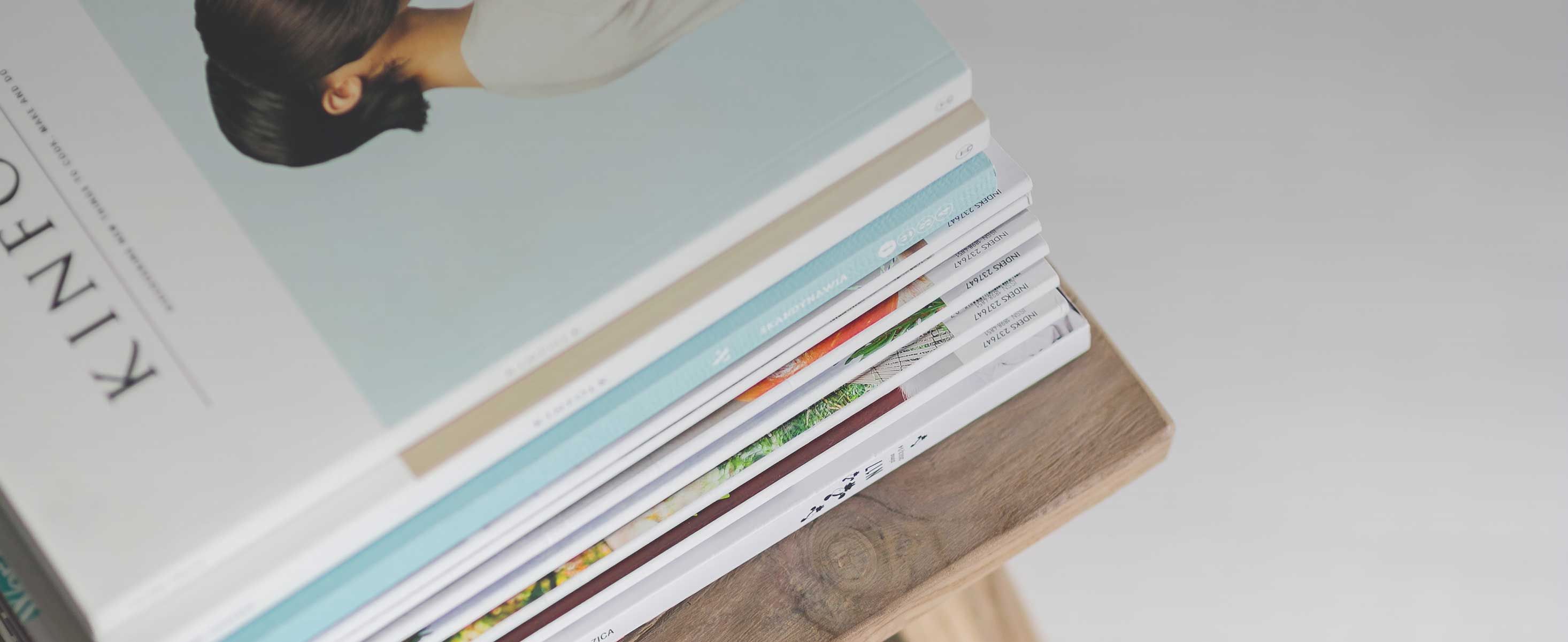
3 minute read
Don’t react. Prevent.
Mitigating food safety risks starts with thoroughly understanding the hazards and developing safeguards.
(PSOR\HHVZKRDUHWUDLQHGDQGFHUWLƮHGLQWKHODWHVW best practices of preventive controls are crucial to successful implementation of a food safety plan.
:HRƬHUFRQYHQLHQW)63&$WUDLQLQJERWKRQOLQH and in-person for individuals or groups.
'D\3UHYHQWLYH&RQWUROV IRU+XPDQ)RRGV
'D\3UHYHQWLYH&RQWUROV IRU+XPDQ)RRGV3DUW
'D\,QWHQWLRQDO$GXOWHUDWLRQ &RQGXFWLQJ9XOQHUDELOLW\ $VVHVVPHQWV,$9$ dennisgroup.com info@dennisgroup.com
7RVLJQXSIRUDQXSFRPLQJFRXUVHYLVLW dennisgroup.com/services/food-safety. )RUJURXSLQTXLULHVFRQWDFW.DUD6FKHUHU at scherer@dennisgroup.com.
