
8 minute read
Additives
Remaking plastics with new additive developments
Additive specialists are on a drive to develop and improve additive compounds to bring safety, convenience and environmental benefits to the marketplace, says Angelica Buan in this article.
Advertisement
Antimicrobials: armour against pathogens
Sanitation has been added to our list of daily routine due to the pandemic. Nonetheless, habitually cleaning surface is not quite enough. It is, thus, not surprising that materials that provide a layer of microbial protection are getting consumer attention. Among the recent advances in this segment is Dutch biocompatible plastics and antibacterial polymers manufacturer Parx Materials’s Saniconcentrate, a patented additive technology that reduces Covid-19 virus on plastic surfaces by up to 99% in 24 hours. Saniconcentrate is homogenously incorporated into plastics to create an ’immune system’ inherent to the material. In particular, it works without biocides, leaching or adverse side effects, contrary to other antimicrobial technologies that have always used biocides, such as silver or copper, to destroy microorganisms. While this method may effectively destroy bacteria and viruses, it can lead to toxic substances leaching out of the material, contaminating the products or surfaces it is trying to protect, as well as contaminating the environment and making recycling a more challenging task. Moreover, bacteria and viruses tend to become resistant to biocides over time, reducing the efficacy. According to Parx Materials, Saniconcentrate uses a trace element abundantly found in the body Parx Materials’s to prevent bacteria and viruses from adhering to surfaces, causing them to run through Saniconcentrate is a patented additive technology that reduces Covid-19 virus on plastic their usual lifecycle and die surfaces by up to 99% in within hours. Because of this, 24 hours it is biocompatible, safe and its applications are limitless, adds Parx. It is currently in use in major supermarkets and has shown results in medical trials. Similarly, US-domiciled resin manufacturing company Avient Corporation offers antimicrobial solutions demonstrating high efficacy against bacterial growth. It recently launched three proprietary thermoplastic elastomer (TPE) formulations that contain antimicrobial additives, adding to its GLS TPE range. Tested in accordance with JIS Z2801 and ASTM G21-15 standards, these additives protect moulded plastic parts by inhibiting bacterial growth by 99.9% or more, and resisting fungal and mould growth. Additionally, GLS TPEs with antimicrobial additives can also help extend Avient has launched three proprietary TPE formulations that a product’s useful life, preserve its surface integrity, and contain antimicrobial additives increase its durability, adds Avient.
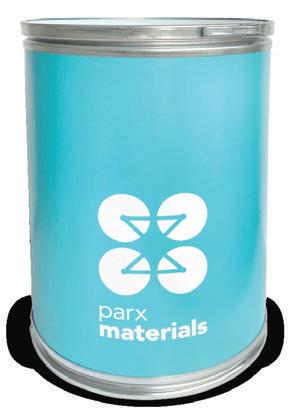
Aside from causing odour issues, the microorganisms can cause detrimental aesthetic and mechanical property changes to a finished plastic part, Avient said. High-touch surfaces and applications are especially vulnerable. The GLS TPEs with antimicrobial additives, available as Versaflex and OnFlex grades, have potential applications in consumer electronics, personal care item grips, and automotive parts such as cup holder mats and HVAC seals.
Advancing recycling efficiency for coloured plastics and PS
The issue with plastics being environmental nuisance has been around for ages because plastics, by design, were not recyclable. The need to recycle plastics, however, has gained momentum in view of its role in climate change.
Recycling technologies have improved alongside the capability to sort materials in the recycling stream. Infrared (IR) and near infrared (NIR) sorting technologies used in material recycling facilities (MRFs) have also gotten better to increase throughput rates.
Newer recycling systems are likewise addressing the challenge of recycling hard to recycled plastics like PVC, PP and LDPE; sorting through wastes mixed with contaminated plastics; or properly identify and accurately sorting black or dark coloured plastics. For instance, carbon black absorbs the light emitted from the IR devices and also prevents the successful identification of the type of plastic. These unsorted black plastic products are rejected and, in most cases, end up in landfills.
