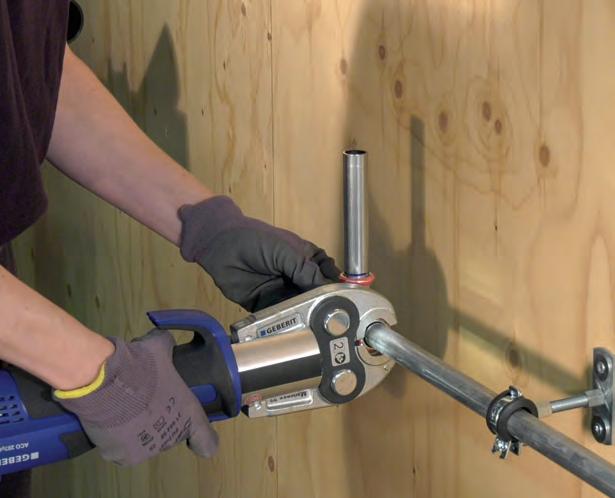
3 minute read
Responding to questions on press-fitting technology
Offering a host of installation benefits, press fitting offers a smarter, more efficient way of working –so says Antony Corbett at Geberit, who answers some of the most common questions installers have around press fitting for supply piping systems.
In an increasingly competitive market, plumbers and heating installers must evolve their working practices as much as any other business. And that means looking to processes that can improve productivity and, ultimately, profitability.
Pipe fitting is one area where installers have the opportunity to make time and cost savings through continued product development. Traditional jointing methods such as soldering and screwed pipe can be cumbersome, produce a lot of waste and can sometimes be impractical for the job at hand.
Additionally, site conditions and safety regulations sometimes make any form of hot works an impossibility: the cooling down periods and monitoring required for hot works are not conducive to more efficient working practices in competitive markets.
Press fitting systems are a more cost-effective and time-efficient method which also improves site safety. Let’s examine some of the more common questions asked by installers looking to make the switch to press fit systems like Geberit Mapress.
Antony Corbett Product applications engineer at Geberit
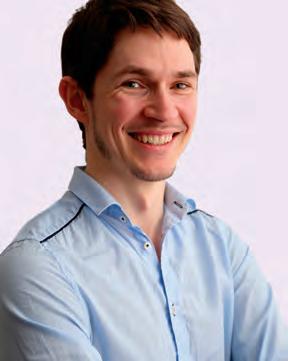
What materials are suitable for press fitting?
Press fittings are made from most common metals. Mapress, for example, is available in copper, stainless steel, carbon steel and CuNiFe, which ensures scope to use across a wide variety of applications including gas, potable and grey water, compressed air, and heating and cooling systems.
Is this a new technology?
Press fitting technology has been around since the late 1950s but it has previously been used more for commercial applications. With more domestic tradespeople keen to streamline their jobs and work smarter, it is becoming an increasingly popular choice for domestic installations.
How does it work?
The jointing process is simple. An installer simply needs to cut the pipe to size, debur the inside and outside edge of the pipe end, mark the socket insertion depth on the pipe using the appropriate gauge, push the pipe into the socket of the fitting, then complete by pressing the joint using a pressing tool. Coloured pressing indicators cover each end of the fittings, which offer easy identification of both the material and any unpressed joints during the installation process. In addition, the fitting and pipe are pressed only once the pipe has been inserted to the required insertion depth, which ensures a safe, dependable and longlasting connection.
