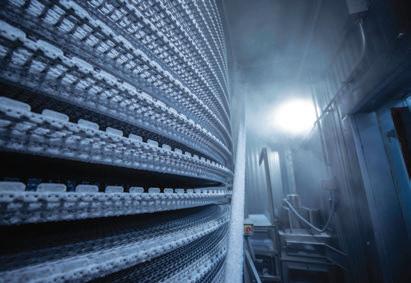
6 minute read
The World’s Most Hygienic Freezers
Hygiene
CIP with Pasteurization
Flexibility
Horizontal Airflow with subject matter experts around the plants that was key to why they’re using Movicon,” he says.
Through its partnership with PTC, Rockwell Automation provides Vuforia Chalk, which combines AR collaboration tools with real-time video communications for remote troubleshooting. It also incorporates the ability for the expert on one end to draw on the screen to help the technician on the other end, Garski explains.
It’s a fallacy to think that remote troubleshooting means you don’t need anyone local on the scene, Fondl comments. But with remote expertise, the person on site does not have to have such a high level of knowledge. This is a big part of where augmented reality can come in handy—to use the technician on the plant floor to give eyes to the expert at another location.
Predictive maintenance
To take this discussion in another direction, not all remote connections are about troubleshooting failing systems. The flip side is ongoing analysis, in many cases to keep the system from going down in the first place.
With its OEM customers, Emerson has been focusing increasingly on helping them understand how to create new revenue models with the connection capabilities available. “Using Movicon and/or IoT, they now can monitor and provide data to themselves at their home o ce that will help maintain that equipment and predict failure for the customer,” Millar explains. “I think that you’re going to start seeing that more and more, where end users will be demanding that from their OEMs.”
In some cases, it’s hardly even possible to get physical access to the machine to check on any potential issues. This was the situation for House of Raeford’s plant in Hemingway, S.C., which makes mini corndogs. Every product in the facility goes through its spiral freezer at some point. To say a spiral freezer is di cult to maintain is a bit of an understatement.
“For someone who has never had exposure to the spiral freezer, they have no idea that walking on the inside is like walking in a hurricane,” says Dean Page, plant manager for House of Raeford. “We operate from about -36°F to -40°F, so it’s extremely cold. The wind that is generated by the large-velocity fans is tremendous, so it doesn’t present a good opportunity for a technician to diagnose issues or work on problems once they’re found.”
The spiral freezer House of Raeford has from Ashworth, however, is equipped with a SmartSpiral system—designed to help users run and maintain the equipment correctly. The system analyzes data for alarms, which are sent to the customer.
Unplanned downtime used to cost House of Raeford about $6,000/hr, according to Page, with no way of seeing into the spiral to anticipate bearing failures and belt crashes. Now, with SmartSpiral, the food company has reduced downtime by 200%.
It can be di cult to get customers to understand the importance of the trending data and what it can discover, explains Chris Trinch, senior product engineer for Ashworth, recalling a time when they spotted a deviation with a customer in Minnesota.
“We saw a pattern of a certain temperature range— it was -33 to -32°F. Well, one day we started seeing about a degree and a half fluctuation in that temperature range,” he says. “But when we notified the customer, the customer elected not to do anything about it. The week after that, they crashed—the entire plant refrigeration, not once, but twice.”
FPS Food Process Solutions has had its Remote Monitoring System (RMS) out in the industry for about a year to help its customers monitor their freezing systems. It’s been a vital development in the industry, according to Brock Price, manager of global reliability and maintenance programs for FPS.
“Production’s huge right now in food and beverage,” he says. “Downtime and their equipment not creating the quality they need is not an option. So they’re moving toward this more predictive style of remote monitoring tools.”
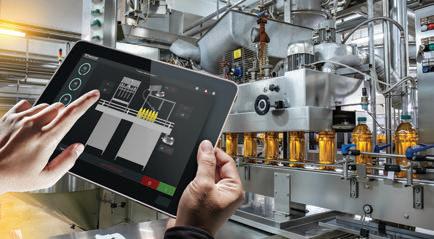
The nature of a spiral freezer—like walking inside a hurricane—makes it di cult for technicians to diagnose issues or work on problems once they’re found. The SmartSpiral system makes it easier to know where to focus maintenance e orts.

