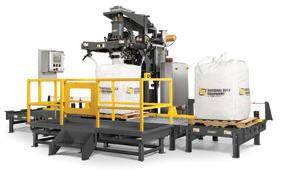
6 minute read
New Products
DIGITAL SORTER FOR PETFOOD INTEGRATES WITH MATERIAL HANDLING SYSTEMS
s
The Key Technology digital sorter for petfood can be configured to sort a range of petfood types to find and remove foreign material (FM) and products with defects. Installed at the end of the line, the Veryx sorter helps ensure final product quality for kibble, chews, and treats, including dried, dehydrated, and freeze-dried products. When installed upstream near raw receiving, it inspects ingredients, such as frozen proteins and other ingredients for wet petfoods. By detecting the color, size, shape, and/or structural properties of every object, the sorter removes plastics, glass, paper, and other FM. The unit can be equipped with Pixel Fusion technology, which combines signals from multiple cameras and laser scanners at the image pixel level to identify the most di cult-to-detect FM and defects. Key Technology | key.net
SCREW FEEDER OFFERS HIGH DEGREE OF ACCURACY AT LOW FEED RATES
The Vibra Screw feeder has an internal and external all-stainless-steel construction. Screw sizes range in size from ¼ to ¾ in., with feed rates as low as 0.0037 ft3/hr. The sanitary mini screw feeder can be configured as a volumetric feeder with accuracies of ±1 to 2% or as a gravimetric feeder with accuracies of 0.25 to 0.5%. The unit’s motor is available with a multi-layered, stainless-steel finish coating process or an all-stainless-steel construction. Vibra Screw | vibrascrew.com
s
Capable of handling highly abrasive, fine, and dusty bulk raw materials, the NBE bulk material packaging system has a cantilevered bulk bag support framework with a bag-load capacity of 4,000 lb. Pneumatically actuated traversing rear bag loop hangers bring the rear bag loop hangers forward to within operator reach, while a traversing fill head enables access to the full radius of the fill. Automation monitors the base-weigh scale system engineered into the framework and, based on preset weight specifications, adjusts upstream material supply to deliver controlled material infeed and bag filling. At preset intervals during the bag filling cycle, the densification base raises to isolate the pallet and bulk bag from the conveyor deck, and then initiates a vertical-motion vibratory action, causing air to be displaced.
National Bulk Equipment
nbe-inc.com
VOLUMETRIC FEEDER PROVIDES VERSATILE METERING AND HOPPERING CAPABILITIES
Suitable for continuous and batching applications, the Acrison volumetric feeder incorporates two independently driven metering augers with a dual agitator flow-inducing mechanism. The Model BDF-1.5-2 bin discharger feeder eliminates changing the size of the metering auger whenever a wide feed range is required. In a batching mode, a larger metering auger feeds the majority of the material for the selected batch weight, while a smaller metering auger provides the final “dribble” amount. The feeder is available with a range of options, including quick-disconnect and sanitary construction to satisfy FDA and USDA codes. Acrison | acrison.com
s
DISCHARGING SYSTEM PROMOTES FLOW OF MATERIALS THAT HAVE SOLIDIFIED
The Flexicon bulk bag discharging system has a cantilevered I-beam with an electric hoist and trolley that lowers a bag-lifting frame to floor level for attachment of the bag to the bag strap holders, and then hoists and rolls the bag into the safety frame. The BulkOut BFC system includes an integral conditioner consisting of two hydraulically actuated rams with contoured conditioning plates that press opposing sides of the bulk bag. A human-machine interface (HMI) housed in a NEMA 4 enclosure controls the stroke and number of ram actuations. For bulk bag discharging, the bag outlet spout is pulled through an iris valve mounted atop a dust hood over the hopper. Once the bag outlet is secured, and the iris valve is closed, the bag spout drawstrings can be untied, the access door is closed, and the valve is released. The hopper can be configured to connect to pneumatic or mechanical conveyors, or directly to downstream process equipment. Flexicon | flexicon.com
CONVEYING SYSTEM ROLLS TO TRANSPORTERS FOR CLEANER TRANSFERS
s
