
42 minute read
SOLUTIONS
By Liz Stevens, contributing writer, The American Mold Builder
Don Dumoulin, the CEO and owner of Precise Tooling Solutions, Columbus, Indiana, knows that plastic tooling manufacturing is a challenging business, even in the best of times. With COVID-19 affecting supply chains and deliveries, and Chinese businesses competing for market share, Dumoulin believes that now is an excellent time for moldmakers to expand their resourcefulness, boost their productivity and increase their bottom lines. He admits, however, that achieving this is not a slam-dunk.
“We have somewhat limited resources as toolmakers,” he said. “We only have so much capital we can deploy every year. We only have so much time that we can put against projects that will change our dimensions, if you will. And we only have so many things that we can do in a given year to really drive improvement.”
Dumoulin believes that gaining a better understanding of a plant’s machines and how operators run those machines can give manufacturers valuable insight that can lead to profit-yielding changes. For him, advancing beyond the use of paper scorecards to record machine downtime is a key to gaining greater understanding, and machine monitoring is an ideal next step. After all, he notes, “the machine monitoring industry will tell you that the average machine utilization in our shops is 26%.” This equates to a loss of about $1.5M per manufacturer for downtime.
Finding ways to reduce or eliminate machine time loss, and thereby increase the productivity of both machines and operators, is critical to profitability. And while reducing repair time and set-up time is an obvious way to improve operations, in Dumoulin’s experience, “continuous improvement also can happen with reducing the time needed to track down cutting tools, with improving steel availability, with making sure that programs are available for machinists.”
During the AMBA Continuous Improvement virtual conference, held November 4 and 5, 2020, Dumoulin and co-presenter Akshat Thirani, the co-founder and CEO at Chicago-based technology company Amper, outlined Precise Tooling Solutions’ journey to find and implement a machine monitoring solution.
THE SEARCH FOR A MACHINE MONITORING SYSTEM “I have long believed that machine monitoring was part of the solution,” said Dumoulin, “but I really struggled to find a positive return on investment.” He found that sophisticated machine monitoring systems can come with a $30,000 or $50,000 price tag for software, plus an additional $10,000-15,000 to get all of a plant’s machines retrofitted for monitoring.
So, when Dumoulin sat down with his team to prepare for another round of searching for a machine monitoring system, he and the team boiled down their wants and needs to a succinct shopping list. “We wanted leading indicators versus lagging indicators,” he began. “We wanted a culture of lean and accountability. We wanted to make sure that our technology was data-focused and staying ahead of the curve. And we wanted to make sure that we also were looking at the opportunity cost to collect that data.”
Since machine monitoring includes integration with existing equipment – be it brand-new equipment or 20-year old machines – any plant considering the addition of machine monitoring should consider the cost of outfitting older machines with updated technology to allow for the most advanced monitoring systems. If the cost is prohibitive, Dumoulin suggests considering a more modest approach. “Maybe you don’t jump right to full-blown machine monitoring,” he said, “but you work instead on getting some of the machine monitoring aspects in place first. If you can’t afford those kinds of upgrades, but you at least need something that gets you going down the data path, a simpler version of machine monitoring might be a good choice.”
FINDING THE RIGHT FIT FOR PRECISE TOOLING SOLUTIONS Don Dumoulin and his company refined their search criteria to five key points to evaluate in a machine monitoring system: the true cost of the implementation, the implementation requirements (for upgrades and additions), the ease of use of the system, the simplicity and flexibility of the system’s reporting options, and the ability to get the company team engaged in using the new system.
Dumoulin moved forward with Amper’s offering for machine monitoring. “Of the three systems we looked at, the Amper solution was the best across the board,” he said. “Some of the vendors had a very high true cost; they were very expensive to purchase and complex to install, and driving our existing machines was really hard to do.”
Dumoulin had long been convinced of the benefits of software as a service (SaaS), another attractive feature of the system his company chose. “The great part about a SaaS model is you don’t have any capital cost,” said Dumoulin. “You literally hit the return on investment running as opposed to the average $35,000 or $50,000 in a purchase fee model, which immediately puts you in the hole.” The solution Dumoulin implemented with Thirani required no machine upgrades. “We know that PLC boards are very different,” said Dumoulin. “We asked ourselves, do we have the time to figure out each one and the cost necessary to modify it, and how you code those things? One of our potential vendors wanted to send somebody to our shop at $1,500 a day for three weeks to reprogram all of our machines. I just wasn’t sure I wanted to let them into the code of my machines.” Amper’s design eliminates this requirement.
The reporting features of a machine monitoring system needed to be robust, easy to use and flexible to meet Dumoulin’s criteria. The chosen system included emailed alerts when a machine went down, a variety of sample reports to choose from, and the ability to use unassigned data fields that allow plants to create custom reports with specific data (such as KPIs). “Also,” said Dumoulin, “we can look at longitudinal data over a month or a year and ask ourselves, ‘What is the biggest continuous improvement opportunity that we see that would make us more productive for machine timing?’”
In November, when Dumoulin presented this AMBA workshop, his plant had been using Amper for about three months. Although page 22
I am top-grade.
Stainless Steel Cooling Range
The new HASCO cooling range in stainless steel is employed in cleanrooms or medical technology applications for the temperature control of injection molds in reliable processes, using hot/cold water or oil. – Ideal for medical and clean-room technology – Seals in special FKM – Thread tightness even with large temperature differences – Choice between open flow, or shut-off valves on one or both sides – Quality material 1.4305 ––Damage to functional surfaces is avoided Compatible with the HASCO brass cooling range “ Thank you for allowing HASCO to serve you in 2020. “
• (800) 558-6040 • WWW.SUPERIORDIESET.COM •
SHOP NOW
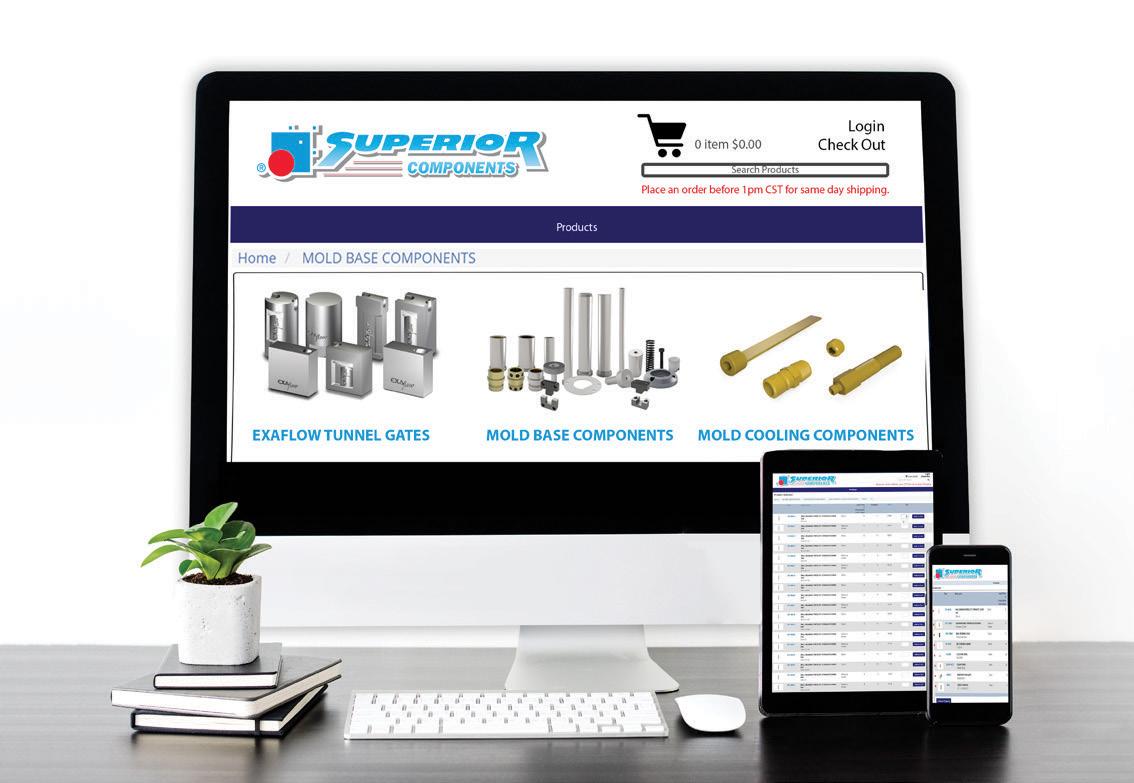
WWW.SUPERCOMP.COM MOLD BASE COMPONENTS
MADE IN THE USA
Manufacturing high quality abrasive products for nearly 50 years American made deburring and metal finishing products
Aerospace, automotive, electronic and oil and gas drilling industries

page 21
there was some initial pushback from machinists, they embraced the system once Dumoulin assured them that the system was a machinemonitoring system rather than a machinist-monitoring system. “This is not about the failings of you as a machinist,” Dumoulin had told his machinists, “This is about what we can do to help you to be more productive.”
HOW MACHINE MONITORING CAN INFORM CONTINUOUS IMPROVEMENT Akshat Thirani described his company’s general approach as a quest to improve quality, cost and delivery by helping businesses use overall equipment effectiveness (OEE) as the leading indicator for their operation. “Everyone generally tracks QCD (quality, cost, delivery) and profit and loss (P&L) at the end of the month and the quarter,” he said, “and the purpose of our OEE-type tool is to provide the leading indicators so that business owners can make an impact at the end of the day.”
“Amper is the simplest machine monitoring tool out there,” Thirani said. “It is a noninvasive sensor that measures the electrical signals of a machine.” The electrical energy used by a spindle varies, and a sensor tracks the electrical usage, recording whether a machine is off, idling or running at top capacity. Sensor installation takes only 10 to 15 minutes per machine. “You basically clip the sensor,” said Thirani, “hook up the internet-connected gateway, and then you are ready to look at real-time analytics via a computer or smartphone.” Installation of a sensor does not require integration with the PLC or control panel.
As Thirani puts it, “Data in itself has no value if no one is using it,” and the data from these sensors has value at a variety of decisionmaking loops in plant operations. “The first loop,” said Thirani, “can revolve around daily improvement so, for example, the operator and supervisor level can have access to real-time alerts showing when a machine has had too much downtime or indicating that an operator is spending excess time on set-ups.” The data then can roll up into a second loop – weekly reviews from a plant management standpoint – guiding the focus of engineering projects.
“The third loop,” Thirani said, “can be about taking a broad perspective regarding capacity management over an entire year: Does a company really need to buy a new machine? Are machines already utilized to the point that justifies bringing on more people or new machines? How can cost of capacity be adjusted to bring on new sales?”
