under the seal, burning the oil and wearing out the rubber seal.
It’s clear there is a need to measure this and it’s simple. Rubber processors need a speed-controlled motor, a length of quilting thread, a small weight and the shaft to inspect. Together these make up the oldest, unfortunately too variable, but still a very current method for checking machine lead.
ARPM OS 1-1 contains the specifics for this test which dates to at least the 1970s but is probably older. It is in use today thanks to its low-tech equipment, ease of use and fairly good correlation to finding root cause for actual seal failures.
The shaft to be tested is mounted on the motor and a loop of thread wrapped around the shaft and the weight hung from the thread. Using the motor, rotate the shaft. The thread either will stay where it is or move to the right or left. If set up correctly, any movement of the thread indicates the shaft has machine lead and the potential to cause seal failure. The speed of the thread movement is an indication of the severity of the lead problem.
All major seal manufacturers use this test to detect machine lead – but they don’t like it for good reason. Its results vary due to both the test equipment and technician attentiveness. But there are new techniques on the market with far fewer of these issues. In next quarter’s column, the new methods and a new project by the ARPM Seal Committee will be discussed to see how well they work. n
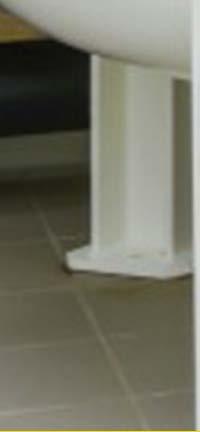
ACE Laboratories in Miami-Dade Earned Certification
ACE Laboratories, Ravenna, Ohio, earned certification from the Miami-Dade Department of Regulatory and Economic Resources as an approved testing laboratory for a range of construction industry tests under its ISO/IEC 17025 scope of accreditation. ACE’s responsibilities include the approval of construction materials and products under the most common tests performed for Miami-Dade County that are to international standards ASTM D6083, ASTM D6694, ASTM D5147 and ASTM D5869. For more information, visit www.ace-laboratories.com.
[1] AGCCA Opens New Business Office
AGC Chemicals Americas Inc. (AGCCA), Exton, Pennsylvania, a manufacturer of glass, electronic displays and chemical products, opened a new office in Cupertino, California, to support the advanced materials needed by semiconductor and electronics manufacturers on the northern West Coast. The Cupertino office promotes a wide variety of advanced materials of ETFE and PFA resins for tubes, hoses, gaskets and sheets; ETFE films for mold release film; and fluoroelastomers for components used in semiconductor plasma processes at elevated temperatures. For more information, visit www.agcchem.com.
USDA Climate-Smart Grant Awarded to Bridgestone
The USDA awarded Bridgestone $35 million to grow its investment in desert shrub guayule to advance a climatesmart domestic rubber industry and offer a water-smart solution. The company also will work to educate growers on water utilization, soil health, nutrient delivery and the ecological benefits of guayule. The viability of guayule as a sustainable, domestically produced alternative to imported tropical rubber also has been explored by Ford and fellow tire maker Cooper, as well as Patagonia, for use in wetsuits. For more information, visit www.bridgestoneamericas.com.
LanzaTech and Sumitomo Riko Announce Joint Partnership
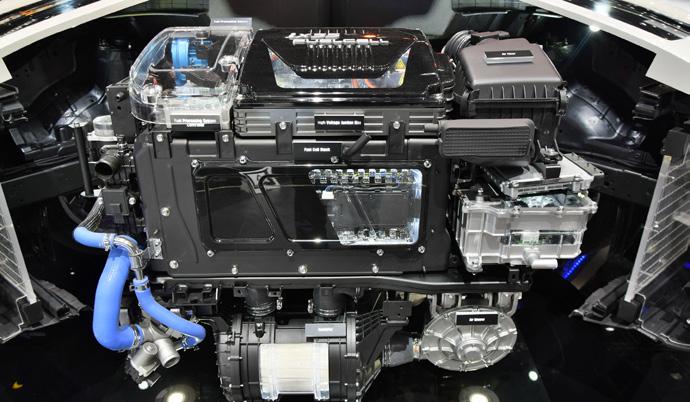
LanzaTech NZ, Inc. (“LanzaTech”), Skokie, Illinois, is an innovative Carbon Capture and Transformation (“CCT”) company that transforms waste carbon into materials and
Sumitomo Riko Company Ltd., Nagoya-shi, Aichi, Japan, announced a joint-development agreement to reuse rubber, resin and urethane waste for the production of a chemical intermediate, isoprene. Isoprene is produced by plants and is the main component of natural rubber. For more information, visit www.lanzatech.com.
[2] Momentive Releases New LSR and HCR Grades
Momentive Performance Materials, Waterford, New York, released its new LSR and HCR-based NEVSil product family. Suitable for a wide range of sealing applications in vehicles powered by alternative energies, including e-mobility, hybrid concepts and fuel cell technology. In addition to a generally low compression set, the wide range of grades include hightemperature resistance, flame retardancy, self-lubricating, low viscosity, low stiffness, fast curing, increased crack and aging resistance, good colorability and thermal conductivity. For more information, visit www.momentive.com
[3] Racho Rubber Expands Team
Rahco Rubber, Inc., Des Plaines, Illinois, announced the hiring of Brian Mnichowicz to its engineering and technical team. Mnichowicz comes to Rahco with over five years of manufacturing engineering experience and extensive knowledge in process engineering, lean manufacturing, project management, automation systems, Six Sigma and mold design. For more information, visit www.rahco-rubber.com.
Minnesota Rubber & Plastics Now Part of Trelleborg
Minnesota Rubber & Plastics (MRP), a Minneapolis, Minnesota leader in material compound development and the manufacturing of custom elastomeric and thermoplastic components, has been acquired by Trelleborg, a worldwide provider for engineered polymer solutions that seal, damp and protect critical applications in demanding environments. Becoming part of Trelleborg Sealing Solutions unlocks new benefits for MRP customers, leveraging the strengths of both companies to become a one-stop-shop for customers requiring accelerated time to market, especially in the medical device market. For more information, visit www.mnrubber.com or www.trelleborg.com.n