
1 minute read
10 good reasons to implement extra filtration alongside condition monitoring
1. 80 to 85% of Hydraulic Problems are attributed to contaminated oil.
2. Micron Size Particles are the root cause of wear and tear of Pumps and Valves. Wear and Tear generates more particles, and the cycle goes on reducing component life.
3. Micron Size particles damage OIL itself; as they work as a catalyst in chemical reactions to reduce oil life through using up its additive package.
4. Replacing the Oil with New oil is not the whole solution; New Oil is not as clean as the International standards of NAS/ISO and the process can just as readily introduce fresh contaminant.
5. Damaged Pump / Valves / Hydraulic Controls directly affect the Performance of the Machines and Production is affected.
6. Excessive Contamination will overload the standard System Filters that have minimal affect to cope with full flows.
7. Contamination damages Hydraulic Seals to result in Internal / External leakage.
8. Internal leakage is a loss of Power resulting in lower production rate. Quality of finished product is not achieved, and rejection rate is increased.
9. Continuing high Contamination levels can result in Catastrophic Breakdown of the machines.
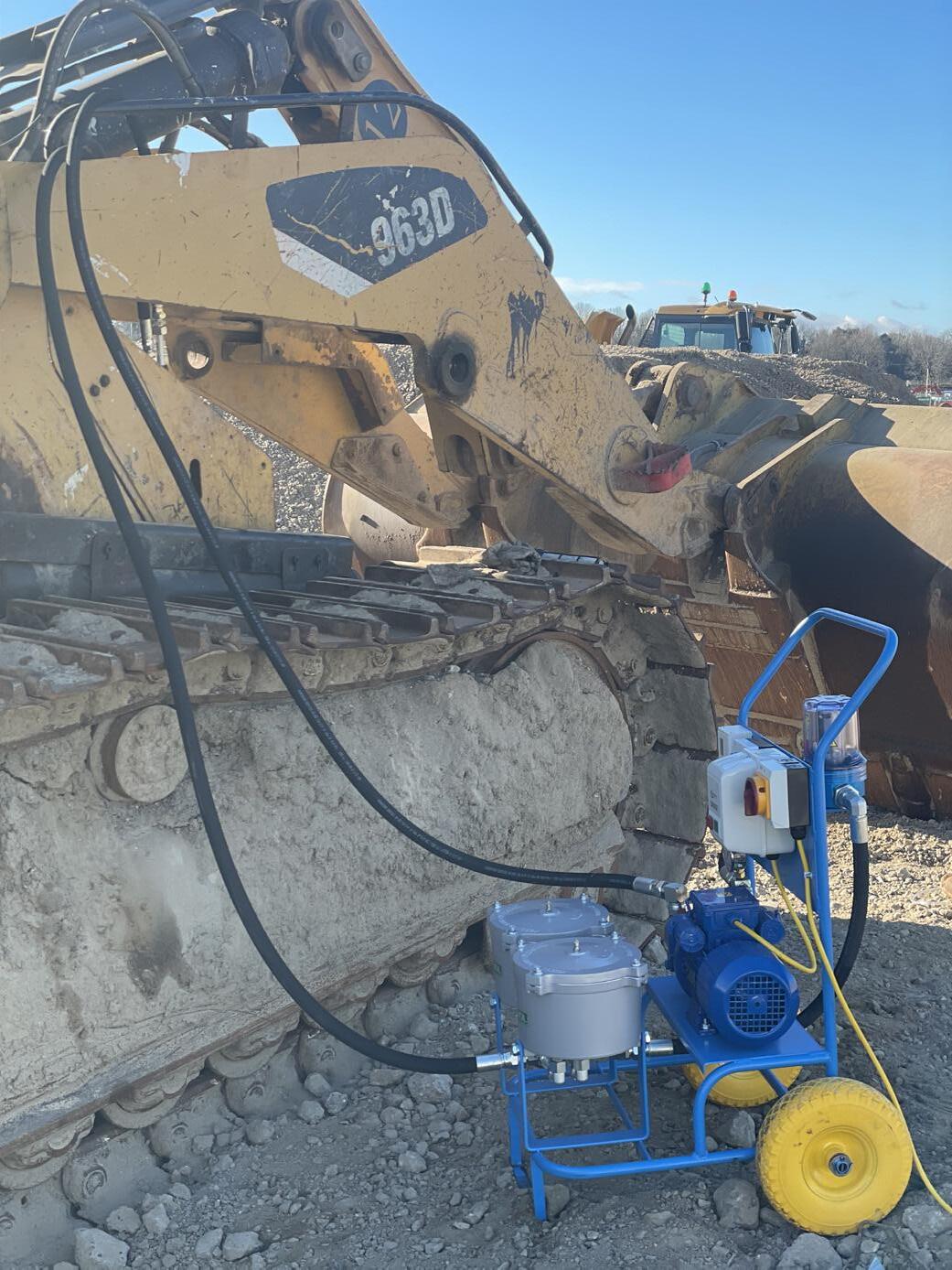
10. Poor Performance of the machine affects the quality of Finish Products, offering rejects and higher raw material costs.
If you recognise any of these issues – KLEENOIL can resolve this
Even the best oils under impeccable operating practices are vulnerable to contamination but can be minimised and controlled by simple and affordable measures.
KLEENOIL is a cellulose depth filter that not only removes particulates – such as ferrous, oxides, airborne contaminants, and fibres, but also water in the same simple application. With a robust system working alongside fixed plant, the added finest filtration will continuously maintain working oils to the best cleanliness levels, and for mobile plant; a mobile filtration unit can be used to routinely cleanse tanks of contaminant and moisture.