Don Dumoulin summed up his biggest takeaway from installing a machine monitoring tool. “You learn what your productivity really is, and that’s a little shocking. Once you get the bad news, you then start to see what the reason codes are – why you are getting those kind of results – and you can fix those issues. To me, that is the essence of continuous improvement.”
NPE2021: OPPORTUNITIES IN VIRTUAL AND IN-PERSON FORMATS
By Dianna Brodine, managing editor, The American Mold Builder
Once every three years, the plastics industry gathers to attend the largest plastics tradeshow in the Americas. Scheduled for May 17 through 21, the 2021 edition was on track to bring more than 2,100 exhibitors to the Orange County Convention Center in Orlando, Florida, with equipment, machinery, consumables, processes and support technology convened within more than one million square feet of exhibit space. The pandemic has forced the event to change shape – to what extent is yet unknown – but opportunities exist within the combined virtual and in-person event being developed by The Plastics Industry Association, producers of NPE. PLASTICS VERTICALS ON DISPLAY Event organizers say every sector of the global plastics industry and its vertical markets will be represented at NPE. From automotive/ transportation, consumer products and bottling/containers to medtech and packaging, the Orange County Convention Center will provide opportunities for those looking to diversify their supply chain, explore new market opportunities or compare potential capital expenditure options. The event halls will feature 13 technology zones, including sectors that focus on innovation and offerings in the following areas: 3D/4D printing; bottling; contract manufacturing; decorating and secondary processes; flexible packaging; inspection and measurement; medtech; moldmaking; polymers and additives; product design and engineering services; recycling and sustainability; rigid packaging; and robotics and automation. These technology zones have the advantage of bringing together those working within specific spaces, simplifying access for event attendees and providing opportunities for collaboration. “NPE2021 is the premier event for all sectors of the plastic industry to network, exchange ideas and see the latest innovations molding the future of plastics,” said President and CEO of PLASTICS, Tony Radoszewski, CAE, in a recent press release. “Attendees will be able to learn about emerging plastics trends; purchase the latest machinery, materials and equipment that are revolutionizing manufacturing; and connect with industry leaders.”

In addition to the tradeshow floor exhibits, NPE offers education programs, with sessions featuring topics ranging from sustainability and recycling to additive manufacturing.
COVID-19 PRECAUTIONS ON TAP Whether a COVID-19 vaccine readily is available or not, health and safety precautions while at the Orange County Convention Center
will be a key consideration for attendees and exhibitors alike. First, given the inability of some to travel to Orlando in May, event organizers will offer NPE2021 as a hybrid event. A digital component will provide access to the technology and education, although details have yet to be released.
The priority, according to show organizers, is the in-person event. Recent communication posted to the NPE2021 website explained, “The health and welfare of all NPE participants is, of course, our top priority. We have been closely monitoring the situation, including all guidance from governmental health agencies such as the Centers for Disease Control and Prevention (CDC), as well as information from the State of Florida and the Orange County Convention Center (OCCC), and will take into consideration all current health guidelines necessary to create a safe and healthy environment for our show.”
Whether this includes face masks, pared-down exhibitor booths or other as-yet-unnamed precautions likely will depend on the United States’ ability to bring the spread of coronavirus under control prior to the May event. As of press time, the event still is six months in the future, and hope exists that it can proceed as planned.
“Given the challenges of the past six months, it is vitally important for the plastics community to come together and support each other with a positive outlook to the future,” said Radoszewski.
Learn more about NPE2021 or register to attend: www.npe.org
See the American Mold Builders Association (AMBA) at NPE2021 in Booth W9405.
1 2 3
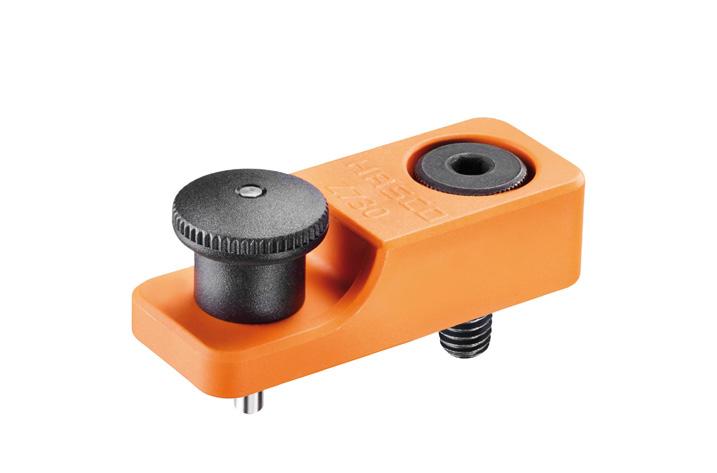


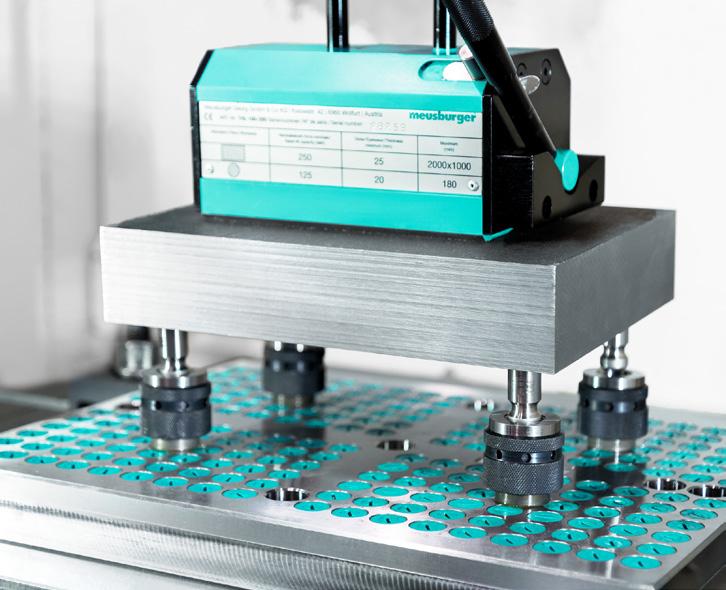
4

[1] HASCO OFFERS HOT RUNNER SYSTEM, TOOL LOCK Standard component provider HASCO, Lüdenscheid, Germany, offers Streamrunner®, a new, additively manufactured hot runner system from HASCO hot runner. Flow channels can be configured with the optimum rheological layout, avoiding sharp edges and areas with poor flow. The gentle passage of the melt through the manifold makes for considerably lower shear stress in the material, resulting in better quality moldings. And the flow-optimized design speeds up color changes, too, since the melt can be divided and deflected over generous radii. In addition, the company now offers the new mold lock Z730/… to prevent injection molds from opening during installation and removal as well as during transport and to prevent any moving plates, like ejector assemblies, from shifting out of position. The Z730/... can be operated with just one hand and without any tools, avoiding any damage to the mold. For more information, visit www.hasco.com/en.
[2] HEIDENHAIN’S ANGLE ENCODERS, INTERFACE UNDERGO UPGRADE Motion control feedback solutions provider HEIDENHAIN, with US headquarters in Schaumburg, Illinois, has announced technical upgrades to the ERA 4000 angle encoder series. The ERA 4000 series offers increased accuracy, ease of use and logistical flexibility, while remaining mechanically compatible with past models. ERA 4000 angle encoders consist of a steel drum at various diameters with the 20-, 40- or 80-micron graduation on the outer diameter, and a scanning unit that reads the graduation. The addition of HEIDENHAIN Signal Processing (HSP) to the scanning units increases the speed capabilities of the encoder system to 1 MHz 5 6

scanning. The company also has debuted its EnDat 3 encoder interface protocol. Now available in HEIDENHAIN’s ExI 1100 series of inductive rotary encoders, this interface offers users faster and more efficient operation in their machine motion control. The new EnDat 3 protocol carries forward the features and benefits of the well-established original EnDat with a new architecture that maintains continuity and compatibility with previous versions. For more information, visit www.heidenhain.us.
[3] ROLLOMATIC SPOTLIGHTS FULLY INTERPOLATED 6‐AXIS TOOL GRINDER Rollomatic, a machine tool manufacturer based in Le Landeron, Switzerland, highlights the new GrindSmart® model 630XW machine with new and innovative capabilities relating to the production grinding of solid carbide boring bars and other stationary cutting tools. Boring bar grinding on the Rollomatic 6-axis tool grinding machines offers exceptional flexibility in comparison to conventional single-purpose grinders. With its six fully interpolating CNC axes and a 6-station wheel/nozzle changer, the machine easily can be adapted for individual boring bar designs, both for short and long runs. The compact and versatile design allows full interchangeability between boring bars, inserts and round tools. Rollomatic provides service/support from its North American headquarters in Mundelein, Illinois, and satellite offices in California, Florida, Indiana and Massachusetts. For more information, visit www.RollomaticUSA.com.
[4] MEUSBURGER OFFERS NEW CLAMPING CONFIGURATOR Austrian parts provider Meusburger now offers a new configurator service. Moldmakers spend an average of 600 hours per year on
machine set-up. This time can be slashed by using a zero-clamping system. Customers can order the plates they need to machine with the fitting holes for the clamping bolts of their zero-clamping system. Introducing fitting holes for the clamping bolts of a zero clamping system takes time, personnel and machine resources. With Meusburger’s service for the P standard and P special plates range, customers can skip this step since the fitting holes have already been made in the plate. The selection is made using the clamping configurator in the Meusburger shop. For more information, visit www.meusburger.com/clamping-configurator.
DOOSAN PRESENTS 5-AXIS DVF SERIES, PUMA SMX5100L Doosan Machine Tools America, Pine Brook, New Jersey, presents the DVF Series of compact 5-axis machining centers, built for a wide range of five-sided and simultaneous 5-axis applications. The FANUC 31i-B5 CNC controller makes full 5-axis simultaneous control (all axes feeding at once) possible, giving full contouring capabilities. The DVF 5000 is equipped with a CAT40/BIG PLUS® taper 18,000 r/min spindle, which facilitates high-speed metal removal. The DVF 5000 features a 19.7" (500mm) diameter B- over C-axis rotary table with a 24.8" (630mm) option. The machine table is an integrated cantilever style full 5-axis table, which allows for the machining of parts from a variety of angles. The company also presents the PUMA SMX5100L, the latest addition to the company’s twin-spindle, multitasking turnmill centers. The PUMA SMX5100L is the largest machine in the series, with a maximum turning diameter of 32.7" and maximum turn length of 120.1". Chuck sizes of 15", 18" and 21" are available for the standard main turning spindle, which features a 49.6 horsepower built-in motor that spins at 2,400 r/min. For more information, visit www.doosanmachinetools.com.
