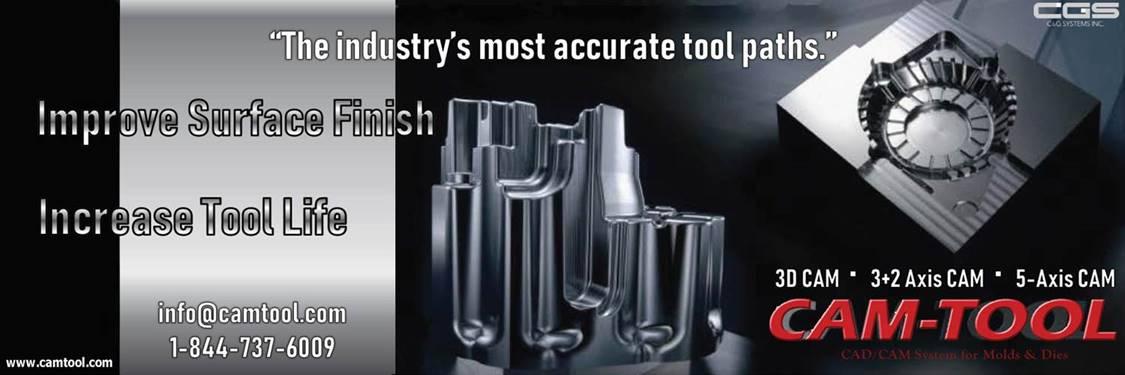
16 minute read
SOLUTIONS
INFORMATION DOWNLOAD: HOW MOLD BUILDERS ARE MOVING FORWARD DURING COVID-19
40 the american MOLD BUILDER | Issue 2 2020 Q. Q. Q. Compiled by Dianna Brodine, managing editor, The American Mold Builder T he AMBA has been offering roundtable discussion webinars for its members where member company representatives can discuss issues related to the current pandemic with their peers as businesses begin to ramp up production and bring employees back on site. Here, a brief glimpse is provided into the conversations happening between mold builders across the country. Member companies are not identified in this article. HOW ARE YOU SCREENING EMPLOYEE HEALTH? WHAT SAFETY MEASURES ARE IN PLACE? • We asked our employees to complete a five-question questionnaire, with questions based on recommendations from the CDC, such as have you been exposed to people who have traveled internationally, are you experiencing flu-like symptoms, etc. We are verifying their survey responses every day. One entrance has been designated for employees, and we are taking temperatures, which is now mandated by our governor. • We are taking employee temps before they clock in, have made it mandatory for everyone to wear masks and are encouraging anyone who is sick to stay home. We have one person (foreman or plant manager) taking temps in each building. Also have a checklist so we know who is in the buildings each day and that their temps were taken. • Masks are available, but not mandatory. However, we need to start taking temps. We have varying start times, and there’s no one up front right now when people come in, so it’s a logistics issue as to how that is implemented. • We have masks available, but not mandatory. We haven’t done anything formal with the temperature-taking yet. We also are following the CDC-recommended precautionary cleaning in high-touch or high-traffic areas. • We have made masks mandatory. We also have restricted visitors until June and no one is going out to visit customers. There is no temperature testing right now, but every employee has the HR manager’s cell phone number and all employees have been told to stay home and call if they are ill or have been exposed. • We are mandating face masks, so we’ve provided reusable, washable face masks to all employees. • We’re treating masks like all of our other PPE, where in certain areas of the plant it is mandated that masks are worn and in other areas it is not. • Our facility put yellow tape on the floor to remind everyone about maintaining safe distances. We also have put Xs at the entrance to offices to stop employees from walking into those spaces, and we have measured appropriate distances between chairs in the break room. HOW WILL YOU BRING OLDER WORKERS (OR EMPLOYEES IN GENERAL) BACK AND KEEP THEM SAFE? • Some workers are able to work remotely, so we keep them there. Also, we have one employee nearing retirement and we are working out an alternative position that will enable him to minimize interaction. We also are offering a second shift that a lot of people are taking advantage of – both those who are older and people who suddenly had children at home when school was cancelled. We want to make sure everyone feels safe and comfortable coming to work. • We staggered shifts so that fewer employees are working each shift. Also, we changed our schedule so more people are working four 10-hour shifts and then spread those employees out over six days. • We went from four 10-hour shifts to two different cells – so now one cell works M,T,W and the other works Th-F-S. This gives us less people on each shift, less people co-mingling. It’s been a difficult process, but this is our third week and we’re starting to get the bugs out. It’s all about keeping people safe, so we’re doing the best we can. I’m not sure we’ll go back to our old shift schedule. Eventually, we’ll be running more hours – we are more efficient now, but we don’t have the bodies to be as efficient as we can. We may stay in this setup and hire more employees down the road. HOW ARE YOU CLEANING / DISINFECTING? • Disinfection materials are available at each station. We’re lucky in that we already have some distance between each work station, and we’re asking the operators to clean and disinfect their own stations. • We have gotten multiple quotes for outside cleaning services, but haven’t implemented anything yet. • We’re using an internal person working full-time. They have a checklist that goes hour-by-hour as to which high-touch areas and which parts of the shop to clean at specific times.
