
12 minute read
COMPONENT RELIABILITY IN EMERGENCY VEHICLES
SYSTEM LEVEL CONSIDERATIONS FOR ENSURING COMPONENT RELIABILITY IN EMERGENCY VEHICLES


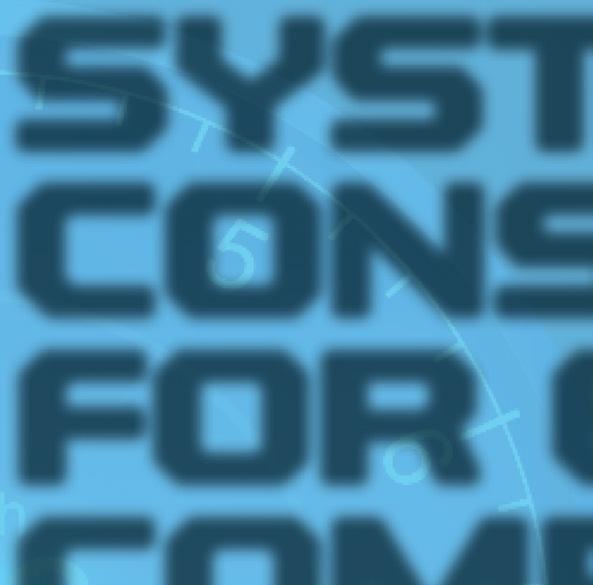
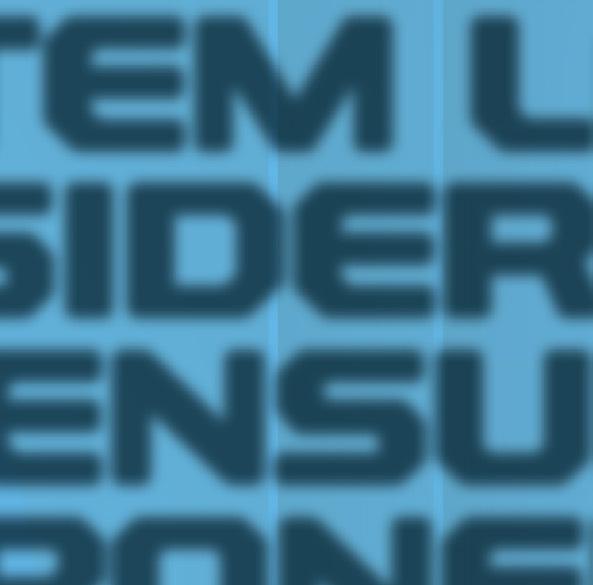
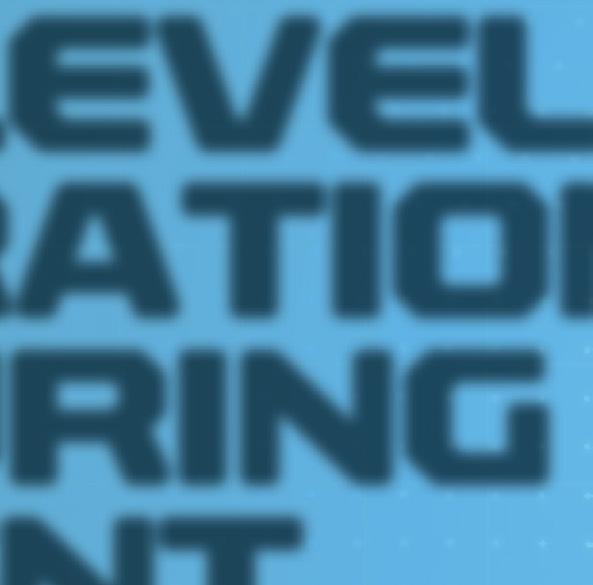
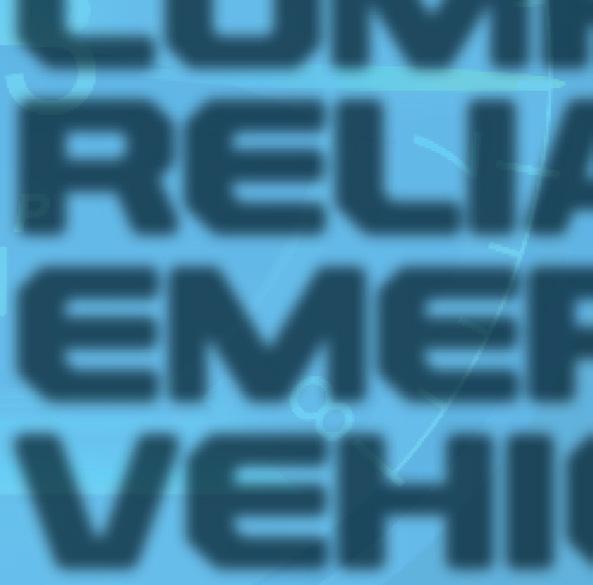
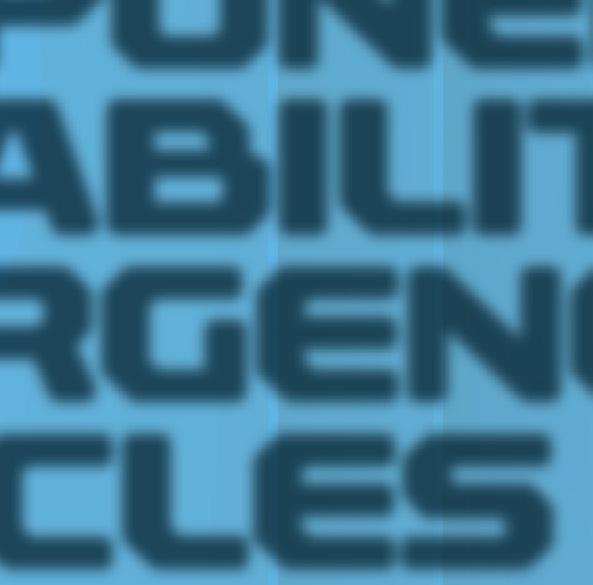
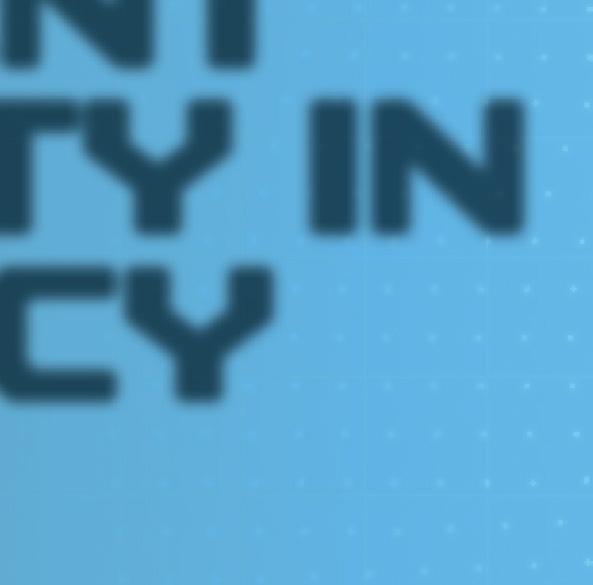

BY ERIC GRAHAM

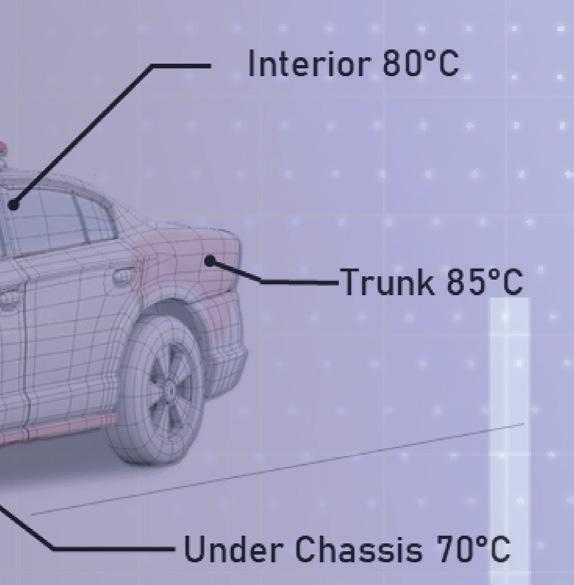






Police and emergency vehicles have increasingly become more complex with a growing number of systems and components required to support the expected operational readiness and mission scope. Beyond the traditional needs for lighting and siren control systems as well as radio communications, new technologies have become necessary mainstays for agencies and eets. In-vehicle computer systems and laptops have established a permanent place next to the driver’s console. Real-time, data-rich, secured communications with dispatch and data centers via 4G routers have replaced slow, radio-based uplinks. Video camera recording and storage systems are practically mandatory, as is the ability to upload recordings via WiFi or 4G networks. K9 units introduce more complexity than ever with life support systems, remote door release, and alarm reporting. is abundance of systems not only requires more space within the vehicle, they also are competing for that space with general safety and emergency equipment, weapons, and medical supplies. e competition for valuable real estate within the vehicle necessarily prioritizes items that require immediate availability, resulting in the majority of electrically powered systems being tucked away in increasingly smaller compartments such as center consoles, spare tire compartments, and engine compartments. Similarly, the multitude of power and control wires interconnecting these systems has grown with large wire bundles routed throughout the vehicles within minimal cableway spaces.
With the challenge of ensuring a robust vehicle installation that works awlessly for the expected operational lifetime, the potential for system or component failure is higher than ever. A wide range of individuals and groups are involved with the selection of components and systems, including up tters, eet managers, technicians, and end users. However, it is vitally important that the owner for the overall system success and safety be clearly de ned. During the system de nition stage for a build, the typical focus is on component selection and communication interoperability. While these are no doubt important areas of focus, an equally important yet often overlooked issue is the need to ensure safe and e ective switching, distribution and protection of the electrical power derived from the OEM vehicle systems.