[5] NEW EMUGE MICRO END MILLS AND CHUCKS OFFER EFFICIENT MACHINING OF CHALLENGING MATERIALS Cutting tools and accessories supplier Emuge Corp., West Boylston, Massachusetts, has announced the introduction of its new micro end mills and micro milling/drilling chucks for a wide range of applications such as die and mold, medical and more. The micro end mills feature a patented neck design with up to 10x diameter, enabling reach into deep contours. For optimal machining performance, a high radial bending strength withstands alternating stress on the cutting edge and relieved neck. The new Emuge end mills offer high-speed cutting finishing of 2D and 3D contours, and are offered in square, ball nose and torus end types. Featuring a short, stable cutting geometry, the end mills are available in solid carbide and CBN designs. For more information, visit www.emuge.com.
BORIDE OFFERS THREE NEW FINE GRIT CERAMIC STONES BORIDE Engineered Abrasives, Traverse City, Michigan, a manufacturer of abrasive products for industrial and consumer applications, has extended its offering of Ceramic Super Stones to include three new fine grits: 1500, 2000 and 3000. This new series page 29
Mold Polishing & Repair
Providing the Latest Technology for:

Micro-TIG Welders Ultrasonic Polishers Laser Welders Finishing Stones Power Tools Diamond Abrasives Mold Polishing Classes
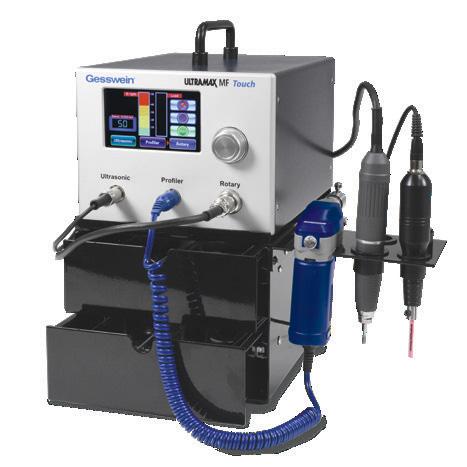
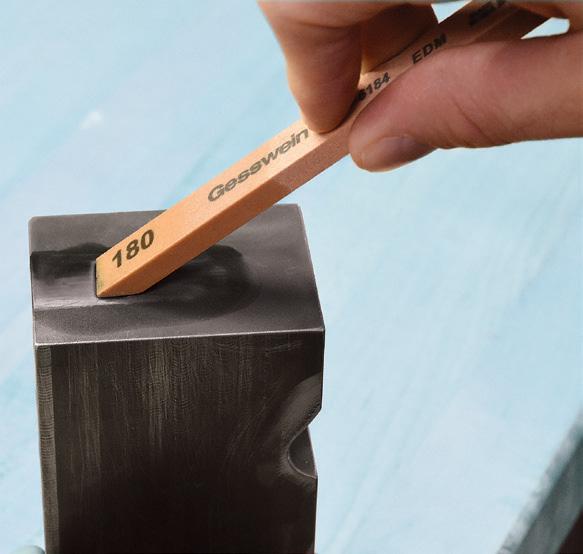

page 27
7
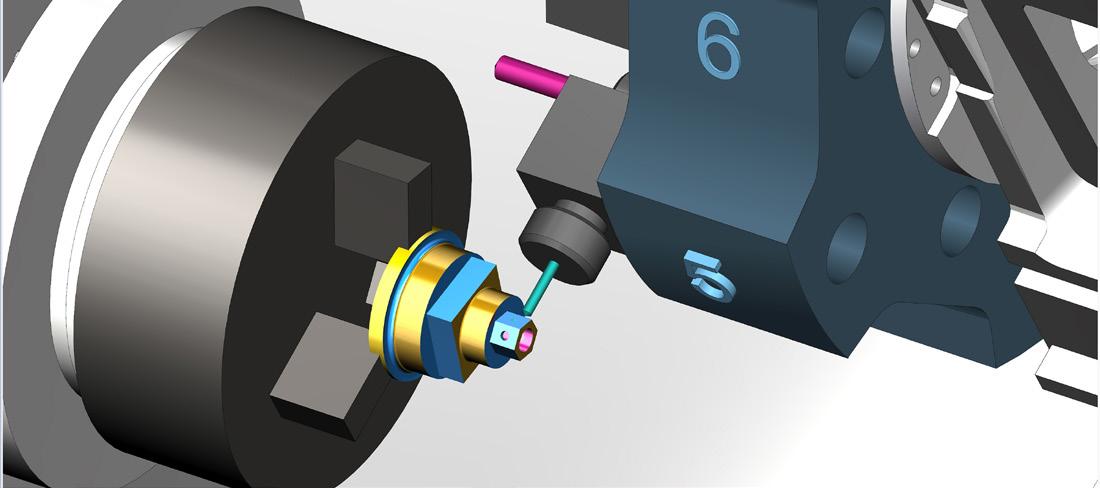
is for semi-finishing, final finishing and mirror polishing on any mold and die, leaving a smooth, polished surface and excellent polishing results. Ceramic Super Stones are an excellent choice for fine detail polishing. They are strong, flexible and non-loading for use on all types of materials, and also are thin for use in tight ribs and slots. The complete line of Ceramic Super Stones now is available in 12 grits, ranging from 80 to 3000 and in over 20 sizes. For more information, visit www.borideabrasives.com.
[6] HRSFLOW INTRODUCES HYFLOW Hot runner systems producer HRSflow, San Polo di Piave, Italy, has introduced HyFlow, a technology developed for applications with hydraulically actuated cylinders, in which the opening and closing speeds and the positioning of each pin can be adjusted precisely via the oil flow rate. HyFlow uses a controller with a user-friendly interface to set the lock position of each pin. The opening and closing speed for each nozzle can be set by a manual adjustment mechanism, allowing for controlling the melt flow rate so that cascade injection molding results in a uniform mold filling process without sudden pressure drops and associated surface defects. The positioning of the pin also allows for balancing of the pressure distribution in the cavity during the entire injection process. For more information, visit www.hrsflow.com.
KENNAMETAL INTRODUCES THE KCFM™ 45 FACE MILLING CUTTER Industrial technology provider Kennametal Inc., Pittsburgh, Pennsylvania, has introduced a new face milling platform for cast iron applications, the KCFM 45. With fixed and adjustable pocket seats, the new milling cutter provides the option for semi-finishing as well as fine-finishing applications, exceeding the highest surface quality requirements. With carbide, ceramic and PcBN inserts, the tool is a flexible, cost-effective and user-friendly solution for any type of CNC machining center. Carbide inserts are ideal for machining at lower RPM, or in thin-walled workpieces and less stable conditions, while ceramic inserts (KY3500 grade) provide elevated surface speeds that result in higher productivity. For fine finishing operations, PcBN inserts will deliver the best possible surface finish, tool life and throughput. For more information, visit www.kennametal.com. [7] CGTECH ADDS ADDITIVE SIMULATION CAPABILITIES TO VERICUT Irvine, California-based CGTech introduced the new release of VERICUT version 9.1.1, along with other VERICUT modules, including additive and composites applications. VERICUT CNC machine simulation, verification and optimization software simulates all types of CNC machining, including mill/turn and parallel kinematic/hexapods, drilling and trimming of composite parts, additive and hybrid manufacturing, water jet, riveting, robots and more. It operates independently but also can be integrated with leading CAM systems. VERICUT software version 9.1.1 has new features and enhancements to boost productivity and streamline workflow, including a refined AUTO-DIFF display, streamlined optimization controls for faster NC program optimization, a units converter in Tool Manager to easily switch between metric and imperial values, and enhancements to the CAD/CAM and tooling interfaces. For more information, visit www.cgtech.com.
SECO TOOLS EXPANDS RANGE OF JETSTREAM TOOLING® HOLDERS FOR GENERAL ISO TURNING Seco Tools, Fagersta, Sweden, a provider of metal cutting solutions, has announced the expansion of its Jetstream Tooling® Integrated (JETI) technology with a complete range of holders for general ISO turning. This internal coolant technology increases tool life dramatically while shortening set-up and indexing times, thanks to a new single-screw insert clamp design and the absence of external hoses. By placing high-pressure coolant directly in the cutting zone, JETI technology ensures superior chip and temperature control. For further process optimization, holders equipped with Jetstream Tooling® Duo feature a second coolant outlet from the clearance side that can be turned on or off. As a result, manufacturers can run much higher cutting data without impacting application security for any ISO-S, ISO-M or ISO-P turning application. For more information, visit www.secotools.com.
TECH SOFT 3D AND OPEN MIND COLLABORATE ON CAM SOLUTIONS OPEN MIND Technologies AG, Wessling, Germany, a developer of CAD/CAM software solutions, and Tech Soft 3D, Bend, Oregon, a provider of engineering software development toolkits, have announced the availability of HOOPS Exchange. HOOPS Exchange is a CAD data access and reuse technology for manufacturing and architecture, engineering and construction (AEC) workflows that will be integrated into hyperCAD®-S and hyperMILL® to ensure that all CAD and product manufacturing information (PMI) data are transferred seamlessly between applications. hyperMILL® is a modular CAM solution for 2.5D, 3D, 5-axis, HSC/HPC and millturning processes. The CAM software provides geometry analysis and tool path calculations. For more information, visit www. openmind-tech.com and www.techsoft3d.com.
WORKFORCE TRENDS, SALARY FREEZES AND NEW DATA IN ANNUAL WAGE REPORT
By Rachael Pfenninger, director of strategic execution, AMBA
When comparing wage data from 2019 to 2020, more than 70% of jobs in the US mold building industry experienced wage increases in 2020. Across the board, mold manufacturing positions experienced an average of a 7% increase in compensation (approximately $1.41 per hour), according to the most recent Wage and Salary Report published by the American Mold Builders Association.
Now in its tenth year, AMBA’s annual Wage and Salary Report analyzes data collected from mold building executives on reported wages of more than 50 different job classifications within mold manufacturing organizations. The 2020/2021 report includes data from over 95 US mold manufacturing companies, representing nearly 4,000 full-time and part-time employees.
Of the 50+ job titles analyzed in this year’s report, 40% of the positions revealed a greater than 5% growth in compensation (a rise in 12% over last year). The positions reporting the most significant rises in compensation include inspectors, purchasing agents/buyers, press operators and quality managers – all of which experienced an average of a 30% wage increase over last year’s reported data.
New to this annual survey is the addition of the CNC programmer – 5-axis role. Added with insights provided by AMBA mold manufacturing members, this position represents those employees who have received specialized training in 5-axis machines. On average, CNC programmers with specialized 5-axis training receive $1.87 per hour more than CNC programmers without specialized training.