Q. Q. • We’ve got an internal cleaning crew and have added a couple of workers to that crew to deal with the added disinfection. • We have an internal person who wipes everything down at the end of the day, so the next day it’s clean. We also have an external cleaning service that we have given specific direction to that complies with CDC recommendations. • We have four shared CNC programming stations, so that’s a concern for us. We’re constantly cleaning those, and they all have Clorox wipes near them, but the habits of our employees haven’t been reinforced yet – they aren’t doing it as consistently as they should. HOW ARE YOU TRACKING PAYCHECK PROTECTION PROGRAM (PPP) SPENDING? • We received money pretty quickly. It appears the bank is in charge of validating what that money is used for, and our bank recommended that the funds be placed in the general fund. Because we are working with a local bank and have a relationship with them, we’ll validate the funds that qualify at that time. • Our company is creating a sub-area in Quick Books to have the ability to track those funds. • We’ve put all of that money into a payroll account, with no tracking after that. • Assuming we receive it, we’ll keep it in a separate account and transfer money into the bill-paying account for payroll, using a spreadsheet to see if there’s room to work in utilities, etc. There are several calculators available that will show if we can get it forgiven, allowing us to maximize the potential for forgiveness. HOW MANY LAUNCHES ARE BEING DELAYED OR CANCELLED DUE TO THE COVID-19 SLOWDOWN? • We’re getting a few small hit-or-miss jobs, but are hearing that cancellations may be coming. • We are just starting to hear from customers that they are holding back. We have a good workload, and I’m getting quotes
Q. in, so it still feels pretty good. But I’m concerned that the quotes will stop coming in. it’s more of a gut feel, but I have heard from customers in the last week that they are holding off on spending. • We’re hearing the same thing from a couple launches we’re involved in – that the launches are getting backed off. These customers are waiting to see what the global economy does, because they get parts overseas, which will affect timing. ARE YOU STILL QUOTING A NORMAL NUMBER OF PROJECTS? • We are busy quoting right now in most areas. • We’re down approximately 15 to 20%. • Our shop is down approximately 40%, but we’re tied to automotive so it’s expected. • Quoting volume is only 70% of where we want to be over the last two weeks, but the more concerning thing is that our release jobs is only 30% to 40% of where we want it to be. • Our quoting is down significantly, but the quotes have a high capture rate – like 90%. • Quoting is up, but potential start dates have really moved out.
Everything used to be two to three months, and now it’s four to six months. • We have a record quote book right now, but only $9,000 in orders last week. It’s a tale of two cities. • Our shop is down in quoting about 30%.
This sampling of perspectives from around the US provide mold builders the opportunity to benchmark their own facilities and evaluate best practices. To join the next AMBA webinar, visit www. amba.org/events. n
1
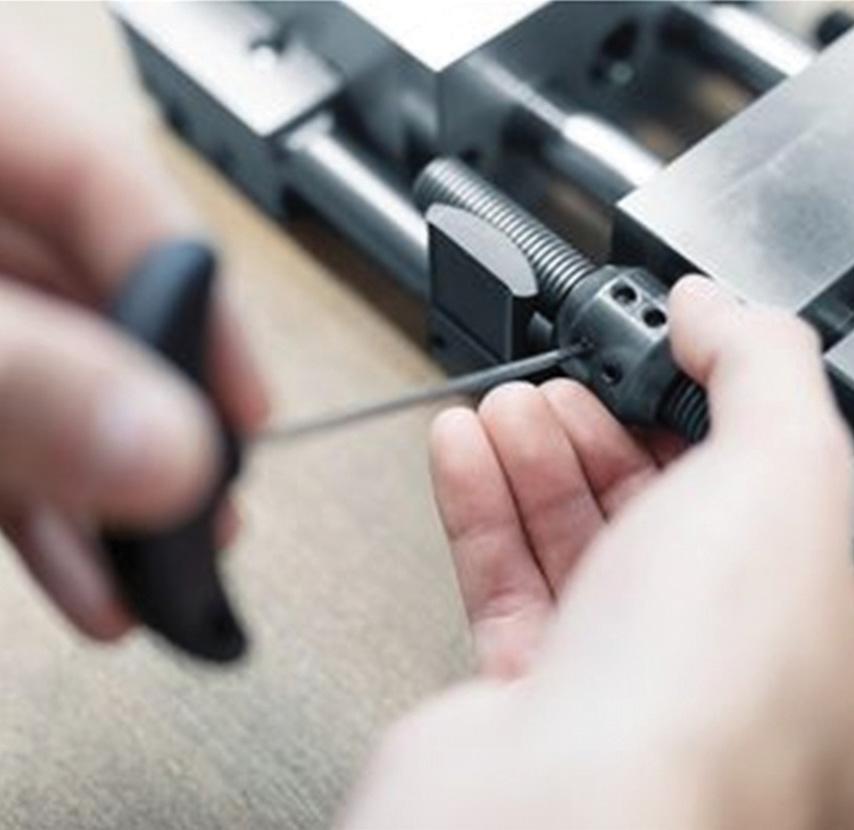
2