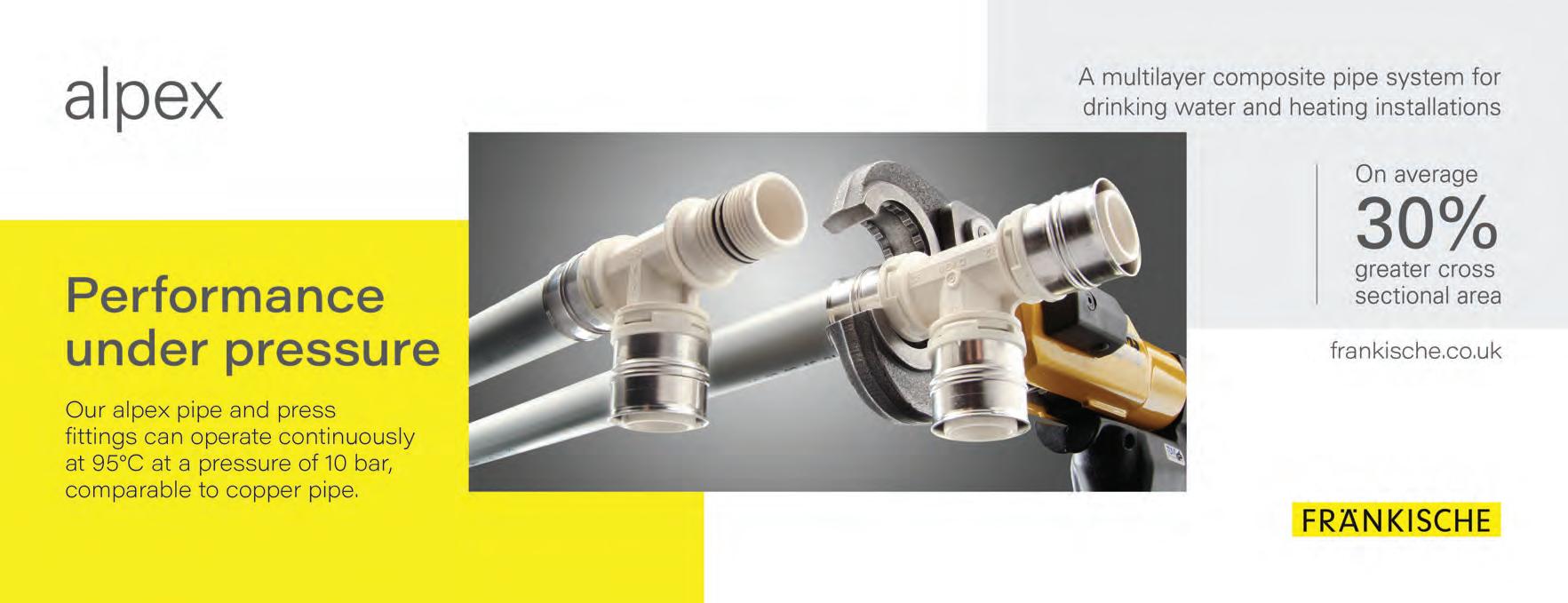
What about testing – if we have missed a joint, do we need to drain the system?
No, with press fitting there is no need. The joints will leak until pressed to show incomplete pressing during inspection and pressure testing. This means that there is no need to drain the system, as it can be fi xed wet.
What makes it quicker to install?
The biggest time saving when compared with soldering is there is no requirement for a cooling down period. This makes it a quicker and safer job, but there are a host of other time-saving benefits too.
By its very nature, the simple jointing method removes the most time-consuming process of traditional methods such as threading, soldering or welding. Components can also be prefabricated on or off-site before installation, which is particularly useful when working at height. Press fitting does not require any sealants or tapes. The system is also thin-walled precision pipe, so it is much lighter which makes for an easier installation.
What training is required?
Despite its simplicity, it is important to get the right training to fully understand the nuances of press fitting and deliver the best possible results. Leading manufacturers like Geberit offer training which combines best practice methods with the specific product knowledge required to maximise the quality, speed and integrity of every installation. Such courses also cover the tools required, as well as the maintenance and calibration requirements to make sure those tools remain fit for purpose.
Isn’t
it more expensive?
It is important to consider the whole project cost – and to get your customers to do the same. With press fit there are fewer additional materials, you can get the job done quicker so it saves on labour and it’s also a cleaner, tidier, less disruptive job, which is increasingly important in the current climate. In virtually all cases, the overall job cost benefits will outweigh the additional material costs and sometimes even the tools too.
◼ phamnews.co.uk/623/28
WHY PRESSFIT?
