
5 minute read
PHI'S ENGINEERING TEAM IS PRINTING THE FUTURE
by PHI
HomeBase spoke to members of the engineering team Ken Boyer, Stewart Trahan, Mike Melton and Ryan Guillot to find out how 3D printing is increasing our efficiency.
At PHI, we’re always looking for ways to be more efficient—and more effective—with our time, resources and energy. Whether that’s investing in the latest and greatest technology or implementing ideas from our team, we strive to live each day by our core values of safe, efficient, quality, service. One way our engineering team is doing this is by incorporating 3D printing technology into their existing processes—and with great success so far!
Traditional fabrication is a time-consuming process that often limits designs. With high tooling costs and production limitations, initial designs, tooling and prototyping can take days, weeks or even months to complete— and not to mention requires a significant investment from our teams.
3D printing offers a flexible solution that can greatly reduce the number of components and enable on-the-fly innovation that’s not possible in traditional fabrication and manufacturing chains. Its impact on turnaround time, customization possibilities and design freedom, opens a world of exciting potential applications for our teams.
The Benefits of 3D Printing
Flexible Design Cycle
Traditional R&D fabrication requires a lot of trial and error, but with 3D printing, designs can go straight from sketch to production-ready using an AutoCAD file. Reducing and eliminating molds and the costs and time associated with tooling allows our teams to test multiple design variations before ever sending them to the sheet metal or machine shop for fabrication. With the ability to create fully-functional prototypes, the engineering team can print and test numerous variances—usually within a couple of hours—to quickly determine the final design.
Durable & Lightweight Materials
Although plastic is the primary material used in 3D printing, there are a variety of advanced mediums available in a wide range of colors including those infused with nylon or carbon fiber. Traditional mediums like plastic offer an inexpensive, durable and lightweight material that makes it easy to transport printed tools and components for customer review or feedback.
Better Resource Management
Not only does 3D printing help save time throughout the fabrication process, but it can also help to save on material and labor costs. 