ROLLOMATIC INTRODUCES CAPABILITY IN SHARPENING OF DIAMOND-COATED CARBIDE TOOLS Rollomatic Inc., a Swiss machine tool manufacturer with North American headquarters in Mundelein, Illinois, announces new capabilities related to the LaserSmart 510 laser cutting and ablation machine. A drawback of diamond-coated carbide cutting tools is that thick-film coating makes the cutting edge dull, and thin film coatings often wear prematurely. Rollomatic has developed a process to sharpen thick film diamond-coated cutting tools. The Rollomatic CNC Laser Cutting Machine LaserSmart probes the surface of the coated cutting edge to detect the exact shape and position. Then the laser cutting process removes just enough diamond coating to make the cutting edge sharp. Only a predetermined amount of the coating, just around the cutting edge, is removed by the laser process. For more information, visit www.RollomaticUSA.com or email solutions@RollomaticUSA.com.
[1] MEUSBURGER OFFERS LATCH LOCK Austria-based Meusburger Georg GmbH & Co KG, maker of dies, molds, jigs and fixtures, now offers the E 1817 latch lock. Latch locks are used to control molds with two split-line, three-plate molds. With the new E 1817 latch lock, Meusburger has created an exclusive and cost-effective alternative to existing products on the market. The new latch lock’s simple mechanical functional principle offers maximum reliability in the control of three-plate molds. It features a compact design and low machining effort prior to its installation. An animation of the E 1817 latch lock is available to show the individual steps in detail, and CAD data can be downloaded in the shops. The E 1817 latch lock is available from stock. For more information, visit www.meusburger.com.
42 the american MOLD BUILDER | Issue 2 2020 [2] TOOLING TECH GROUP ANNOUNCES FLEXBASE MODULAR AUTOMATED WORK CELL Tooling Tech Group, Macomb, Michigan, a provider of custom automated systems for assembly, joining and inspection as well as tooling, has announced the availability of its FLEXBASE standardized modular automation cell. Easily integrated, flexible and scalable, the FLEXBASE system can be configured as a stand-alone, automated workstation with manual loading and unloading, or linked together via conveyors to quickly create a complete automated assembly line. FLEXBASE features a welded steel frame base in standard sizes of either 48" x 40" or 72" x 40" and a 37" high aluminum top plate ready to be fitted with custom tooling or fixturing. Each standard system comes with an upper and lower conveyor with stop and blocked sensors and pallets with nests that conform to almost any product. For more information, visit www.toolingtechgroup.com.
[3] ACU-RITE OFFERS FREE UPGRADE DOWNLOAD FOR ITS POPULAR DROS Motion control feedback solution provider HEIDENHAIN Corporation, Schaumburg, Illinois, has announced that to enhance digital readouts (DROs) in machine shops across the world, HEIDENHAIN’s ACU-RITE brand is making new free downloadable upgrade software available. The upgrade assists users of current model ACU-RITE digital readouts to be more productive and efficient, while continuing its ease-of-use tradition. ACU-RITE’s current family of DROs includes models 100, 200 and 300. The new software version – “v1.4.0” – is available on the ACU-RITE website / Software Updates. Highlights include: Axes Q – the letter Q has been added to the axes’ names list; a “Zoom Timeout” time delay has been added to the Dynamic Zoom & Highlight feature; and a “Send Position” soft key has been added. For more information, visit www.acu-rite.com.