Overall, the significant rise in compensation is promising for the mold manufacturing industry and indicates that it is looking to improve internal operations and job quality now more than ever. However, given that 17% of mold manufacturers reported a current salary freeze due to continuing economic conditions, this trend may falter in the coming months as the COVID-19 pandemic continues. Over the next 12 months, 67% of respondents plan to hire additional employees (a 3% increase when compared to 2019 data), while 12% report no plans to hire new employees in 2021 (no change from last year’s data).
The need to find skilled people to fill technical positions continues to significantly outweigh the need to fill administrative and leadership positions. Of the positions that respondents report needing to fill, 82% of the jobs are technically based. Administrative positions make up 12% of open positions, while leadership positions represent only 6% of jobs needing to be filled in 2021.
Of all data reported in this year’s 2020/2021 AMBA Wage and Salary Report, the most alarming is the continuing workforce age trend. This year, the percentage of employees 50 years or older hit an alltime high of 43%, while the percentage of employees ages 18 to 50 fell to 57% (a drop of 4% from last year’s data). Although the arrival and continued stay of the COVID-19 pandemic likely has hindered workforce development efforts – as open houses were canceled, schools were closed, employees were furloughed and businesses were shut down – these data highlight the acute need to continue efforts to attract younger generations of employees and establish a succession plan that can survive an aging workforce.
Hiring Forecast for the Next 12 Months
No, 12% Not Sure, 21%

Yes, 67%
Although economic times are difficult for many, there may be some opportunities for mold manufacturers to entice new talent to their facilities. For instance, while 75% of this year’s respondents report offering merit increases based on performance, less than onequarter offer across-the-board increases – something that could be considered when the company as a whole succeeds, particularly because younger generations thrive on being a part of the “bigger picture” and the company’s overall goals.
For more information or to purchase the report, visit www.amba.org.
80%
Workforce Age Trend
70%
60%
50%
40%
30% 70%
68% 67% 64% 61% 61% 61%
59% 58% 57%
32%
30% 36%
33% 41% 42% 43%
39% 39% 39%
20%
10%
0%
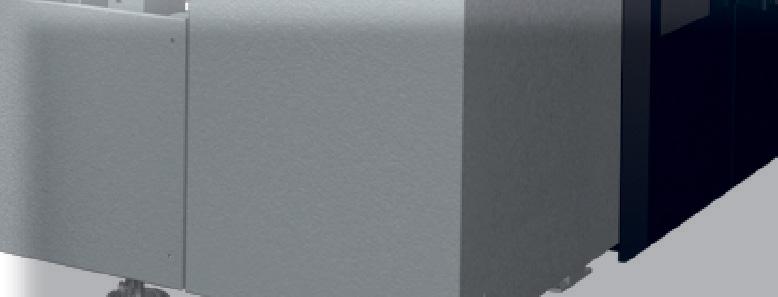

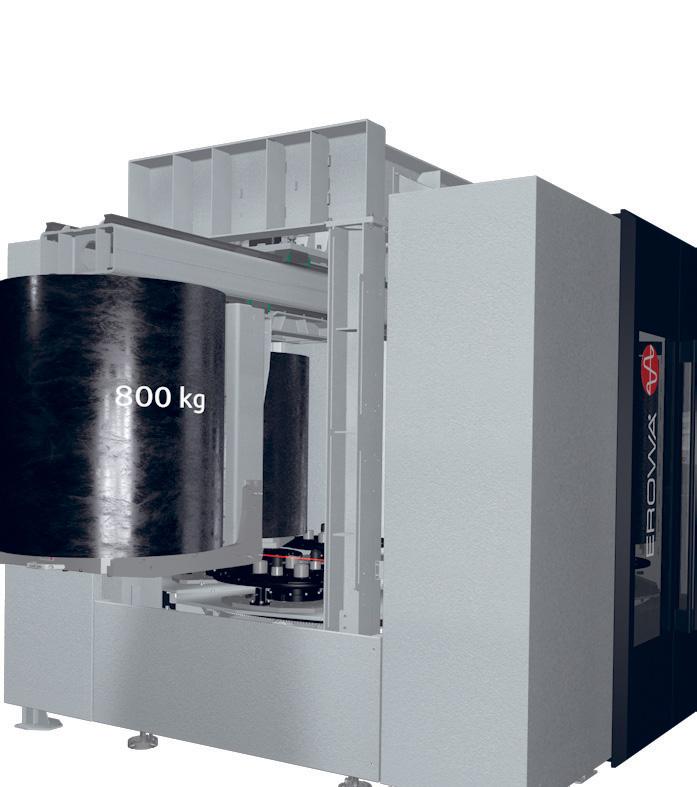
Robot Easy 800
The Robot Easy 800 features a compact design, high degree of con gurability and a transfer weight of up to 800kg. The 7 ton magazine capacity can be con gured with 6 to 12 positions using various pallet sizes. The Robot Easy 800 has 2,000mm of reach and only takes up 20 sq/ft of oorspace making it the ideal solution for heavy loading made easy.

1

4
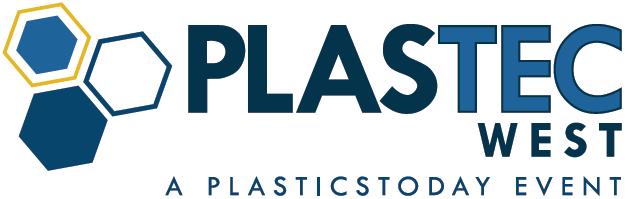
MEUSBURGER PROVIDES CAD TOOL FREE OF CHARGE Standard parts provider Meusburger, Wolfurt, Austria, has developed a CAD tool that is available free of charge. This tool is coordinated with the Siemens NX CAD system and enables designers to carry out a simple and time-saving design process. Configurations of components that are native in the system can be selected and all parameters automatically are adjusted. Installation spaces and the color table standards developed by Meusburger and the Association of German Tool and Mould Makers also are integrated in the tool. The parts list automatically is updated when changes are made. For more information, visit www.meusburger.com.
[1] IWARRIORS LAUNCHES NEW WEBSITE iWarriors – a 501(c)(3) nonprofit whose mission is to honor severely injured soldiers from all branches of the US armed forces by providing personalized technology packages to aid in their rehabilitation and recovery – has launched a new website. The website features information about the organization and its mission, and about the US military recipients of personalized technology packages, including photos and testimonials from grateful recipients. The site also includes application information for injured service members who would like to be considered as recipients, and information for making donations, for purchasing branded merchandise and for setting up individual and corporate yearly sponsorships. For more information, visit www.iwarriors.org.
[2] HEIDENHAIN DONATES NUMERIK JENA ENCODERS TO SUPPORT ASPE STUDENT CHALLENGE Twelve NUMERIK JENA LIKgo encoders from motion control feedback solutions provider HEIDENHAIN, Schaumburg, Illinois, were donated to support the ASPE Student Challenge. These 2 3
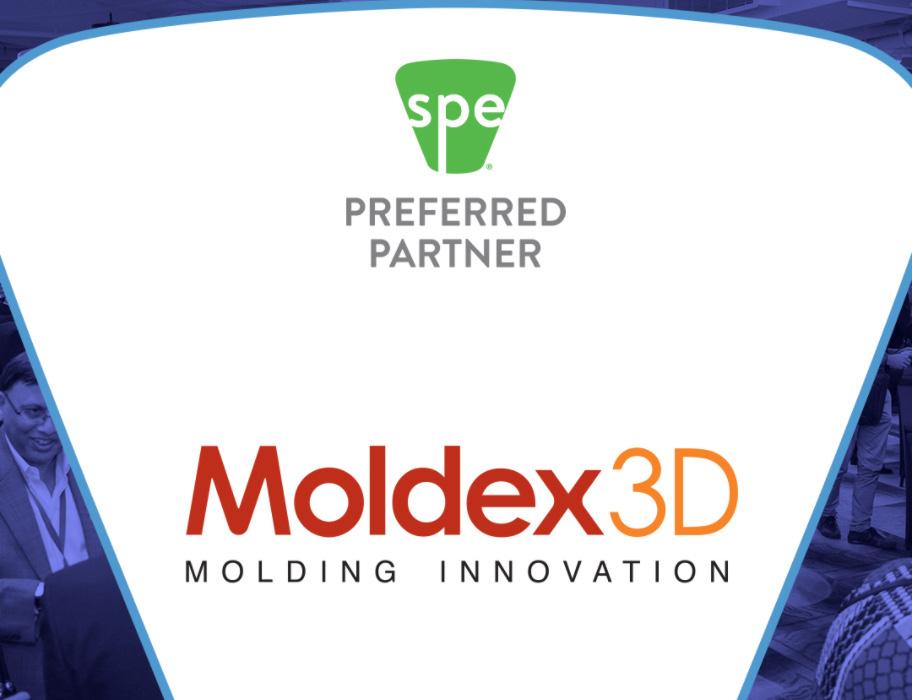
encoders were used in the six critical XY stages being provided to the student teams for use in the competitions. The goal of the 2020 Challenge was to build a scribe tool controller and Z-axis mechanism that can be integrated with an XY scanning platform to produce a mechanical ruling system. The universities competing included The University of Texas at Austin, North Carolina State University, University of Michigan, University of Michigan – Dearborn, The Chinese University of Hong Kong and Navajo Technical University. For more information, visit www.aspe.net/35th-annual-meeting/35thannual-meeting-student-challenge/.
KRUSE TRAINING LAUNCHES MOLDING DEFECTS LEVEL 2 Kruse Training Inc., Naples, Florida, a developer of interactive online training programs, is introducing Molding Defects Level 2 to its training program. The self-paced, interactive, step-by-step training builds on the company’s successful Level 1 online training. The goal of this section is to teach the causes of common molding defects and how to prevent them. The training combines interactive parts, animations, simulations, videos, quizzes and multimedia presentations. Molding Defects Level 2 users will learn about various molding defects that can occur during the injection molding process; will gain an understanding of how part design, mold design and the injection molding process impact molding defects; and will analyze molded parts to learn the cause and effect behaviors of design and process. For more information, visit www.krusetraining.com.
SUPERIOR DIE SET PARTNERS WITH TOOL PLANNERS TO OFFER ESTIMATING SOFTWARE Steel and aluminum product provider Superior Die Set Corporation, Oak Creek, Wisconsin, announced that the company has aligned with Tool Planners, Inc., as the exclusive distributor of Tool Planners’ DieEstimator software for global representation. DieEstimator, the die cost estimating software, is a solution to the traditional, timeconsuming quoting process and quickly adapts to the way shops quote, providing Superior Die Set customers with greater consistency and more accurate pricing compared to a ballpark estimate in calculating the cost of dies. Jeff Bennett, Tool Planners, Inc., founder, owner and president, created the software to be a comprehensive product based on years of solving difficult die problems for metal
page 32
stampers and die shops. After the software is installed, online training videos are available for quick use of the tool, and it is compatible with any Apple or PC device and effective on multiple browsers. For more information, visit www.superiordieset.com.
