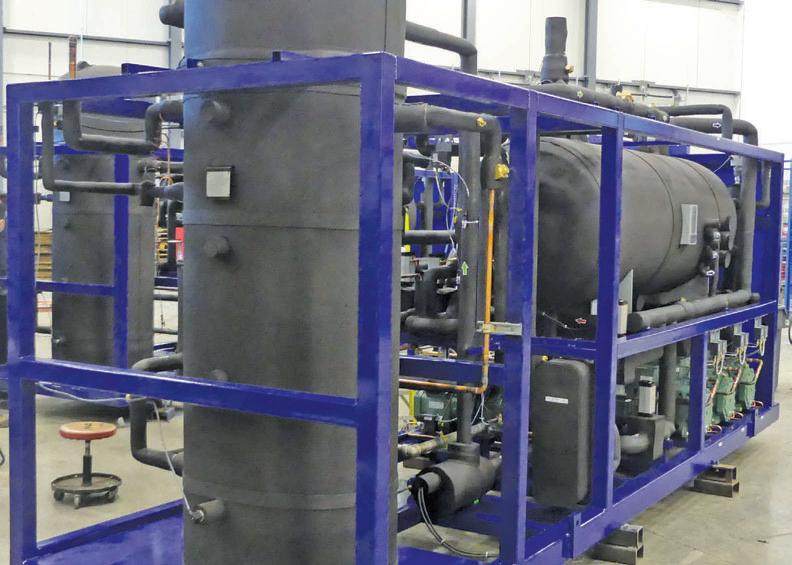
7 minute read
Refrigeration
from Jan/Feb 2023
Continued from page “35” ammonia refrigeration plant with a capacity in the 1,000s of tons of refrigeration (TR) is massively different than your restaurant walk-in cooler that might be a ton or two at most. The refrigeration cycle is based on the same scientific principles, but the technology used to achieve the refrigeration can be very different and the skill set required to design and service the systems are different. Industrial is not necessarily better than commercial, but they are different.
This difference has resulted in a divergence over time that has caused a bit of a split in the industry. Are you an industrial refrigeration mechanic or a commercial refrigeration mechanic? Having done both to some extent (you could maybe call me a com-dustrial refrigeration mechanic but please don’t) and having spent years designing and analyzing industrial systems and large or missioncritical commercial systems, I can tell you that there is an application suited to most types of equipment and no magic bullets.
While there is, of course, no clear line between commercial and industrial, and there has never been, certain parameters can lead to a better understanding of the landscape.
Refrigeration capacity
As was already mentioned, the size of refrigeration systems can vary by several orders of magnitude. It is true that you could do a large amount of refrigeration with a whole lot of small units — this is sometimes done. This type of solution definitely improves redundancy as one or two system failures don’t have a large effect on system capacity, but it can get silly. I have seen warehouses with more than 20 condensing units and evaporator pairs installed. Another common challenge is maintenance. It’s hard to notice industrial solution. There are many reasons for this, but as an example, large and rapid temperature changes can easily damage less robust components and large and rapid load changes often require the ability to mitigate system upsets and manage high liquid flood-back. You tend to see more industrial equipment in more demanding environments.
Lifespan
when one of the systems isn’t working well. Conversely, it would make no sense to put an open drive reciprocating industrial compressor on a one TR walk-in cooler as the cost would be astronomical.
Applications
Another place you see the difference between industrial and commercial equipment is application. Some applications, like product freezing, can be extremely demanding on equipment and are more suited to an
Many restaurants and grocery stores turn over their refrigeration every 15 to 20 years or less, while a large industrial production facility may be intended to last 40-plus years. This extended lifecycle leads to a willingness to invest in equipment that is more robust and will last longer. Of course, this is not to say that industrial equipment doesn’t fail, but it is typically designed to be overhauled and repaired repeatedly. It is not abnormal to see a well-maintained industrial plant installed in the 1990s still running today as if it’s almost new.