[4] SUHNER OFFERS NEWLY DESIGNED VERSION OF BEX 15 Suhner Industrial Products, Rome, Georgia, manufacturer of special industrial tools and special components, introduces the BEX 15 machining unit. With maximum spindle speed up to 23,000 RPM, the BEX 15 offers higher speeds and improved production inline. Standard variations are equipped with 0.55 kW, 0.75 kW and 1.5 kW electric motors. An adapter flange allows installation of multiple spindle heads and angle heads. A new style timing belt drive multiplies the motor speed up to 13,050 RPM spindle speed. An AC inverter drive increases the spindle speed up to 23,000 RPM at 87 Hz. Standard motor mounting on BEX 15 machining spindles is in
4


5

the rear. Optional front motor mounting is available upon request. Additional optional features include frequency converter and direct drive servomotor. For more information, visit www.suhner.com.
RUD OFFERS TOOL MOVER: A REVOLUTION IN TOOL MAINTENANCE RUD Ketten Rieger & Dietz GmbH u. Co. KG, Aalen, Germany, maker of tyre chains, sling chains and chain systems, offers Tool Mover for moving heavy tools and bulky items. Ideal for unmounting tools from injection molding machines or dismantling machine parts weighing several metric tons, the latest generation features a larger working surface at the lowest possible working height. The machine axially rotates tools and machine components up to 64 metric tons. Available in six standard sizes, the smallest (with a table area of 800 x 1300 mm) can handle up to 10 metric tons. The largest standard version – THS 64 – can rotate tools and machine components weighing up to 64 metric tons on its 3500 x 2500 mm table area. For more information, visit www.rud.com.
VIRAL SIGN OFFERS ADVANCED COVID-19 SCREENING Viral Sign, Inc., Edina, Minnesota, has announced the launch of the company’s advanced screening technology at the manufacturing facility for Precise Tooling Solutions in Columbus, Indiana. Viral Sign enables users to identify the presence of virus, including COVID-19, in individuals prior to the onset of symptoms. Viral Sign leverages the power of infrared imaging and an advanced screening algorithm to produce a comprehensive thermal signature of the face. In real time, the algorithm assesses the thermal signature to identify patterns consistent with early, pre-symptomatic influenzalike illness, including COVID-19. The total time required for Viral Sign to capture the infrared image, evaluate the thermal signature and indicate the suspicion of virus is approximately two seconds. Don Dumoulin, CEO and owner of Precise Tooling Solutions, said, “Our customers depend on us for on-time deliveries, and this technology helps ensure that Precise craftsmen can continue to meet the high expectations of our customers. We are happy to showcase the Viral Sign technology to other interested employers.” Viral Sign, Inc. develops and markets advanced screening technology to limit the spread of virus and communicable disease in the workplace, in healthcare facilities and in public venues. To learn more, visit https:// viral-sign.com/. Precise Tooling Solutions is a specialty manufacturer that designs, builds and repairs injection molds and is an authorized seller of Viral Sign. For more information, https://precisetooling.com.
BORIDE’S CRISTONE ® MATERIAL NOW AVAILABLE IN END BRISTLE BRUSHES BORIDE Engineered Abrasives, Traverse City, Michigan, a developer, manufacturer and distributor of abrasive products, has added Cristone ® End Bristle Brushes to its extensive offering of polishing products and accessories. Made from the same highquality crystalline fibers as the popular Cristone ® Crystal Fiber Detail Polishing Stones, End Bristle Brushes are the perfect tool to use for cross hole deburring, surface finishing and polishing aircraft parts, engine blocks and medical devices. The Cristone ® Bristle Brush structure incorporates nanotechnology that saves time by allowing the finishing of surface roughness with only one fine grit. Brushes come in one size and many grits – ranging from 150 to 6,000 – allowing work on the hardest of materials, such as carbon, to nonferrous metals, such as aluminum. For more information, visit www.borideabrasives.com.