[3] MOLDEX3D ANNOUNCED AS SPE PREFERRED PARTNER The Society of Plastics Engineers (SPE) announced that plastic injection molding industry solution provider CoreTech System Co., Ltd. (Moldex3D), Taiwan, has been named as an SPE Preferred Partner. An SPE Preferred Partner is a converter, manufacturer, solutions provider or product distributor that has been recognized by SPE for demonstrated leadership and innovation in the plastics industry. Their products and services are valuable to SPE’s members. “We are very honored to be named as an SPE Preferred Partner,” said Dr. Rong-Yeu Chang, Moldex3D CEO and a fellow of SPE. “Providing global customers with advanced and innovative technologies and services has always been Moldex3D’s mission. SPE’s recognition certainly gives us more momentum to assist industries to level up their competitiveness in the ever-changing global market.” For more information, visit www.moldex3d.com and www.4spe.org.
[4] NORTH AMERICA MANUFACTURING EVENT ANNOUNCES NEW 2021 DATE PLASTEC West has announced that the 2021 edition of the conference and exhibition – typically held in February – now will be held August 10-12, 2021, at the Anaheim Convention Center in Anaheim, California. In the interim, Informa Markets – Engineering brought the manufacturing community together in late November for Virtual Engineering Week, five days in a virtual setting featuring networking, education, buyer and seller sourcing. For more information, visit www.plastecwest.com.
AMERIMOLD MOVES TO SEPTEMBER 2021 The annual Amerimold show will return in 2021 to the Donald E. Stephens Center in Rosemont, Illinois, on September 22nd and 23rd. The show organizers anticipate that, in a post-COVID world, moldmakers, molders, OEMs and tier suppliers will be eager to come to together to network, build their brands and learn. The 2020 edition of the event – Amerimold Connects – was held virtually in June, and the livestreamed sessions still are available for viewing. For more information, visit www.amerimoldexpo.com.
Services
• Finishes to all SPE-SPI standards • Diamond Lapping • Textured Surface Prep • Benching • Quoting from Drawings,
Prints, Pictures and Parts • On-Site Support
Capabilities
• 50+ Polishers • 40 ton Capacity • 24 hours – 7 days • Pick-up and Delivery • 3-D CAD File Capabilities
Partnerships
• Welding • Plating • Texturing
Gets you to market faster
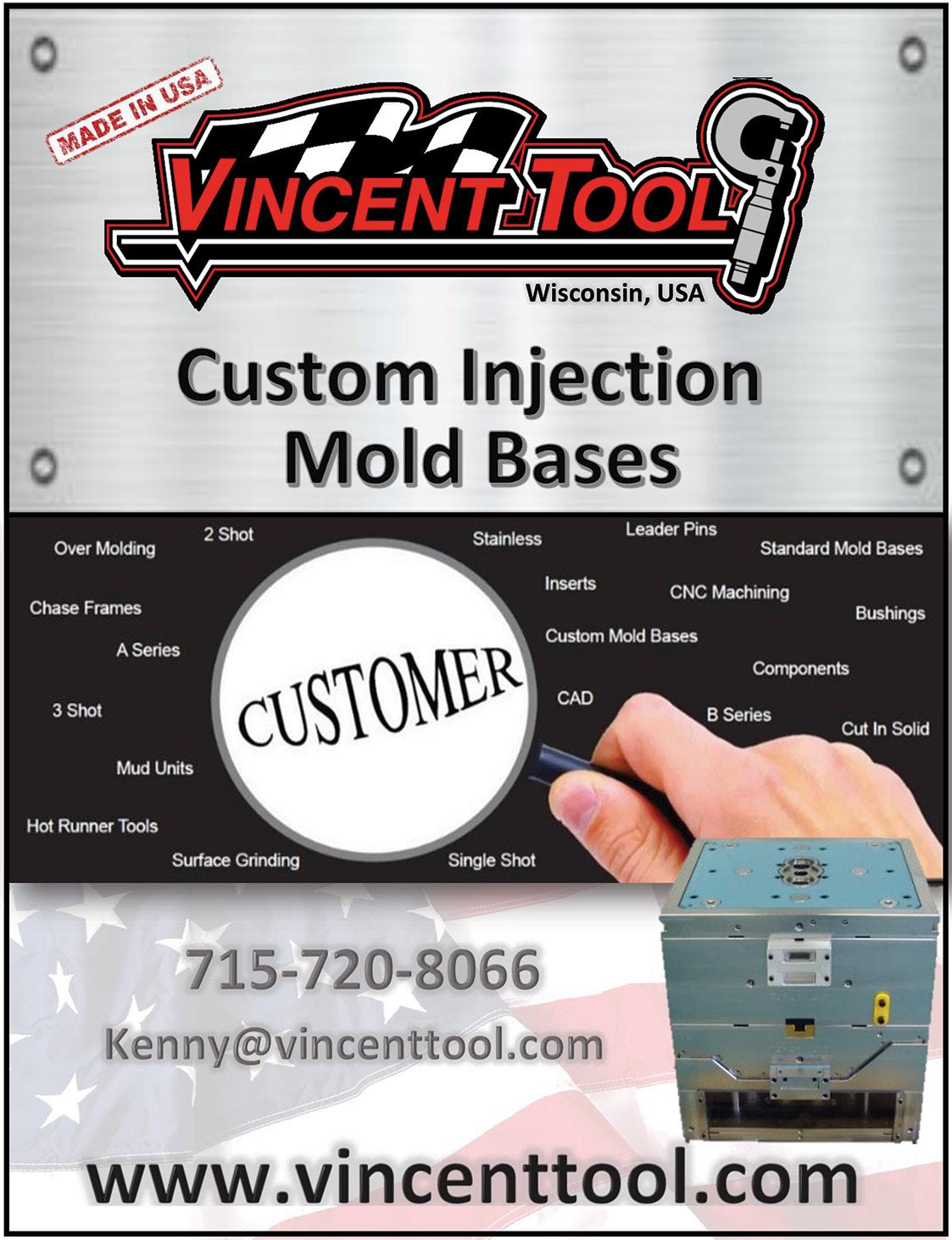
ISO 9001-2015 CErTIFIED
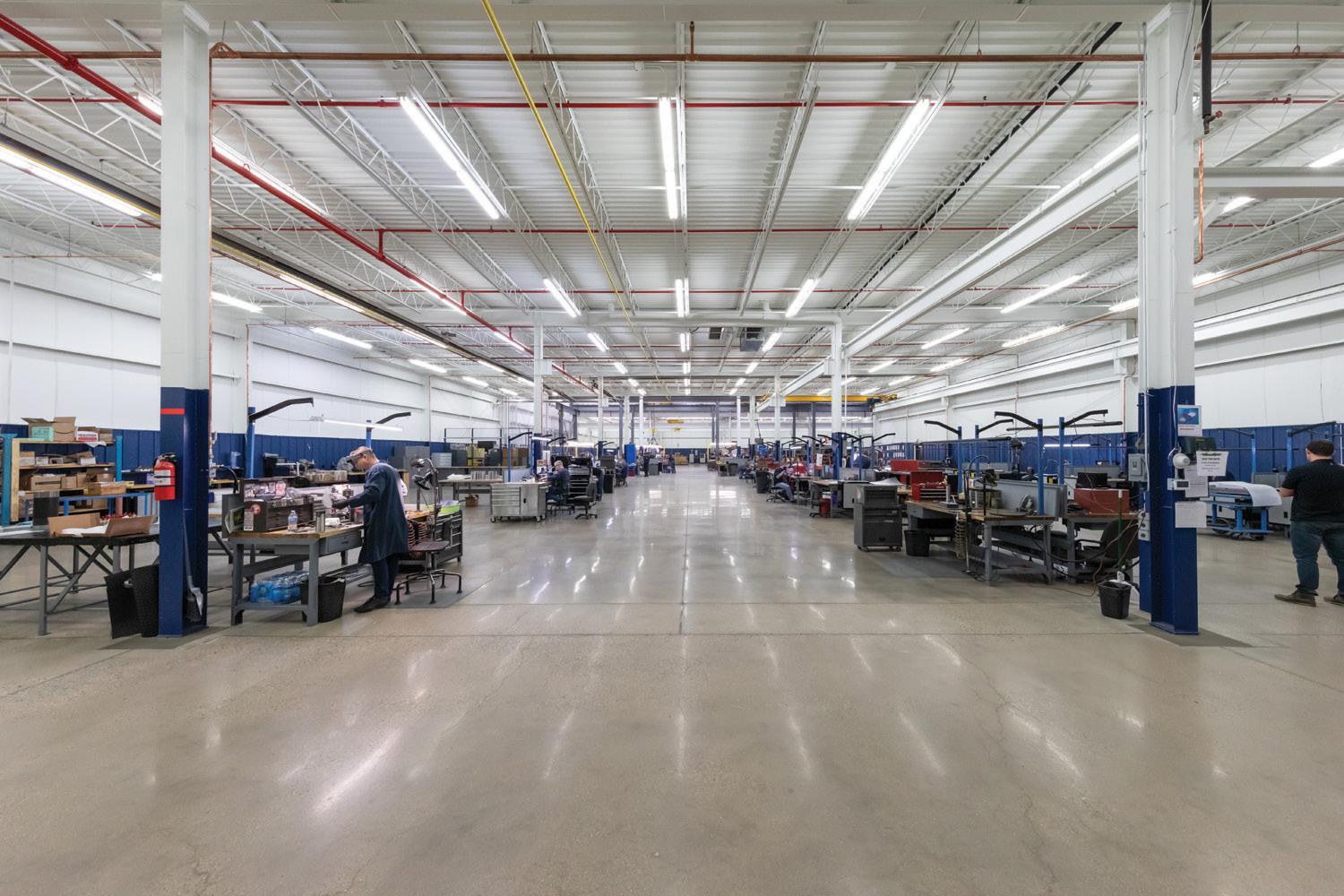
1320 Holmes Rd., Elgin, Illinois
Ph: 847-352-5249
Fx: 847-352-4052 sales@ultrapolishing.com
www.ultrapolishing.com
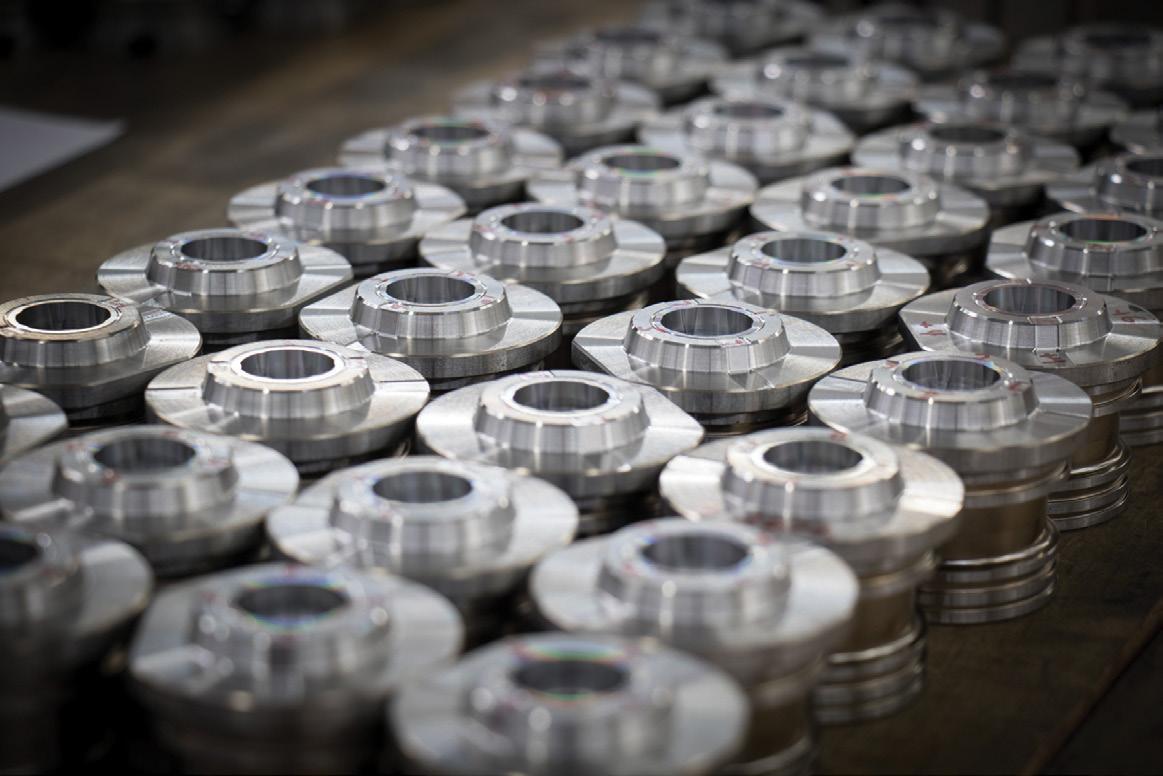
HEALTHCARE TRENDS TO INFLUENCE 2021 INSURANCE RATES
By Dianna Brodine, managing editor, The American Mold Builder
Predicting health insurance rates for 2021 is a difficult task. In some ways, the pandemic has resulted in declining healthcare costs in the current year: Individuals have reduced nonemergency visits to physicians and hospitals, and telehealth appointments have become more prevalent. On the other side of the coin, treatments and hospitalizations for COVID-19 and related illnesses have driven costs higher, and mental health treatment frequency has increased as the pandemic stretches on. As insurers submitted their 2021 rates ahead of the October 15 deadline for the health insurance marketplace, the Kaiser Family Foundation (a nonprofit organization focused on national health issues) found most insurers intend a modest increase or decrease in premium costs in the upcoming year.
“The most common factors that insurers cited as driving up health costs in 2021 were the continued cost of COVID-19 testing, the potential for widespread vaccination, the rebounding of medical services delayed from 2020, and morbidity from deferred or foregone care. At the same time, many insurers expect health care utilization to remain lower than usual next year as people continue to observe social distancing measures and avoid routine care, especially in absence of a vaccine or in the event of future waves of the virus,” KFF explained.1
However, insurance costs remain a major financial factor for both employer and employee. KFF’s annual Employer Health Benefits Survey, released in October 2020, showed, “Annual premiums for employer-sponsored family health coverage reached $21,342 this year, up 4% from last year, with workers on average paying $5,588 toward the cost of their coverage.”2
The report also pointed out that, “Since 2010, average family premiums have increased 55%, at least twice as fast as wages (27%) and inflation (19%).”
Businesses continue the fight to find ways to reduce healthcare costs, employing strategies that range from incentives for healthy habits to in-house wellness visits. The following article, originally printed in Plastics Business magazine (www.plasticsbusinessmag.com), provides another perspective on reducing healthcare costs – a collaborative on-site clinic shared by four Minnesota-area businesses.
1. 2021 Premium Changes on ACA Exchanges and the Impact of COVID-19 on Rates, accessed Nov. 18, 2020, https://www.kff.org/private-insurance/issue-brief/2021-premium-changeson-aca-exchanges-and-the-impact-of-covid-19-on-rates/ 2. Average Family Premiums Rose 4% to $21,342 in 2020, Benchmark KFF Employer Health Benefit Survey Finds, accessed Nov. 18, 2020, https://www.kff.org/health-costs/press-release/ average-family-premiums-rose-4-to-21342-in-2020-benchmark-kff-employer-health-benefit-survey-finds/
REVAMPING HEALTHCARE AT VITAL PLASTICS by Lara Copeland, contributing writer, The American Mold Builder