Once a system of components is determined, the specifying agency has ultimate accountability for ensuring all components and associated electrical circuits can adequately operate in the intended vehicle system. While the responsibility of ensuring successful system performance can be delegated (e.g. to an up tter), the agency must make all e orts to ensure all potential risks are considered and addressed. At the component level, four critical questions need to be asked and answered for each system component in the expected installation location.

1. What is the expected moisture (water) and particle (dust) environment, and can the component operate as expected in those conditions? 2. What Electromagnet Interference (EMI) tests has the component passed and do those tests su ciently represent the stringent standards set by automotive OEMs? 3. What are the expected minimum and maximum ambient temperatures, and how has the component proven it can operate at those temperatures? 4. As part of the component temperature testing, what were the speci c test conditions and how do those conditions di er from the expected installation?
It is critical to recognize that while individual components are validated by manufacturers that market products as suitable for installation in emergency vehicles, those components are almost universally tested individually and with evaluation criteria that may or may not meet the needs of your particular build. Question #1 deals with the Ingress Protection (IP) provided by the component. We have outlined the sealing protection expectations for several IP levels in the attached table. Components designed to be installed in the engine compartment or outside of the body of the vehicle should resist both dust and water intrusion to ensure long life and hold an IP rating of IP66, IP67, or IP69K. Components located within the vehicle can carry a lower IP rating and some manufacturers simply do not provide a rating for such components. However, consideration should be made for likely dusty environments such as truck compartments before determining that an unsealed product would be su cient.