43www.americanmoldbuilder.com | AMBA.org TRELLEBORG UNVEILS NEW ECO-FRIENDLY DUST-FREE TOOLING BOARD Swedish engineered polymer solutions provider Trelleborg has announced a new tooling board, TC760X. Kerry Lyons, sales manager for Trelleborg’s applied technologies operation globally, stated: “Our TC760X tooling board is really unique in that it does not dust during machining; the board flakes rather than chips, for a cleaner cut. Less dust means less machine breakdowns, resulting in improved production efficiency and greater cost savings, with reduced environmental impact.” Will Ricci, business development manager for Trelleborg’s applied technologies operation in the US, stated: “The TC760X board provides toughness without sacrificing the glass transition temperature (Tg). The material has a Tg of +140 page 44
Mold Polishing & Repair Providing the Latest Technology for
• Finishing Stones • Laser Welders • Ultrasonic Polishers • Micro-TIG Welders • Power Tools • Diamond Abrasives • Mold Polishing Classes






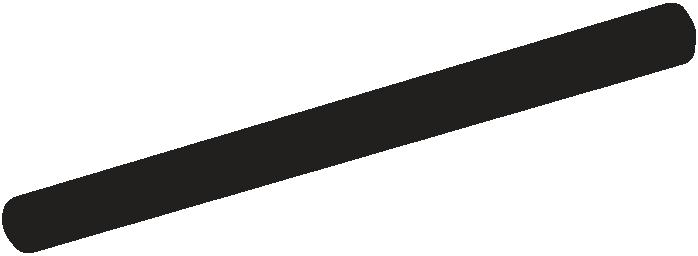
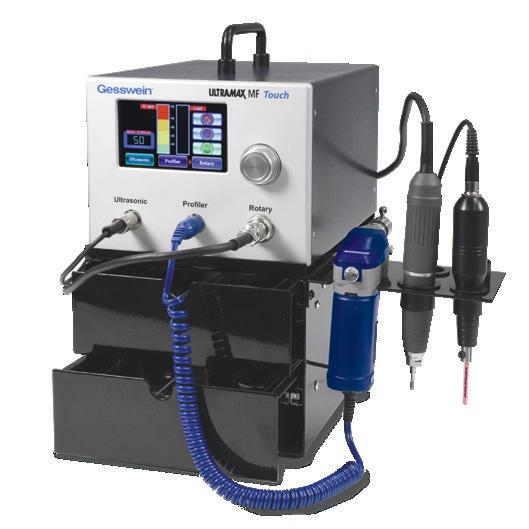

For more information www.gesswein.com 800.243.4466 Ext. 223 or 227



°C, with a low coefficient of thermal expansion, resulting in faster curing, improved machining, and quick and easy direct-to-part manufacturing.” For more information, visit http://bit.ly/31PdYu8 and www.trelleborg.com.
[5] NEW RING ENCODER FROM HEIDENHAIN RESISTS CONTAMINATION Motion control feedback solution provider HEIDENHAIN CORPORATION, headquartered in Schaumburg, Illinois, and San Jose, California, has introduced a new midrange, high-accuracy ring encoder that is suitable for position measurement applications that require high tolerance to contamination but do not demand the accuracy level of an optical encoder. The HEIDENHAIN ERM 2203 is optimized to meet those needs. HEIDENHAIN ERM 2203 ring encoders are most suitable for applications such as gear-wheel grinding machines and others that require similar high accuracy but must operate in an often-contaminated environment. The ERM 2203 retains the 200 µm signal period of other current ERM products, though the graduation error has been reduced by approximately 30%. For more information, visit www.heidenhain.us.
HASCO INTRODUCES NEW AIR VALVE Z4913/… Austria-based Hasco, a supplier of modular standardized components and accessories, has introduced the Z4913/… air valve for a safe, reliable production process. With targeted venting of the plastic component on the moving half of the mold, the vacuum can be optimally released with the air valve. Simple assembly and dismantling in the mounting hole allows rapid, reliable fitting and removal, with the feed tolerance reducing tilting danger. The mechanical stroke limitation boosts process reliability. The air valves can be flexibly positioned and installed to save space. All components in contact with the melt are stainless steel and resistant to aggressive plastics. The series, suitable for fast runners, can be used for working pressures of 3 to 10 bar and temperatures of up to 250°C maximum. For more information, visit www.hasco.com.
[6] OPEN MIND OFFERS ADVANCED CAM SOFTWARE OPEN MIND Technologies AG, a German developer of CAD/ CAM software solutions, has announced the advanced capabilities of hyperMILL ® CAM software which offers advantages when using 5-axis machining for moldmaking. The hyperMILL ® MAXX Machining Finishing Module, a performance package of the hyperMILL ® CAM software suite, is the CAM programming source enabling the use of conical barrel cutters to reduce cycle times over 90% and is ideal for planar, ruled and curved surfaces often found in complex 5-axis components. hyperMILL ® MAXX Machining offers three powerful modules for finishing, roughing and drilling. OPEN MIND’s hyperMILL ® 2020.1 has powerful 3D and 5-axis machining enhancements for complex machining applications including mold and die. In addition, it increases ease of use and overall programming performance, and includes new automation and additive manufacturing strategies. For more information, visit www.openmind-tech.com. n