Time-saving: with no hot works or cooling peirod, it’s safer as well as quicker
Fool-proof: Unpressed joints will leak to show incomplete pressing
Wide application: Press fittings are made from a wide variety of materials, including copper, steel and CuNiFe
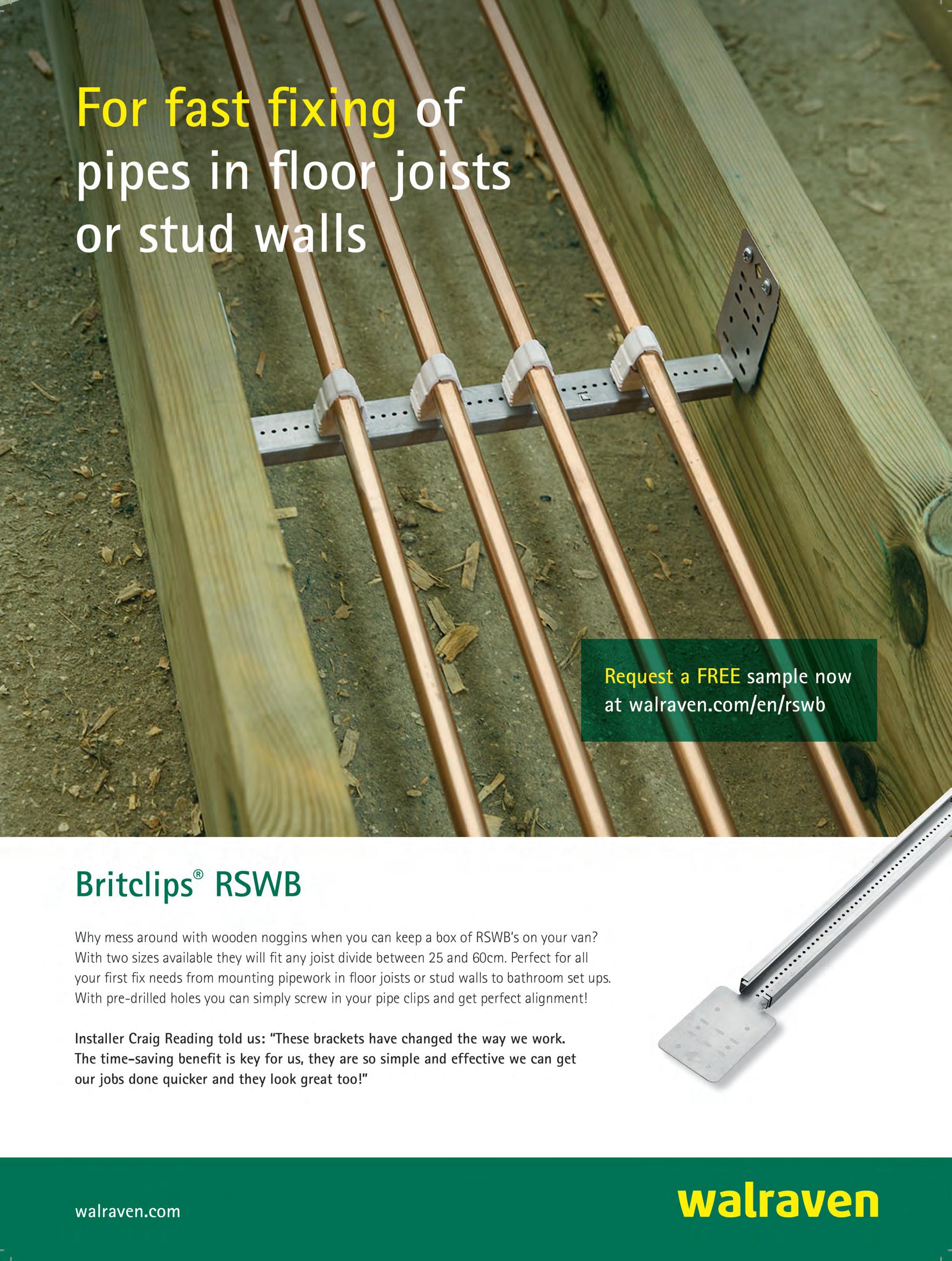