This lifespan is also why you see a
Continued on page “39”
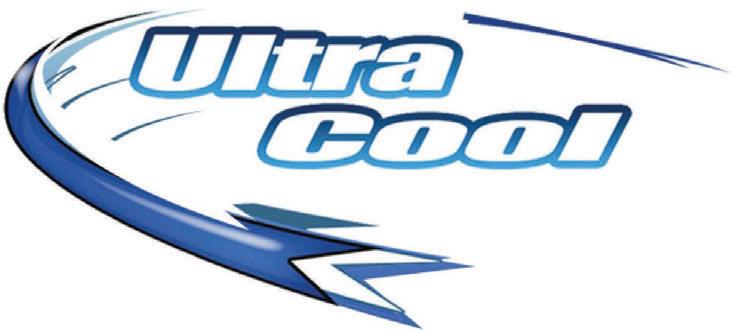
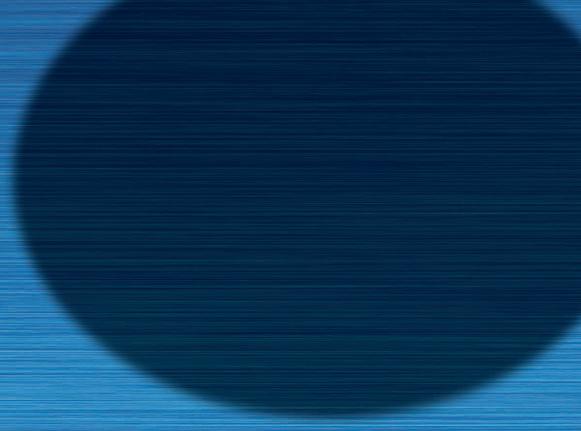
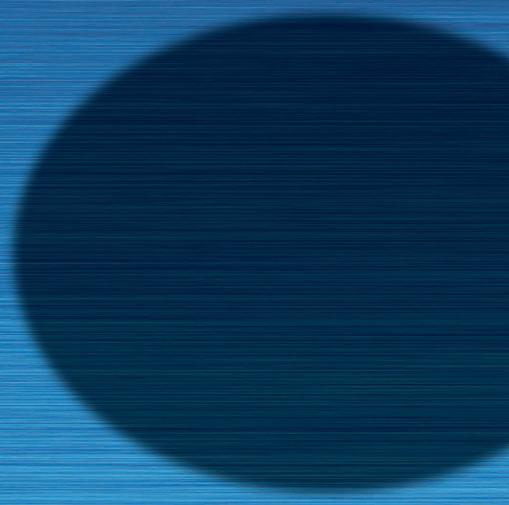
The lines between commercial and industrial applications have never been more blurred than it is today.
Continued from page “37” willingness to use industrial-style equipment in civic infrastructure projects, like ice rinks. Ice rinks are not an overly large refrigeration system. You can make ice with anything from ground source heat pumps, commercial style chillers, grocery store racks, CO2 racks, to open drive ammonia or halocarbon systems. While people do employ all these options regularly, the majority of municipal projects are still built with an industrial-style system because municipalities have the desire to build facilities with much longer life cycles than much of the private industry.
Reliability
Another differentiating factor is reliability. I am aware of industrial refrigeration systems that run for years between shutdowns; there are some that have quite literally never been completely shut down in their entire existence except for during a power outage. Repairs and replacement of components, of course, but not shut down. In many large food production facilities, a shutdown is massively expensive, and money put into reliability and long-term operation is much preferred over less expensive investment in equipment.
One example of increased liability is related to the piping design. Smaller commercial equipment is not often built to comply with ASME B31.5 and instead relies on a UL rating for its pressure containing components (other than pressure vessels). This is not bad, but since UL is a test-based method compared to ASME’s much more conservative calculationbased methods, the commercial equipment does experience (in my experience) a significantly higher rate of piping and pipe joint failures. A frequent location for this is discharger headers on compressor rack-style systems. This pipe can get very hot and often doesn’t incorporate appropriate flexibility into the piping design.
I have seen dozens of cracked discharge headers or failed discharge branch piping in commercial rack-style systems in both CO2 and halocarbons. I don’t recall ever having seen failed/cracked discharge piping on a system that complies with ASME B31.5.