Across the business landscape, companies are employing creative strategies to draw in new talent while also trying to hold onto current employees. Attractive incentives – like flexible hours and good pay – are among some of the leading priorities potential employees are looking for; however, affordable and unique healthcare packages also are top contenders. Some large corporations, such as Amazon, Apple and Facebook, have been offering on-site health clinics for a number of years, but this growing trend is making its way into smaller companies, too. The modern on-site health clinic not only treats injured employees, it also addresses overall health and wellness.
MOTIVATION FOR CHANGE In January 2019, Vital Plastics, located in an industrial park just east of the Twin Cities metro area in Minnesota, became self-insured, offering healthcare, dental and short-term disability plans for its 112 part-time and 110 full-time employees and their families. Additionally, in July 2019, this custom injection molding and contract assembly
company – along with two other businesses and a local school district – opened a shared, on-site health clinic.
According to Vital Plastics President George Hauser, two main factors motivated the company to make this move. “We looked at it as a differentiator,” he said. “At the time we started participating in this conversation, attracting and engaging employees was quite difficult. So, we did something to be different, look different and feel different – we wanted to be appealing to people so they could see the value in our company.”
Company-sponsored healthcare offered another advantage. “The other thing we were striving to do is to control our healthcare costs,” Hauser added. “Every year we are faced with increases, and it just wasn’t sustainable anymore.” He commented that becoming self-insured and offering the on-site clinic were two ways Vital Plastics could get control of its healthcare costs and establish transparency. The company had spent money in the past offering wellness services, like a mobile blood unit or offering a copay for health memberships, but Hauser found that those services weren’t getting much “lift,” as he put it. “We simply decided to redirect our dollars,” he explained.
The clinic is staffed with a couple of medical assistants and a nurse practitioner. It operates 40 hours each week, but its schedule is staggered so that it can accommodate employees from various shifts. And, despite being shared among four entities and a large pool of insureds, people are seen very quickly.
As for the self-insured healthcare plan, Hauser remarked that it is “virtually the same plan we had when we were insured through a regular carrier. The only difference now is we fund it ourselves and have a third-party administrator while also having an over-line protection to help protect us from catastrophic issues.”
COLLABORATION AND COMPLIANCE Becoming self-insured and opening an on-site clinic still may be a rarity, but as healthcare costs go up, the concept continues to attract interest. For others looking to implement something similar, Hauser mentioned some facets that have worked well for Vital Plastics and what a company should think about when considering such a paradigm shift.
“We collaborate well with the other companies in our group, and we have the ability to customize our specific plan to meet our own needs,” he said. “I don’t have to offer the exact same plan as the others in our group, but some items do need to be the same.” He continued, saying that while another company in the group offers to cover parttime employees, Vital Plastics only covers full-time employees. “We also can set different copay prices, for example.”

Hauser also emphasized the importance of staying compliant with any health savings account (HSA) regulations. “With an HSA, we can’t offer the clinic for free, so we ended up doing preventive care for free,” he explained. In this case, any diagnostic care is a $25 copay, but Vital Plastics contributes enough to the HSAs for these copays to be covered. He said there’s “room for maneuvering, but make sure you remain compliant,” while also noting that it is “important to research vendors and make sure you know who your administrator and your clinic provider is.
“Every single one of our plans is going well,” Hauser assured. “We are 17 months into the insurance plans and about 10 months into the clinic, and I can say that participation in each of these has increased over time.”
Vital Plastics is not resting on its laurels though. In 2020, the company added an incentive to its health savings account. If an employee goes to the on-site clinic for a physical, which is free, Vital Plastics makes an additional contribution to their HSA. “This has been well taken advantage of and well received,” Hauser noted. As the company moves forward, controlling healthcare costs remains a top priority.
“We did not increase health premiums in 2020, and if I stay on trajectory this year, I can hold healthcare costs again for another year,” Hauser commented. Vital Plastics also strives to create more responsibility for the user. As for now, he is pleased with all aspects of the company’s healthcare offerings. “We are ahead of the game with all of our healthcare plans – we were last year, and we are again this year. That tells me that we’re doing it right.”
UV SURFACE AND AIR DISINFECTION DEVICES: LET THE BUYER BEWARE!
By Castine A. Bernardy, Nicola M. Elardo, Alexa M. Trautz, and James P. Malley, Jr., Ph.D., Environmental Engineers, University of New Hampshire
Worldwide concern over the risk of contracting or spreading COVID-19 has sparked widespread interest in using UV devices for air and surface disinfection. The purpose of this article is to provide tips to the consumers and users of UV devices intended to inactivate air and surface pathogens. That market contains thousands of different products, with over 50 million UV products sold to consumers since March 2020. Unfortunately, these products lack uniform validation protocols, manufacturing specification, or guidelines. Therefore, consumers need to be informed before purchasing or using UV devices.
