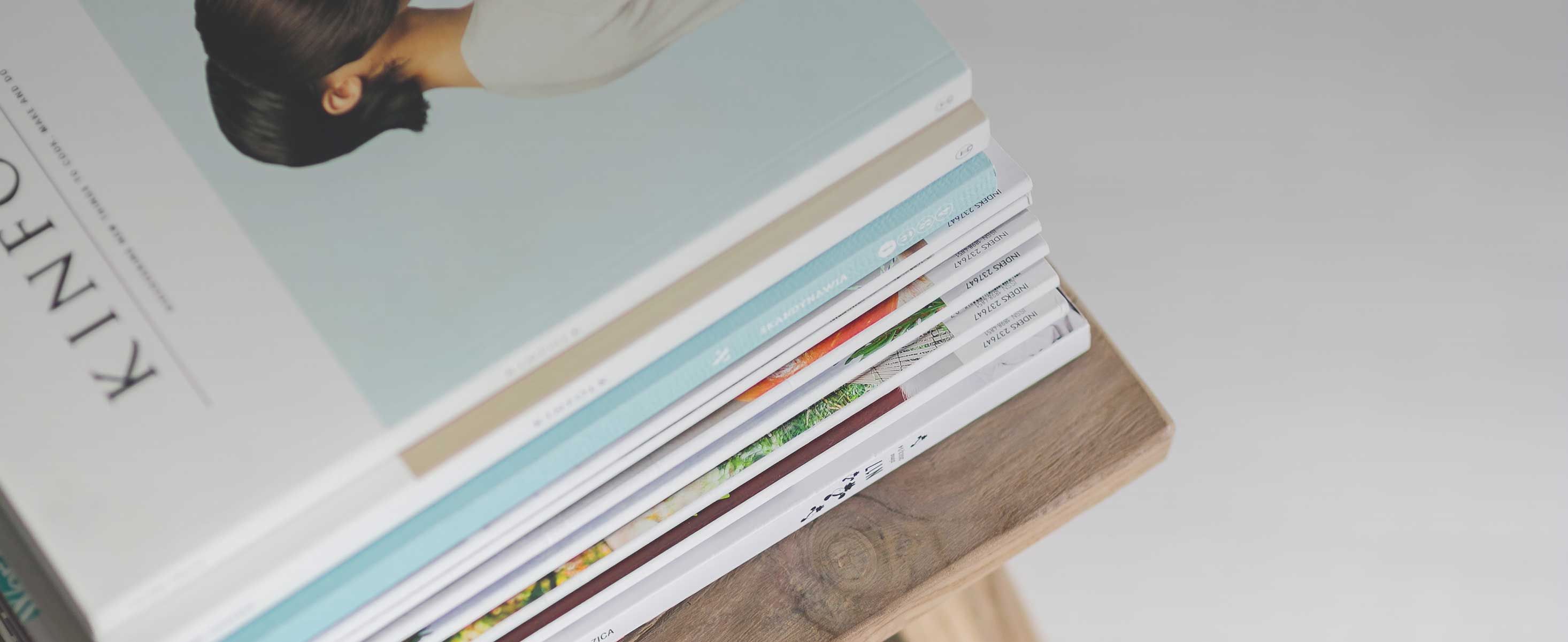
2 minute read
PRODUCTION POINTS
Improving Human-Robot Collaboration for Material Handling Tasks
By David Miller
dmiller@pmmimediagroup.com
Senior Technical Writer
Automation technologies aimed at streamlining material handling tasks have been on the rise both in manufacturing settings and the logistics space for some time now. Why? Because companies looking to match supply to demand are faced with a double bind. On the one hand, labor shortages are reducing the availability of manual workers. On the other, swelling e-commerce sales and a growing demand for customized orders mean that, not only are there more products to be moved, but doing so is more complex than with traditional mass production processes.
Autonomous mobile robots (AMRs) have proven a popular solution to these problems due to their flexibility and ease of deployment. However, even when outfitted with robotic arms, they still have some limitations. While ideal for moving items across large plant floors or warehouses, AMRs may still struggle with tasks such as picking, particularly if items are of diverse shapes or sizes, or are arranged in a non-uniform manner, such as what might be encountered in a box of mixed parts.
Artificial intelligence (AI) driven deep learning has been proposed to help robotic picking become more intelligent and adaptable in the long-term, but it could be years before most companies can benefit from such an endeavor. In the meantime, many are seeking to facilitate more efficient collaborations between humans and robots instead.
A recent partnership between robotsas-a-service (RaaS) provider Fetch Robotics and software company Lucas Systems exemplifies this approach. Lucas Systems will provide end-users of Fetch’s AMRs with AI-based warehouse optimization software that aggregates order, inventory, and location data from other systems and uses it to generate instructions for workflow optimization in real-time.
For instance, AI-driven analytics delivered via Lucas Systems’ software can direct workers as to how inventory can most efficiently be picked and packed out, while Fetch’s AMRs remain responsible for transporting the picked items to a conveyor or other system for further packing or processing.
Lucas Systems’ software includes a mobile application that allows users to scan items, view information, and issue voice commands. In addition, a console provides managers with real-time performance visibility and control of operations. Beyond monitoring operations, the software also allows managers to oversee workers and work-in-process, and update rules, settings, and configurations.
“The future environment of warehouses and distribution centers will be a mix of people, robots, machines, and systems all working together. The precise orchestration of all the pieces will be key to achieving a competitive advantage in performance,” said Ken Ramoutar, chief marketing officer at Lucas Systems. “That intersection of how people and robots work together is a hugely important and often overlooked part of warehouse automation equation, but it’s where a lot of the unseen value exists.”