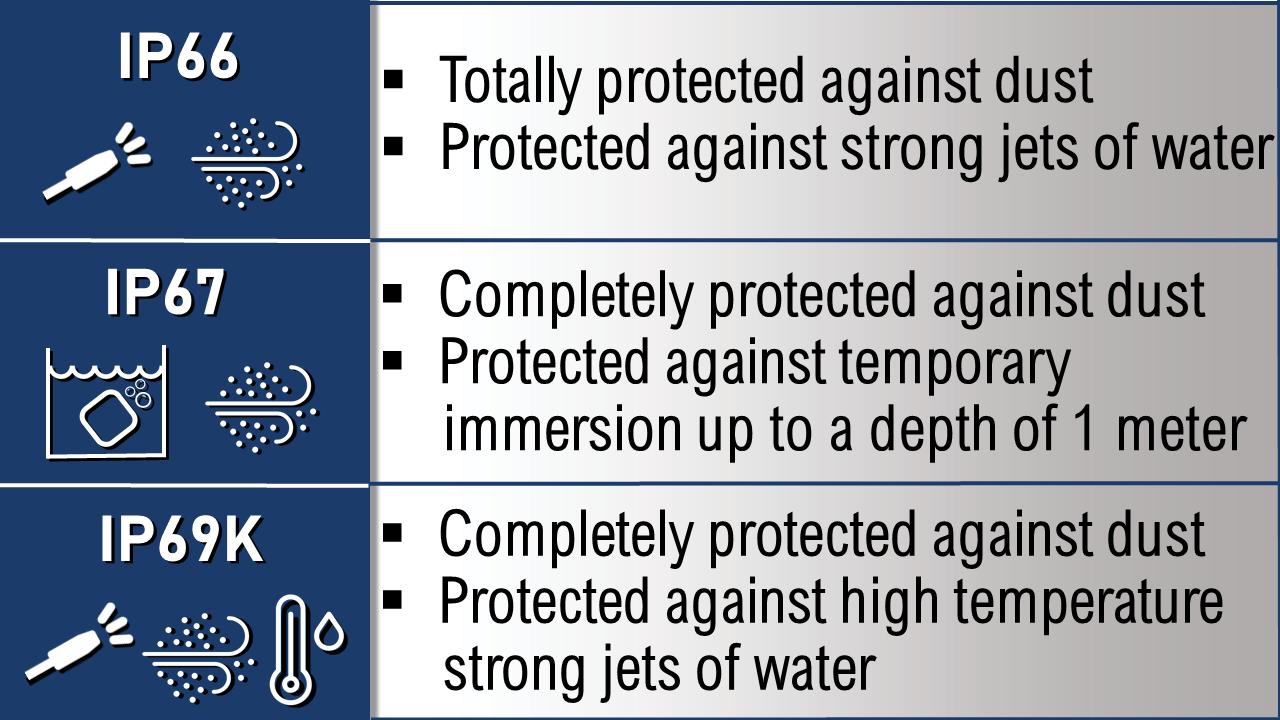
e second question relates to a component not causing excessive electrical emissions and similarly being able to withstand various levels of electrical abnormalities and emissions from other components. Well-vetted standards for limits of emissions and levels of immunity have been developed by SAE (J1455 & J1113) North America and ISO (11452) / IEC (EN 61000) in Europe. Additionally, vehicle components should be able to withstand potential electrical abnormalities caused by

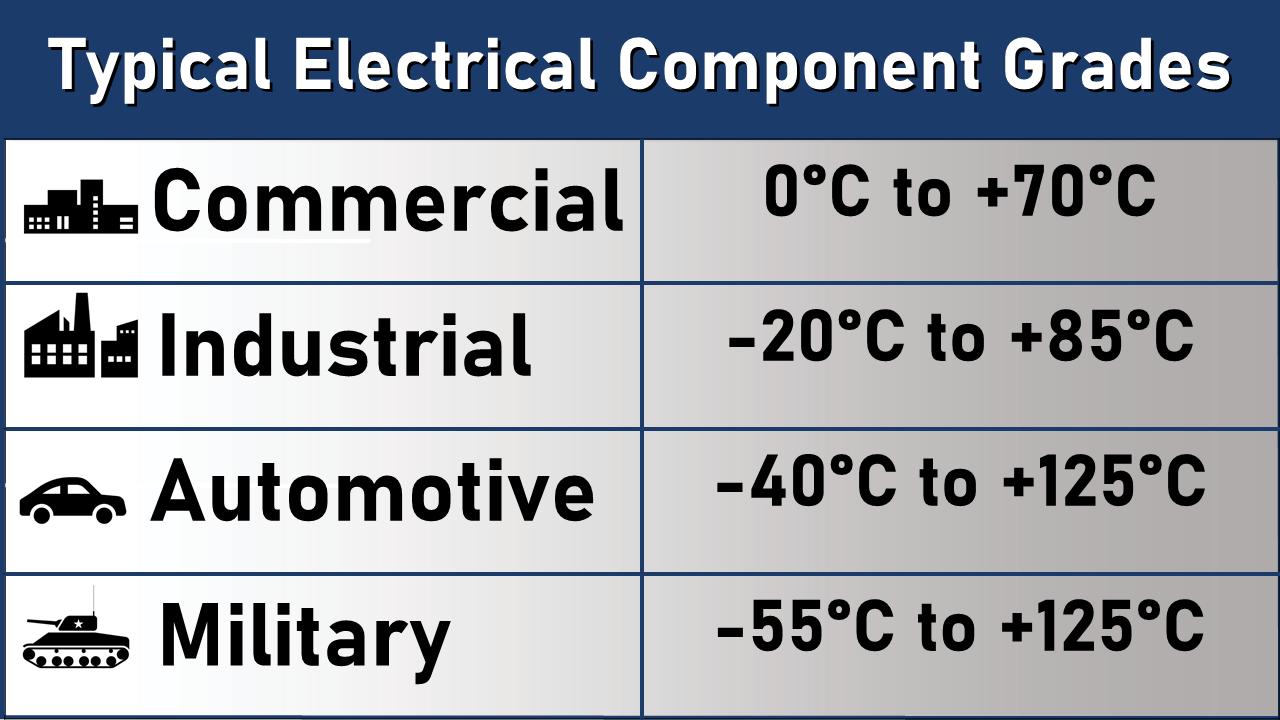
human error including over-voltage charging (+24V) and reverse polarity. While infrequent, these situations can and do happen and components must be able to withstand them and resume normal operation once the abnormality is corrected. e nal two questions involve operational temperature and require a detailed veri cation to ensure a successful system. Successful low temperature operation requires knowledge of the intended operational conditions. Vehicles used in the southern United States do not need to operate at the extremely low potential of -40 Deg C, which is the temperature a vehicle could be called to operate at in Minnesota,
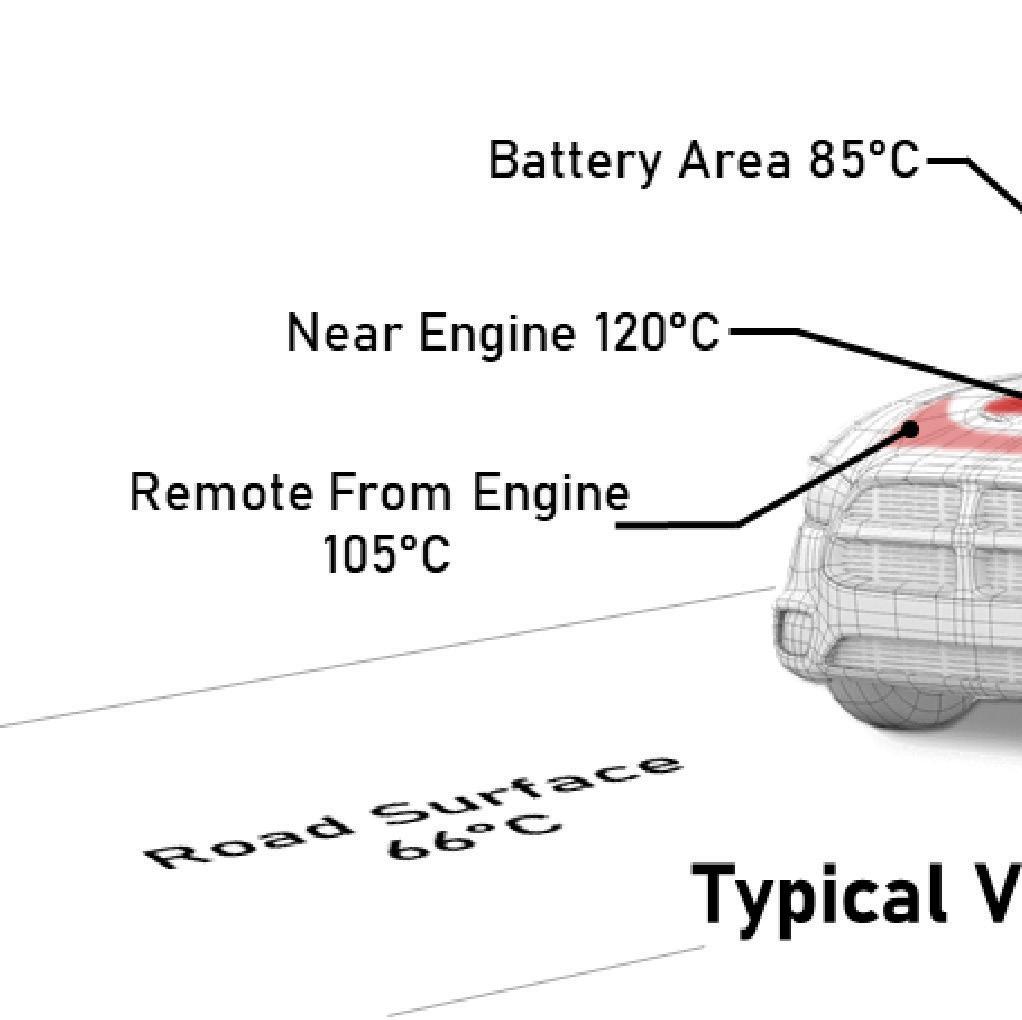
Wisconsin, Michigan, or the Canadian territories, for example. System components need to utilize automotive-grade electronics to ensure long-term operation in extremely cold weather. e typical operational temperature range of standard electronic component grades are shown here and should serve as a helpful talking point with component manufacturers.