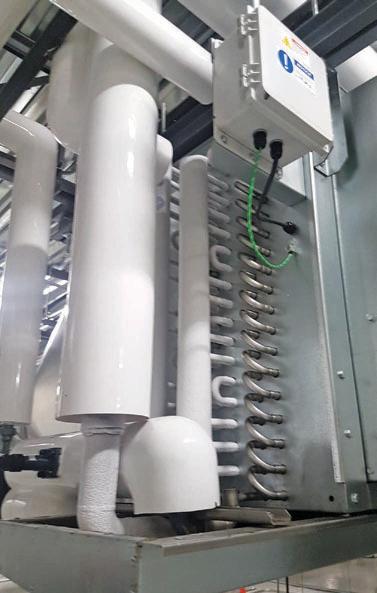
End of the day
As with many things in engineering or design, it comes down to lifecycle costs. I once worked on a facility that insisted on planning everything — including the spiral freezer and refrigeration system — on a five year life. They had their business reasons for doing this, and I can assure you it doesn’t make sense to use the most expensive equipment in this scenario.
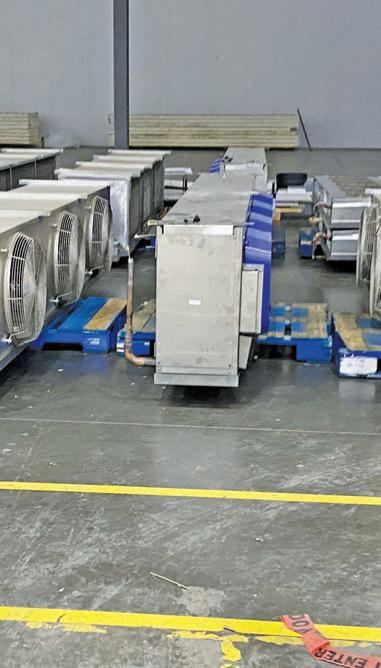
Only a thorough understanding of the owner’s needs can help guide how “industrial” or how “commercial” you make the equipment. The closer you get to the grey area in between them, the harder it is to know what the right decision is. And as I mentioned at the beginning of this article, CO2 is upsetting the long-standing industry balance. There is a huge interest in using CO2 in industrial applications – and we are – but the systems are still often more “commercial” and don’t have many of the benefits that the old stick-built ammonia and R22 systems did. Over time this will change; it is changing. But in the meantime, we should all work together to make sure the word com-dustrial dies. :
Greg Scrivener is the lead refrigeration engineer and a partner at Laporte Consultants, Calgary, and works throughout Canada and the U.S. He is a professional engineer and journeyperson refrigeration mechanic. He can be reached at GScrivener@laporteconsultants.com.
Whenever Piping Is Involved
In memory of Jon Leeson
Francois Deschênes, president and CEO, issued a note to Leeson, “During all these years that I have known you, I always felt that you wanted to go for it, to persevere despite the pitfalls and that you said things as they really were with honesty and sincerity. All this with your sense of humour, your humility, and your desire to put others first rather than yourself.”
During his time in the industry, he held various marketing and sales roles before becoming vice president and general manager. Leeson was also long involved with the Canadian Institute of Plumbing and Heating (CIPH).
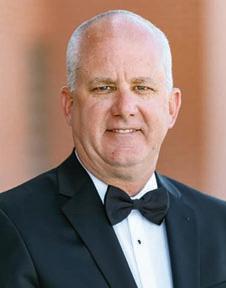
In tribute to the nearly 20 years of work at the Deschenes Group,
Leeson passed away on Dec. 15 after a lengthy batter with cancer. He leaves behind his wife of 29 years, Linda Leeson, and his two children, Madison (Yazeed) and David.
Funeral details will be announced at a later date. Leeson would like for those interested and able to make donations in his name to the Sinai Health Foundation in Toronto. A page has been set up on Arbor Memorial for people to share condolences.
Sluyter announced that Melissa Barrett had joined its team as the new marketing manager. Barrett has more than 13 years of experience in business, marketing, sales and management. She previously worked at Evolve Home Services
Angela Grieb has been named as the new assistant national sales manager at General Pipe Cleaners. Grieb has been with General for 17 years, which included working as an executive sales coordinator.
Blanco has appointed Diana Windsor as its senior vice president of sales for North America. Windsor has more than 13 years of sales and management experience in the plumbing industry. She previously held senior leadership roles at Watts Water Technologies and Kohler.
Cam Giroux has joined Barclay Sales serving as its mechanical and hydronic specialist. Giroux has owned his own hydronics installation company and has been in the industry for more than 17 years.
Johnson Controls has appointed Lei Schlitz as its vice president and president of global products. Schlitz will lead the global products business and will be based in Milwaukee, Wisconsin. She joins from Illinois Tool Works.