3D printing allows for more efficient and effective collaboration between project teams. The engineering team can focus on testing and adjusting the product design before looping in the machine shop or sheet metal teams for the final design, making better use of everyone’s time and increasing team-wide productivity. In addition, the 3D printer only uses the amount of plastic required for the job itself with little to no wastage, and any adjustments to the design can be easily fulfilled at a nominal cost as compared to traditional fabrication methods.
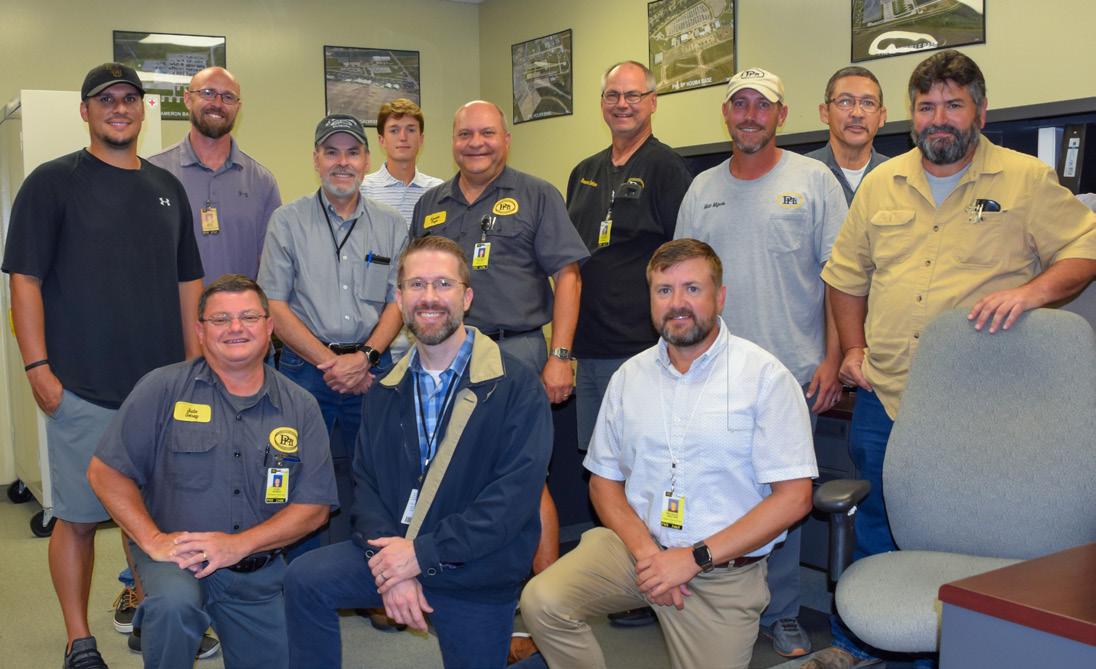
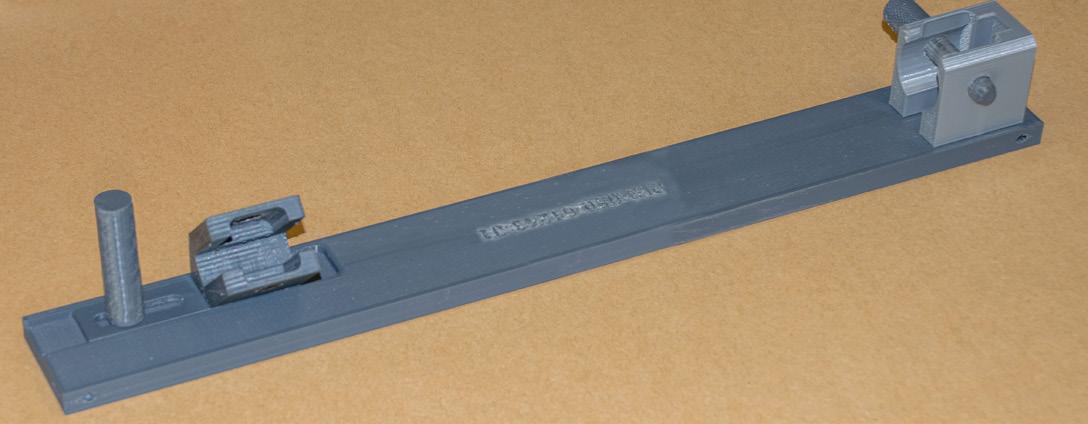
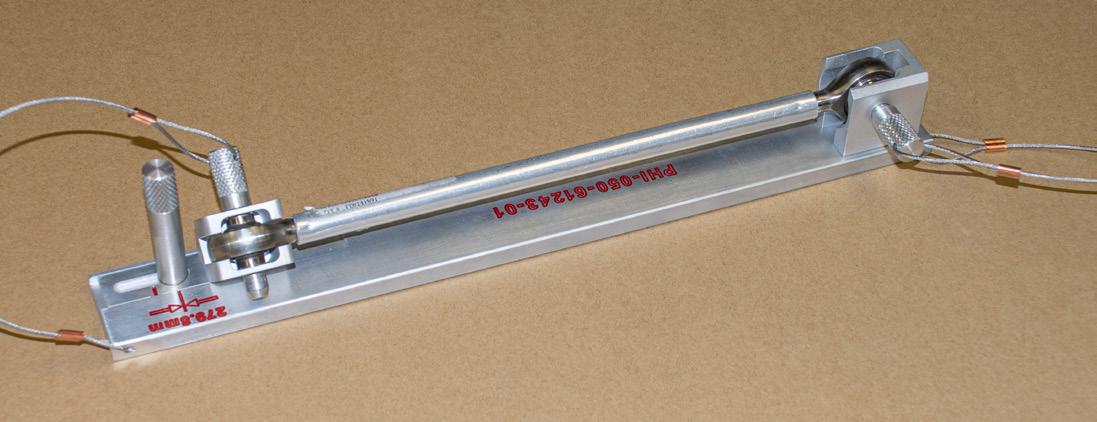
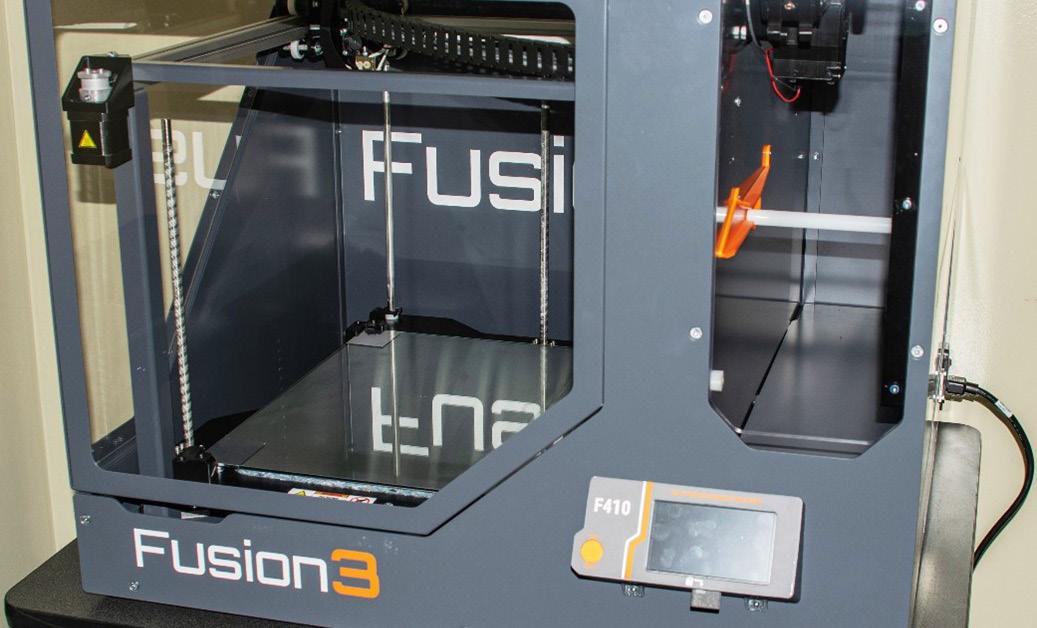
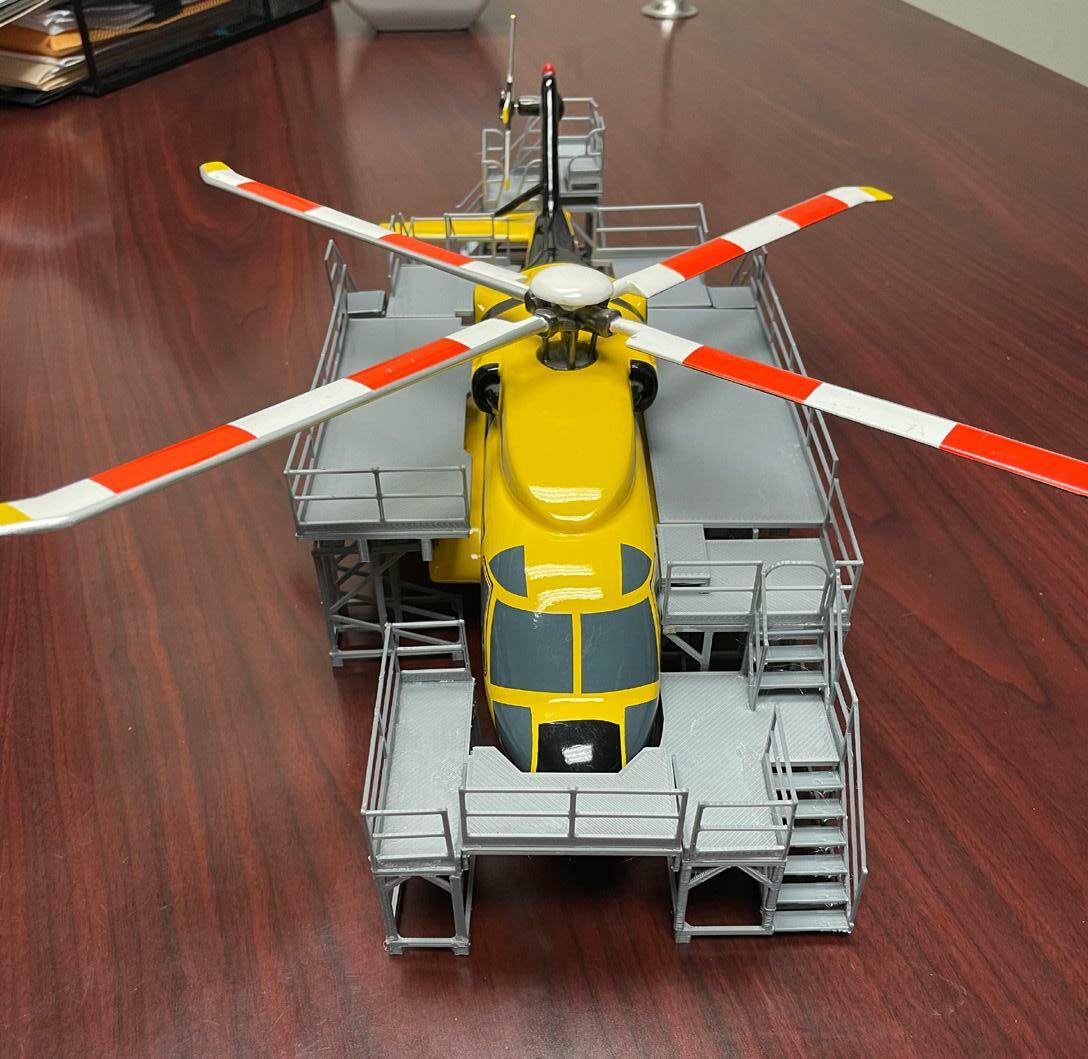
Increased Efficiency—Now in 3D!
Prototyping is a key part of our engineering design process—ideas are developed, and designs are refined based on the project scope and requirements. To help speed up and sharpen that process, our engineering team purchased a Fusion3 F410 3D printer for in-house use. The printer uses fused filament fabrication to produce large parts—or a large number of smaller parts in one print job—in as little as a few hours.
So when the team began working on a new tool to support control rod alignment, the 3D printer played a key role. After printing and examining the initial prototype, the team discovered that the rod assembly was too difficult to install and remove as an assembly. They were able to make minor adjustments to the technical design and print a second iteration of the prototype to validate their changes. From there, the design was altered again before arriving at the final design. What took about an hour to print would have taken days of back-and-forth with the machine shop to manufacture a successful unit. Instead, the engineering team was able to vet the assembly tool as it was intended, making adjustments to improve its ergonomics, before it was ever sent to the machine shop for fabrication.
Since then, the 3D printer has also been used to create scaled replicas of our maintenance stands for PHI Health. Similar to the assembly tool, the team was able to easily identify a crucial design flaw, make the design change and reprint the models in a matter of hours. Thanks to their light weight, the 3D-printed stands were easily shipped for final review by the customer.
3D printing allows our teams to explore more fabrication and manufacturing possibilities than ever before, and we’ve already seen improvements in our traditional R&D process. Whether the goal is quicker production, flexible design, customization or increased efficiency, 3D printing may be the next big thing in PHI’s long list of innovative solutions.
For more information about our 3D printing capabilities or for project requests, please contact Mike Melton.