Successful component operation at maximum ambient temperature involves examining two elements simultaneously and sometimes recursively. Understanding the maximum expected ambient temperature at each installed location is an important starting point. Maximum air temperatures
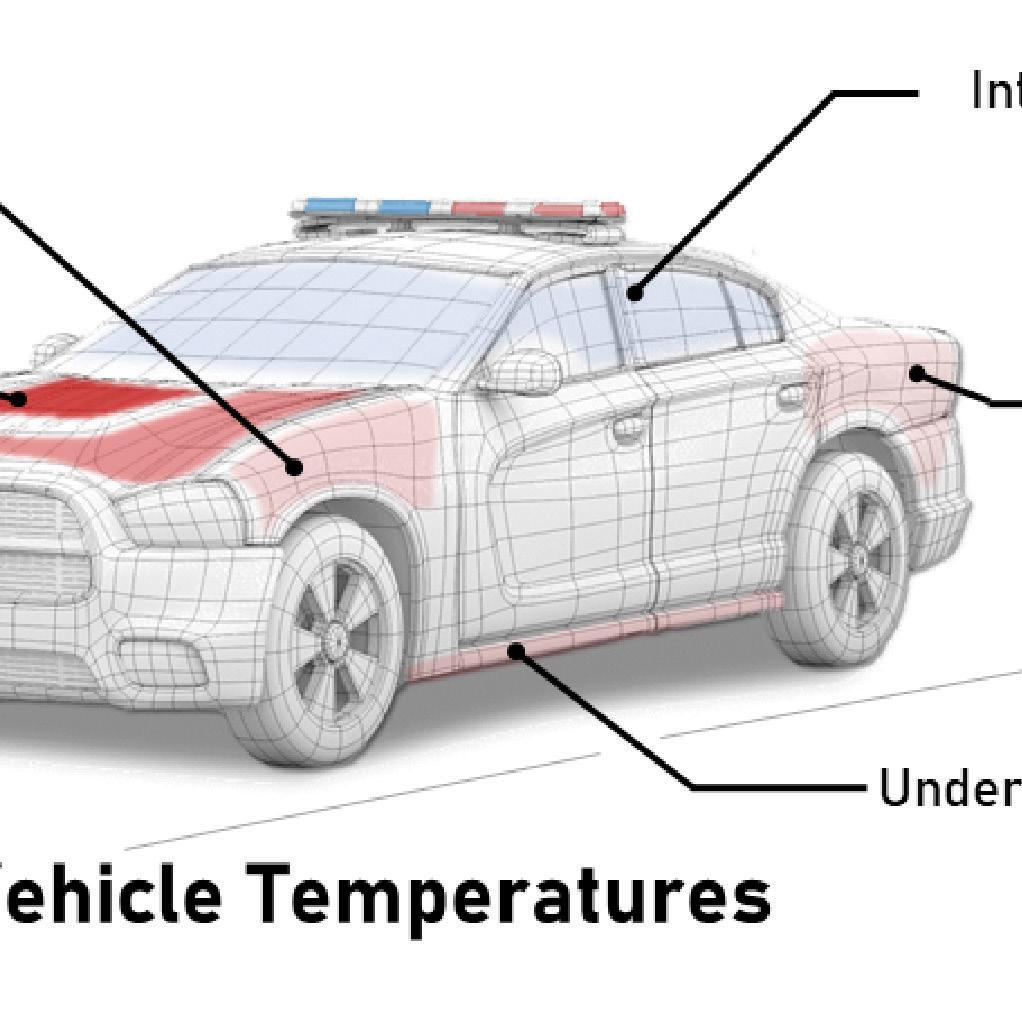

in various vehicle locations are outlined, where the values should be used as guidance but veri ed through testing if possible. Special care should be taken to examine components (and electrical wiring) located in small, enclosed spaces subject to self-heating such as center equipment consoles and other locations where one or more heat-generating components are located. In such cases, the spot ambient temperature could be much higher than typical maximum interior temperatures. ere is an additional factor that results in raising a component’s e ective ambient temperature. To understand this factor, it is important to recognize that emergency vehicle components are typically tested on their own (not part of a system) with electrical feed, return, and ground wires chosen to be representative on expected installs and ambient temperatures simulated by test chambers. Documenting what cable sizes and lengths were used by the manufacturer to verify component operation is an important element of this evaluation, as is comparing those cable sizes to those being contemplated for your system.