Viessmann has three new additions to its team: Joshua Burns , Tarandeep Singh , and Jeremy Manalo Burns will act as the marketing coordinator in Waterloo, Ont. Singh will serve as the territory sales manager in Langley, B.C. While Manalo will op erate as the logistics coordinator in Langley as well.
Canadian General Filters Ltd. announced that Sam Argentino would serve as its new president. Argentino brings over 33 years of senior management experience.
Latisha Rathell has been announced as Bradley Corporation’s new director of customer service. Rathell brings over 20 years of experience in financial and business analysis, reporting, project management and contract performance management roles.
NTI Boilers announced that Kyle Silvio will be joining its team as regional sales manager in the Massachusetts, Rhode Island and Connecticut areas. He is a licensed journeyman plumber with previous employment as a service manager at a Massachusetts heating company. Silvio has previous sales representative experience and was a condensing boiler technical trainer at a manufacturer’s representative agency.
Introducing the Infiniti® GS and Infiniti® GR
At Bradford White, innovation is important. So we’re proud to introduce the Infiniti® GS and GR tankless water heaters which offer the energy-efficiency, high-performance and cutting-edge features you and your customers expect.
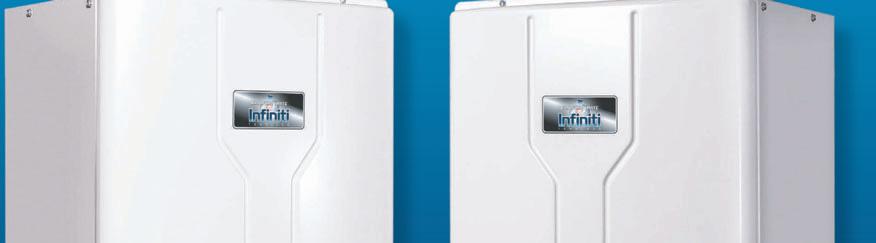



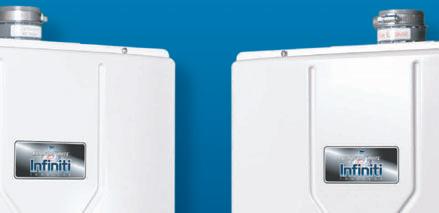
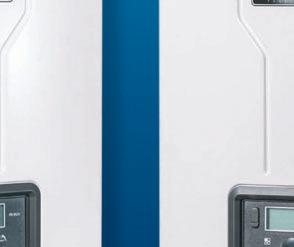
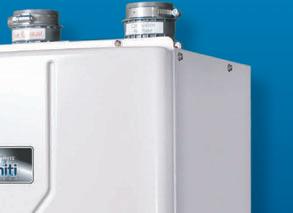
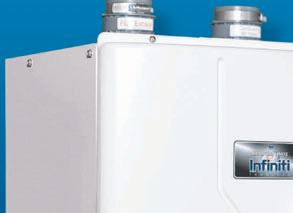
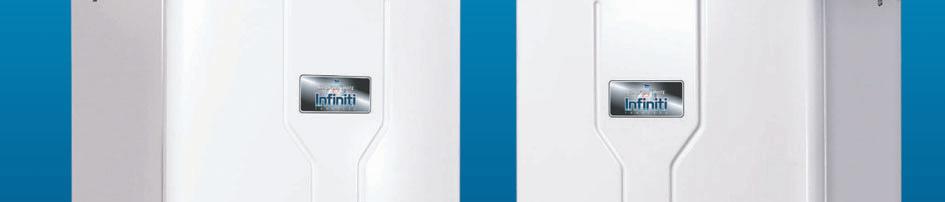
• RESIDENTIAL AND COMMERCIAL.
• OUTSTANDING RELIABLITY. Robust stainless steel heat exchanger for longer life.
• POWERFUL PERFORMANCE.
11:1 turndown, high GPM output of 5.1 GPM at a 77°F rise. High temperature setting – up to 180° F (Infiniti® GS).
• REMARKABLE FLEXIBILITY:
• Available in natural gas or propane
• Indoor or outdoor (with outdoor kit)
• Available as standard model (Infiniti® GS): Cascadable up to 16 units, common vent up to 8 units
• Or with built-in recirculation pump (Infiniti® GR)