
6 minute read
Refrigeration
from May/June 2022
The next step forward for the heat pumping market is to convince the right decision-makers that there needs to be an increase in the number of refrigeration mechanics as heat pumps gain popularity. By Greg Scrivener
Ammonia is one of the most efficient high temperature heat pumping refrigerants, which is being used in this industrial heat pump. (Photo taken at
International Institute of Ammonia Refrigeration 2022)
Over the last several issues, we’ve discussed heat pumping in various applications. As the technology becomes more affordable and the desire to reduce carbon emissions increases, heat pumps will be used in more and more applications.
Commercial equipment is now becoming available with the ability to produce hot water to 180F using refrigerants other than carbon dioxide. Providing the proper motor and oil are selected, the application window of some compressors is significantly larger than they used to be. Figure 1 shows that application limits for a compressor from a manufacturer’s webpage. You can see that operation at very high condensing temperatures is possible.
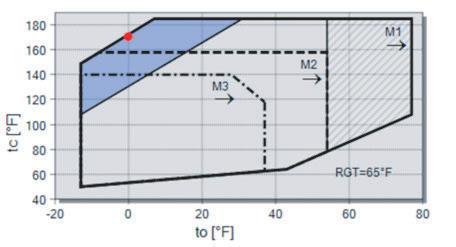
Figure 1: Application limits for a 6FE-50Y Bitzer compressor.
(Photo by Bitzer.de)

Figure 2: Approximate coefficient of performance (COP) for a compressor used in high temperature air-source heat pumping at different outdoor ambient temperatures.
Figure 4: A basic representation of a cascade heat pump
While there are compression ratio limits that occur as the evaporating temperature decreases, meaning that high condensing temperatures may not be possible at really low evaporating temperatures, this particular compressor can operate at very high condensing temperatures throughout a really wide range of evaporating temperatures.
Figure 2 shows the approximate heating coefficient of performance (COP) for this compressor used in an air-source heat pump and Figure 3 shows the approximate heating capacity. Looking closely at these figures, you can see many of the problems we’ve discussed over the last several issues. The capacity of the system decreases rapidly with a decrease in the temperature of the heat source and the efficiency also drops off in the same manner. In other words, if used for space heating or another type of heating load that is governed by outdoor ambient conditions, you either have to buy large and oversized equipment or add a secondary heat source in order to meet the requirements at low ambient conditions.
Market challenges
There are several ways to address some of the operating challenges with heat pumping. First, let’s look at the operating ranges. It is likely that in many cases at least some electric back up heat will be required. However, in Canada, most high temperature heat pumps that produce hot water for space heating or process loads are likely going to need to be able to produce this heat as efficiently as possible and at ambient temperatures below -30C.
In order to decrease the compression ratio of individual compressors, it’s possible to design high temperature heat pumps as cascade-style systems when large temperature lifts are required. Figure 4 shows a basic example of this type of system.
While there is a cost associated with the extra compressor and heat exchanger, these types of systems can keep compressors in a narrow operational window, which can extend the life of the compressors, they can optimize the refrigerant selection by using refrigerants that are more efficient on both the high and low stage (i.e., they can use two different refrigerants if that brings a benefit), and they can be more energy efficient.
For example, we can select a low stage compressor to evaporate at -40F and condense at 50F and match it to the compressor we used in the example above with an evaporating temperature of 40F (assuming a 10F temperature difference in the heat condenser/evaporator heat exchanger) and a condensing temperature of 180F. This results in an approximate COP of 1.85, which compared to purely electric heat is still much less expensive to operate (at least as far as energy costs are concerned).
Shining star
Ammonia turns out to be one of the best high temperature heat pumping refrigerants and in cascade-type arrangements, can achieve temperatures as high as 95C (203F) in commercially
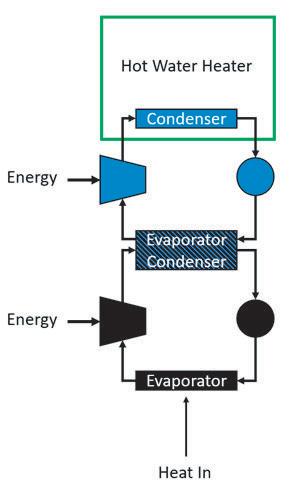
Continued on page “39”
Continued from page “37”
available equipment today.
So far, we have been discussing “heatonly” systems. However, a significant benefit of using high temperature heat pumping can come when cooling is needed simultaneously. Consider a 40F freezing tunnel—it would be possible to cascade this with an ammonia heat pump and achieve 200F process water. The combined COP of a heat pump cooling system can be very appealing, and they can result in large energy and/or carbon emission savings compared to a more typical refrigerationboiler system.
Unfortunately, introducing heat pumps into refrigeration systems is difficult. This difficulty rises primarily because it is hard to balance the heat and cooling needs effectively without one sacrificing the other. In other words, you need to provide heat when you need it and cooling when you need it. Operating the cooling without a demand for heat is relatively easy because you can always reject heat to the outdoors and the refrigeration system will continue to function normally.
Providing heat when cooling is not required is much harder because there is not always a source of heat readily available, and as we’ve already seen, the outdoor ambient air is not always able to
provide enough heat. Therefore, it becomes necessary to use alternate techniques like, low temperature electric boilers, buffer tanks, and/or phase change materials to save the heat from when the system was operating. These solutions add cost and complexity to an already expensive and complex system.
Keeping costs low
The industry will face continued reliability and cost challenges as these systems are often more expensive and complex than fossil fuel burning counterparts. There will be an effort by manufacturers to drive down costs in order to make the technology affordable, particularly in the commercial and residential markets. While this kind of pressure does help keep consumer pricing low, it can make the technology less reliable and ultimately this strategy may backfire if people revert back to fossil fuel options.
Unfortunately, in cold climates, this seems to be happening already with geothermal heat pumps. They are very expensive to install properly and many of the products available simply do not have refrigeration components with a very long lifespan.
When an owner is faced with an extremely large repair bill, they often revert back to the “cheap” gas furnace. Ultimately, as the world continues to transition away from fossil fuels and attempts to minimize carbon emissions, the rise of heat pumping technology is almost inevitable. The next step is to convince the industry that it needs to gear up for a fairly significant increase in refrigeration mechanics and people qualified at working on refrigeration systems. This is not an easy task.
Note: In an earlier article, it was mentioned that we would discuss the low temperature heat pump installed this year at this author’s house. While it is installed and operating, there wasn’t enough time in cold weather to gather the data needed for a good article. Look forward to that article next winter. :
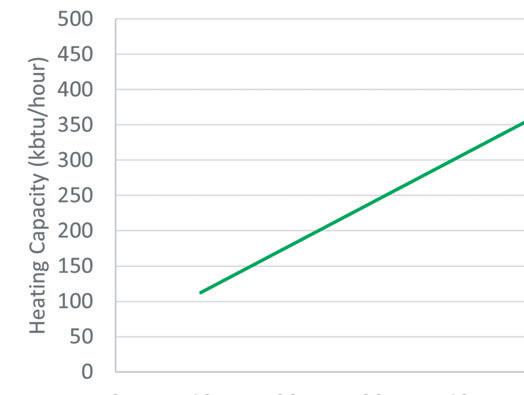

Figure 3: Heating capacity of the example compressor at different outdoor ambient temperatures.
Greg Scrivener is the lead refrigeration engineer and a partner at Laporte Consultants, Calgary, and works throughout Canada and the U.S. He is a professional engineer and journeyperson refrigeration mechanic. He can be reached at GScrivener@laporteconsultants.com.