A key driver for remote monitoring is the trouble that companies are having hiring the skilled workforce they need, Price says. “This is a way to get ahead of that resource issue that a lot of companies are having today,” he says. Remote monitoring also helps bridge the gap between experienced and inexperienced workers. “Now they have a place to call to get some help.”
How to manage the data
For its remote monitoring, FPS relies on Ignition technology from Inductive Automation. “It’s a oneway communication, so we can’t go back past the MQTT module and back into the PLC and do anything with their equipment,” Price explains.
This kind of established security is key to bringing the data out safely. “For most companies that we’re working with, that works well for them,” Price says. “Secure information is a huge concern for all of our customers, as well as us.” that their main valuable asset
There is plenty to be said about the value of remote connections that allow the OEM to continually analyze the data coming from the machine. But it also brings up an increasingly hot topic of data governance—which data should be available for which parties. “Just because the data has some value to one and no value to the other doesn’t mean that all data should be denied to leave the facility, but rather sophisticated data governance policies should be put in place so that the data can be carved out in ways that make sense,” Cramer says.
Tetra Pak has seen more concerns even just within the past year from its customers about what is happening with the data that the equipment maker gathers, Marra notes.
“There are a lot of customers that their main valuable asset nowadays is data,” she says.
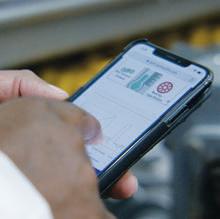
“Everyone knows how to do a lot of things, and equipment is the same, basically. What is going to change is how they are operating, how they are improving the way that they operate, the parameters that they are using, especially when we are talking about new kinds of products.” cially when we are talking about
OEMs are finding that the data gathered for ongoing analytics can be helpful within the day-to-day troubleshooting as well. Remote troubleshooting is no easy task. “Being by the machine and being able to see and smell and feel and hear all those things that are going on really aids in your troubleshooting ability. So if you’re being called up to do a remote connection to the machine, a lot of the things that would have been available to you when you were there aren’t available,” Cramer notes. “So what do you replace it with? You replace it with the data.” gathered for ongoing analytics can
That data can often be considerably more fruitful than trying to get the information from the people on the other end of the line, as Garski describes.
“When the service phone rings, the first question the guy asks is, ‘What did you do to it? What changed?’ And the operator or the maintenance guy always responds, ‘Nothing. I didn’t do anything.’”
From there, the detective game starts.
“Historically, that fault history would have been stored on the machine itself. So now you’re rely-
OUR PASSION FOR YOUR PROJECT’S SUCCESS RUNS AS DEEP AS YOUR OWN ing on a human being to connect with a computer or a USB stick or something else to try to get you this log file to be able to walk backwards in time,” Garski explains. “If I don’t need to rely on somebody to do that, it’s faster.”
Not everything can be solved remotely
Just like doctors cannot diagnose every illness without running extensive tests, not every mechanical issue will be able to be resolved through a remote diagnosis.
“There are situations that are a combination of programming, mechanical, electrical—it could be a hotspot of five di erent things, almost impossible. But there are other things that are really easy to solve,” the CPG’s engineer says. “It goes both ways—not every problem can be solved remotely; that is the trick. But some can be.”
If nothing else, the remote diagnosis can often provide an indication of which technician it would be best to send out for on-site servicing, Garski notes.
“I don’t think there’s ever a fix for not having a great maintenance person in your plant,” says Jonathan Darling, CPG industrial automation market segment leader at Schneider Electric. “But what remote connectivity allows you to do is to be a Band-
Aid of sorts, or a fix to where, even if your maintenance team hasn’t been there for 25 years and they can hear that tick as they’re walking by that piece of equipment and know something’s wrong, they can connect with the OEM who made the piece of equipment, can sit there on their iPad or whatever, and be able to, with that tech, who is an expert on that equipment, look at what’s going on, look at the data that’s being produced, have visibility into the equipment and the diagnostics, and be able to help make decisions on how to fix that piece of equipment.”
The general consensus is that remote troubleshooting is a necessity. “It should always be the first thing before we call out a technician,” Gri en says. “There’s absolutely value there, but let’s not fool ourselves into thinking that means we won’t ever need to have a technician on site again.”
Ashworth www.ashworth.com
Bosch Rexroth www.boschrexroth.com ei3 www.ei3.com
FPS Food Process Solutions www.fpscorp.com
OMAC www.omac.org
Rockwell Automation www.rockwellautomation.com
Schneider Electric www.se.com
Tetra Pak www.tetrapak.com