For components focused on delivering, protecting, or controlling electrical power, cable conductor sizes and lengths play a critical role in determining how much de-rating (the reduction of component capability) should be planned. Electrical components create signi cant internal heat



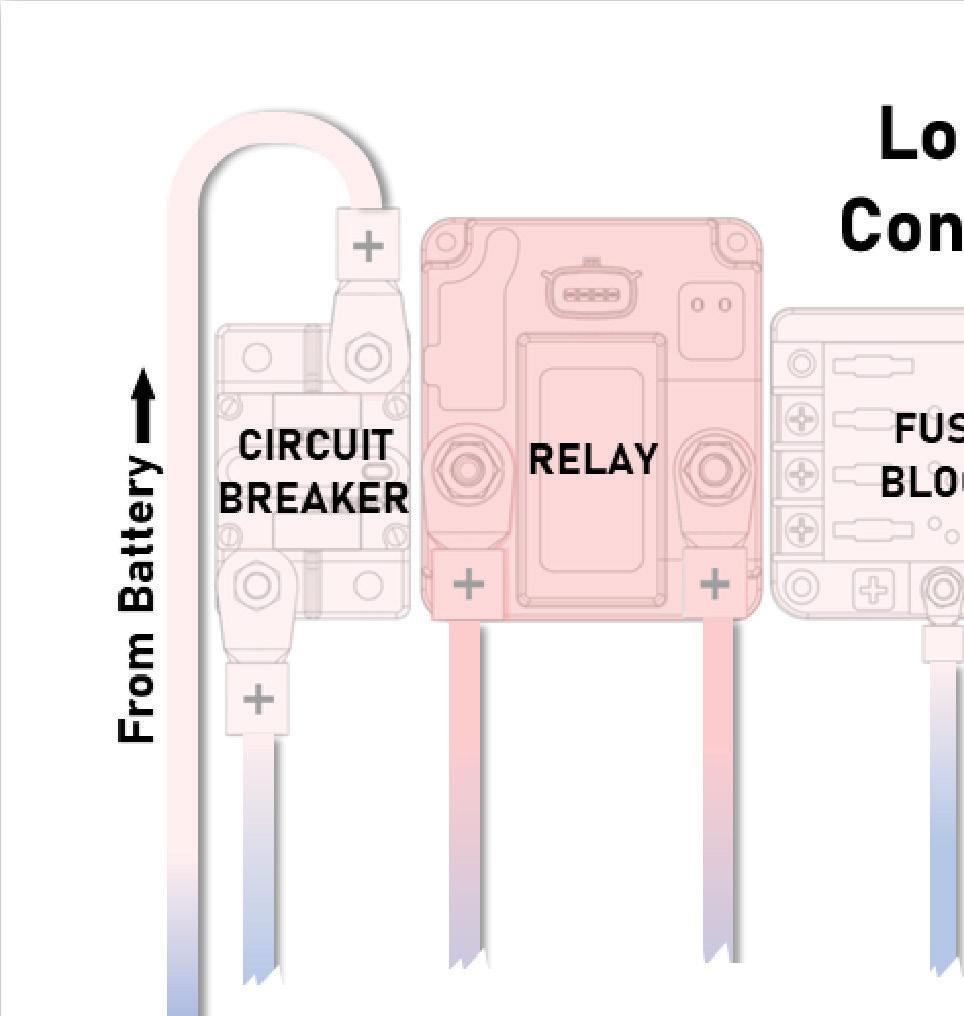

that must eventually be dissipated. Circuit breakers and fuses are designed to create this heat as part of their function, while solid state switches and mechanical relays also introduce elevated internal heating as they provide the ability to turn circuit on or o . is excess heat must be removed instead of building up inside the product until it exceeds internal material limits. Because the air inside a component is a poor conductor, the primary method of heat removal for vehicle electrical components is through the power cables entering and exiting the device and then from those cables to the surrounding air. e cables act as a cooling radiator that have an e ectiveness proportional to their gauge and length. Larger gauge cables not only conduct heat away from the device more quickly, they act to lower the conductor temperature far away from the component. is is because the cables themselves introduce heating; and for any given amount of current, a larger cable will be cooler than a smaller one. e length of cable provides a diminishing bene t the further away the conductor is from the component. is is because the cable dissipates heat to the surrounding air along its full length, but the temperature along its length is reduced until it reaches the ambient conductor/air temperature equilibrium. A rule of thumb on cable length for component cooling is that cable length beyond 4 feet from the component is no longer assisting in the cooling of the component. As a result of this knowledge, many published test standards for electrical components specify the test cable length to ensure consistency of expectations.
