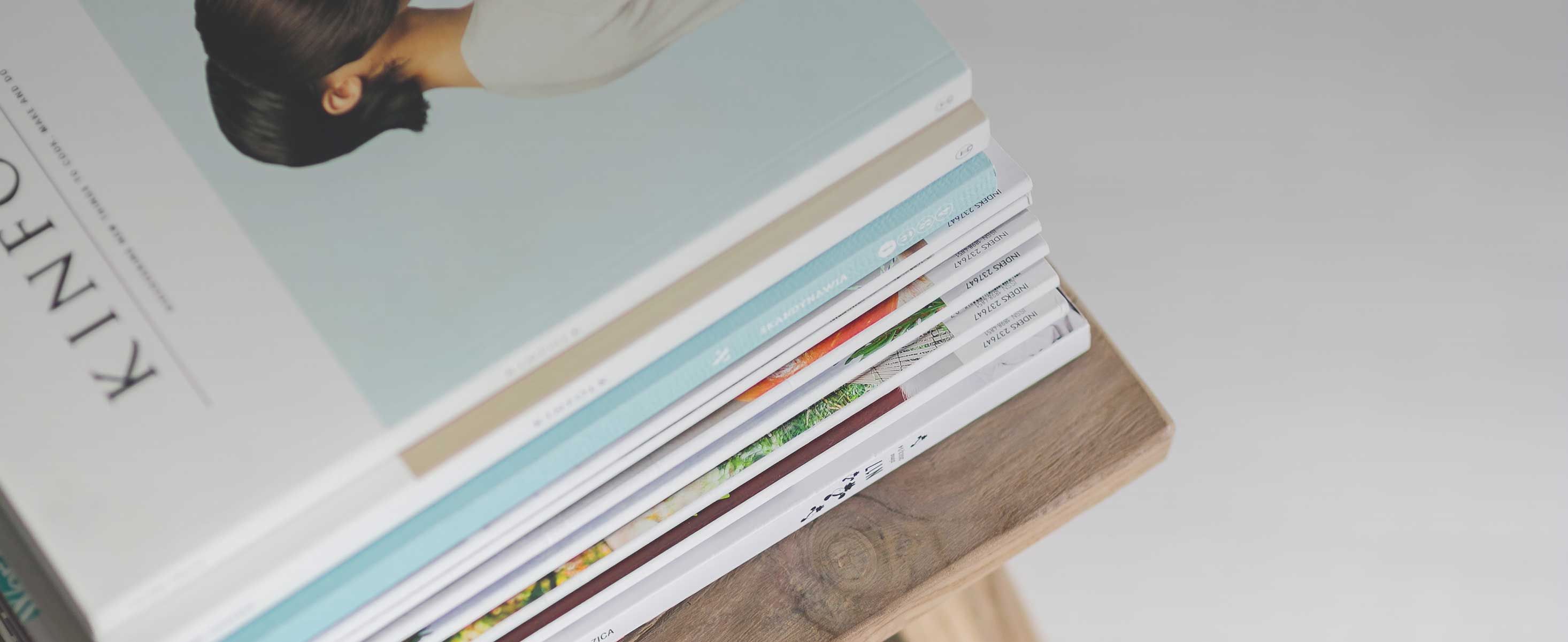
3 minute read
Workforce solution
Redzone introduced its Frontline Learning Module (21), an addition to the company’s workforce solutions software platform. Richard Tester, Redzone’s co-founder and CEO, says the new module aims to take tribal knowledge about operating manufacturing equipment out of the heads of machine operators and onto Redzone’s platform as video, where it can be watched as a best practice by other employees.
“If you’ve run a filling machine, for example, for 25 years, you know the best way to use it, or do the startup or changeover on it,” Tester says. “With our new module and an iPad or iPhone, you can record a quick two- or three-minute video, which can become a best practice for that machine at your company. It’s like a YouTube application for the plant floor. Like anything in life today, if we want to learn how to change a tire on a car, for example, we can go to YouTube and watch a five-minute video, right? So we’re introducing that technology onto the plant floor, and it looks at the
The new mixer’s variable gap allows the user to dial in the particle size needed for shelf-stable emulsions, resulting in more consistent particle sizes with a tight distribution. Some applications for this mixer include mayonnaise, dressings, dips, oil and fat emulsions, condiments, dairy solids, and more.
“We have a blender, but blenders only go so far,” says Jim McCoy, sales manager, Americas, Fristam Pumps. “We were getting a lot of requests saying, ‘Hey, I need you to move down the particle size range.’ So this is the result of that, and we can meet their exact, precise requirements for particle size. Plus, this mixer fits in with our whole portfolio of products.” whole frontline employee experience, which we think is something that’s been massively overlooked in manufacturing for the last couple of decades.”
The Fristam FCM also features CIP without disassembly, designed for hands-o use that allows you to adjust the gap to the maximum setting and CIP through the mill without removing any parts. The mixer has a max shear rate of 143,000 1/s, can handle sub-micron particle size, has a max inlet pressure of 250 psi, a max product fl ow rate of 50 GPM, a max CIP fl ow rate of 100 GPM, is bi-directional, and has a 50 HP motor size.
The Frontline Learning Module comes on the heels of Redzone’s other recent addition, the Reliability Module, which puts basic machine maintenance knowledge into the hands of operators and tracks machine OEE and maintenance schedules, so maintenance crews can focus on crucial repairs, especially helpful for manufacturers with a labor shortage.
“The technology really drives all of the daily operating behavior for the frontline teams,” Tester explains.
“Whether it’s running the line and tracking performance, whether it’s quality, whether it’s maintenance— this gives operators the ability to do basic preventive maintenance. So we shift maintenance resources away from performing day-to-day tasks and move basic care for the equipment into the role of the operator.”

Axiflow Technologies debuted its bulk drum unloader (22) at PACK EXPO International. This new tool for removing fluids and soft solids up to 3 ⁄4 in. from plastic, metal, and fiber drums of 16, 20, 30, 55, and 75 gal features a speedy 50+ gal/min (GPM) unloading, with discharge pressures up to 375 psi. This CIP-ready bulk drum unloader can handle product viscosities over 500,000 centipoise, and it can be fitted with custom plates for di erent sized drums, as well as mix kettles and pots. The plates are also removable for pumping out totes and tanks.
Graco unveiled its updated electric pump (23) for food processing, boasting energy savings up to 80% more than traditional pneumatic air diaphragm pumps. According to Je rey Sha er, senior product manager and North American sales manager hygienic equipment at Graco, the company has been making electric pumps for about six years, but Graco recently developed patented technology that eliminates the need for a gearbox inside a pump, reducing the footprint and significantly increasing its energy savings.
“We have the motor and drive package right in the middle of the pump, but there’s no gearbox now, which reverses package size and cost to the user,” explains Sha er. “A big benefit with electric is it reduces your energy costs as far as e ciencies by up to 80%. So while a pneumatic pump might cost you $2,000 a year to operate, this might cost you $200 a year. So big savings, and it also qualifies for energy incentives from our company.”
Sha er adds that the new version of Graco’s electric pumps works seamlessly with facility control systems that can monitor the pump’s usage around the clock, which facilitates predictive maintenance, saving time and labor.