+1.888.514.7270
United States Г Canada Г Brazil
“We spent years figuring out how to get into the U.S. market. We were looking at all our customers’ sore points,” says Russell Jones, commercial manager for pumps at Alfa Laval. “This tackles about five common problems.”
One improvement is the elimination of contact between the pump’s rotor and casing. Traditional CPPs have constant contact between the rotor and plate, Jones notes. Alfa Laval guarantees no contact until at least 360 psi, he adds, helping to increase durability and pump life while also reducing the chance of media contamination.
The pump is certified to meet 3-A Sanitary Standards, but goes beyond those standards to ensure cleanliness. The fully CIPable design is standard. “After the CIP cycle, it’s not only clean, but there’s no residue,” Jones says. That’s true even with viscous products, which can have challenging particulates, he adds. Also meeting EHEDG guidelines, the DuraCirc pump assures process integrity and product quality. For a crevice-free design with no dead zones, all product-wetted elastomers are made of FDA-conforming materials and profiled and defined compression as standard; this reduces contamination risks and cuts both cleaning time and costs. The all-stainless steel construction is also suitable for hygienic washdown.
Maintenance is also reduced through an FDAconforming oil lubricant that has an extended service interval—about 3,000 hours vs. 750 hours for a typical competitor. Front-loading self-setting mechanical seals are easy to get to, making them quick and easy to change without the need to remove the pump from the system.
More recently, Alfa Laval introduced a subscription-based digital monitoring system for pumps and other rotating equipment such as agitators and mixers in hygienic processing industries. CM Connect enables operators to access data from a remote location. It provides operators the information they need to make informed maintenance decisions—such as actual runtime, trend analysis, and time to the next service. Advanced vibration analysis enables early detection of any deviation from pre-set equipment threshold values.
Equipment for depalletizing also made a splash at PACK EXPO International, especially at Ska Fabricating. Though the U.S. has standardized on mainly one pallet size, this is not the case in Europe, where manufacturers are dealing with a much broader range of pallets. With this in mind, Ska introduced an international configuration of its Microbus depalletizer (27 )—now able to handle six of the world’s common pallet sizes.
Like the original Microbus launched earlier in 2022 in the U.S. and Canada, the International Microbus, which made its debut at PACK EXPO International, is a semi-automatic empty-can depalletizer that features a manual hand crank to raise the pallet carriage and an automatic belt sweep that advances cans onto a rotary table prior to rinsing and filling. Capable of speeds to 30 CPM, the portable depalletizer is optimized for lower-speed applications in the smallest of spaces.
“This is a good fit for really small companies because it folds up and can be tucked away,” says Jake Kolakowski, chief customer o cer for Ska Fab. Both the rotary infeed table and the automated sweep can be folded and locked down for storage after canning runs. This reduces the footprint of the already small machine to about half its full size, which is much needed in many small craft brew facilities, Kolakowski notes. “These places are so packed in, they don’t have a lot of space to work with,” he says.
Ska Fab also showcased the fruits of its acquisition early this year of GR-X Manufacturing , which specializes in depalletizing and palletizing equipment systems for consumer products and food and beverage industries. Though both companies play firmly in the palletizing/depalletizing space, there is very little overlap in their market segments.
The expanding world of inspection
Wipotec used PACK EXPO International to showcase its new Traceable Quality System with Modular Design (TQS-MD). The system (28) uses a “building block” concept yielding compatibility with a broad array of products.
“This system is designed for trays, for food products, medical device, and more,” says Daniel Brandao, regional sales manager at Wipotec. “We have the system set up with infeed metal detection integrated into our weigh cell, then we have our labeling device for top and bottom labeling. The bottom labeler includes a printer for variable data. The system applies those labels and scans for posi-