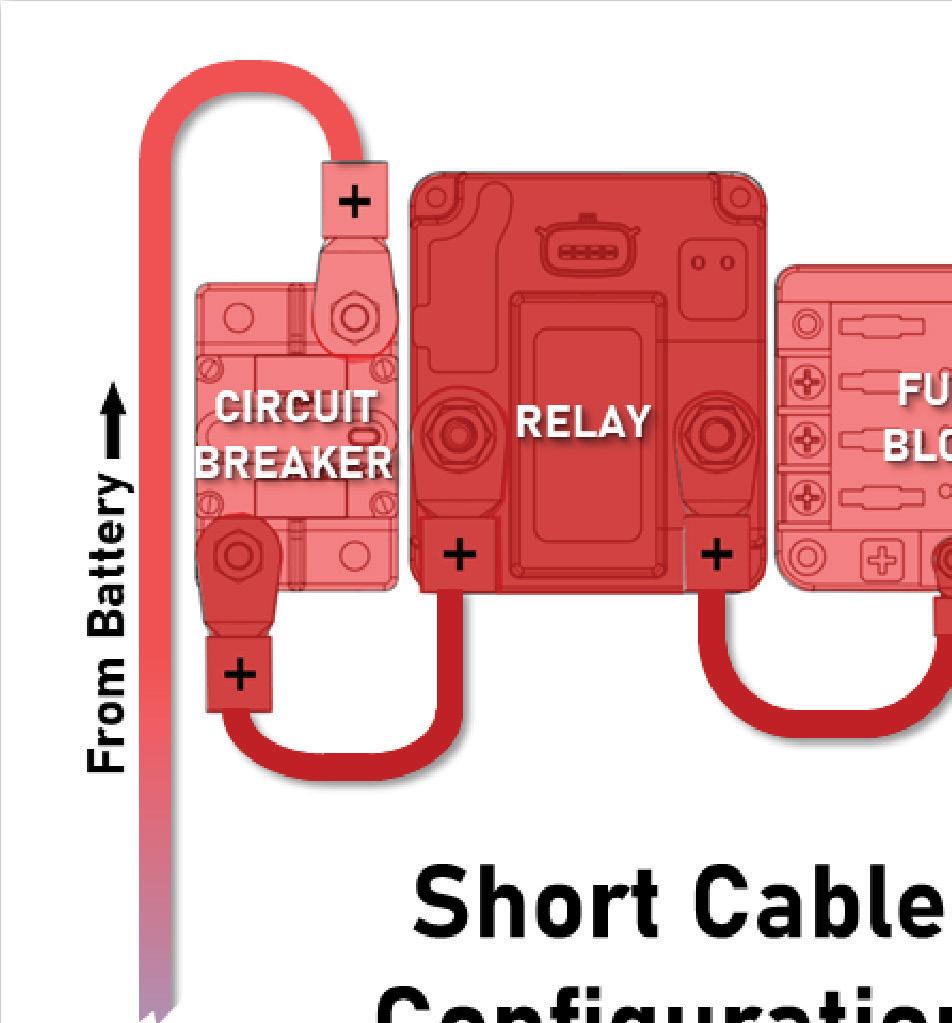

Understanding that cable length has a measurable e ect on elevated temperature component performance, system designers must rigorously evaluate and possibly reconsider component location, cable sizes, and cable lengths. Modern vehicle installs regularly combine multiple electrical components in close proximity, which results in very short cable connections between electrical adjacent components. is not only eliminates a critical cooling element for each component, it introduces an additional heat-generating component in close thermal proximity. e combination of these two e ects represents a signi cant potential degradation in expected component performance or capability that must be either planned or improved.
Two illustrations are included as examples of the comparative thermal equilibrium e ect due to length of wires between heatgenerating electrical components. Both diagrams re ect a power distribution element within an engine compartment with a circuit breaker (connected from the battery + terminal) with its output connected to a remote switching relay that is then connected to a fuse block designed to protect and distribute small gauge wires to the vehicle. e example with cable lengths su cient for dissipating the heat from each component results in component temperatures far



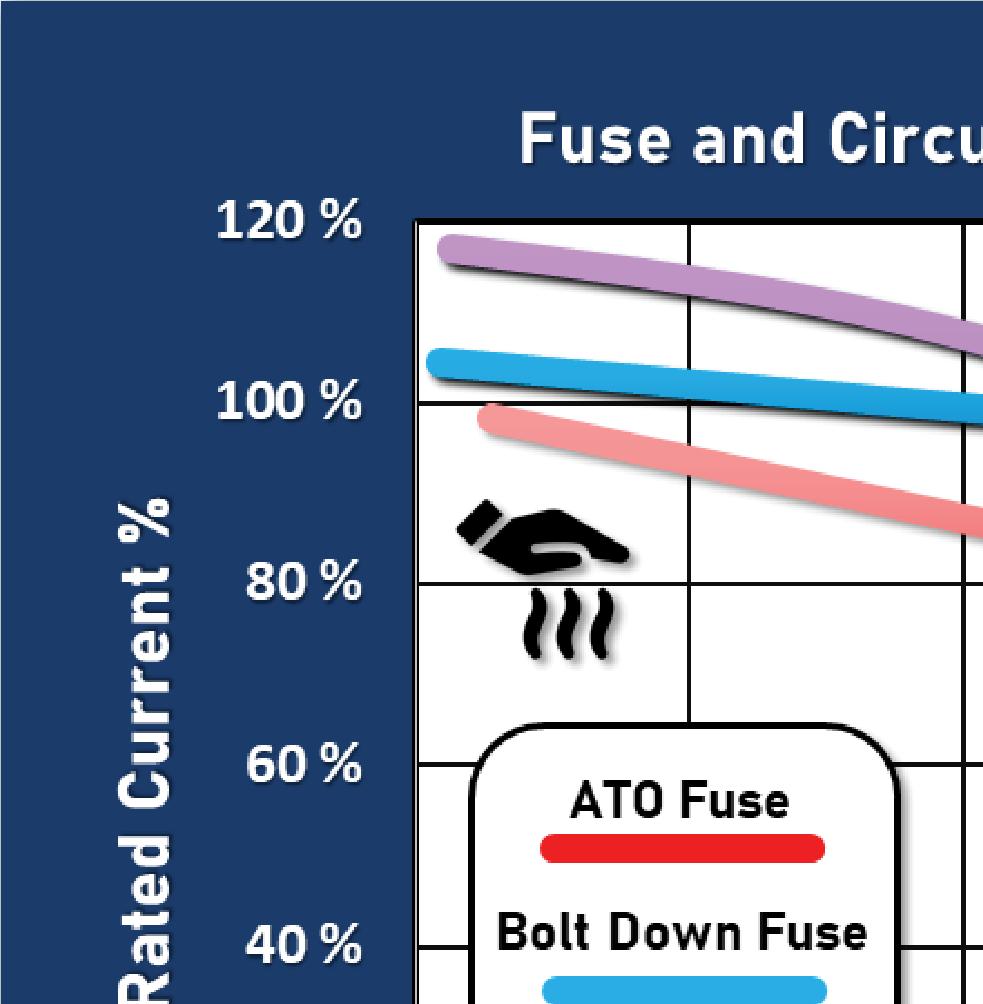
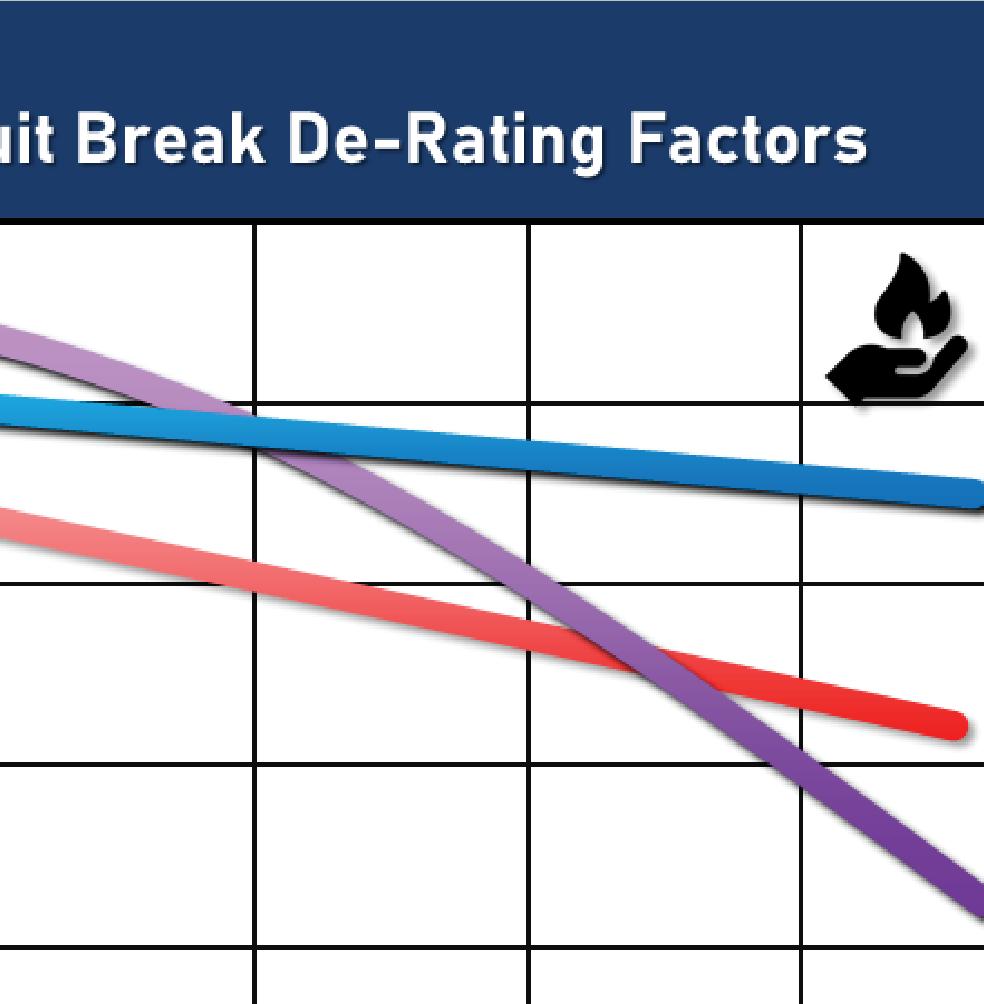
lower than the example with minimal cable lengths between the three components. When cable length is reduced in series component connections, not only is the necessary cooling capacity decimated, the adjacent components act thermally as one component with the combined heat load of all components in the series. e result is either component failure or the recognition that increased de-rating needs to be factored into the component and cable size decisions. While this example outlined an engine compartment application, scenarios with other functional components in locations such as center consoles or rear equipment trays should be evaluated in a similar manner.