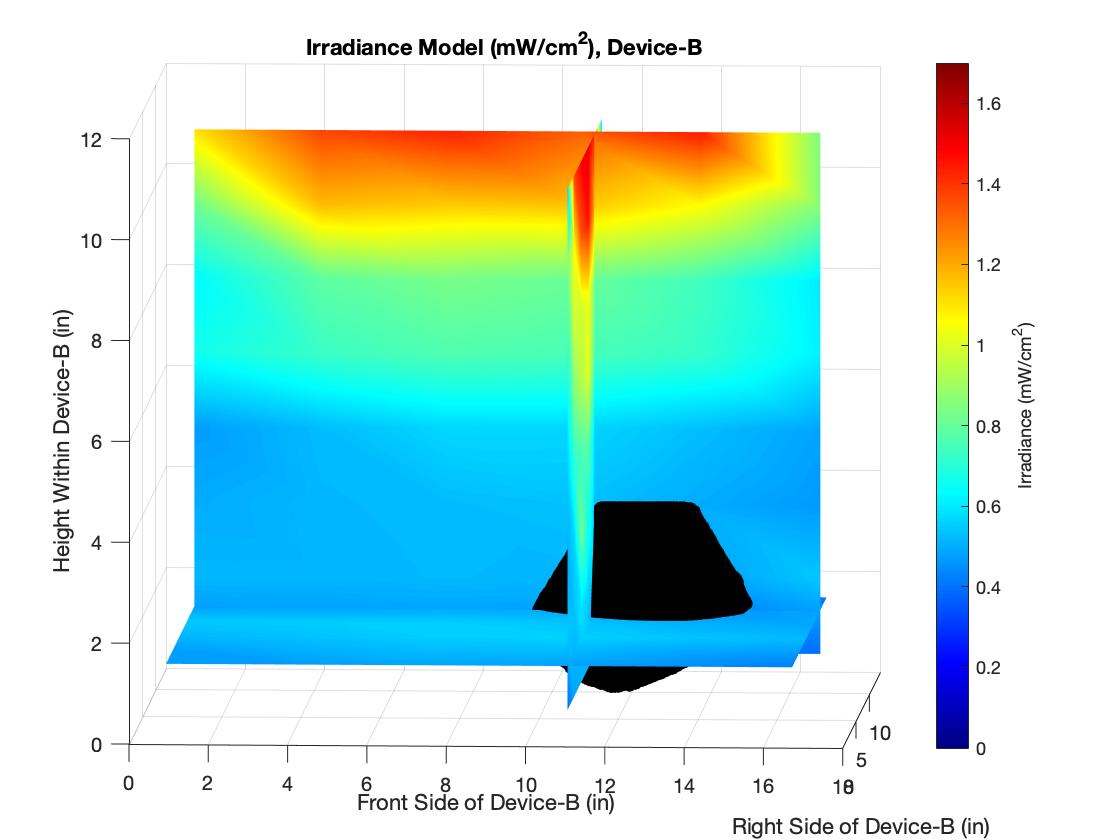
There are three types of UV light commonly discussed in disinfection. UV-A and B wavelengths come from the sun and reach the Earth. UV-C wavelengths vary from 200 to 280 nm and are emitted from these purchased UV devices.
Generally, the lower the wavelength, the greater the photon energy of the light that is being emitted by the device. This is important to note when discussing disinfection due to the sun, as UV-A and UV-B have longer wavelengths. While disinfection from the sun may be demonstrates that many regions of a typical UV device (blue) deliver
possible, the time required to achieve adequate disinfection from the sun is excessive and often results in desiccation of the pathogen before it is inactivated by the UV ray.
WHAT YOU SHOULD KNOW Often the information provided by advertisements and many very brief user manuals for UV devices simplifies operations to talking about time, instead of dose. Dose is the measurement that is recommended by all UV professionals because time is not the most important factor. The effectiveness of any UV device or application depends upon at least four key factors: a) the irradiance or fluence rate of the light source at specific wavelength(s) emitted (some refer to this as intensity or strength of light, but those are vague, nontechnical terms), b) the optical geometry of the UV device, or how it is to be applied, c) the type of organisms to be targeted, including their action spectra and what percent removal (or log inactivation), geometry and organism characteristics are far more important than time.
Figure 1. UV Heat Map – Highest UV Dose (red) to Lowest UV Dose (blue).
map” of a typical device disinfecting a KN95 mask (black). The heat map measures the sum of all optical factors that affect delivered UV dose, as confirmed by UV radiometer readings. The figure is desired and d) contact time. Of these lamp characteristics, optical
a very low UV dose and will produce poor disinfection.
One way to determine if the UV device is effective at inactivating the pathogen of interest is by using UV dosimeter badges. UV dosimeter badges are reusable or single-use labels that change color as they receive UV radiation. When purchased, a pack of dosimeter badges will come with a color scale that matches each color to a UV dose. With this tool, the user visually can see if the required dose for disinfection has been achieved by matching their badge to the corresponding color on the scale after dosing. Thus, UV dosimeter badges offer consumers an easy way to confirm a UV device has done its job.
SAFETY CONCERNS Virtually all UV devices come with warnings about the potential electrical hazards and about the fact that UV light is known to cause harm to skin and eyes. page 40
page 39
Dosing human and animal tissues with any forms of UV energy should not be done by the buyers and users of these UV devices. Special cases performed by experienced medical professionals under very tightly controlled conditions for very specific medical problems may be found in internet searches, but “do not do this at home” is the message for buyers and users of UV devices.
The current US and international guidelines set limits on maximum exposure to UV and highly recommend that living tissue should not be exposed to any forms of UV light unless it is prescribed and monitored by healthcare professionals.
Users must be vigilant to protect themselves from all direct, reflected or otherwise stray UV light when using any UV device, especially items such as UV wands.
In addition, ozone production is another potential hazard when operating enclosed UV devices. Normal use of UV devices for applying lower doses (0 to 100 mJ/cm2) to surfaces or air is being increased 10- to 20-fold (e.g., 2,000 mJ/cm2) to ensure PPE is adequately disinfected before reuse. The elevated doses may result in the unwanted generation of low levels of airborne ozone. Such ozone levels can cause minor irritation to the eyes, nose and throat, as well as low-grade headaches if people use these devices for extended periods of time.
In addition, the effectiveness of using UV wands is doubtful. Normal human limitations and error make it unlikely that consumers will hold the wand an appropriate distance from a surface, use the correct sweeping motion to cover the whole surface or expose the pathogen to a high enough UV dose to cause adequate inactivation.
Finally, it is extremely important to verify that you have purchased a quality UV device. Generally, the better-quality devices are hundreds to thousands of dollars and come with independent third-party testing data. However, price is not the only determinant for UV device excellence, and it is crucial to confirm that the UV device delivers the specified dose from the lamp by use of dosimeter badges. Finally, UV devices cannot replace the multiple barriers recommended by health experts to prevent the spread of diseases like COVID-19.
This article written under the supervision of Jim Malley, jim.malley@ unh.edu. For more information on UV disinfection technologies, visit www.uvsolutionsmag.com.
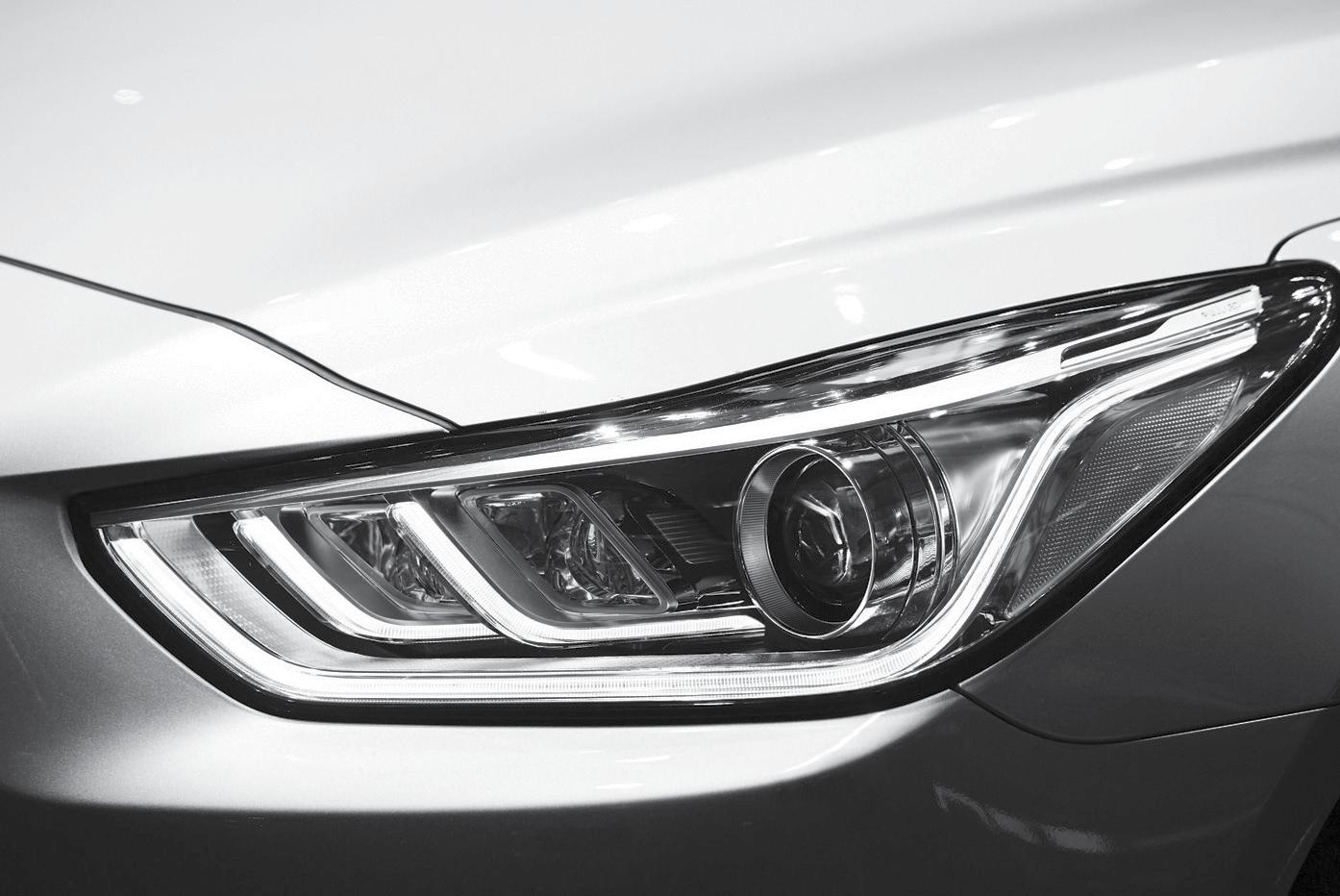
Steel for the Future
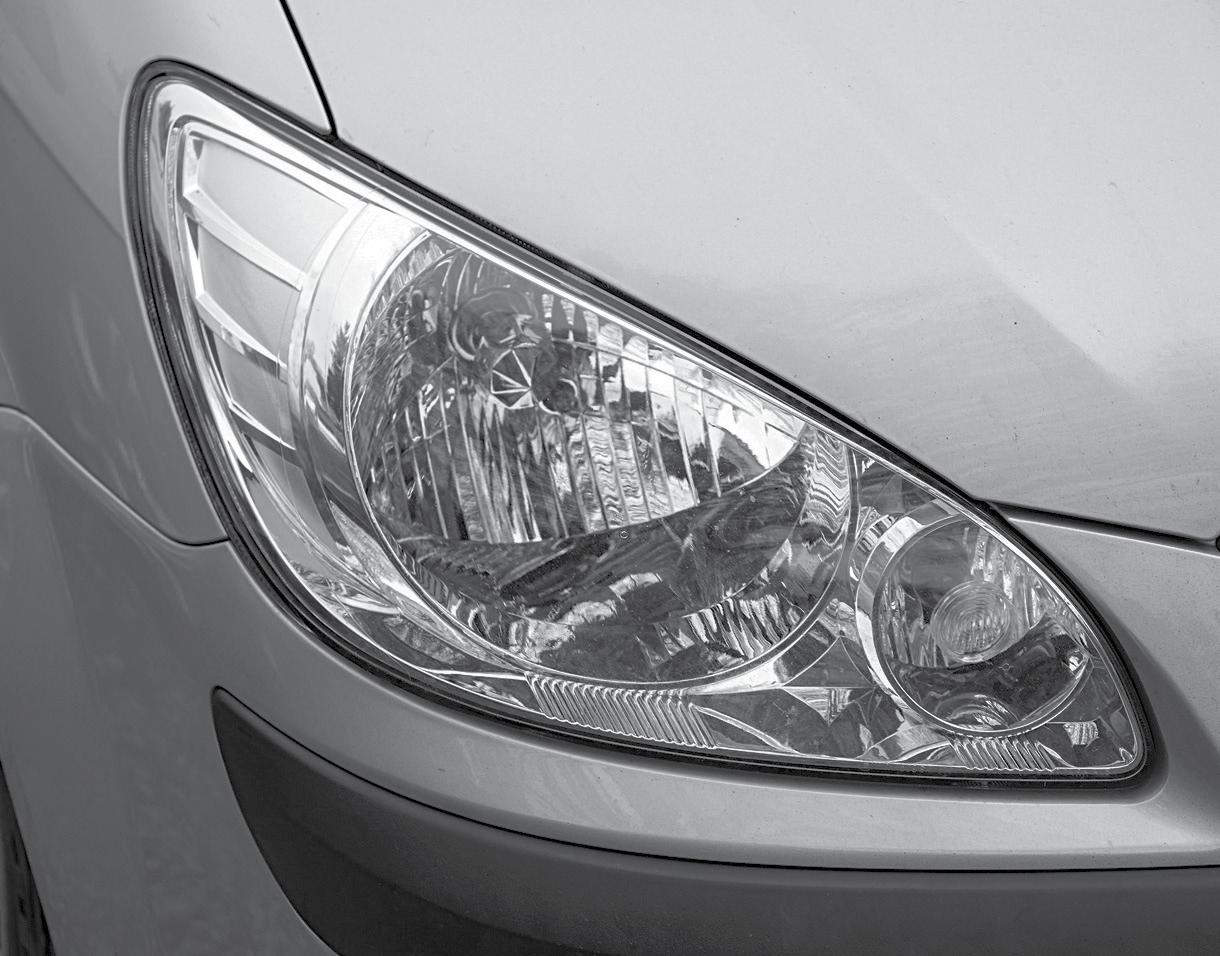
Superior visibility is the new standard in automotive lens tooling. Finkl Steel produces the highest quality mold steel guaranteed to SPI A1 finish for enhanced plastic injection clarity. Headlights have improved, shouldn’t your steel? www.finkl.com Chicago Composite Sorel 800-DIE-BLOCK 800-521-0420 800-363-5540 (USA) 800-363-9484 (CAN)
DECEMBER 2020 Building a Foundation: Buy-in, Accountability and Empowerment, December 9, 12:00 p.m. EST, www.amba. org/events
Preparing for 2021: Business Roundtable Discussion, December 16, 12:00 p.m. EST, www.amba.org/events
MARCH 2021 Sales & Marketing Virtual Summit, March 10-11, 2021, www. amba.org/events
MAY 2021 NPE2021, May 17-21, 2021, Orlando, Florida, www.npe.org JUNE 2021 Plastec East / MD&M East, June 15-17, 2021, New York, New York, www.advancedmanufacturingeast.com/en/shows/ plastec.html
AMBA Conference 2021, June 22-24, 2021, Grand Rapids, Michigan, www.amba.org/events