US-headquartered additives masterbatch supplier Chroma Color offers a carbon black alternative that allows the MRF sorter to accurately and repeatedly identify and sort the plastic articles.
Chroma Color’s IR reflecting black technology, the NIR Black, is based upon a family of complex inorganic pigments (sometimes referred to as mixed metal oxides). The NIR Black is inert, heat stable and non-migratory; and can be used in a variety of polymers. The FDA-approved technology is available in a variety of resins that include the most common packaging resins like PP, PE, PS, ABS and PET.
In a related development, Trinseo, a manufacturer of plastics, latex binders and synthetic rubber, has recently commercialised its recycled polystyrene (PS) from dissolution technology and is offering a new material, namely, Styron CO2RE 687DI30. This is the first of a series of recycled PS products that Trinseo intends to launch under the Styron CO2RE brand in the coming years. Dissolution of PS preserves the molecular structure of the recyclate.
PS is slow to biodegrade and often, if not totally, rejected by recyclers due to its density and, if used as food packaging, its contamination.
With Trinseo’s material/recycling method, postconsumer recycled (PCR) material is dissolved in a solvent followed by a series of purification steps to separate the polymer from additives and contaminants. The material is fed into a polymerisation reactor train, resulting in a PS polymer with 30% PCR content for use in applications such as consumer electronics, packaging, and food contact materials if a functional barrier is present to ensure compliance.
Meanwhile, Trinseo also engages in depolymerisation with technology provided by UK-based mixed plastic recycling solution provider Recycling Technologies. Trinseo’s planned dedicated plant at its Tessenderlo, Belgium, site will be one of two PS recycling plants in Europe estimated to add a total of 30,000 tonnes of PS feedstock into the European market.
Oxygen scavengers: value adding rPET
Growing demand for longer and better shelf-life and improved safety in products in the food and beverage, pharmaceutical, medical, energy, oil and gas, chemical, and paper industries is boosting the market for functional oxygen scavenger additives.
The food and beverage segment accounts for the largest share in the oxygen scavenger market, especially since safety and quality of food products are predominant concerns of consumers. Oxygen scavengers in packaging for food and drinks help maintain the quality, efficacy and freshness of the products for an optimum period. The benefits derived, in a larger perspective, reduces food wastage, which is a global concern.

Trinseo's dissolution technology preserves the molecular structure of the recyclate Additives
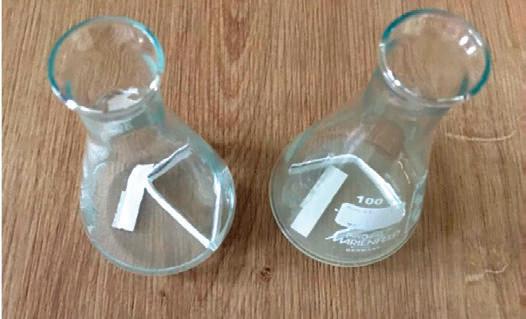
Additives
Meanwhile, the call for reducing plastic use and increasing recycled content in packaging and products confront the issue of safety: are recycled materials safe enough for food-contact applications? Another latest additive offering from Avient tackles this important area.
The new ColorMatrix Amosorb 4020R, a non-nyloncontaining oxygen scavenger additive, is specifically formulated to enable the use of fully recycled PET (rPET) content. This new additive joins the Avient portfolio of ColorMatrix additives that enable improved recycling for plastic packaging.
According to Avient, the Amosorb 4020R delivers full, consistent oxygen scavenging performance with 25%, 50%, and 100% rPET content. This new solution also improves the aesthetics of recycled packaging in terms of haze and colour, including a reduction in the yellowing effect that may occur during recycling. Additionally, during recycling, aesthetics and oxygen scavenging performance can be affected. Amosorb 4020R has been formulated to address this performance issue, making for high-quality recycled packaging, says Avient.