Completing the thermal veri cation of components involves a recognition of the need to ensure components operate after considering de-rating factors. After an analysis of potential series heating, which has the e ect of increasing the e ecting operating temperature, any component subject to measurable reduction in performance within the expected operating temperature must be veri ed to operate with ratings reduced according to the manufacturer’s recommendation. Many manufacturers of temperature-dependent components such as circuit breakers and fuses provide de-rating guidance curves, while other component manufacturers provide parameters at maximum ratings that must be followed to achieve the targets. If deviations

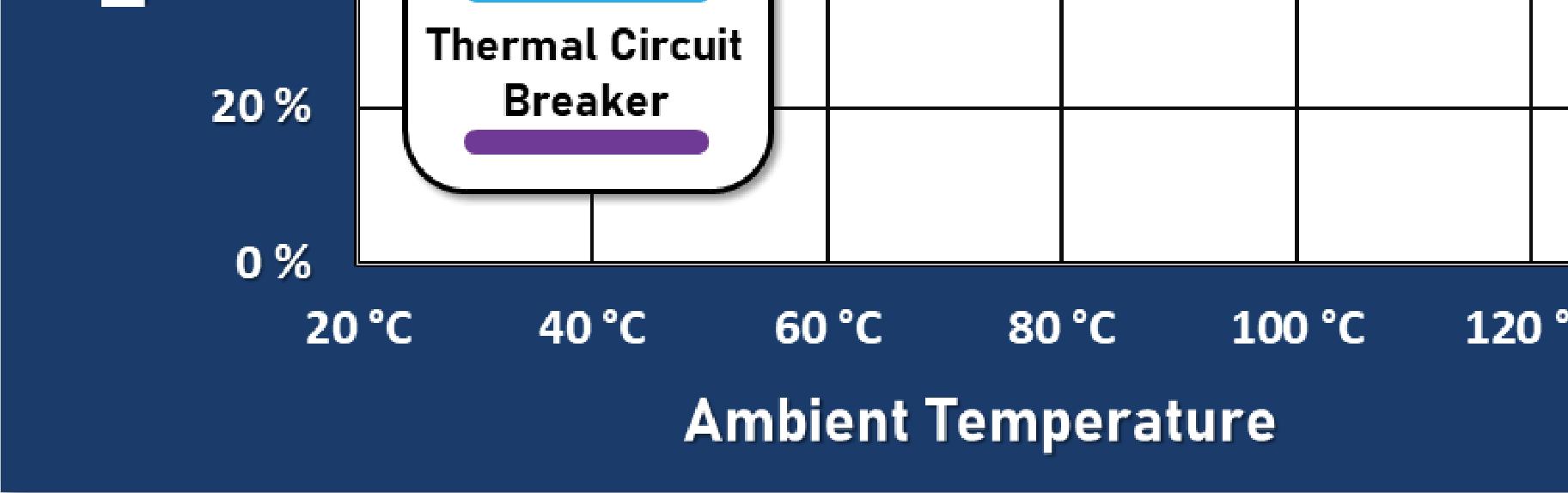
from manufacturer requirements are planned, further investigation with the manufacturer should follow.
Designing a robust system of incremental vehicle components is an increasingly complex task that demands system and component speci ers as well as vehicle up tters work together to ensure longterm reliability and full operational performance. Several prominent areas of consideration have been reviewed here, however, this should not be considered an exhaustive outline of risk mitigation concerns. Establishing deep engagement with all key stakeholders during the speci cation and implementation phases of emergency vehicle builds with the goal of identifying and eliminating all potential failure modes is ultimately the best method for delivering a successful nished system to demanding end users.
Eric Graham is the President/CEO of Egis Mobile Electric, which develops and manufactures products designed to provide dependable electrical battery saving and circuit protection technology for eet vehicles.
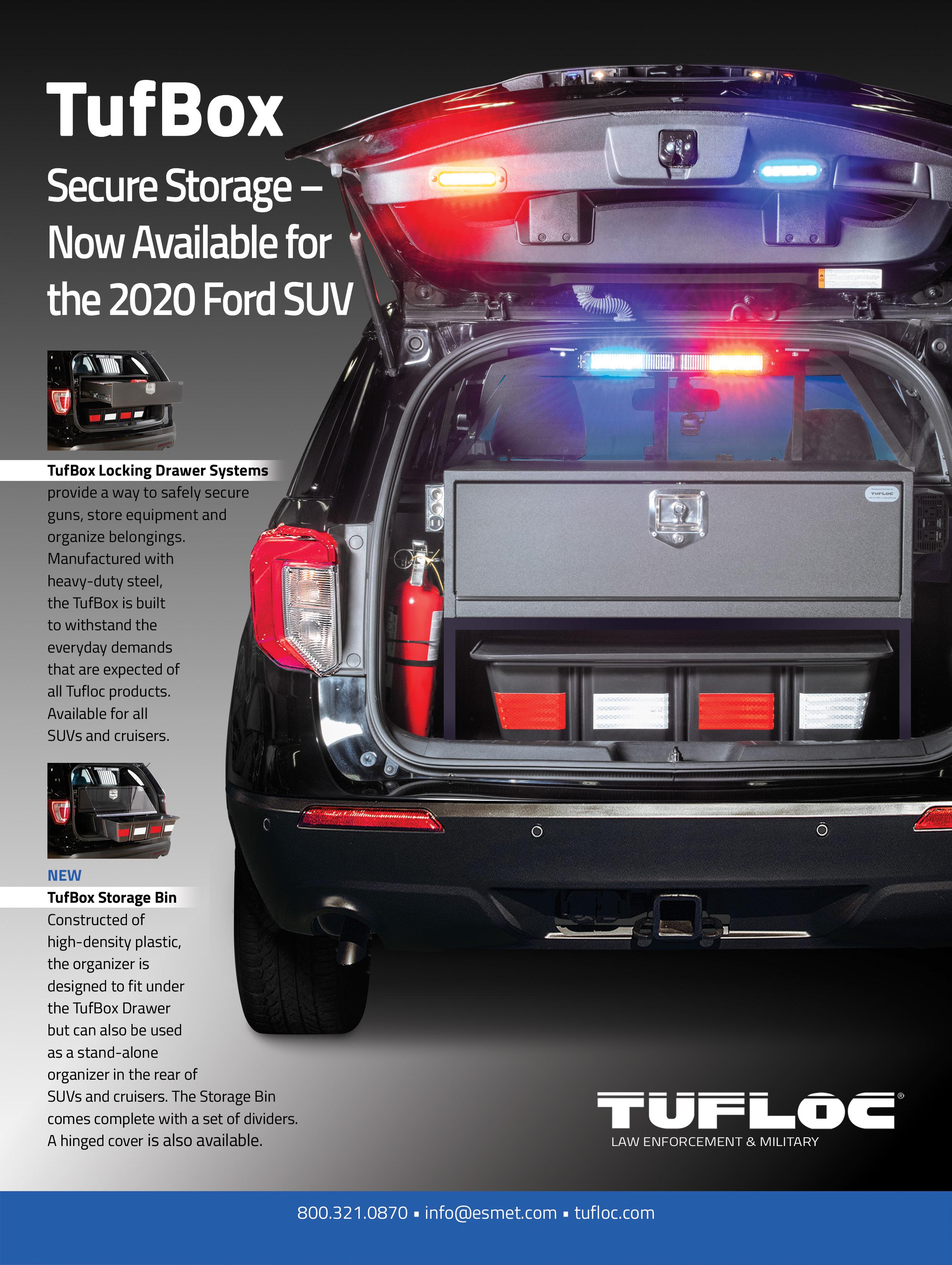