The Gericke conveying system allows the company’s dense-phase pneumatic conveying technology to be rolled and connected to the discharge of a tanker, railcar, or other bulk transporter. Developed to automatically transfer powders and other bulk materials from receiving outside the plant to storage inside the plant, the Pulseline PTA-PL mobile pneumatic conveying system transfers material as a pulsed plug at low velocities to safeguard particle integrity and maintain the distribution of mixed products. Engineered for conveying abrasive, fragile, and sensitive materials, the mobile docking station and conveyor transfer vertically to reach silo hatches and horizontally up to 500 m or greater using pulsed secondary air injections along the pipe. Gericke USA | gerickegroup.com
s
PADDLE BLENDER MINIMIZES AMOUNT OF REMAINING MATERIAL IN THE VESSEL FOLLOWING DISCHARGE
Able to de-agglomerate, blend, and condition dry bulk solids, pastes, emulsions, and slurries, the Munson paddle blender handles dry, moist, oily, paste-like, or otherwise di cult to blend free- and non-free-flowing materials in batches up to 25 cu ft. The Model HD-2.5-5-SS sanitary paddle blender features a heavy-gauge, stainless-steel U-shaped vessel that allows tolerances of 1/16 to ⅛ in. between the outer paddle edges and trough wall. Rotating paddles are forced through the batch, creating small zones where materials are repeatedly combined as they move slowly along the length of the vessel. Powered by a 10 hp (7.45 kW) motor with a helical gear reducer, the agitator is comprised of welded paddles projecting radially from the main shaft. Optional internal spray manifolds are available for liquid additions. Munson Machinery | munsonmachinery.com
CONVEYOR HANDLES FLOW-RESISTANT, SEMI-FREE FLOWING, AND OTHER CHALLENGING MATERIALS
s
The AFC flexible screw conveyor automatically transfers powders, pellets, and other dry bulk materials from a high-capacity hopper into mixers, reactors, tablet presses, or other equipment at various stages in the process. Available in five standard sizes plus custom sizes, the Spiralfeeder conveyor design increases ground clearance under the hopper for the capture of residual materials for reuse. It comes with a choice of optional accessories, such as a material agitator or vibrator for enhanced material flow, and a mobility package that sets the entire conveying system on casters. Automated Flexible Conveyor | afcspiralfeeder.com
VACUUM CONVEYING SYSTEM PROTECTS MATERIALS FROM CONTAMINATION
s
The Volkmann vacuum conveying system automatically transfers powders, pellets, and other bulk materials in a sealed, dust-tight design. Replacing bucket elevators, belt conveyors, and other open-air conveying systems, the VS pneumatic vacuum conveying system eliminates exposure to the plant environment, along with the potential for contamination due to humidity, pests, lubricants, and other risk factors. The sealed conveying system is explosion proof and ATEX certified for use in hazardous and non-regulated environments. Volkmann USA | volkmannusa.com
s
FILLING SYSTEM ECONOMICALLY PACKAGES VARIETY OF POWDERS
Designed for sanitary powder processing, the Powder Process-Solutions system utilizes four fully automatic bulk bag fillers with an overhead trolley transfer. The bags are filled in a critical hygiene zone and palletized in a medium-hygiene zone. The fully automatic bulk bag filling system features a suspension system for weighing bulk bags, a dust-tight fill head, and an inflatable bag seal ring that secures itself around each bag during filling to prevent product leakage. An impulse heat sealer is available as an option for integrated bag sealing. Powder Process-Solutions | powder-solutions.com
FEEDERS ENSURE HIGH-ACCURACY RESULTS
s
Coperion K-Tron tray feeders handle fragile inclusions, such as nuts, candy pieces, dried vegetables, and heat-sensitive chocolate chips, that may not be suitable in twin screw feeders. The K3 hygienic loss-in-weight vibratory feeders have a modular design that allows for custom tray designs for feeding into blenders or packaging lines. All the product contact parts are made of stainless-steel or FDA- and EC 1935/2004-compliant materials. Rates vary from 0.035 up to 300 ft3/hr. Coperion K-Tron | coperion.com