Preventing scuffs and scratches in PET products
PET bottles undergo a laborious quality check before reaching end users. Foremost, they must be safe for use and of high quality. Therefore, the plastics used for these bottles must possess the desired properties, including transparency, gloss, thickness, resistance to breakages and scratches, and more.
New York-based masterbatch producer Ampacet offers two additives, the latest addition to its ScratchShield line, to protect plastic products against scratch and abrasion without impacting gloss or mechanical properties of the resin.
The new additives are said to minimise the appearance of scuffs and scratches in preforms, bottles and a range of PET packaging without the need to apply a surface coating. They are also said to significantly improve the demoulding of preforms, while offering protection from guiderails and conveyor systems in the manufacturing process.
ScratchShield also helps converters to reduce scrap, the need to regrind scratched bottles and cleanup associated with lubricant sprays, Ampacet adds. This additive can be applied to alcoholic beverages (low alcohol), automotive products, cleaning products, lotions, juices and soft drinks, pet care products and water cooler bottles
Used to enhance PP, ABS, PET, PE, clear PS, and HDPE materials ScratchShield has been tested to reduce scuffs at load forces up to 100N; and at forces lower than 25N, scuffs were virtually eliminated in bottle-to-bottle scuff tests, claims Ampacet.
Halogen-free FRs with improvements
Plastics, textiles, foams, coatings and virtually all commonly used materials are flammable or susceptible to fire. Non-halogenated flame retardants (FRs) are additives added to these materials to retard fire and produce less heat and widely used in transportation, electrical, and construction industries and high-end applications.
A leading player in this arena, American chemicals company Teknor Apex offers four new Halguard lowsmoke FR jacketing compounds. The compounds include new-generation EVA-based products with an enhanced balance of properties, and flexible TPE-based products that exhibit oil and sunlight resistance.
The assessment of halogen content was conducted in accordance with UL 2885 standard for the presence of fluorine, chlorine, bromine and iodine at a maximum individual limit of 1,000 ppm.
The EVA-based compounds’ Halguard grades 58240 and 58242 provide flame retardance, resistance to heat shock and heat deformation, and ease of processing, the latter translating to increased throughput. The compounds enable cables to comply with UL 1685-FT4/IEEE 1202 standards for vertical tray cable and the UL 1666 standard for riser cable. Other applications include fibre optic data cables and cables used in transit infrastructure, as in the case of tunnels.
Meanwhile, the TPE-based compounds, incorporating elastomers, comply with UL 62 and UL 758 standards for flexible cord and appliance wire, respectively. Halguard E 59001 exhibits 80% and 90% retention of tensile strength and elongation at break, respectively, upon immersion in IRM 902 oil for seven days at 60°C. Halguard E 59002 retains 90% and 95% of tensile strength and elongation at break upon exposure for 720 hours in a weatherometer.
With the four new grades, there are now 15 Halguard low-smoke, halogen-free (LS-HFFR) compounds with UL AATJ2 component recognition as halogen-free, adds Teknor Apex.
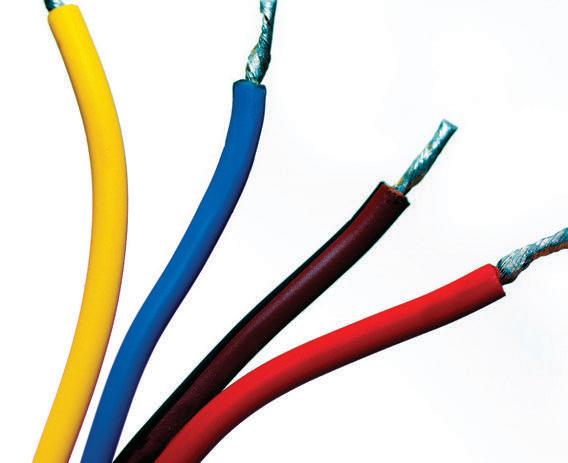