Alliance Specialties and Laser Sales................................................................www.alliancelasersales.com...................................................................................................23 AMBA Conference 2021 .....................................................................................www.amba.org.............................................................................................................................. 3 AMBA Membership..............................................................................................www.amba.org............................................................................................................................34 Boride Engineered Abrasives............................................................................www.borideabrasives.com......................................................................................................22 Crystallume, a Division of RobbJack Corporation.....................................www.crystallume.com...............................................................................................................15 Dynamic Surface Technologies........................................................................www.dynablue.com...................................................................................Inside Back Cover Erowa System Solutions......................................................................................www.erowa.com..........................................................................................................................31 Federated Insurance .............................................................................................www.federatedinsurance.com............................................................................................... 33 Finkl Steel .................................................................................................................www.finkl.com........................................................................................................................... 40 Gesswein...................................................................................................................www.gesswein.com...................................................................................................................27 Grainger.....................................................................................................................www.grainger.com.....................................................................................................................28 HASCO America, Inc...........................................................................................www.hasco.com...........................................................................................................................21 HEIDENHAIN CORPORATION..................................................................www.heidenhain.us..................................................................................................................... 7 INCOE Corporation............................................................................................www.incoe.com..........................................................................................................................10 Milicron.....................................................................................................................www.dme.net............................................................................................................Back Cover Mold-Tech Midwest..............................................................................................www.mold-tech.com.................................................................................................................17 MoldMaking Technology....................................................................................www.moldmakingtechnology.com.....................................................................................38 NPE2021....................................................................................................................www.npe.org................................................................................................................................ 41 PCS Company.........................................................................................................www.pcs-company.com...........................................................................................................13 Plastic Engineering & Technical Services, Inc. ...........................................www.petsgroupintl.com.......................................................................................................... 19 Progressive Components....................................................................................www.procomps.com............................................................................... Inside Front Cover Superior Die Set Corporation...........................................................................www.superiordieset.com ........................................................................................................22 Ultra Polishing, Inc................................................................................................www.ultrapolishing.com ......................................................................................................... 35 Vincent Tool............................................................................................................www.vincenttool.com.............................................................................................................. 35 Wisconsin Engraving Co. Inc./Unitex............................................................www.wi-engraving.com............................................................................................................12 YRC Freight .............................................................................................................www.enrollhere.net...................................................................................................................24

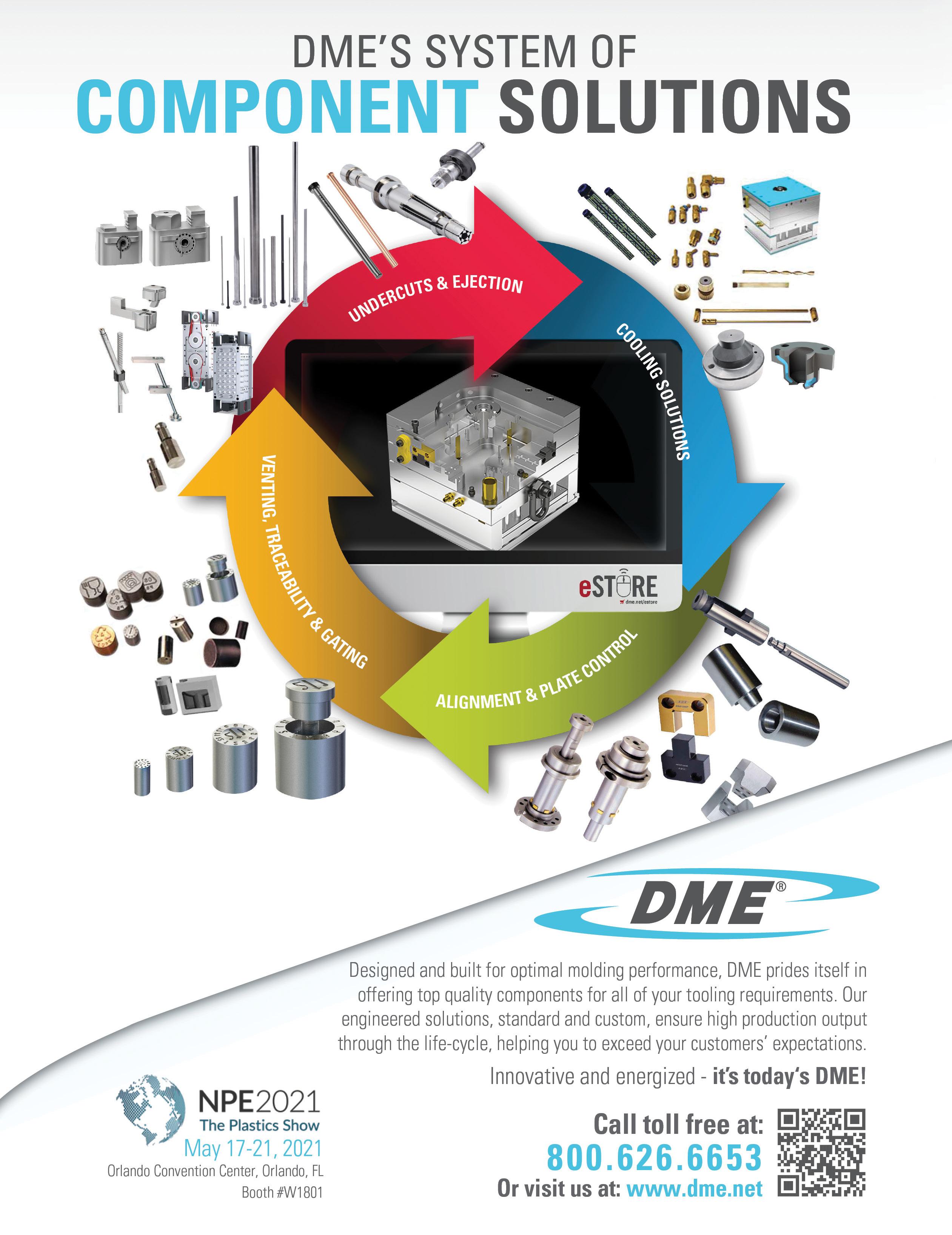